Studienreise Nachhaltigkeit im Produktdesign
Besuche bei zukunftsfähigen Unternehmen in der Schweiz Februar 2023

Melanie Amstutz
Anuschka Berger
Laurent Boschung
Monika Brzozowska
Alexander Danuser
Sebastian Erb
Kerim Ergül
Lilia Glanzmann
Marc Lieberherr
Miriam Nietlispach
Christoph Schindler
Sivan Sureskumaran
Bigna Suter
Annina Weiss
Daniela Zimmermann
Studienreisen sind neben Praktika und Modulen mit Partnerfirmen ein wichtiges Element eines Studiums, sich mit den konkreten Möglichkeiten und der Breite des Horizonts der Berufspraxis auseinanderzusetzen. Wir erleben im Produktdesign einen Moment, in dem die Auseinandersetzung mit zukunftsfähigen Haltungen zum Produktdesign einen «Tipping Point» erreicht, eine Schwelle überschreitet, in dem nachhaltige Konzepte sich relevant und tragfähig in der Praxis verankern – etwa zum Umgang mit Rohstoffen, Mobilität, Besitz, Ernährung und Inklusion. Vieles deutet darauf hin, dass sich diese Entwicklung fortsetzen wird und ein immer grosser werdender Teil unserer Alumni jenseits der bestehenden Berufskategorien ganzheitliche Ansätze zum Produktdesign verfolgen wird. Es ist uns ein Anliegen, unsere Studierenden mit diesen neuen Möglichkeiten und Denkweisen vertraut zu machen. Wir haben mit Miriam Nietlispach vom Cerca Research und Design Lab eine einwöchige Studienreise organisiert, in der wir Firmen besuchen, die sich nachhaltigen Konzepten verschrieben haben. Zunächst hatten uns den Fokus auf die Schweiz gelegt, um im Angesicht der Pandemie etwas mehr Planungssicherheit zu gewinnen. Im Verlauf wurden uns weitere Aspekte bewusst: Neben den geringen Emissionen durch die kurzen Wege lernten wir den Entwicklungsstand Nachhaltigkeit im eigenen Land kennen und erkannten das Potential langfristiger Kontakte zu den besuchten Firmen, sei es für Projektzusammenarbeiten wie auch als zukünftige Arbeitgeber:innen für Studierende.
Wir beobachteten mit grosser Freude, dass es Produktdesigner:innen gelingen kann, über die Denk- und Arbeitsweisen der Industrialisierung hinauszugehen. Wir sind gespannt, was die Eindrücke aus dieser Woche bei unseren Studierenden auslösen.
Christoph Schindler Studienrichtungsleitung Objektdesign
Lilia Glanzmann Studienrichtungsleitung Textildesign
Klaus Marek Studienrichtungsleitung Spatial Design
Montag, 06. Februar 2023
Halle 118, Umbau durch Insitu
Lagerplatz 22, 8400 Winterthur
Führung von Michèle Toboll
Planted
Kemptpark 32-34, Kempthal
Kompotoi
Zürcherstrasse 254, 8406 Winterthur
Führung durch Gründer Jojo Linder
optional: Sonne, los jetzt! von Elfriede Jelinek
Aufführung im Schauspielhaus Zürich
Dienstag, 07. Februar 2023
FREITAG
Binzmühlestrasse 170b, 8050 Zürich
Vorstellung Circular Trap und Führung Produktion
JungleFolk
Sihlquai 55, 8005 Zürich
Besuch NEST der Empa
Ueberlandstrasse 129, 8600 Dübendorf
Führung durch die Einheiten UMAR, HiLo, WaterHub
UMAMI
Badenerstrasse 569, 8048 Zürich
Führung und Apéro
Mittwoch, 08. Februar 2023
Mycrobez
Grellingerstrasse 27, 4052 Basel
Innorecycling
Hörnlistrasse 1, 8360 Eschlikon Betriebsführung
Donnerstag, 09. Februar 2023
Remei
Lettenstrasse 9, 6343 Rotkreuz ZG
Nachhaltige Textilherstellung
Ausstellung Planetopia MFK
Helvetiastrasse 16, 3000 Bern
Führung durch Offcut Szenographen Silvan und Simone
Film Going Circular
Viadukt, Bogen D – Impact Hub Zürich mit Reform, Simon Widmer und SDA
Freitag, 10. Februar 2023
Girsberger
Bernstrasse 78, 4922 Thunstetten
Input Remanufacturing und Führung durch die Produktion
Kochen mit Maurice Maggi
HSLU D&K, Nylsuisseplatz 1, 6020 Emmenbrücke in der Küche Objektdesign
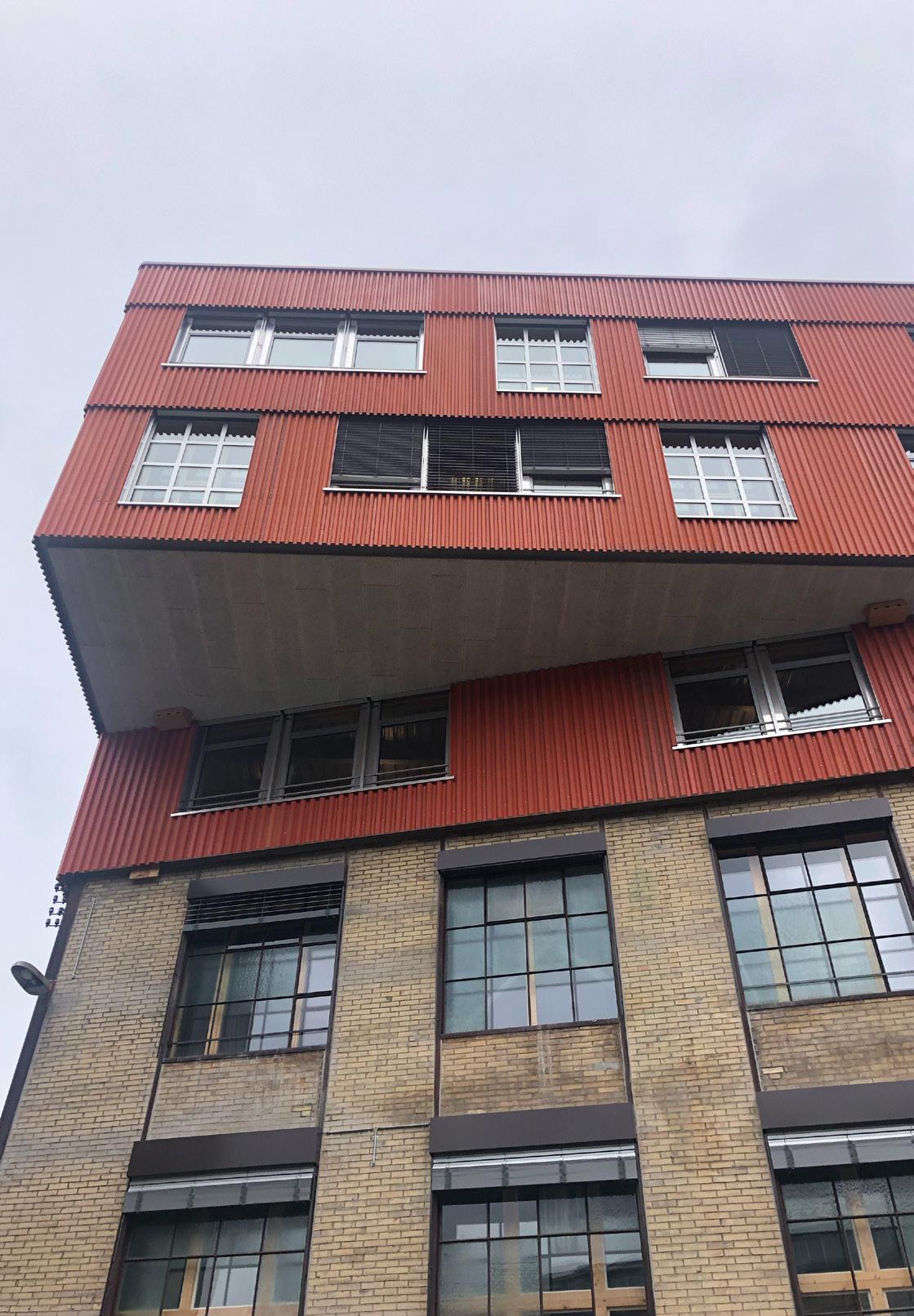
Abfall und Industrie

Das Alte Industriegebiet Sulzerareal ist ein wichtiger Bestandteil von Winterthur. Das Gebiet wird seit Jahren urbanisiert und bietet viele Möglichkeiten für Umnutzungen. In diesem Areal treffen Vergangenheit, Gegenwart und Zukunft aufeinander. Die Grösse dieses 20 Hektar grossen Areals wird einem erst wirklich bewusst, wenn man auf der Dachterrasse des «Abfall-Hauses» Kopfbau Halle 118 steht. Doch so abwertend «AbfallHauses» auch tönen mag, so ist dies wortwörtlich zu nehmen. Doch ganz von Anfang an.
Kalter Morgen
Unsere Studienreise startete an einem kalten Montagmorgen vor einem Kaffee mitten im Sulzerareal in Winterthur. Ich wusste nicht, was uns an unserem ersten Tag genau erwartet und war sehr gespannt darauf. Nachdem alle vor dem besagten Kaffeehaus eintrafen und Christoph mit einer Volkszählung sicher gegangen war, dass wir alle sind, liefen wir weiter in Richtung der Industriegebäude. Von weitem ist unser Zielobjekt mit seiner rot-orangen Alublech-Fassade inmitten der braunen Steinfassaden nicht zu übersehen.
In Kreisläufen gedacht
Kaum war die gläserne Tür zu den hellen Räumlichkeiten geöffnet, entdeckten wir viele Sachen, die nicht alltäglich waren.
Fenstergriffe die um 90 Grad verschoben waren; eine Wand, welche aus gestapelten Ziegeln bestand und an der Decke hingen einige aus etlichen Lichtröhren zusammengestellten, zylinderförmige Lampen. Doch diese Sachen ergaben dann auch erst wirklich Sinn, als uns eine Architektin vom Büro Insitu mehr über den Bau erzählte. Denn dieser Bau ist etwas Spezielles und sehr wertvoll für das Kreislaufdenken. Der Kopfbau Halle 118, oder einfach K 118 wurde ausschliesslich aus «Abfall» Materialien gestaltet, geplant und schlussendlich umgesetzt. Bewusst wird hier «Abfall» in Klammern gesetzt. Denn für die meisten dieser genutzten Materien war die Müllhalde vorgesehen. Diese wertvollen und zumeist intakte Werkstoffe werden hauptsächlich aus Kostengründen nicht abgebaut. Denn Abreissen ist überwiegend günstiger als diese Rohstoffe und Gegenstände aufwändig abzubauen, zu lagern und dann wieder in den Kreislauf zu setzen.
Umsetzung
Das 2,257 Mio. CHF schwere Bauprojekt wurde 2021 fertiggestellt. Es umfasst vier neue Geschosse, auf denen zwölf Ateliers und Denkstuben sowie ein Tüftlerlabor, mit Werkstatt im EG und im Zwischengeschoss, Platz finden. Das Stahltragwerk der Aufstockung stammt aus einem ehemaligen Verteilerzentrum einer Supermarktkette in Basel. Die Planung sah zwar eine formgleiche Aufstockung vor, das Stahltragwerk wies aber eine Abschrägung an der Südostfassade auf. Ab dem 4. Geschoss kragt der Kopfbau daher aus und vollendet dabei eine andere Flucht, die in den unteren Geschossen durch den Verlauf eines Industriegleises unterbrochen ist.
Wieso entschieden sich die Architekt:innen dafür, das Stahlskelett in seiner originalen Form einzusetzen?
«Ein Bauteil anzupassen ist weitaus schwieriger, als die Idee zu adaptieren», fasst Marc Angst, der an diesem aussergewöhnlichen Projekt mitwirkt, eines der Konstruktionsprinzipien im zirkulären Bau zusammen. So kommt es, dass die von einem Zürcher Bürogebäude stammende Aussentreppe aus Stahl schliesslich die Höhe der sechs Geschosse vorgibt.
Strohige Wärme
Der Innen- sowie Aussenbereich des Gebäudes wurde ausschliesslich mit gebrauchten Materialien gebaut und aufgewertet. Bei der Isolation wurden unbehandelten Strohballen aus konventioneller Getreideernte genutzt, die innen gleichzeitig als Putzträger für den Lehmputz aus einer nahen Baugrube diente. Die Ballen wurden in eine extra dafür vorgerichtete Holzkonstruktion eingefügt. Damit wurde eine gute und im zirkulär
gedachte, nachwachsende Lösung für die Isolation gefunden. Bei der Fassade entschied sich das Büro für auffallend rot-orange Aluminiumplatten, welche bei einer Druckerei in Oberwinterthur entnommen wurden. Das Gebäude fügt sich durch diese Fassade und die Farbe gut in die industrielle Umgebung ein und setzt bewusst Akzente. Auch steht es sinnbildlich über all den andern Gebäuden und wirbt so für das Nachhaltige Bauen.

Die Vor- und Nachteile
Die grössten Vorteile bei diesem Vorgehen sind, dass man schon produzierte Materialien nutzen kann. So sparte man die aufwändige Produktion neuer Materialien und verbraucht weniger CO2. Vor allem aber wird der gesamte Bauprozess überdacht. Muss man wirklich bestehende Gebäude abreissen oder kann im Bestand geplant und umgebaut werden? Was als Vorteile zugleich aber auch als Nachteil betrachtet werden kann, ist dass

der Planungsprozess vom Material und nicht von der Vision ausgeht. So muss man ein Feingefühl für die Kombination dieser verschiedenen Materialien besitzen und zugleich flexibel in der Gestaltung sein. Oder wie es Juliane Trahan Architektin bei Insitu sagt:
«Um Sekundärrohstoffe einzusetzen, muss der Planungsprozess umgekehrt werden: Es gilt, erst Altmaterialien aufzutreiben und diese zu erfassen, bevor der Entwurf- und Montageprozess beginnen kann. So müssen die Planerinnen und Planer stets agil in ihrer Vorstellung bleiben, da sich mit laufender Materialsammlung auch die Möglichkeiten des Endproduktes stetig verändern. Die Bauteile werden anschliessend penibel ausgemessen und katalogisiert. So entsteht in einem ständigen Abwägen schliesslich der finale Entwurf.»
Schlusswort
Der Besuch im Gebäude K 118 war sehr interessant und inspirierend und zeigt auf, dass aus gebrauchten Materialien schöne Architektur entstehen kann. Auch das Vorgehen des Büro Insitu ist bewundernswert und benötigt grosses Fachwissen um den grossen logistischen Aufwand sowie die Gestaltung und Planung dahinter zu stemmen und daraus schöne, nachhaltige Architektur zu erschaffen.
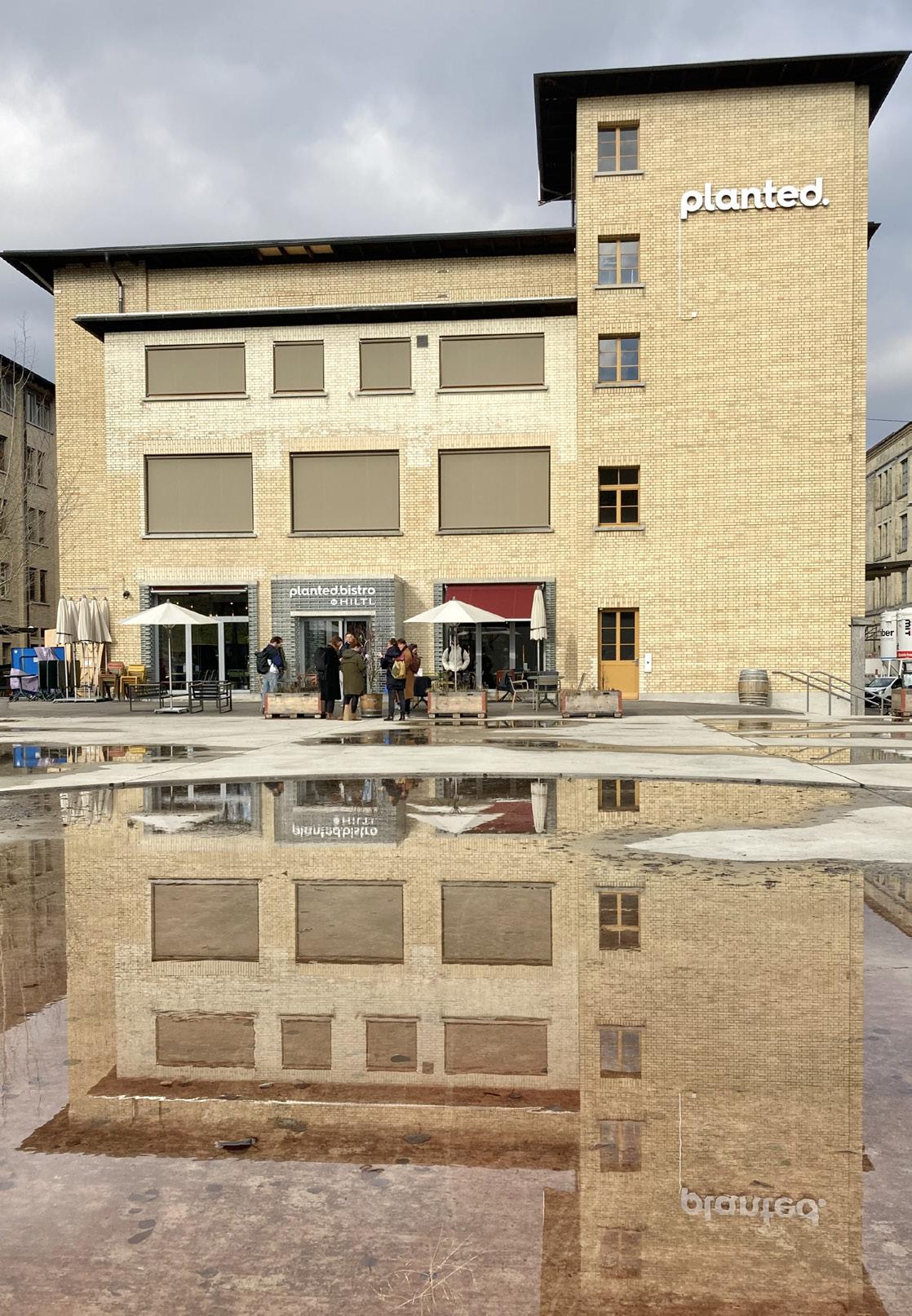
Der Fabrikationsstandort der Firma Planted, liegt südlich von Winterthur. Das Industriegebiet «The Valley» hat trotz neuem Namen jedoch eine bereits ereignisreiche Geschichte hinter sich. Denn da, wo heute ein Sammelplatz aufstrebender Firmen ist, war zuvor rund 130 Jahre lang die Firma Maggi ansässig.
Die Kombination von altem, backsteinernem Industriegebiet und neuen Unternehmen löst Tatendrang aus. Der Haupteingang von Planted liegt an einem Platz und führt direkt ins hauseigene Restaurant, natürlich vegetarisch.
Planted wurde 2019 von Pascal Bieri und dessen Cousin Lukas Böni gegründet. Pascal Bieri störte sich auf einer USA Reise an den vielen Zusatzstoffen in den Fleischalternativen. Lukas Böni absolvierte zur selben Zeit den Doktor in Lebensmittelverfahrenstechnik, womit sich eine Zusammenarbeit anbot. Ziel war es eine Fleischalternative herzustellen, welche keine Zusatzstoffe enthält.
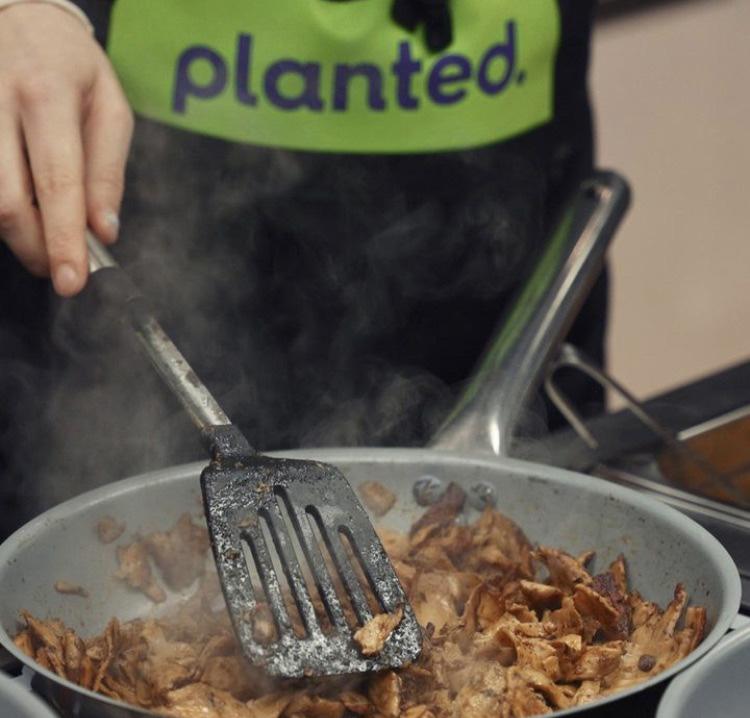
Nebst anderen Auszeichnungen erhielt Planted auch den Swiss Start-Up Award 2021 und bekam so zusätzlichen Schub. So ist die Belegschaft bis heute bereits auf rund 200 Mitarbeiter; innen angewachsen und die Firma produziert immer mehr unterschiedliche vegetarische Produkte. Zum Start unseres Besuches kommen wir in den Genuss, uns grosszügig am Buffet bedienen und so auch direkt von den Planted Produkten kosten zu dürfen. Nach einem sehr leckeren Mittagessen geht es dann hoch in den Präsentationsraum mit Blick auf die Produktion.
Während der Präsentation erhalten wir einen sehr spannenden Einblick in die Entstehung der Firma Planted sowie in die Entwicklung neuer Produkte. So wird uns der genaue Ablauf erläutert, welchen wir später zu Gesicht bekommen, um dann auch zu verstehen, was man sieht. Immer wieder entstehen während der Präsentation kleine, spannende Diskussionen. Die meisten führen zur Erkenntnis, dass es aktuell einfach noch zu viele Regeln gibt, welche die Produktion von Fleischalternativen massiv einschränken und verteuern. Erst vor kurzem konnte man einen kleinen Erfolg verbuchen. Da Planted ihre Produkte hauptsächlich aus Gelberbsen produziert, welche sie zu grossen Mengen aus Frankreich importieren, stiessen sie auf ein spezielles Gesetz. Gelberbsen, welche als Nahrung für den Mensch gedacht sind, kosten 3mal so viel wie Gelberbsen für Tierfutter. Dies konnten sie kürzlich dank viel Engagement korrigieren.
Die anschliessende Führung durch die Produktion war sehr spannend. Dies lag daran, dass Planted kein Geheimnis aus der Produktion macht und sämtliche Schritte durch ein Glashaus betrachtet werden können.
Die Produktion verfügt über zwei parallele Produktionsstrassen. Während unseres Besuchs war jedoch nur eine in Betrieb, da die aufwändigen Planted Grillspiesse hergestellt wurden und diese alle Produzierenden in Anspruch nehmen.
Zu Beginn der Produktion steht die Fertigung der Masse, aus welcher die Produkte gefertigt werden. Mit kleinen Abweichungen ist die Mischung immer gleich. Die Masse kann mit einem Pastateig verglichen werden, welcher konstant aus der Maschine extrudiert wird. Während den nächsten zwei Schritten wird die gewünschte Grösse der Stücke erzeugt, dies mit rütteln und zupfen der Masse. Nun kommt der aufwändigste Schritt in der Grillspiess-Produktion. Sämtliche Spiesse werden von Hand aufgereiht, damit die Maschine anschliessend den Holzspiess problemlos durchstecken kann. Nach dem Aufspiessen wird das Produkt dann nur noch gewürzt und
vakuumverpackt. Bei der Verpackung wird generell in Packungen für den Privathaushalt und Packungen für die Gastronomie unterschieden. Als Abschluss des Rundgangs wurde für uns noch zwei verschiedene Produkte angebraten und zum Probieren bereitgestellt, sehr lecker.
Aktuell ist die Produktion von Planted im Kemptthal noch die einzige. Schon sehr bald soll aber eine weitere und deutlich grössere Produktion entstehen. Diese wird allerdings wohl aus Kostengründen nicht mehr in der Schweiz stehen. Bedenkt man doch, dass die Schweiz hohe Löhne zahlt und die Gelberbsen auch importiert werden müssen, ist eine Produktion beispielsweise in Frankreich doch sehr viel sinnvoller.
Leider konnten wir die Produktion nicht unter voller Auslastung beobachten. Umso spannender war es jedoch zu sehen, dass auch in einer etwas grösseren Firma in der Schweiz noch Handarbeit gemacht wird. Mit diesen Eindrücken kann man dann auch den Preisdruck verstehen mit welchem Planted zu kämpfen hat. Da sie sich als Fleischersatz sehen, gilt es sich auch an den Fleischpreisen der Schweiz zu orientieren.
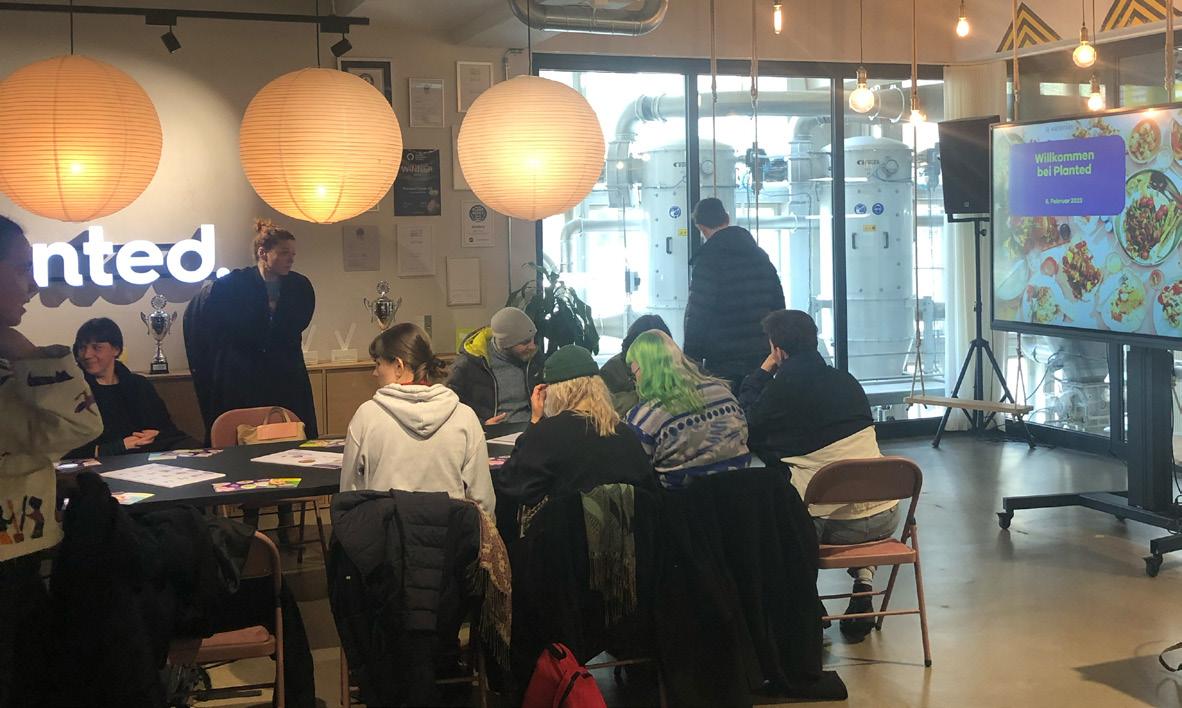
Der Besuch bei Planted war für mich sehr aufschlussreich. Bei Fleischersatz stellen sich mir oft Fragen wie: Was ist der Grundstoff? Wieso so wenig Produkte? Herkunft der Zutaten?
All diese Fragen und viele weitere konnten mir super beantwortet werden und ich kann nun auch viel besser beurteilen, welche Produkte sinnvoll zu kaufen sind und welche weniger.
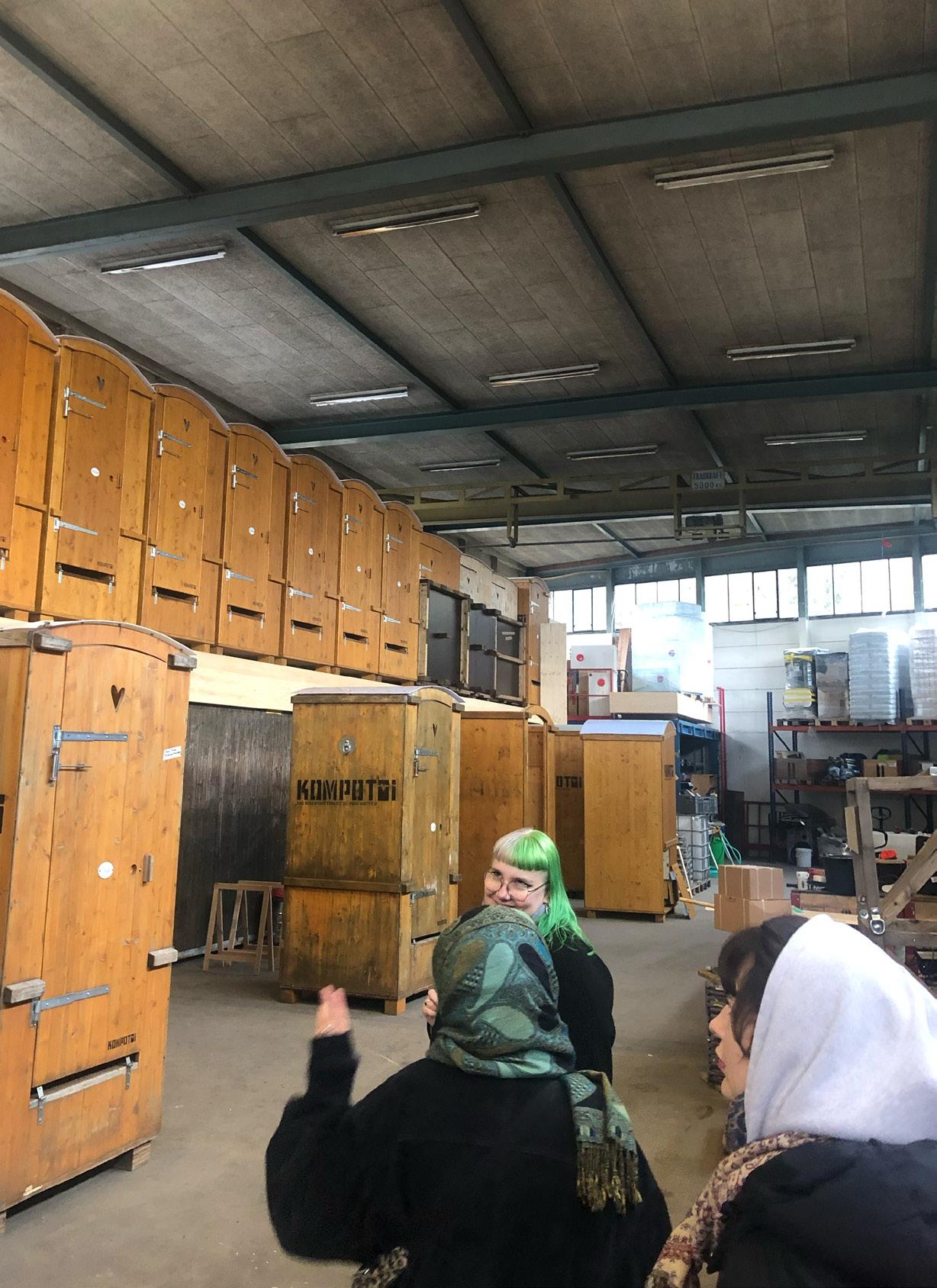
Das nächste Ziel unsere Reise war die Firma Kompotoi. Nach einem kurzen Spaziergang durch Winterthur konnte man die Toiletten vor dem Lager schon erblicken. Beginns hatte ich nicht so recht eine Idee, wie wir bei einem WC Hersteller etwas über Nachhaltigkeit lernen sollen, jedoch waren wir alle ziemlich überrascht, was alles dahinter steckt.
Geschichte
Begonnen hat alles im Jahre 2008 als Jojo (Co Gründer) für ein Projekt in Indien, im Rahmen einer Weiterbildung zum Thema Permakultur, Löcher in die Erde graben musste. Es begeisterte ihn, wie einfach aus menschlichen Ausscheidungen gute und wertvolle Erde hergestellt werden kann. Mit diesem Hintergedanken entstand 2012 dann die erste Kompotoi Toilette. Zusammen mit seinen Freunden bauten sie einen Prototyp. Das Ziel ist ein Ersatz von den herkömmlichen Plastik-Chemie-Toiletten. Das Produkt kommt bei den Leuten sehr gut an und so gründen sie den Verein Kompotoi. Es folgen weitere Prototypen, diese sollten möglichst einfach aufbaubar sein und platzsparend verstaut werden. Anfangs gibt es Schwierigkeiten was Stabilität angeht, die Toiletten stehen meistens an Events, so ist die Anzahl der Nutzer/innen sehr hoch. 2014 bauen sie die erste Kleinserie von 35 Stück. Die Anfrage steigt und das ikonische Holz WC gewinnt an Anerkennung. 2016 entschieden sie sich, das Team von einem Verein zu einer AG zu wechseln, ein grosser Sprung, doch die Bemühungen lohnen sich. Die Firma wird immer beliebter und installiert erstmals in Basel öffentliche Trocken-WCs. Durch das Vermieten der Kompotois können sie nun regelmässig Gewinn erzeugen.
2018 sind es schon 150 Kompotois, 20 Pissoirs und eine erste Serie von 10 barrierefreien Toiletten. Die Zürcher Firma arbeitet mit Partnern in der ganzen Schweiz, die Idee dahinter ist, dass die Lieferwege gekürzt werden und so auch die Abgase vom Transport. Aufgrund der Pandemie 2020 herrscht Stress, denn es werden 400 Festivals gestrichen, welche Kompotoi WCs genutzt hätten. Durch diesen Vorfall versuchen sie sich mehr auf die Vermietung zu konzentrieren und verwenden so die Trocken-WCs im Bereich Tourismus. Heute besitzt die Firma über 400 Kompotois und ist dran, die Produkte weiterzuentwickeln. Mit einem Team von 12 Leuten sind Sie daran, unsere Gewohnheiten in der Toilette zu revolutionieren.
Wie funktioniert Kompotoi
Bei einem Spülgang in einem normalen WC spülen wir ca. 9L Trinkwasser, aufgerechnet auf ein Jahr kommt man bei einem Haushalt von 4 Leuten

auf knapp 66‘000 L Trinkwasser. Auch wenn das Wasser in die Kläranlage gespült und gereinigt wird, ist das eine riesige Menge an Wasser, welches verloren geht. Bei Kompotoi hingegen spült man mit Holzspänen. Die Schicht Holz saugt die Feuchtigkeit der Ausscheidung auf und so trocknet die oberste Fläche. Aufgrund dieser Reaktion kommt es nicht zum Stinken. Ein weiteres Beispiel sind Kuhfladen, diese stinken auch nicht so stark, wenn man jedoch auf einen drauf Tritt und die getrocknete Oberfläche gebrochen wird, fangt es an zu stinken. Unter dem Sitzdeckel gibt es einen Tank, der für ca. 500 Stuhlgänge reicht. Diesen muss man je nach Nutzung immer wieder leeren. So bietet Kompotoi auch die Zusatzleistung, die WCs zu reinigen und leeren. Die gesammelten Reststoffe werden in stabile Humuserde umgewandelt. Dabei wird eine kombinierte Verfahrenstechnik von Fermentation und Kompostierung angewendet. Der gesammelte Urin vom Pissoir wird mit einem Nitrifikationsreaktor, welcher Stickstoff im Urin stabilisiert, in Dünger umgewandelt. Das Ziel wäre auch, dass die herkömmlichen WCs bei uns zu Hause getrennt werden und in der Kläranlage zu Rohstoff umgewandelt. Man ist auch an Forschungen dran, mit unseren Ausscheidungen Energie zu erzeugen, es ist nur noch eine Frage der Zeit, bis es verbreitet wird.
Was konnte ich vom Besuch mitnehmen?
Jojo war sehr gut gelaunt und hat uns auch alles erklärt. Ich fand es spannend wie transparent alles war, er zeigte uns sogar die momentanen Prototypen und was die nächsten Schritte der Firma sein werden. Man hat schnell gemerkt, wie begeistert er von den Kompotois ist und auch wie viel Wissen und Mühe dahinter steckt. Die Gründer haben aus Spass angefangen und haben sich langsam aufgebaut. Durch Zusammenarbeit mit anderen konnten sie das erreichen, was sie nun sind. Es zeigte mir auch, dass man nicht studiert haben muss, um Designer/in zu sein, jeder und jede kann etwas neues Kreieren un einen Einfluss auf unsere Gesellschaft/ Umwelt zu haben.
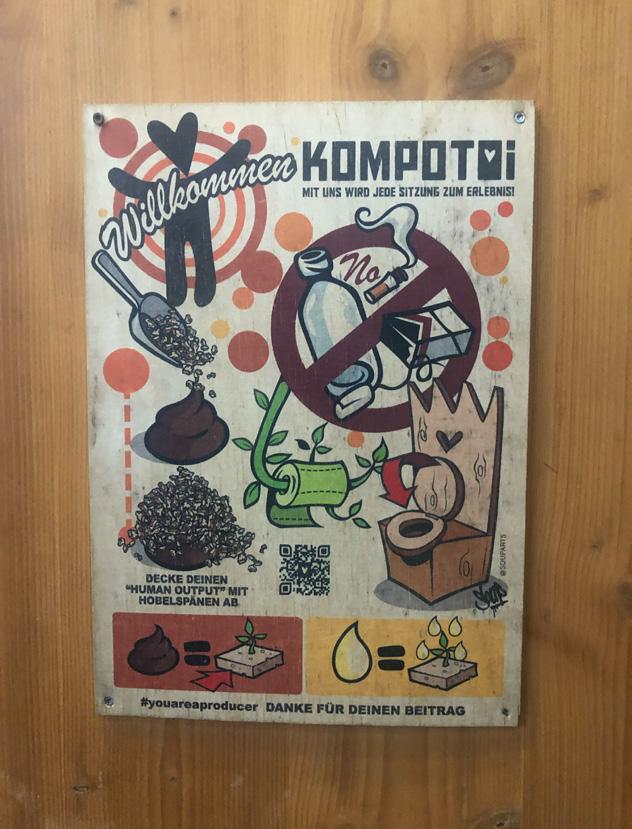
Ich fand auch spannend, dass Sie etwas umändern wollen, das seit Jahrzehnten immer gleich geblieben ist und wir im Allgemeinen unsere Gewohnheiten ändern müssen, um eine erfolgreiche Zukunft zu haben. Diese Ansicht hat mich persönlich sehr motiviert und ins Denken gebracht, was wir Menschen alles machen nur aus Gewohnheit. Uns ist nicht immer bewusst, was wir durch unsere Aktionen ausrichten, weil wir die Resultate gar nicht sehen oder spüren. Doch ich glaube fest daran, dass in der Zukunft mehr Leute sich der Umwelt anpassen und bewusster mit Ressourcen umgehen. Falls nicht, wäre das ziemlich Scheisse.


Im Jahr 1993 suchten Bruder Markus und Daniel Freitag nach einer stabilen, schützenden, widerstandsfähigen und Wasser robusten Tragetasche. Da sie in der Region keine finden konnten, entschieden sie sich eine selber zu gestalten aus dem PVC der LKW-Planen.
Nach mittlerweile 30 Jahren werden etwa 400ʼ000 Taschen im Jahr produziert.
Im ersten Schritt werden LKW-Planen mit den aussergewöhnlichsten und begehrtesten Muster und Farben durch die sogenannten «Truckspotter aufgefunden. Die Rohstoffe entstehen aus Planen von Lastwagen, welche fünf bis acht Jahre im Gebrauch waren. Diese werden aufgefasst, abgekauft und kommen in die Fabrik, um dort weiterverarbeitet zu werden. Pro Jahr sind es etwa 350 Tonnen Planen von etwa 700 bis 800 Zulieferern oder Speditionen. In der Fabrik werden die Planen auf einen Zerlegplatz gebracht und dort die verschiedene Zusätze wie Ösen, Riemen, Gurte und Reflektoren von Hand entfernt. Die Planen werden dann auf 2,5 Meter zugeschnitten, gefaltet und ins Lager geschickt. Im Lager landen die Planen im nächsten Schritt in der Wäscherei, um in riesigen Waschmaschinen gewaschen und am Schluss getrocknet zu werden.
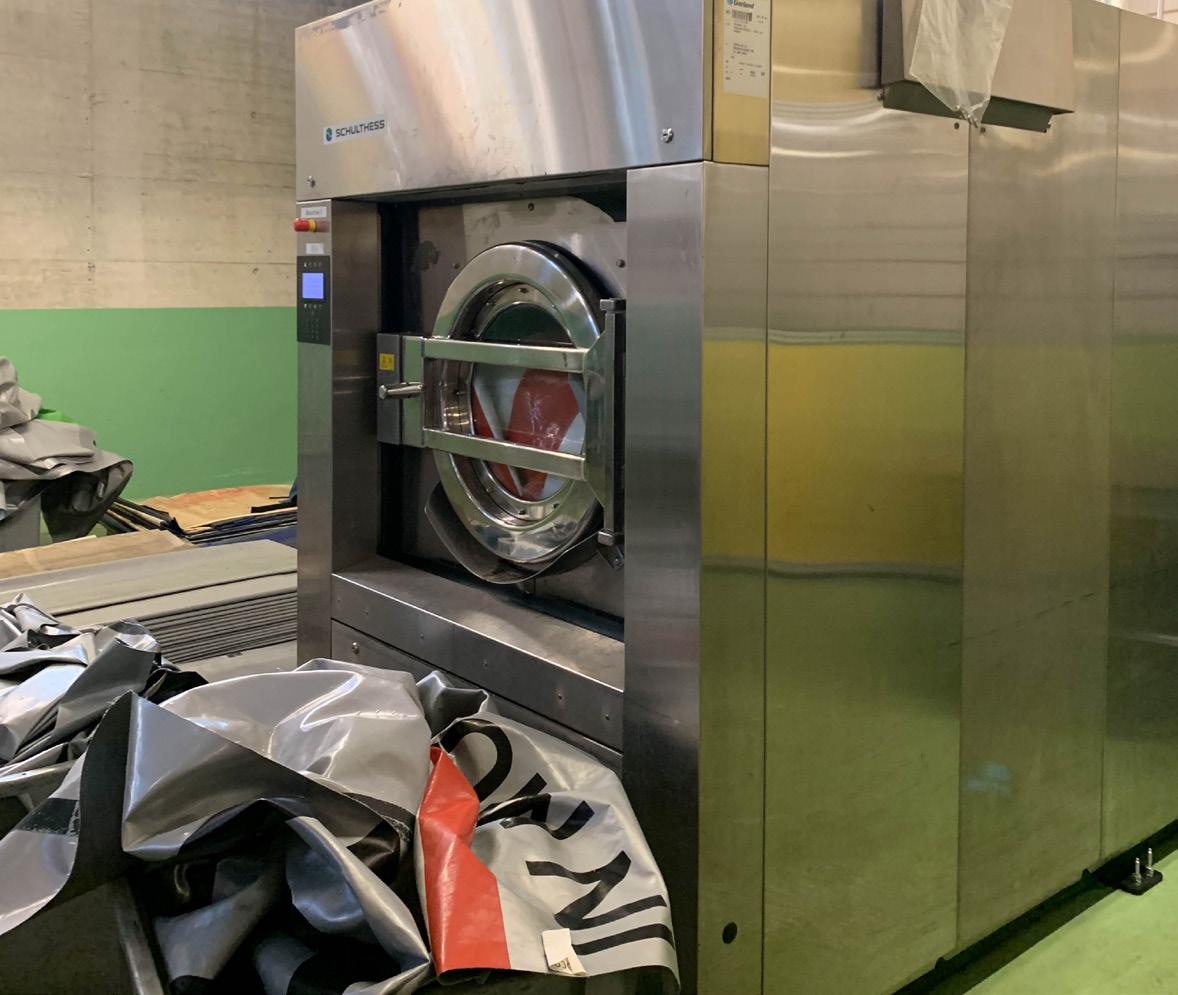
Die gewaschenen Planen werden zugeschnitten und abfotografiert. Sie werden im Protokoll aufgenommen und nach Muster und Farbe sortiert. Im Lager gibt es einen Vorrat an Planen für weitere drei Monate. Jede Plane ist ein Unikat und muss ungefähr die gleiche Qualität aufweisen.
Aus der Plane werden einzelne Planenstücke mithilfe von Schablonen von Hand oder auf dem Plotter zugeschnitten. Dabei wird auf die verschiedene Farbmixe und die Anteile der schönsten Motive geachtet. Somit wird das Material bestmöglich genutzt. Die Planenstücke werden gestapelt, nummeriert und in die Näherei übergeben. Das Restmaterial kommt in die Stanzerei, in der die kleineren Reststücke für die Accessoires eingeteilt werden. Das, was übrig bleibt, wird wenn möglich recycelt oder verbrannt.
Die dicken Planen werden nach Portugal, Tschechien, Bulgarien, Rumänien und innerhald der Schweiz versandt und in den Nähereien sorgfältig genäht und zu Taschen verarbeitet. Wenn die Taschen zurückkehren und die Qualitätskontrolle bestanden haben, werden sie zum Wareneingang übergeben. Hier wird das Sortiment für die Läden ausgesucht und für den Verkauf vorbereitet.
Für den Onlineshop wird jede einzelne Tasche mit den 360° Kameras von verschiedenen Seiten abfotografiert, um den Kunden auf der Website einen guten Überblick zu gewährleisten.
In der Repairstation gibt es die Möglichkeit, Taschen zu reparieren. Dabei sollen die Produkte wieder funktionieren und nicht wie neu aussehen. Denn die Spuren des Gebrauchs und des Alterns sind Markenzeichen der Firma


FREITAG. Es werden Reisseverschlüsse gewechselt, Löcher in der Plane geflickt und Risse zusammengenäht. Der Reparaturservice ist zum einen wichtig für die Langlebigkeit und Nachhaltigkeit des Materials, zum anderen wird das Design in der Produktentwicklung angepasst und verbessert. Weil von Fehlern gelernt wird, kann somit das Design der Taschen möglichst optimiert werden und die Gestaltungsfragen bekommen einen anderen Sinn.
In der FREITAG Fabrik gibt es ein Schaulager, das Produktentwicklungsarchiv. Es dient zur Aufbewahrung der ehemaligen Designs und die Produktdesigner können sich im Archiv von existierenden Designideen der Taschen oder Accessoires inspirieren lassen.
FREITAG setzt sich immer mehr mit Nachhaltigkeit auseinander. Die Lastwagenplanen bestehen aus PVC, welcher als Material nicht recycelbar ist. Jedoch kann ein geschlossenes Materialkreislaufsystem entstehen, in dem die Taschen trotzdem in einem Kreislauf erhalten werden können. Wie zum Beispiel mit der Circle Economie Technik. Hier werden Projekte zur Kreislaufwirtschaft gebracht. Anders genannt: Circularity. Im Technical Circle gibt es vier Möglichkeiten, eine Tasche lang am Leben zu erhalten. Share dient dazu, die verschiedenen Taschen zu teilen, beziehungsweise die eigene Tasche mit jemensch auszutauschen. Im Bereich Access ist es möglich, sich eine FREITAG Tasche auszuleihen. Dann gibt es, wie schon erwähnt, die Repairstation, bei der die Taschen wieder geflickt werden. Im letzten Schritt können die Taschen upcycelt oder recycelt werden. Denn die Taschen sollen nach dem Gebrauch zum technischen Kreislauf hinzugefügt werden.
Nicht nur das Design von Produkten und die Wahl der Materialien, auch das Ende des Produktlebenszyklus wird schon am Anfang der Produktentwicklung mitberücksichtigt. Da die Planen abgekauft werden, sind sie somit kein Abfallprodukt und bestehen aus sich lang erhaltenem Material und können über viele Jahre benutzt werden.
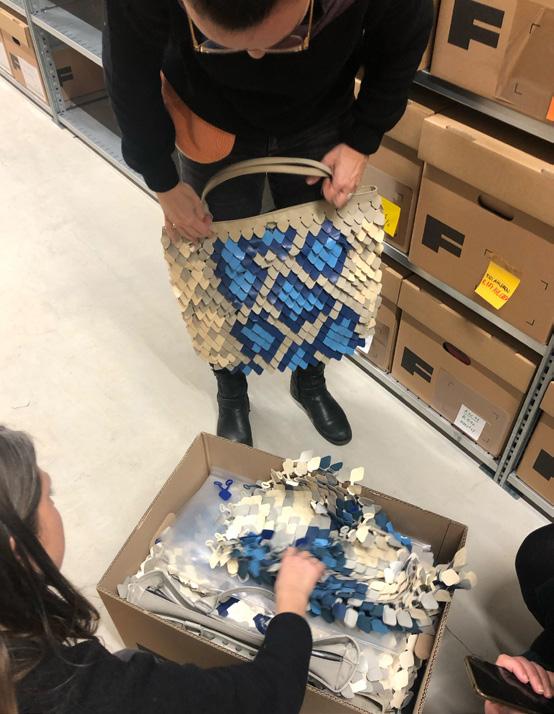
«We create products with their end in mind»
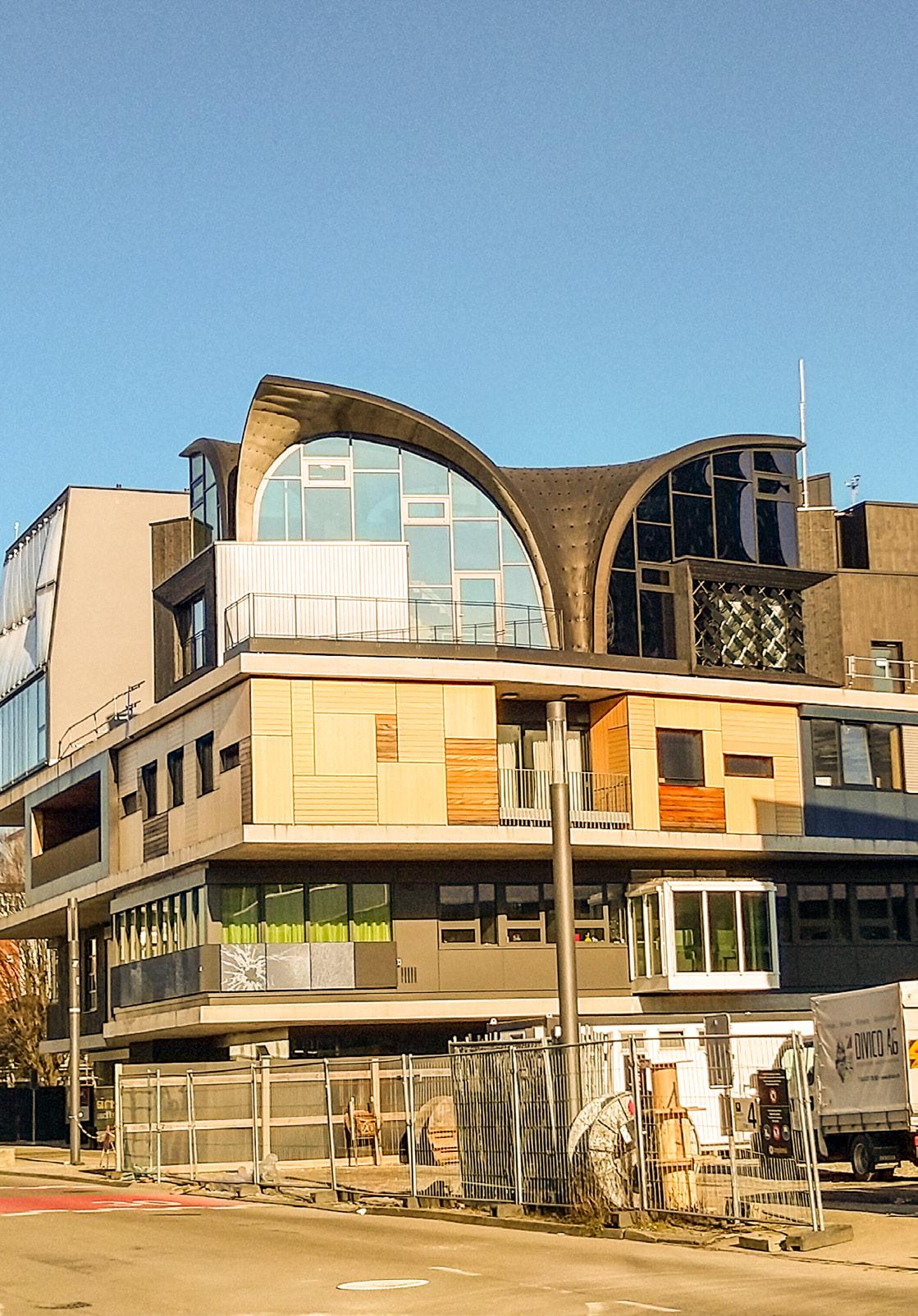
Gebäudekonzept
Das NEST (Next Evolution in Sustainable Building Technologies) besteht aus einem Turm, Backbone genannt, und drei Plattformen, auf denen einzelne Units ein- und wieder ausgebaut werden können. Jedes Unit ist eigenständig, hat andere Verwendungs- und Forschungszwecke und wird an die Haustechnik des Backbone angeschlossen. Es ist ein «reales Gebäude mit einer realen Nutzung», in dem Menschen arbeiten, Menschen wohnen, forschen – und selbst immer auch Forschungsobjekt sind und Feedback geben sollen zum Bau.
Die Konzeption, Forschung und der Bau entsteht immer in Zusammenarbeit zwischen der Empa, Forschungsinstitutionen, sowie Partner:innen aus der Wirtschaft. Und trotzdem: Hier dürfen, ja sollen Fehler gemacht werden, um die Forschung weiterzutreiben.
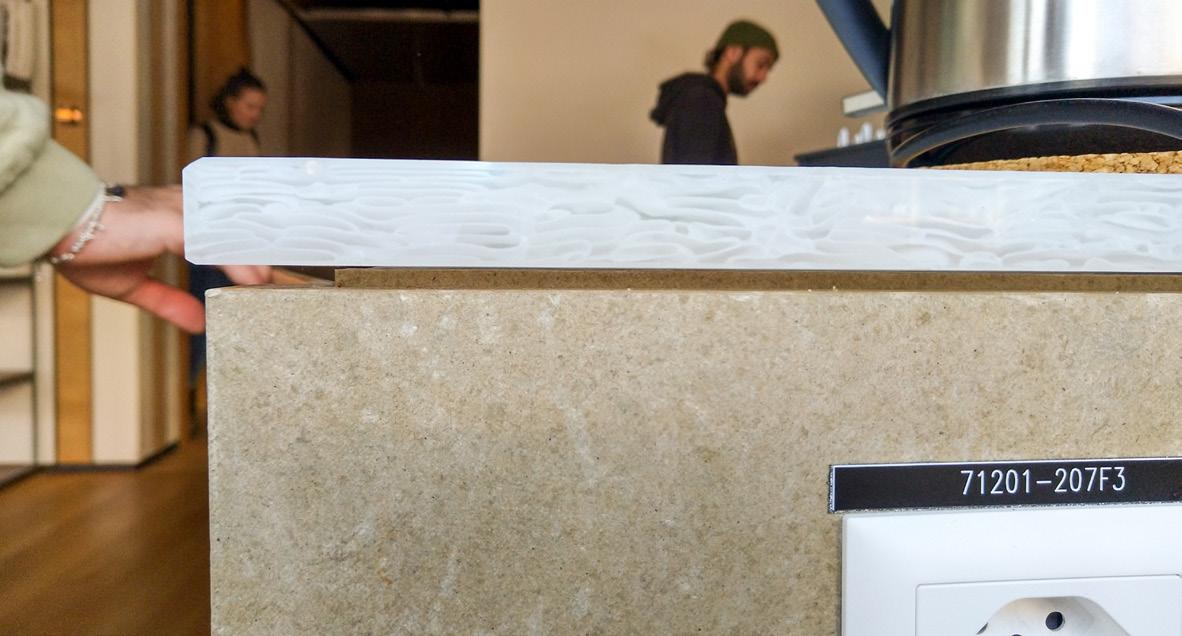
Was an überschüssiger Energie anfällt, wird gleich an MOVE, eine weitere Forschungsstätte der Empa, weitergeleitet, die sich mit nachhaltiger Mobilität befasst.
UMAR – Urban Mining & Recycling
In diesem Unit dreht sich alles darum, wie schon einmal gebrauchte Materialien neuen Verwendungszwecken zugeführt werden können und Materialien temporär einem Kreislauf entnommen und diesem später wieder sortenrein zugeführt werden können. Ein weiterer Schwerpunkt ist die maximale Modularisierung und Vorfertigung, auf Klebeverbingungen und Beschichtungen wird gänzlich verzichtet, um alles reparierbar und z.B. Holz biologisch abbaubar zu halten.
Die Grundstruktur besteht aus Holz und sieht ganz gewöhnlich aus; viele Elemente sehen aber auch ungewohnt aus, weil sie zum Beispiel aus Altglas gewonnen wurden, das bei geringerer Hitze, und somit weniger Energieverbrauch, eingeschmolzen wurden (siehe Abbildung der Küchenplatte).
Die Wohnung ist für zwei Personen ausgelegt und wird von Studierenden und Forschenden bewohnt und ausgiebig getestet.
Forschungs- und Innovationsunit HiLo
Die zweistöckige Konstruktion ist inspiriert von historischer Baukunst und modernsten, digitale Technologien. Mittels wiederverwendbarer Schalungselemente aus Kabelnetzen und Membranen wurde eine selbsttragendes, mehrlagiges und somit auch gut isolierendes Gewölbe aus Beton und Glasfaser konstruiert. Die Bodenelemente weisen eine gerippte Struktur auf und es wird dadurch 70% weniger Material verbraucht. Aussen an den Fenstern sind bewegliche, sich automatisch dem Sonnenstand ausrichtende Solarpanelen angebracht, die gleichzeitig Strom liefern und Schatten spenden. Durch die gewölbten Formen sind akustische Probleme aufgetreten, die aber mit relativ einfachen Wand- und Deckenelementen aus recyceltem PET behoben werden konnten.
Water Hub
Im Water Hub, das im Keller des NEST angesiedelt ist, wird an drei Bereichen der Wassernutzung auf Haus- sowie auch Quartierebene geforscht:
Im ganzen NEST sind Trenntoiletten verbaut, die den Urin separat abführen. Dieser wird stabilisiert und mittels Aktivkohle gereinigt und ist danach
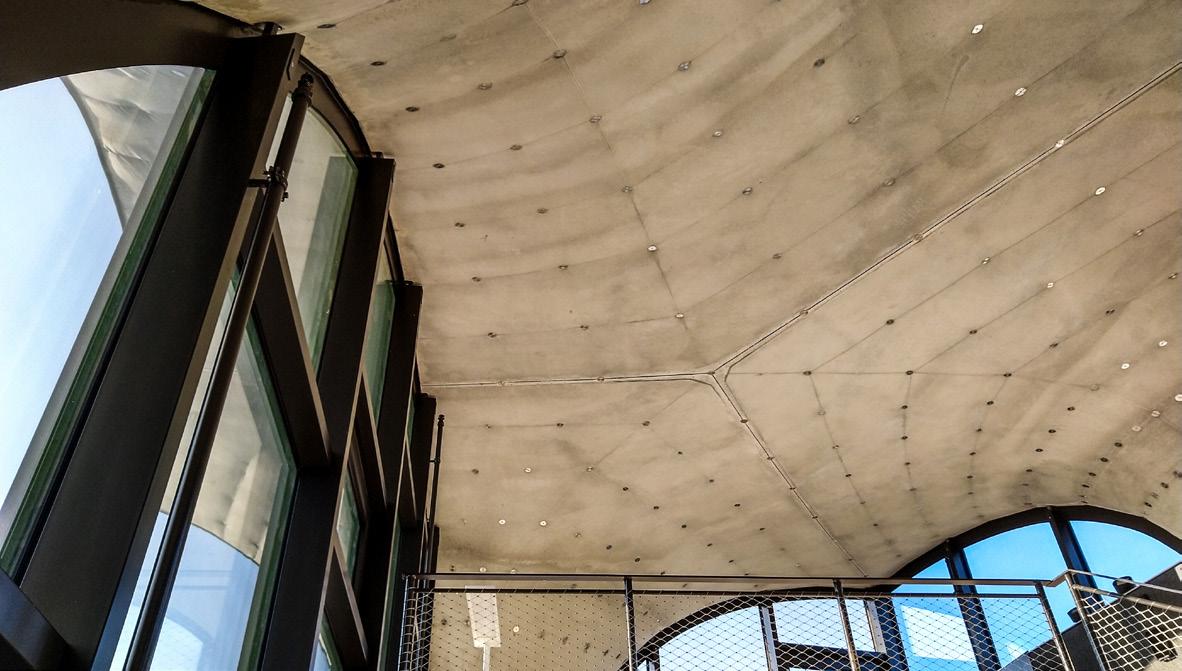
absolut schadstofffrei. Danach wird es eingedampft zu Konzentrat und seit 2015 als zugelassenes Düngemittel verkauft. Somit bleibt ein sehr wertvoller, aber weitestgehend verpönter Rohstoff in der Region und muss nicht künstlich hergestellt werden. Leicht verschmutztes Wasser aus Dusche und Waschbecken wird als Grauwasser bezeichnet und ebenfalls im Water Hub aufbereitet. Nach einer Filterung und biologisch/chemischer Nachbehandlung, wird es wieder zur Bewässerung, zum Reinigen und Waschen verwendet und spart somit etwa 50% Frischwasser im ganzen Gebäude ein. Als letztes wird das Schwarzwasser so aufbereitet beziehungsweise der Fäkalschlamm so getrocknet, dass daraus Pellets zur Energiegewinnung gepresst werden. Dieses Projekt ist noch nicht zertifiziert und es wird momentan noch viel Forschung dazu betrieben.
Fazit
Die Studienreise war sehr spannend, da wir Einblicke in ganz viele verschiedene Betriebe und Projekte erhalten haben, die sich alle stark mit Nachhaltigkeit beschäftigen. Dabei war es doch erstaunlich, wie vielfältig und komplex dieses Thema ist und wie verschiedene Positionen eingenommen werden können und werden. Bei einzelnen Positionen wäre ich gerne länger eingetaucht, was aber leider aufgrund der sehr straffen Planung nicht möglich war. Dafür ist es nicht nur aus ökologischer und ökonomischer Sicht ein grosser Vorteil, dass wir in der Schweiz geblieben sind, da wir somit theoretisch immer die Möglichkeit haben, anzurufen und vorbeizugehen.
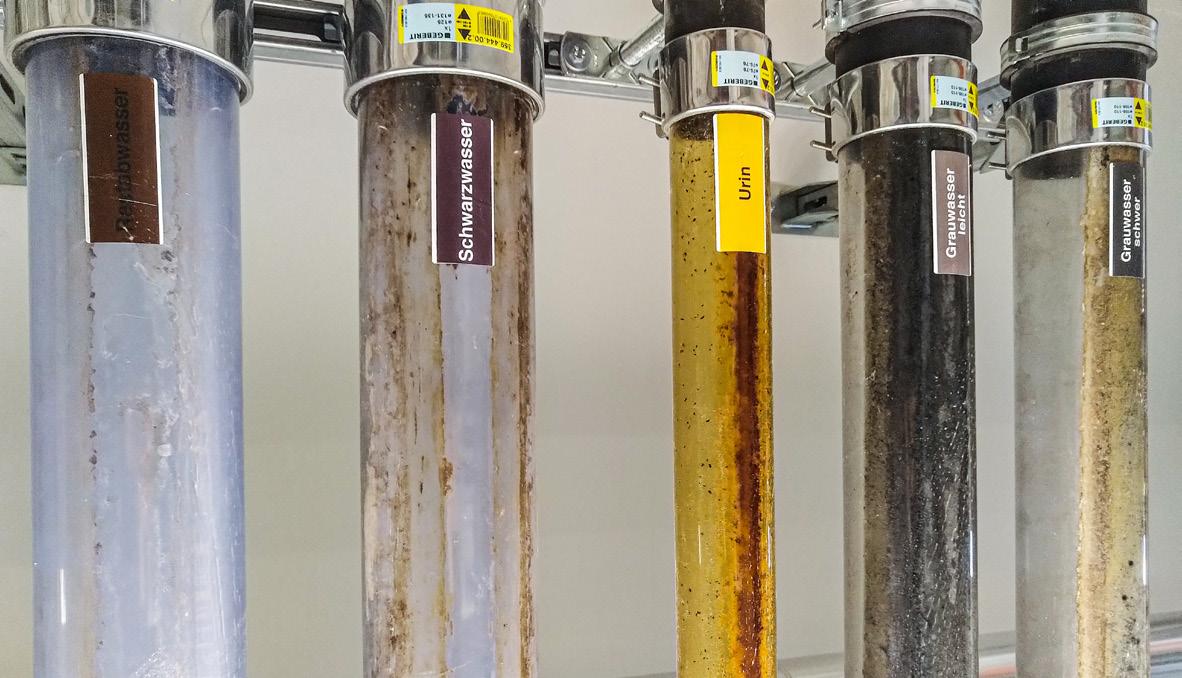

Am Dienstagabend waren wir zu Besuch bei Umami in Zürich. Wir durften an einer Führung teilnehmen und wurden im Anschluss mit einem Apéro vergnügt.
«Umami» ist japanisch und steht für delikat und lecker. Umami besteht aus einem Team von Visionär:innen und Macher:innen, die entschlossen sind zu beweisen, dass niemand Nahrung besser anbaut als die Natur. Ihre Vision ist durch das Erlernen und Verstehen der Gestaltung der Natur, ihre Prozesse replizieren und Nahrungsmittel so anbauen, wie sie sein sollen: als Teil eines komplexen Systems aus vielen Pflanzen und Tieren.
Arbeiten mit künstlichen Pestiziden, Antibiotika oder Düngemittel seien kurzsichtig und selbstzerstörerisch. Die Natur habe ihre eigene Art, ihre Bedürfnisse in einem sich selbst tragenden Gleichgewicht zu regulieren. Durch die Nutzung natürlicher Synergien und die Optimierung der Ressourcen produziert Umami reinste Lebensmittel. Sie sagen alles, was Umami umsetzt, summiert sich zu ihrer Ernte. Der Geschmack ihrer Speisen sei ihr Qualitätssiegel. Man könne es schmecken und fühlen in ihren Mikrogrünen, Kräutern, Muscheln und Saucen.
Sie verfolgen klare Ziele beim Ökosystem.
Inspiriert von der Natur
Umami sei die Heimat einer großen Vielfalt und Anzahl von Pflanzen und Tieren. Sie alle sind Teil eines komplexen Nährstoffkreislaufs - eines Ökosystems wie Wald oder Meer. Wassertiere erzeugen nährstoffreiches
Wasser, während Pflanzen es gedeihen und reinigen. Biodiversität steigert die Nährstoffqualität und Wasser wird auf natürliche Weise recycelt. Niemand könne das besser als die Natur.
Permakultur in Innenräumen
Mikrogrünes, Kräuter, Blumen, Fische, Garnelen, Muscheln, Plankton, Algen, Pilze: Mit viel Liebe gepflegt, fülle jeder Organismus eine Nische in der Nährstoffverarbeitung. Sie machen Kunstdünger, Medikamente und Giftstoffe überflüssig und unsere Nahrung rein und reichhaltig. So einfach sei das.
Städtische Landwirtschaft
Unsere Landwirtschaft sei ein Beweis dafür, dass Ökologie und Ökonomie dieselbe Sprache sprechen. Einmal verstanden, sei es nicht verwunderlich zu
hören, dass hohe Effizienz, kreisförmige Systeme, keine Chemikalien und ein guter Geschmack die Regel der Natur sind.
Örtlich
Umami baut ihre Nahrung dort an, wo sie sie brauchen und essen: in der Stadt.
Zeiteffizient
Optimale Klima- und Nährstoffbedingungen führe zu bis zu 3-mal schnelleren Erntezyklen als herkömmliche Methoden.
Raumeffizient
Durch vertikale Landwirtschaft könne Umami 9-mal mehr pro m2 anbauen als mit konventionellen Methoden.
Energieeffizient
Innovationen in den Bereichen Wasserfluss, Beleuchtung, Wärmerückgewinnung, 12V-Technologie, Solarstrom und viele mehr halte den Energiebedarf niedrig.
Kreisförmige Rohstoffe
Alle ihrer Rohstoffe seien von Bio-Qualität. Ihre Pflanzen wachsen in einem natürlichen Substrat, das sie abbauen und in Biokraftstoffe umwandeln können. Ihre Verpackungen sind biologisch abbaubar.
Keine künstlichen Zusatzstoffe
Natürliche biologische Synergien schaffen eine komplexe Nährstoffmischung, die zu einem einzigartigen Geschmackserlebnis führt. Sie fügen NIE etwas Künstliches hinzu.
Alle Jahreszeiten
Durch die Regulierung von Klima, Beleuchtung und Nährstofffluss in geschlossenen Räumen sichern sie die Versorgung ganzjährig.
Umami hat Restaurant-Partner:innen. Von renommierten Gourmetrestaurants mit Michelin-Sternen bis hin zu kleinen lokalen Cafés arbeiten sie mit Restaurants zusammen, die ihre Leidenschaft für Qualität und Nachhaltigkeit teilen. Restaurants und Cafés wie beispielsweise Igniv Bad Ragaz, Krone Regensberg, Villa Honegg, Park Hyatt, Maison Manesse etc.
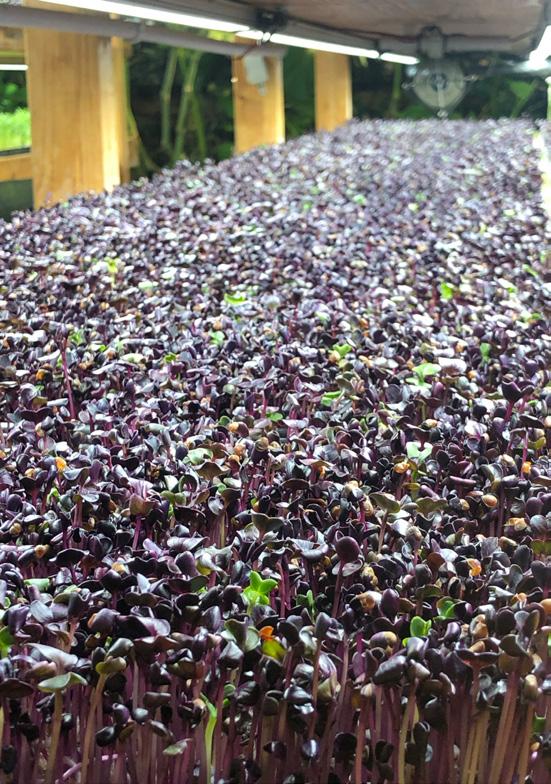

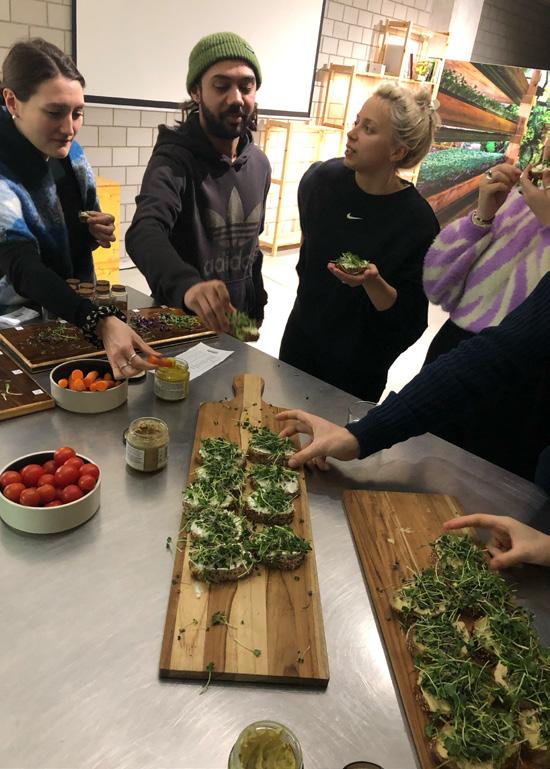
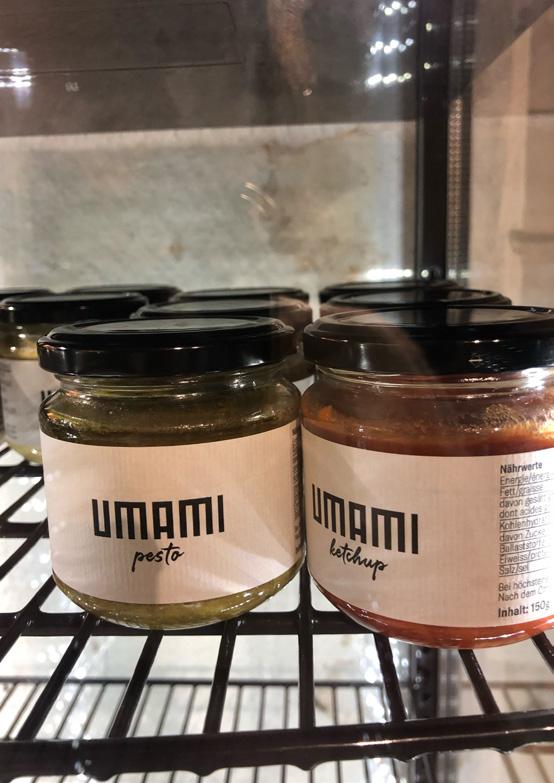
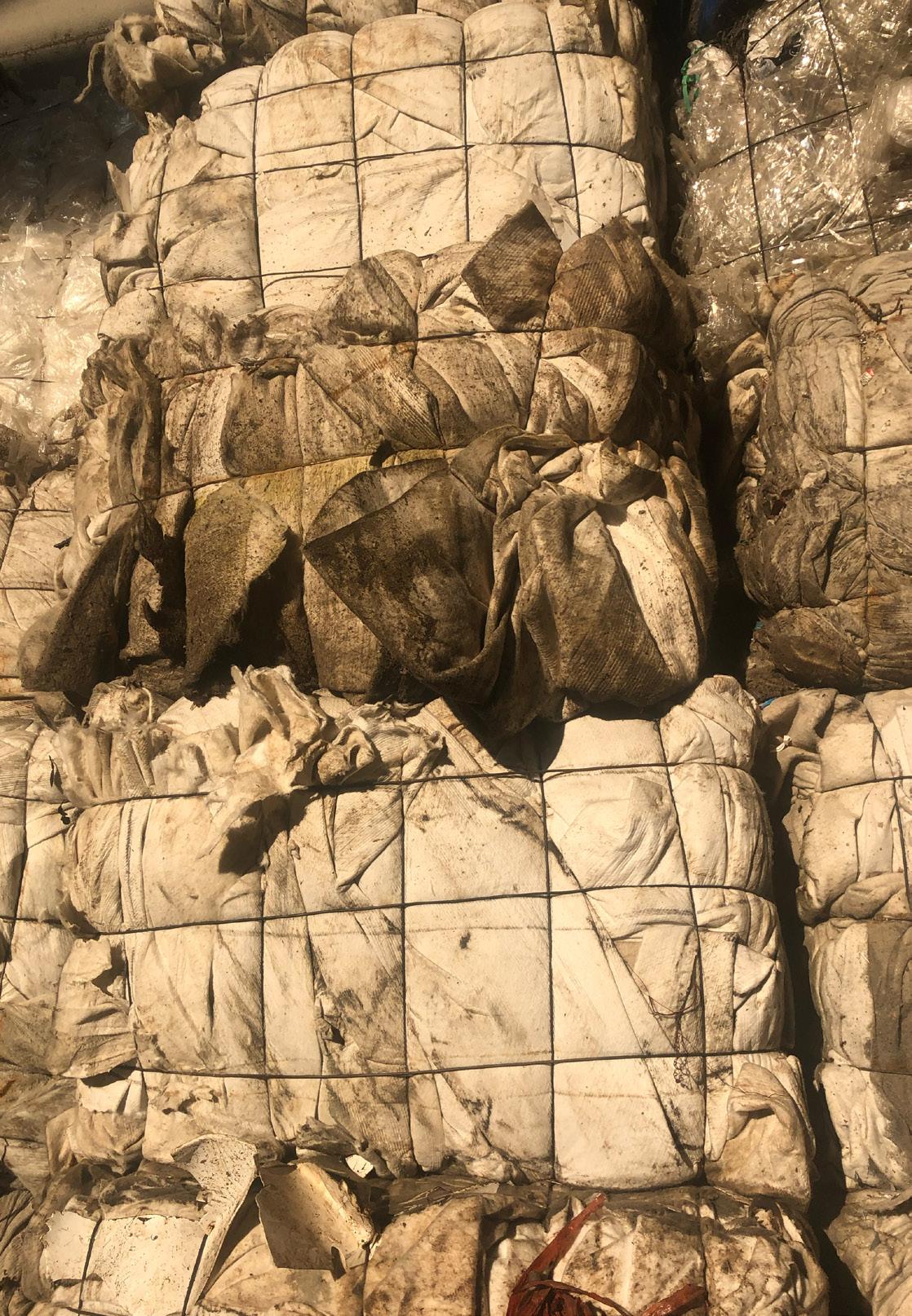
Das Rohmaterial der Kunststoffabfälle ist sehr wertvoll und deshalb ist es nicht mehr zeitgemäss diese zu deponieren oder verbrennen. Kunststoffe lassen sich mit innovativen Technologien immer wieder recyceln und die Entwicklung schreitet laufend voran. Die InnoRecycling AG hat 2020 über 39ʼ000 Tonnen Kunststoffe verwertet, anstatt zu verbrennen. Die Wiederverwertung des Kunstoffes ist umweltschonend, kann vielfach eingesetzt werden und der Kunststoff bleibt als Rohstoff im Materialkreislauf. Gerade die Herkunft und der Verbrauch von Erdöl erzeugt enorme Mengen CO2, die mit der Wiederverwertung gesenkt werden. Der Mehrwert für die Umwelt und der wirtschaftliche Nutzen bringen lokale Wertschöpfung und neue Arbeitsplätze. Das Kunststoffrecycling wird von der InnoRecyling AG gefördert und forciert. Nur noch Abfälle, die nicht mehr wiederverwertet werden können, gehören in die Kehrrichtsverbrennungsanlage.
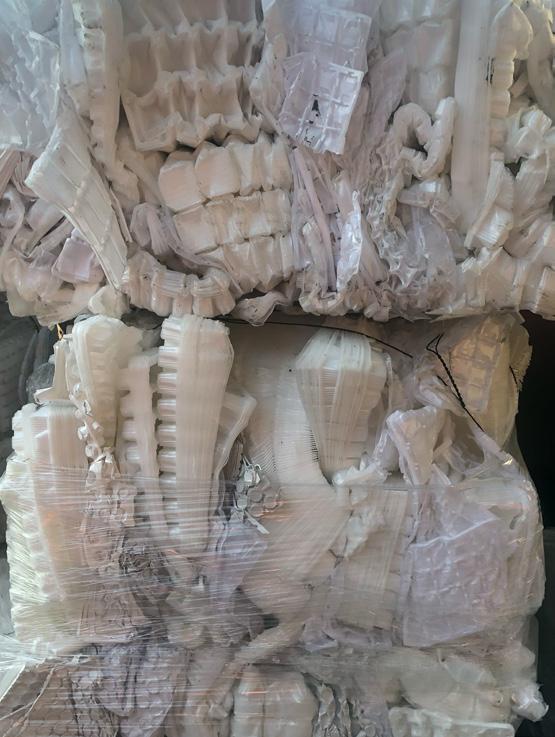
Prozess InnoRecyling
Der erste Schritt zur Rohstoffrückgewinnung ist die Entsorgung an der richtigen Stelle. Die InnoRecycling sortiert die Abfälle und presst sie zu Ballen die anschliessen gelagert werden. Es wird auch Kunststoff aus der ganzen Schweiz und Deutschland eingekauft. Das Sortieren ist im Moment noch aufwändige Handarbeit. Für die Zukunft wünscht sich InnoRecycling eine Infrarot–Sortierungsanlage. Hier trägt aber auch der Kunststoff Produzent Verantwortung, da bereits in der Herstellung die Wiederverwertung mit einbezogen werden sollte. Nach der Lagerung übernimmt die Partnerfirma InnoPlastic die Wiederverwertung.
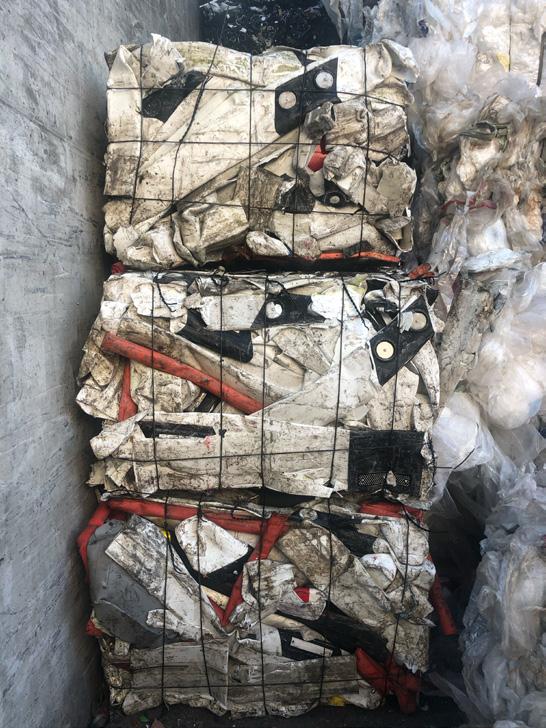
Produktionsablauf InnoPlastic
Je nach gewünschter Granulat Mischung werden die Ballen wie nach einem Rezept zerkleinert, gewaschen und in verschiedenen Anlagen getrocknet, bevor es zu neuem Regranulat extrudiert wird. Nach dem Homogenisieren und der Qualitätsprüfung wird es in Silos gelagert und anschliessend ausgeliefert.
Anwendungen von Regranulat
Aus dem Granulat entstehen verschiedene Rohre, Abfallsäcke oder Tragetaschen. Auch die Folienindustrie ist ein zukünftiger Abnehmer. Mit dem Spritzgussverfahren können Betriebe in ganz Europa das Granulat für verschiedene Produkte verwendet werden. Mit den gewünschten Materialeigenschaften entwickelt InnoPlastic eine geeignete Rezeptur für das passende Granulat. Der Materialkatalog umfasst über 120 unterschiedliche Kunststoffsorten und -qualitäten.

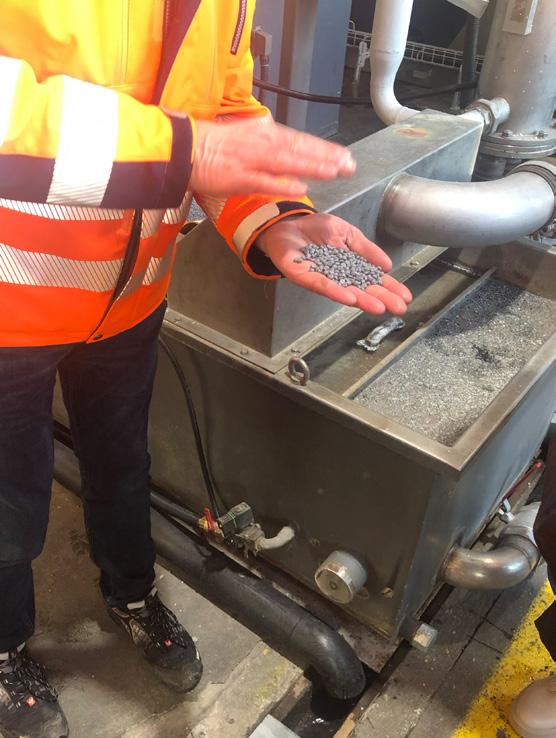
Bring Plastic Back!
Im privaten Bereich liegt die Recyclingquote für Kunststoffe in der Schweiz bei unter 20, während andere Separatsammlungen Quoten von über 80% aufweisen. Mit dem Sammelnetz und dem Motto «Bring Plastic Back» bestrebt InnoRecycling AG mit Sammelsäcken Kunststoffe nicht länger zu verbrennen. In über 460 Annahme- und Verkaufsstellen können die gefüllten Säcke zurückgebracht und dem Recycling zugeführt werden.
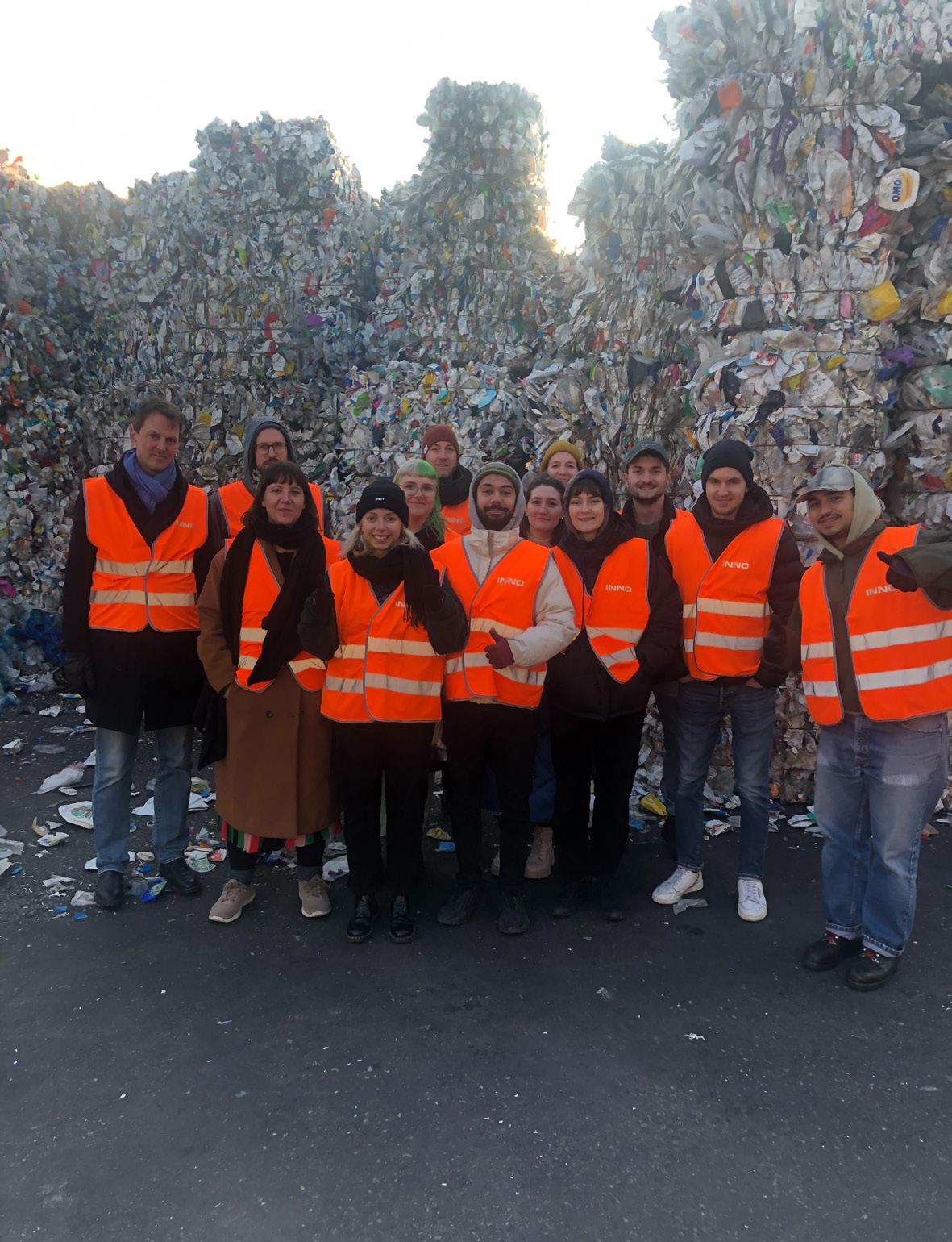
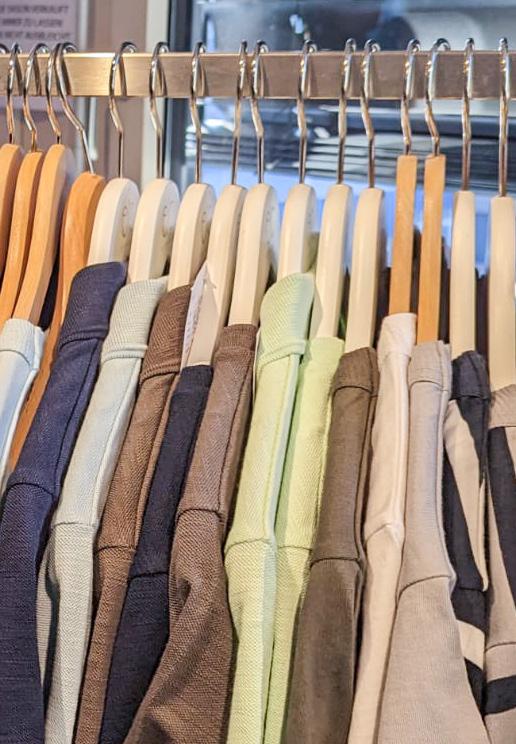
Wer ist Remei
«Wir denken Textilherstellung neu. Unique Sustainable Solutions mit All-Holder-Value».
Remei ist eine Schweizer Unternehmen, welches mit nachhaltig angebauter Bio-Baumwolle handelt. Besser gesagt mit dem Garn und dem Textil aus der Bio-Baumwolle. Sie wollen ihr Textil fair, biologisch und auch 100% transparent herstellen. Sie arbeiten direkt mit Firmen zusammen und gestalten mit ihnen Kollektionen, welche laut Remei die höchsten Nachhaltigkeitsstandards erfüllen, ohne Kompromisse bei der Qualität oder dem Design einzugehen. Sie haben sich ausserdem auf eine nachhaltige Wertschöpfungskette vom Saatgut zur Faser bis hin zum fertigen Textil spezialisiert. Sie bieten internationalen B2B-Handelspartner*innen Zugang zu einem Geschäftsmodell, das ökonomische, ökologische und menschenrechtsbasierte Anforderungen in der Textilproduktion erfüllt. Remei hat den Hauptfirmensitz in der Schweiz, in Rotkreuz. Zusätzlich haben sie noch verschiedene Sitze in Tansania und Indien. Sie beschäftigen insgesamt 5000 Kleinbauern und Kleinbäuerinnen und haben 29 industrielle Partner. Sie arbeiten mit mehr als 20 internationalen Retail-Partnern und Marken zusammen wie beispielsweise naturaline, Gerry Weber, Grüne Erde, Greenpeace etc.
Kurz etwas zur Baumwolle
Laut der WWF besteht die Hälfte aller Textilien aus Baumwolle. Die Reichweite der Baumwolle ist daher riesig, aber die Methoden der Baumwollgewinnung Grotten schlecht. Sie ist nicht nur ökologisch gesehen nicht nachhaltig. Im «Market Report 2018» wurde von Textile Exchange angegeben, dass 2016/17 von 22.000.000 Tonnen weltweit angebauter Baumwolle etwa 118.00 Tonnen Bio-Baumwolle waren, also gerade so 0,5 Prozent. Das ist gar nichts. Es ist daher umso wichtiger, dass Firmen wie Remei Bio-Baumwolle fair und ökologisch herstellen.
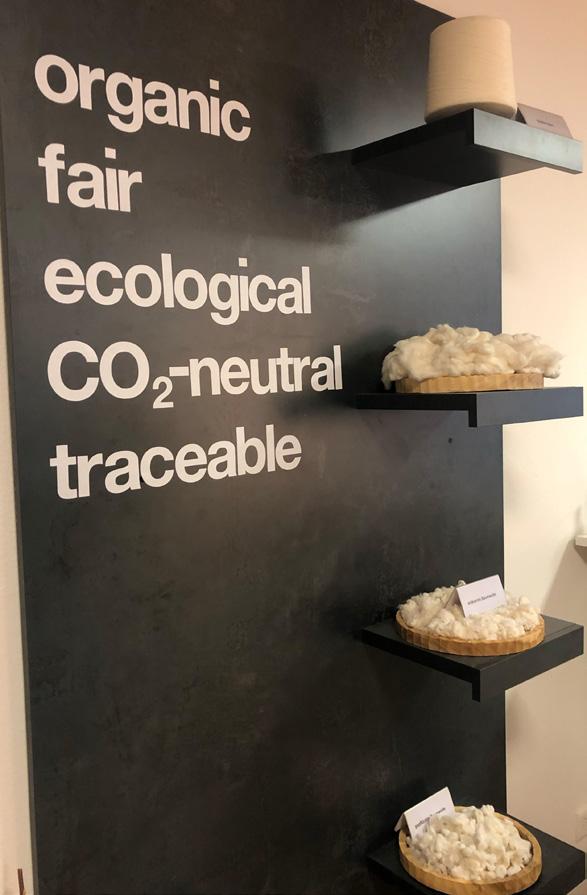
Produktionskette
Remei verkündet in ganz vielen Texten und Werbefilmen den Slogan «From Fibre to Fashion», was genau wollen sie uns damit sagen? Normalerweise wird von einem Betrieb zuerst das Produkt oder etwas vergleichbares festgelegt. Wenn dieses feststeht, wird dann ein Produktionsort gesucht. Dieser muss mit Rohstoffen beliefert werden. Die Kette ist also von der Firma zum Produktionsort zu den Rohstoffproduzent*innen. Da Remei eine fairere Gewinnung von Baumwolle anstrebte, wurde es hier genau andersrum gemacht. Die Produktionskette beginnt bei den Biolandbaubetrieben in Indien und Tansania und das ist viel früher als im Markt üblich. Remei verantwortet die gesamte Produktionskette, das heisst vom Saatgut bis hin zum fertigen Textil wird alles geprüft.
Die fertigen Stoffe werden dann mit Partnerfirmen zusammen in Kollektionen von Kleidern oder dergleichen weiterverarbeitet. Bei jedem Stück kann dann der transparente Weg des Textiles nachverfolgt werden. Das sollte laut Remei wichtig und für sie kein Problem sein, da sie Wert auf hohe Sozialstandards legen und ein strenges Chemikalienmanagement pflegen.
Zusammenarbeit mit B2B
In den oft sehr komplexen und undurchsichtigen Lieferketten der Baumwolle und der Textilien gibt es einige grosse Ungleichgewichte. Durch eine Abnahmegarantie möchte Remei einige Risiken, welche bei der Landwirtschaft anfallen könnten, mittragen. Das könnte z.B. eine Über- oder Unterproduktion sein. Sie vergüten den Rohstoff direkt beim Baumwollankauf und zahlen eine Prämie über dem Marktpreis, um somit einen faireren Handel zu schaffen. Für die Leistungen im Bio-Bereich werden den in der Landwirtschaft arbeitenden Personen eine Prämie von 15% bezahlt. Die Prämie basiert auf dem durchschnittlichen Baumwoll-Marktpreis der vergangenen 5 Jahre. Sollte sich jemensch dazu entscheiden, auf BioBaumwolle anzupflanzen (der Wechsel dauert min. 3 Jahre) wird diese Prämie, (soweit ich es verstanden habe) nicht gezahlt, aber die Baumwolle wird trotzdem gekauft und die in der Landwirtschaft arbeitende Person unterstützt.
Die Beziehungen und der Austausch der Produktionspartner*innen ist für Remei sehr wichtig, daher gibt es einige Bauer/Bäuerinnenverbände vor Ort. Die Landwirtschafts Mitarbeitenden haben Zugang zu Coachings und Schulungen und können Verbesserungsvorschläge einbringen. Aufgrund der Vorfinanzierung stellt Remei auch eine sichere Lieferkette und Verfügbarkeit des Rohstoffes für sich selbst dar. Durch diese ganzen Faktoren soll eine
nachhaltig gestaltete Zukunft für alle Beteiligten geschaffen werden. Die Sozialstandards bei der Produktion und auch beim Bedrucken und Besticken des Stoffes werden regelmässig von unabhängigen Institutionen geprüft.
My-Trace von Remei
Durch den Scan eines QR-Codes oder der Rückverfolgungsnummer auf den Kleidern kann mensch den Weg des Textils nachverfolgen. Der*die Nutzer*in kann alle einzelnen Produktionsstufen vom Saat bis zum fertigen Textile navigieren und auf individuelle Standortinformationen, Bilder und Inhalte zugreifen.
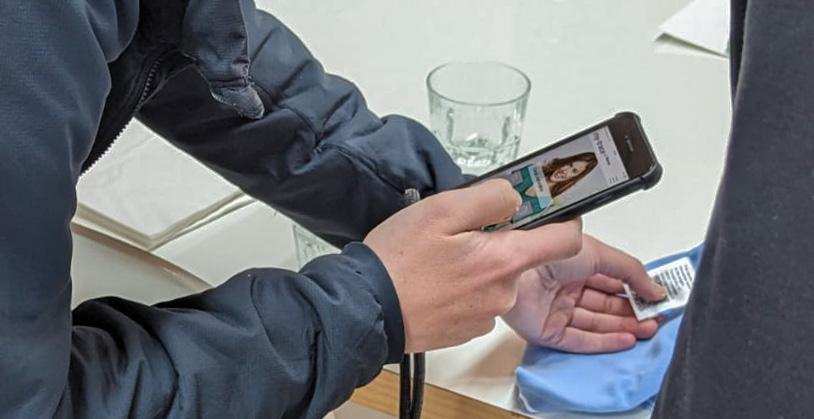
Bio-Baumwolle
Remei ist Gründer und Inhaber von Remei India Ltd. und Remei Tanzania Ltd. In Indien arbeiten etwa 3’300 und in Tansania etwa 1›800 Kleinbauern/Kleinbäuerinnen für Remei. Der Anbau entspricht der EU-Richtline 834 / 2007. Bei biologischen Baumwollanbau wird auf gentechnisch verändertes Saatgut verzichtet. Remei kontrolliert daher schon beim Saatgut, was sein darf und was nicht. Es dürfen keine chemischen oder synthetische Pestizide verwendet werden, es kommen ausschliesslich Nützlinge und natürliche Pflanzenschutzmittel zum Einsatz.
Kurze eigene Meinung
Die Produktion und der Prozess, Baumwolle in ein Textil zu verarbeiten, braucht enorm viel Wasser und andere Ressourcen. Es ist ein neues Produkt und kann deswegen gar nicht 100% nachhaltig sein. Remei verspricht durch den Kauf von neuen Maschinen und anderen Leistungen klimaneutral zu sein und die Emissionen dadurch aufzuheben. Der Schaden, welcher
durch die Produktion neu hergestellter Textilien entsteht, passiert jedoch jetzt.
Eine riesige Menge an Landwirt:innen ist auf die Abnahme der Baumwolle angewiesen. Diese haben bei Remei, im Vergleich zum Ortsbezogenen Einkommen, bessere Konditionen, jedoch verdienen sie immer noch sehr wenig. Auch wenn ich nicht nachvollziehen kann, wie und wo Geld ausgegeben wird, finde ich es wichtig, das nochmals zu erwähnen.
Ich finde gut, dass durch die Bio-Standards und die Unterstützung von Remei die Chance ergibt, Felder nachhaltiger zu betreiben, was die Umwelt wie das Grundwasser, welches zur Gesundheit vieler Arbeiter:innen beiträgt, zu verbessern. Es gibt immer noch einige bessere Lösungen wie Second Hand Kleidung oder Up- und Recycling von Stoffen und Materialien. Jedoch ist es schwer, in der kapitalistischen Gesellschaft, in der wir leben, etwas davon zu konsumieren, ohne Leid entstehen zu lassen. Unter Ansicht der aktuellen Lage finde ich es beachtenswert, was Remei macht und ein Schritt in die richtige Richtung. Ich glaube, sie haben es sich sehr zu Herzen genommen, den Handel und die Produktion der Baumwolle fairer und ökologischer zu machen. Jedoch denke ich, dass das heute noch nicht möglich ist. Wenn mensch aber ein neues Shirt kaufen will, welches aus Baumwolle ist, finde ich das Textil von Remei eine gute Lösung. Es ist schön zu sehen, dass ein transparenter Weg heute möglich ist und hoffe, dass sich immer mehr Unternehmen für einen transparenten, sozialen und ökologischen Weg wie Remei entscheiden.
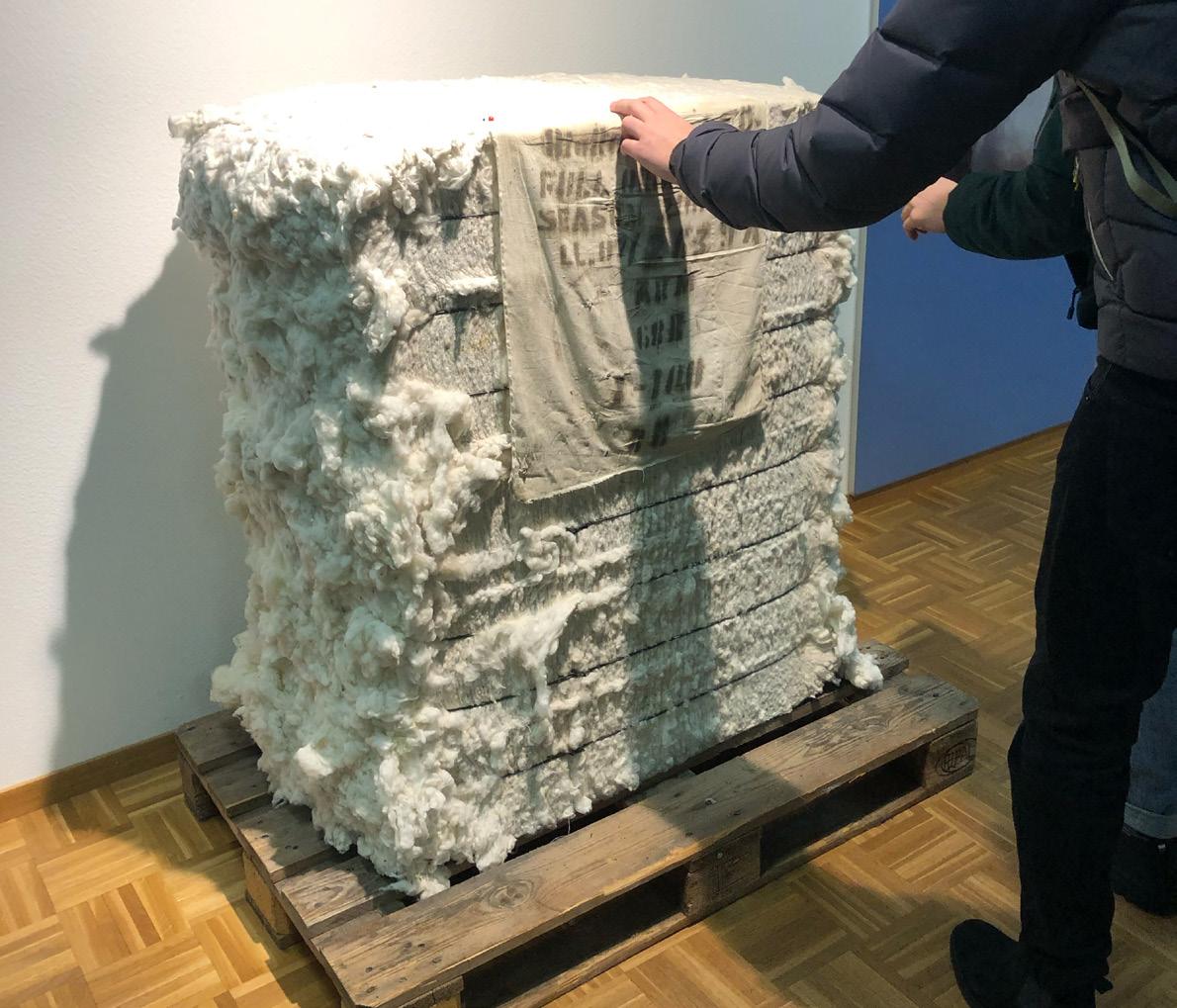
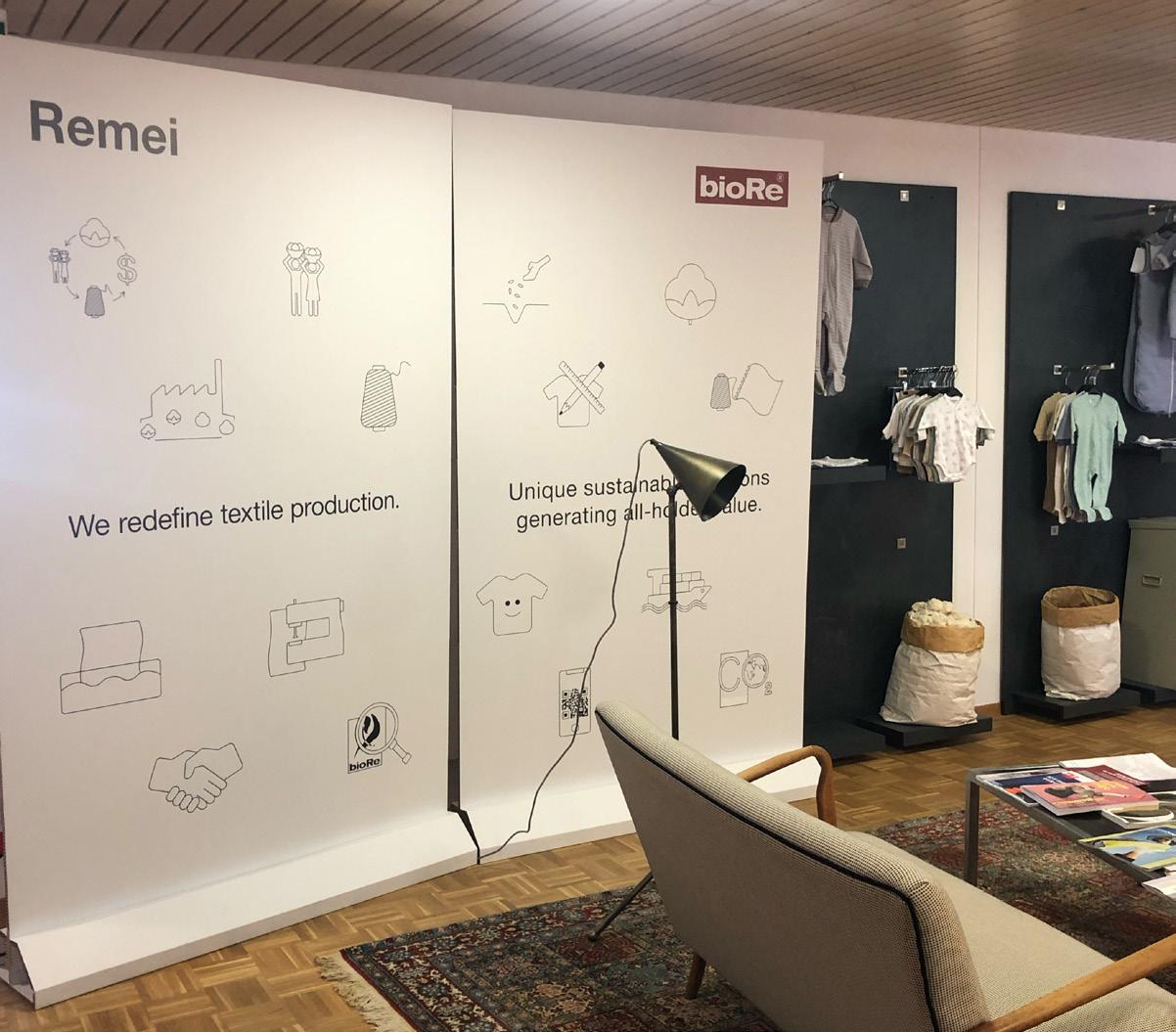
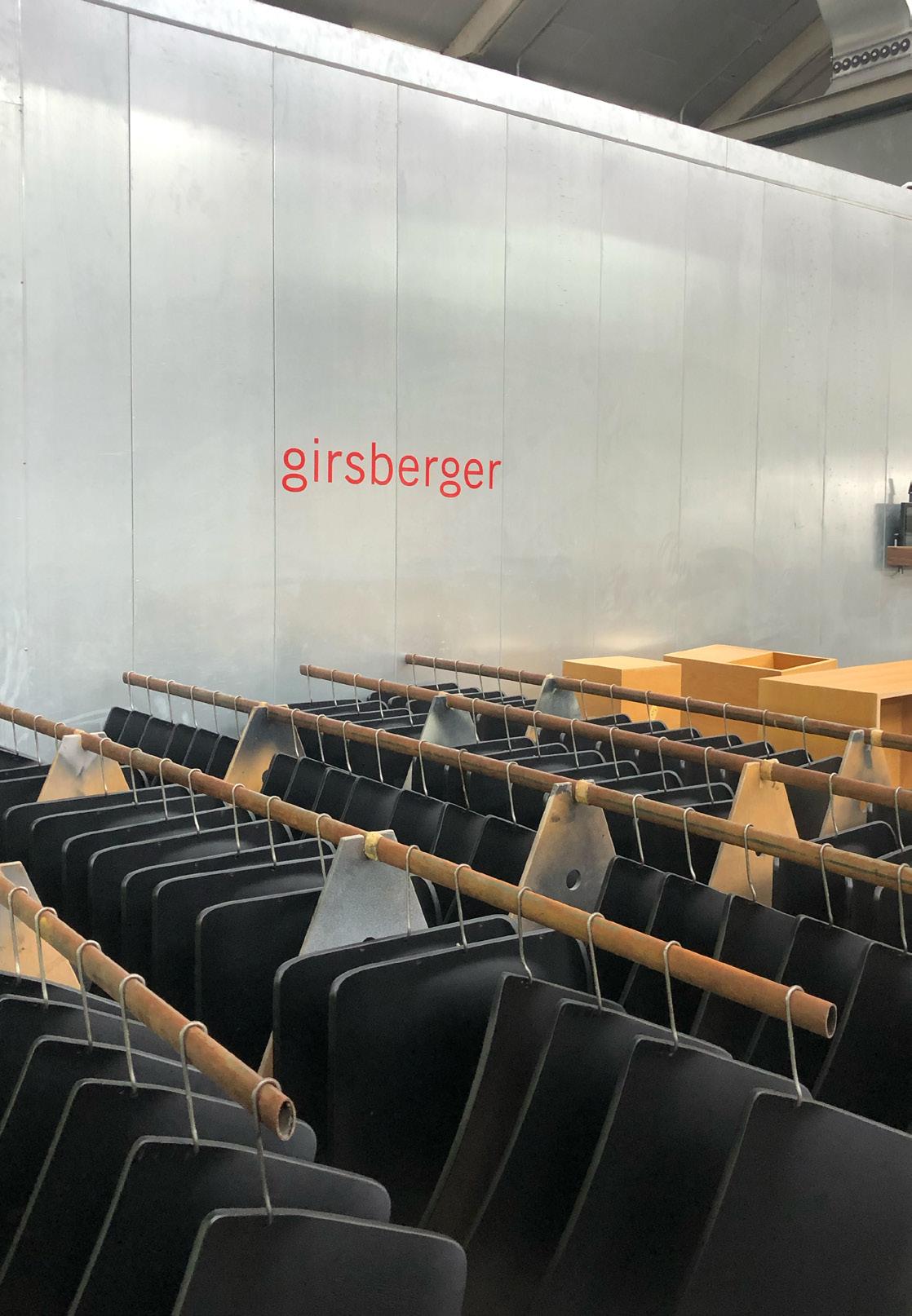
Am Freitag, dem zugleich letzten Tag der Studienreise, führte unser Weg zur Firma Girsberger im etwas abgelegenen Ort Bützberg, im Kanton Bern. Das Unternehmen zählt mit dem Gründungsjahr 1889 zu den ältesten Möbelherstellern der Schweiz und ist europaweit gut vernetzt. Worin besteht bei diesem Grossunternehmen die Nachhaltigkeitsstrategie? Auf diese Frage möchte ich im Rahmen der Studienreise 2023 genauer eingehen.
Girsberger ist bekannt für sein Office, sowie auch Home-Möbelsortiment. Hergestellt werden Bürostühle, Konferenztische, Sitzlandschaften sowie auch Esszimmertische, die hauptsächlich aus Massivholz hergestellt werden. Ein weiterer ungewöhnlicher Rohstoff erhält beim Unternehmen mindestens eben so viel Aufmerksamkeit: alte Raummöblierungen. Eingesetzt werden fürs Upcycling ausschliesslich Modelle, die in grosser Stückzahl vorhanden sind, da es für Girsberger wichtig ist, ein Gleichgewicht zwischen Wirtschaftlichkeit und Nachhaltigkeit herstellen zu können, wenn es um die Weiterverarbeitung von bereits Bestehendem geht. Das Remanufactorig macht den zweitgrössten Geschäftsbereich beim Möbelhersteller aus. Attraktiv sind dabei Möblierungen von Kirchen, Kinosälen, Schulzimmern oder auch von Konzerthallen, wie beispielsweise das KKL in Luzern.
Je nach Wunsch des Kunden wird häufiger renoviert als umfunktioniert. Quietschende Stühle in Konzertsälen wurden von Girsberger an die Akustik der Räumlichkeit angepasst. Zukünftige Musikevents können nun ohne störende Nebengeräusche stattfinden. Bei dieser Art von Arbeit spricht mensch jedoch eher von Remanufactoring, das gewisse Ähnlichkeiten mit dem Upcycling aufweist, aber auf ein anderes Ziel hinarbeitet. Aus alten Bürotischen oder Korpussen werden Sitzlandschaften für Büros oder das Eigenheim designt. Die ersten Prototypen wurden der Studienreisegruppe ebenfalls auf Fotos präsentiert.
Bei Studierenden im Objektdesign löst das eine grosse Begeisterung im Zusammenhang mit dem Begriff Nachhaltigkeit aus. Oft wirkt die Zukunft für Designer:innen im Bereich Umweltbewusstsein eher düster, da uns die Rohstoffe ausgehen. Daher ist es erfrischend, nun ein Unternehmen zu kennen, das ungeliebte ,unerwünschte, vermeintlich nicht mehr modern genug wirkende Einrichtungen gewinnbringend umgestaltet. Auch wenn viele dieser Konzepte noch nicht voll ausgereift sind, sind die Designs auf intelligente Weise den Bedürfnissen der Nutzer:innen der Gegenwart angepasst. Korpusse werden in Büroräumlichkeiten immer überflüssiger, aufgrund der voranschreitenden Digitalisierung.
Daher stellte die Firma Giersberger aus diesem Objekt, das ursprünglich nicht von Ihnen hergestellt wurde, einen Hocker mit Überzug und Schubladen her. Anhand dieses Beispiels sieht man, dass sich der Möbelhersteller selber keine Grenzen setzt. Es ist nicht mehr wichtig, wo etwas mal hingehörte oder was der Nutzen war. Aus einem Exemplar können zudem auch drei neuartige Stücke entstehen mit unterschiedlichem Einsatzgebiet. Da die Möbel dennoch aus dem gleichen Rohstoff gefertigt wurden, passen sie optisch gut zusammen. Das Leben der Möbel wird nicht nur verlängert, sondern teilweise verändert (Upcycling: aus alt mach anders).
Nach der etwa 1-stündigen Präsentation und Fragerunde mit Kaffee und Gipfeli folgte eine Führung durch die hauseigene Schreinerei mit Massivholzlager, den Remanufactoring Bereich, sowie auch die Upcycling Werkstatt des Firmenhauptsitzes.

Girsberger hat sich seit dem Bestehen des Betriebs auf die Herstellung von Esstischen aus Massivholz spezialisiert. Dessen Beschaffung erfolgt maximal 600 km ausserhalb der Produktionsstandorte in Ruma, Serbien. Der serbische Standort ist für die Holzverarbeitung verantwortlich, während die Eigenbeschaffung durch den gelernten Zimmermann und Rundholzspezialist des Unternehmens Jakob Röthlisberge ausgeführt wird. Er ist für die Auslese der Bäume, sowie deren Einkauf zuständig und entscheidet über die Art und Weise, wie der Stamm aufgesägt wird. Die Stämme werden anschliessend längs, quer zu den Jahresringen in gleichgrosse Bretter geschnitten, die 2-3 Jahre gelagert werden.

Auch der besuchte Standort in Bützberg verfügt selbstverständlich über ein solches Lager mit unterschiedlichsten Holzsorten. In der Schreinerei des Werks werden hauptsächlich benutzerdefinierte Aufträge mit kleineren Produktionsauflagen umgesetzt. Während unserer Führung durch den Betrieb konnte die schrittweise Herstellung eines Tisches aus Massivholz hautnah mitverfolgt werden. Es beginnt mit dem Hobeln und Entrinden der Holzrohlinge, dem Schneiden gleich grosser Bretter, dem Setzen des Tischbildes und geht anschliessend über zum Verbinden und Verleimen der Bretter. Zum Schluss werden die Tischbeine angefertigt und mit der Tischplatte verbunden. Die Holzoberfläche wird geölt oder lackiert, abhängig vom Wunsch des jeweiligen Kunden. Girsberger setzt auf eine geölte Oberfläche. Abgeschlossen wurde die Betriebsbesichtigung mit einem Einblick ins Lager des Remanufactoring, wo sich Dutzende abgenutzter aber noch immer funktionstüchtiger Möbel befanden. An den Wänden waren Designentwürfe zu sehen und auf kleinen Regalen wurden Modelle zukünftiger Projekte präsentiert.
Im Showroom erhielt man einen Einblick in die Breite Produktpalette des Möbelherstellers, der vielseitige Kompetenzen im Umgang mit unterschiedlichsten Materialen und Rohstoffen, wie Metall, Textil oder auch Kunststoff aufweist. Das Fazit, welches sich aus unserem Aufenthalt ziehen lässt ist ein gutes: Nämlich das auch etablierte Unternehmen ohne Start-up Charakter in der Lage sein können im grossen Stil ökologisch zu wirtschaften, indem sie den Fokus auf qualitative, rentable, nachhaltige Produkte legen, die weder gebastelt noch utopisch wirken.
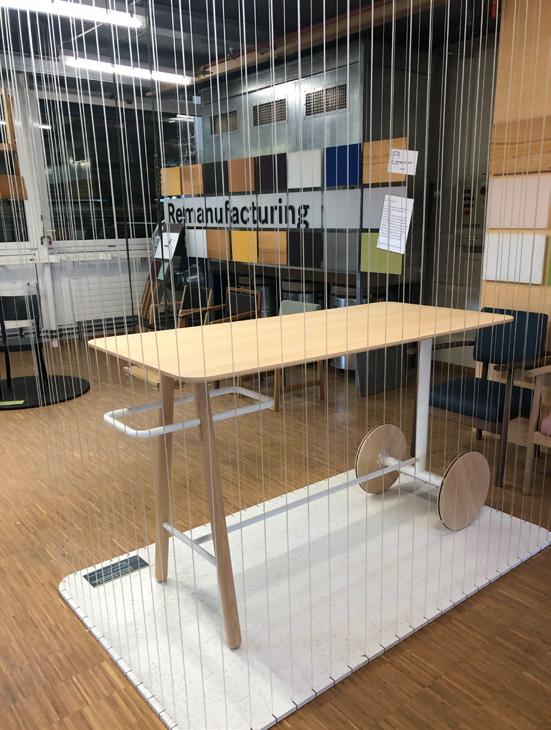

Studienreise
Produktdesign
06.–10. Februar 2023
Organisation und Leitung: Miriam Nietlispach mit Bigna Suter
Gestaltung: Alessa Gassmann
ein gemeinsames Modul von BA Objektdesign, Christoph Schindler
DK.BA_OD_106.H2201
BA Textildesign, Lilia Glanzmann
DK.BA_TX_102.H2201
BA Spatial Design, Klaus Marek
DK.BA_SD_104. H2201
Hochschule Luzern Design & Kunst
745 Viscosistadt
Nylsuisseplatz 1
6020 Luzern-Emmenbrücke
T +41 41 248 64 64
design-kunst@hslu.ch
www.hslu.ch