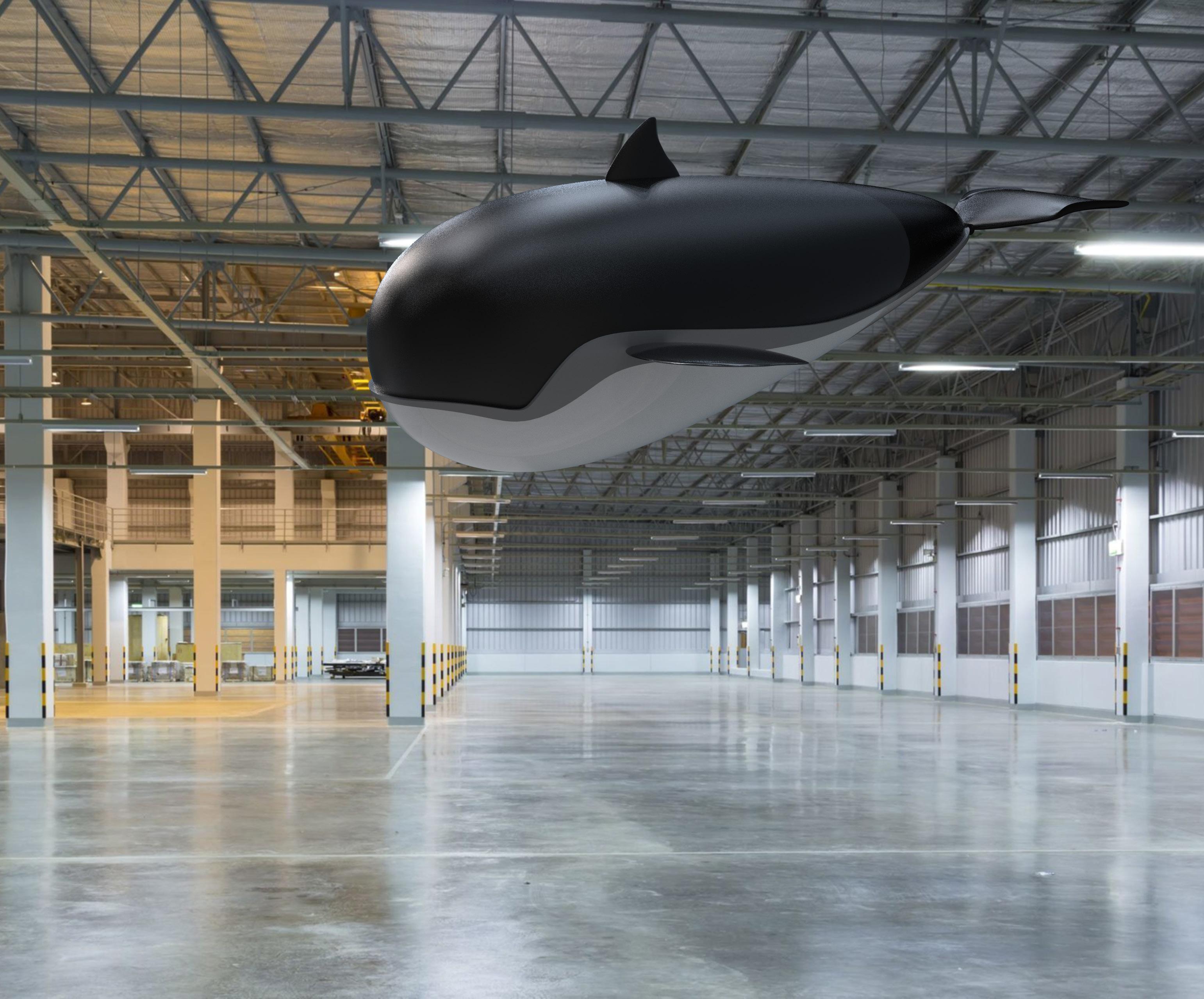
2 minute read
Leichtgewichts Materialreserche
Styropor = 0.06 g/cm3
Sikablock m80 = 0.08 g/cm3
Balsaholz = 0.15-0.3g/cm3
Fichtenholz = 0.6g/cm3
Leichte Verarbeitung
Stabiler als Polyuteranschaum / Teuer e Sun Lightweigt Filament = 0.6 g/cm3 mögliche wandstärke 0.4 mm, Frei formbar
Pla = 1.2 g/cm3
KFC =1.5 g/cm3 extrem Stabil
Aluminium Rettungsdecke 25g/m2
Solafirm Pet Folie 18-20g /m2
Formstudie 3 Orka
Gesamtlänge 160cm
Gaszelle 140cm
Volumen 0.21m3
Auftrieb ca.200 g
Die Gaszelle wird aus aluminiumbeschichteter Folie selbst gemacht. Sie ist umgeben von einem Rahmen aus Hartschaum, an der Technik und Flossen befestigt sind. Da der Rahmen an der Unterseite verläuft, sollte eine Austarierung der Schwanzflosse kein Problem sein. Ich bin skeptisch, was die Machbarkeit der Hülle angeht. Der Vortriebt wird durch einen kleinen Propeller im Rahmen erzeugt. Schwanz und Brustflossen dienen als Höhen und Seitenruder.
Vorteil ist, dass die Technik im Rahmen verbaut und getestet werden kann.
Rahmen
Volumen ca 400cm3
Erstellt in Sikablock m80 ( 0.08g/cm3 ) = 32 g
Flugfähikeit
Rahmen 32g + 50g Folie + Flossen ( Folie+ Sika/ Balsa) 60 g +30 g Elektonik = 172g damit würden 28g Spielraum Verbleiben.
Probleme: Herstellung der Gaszelle/ Kolorierung Relativ gross
Besuch In Der Sarna Plastec Ag
Spezialist für Folientechnik
Der Besuch war sehr aufschlussreich, der Abteilungsleiter Daniel Bucher ist sehr hilfsbereit und bietet mir seine Mithilfe bei dem Verschweissen der Hülle an. Die Firma Sarna Plastec hat sich auf maschinelle Fertigung, vor allem mittels Hochfrequenzschweissen spezialisiert. (Prinzip ähnlich einer Induktionsplatte oder einer Mikrowelle. Das heisst allerdings auch, dass sich die Auswahl an Materialien für die Gaszelle reduziert, möglich sind PVC, TPU und PET
Da mir nun in der Formgebung der Gaszelle mehr Optionen zur Verfügung stehen, muss ich das Designkonzept anpassen. TPU würde sich zum Beispiel anbieten, jedoch nur in transparenter Form, die Färbung oder Bedruckung wäre im Rahmen dieser Bachelor Arbeit zu teuer. Auch hat TPU eine relativ hohe Dichte von 1.22gr/cm2. Was es einerseits perfekt für den Einsatz mit Helium macht, da es dies relativ gut hält, anderseits aber auch eine Menge Gewicht bedeutet.
Nächste Schritte:
Damit Daniel mir den Prototypen schweissen kann muss ich ihm ein Schnittmuster vorbereiten. Da ich in der Formgebung der Gaszelle nun mehr möglichkeiten habe will ich mir das Gewicht eines Gestells wie beim Kugelfisch sparen indem ich die Gaszelle bereits so Forme dass sich ein fisch ergibt. ( Konkret habe ich mich für einen Kofferfisch entschieden.
Konkret bedeutet dies:
Schritt 1:
Erstellen eines 3D Models ohne geolte Flächen ( Da diese probleme bei der Abwicklung erzeugen würden ), Ziel so wenig Schweissnähte wie möglich, Laschen für Elektronik und Flossen bereits intergieren. Rollenbreite von 1.35m nicht überschreiten.
Schritt 2:
Volumen, Foliengewicht und Auftrieb berrechnen, Materialauswahl treffen. ( mindestens 100gr für Flossen und Elektronik einberrechnen)
Schritt 3:
Stimmt die Form und der Auftrieb 3D Render erstellen, ( Blender Tool aufblasen um zu simulieren wie sich die Form unter Druck verhält. Dann Schnittmuster erstellen und TFX File An Daniel schicken.
Schritt 4:
Erstellung Prototyp n.1
Nebenbei: Bemalungstests durchführen.