
7 minute read
WHAT HAS BEEN DONE
What’s Been Done
MycoComposite™ by Evocative
Advertisement
MycoComposite is a 100% home compostable packaging alternative to synthetic foams like styrofoam developed by the Ecovative company (Ecovative Design, 2014). The composite is made by inoculating liquid mushroom mycelium that has been dried, into a substrate of agricultural waste such as hemp hurds, chopped up corn stalks and seed husks. The mycelium mixture is then dehydrated, placed into a plastic mould, as seen in figure 8 , where the mycelium binds the agricultural waste together to create a lightweight form (Manton, M 2015).
Once the mycelium has consumed the substrate the design is then heat treated to stabilise the final shape and to stop the fungi from growing and flowering. Ecovative’s packaging has now gone mainstream with big companies like IKEA and other Fortune 500 companies starting to adopt its packaging for their products. (Redaktion, D, 2016) Ecovative also sells a ‘grow your own’ product where you can buy the dried mycelium and substrate material (annoyingly packaged in plastic as seen in Figure 10) and to mould and use however you wish!

Left
Figure 8. Mould for MycoComposite™ material. Reprinted from Mushroom-based modelling kit allows users to grow their own designs, by Manton. M, 2015, Retrieved from https:// www.dezeen.com/2015/03/25/mushroom-materials-ecovative-modelling-kit-mycelium-designs-of-the-year-2015/
Above
Figure 9. Breakaway corners. Reprinted from Breakaway Corners, by Mushroom® Packaging, 2019, Retrieved from https://mushroompackaging.com/collections/mushroom-packaging/products/breakaway-corners-small Figure 9. 11
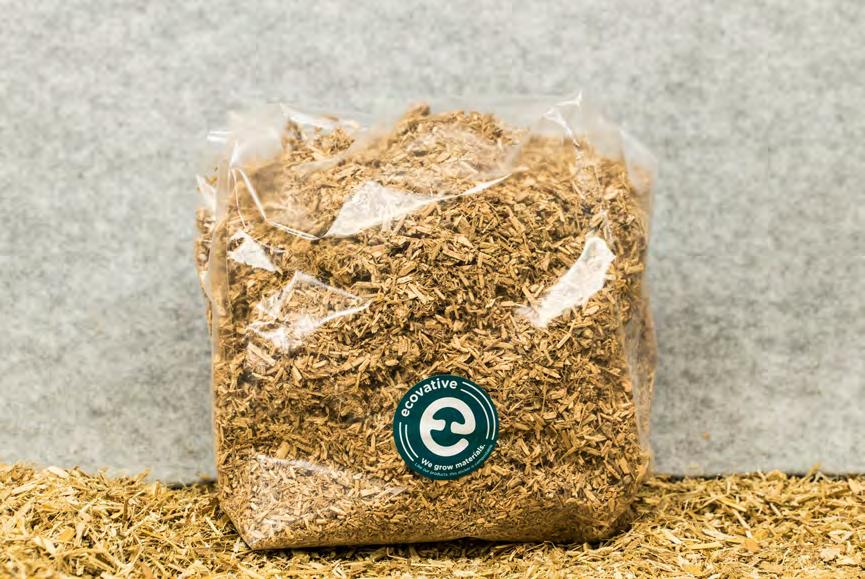
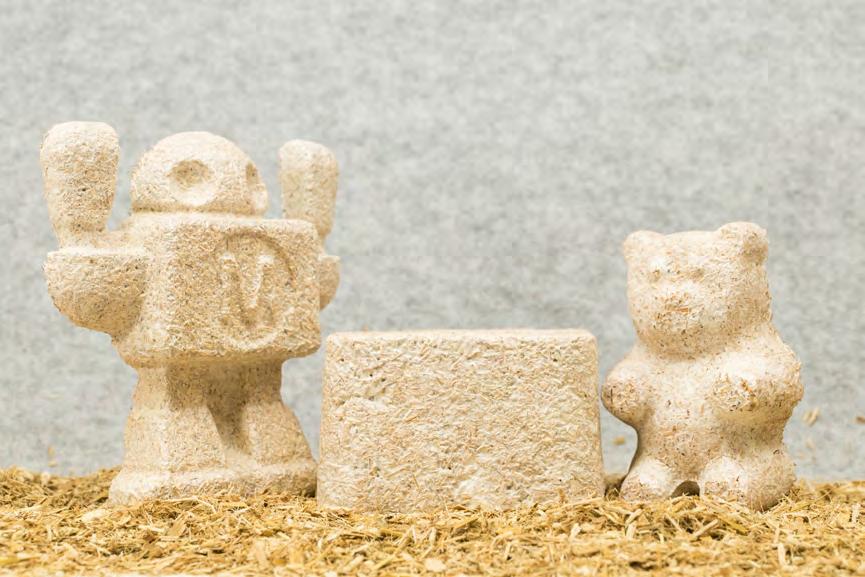
Figure 10 and 11. GIY (Grow It Yourself) example. Reprinted from MakerShed.com – Webstore to the Maker Community – Now Features Ecovative’s GIY (Grow It Yourself) Mushroom® Material Kits, by Ecovative Admin, 2016, Retrieved from https://grow.bio/blogs/press-releases/makershed-com-webstoreto-the-maker-community-now-features-ecovative-s-giy-grow-it-yourself-mushroom-material-kits
Ecovative also run a yearly competition called the Mycelium Design Contest to expand the potential uses for their composite material. The winners in 2019 were Jerome Tavé and Kyle Lawson at 10th Floor Studios with their Room Divider Concept, as seen in figure 12. The concept explores the materials acoustic properties (GROW.bio, 2019). I found their project insightful as they used a plywood mould rather than the plastic ones used by Danielle Trofe and Ecovative. To ensure the mycelium did not bind with the plywood mould (and to protect the inside of the mould), a thin layer of vinyl and a thin coating of paste wax was applied to the inside surfaces. (GROW. bio, 2019)
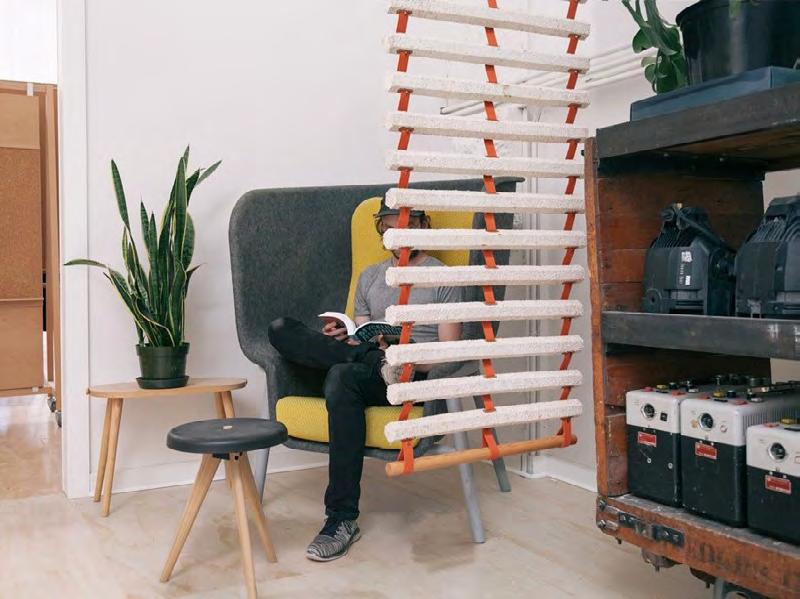
Above
Figure 12. Room Divider Concept. Reprinted from GIY Maker Spotlight: Jerome Tavé and Kyle Lawson, 2019, Retrieved from https://grow.bio/blogs/grow-bio-blog/giy-maker-spotlightjerome-tave-and-kyle-lawson

Danielle Trofe
The designer Danielle Trofe has partnered with Ecovative and used their Grow It Yourself material in her lampshade collections Glow Lamp and MushLume. Trofe simply re-hydrates the MycoComposite material by mixing through water, then pressing the wet composite into a plastic mould that she has either 3D printed or cast, and then waits for the mycelium to work it’s magic. (PIX11 News, 2016). I love her designs as they are a simple and beautiful use of the GIY material; elevating it to a glamourous and desirable design product.

Left
Figure 13. Mushlume Trumpet Pendant, Reprinted from Biofabricated Lighting, Danille Trofe, 2019, Retrieved from https://danielletrofe.com/the-work
Above
Figure 14. MushLume lighting collection. Reprinted from Danielle Trofe, by Danielle Trofe Design, 2019. Retrieved from https://danielletrofe.com/ 15
Mycelium Lamps by Nir Meiri
Mycelium Lamps is a collaboration project between Nir Meiri Studio and BIOHM. The flat mycelium structure forms the shade part of the lamp which sits on top of a metal pole and stand. To make the shade, Mycelium spores are inserted into a mould that is filled with waste paper, which the mycelium consumes; forming a solid base with fungus growing on top. Once the fungus is removed and the mycelium dried, the stable form is then pressed to get the final flat smooth shape. (Nir Meiri, 2018)
Nir Meiri also states that “mycelium consumes organic and synthetic waste”. The potential ability for mycelium to consume synthetic materials like plastics is an exciting prospect, because, if developed this theory could change the way our waste streams work entirely as well as tackle the growing crisis of plastic waste. The ability for fungi to break down plastic is supported by a recent study published by the Kew Royal Botanic Gardens. “fungus (Aspergillus tubingensis) [is] capable of breaking down plastics such as polyester polyurethane (used in a wide diversity of products such as refrigerator insulation and synthetic leather) in weeks rather than years.” (Willis, K. J, 2018)

Above
Figure 15. Growing mycelium experiments. Reprinted from Mycelium lights, by NirMeiri Design Studio, 2018, Retrieved from https://www.nirmeiri.com/mycelium-lights
Right
Figure 16. Mycelium Lights. Reprinted from Mycelium lights, by NirMeiri Design Studio, 2018, Retrieved from https://www.nirmeiri.com/mycelium-lights
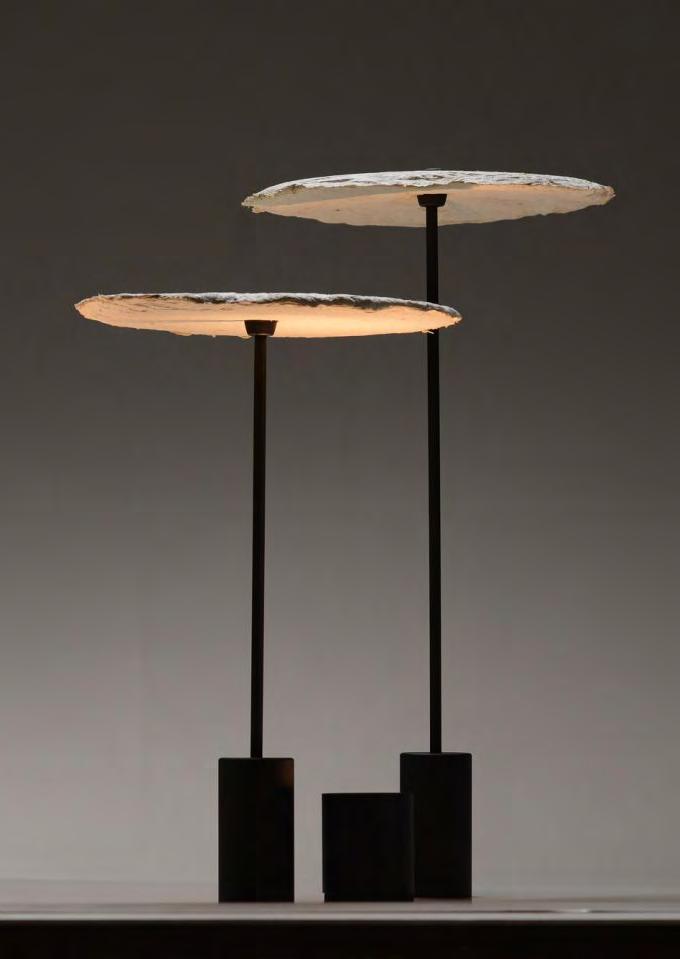
Redhouse Architecture – Bioterials
Redhouse architecture are researching ways to help solve the housing crisis in Cleveland by recycling the derelict buildings into new building materials using mycelium. The process involves breaking down waste building materials like wood into a pulp, and then adding mushroom mycelium to create any number of building materials, from boards and brick to structural insulating panels. (Dezeen, 2018) As seen in Figure 17 Redhouse tests have found that the grown material has strengths comparable to hardwood and concrete.
While the design itself is not inventive, I think the idea they have developed is. To turn derelict houses into new building material is a wonderfully circular and useful idea, especially when the materials strengths can compare to other building materials. The pulp from the old building could also be used to create any design, not just new building materials.
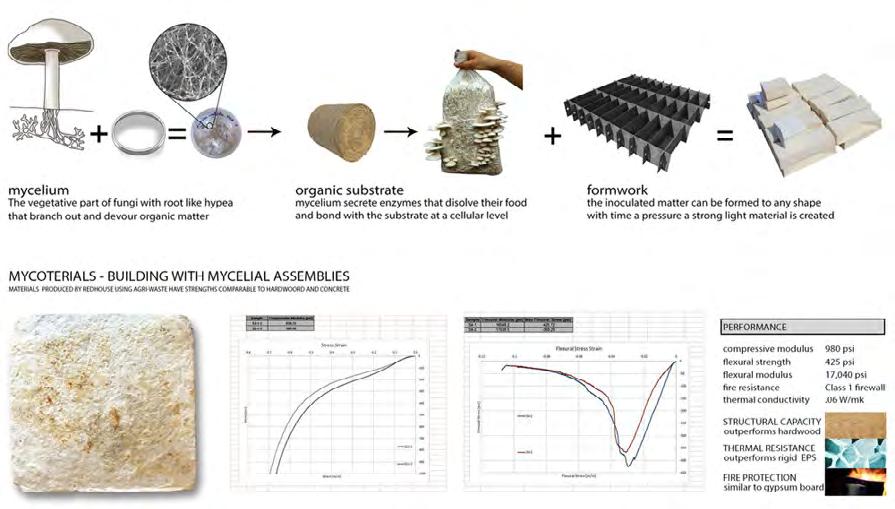
Above
Figure 17. Processes and Performance, Reprinted from bioterials, by redhouse architecture, 2018, Retrieved from http://www.redhousearchitecture.org/mycoterials/ho115ljk2evokt0rihz8gv6jnoz78r
Right
Figure 18. Brick, Reprinted from bioterials, by redhouse architecture, 2018, Retrieved from http://www.redhousearchitecture.org/mycoterials/ho115ljk2evokt0rihz8gv6jnoz78r
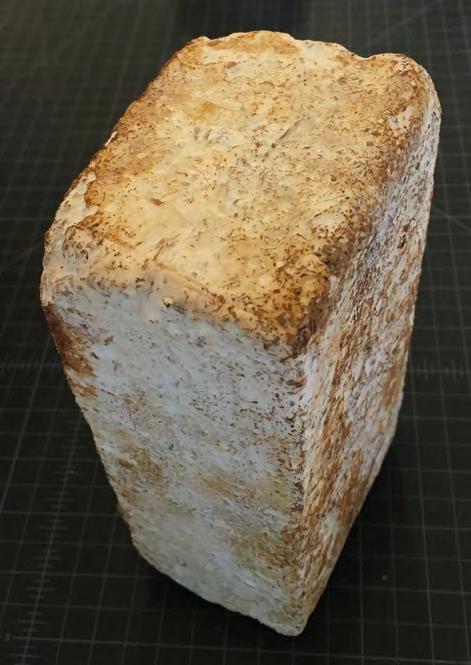
DIY Growers
There are a growing number of people around the world sharing their own do it yourself test working with mycelium and growing mushrooms. While, like most of the academic research out there and the focus is on the mushrooms produced, you can still draw from their knowledge and their tests working with different substrates and growing environments. Many people recommend starting with Ecovative’s GIY (grow it yourself) product, which takes most of the steps out for you, and makes working with mycelium more accessible. (Woodfin, 2019) Then once you have a handle on the basics and ensuring the mycelium is happy in the conditions in your home you can move onto more involved tests.
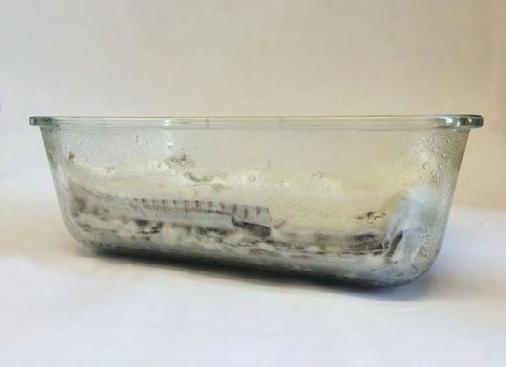
One example of a DIY grower who highlighted how ‘low tech’ growing mycelium can be is Ashley Scarborough who shared her experiment on Instructables. (Scarborough, 2017). She successfully created a mycelium culture using only store-bought mushrooms, cardboard, water, a glass container and a bucket! The cardboard is soaked in water and then layered with finely cut up mushroom stems. The container is then sealed, and left is a dark place to grow. This method would eliminate the need for purchasing a grain spawn or creating your own mycelium culture.
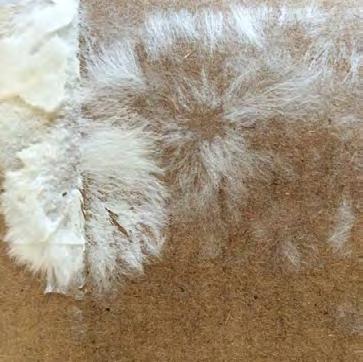
Left
Figure 19. Making Mycelium growth results. Reprinted from Making Mycelium, by Ashley Scarborough. Retrieved from https://www.instructables.com/id/Making-Mycelium/
Right
Figure 20. Making Mycelium close up results. Reprinted from Making Mycelium, by Ashley Scarborough. Retrieved from https://www.instructables.com/id/Making-Mycelium/
What next?
I would like to take a closer look at the material properties of mycelium grown products and how these properties can change with different waste substrates. I will look at the two types of fungi species commonly used for mycelium based composites, Pleurotus (oyster mushroom) varieties and the Ganoderma Lingzhi (Reishi or Lingzhi Mushroom) varieties. There are so many varieties of mushrooms out there, and with a staggering 2189 new species described in 2017 alone (Willis, K. J. 2018), how do we know which varieties and substrates work best for this sort of production? The next step is then to conduct some material experiments, to source local waste materials as substrates and to begin the process of growing my own mycelium based composites!