
5 minute read
WHAT NEXT
Substrates from waste
The type of substrate and production method heavily impacts the final appearance, strength and density of the mycelium composite produced. Once the basics of what a family of fungi grow on is understood, there are so many viable substrate options that a designer is then able to choose from a wide variety of substrates, based on the aesthetic and desired mechanical properties. That being said, as the amount of research and experiments done in this field increase, so will the options of finishes and applications available for designers and makers.
Advertisement
Most of the research done in this field focuses on the substrate effect of the yield of fruiting mushrooms, for example (Hoa, Wang, & Wang, 2015) and (Mehta, Jandaik, & Gupta, 2014) and the potential bioremediation uses (Matos, Bezerra, & Dias, 2007) rather than the mechanical and aesthetic qualities of the mycelium composite. Though enough research has been done about the general needs of the mycekium understood, a designer can make an informed choice when deciding on a substrate that will work best for their design.
Any mushroom variety will grow best on a substrate closest to the one it naturally grows on in nature. For growing mycelium based composites Saprotrophic fungi are the best candidates as this type of fungi feeds off and breaks down carbon (Assembling the Fungal Tree of Life Project, 2005) Within this category the white rot fungi is best suited to producing mycelium composites as they are able to break down both cellulose and lignin. Lignin is a complex polymer in the cell wall of many plants and makes them ridged and woody and is one of the hardest substances to break down in nature. (Sun, 2010) White rot mushrooms are one of the only organisms that can decompose it.
Left
Figure 21. Mushroom Grain Spawn Ganoderma Steyaertanum Tasmainain Reishi. Credit Author.
The most commonly used white rot fungi for mycelium composite production are the Pleurotus (oyster mushroom) varieties and the Ganoderma Lingzhi (Reishi or Lingzhi Mushroom) varieties. Both varieties naturally grow on hardwood, have fast growing and very strong mycelium hyphe (FreshCap Mushrooms, 2017) They are also able to break down a variety of lignocellulosic substrates sourced from the waste streams from the agricultural, forest and food-processing industries. (Sánchez, 2010). With this in mind the options for substrates a designer can use really opens up. Sawdust, varieties of straw, cotton bi products, sugarcane bagasse, coffee grounds, and corncobs are just some of the many substrate options.
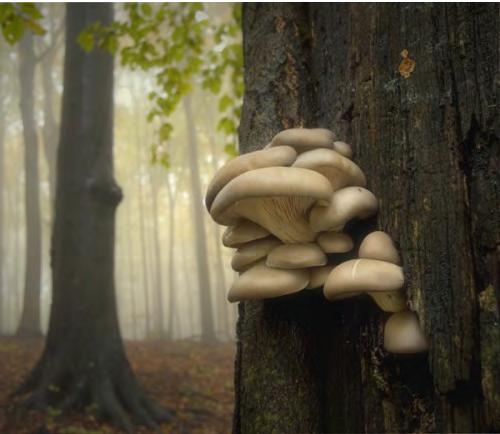
Figure 22. Pearl Oyster Mushroom (Pleurotus Ostreatus). Reprinted from Mushroom, 2019, Retrieved from https://www.mushrooms.com/pearl-oyster-mushrooms
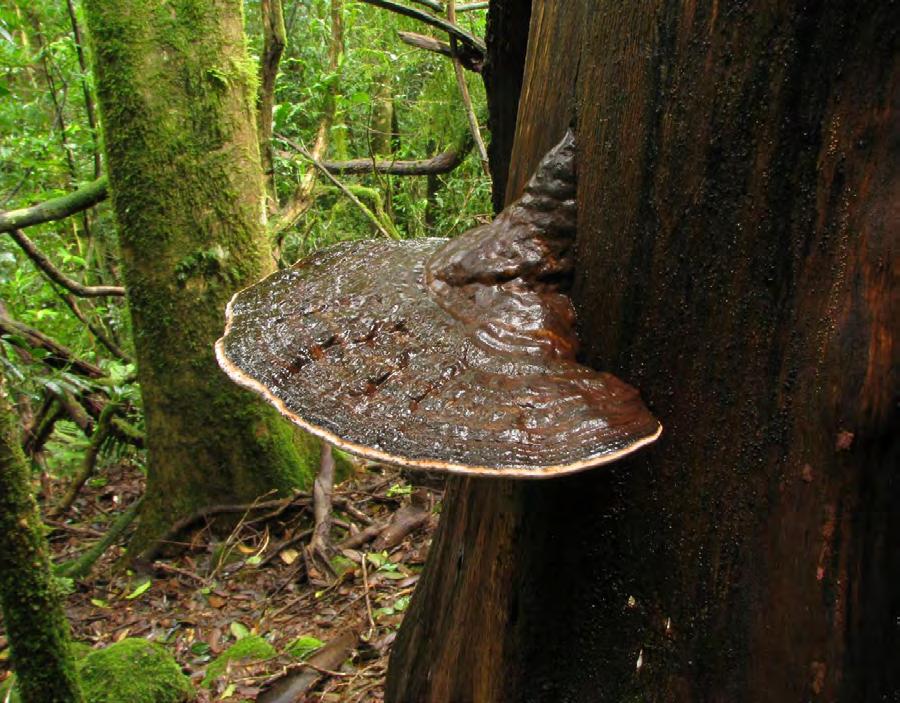
Figure 23. Tasmanian Reishi (Ganoderma Steyaertanum). Reprinted from Queensland Mycological Society, 2012, Retrieved from http://qldfungi.org.au/fungi-id/fungi-keys/fungi-key-ganoderma
Form, aesthetics and mechanical qualities of a mycelium composites
The substrate a mycelium-based composite is grown on is one of the many factors that influence the final result. Haneef et al. (2017) found that the “addition of dextrose to the cellulose based substrate makes both fungal materials more elastic” as the added dextrose is easier for the fungi to break down. Appels et al. (2019) found that a finer substrate like sawdust has a smoother and more dense appearance than straw and cotton which has larger substrate particles, and T.multicolor grown on rapeseed straw had a soft velvety skin and an elastic foamlike appearance.
Appels et al. (2019) also explored the effect of different substrates and mechanical properties of mycelium-based composites with the focus on seeing if non-foam type of mycelium composite materials can be made. Appels et al. (2019) excitingly discovered that “heat pressing improves homogeneity, strength and stiffness of the materials shifting their performance from foam-like to cork- and wood-like” Figure 4 illustrates the how the density and Young’s Modulus of the heat pressed samples (TRH ●, PCH , PRH ) enter the realm of natural materials in both strength density and appearance. The two heat press samples grown on Rapeseed straw had the results closest that of the natural materials in contrast to the heat pressed sample grown on cotton landing higher on the Young’s Modulus scale.
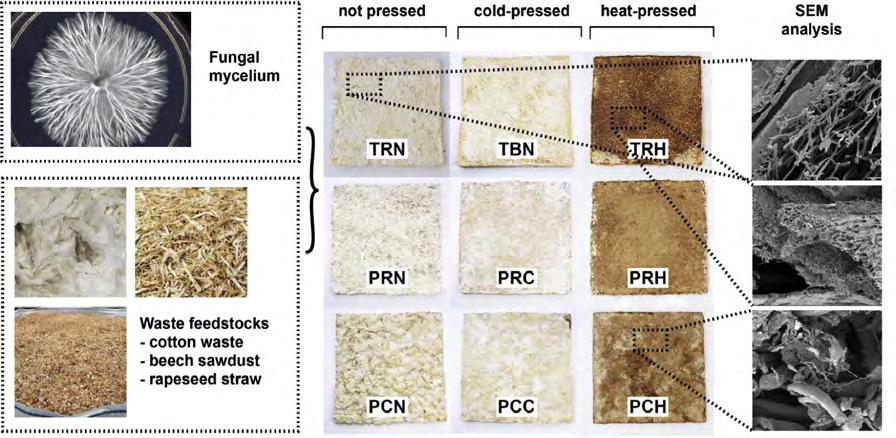
Figure 24. Materials resulting from growth of T. multicolor on sawdust (TBN) and straw with (TRH) or without (TRN) heat pressing and growth of P. ostreatus on cotton with heat pressing (PCH), cold pressing (PCC) and without pressing (PCN) and on straw with heat pressing (PRH), cold pressing (PRC) and without pressing (PRN). Reprinted from “Fabrication factors influencing mechanical, moisture- and water-related properties of mycelium-based composites,” by Appels, F. V., Camere, S., Montalti, M., Karana, E., Jansen, K. M., Dijksterhuis, J., ... & Wösten, H. A., 2019, Materials & Design, 161, 64-71.
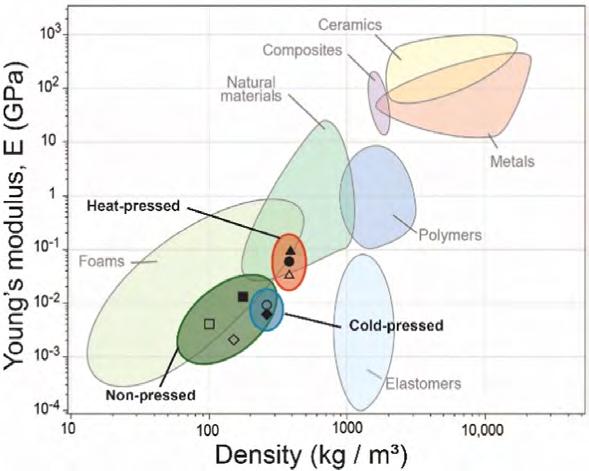
Heat pressing also influenced the final appearance, in both texture and colour. “In all cases, individual hyphae within the mycelium were less clearly visible after heat pressing probably due to gluing of hyphae and substrate together.” Making the hyphae less visible would also result in a smoother and more consistent texture finish. The colour of heat pressed samples ranged from white to brown as opposed to the white and cream non-pressed samples. “The browning of the material is most likely caused by… reactions involving sugars and proteins present in the fungal cell walls and the plant material. Alternatively, it may be caused by caramelization of plant and fungal sugars or by pyrolysis of organic material.” The idea of heat pressing is an exciting new addition to the field of mycelium-based design and composite creation. It opens up many more options for products that require a structural element such as building materials.
Figure 25. Material family chart of the Young’s modulus (GPa) vs density (kg/m3). Non-, cold-, and heat-pressed materials form clusters within foam- (TRN, TBN, PRN, PCC, PRC), and natural-like materials (TRH, PCH, PRH). Reprinted from “Fabrication factors influencing mechanical, moisture- and water-related properties of mycelium-based composites,” by Appels, F. V., Camere, S., Montalti, M., Karana, E., Jansen, K. M., Dijksterhuis, J., ... & Wösten, H. A., 2019, Materials & Design, 161, 64-71.