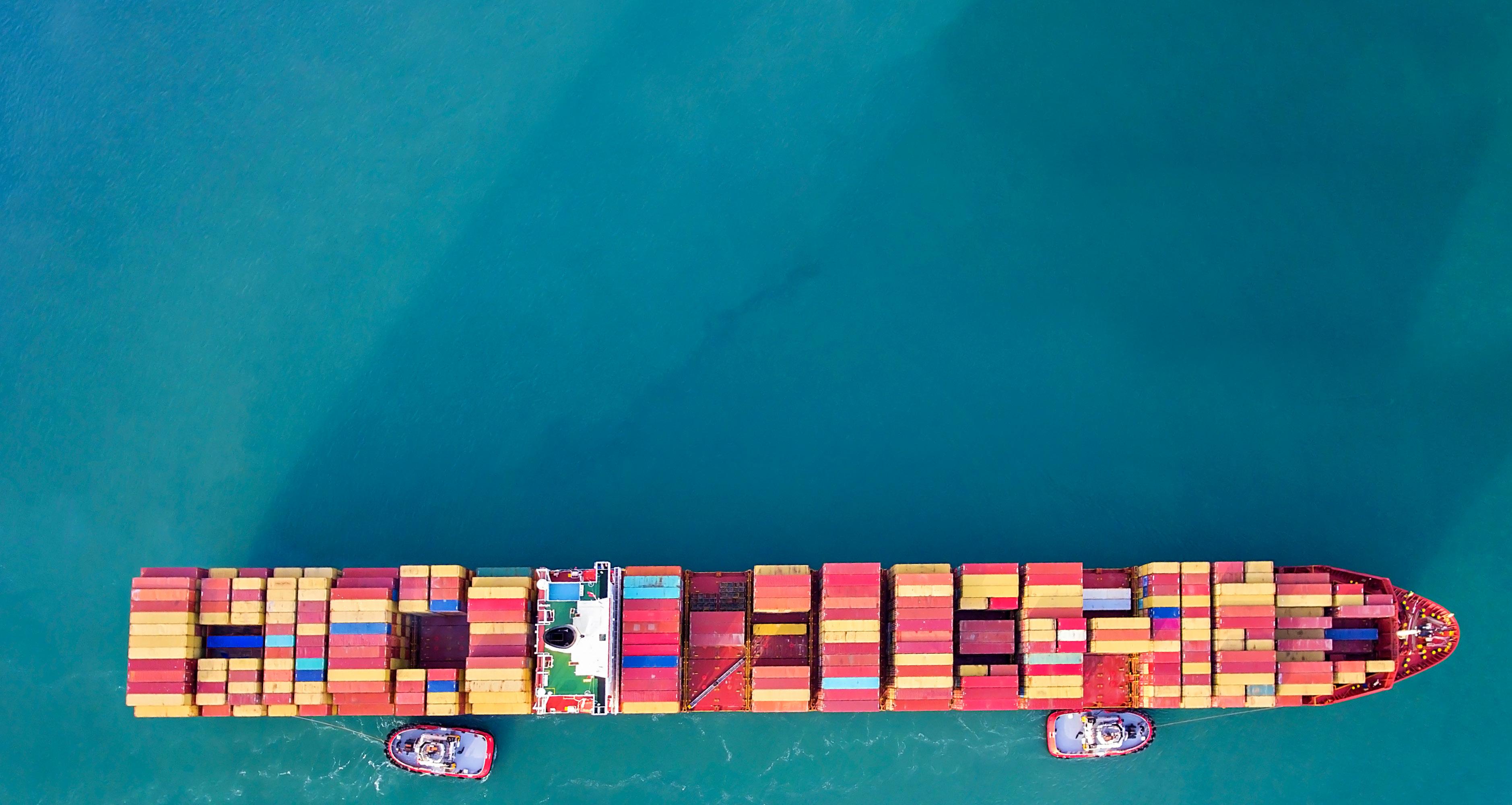
4 minute read
Supply Chain Delays Continue to Affect the Homebuilding Industry
You wonder how Santa did it a couple of weeks ago. A present delivered to every single child in the world. No supply chain shortages of peppermint, poinsettias, or pop guns. No elves lounging on the couch, and his workshop just hummed like it always does. Fortunately for Santa, he didn’t get a lot of present requests from children for Canadian softwood lumber, residential electrical panels, dishwashers, or semiconductors.
Those are just four of myriad product lines plighting a home building industry that is experiencing broad supply chain shortages, which in turn lengthens the time it takes to build a house, increasing the home price and generally making new-home buyers kind of antsy.
Eighteen months ago, we were lamenting home inventory shortages because the demand was so high, with people buying new, larger homes to find more indoor and outdoor space in which to shelter in place.
Today the challenge is the same, home inventory shortages, but the reason is that building supplies are sitting in dank steel containers in a cargo ship bobbing off the shore of Long Beach, CA.
According to William Bullock, president of Minto Communities’ Latitude Margaritaville division, “There are supply disruptions throughout the entire global economy. There are so many components that go into a house. One day it’s windows on delay, the next day breaker boxes; then the day after that, it can be insulation. We are constantly adjusting to the supply constraints. You can’t get the goods through the system fast enough anymore due to shipping and logistical challenges. This is having drastic effects on the deliveries for all types of industries, homebuilding included. At Minto, we are closely monitoring the supply chain and constantly adapting to meet our commitments to the customer.”
“It is still a great time to buy a house, and interest rates are historically low. But, please come in with patience and understanding. The good thing about Minto is, when we give you a date, we keep it. We haven’t been bumping people on an estimated completion date. While we can continue to deliver homes, we are mindful of the number of homes that we sell, so we can maintain quality and maintain a viable construction pace,” added Bullock.
Lumbering Toward Progress
American homebuilders rely greatly on millions of board feet of lumber for studs, joists, rafters, sheathing, and more. There’s good and bad news on the lumber front. The good news is the price of lumber has dropped dramatically from a high of $1,500 per thousand board feet last summer to roughly $600, where the price was at least holding steady last November. The bad news is that in that same month, the U.S. reimposed a 20% duty on Canadian softwood lumber imports. The two countries have been feuding forever over imported Canadian lumber, and it’s a long story.
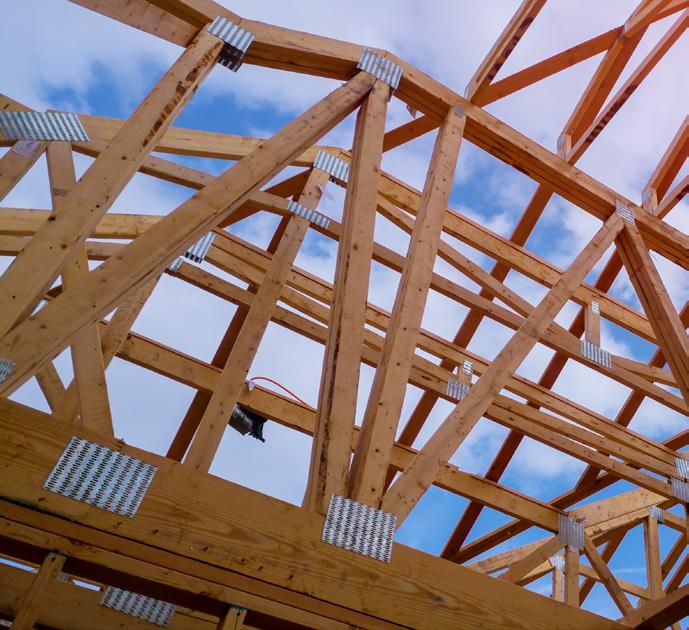
But, at this writing, the chairman of the National Association of Home Builders, Chuck Fowke, was hoping that a brief moratorium on the duty would ease supply shortages of lumber. Said Fowke, “We are imploring U.S. government officials to ease millions of American homebuyers and homeowners who have seen the cost of housing rise by tens of thousands of dollars over the past year due in part to unprecedented lumber price volatility fueled by tariffs on Canadian lumber. Until a long-term solution can be reached, the administration needs to suspend duties on all imported building materials and goods, including Canadian lumber, to ease supply chain bottlenecks that are causing project delays and putting upward pressure on home prices.”
Wash Day
The view isn’t much brighter from one of the country’s leading home appliance manufacturers.
“Shortages of dishwashers and refrigerators are likely to stretch well into 2022, as supply-chain problems constrain production, and consumer demand remains strong,” said Whirlpool Corporation’s chief executive officer, Marc Bitzer.
“We have ramped up appliance production, but delays have grown as waits for components and other snags lead to backorders of around six weeks for the average appliance. We are producing more, but the demand is so strong we just can’t keep up.”
The Faucet Drip
Delta Faucet Co. is also experiencing supply chain shortages, but they have come up with a creative solution to ease the backlogs. Back in the summer, the company decided to “prioritize production” to include “strategic collections and/or finishes in all brands.” In other words, by focusing on the more high-demand product lines and pausing production on less requested, Delta can dedicate available raw materials most appropriately.
A sobering study conducted by the National Kitchen & Bath Association suggests that “supply constraints coupled with rising mate- rials prices and shipping costs are forcing a growing number of kitchen/bath design firms to cope with longer lead times, seek alternative supply sources, and increase their prices in an effort to protect profit margins.”
For the team at Bill Clark Homes, a premier home builder throughout the Wilmington and New Bern towns on the southeastern North Carolina coast, the practical news is that it still makes sense to buy a home now.
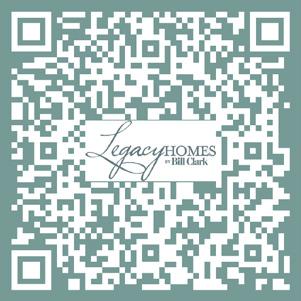
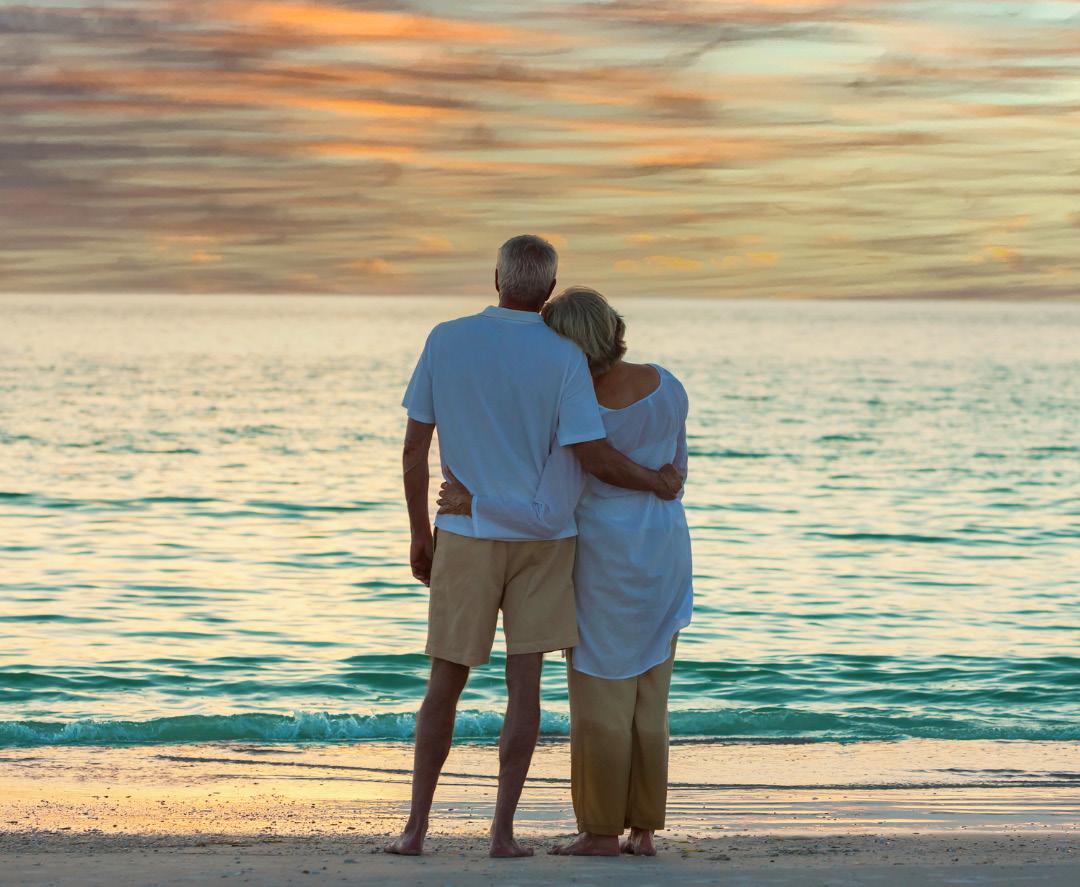

According to the company’s director of sales & marketing, Robin Campbell, “At Bill Clark Homes, we take great pride in what we do. We believe that the clients deserve the best. We are truly in this process together with our clients. However, it’s a different world now. There are true limitations. The supply chain is probably the hardest thing to explain to a homebuyer who starts out really excited. For example, you might not be able to get a certain tile or a certain size of tile that you had chosen. Windows might have a 20+ week lead time. If someone has built a home before, it is a totally different process in today’s market. However, with the low-interest rates, it still makes sense to buy a new home now. You may still be able to get more of the home that you want rather than waiting until later.”
Green Shoots!
There is some positive news coming from Babcock Ranch, a glorious and ultra-sustainable town in southwest Florida. The community’s Sr. V.P. Marketing & Sales, Laura Keller, says, “Hopefully, within the coming year things will loosen up, and builders will be able to get ahead and offer more homes. If you build too far out, you cannot control the cost of building that home, so oftentimes builders will limit the number of homes that they release. At Babcock Ranch, you should expect a nine-month process, but that varies based on the builder.”
So, hopefully, by the time you are reading this, some of the supply chain constraint conditions have begun to alleviate. Until then, maybe Rudolph could make a few more spins around the world and send Santa down the chimney with some fragrant Canadian pines, shiny Chinese steel to build new dishwashers, and some storm windows to keep out the winter chill.
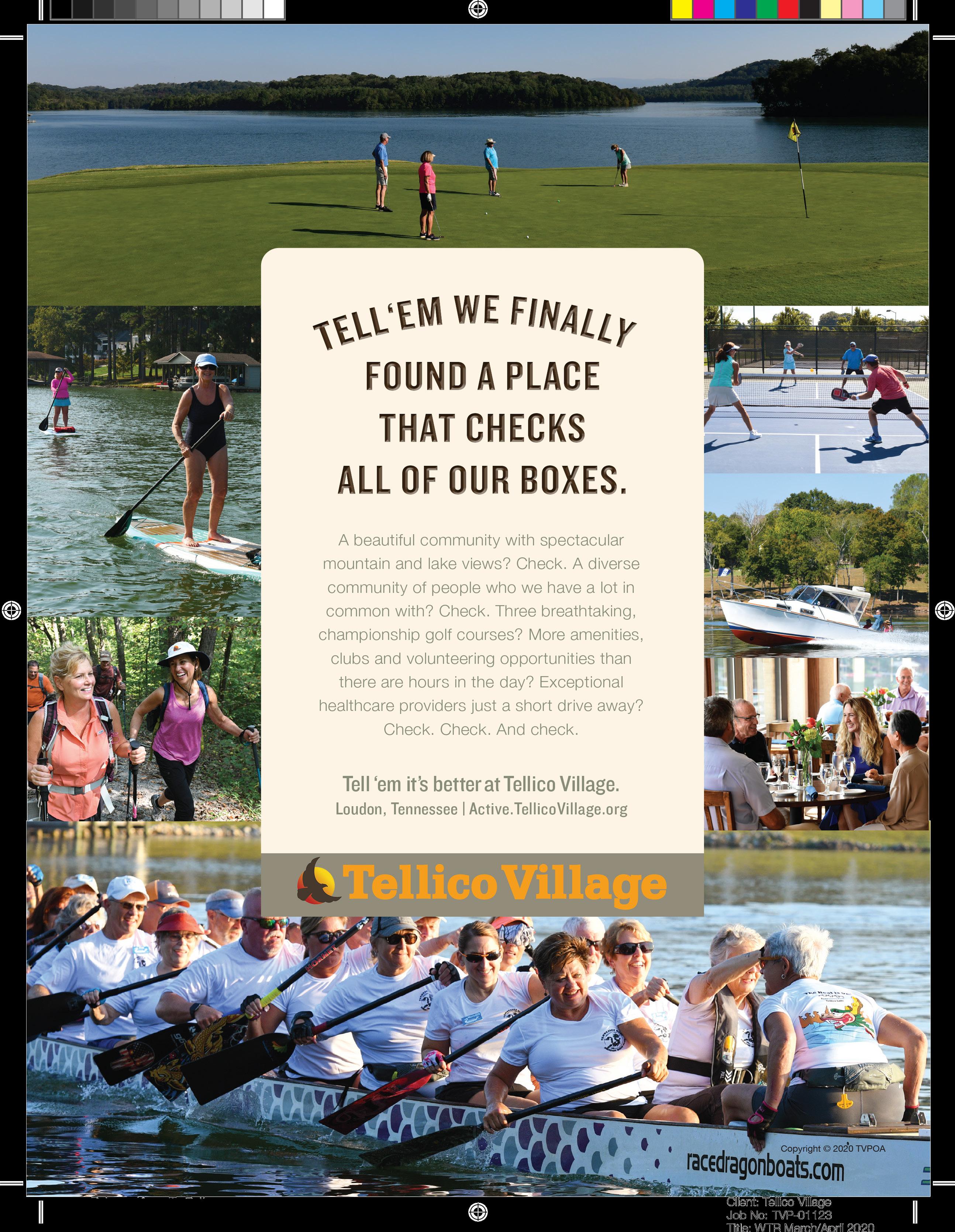
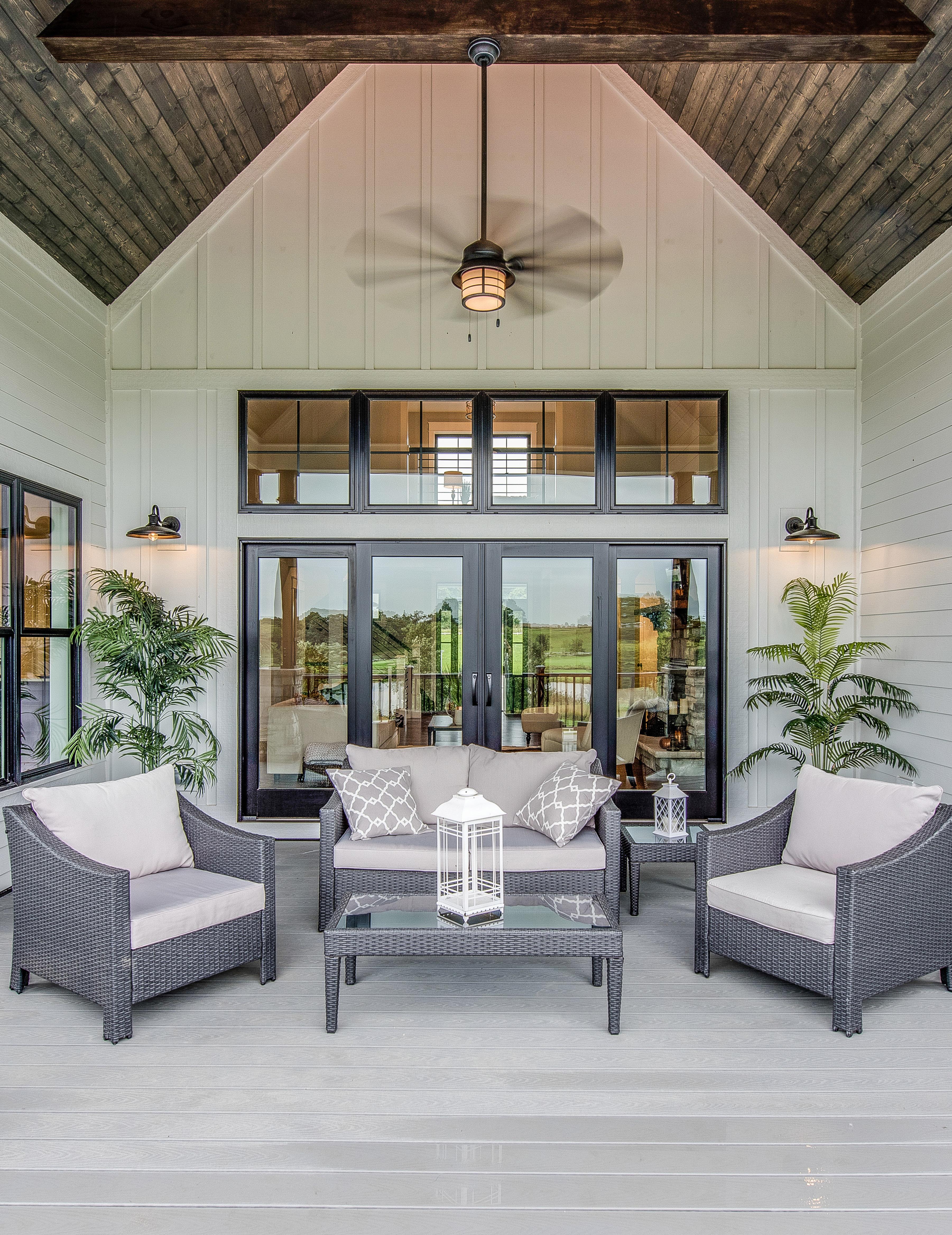
By Warren Grant