
6 minute read
Fishing For Energy-Efficient Heating
from commARCH - July 2017
by IdeaSoil
Above. The units feature high, wood-beamed ceilings; large, steel replica operable windows; and energy-effi cient mechanical systems.
Below. The complex features a variety of sustainable features, including water-saving fi xtures, energy-effi cient mechanical systems, low-VOC fi nishes, effi cient lighting, native vegetation, and a walkable neighborhood.
Advertisement

sonry, stabilized in 2009, had to be redone when the project finally went ahead in 2014,” Lane continued.
In addition, there were some siting issues. The site is bordered by Green River conservation land. The project was subject to riverbank stabilization work before the permeable public Riverwalk was constructed. The Riverwalk also required designated extra parking for walkers.
OTHER DESIGN CHALLENGES A signifi cant design challenge faced by Finegold Alexander Architects was evaluating which buildings to keep, noted Alexander. “As with any large complex spanning over 100 years, many alterations and poor-quality additions were made to the original mill brick buildings,” he added.
The design team identified the most historic and usable eight structures, all built between 1895 and 1924. The re-use of these buildings required demolition of more than 80,000 sq. ft. of useless, dilapidated in-filled sheds and warehouse, many from the 1940s and 1950s. This allowed the remaining 90,000 sq. ft. to be economically reused and also available for federal and state historic tax credits. An additional benefit of the demolition was the creation of new entry courtyards and exterior recreation spaces.
WINDOWS Windows were a particular challenge at Cable Mills, noted Lane. “Because the complex was built and added to at different times in its history, there was a hodge-podge of window openings ranging from some less than 4 ft. tall to others standing at more than 9 ft. There were more than 20 types of windows at the site ranging from traditional steel industrial windows, double hungs, awning windows, to captured hopper windows, where the middle of the window pivots. Since historic tax credits were involved, National Park Service approval was required for the replacement windows.”
According to Bill Wilder, director of technical sales for the window supplier, Graham Architectural Products, York, PA, arriving at the right solution wasn’t easy. “You’re trying to replicate with insulated glass an appearance that basically meets the minimal amount of material required to hold a single piece of glass. So that becomes a challenge–trying to meet the historic criteria while meeting the structural requirements and the enhanced thermal performance as well.”
Cable Mill Lofts was named as the award winner for Biggest Impact Rural/ Suburban by Preservation Massachusetts, Plymouth, MA, a non-profit preservation organization dedicated to preserve the state’s historic heritage. The award was presented in May 2017 at the organization’s annual Power of Preservation Awards event.
Bringing the Cable Mills project to completion was made possible by a high degree of patience, planning, and cooperation. It stands as a testament to the vision of those who conceived it and saw it through. CA
Want more information? To download the information listed below, visit commercialarchitecturemagazine.com/1707cablemills
Finegold Alexander Architects Cable Mills
Complete project team and funding list. Preservation Massachusetts
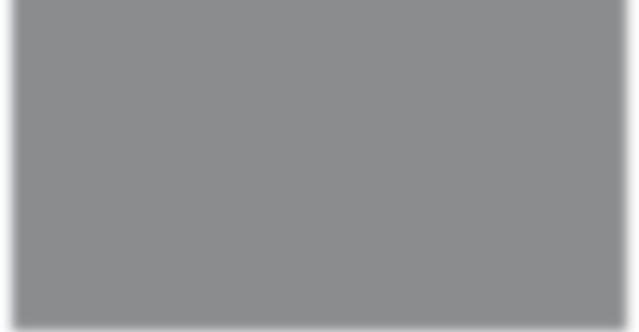
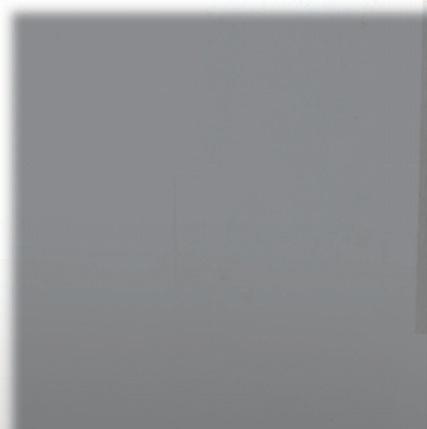

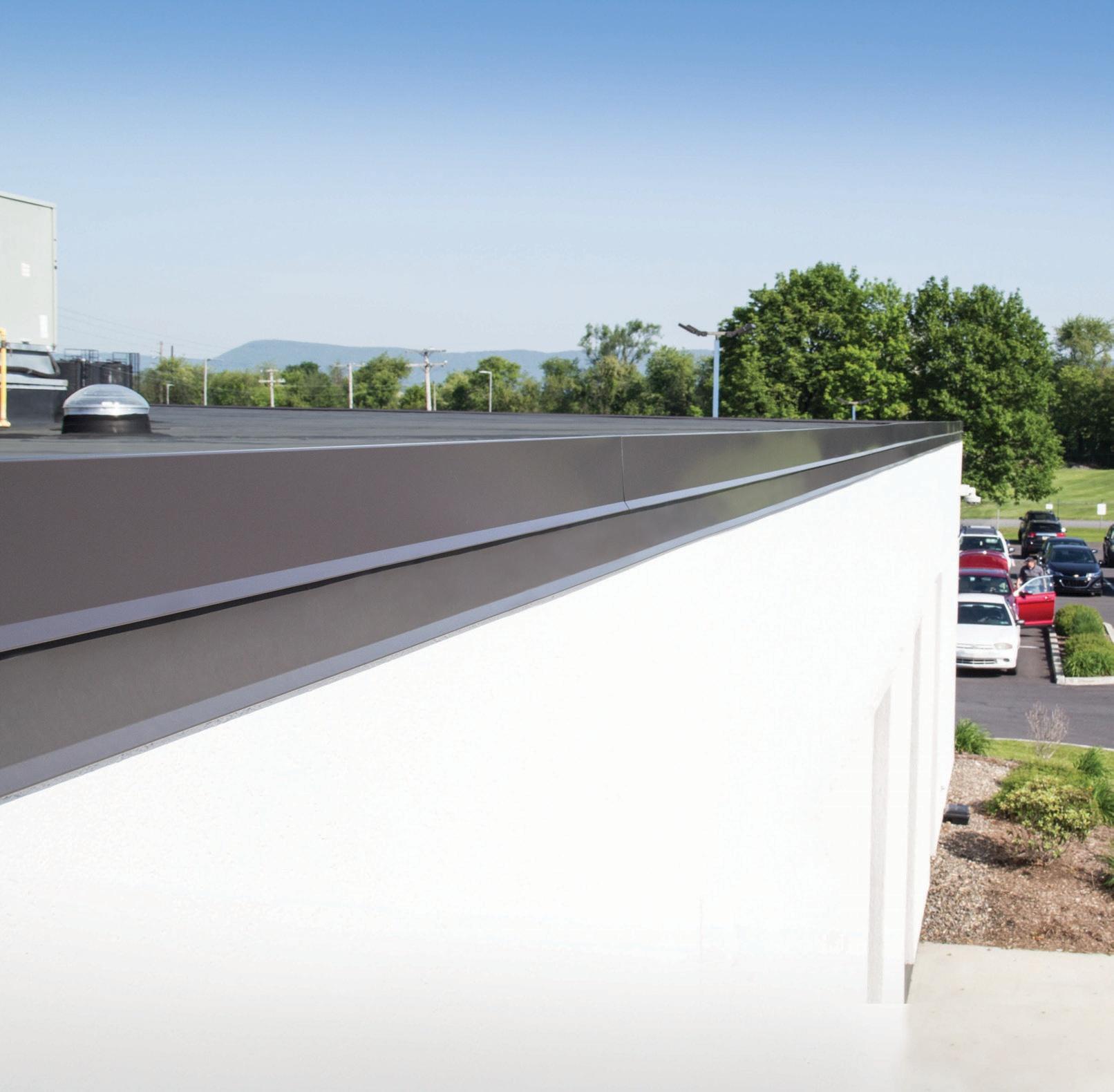
A Weil-McLain boiler system works for an aquaponics farm.
Shifting a career focus from soybeans and corn to tilapia and lettuce, the Goodenough family was in unchartered waters as they began a new venture into aquaponics farming. An advanced building-control system using Weil-McLain, Burr Ridge, IL, Evergreen boilers helped ensure smooth sailing for the first growing season.
The Goodenoughs are a fourth and fifth generation farm family in Mindoro, WI, located on the west side of the state. The farm began with raising hogs and cows, then later moved to a corn and soybean operation, and now is an aquaponics grower. The catalyst for the move to aquaponics occurred several years ago when, according to Tim Goodenough, “input prices were high, grain prices were fluctuating constantly, and Mother Nature was throwing us curve balls.”
As a result, Tim started researching different agricultural methods. He had fish farming in the back of his mind after seeing an operation on an American Soybean Association trip to South America several years earlier. “When I came back home I had a lot of information about fish farming, and we began looking into the concept,” said Tim, who was raised on the farm and runs it with his wife, Bonny, and their four children. The family’s research led them to consider aquaponics.
Aquaponics combines aquaculture, or fish farming, and hydroponics (raising plants without soil), in a closedloop system. The nutrient-rich water that results from raising fish provides a source of natural fertilizer for the growing plants.
Ready to give the aquaponics operation a go, Tim and Bonny purchased a used four-section, 13,600-sq.-ft. greenhouse. The family spent three months physically disassembling and dismantling the structure before transporting the greenhouse piece by piece to their farm. The next year, the family finalized construction plans for the greenhouse and the attached lean-to building that would house the mechanical systems. Concrete piers were poured and support posts and trusses were set.
The re-construction began in 2016. The Goodenoughs worked in tandem with a construction crew for six months until the facility was completed. They also hired Ron Hammes Refrigeration, a residential and commercial HVAC company based in La Crosse, WI, to handle installation of the heating equipment and piping.
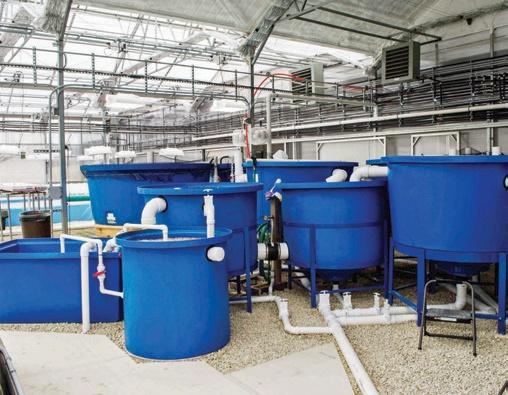
TESTING THE WATERS With the greenhouse ready for operation in November, and the wintry Wisconsin weather setting in, the heating system needed fast installation.
“We require air temperatures of about 70 degrees in the greenhouse year-round and water temperatures between 70 and 75 degrees for the fish and plants to thrive,” said Bonny.
Another important concern was the greenhouse structure, which consisted of lightweight polycarbonate, could collapse under the weight of a heavy snowfall.
“Snow could wreak havoc on our structure and so it was imperative to get the heating system online as soon as possible,” Tim added.
To meet project parameters, James Hammes, presi
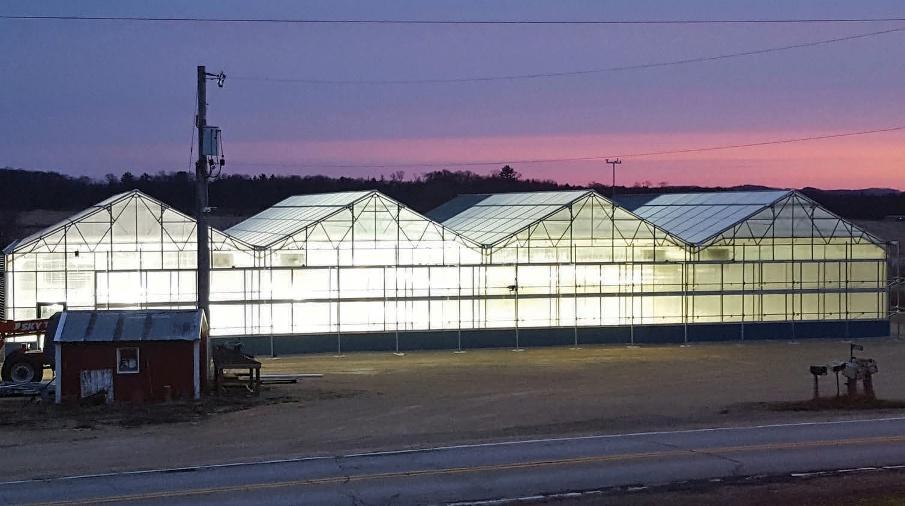
An advanced building-control system uses Evergreen boilers to regulate the growing season for an aquaponics farm.
dent of Ron Hammes Refrigeration, recommended installing four 399 MBH Weil-McLain Evergreen boilers with primary-secondary pumping in a multiple boiler system (MBS). In this configuration, a master boiler controls the modulation and sequencing of boilers on the network to achieve the desired system supply temperature.
“With the automatic sequencing feature, the boilers communicate directly with one another so they sequence themselves and rotate as needed,” explained Hammes. “They operate to optimize energy use and efficiencies. When heat is required, the boilers will stage on one-by-one as needed.”
The Evergreen units were tied to existing heat exchangers on site and installed as part of a Wadsworth system, a building-control solution that monitors external temperature, wind speed and direction, precipitation and humidity, and also internal factors such as temperature and humidity. To maintain conditions, the advanced Wadsworth system cycles the boilers, heat exchangers, and grow lights on and off, and opens and closes vents and shade cloth based on the amount of available sunlight. It is designed to keep humidity and