
12 minute read
Have It All: Quality, Comfort, Efficiency, Cost Savings
by IdeaSoil

An administrative wing added to the Sunshine Health Facilities nursing home is actually a combination of three distinct buildings, all of which are certifi ed by Passive House Institute U.S.
Advertisement
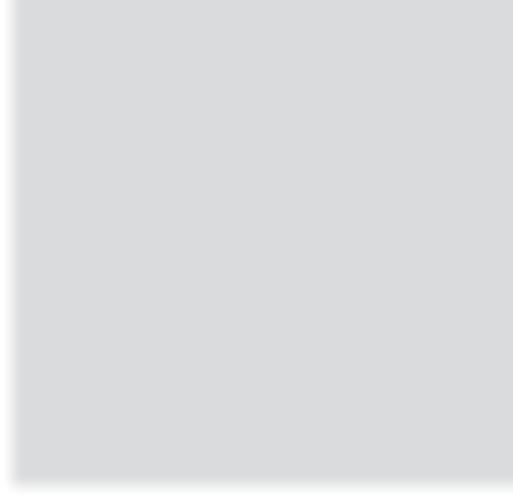

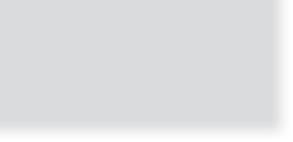

Have It All: Quality, Comfort, Effi ciency, Cost Savings
An architect’s journey through high-performance design as told through two buildings.
When it was time to build a new administration building at Sunshine Health Facilities, Spokane, WA, the construction choice was a no-brainer: PHIUS+ certifi cation through the Passive House Institute U.S., Chicago. Not because the CEO of Sunshine Health Facilities is a tree-hugger, but because of experience on a 58-bed PHIUS+ certifi ed addition to a state licensed boarding home a few years earlier. It was cheaper to build, cheaper to operate, and it delivered superior comfort and healthy indoor air to the occupants.
Founded in 1949, Sunshine Health Facilities was built on the site of one of Spokane’s first universities, Spokane Univ., which closed in 1933. The historical campus brought with it significant challenges, including aging housing susceptible to temperature extremes, a problem for medically fragile residents. The campus includes a nursing home, a boarding home, and several cottages.
The new administrative building, which shares a common atmosphere with the nursing home, is designed to solve an interesting mix of requirements that have cropped up as the company has grown: chiefly, office space, commercial kitchen space, and a commercial laundry facility.
The architect of the project, Sam Rodell, and his partner, Calla Kirkwood, of Sam Rodell Architects AIA, Spokane, have a long history with Sunshine Health, having built, remodeled, or added to all of the buildings over a span of three decades. But until the boarding house addition, design and construction were the old-fashioned way: build to code.
After dipping his toe—and eventually jumping—into
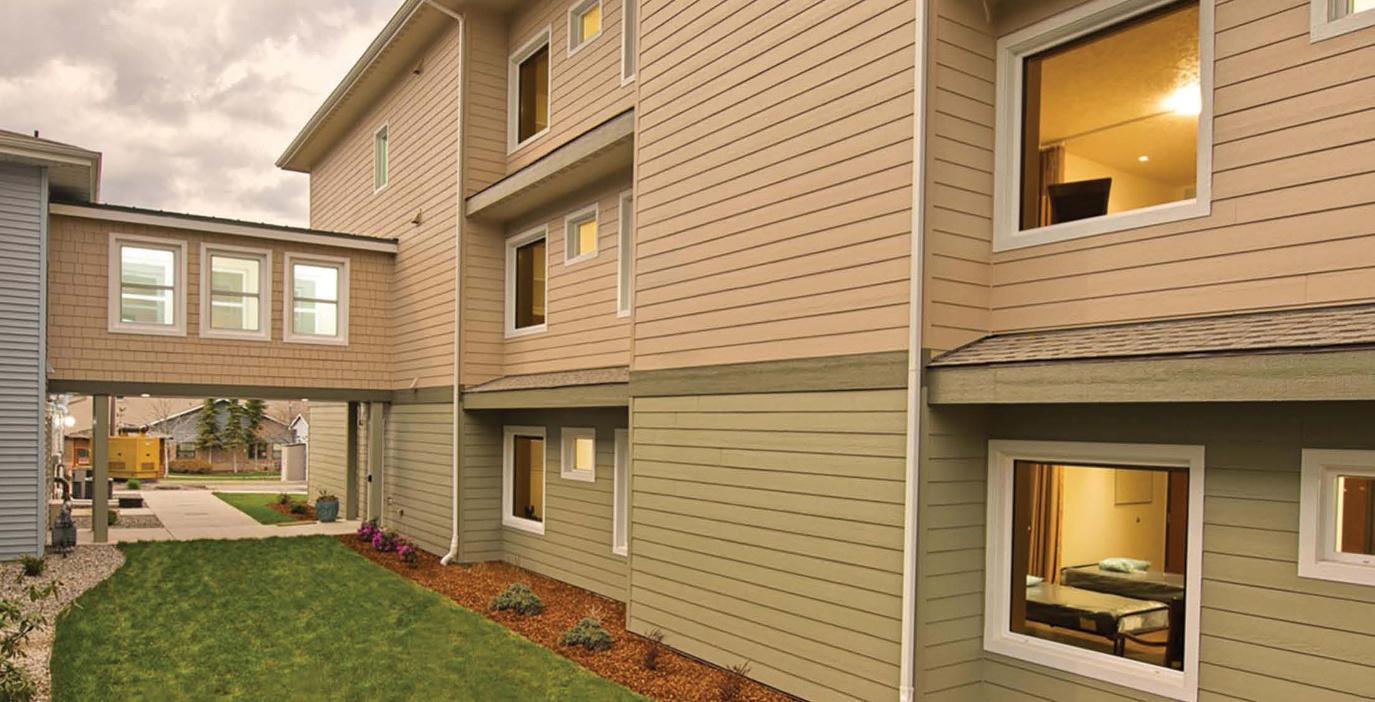
the passive building pool, Rodell suggested modeling the boarding house with 3D energy software that can work side by side with Autodesk Revit software. “Revit has been transformational to our shop, and being able to put the PHIUS software on top of it really puts a lot of power in your hands as a designer.”
Because Sunshine Health Facilities’ business model is based on fixed reimbursements, squeezing utility and value out of capital expenses represents their best opportunity to affect the bottom line. The four-story, 58-bed, 25,000-sq.-ft. boarding home—if built to code minimum—would spend more than $120,000 more each year on utility costs. Building a Net Zero facility represented tremendous low-hanging fruit because it could be done using current construction technology, so Sunshine went for it. The building is pre-wired for solar panels on the roof, which the owner plans to install as funding becomes available. At that point, they could easily have a net-positive building.
More surprising was what it cost to get there: just $134/sq. ft., including soft costs. PHIUS+ construction costs less to build than comparable mainstream construction.
Beyond the financial benefits and energy savings, passive-house construction improves the quality of care and living conditions for the people who live there. Passive-house elements “make a much more comfortable, quieter building...with purified air that eases respiratory problems for our clients,” reported Dr. Nathan Dikes, CEO of Sunshine Health Services.
THE BUSINESS CASE Despite the superior comfort and indoor air quality, the project’s design process was primarily cost driven. Sunshine Health’s income potential is limited and established mainly by outside agencies. Profit margins are extremely narrow, so the design must be as economical as possible—both initial construction and operating costs over time.
Additionally, “The company is very mission driven,” Rodell remarked. “There is more involved than just finances; there are quality-of-life issues at play.” Sunshine has a history of investing in innovative quality-of-life enhancements, so Rodell was not surprised when they embraced passive building.
Rodell didn’t oversell it initially, to manage expectations. The design team modeled a building in WUFI passive-energy modeling software and then modeled it built-to-code to show the owner the differences. Passive House Institute U.S. provided a cost-benefit analysis spreadsheet to paint a more sophisticated financial portrait of the savings over time. In addition to the hard costs of construction and daily operations, the analysis accounted for inflation, interest rates, and rate of change in the cost of energy over time (in Spokane, it is about 2% annually).
“We look at bracketed scenarios, worst-case to best-case, and they can see without needing to have a crystal ball, what the range of possibilities look like,” Rodell explained. The predicted savings were in the six-figures, and the project has delivered more than promised.
After getting so much building for their construction budget, after not paying utility bills for the building, and after experiencing the comfort and indoor environmental quality of the facility, when it came time to build the administration building, there was never a question as to how they’d design it: PHIUS+.
Passive House construction added costs to the building envelope, in the form of thicker walls, better windows, and meticulous detailing, but it lowered other expenses moving forward,particularly with things such as firewalls.
Despite the tradeoffs, the finished cost of the project was lower than a comparable built-to-code building would be because once the building envelope was completed, the remainder of the project went
Sunshine Health Facilities’ resident building has 15-in.-thick walls and can produce more energy than it uses.

Above. Commercial kitchens are “afterburners” for energy use. A lot of heat and moisture is generated that must be exhausted, and these extreme exhaust hoods require calibrated makeup air.
Below. Ozone cold-water washers eliminate water heating and chemical detergents at Sunshine Health Facilities.

faster than usual due to simplified interior mechanical systems, ductwork, and fire dampers.
One of the first questions asked by architects and designers about this kind of construction relates to payback or return on investment (ROI). But ROI presumes an initial investment. Because there was no additional investment beyond what was in the budget, the ROI is either spectacular or irrelevant. “This particular company is not a non-profit, but they act like it,” Rodell said. “So, that wash of funding has allowed them to improve the services they offer their residents.”
DESIGN CHALLENGES The main design challenges for the administration building were the commercial kitchen and the commercial laundry facility. Commercial kitchens are afterburners for energy use—primarily because of the exhaust hoods—but commercial laundry facilities are even worse. The solution for the kitchen exhaust is dedicated makeup-air fans calibrated to the exhaust fans. Maintaining consistent pressure and controlling the airfl ow is a key to passive building.
In the laundry, ozone cold-water washers eliminate heating water from the process and also remove the chemicals from the waste stream.
Another big challenge was that the new administration building had to share a common atmosphere with the nursing home. There’s no way in the world it can ever be made airtight,” Rodell said. The solution was to compartmentalize the air barrier. Three different buildings were built under a single roof. “We let the corridors, the circulation systems, and the stairwells become part of the common atmosphere of the nursing home. You don’t know it, but when you step from the hall into the administrative offices, you are actually stepping into a different environment,” he said.
The kitchen and laundry facilities are a self-contained building; the administrative offices are another. Additional office space for a home-health business is the third building under the common roof. All three share a thermal envelope and a roof, but the interior buildings are compartmentalized with an air-barrier system. “That allowed us to add a passive-house facility onto a non-passive house facility,” Rodell said
CURVE BALL Rodell uses a design scenario from this building that serves as an excellent example of not knowing what you don’t know and the deeply ingrained inertia that litters the path to the high-performance building. In the basement of the boarding home is space where heat pumps use warm air to heat water with cool air as a byproduct. In an adjacent space, computer servers are humming, heating the area and using extra energy to power their internal cooling fans.
The design team initially missed the synergy because “...it is hard to acclimate yourself to understanding how significant little things are inside a high-performance building. Like how the distribution of water lines can challenge you with cooling—or help you with heating.” Intuition, Rodell says, can act as a mask “...before you recognize that those computers can be heating the water, and those showers can be cooling the computers.”
“As an architect, to suddenly learn that everything I knew was wrong,” was surprising, Rodell said. “You can’t unlearn this stuff, and once you’re aware of it, everything around you seems—negligent.” He doesn’t blame negligence on people who don’t know what they don’t know but notes it seems negligent that within the design-and-construction sector, passive building is so foreign to so many. CA
Want more information? To download the information listed below, visit commercialarchitecturemagazine.
com/1711sunshine
Circle 12 on the Reader Service Card.
Visit the Passive House Institute U.S. Get information on WUFI Passive 3.0 software.
Learn about Autodesk Revit software.
EDITORS’ CHOICE Greenguard Gold certification
Certification:
Greenguard Gold For PIR products and QuadCore foam technology Low-VOC products
e company’s products have been certifi ed Greenguard Gold for all current polyisocyanurate foam core insulation (PIR) product sets in addition to products using QuadCore foam technology. Formerly known as Greenguard Children & Schools Certifi cation, the Gold level ensures with the strictest standard of testing that products have low emissions of volatile organic compounds. e certifi cation can be applied to any structure, but has proven particularly important for healthcare facilities and schools where the quality of indoor air is vital to the health of vulnerable occupants.
Kingspan Insulated Panels, DeLand, FL Circle 83 kingspan.com

Waterproofi ng membrane Clay-Tite Bentonite waterproofi ng membrane is a dual-layer product for below-grade use. For vertical and horizontal applications, the material self seals under hydrostatic environments and can be installed in all weather conditions on green or damp surfaces.
W. R. Meadows, Hampshire, IL Circle 84 wrmeadows.com
Self-adhered underlayment Clad-Gard SA-FR with CoreGard technology is a self-adhered, UL Class A, waterproof underlayment for metal roofi ng assemblies. The skid-resistant surface aids installers when working on a sloped roof. With only one-layer application required, there is no primer required to install the product above 40 F.
Firestone Building Products, Indianapolis Circle 85 fi restonebpco.com

800.PAC.CLAD pac-clad.com
Circle 250
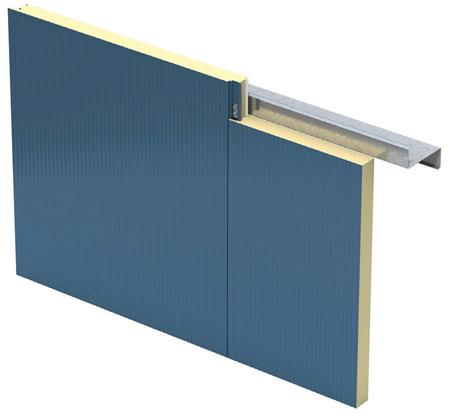


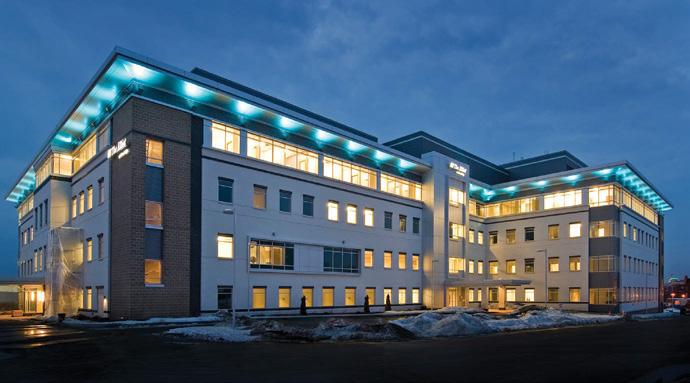
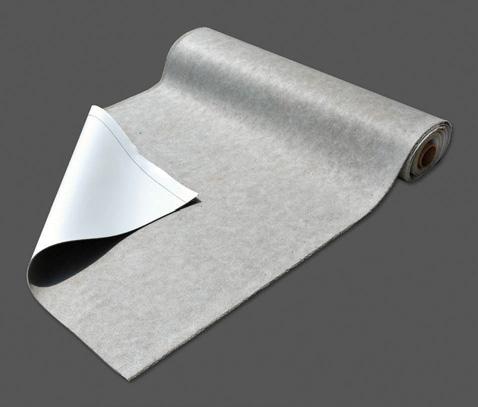
Exterior design systems Aspyre collection combines the company’s Reveal panel system with its Artisan siding. The collection aids design vision across the spectrum of architectural styles from traditional to contemporary and modern. As part of the collection, four siding profi les have been added: Bevel Channel, Square Channel, Shiplap, and Beaded Lap. Reveal is a customizable system of panel, trim, and fastener products.
James Hardie Building Products Inc., Chicago Circle 86 jameshardie.com
Publication Title: COMMERCIAL ARCHITECTURE Publication Number: 0230-77 Filing Date: September 30, 2017 Number of Issues Published Annually: 11 Annual Subscription Price: $24 Complete Mailing Address of Known Office of Publication: 535 Plainfield Road, Suite A, Willowbrook, IL 60527 Contact Person: Glen Gudino, President/CEO; Telephone: 630-325-2497 Complete Mailing Address of Headquarters or General Business Office of Publisher: Applied Technology Media, 535 Plainfield Road, Suite A, Willowbrook, IL 60527 Full Names and Complete Mailing Addresses of Publisher, Editor, and Managing Editor: Phil Saran, Publisher; Gary L. Parr, Editor; 535 Plainfield Road, Suite A, Willowbrook, IL 60527 Owner: Glen Gudino; Applied Technology Media, 535 Plainfield Road, Suite A, Willowbrook, IL 60527 Known bondholders, mortgagees, and other security holders owning or holding 1 percent or more of total amount of bonds, mortgages, or other securities: None Issue data for circulation data below: September 2017
Rubber + Vinyl Flooring Systems


Made in the U.S.A.
flexcofloors.com • 1.800.633.3151
CIRCLE 215
STATEMENT OF OWNERSHIP, MANAGEMENT, AND CIRCULATION
Extent and nature of circulation:
Total no. copies Paid and/or requested circulation (1) Paid/Requested Outside County Mail Subscriptions Stated on Form 3541 (2) Paid In-County Subscriptions Stated on Form 3541 (3) Sales Through Dealers and Carriers, Street Vendors, Counter Sales, and Other Non-USPS Paid Distribution (4) Other Classes Mailed Through the USPS Total paid and/or requested circulation Free distribution by mail (1) Outside-County as stated on Form 3541 (2) In-County as Stated on Form 3541 (3) Other Classes Mailed Through the USPS Free distribution outside the mail Total free distribution Total distribution Copies not distributed Total Percent paid and/or requested circulation Requested and Paid Electronic Copies Total Requested and Paid Print Copies + Requested Paid Electronic Copies Total Requested Copy Distribution + Requested/Paid Electronic Copies Percent Paid and/or Requested Circulation (Both Print & Electronic Copies) Avg. no. copies each issue during preceding 12 months 43,797
31,003 0
0 0 31,003
11,404 0 0 223 11,627 42,630 1,167 43,797 72.73% 5,739 36,742 48,146 76.31% No. copies of single issue published nearest filing date 43,980
30,889 0
0 0 30,889
11,208 0 0 400 11,608 42,497 1,483 43,980 72.69% 5,449 36,338 47,946 75.79%
I certify that all information furnished on this form is true and complete. I understand that anyone who furnishes false or misleading information on this form or who omits material or information requested on the form may be subject to criminal sanctions (including fines and imprisonment) and/or civil sanctions (including civil penalties). (signed) Glen Gudino, Owner