
7 minute read
Perimeter Fire Barriers Are Vital
by IdeaSoil
integral part of the culinary experience.”
The Noma kitchen is designed like a panopticon with an oversized hood hovering over the chefs. From here, the chefs can oversee the entire kitchen and guest areas, including the dining room and adjacent private dining room. These spaces are made of stacked timber planks that resemble neatly piled wood at a lumberyard.
Advertisement
A large skylight and an expansive set of windows that slide to reveal the outdoor permagarden allow restaurant guests to truly sense all of the seasons and the restaurant’s natural surrounds. Outside, three freestanding glass houses provide the restaurant’s garden, test kitchen, and bakery.
Guests have the opportunity to walk through each of the surrounding buildings and to experience a variety of Nordic materials and building techniques. The barbecue is a giant walk-in hut, and the lounge looks and feels like a giant, cozy fireplace made entirely of brick inside and out. In between the individual buildings are spaces enclosed with glass, allowing guests and the
The new Noma dissolves the traditional idea of a restaurant into its constituent parts and reassembles them in a way that puts the chefs at the heart of it all. All photos: Rasmus Hjortshoj, V2com
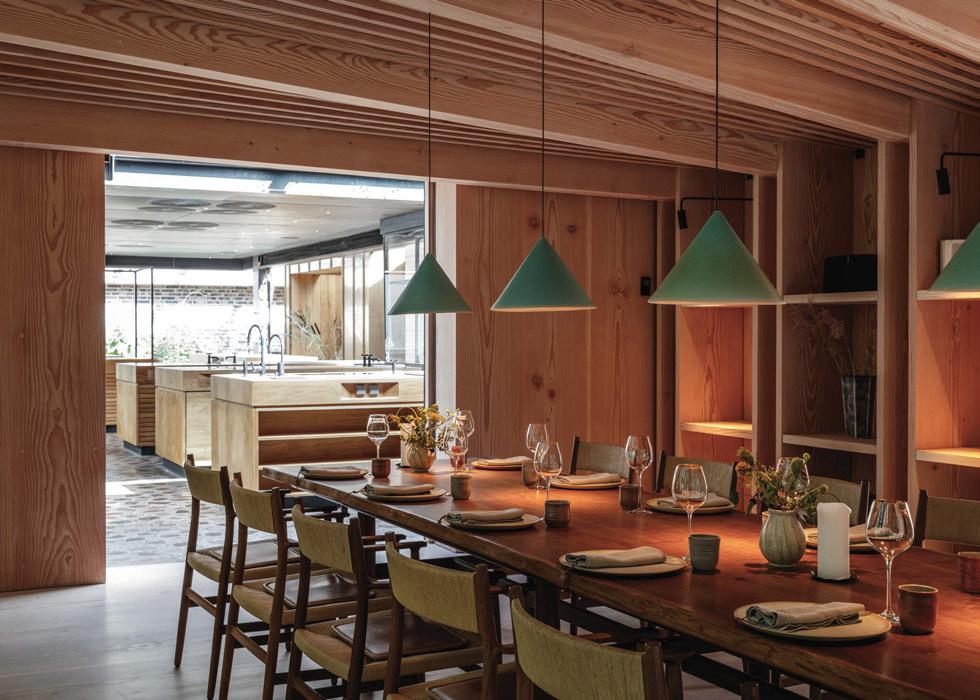
Central to BIG’s design was the idea of changing the restaurant’s individual functions and organizing them as a collection of separate, yet connected, buildings. A total of eleven spaces, each tailored to their specifi c needs, are densely clustered around the restaurant’s heart: the kitchen.
Situated between two lakes and within the community of Christiania, Noma is built on the site of a protected ex-military warehouse once used to store mines for the Royal Danish Navy.
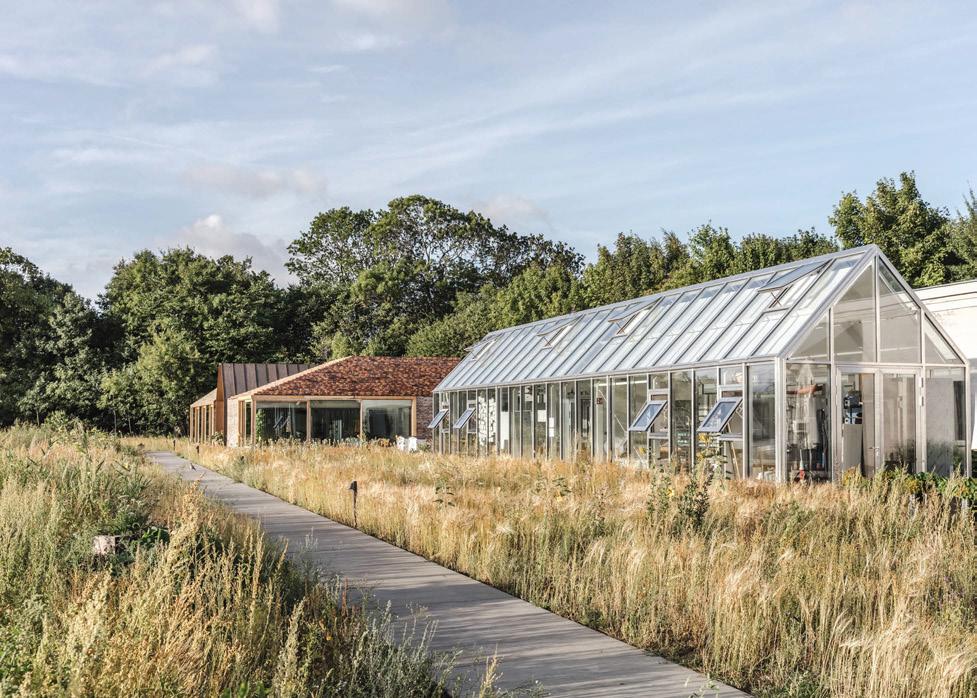
Each building within the building is connected by glass-covered paths that allow chefs and guests to follow the changes in weather, daylight, and seasons—making the natural environment an integral part of the culinary experience.
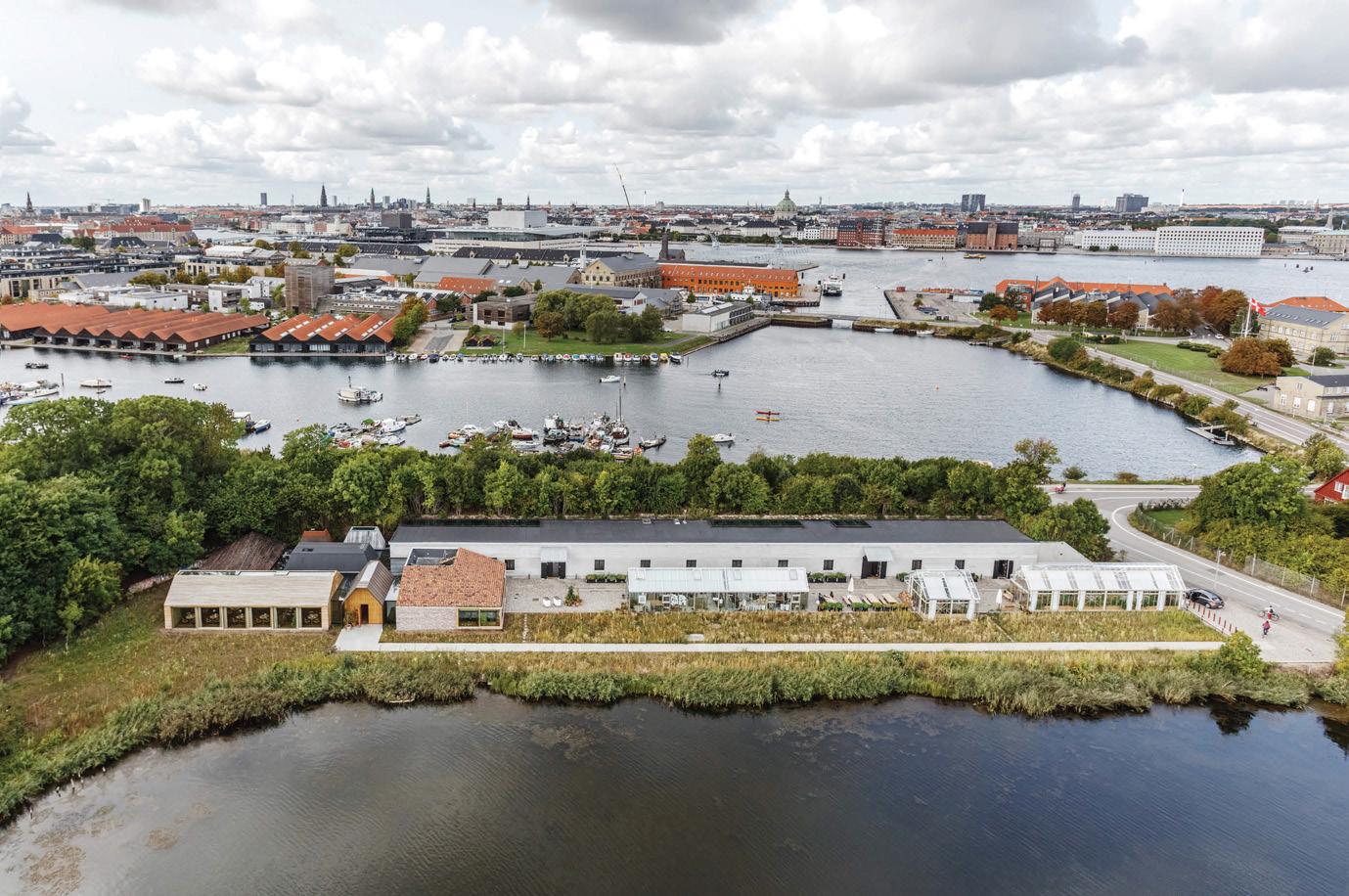
Noma team to roam in constant connection with nature and the changing seasons.
The historic 328-ft.-long single-story warehouse completes the circle of buildings surrounding the kitchen. BIG designers preserved the raw shell of the warehouse’s concrete and inserted a massive wooden shelf for storage and display. All of the back-of-house functions are located here, including the prep kitchen, fermentation labs, fish tanks, terrarium, ant farm, and breakout areas for staff. CA
Want more information? The items listed below are linked at
commercialarchitecturemagazine.com/ 1811big.
Bjarke Ingels Group (BIG), big.dk/#projects Noma, noma.dk
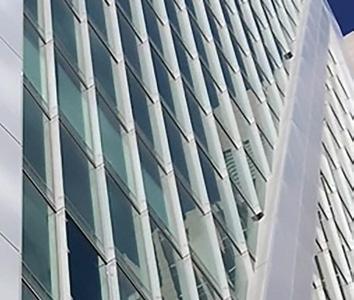
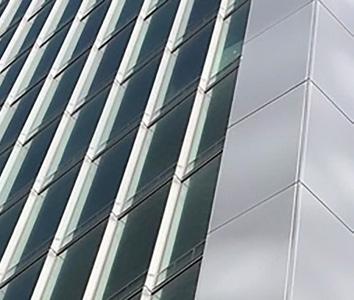

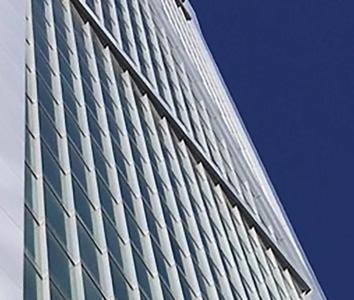

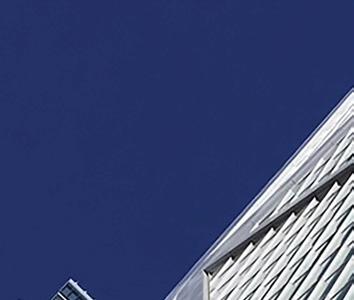

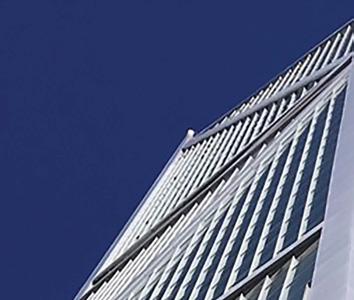
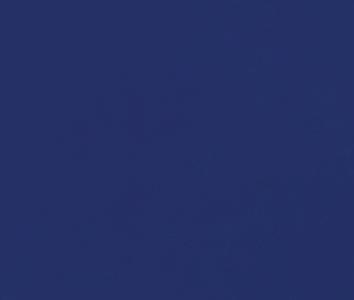
The unique design of 181 Fremont required every fl oor to be evaluated in terms of the perimeter fi re-containment barrier assembly and use of a proprietary mechanical fastening assembly.
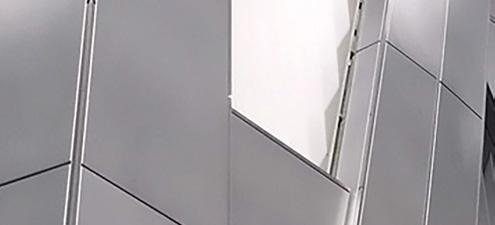
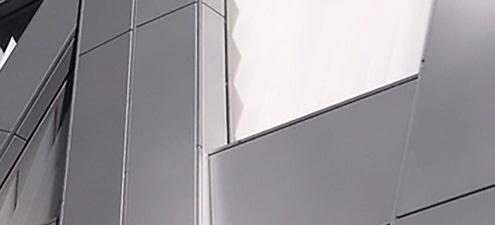



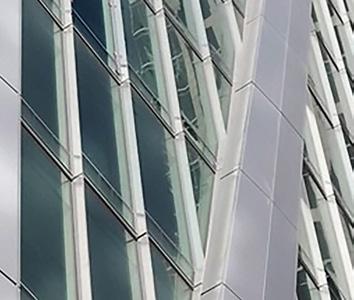
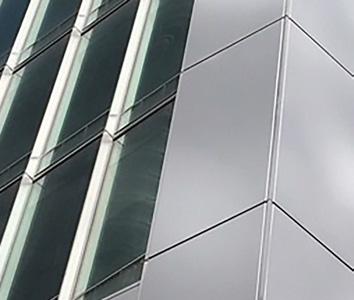
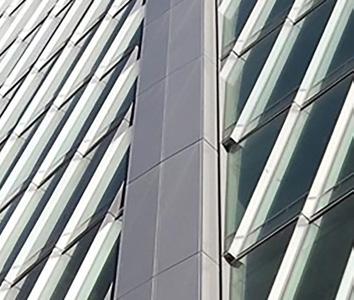
Three San Francisco Transbay neighborhood buildings support passive life safety.
In a city famous for its beautiful light, the deadliest fi restorms in California’s state history brought an eerie post-apocalyptic shade of orange to San Francisco’s skies in early 2018. High wind and hot temperatures from Northern California wildfi res cast many parts of the area in hazy, dusk-like shades of orange and red. Because fi re has been a perennial threat to San Francisco since the city’s earliest days, the building codes that govern perimeter fi re barriers are particularly rigorous.
Three new skyscrapers adding beauty and interest to San Francisco’s skyline—181 Fremont, Park Tower at Transbay, and Salesforce Tower—are supporting life safety for their occupants through carefully planned perimeter fire barriers. Simply defined, the perimeter fire-barrier system is a compilation of installed materials, that when tested to ASTM E2307 conditions (ASTM International, West Conshohocken, PA, “Standard Test Method for Determining Fire Resistance of Perimeter Fire Barriers Using the Intermediate-Scale, Multi-Story Test Apparatus”) must remain securely in place for the time period equal to the fire-resistance of the floor assembly.
While building-code requirements are straight forward, the unique design elements that contribute to a building’s architectural aesthetic typically present challenges when it comes to specifying materials for the perimeter fire-containment system. Various design elements such as curved spandrels, angular symmetry, and complex curtain walls in the three buildings, presented unique concerns for team members collaborating on the perimeter fire-containment systems.
However, not every building material in the perimeter fire-containment system was difficult to specify. All three buildings contain Thermafiber,
Wabash, IN, Firespan and Thermafiber Safing mineral-wool insulation to support passive life-safety systems. Fire tested to ASTM E119, Thermafiber has been shown to withstand temperatures well above 2000 F.
Another life-safety consideration was the height of all three buildings.
Sadly, skyscrapers around the world have been the target of terrorist attacks.
Addressing potential liability risk that could arise in the event of a terrorist attack was an important consideration in selecting the insulating material used. Using products certified by The U.S. Department of Homeland Security’s “Safety Act” designation provides architects with protection against liability related to acts of terrorism. The Safety Act also protects several related parties involved in perimeter fire-containment systems including curtain-wall manufacturers and fire-stopping contractors.
181 FREMONT Completed in 2018, the mixed-use skyscraper at 181 Fremont, towering 802 ft. into San Francisco’s skyline, houses offi ce space on lower levels with luxury condominiums above. The building’s intriguing curtainwall, featuring a complex lap-shingle profi le and large, diagonal columns, presents a unique angle of the façade at every intersection. The complexity of the curtainwall and geometry of the building necessitated a highly customized approach to the perimeter fi re-containment assembly system.
Thermafiber Insolutions, a Thermafiber consulting service, collaborated with curtain-wall manufacturer and contractor Benson Industries, Portland, OR, to secure the third-party engineering judgments required to address San Francisco’s building codes, while honoring the building’s unique geometry. 181 Fremont’s intersecting angles required a robust anchoring system to attach the insulation to the curtain wall. In addition, the differentiated spaces between where the wall and edge of the floor slab intersect on each floor presented the team with additional challenges to curtail leapfrog spread of fire up the sides of the building. Section 715.4 of the International Building Code requires that the void created at the intersection of a floor/ceiling assembly and an exterior curtain-wall assembly be protected. The unique design of 181 Fremont required each and every floor to be evaluated in terms of the perimeter fire-containment barrier assembly and a proprietary mechanical fastening assembly: Thermafiber Impasse insulation hanger system.
From a sustainability perspective, the 70% minimum recycled content in the insulation products contributed valuable credits toward a LEED-Platinum-targeted energy label.
PARK TOWER AT TRANSBAY Also completed in 2018, the 43-fl oor offi ce building, Park Tower at Transbay, pre-certifi ed for LEED Gold, presented an unusual challenge for a West Coast skyscraper. The building’s design featured a back-pan assembly installed on the inside surface of the spandrel façade. Back pans are much more widely used in the Midwest and Eastern regions of the U.S. to address moisture-management challenges. Typically, the choice of moisturemanagement systems is left to mechanical engineers and the various analysts who address the thermal, vapor, and air movement aspects of a building. However, use of a back pan was important to preserve the architect’s design and ensure insulation would not be visible in some parts of the building.
As Thermafiber Insolutions and Benson Industries evaluated options for perimeter fire-containment assemblies, it became clear that only a few assemblies for back pans were listed. Among the options available, none would meet the construction details required for the building’s facade. While the available options could be adapted to work within the design of Park Tower at Transbay, doing so would be cost-prohibitive for the façade manufacturer.
Faced with this dilemma, the teams donated materials and expertise to develop an alternative assembly design that would comply with building