
16 minute read
Landmarked Building Is A Window-Man’s Dream
by IdeaSoil
Replacing nearly 5,000 windows required first winning approval of the New York Landmarks Preservation Commission.
When RXR Realty, New York, acquired the Starrett-Lehigh building, which occupies an entire block on Manhattan’s western edge, the original steel windows installed for its opening in 1931, were still in place. Given the building’s roster of high-end tenants—including Martha Stewart Living Omnimedia, Club Monaco US, Tommy Hilfiger USA, Scholastic Corp., and McGarryBowen advertising agency—RXR prioritized a window upgrade.
Advertisement
It was to be no small task. At 2.3 million sq. ft., the Starrett-Lehigh building is larger than the Empire State Building, which opened less than half a year earlier and stands 83 stories taller.
Starrett-Lehigh had to be enormous. It was originally built, according to its website, as “a novel solution to freight distribution. The Starrett-Lehigh freight terminal, warehouse, and office building was built directly over the Lehigh Valley Railroad Co.’s working freight yard and adjacent to the commercial westside piers. Its unique construction offered railway freight cars access from the westside car float pier directly into the building for unloading and storage.”
Sheer size wasn’t Starrett-Lehigh’s only distinguishing trait. The building features continuous bands of horizontal windows, each curving at the inside and outside corners of the building. It has nearly 5,000 windows, with the typical window standing 5 ft. wide and 9 ft. high.
Left. The Starrett-Lehigh building features continuous bands of horizontal windows, each curving at the inside and outside corners of the building. All told, it has nearly 5,000 windows, with the typical window standing 5 ft. wide and 9 ft. high. Photography: Lenny Casper Photography
Right. The decision to replace or restore the existing windows had to be approved by the New York Landmarks Preservation Commission (LPC), which, among other duties, regulates the replacement of windows on individual landmarks or within historic districts in New York City.
Placed end-to-end, the windows would extend eight miles.
Each of the windows in those bands features an operable vent, the placement of which alternates vertically from window to window, creating a “bouncing ball” effect, also known as “floating vents,” across each floor and façade.
That operable vent, said Michele Boddewyn, AIA, president of Boddewyn Gaynor Architects (BGA), New York, the firm RXR contacted to manage the architectural investigation of the massive project, would become “the Rubik’s Cube” of the Starrett-Lehigh window upgrade. BGA’s senior project manager Michael Ankuda, AIA, led the team. Because of the scope of the job, Ankuda was coy as he approached various window manufacturers. “We were concerned that if the location was identified, everyone would think that they had a product meeting our needs,” he said. “Our first task was to identify those manufacturers interested in supplying eight or 10 units.”
Maurice Benor laughed as he recalled Ankuda’s initial phone call. Benor is the New York City sales representative for Graham Architectural Products, York, PA, a manufacturer of historic replica windows. Ankuda, who had worked with Benor and Graham previously, said simply, “Maurice, there’s a job, it has windows on it. Are you interested?”
Benor had no idea the “job” referred to StarrettLehigh, the building he calls “the window-man’s dream.” But Ankuda’s understated approach made sense. “Michael wanted people truly interested in producing a product that would closely match the existing steel windows. He wanted realistic numbers from people who were going to work with him and not lowball him,” Benor explained.
Ankuda researched several window manufacturers to see if they could match the existing steel-window profiles. He gave them all the same information and they in turn submitted drawings and details. Ankuda then reviewed their profiles and sightlines with the owners. Graham emerged the winner, but the journey was only beginning.
APPROVAL NEEDED The decision to replace or restore the existing windows would have to be approved by the New York Landmarks Preservation Commission (LPC), which, among other duties, regulates the replacement of windows on individual landmarks or within historic districts in New York City. Starrett-Lehigh was declared a New York City landmark in 1986 and is part of the West Chelsea Historic District, designated in 2008.
The bar for approval was extremely high. How high? New York City’s Historic Districts Council (HDC) organizes neighborhood residents in efforts to gain protection for their communities and assists property owners through the LPC’s processes. HDC called the StarrettLehigh project “the window job of the year (if not the century),” adding, “if any windows deserve an aboveand-beyond restoration or specially made replacements, it is these.”
Bill Wilder, Graham’s director of technical sales, said, “Landmarks didn’t want to see new windows. They wanted the old windows to be restored. But the windows leaked a lot of air. They weren’t very thermally efficient from a U-value standpoint or an air-infiltration standpoint, and the windows did very little to reduce the solar heat gain. So you had significant seasonal temperature fluctuations, which would increase heating demands in the winter and air conditioning loads in the summer. And, the fact was, restoration wouldn’t improve the ther
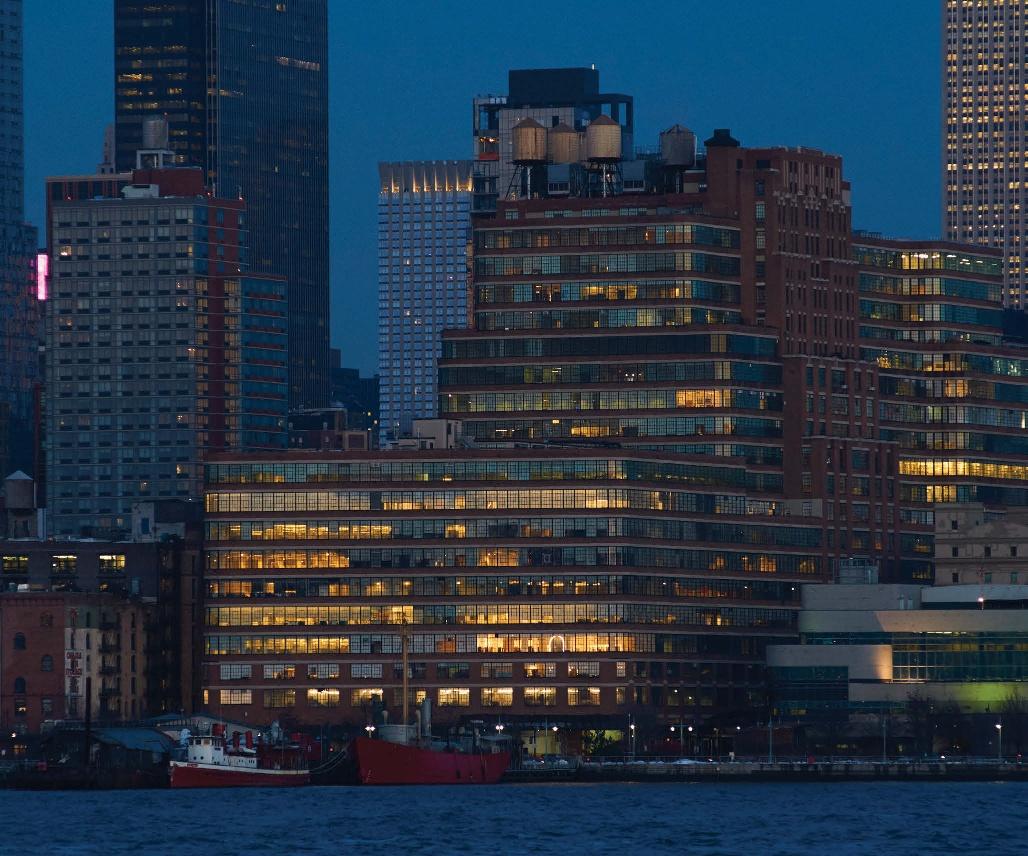
mal situation in the building.”
However, it wasn’t enough to say that. Ankuda’s team had to prove it.
Doing so began with a 5,000-window audit. They evaluated each window, checking the glass and the hardware, testing functionality, and looking for rust in the frame and supporting frame. In many of the openings, they discovered rust, an indication that water damage was occurring in the building.
They also had a certified lab field test a few of the original windows before and after refurbishment.
The result? The restored windows leaked air at least 15 times more per square foot than Graham’s proposed window. When tested for water infiltration, Boddewyn said, the restored windows “failed miserably.”
“The building was taking on water damage due to the windows,” Wilder explained. “Painting them, re-glazing them, re-puttying, re-caulking them, adding weather stripping didn’t stop that. I’ve seen that in other buildings, too; even after you refurbish them, the old steel windows don’t stop wind-driven water from coming in. The reality is, they just leak.”
Additional tests were performed. An acoustic consultant determined new windows would reduce noise infiltration by 50%. That was important, too, since Bod-
Satisfying Review Boards
Satisfying the critical eye of review boards adds an extra degree of diffi culty to any job. Review boards exist to protect their jurisdiction’s historic resources and character through the preservation, protection, and development of historic structures, sites, and
areas.
So, yes, they want windows that offer contemporary thermal performance, but they also want windows that match the ones they are replacing. Here are some insights Graham Architectural Products’ Bill Wilder has gained over the years. • Different review boards have different priorities.
More than anything, Wilder said, national and state boards want to preserve buildings. They will sometimes make concessions if failure to do so will prevent a building from being saved.
Municipal review boards are often more unyielding. “And that’s not a bad thing,” Wilder said. “They’re the ones who live in the neighborhood. They see it every day. When you have a building that’s very signifi cant to an area, such as Starrett-Lehigh, it should be held to very demanding criteria.” • Be prepared to explore all options.
When it comes to windows, owners of historic properties have three alternatives: repair, retrofi t, or replace. The ultimate decision, however, is sometimes made by the historic review board and not the owner.
According to Wilder, the fi rst priority of any review board is, “Can the original windows be saved?” For Starrett-Lehigh, answering this question required a visual survey of each of the 5,000 windows. It required certifi ed lab tests of a sample of windows before and after refurbishing. It required mockups, reports, and hearings.
When the Landmarks Preservation Commission fi nally agreed that, yes, refurbishing was not practical, it then wanted to know if the windows could be replaced in-kind. That meant fi nding a source of new steel windows capable of matching the original windows’ sightlines. Cost and thermal performance eliminated this option, said Michele Boddewyn, AIA, president of Boddewyn Gaynor Architects. Replacement became the only realistic alternative. • Don’t go it alone.
Experience in dealing with review boards is vital. Historic consultants Higgins Quasebarth & Partners, New York, played an important role in helping Starrett-Lehigh navigate the review process.
Review boards appreciate expert assistance, too. In its Fact Sheet titled, “Repairing, Retrofi tting and Replacing Windows,” the New York City Landmarks Preservation Commission says, “Consider hiring architects, suppliers and/or contractors with experience working on historic buildings to come up with the best approach when replacing windows.” • Research the rules.
Projects seeking state or federal tax credits face deadlines for completion. Since Starrett-Lehigh was dealing with the New York City Landmarks Preservation Commission, a municipal approval board, it had no hard deadline.
“Researching the rules” applies to the regional code, too. Regional codes often specify thermal performance. They can require you to meet a certain U-value or ensure a certain amount of fresh air.
As an individual landmark, Boddewyn said Starrett-Lehigh was exempt from complying with the local energy codes. “However,” she added, “from a property-management and also tenant-comfort point of view, it was important that the custom window design of the insulated glass unit (IGU), the argon gas, and the low-e coating met energy-code requirements. This has resulted in a dramatic reduction of the winter heating costs.” dewyn said in one of the lower-floor conference rooms, conversation depended on the rhythms of a nearby traffic light. When the light was green, traffic roared and conversation stopped. When the light turned red, traffic slowed and conversation resumed.
RXR hired a separate firm to conduct an energy-model analysis for the building. Despite using conservative estimates for a replacement window’s performance data, the firm projected annual savings (at 2012 energy rates) to be around $1.2 million. Clearly, replacement was the preferred option. LPC agreed.
FINDING A SOLUTION From the beginning, RXR was hoping to complete the project with an off-the-shelf solution. For the presentation to the LPC, Graham drew up details and created a fullsize mockup of the 6700 Series window originally endorsed by the owners.
Although the window met all LPC criteria, the LPC rejected it, sighting the aforementioned Rubik’s Cube—the floating vent and supporting muntins were too thick.
In the ensuing give-and-take, LPC offered some helpful leeway. As Wilder explained, “The original vents were center pivot on the horizontal axis, which does not perform well for air and water. And the LPC quickly realized no one could do that horizontal pivot. So they agreed to let us hinge the new vent from the top as an awning-type vent. While the concession is a typical step in the process, I think it was a bigger deal on this project since the windows and the vents were really the critical defining feature of the exterior façade.”
Meanwhile, it was around this time that Wilder was discussing windows with National Park Service, Washington, representatives. They indicated there were countless old warehouse-type buildings across the United States with windows similar to Starrett-Lehigh’s. “They kind of made a point,” he said. “Nobody had done a good job of recreating that floating vent in the old steel, true-divided windows found in all these old factories and warehouses. If you were going to devote resources to developing a window, that would be an area where they felt there was a need.”
That was fresh in his mind when news of the rejection came down. “Maurice and I had a conversation and I remember saying, ‘You know what? This is an opportunity.’ And he agreed. There was that little voice in the back of our heads, like, this is the type of job that can pay for the R&D for a new product that is unique to the industry.”
“After the first rejection from LPC, we knew the project was shifting towards a custom product,” Ankuda said. “Time and cost implications entered the equation. It took some time for Graham to sort it out amongst themselves, but they committed to R&D a custom matching unit.”
DIFFERENT THOUGHT PROCESS A number of stars aligned over Graham’s York, PA, headquarters. The company embraced what Wilder called, “a whole different thought process of designing and manufacturing.” Included was the purchase of high-end European CNC (computer numerical control) equipment and the embrace of a CNC-based system.
The company then took the window it developed for 525@Vine, a National Park Service job in Winston-Salem, NC, and reengineered it, using its new philosophy and technology to create a radical design for narrow-sightline true muntins, giving them the strength necessary to support the floating vent. That breakthrough allowed Graham to replicate and incorporate the floating vent without altering the look of the small horizontal muntin bars that supported it.
Development and certification took more than a year, but when Graham unveiled its breakthrough SR6700—with the narrow sightlines and floating-vent appearance that are the signature of the window-centric building—approval followed shortly thereafter.
“Our design guys really rose to the occasion,” Wilder said. “We had to step away from what we had traditionally done. Then we had to take some things that were
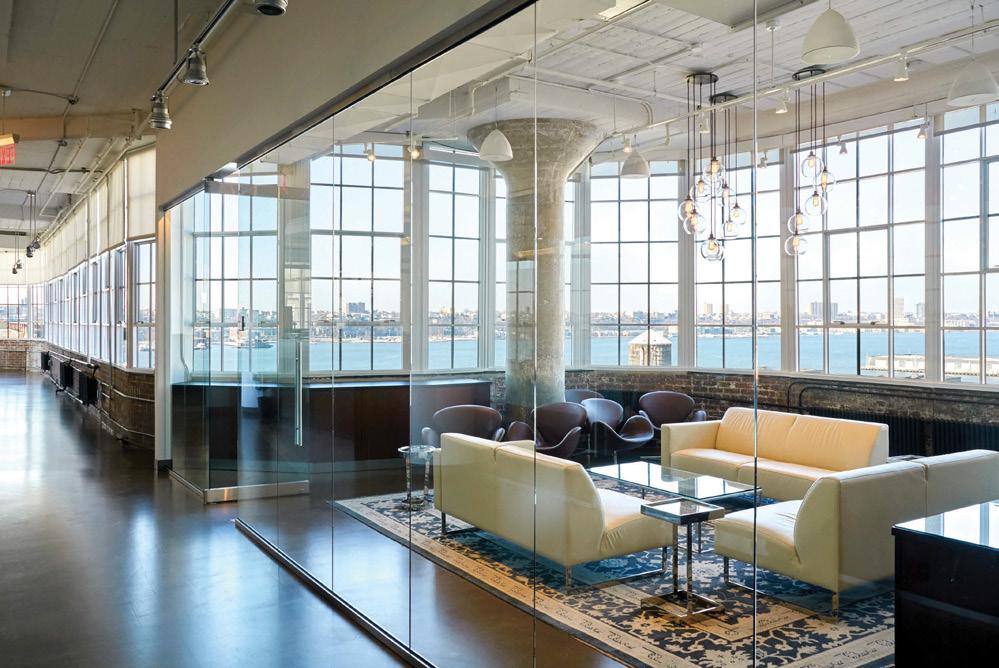
GOOD BETTER BEST
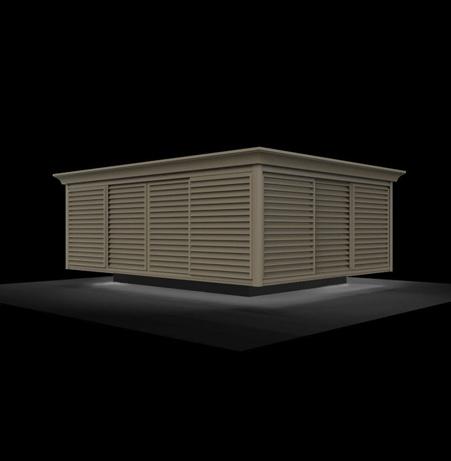

EXACTLY.
Each of the windows in the horizontal bands features an operable vent, the placement of which alternates vertically from window to window, creating a “bouncing ball” effect, also known as “fl oating vents,” across each fl oor and façade.
already being done in the industry and add some of our own ideas that were totally new. And we created a window.”
Additional hurdles awaited.
As Wilder explained, “There is a serpentine pattern to the windows on the setbacks, and replicating all the mullions was a particular challenge. Every corner, every angle, had to be custom-made and matched.” Plus, the building was occupied, making installation a challenge. Since the windows had to be removed and replaced from the interior of the building, nighttime installations optimized the process and minimized tenant inconvenience.
Although it was a long road with periods of uncertainty, Boddewyn remembers a winter’s day when Ankuda viewed the building from about eight blocks away. To his delight, the replacement windows in the upper ten floors were difficult to distinguish from the originals still in place on the bottom floors. That, Boddewyn said, was his “done good” moment.
The project is expected to receive a 2019 Lucy G. Moses Award from the New York Landmarks Conservancy, an organization that has led the effort to preserve and protect New York City’s architectural legacy for more than 45 years. The Moses Awards, considered “the Oscars of Preservation,” are the conservancy’s highest honors for outstanding preservation efforts.
“We’re all proud of what the team has achieved at Starrett-Lehigh,” said Marcelo Renzi, senior vice president, design and construction, at RXR Realty. “It took us a long time to get here, but what a change it has made. I want to thank the BGA and the Graham teams for all their hard work and commitment. We could not have been successful without them.” CA
Want more information from Graham Architectural Products (grahamwindows.com)? Circle 5 on the Reader Service Card.
Sources listed below are linked at commercialarchitecturemagazine.com/1903graham.
• RXR Realty, rxrrealty.com • Starrett-Lehigh Building, starrett-lehigh.com • Boddewyn Gaynor Architects, boddewyngaynorarchitects.com • New York Landmarks Preservation Commission,
www1.nyc.gov/site/lpc/index.page
• New York City’s Historic Districts Council (HDC), hdc.org • New York Landmarks Conservancy, nylandmarks.org • National Park Service,
nps.gov/subjects/historicpreservation/index.htm
• Higgins Quasebarth & Partners, hqpreservation.com
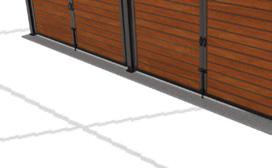
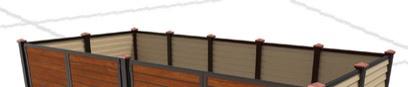

Customized acoustic glass
Sanctuary Glass:
Provides acoustic performance Sound-absorbing lamination 44 STC rating
Sanctuary Glass provides acoustic performance through a combination of wide, asymmetrical spacing between panes, sound-absorbing lamination, and thick glass panes in diff ering widths. Glazing, combined with the tightly sealed and thermally broken window design, provides products with sound protection, energy performance, and visible transmittance. e glass confi guration can be used with any of the company’s product lines. ird-party-testing results reach 44 STC (Sound Transmission Class) and 37 OITC (Outside Inside Transmission Class).
Zola Windows, Steamboat Springs, CO Circle 78 zolawindows.com
Hardware options Two hardware options coordinate with the VistaLuxe window collection. Ashlar handle for casements and awnings has a square silhouette. The crank-out handle is available in white, satin nickel, rustic umber, and matte black. The Dallas handle-set lever for inswing entrance doors is brushed gold and escutcheon, turn knob, and key cylinder are matte black.
Kolbe Windows & Doors, Wausau, WI Circle 79 kolbewindows.com

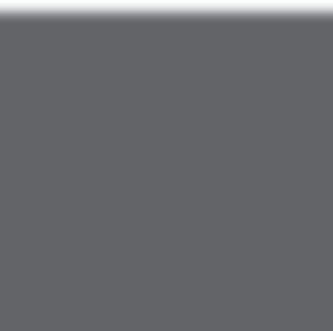

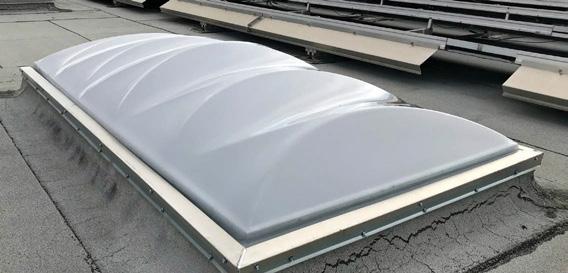
Skylight conversion kit The Capped Conversion Kit converts old, capless skylights to a capped system. The kit includes a universal-fi tting polycarbonate dome, custom-sized aluminum cap built specifi - cally for the unit or smoke-vent make and model, and Tek screws with EPDM gaskets. The product is said to eliminate leaking and cracking. There are no exposed edges.
Skyco Skylights, Costa Mesa, CA Circle 81 skycoskylights.com
Door control Custom door-control systems open or close doors for traffi c fl ow, with operation controlled from inside or out. Most systems include an emergency call plate and fail-safe to lock or unlock doors in a system failure or emergency.
DeltrexUSA, Bronx, NY Circle 80 deltrexusa.com


Mortise lock for sliding doors The PD95 mortise lock for sliding doors has a locking entry function that provides a quick emergency exit to help meet code compliance. The lock’s design features a solid-brass deadbolt with a 1-in. throw, self-retracting hook with a non-marring latch bolt, 2-mm-thick faceplate in either stainless steel or brass, and trim-locking device for emergency egress. The deadbolt automatically releases with a push of the inner handle in case of emergencies, and the ADA thumb turn helps meet code compliance for commercial projects such as entryways, patios, and classrooms.
INOX, Sacramento, CA Circle 82 inoxproducts.com

Expanded color options Expanded exterior color options for the company’s 1620 single-hung and 1630 single-slider product lines now include bronze and black exterior laminates. Available only with white interiors, each can be also ordered with the company’s fi n, fi nless, and fl ange frame profi les to support new construction and replacement projects. Available in two- and three-lite confi gurations, each also includes a DP-50 option to enhance coastal-area performances.
MI Windows and Doors, Gratz, PA Circle 83 miwindows.com

Dynamic glass SageGlass Harmony dynamic glass is a glazing solution said to enhance building-occupant experience by maximizing visual and thermal comfort. The glass provides daylight, heat, and glare management while maintaining a natural and seamless connection to the outdoors. The product uses a gradual in-pane tint transition from fully clear to fully tinted.
Saint-Gobain, Faribault, MN Circle 84 sageglass.com
Pilkington Spacia™
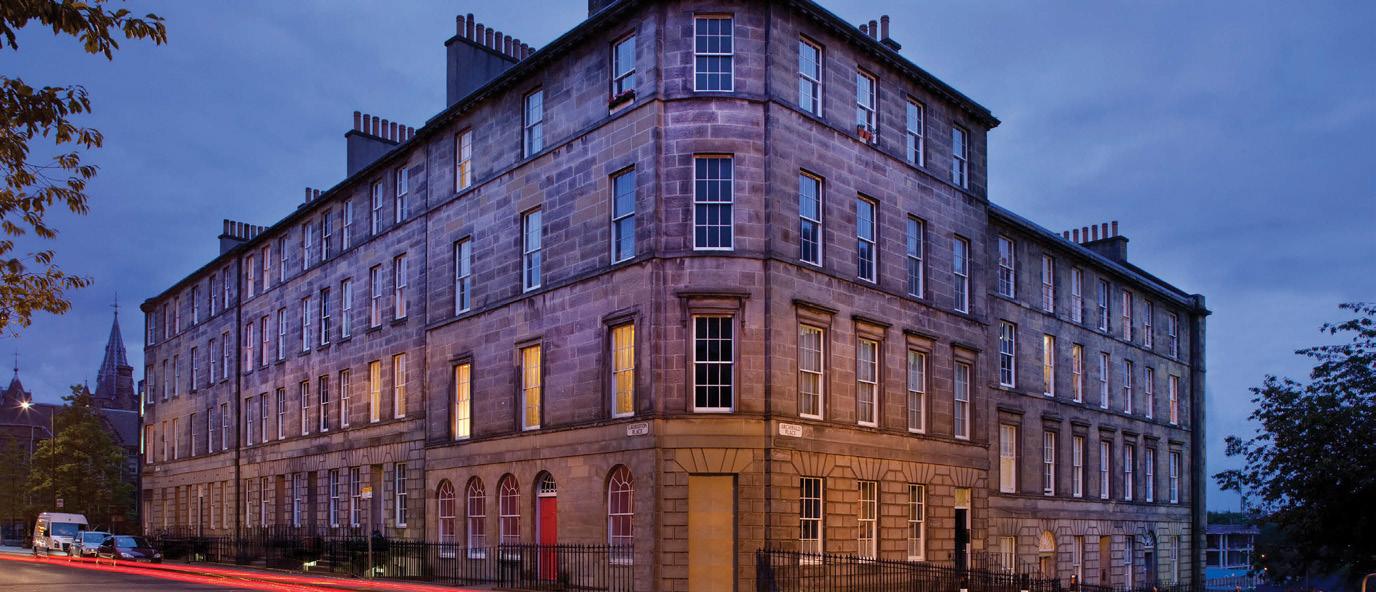
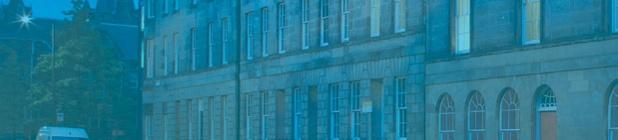
Vacuum Insulated Glazing
The thermal performance of conventional double glazing in the same thickness as a single pane for historical restoration.