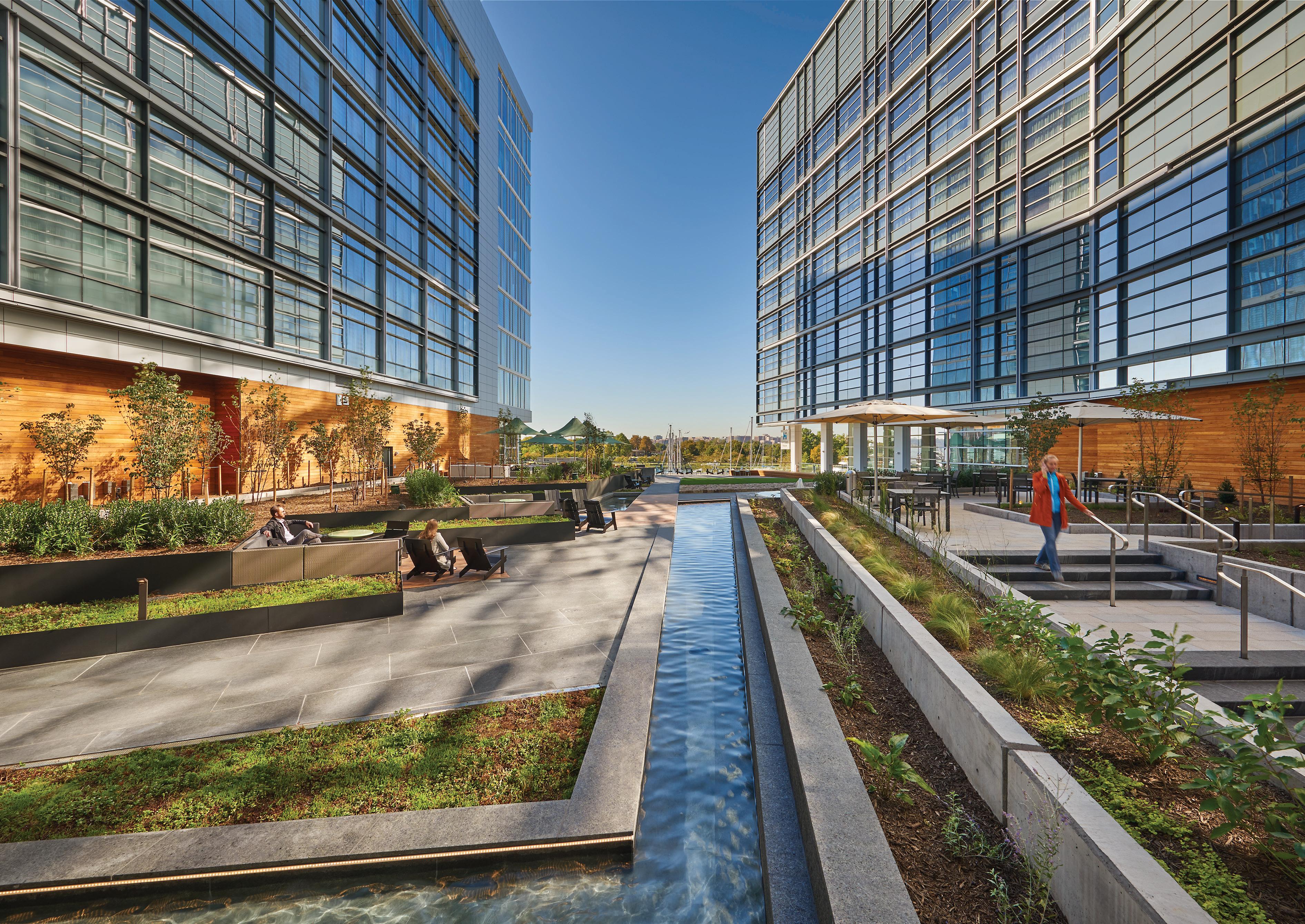
16 minute read
The Wharf Ties Riverfront To Rooftops
by IdeaSoil
A riverfront neighborhood leverages green roofs to manage stormwater and support sustainability.
The vegetative roof assemblies atop buildings throughout The Wharf and at ground level are integral to complying with the District of Columbia’s mandates for managing stormwater runoff. All photos courtesy of the Hoffman-Madison Waterfront. S tretching for nearly a mile along the shore of the Potomac River in Washington’s Southwest quadrant, The Wharf is a mixed-use development that includes elevated spaces for gathering using a network of green roofs. Each building’s green roof also adds interest to the skyline with a variety of foliage and green spaces.
Advertisement
Roofing contractor James Myers Co., Beltsville, MD, worked with Preservation & Protection Systems (PPSI), Laurel, MD, and Owens Corning, Toledo, OH, to design and install protected roof membrane assembly (PRMA) systems for vegetative roofs on several buildings throughout The Wharf area.
While the vegetated green roof assembly for each building featured unique plants and landscaping, the design concept and materials were selected to manage stormwater runoff. PPSI and Owens Corning had previously developed the PRMA assembly for the U.S. Coast Guard headquarters, Washington, and were pleased with its performance.
“Since its installation at the Coast Guard headquarters in 2013,
Architecture throughout The Wharf evokes a diverse sense of community with green roofs providing a unifying theme.

Codes Call For Vegetative Roofs
Vegetative roofs are prolifi c across the nation’s capital. The District of Columbia Department of Energy notes there are currently more than 3 million sq. ft. of vegetative roof in the District. Previous roof designs that infl uenced the vegetative-roof assemblies at The Wharf include several high-profi le buildings including MGM Casino, the National Museum of African American History and Culture, National Museum of American Indians, and the National Archives. One of the largest vegetative roofs in the nation, spanning approximately 500,000 sq. ft., sits atop the Douglas A. Munro U.S. Coast Guard Headquarters in Washington. The innovative assembly used on the Coast Guard headquarters served as a model for the assembly of several vegetative roofs throughout the D.C. area and in The Wharf.
In addition to the Potomac, D.C. waterways include the Anacostia River, Rock Creek, and the Chesapeake Bay. Commercial buildings throughout the District make use of an innovative cistern system, permeable pavements, and substantial vegetative bio-retention using a network of vegetative roofs. According to Jeffrey Seltzer, PE, acting director, Natural Resources Administration, Department of Energy & Environment, Washington, regulated development projects in the District are required to install practices that retain runoff from a 1.2-in. storm event typically through green infrastructure and capture/reuse systems employing cisterns.
Vegetative-roof assemblies are a key tool employed to help control the fl ow of stormwater into cisterns. The Wharf also uses these elevated spaces to provide a unique vantage for viewing several national landmarks and delivering valuable usable space in a densely populated area.
The specifi cation and installation of protected roof membrane assembly (PRMA) systems for vegetative roofs is an integral part of complying with the District’s requirements to manage stormwater runoff and to support developers’ vision of spaces integrating nature into the occupant and visitor experience. The District has mandated green roofs and specifi ed stormwater retention rates relative to a building’s footprint. As the District also specifi es the ratio of pervious versus impervious surfaces, contractors constructing buildings in The Wharf were challenged to achieve the mandated area of greenspace, considering the requirements of vegetation and adequate sidewalk/surface areas.

Vegetative roof assemblies provide spaces for cocktails, public gatherings, and a unique perspective for viewing the city’s waterfront and monuments.
F E A T U R E D PODCAST
Understanding Vegetative Roof Systems
CLICK HERE FOR MORE
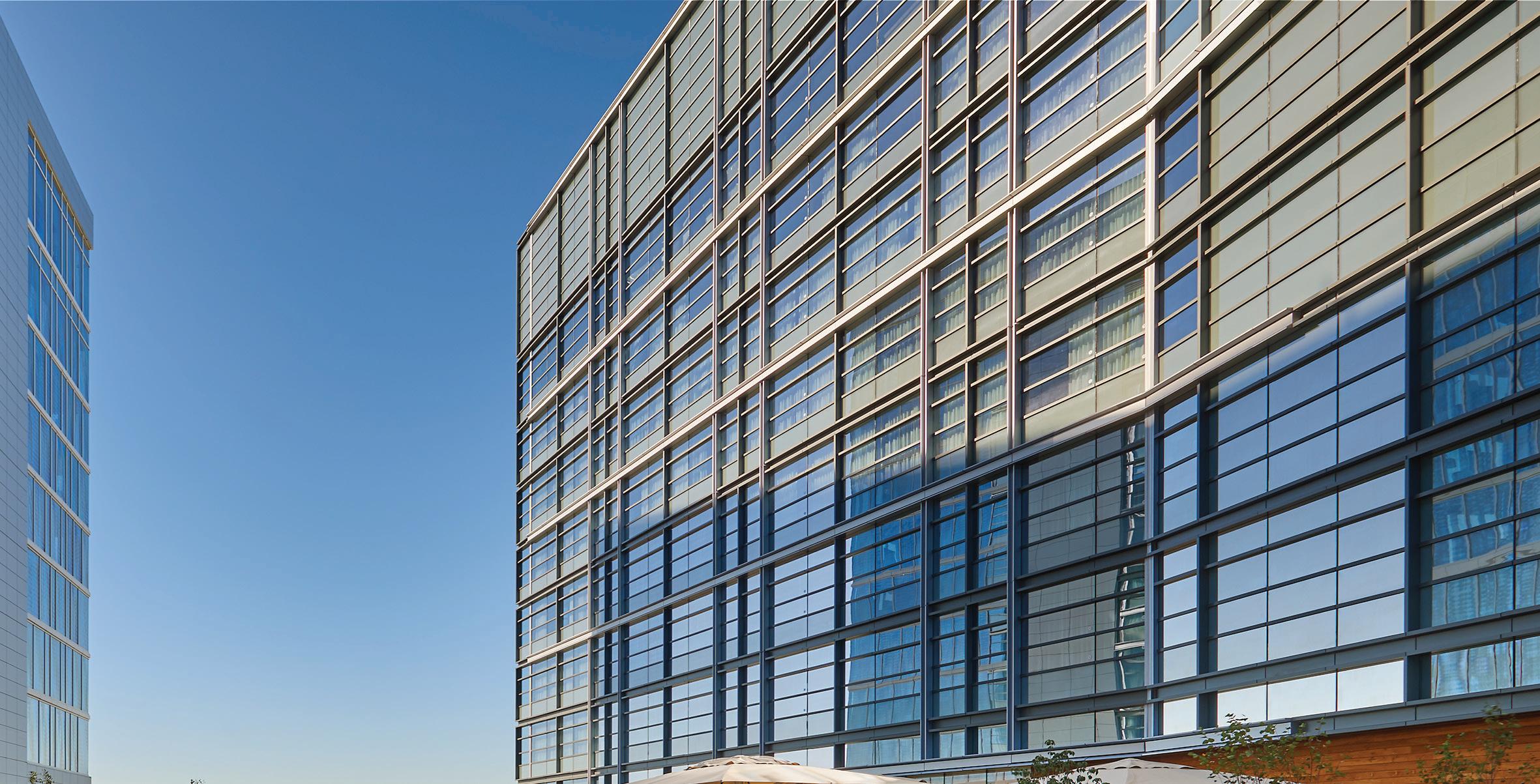
we’ve had no leaks,” said Steve Gordon, president of PPSI.
The PRMA installed on more than half of the roofs in The Wharf used Owens Corning FOAMULAR 404 and 604 extruded polystyrene insulation (XPS). The XPS insulating material was selected based on its compressive strength and ability to support a breadth of overburden materials including plants, pavers, and a unique network of pedestals and basins holding the soil in place. “We wanted an insulation with the water resistance to handle a variety of overburden types including plants and trees and the PSI to support pavers,” said Joe Schneider, RRC, senior project manager at James Myers.
The insulating material was also used in building-enclosure areas throughout The Wharf to deliver energy performance with its high R-value. Structural basins under the roof pavers held soil at depths to 4 ft., demanding a high PSI insulation. Beyond water resistance and strength, the XPS insulation helps control water flow as seams in the insulation help slow drainage, and helps avoid overwhelming drainage systems.
As rooftop plants and vegetation soak up the rainwater, the insulation helps to control the flow of water from the plant layer, growing media, and filter/drainage layer to the waterproofing layer and horizontally to a series of overflow vaults. The Wharf makes use of 700,000-gal. cisterns that collect and control the release of water.
Wind in the region presents an additional challenge for The Wharf’s vegetative roofs. Rock curbs from Hanover Architectural Products, Hanover, PA, help mitigate against winds coming in off the riverfront. Other materials used in the PRMA assembly included waterproofing membrane 790-11 Hot Rubberized Asphalt the by Henry Co., El Segundo, CA. EMSEAL, Westborough, MA, expansion joints tied together air barriers in the roofing system. Hanover Architectural Products provided the pavers, and sedum mats were supplied by Sempergreen, Odijk, The Netherlands.
CHALLENGES Meeting construction deadlines is always a concern, but the high-profile events surrounding the grand opening of The Wharf project meant there was no room for delay. A concert by hometown rock band the Foo Fighters at the Anthem music center officially launched the opening. The concert sold out quickly, filling the Anthem to its 6,000-occupant capacity. As the days toward the grand opening counted down, the District’s sweltering summer climate brought temperatures in the mid 90’s, and construction teams worked around the clock to complete Phase 1.
About The Wharf
As a community that engages visitors in experiences along the riverfront, The Wharf delivers the most public space to the District of Columbia since the redesign of the national mall in 1902. In addition to offering 14 acres of parks and public space, it features a variety of water activities including kayaking, paddle boarding, and water taxis.
The vegetative roofs are also an important component of The Wharf’s commitment to sustainability. Measures to support sustainability started at the master-planning stage and development was designed to achieve LEED ND Gold while targeting LEED Gold or Silver for individual buildings. The Wharf exceeds many of the requirements of the District’s Green Building Act and the Anacostia Waterfront Initiative.
Developed in phases, Phase One of The Wharf took nearly 15 years to complete. Phase One opened on October 12, 2017 and consists of 2 million sq. ft. of space. The fi nal phase is scheduled for completion in 2022. Upon completion, The Wharf will include 1,375 residences, 945,000 sq. ft. of offi ce space, and 800 rooms in four hotels.
A visitor unfamiliar with the project would likely be surprised to learn that the individual buildings are part of a planned community. Cobblestones coexist with glass and steel. Canopies are at different heights and of various shapes. The narrow streets and alleyways that project old-world charm posed challenges during the construction process. “It was an incredible spectacle of logistics to see huge cranes hoisting trees above traffi c and truckloads of extruded polystyrene insulation snaking their way through narrow corridors during construction,” said Tiffany Coppock, commercial-building-systems specialist at Owens Corning.
Perhaps The Wharf’s diverse look is the result of having nine different architects to design the fi rst nine buildings. Amid all this diversity, the Promenade is a central walkway tying the community together and giving The Wharf its most striking attribute—a sense of community. The Wharf attracts visitors and residents not only during the summer months, but throughout the year. Events such as ice sculpting, Curling & Cocktails, and Broomball & Brews keep the public engaged and interacting at The Wharf throughout the year. Nearly every holiday has a special event—including bagpipers on St. Patrick’s Day, Petalpalooza for the annual cherry-blossom celebrations, and a Chihuahua race for Cinco de Mayo. At its heart, The Wharf is a gathering place and much of that gathering takes place on the highly engineered rooftops.
“The magnitude of completing multiple buildings against a very tight timeline was a challenge felt by all of the contractor trades on site,” said Brian Davis, general superintendent at James Myers. With so much work occurring at once, scheduling and coordinating the logistics required of multiple trades was key to success. “As we installed pavers with elevated blocks, we were working throughout the night, seven days a week, the final 60 days of the project,” Davis said. For contractors taking on such high-profile projects, Davis said it’s critical to be prepared to adapt, expect the unexpected, and maximize communications with all trades working on a project.
During the final three months of construction at The Wharf, weekly coordination meetings evolved into daily meetings with precise schedules for exactly what team members would be working in what area at a particular time. According to Davis, the challenge of building nine buildings over six blocks made traffic bottlenecks the biggest challenge. Careful attention was paid not only to the District’s notorious rush-hour traffic but also to area attractions and events that draw traffic into the District. For example, the Washington Nationals schedule featured a number of weeknight baseball games, and trades were required to clear the streets three hours before the first pitch of each home game. While assuring schedules were maintained, the contractor also had to ensure safety and quality were not compromised.
The opening of Phase One brought together the District to create a one-of-a-kind public space that has reenergized one of America’s most historic riverfronts. The addition of green spaces atop the buildings has provided a new vantage point from which to take in one of America’s most beloved waterways, while helping achieve sustainability and
Want more information from Owens Corning (owenscorning.com)? Circle 6 on the Reader Service Card. Sources listed below are linked at commercialarchitecturemagazine.com/
1903owens.
James Myers Co., jamesmyersco.com Preservation & Protection Systems, ppsimd.com Hanover Architectural Products, hanoverpavers.com Henry Co., henry.com EMSEAL, emseal.com Sempergreen, sempergreen.com


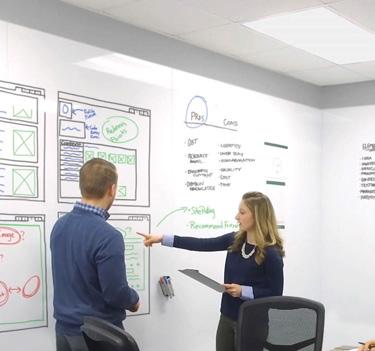
stormwater management objectives. CA
ENDLESS CREATIVITY.
UNLIMITED POSSIBILITIES. WhiteWalls ® Magnetic Dry-Erase
Whiteboard Wall Paneling

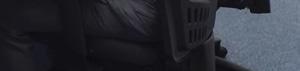

WhiteWalls.com | 800-624-4154
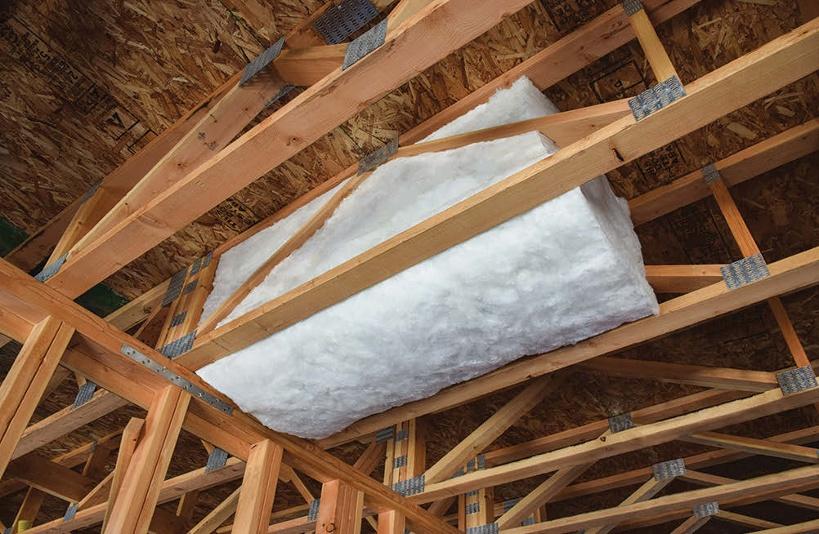
Tile, metal underlayment

Premium HT Tile & Metal:
Self-adhering roof underlayment Fiberglass-reinforced core UV exposure 180 days
Premium HT Tile & Metal is a self-adhering roo ng underlayment composed of a high-grade, reinforced polyester fabric laminated to a high-temperature asphalt adhesive system. e product also has a berglassreinforced core for extreme durability. A 3-in. selvedge edge ensures a secure, monolithic seal. e surface fabric o ers excellent foot traction. UV exposure is 180 days. Used as a whole-roof underlayment, it is said to withstand the high temperatures created by metal and tile roo ng with a high temperature rating of 250 F. Reportedly, the top surface bonds well with foam adhesive systems and works well with nail-down tile roofs. It may also be used underneath cedar shakes and synthetic or asphalt shingles. It is self-sealing around common roo ng fasteners to ensure a complete waterproof barrier. e underlayment has a thickness of 60 mils and is available in a 36-in. x 67-ft. roll. e product meets ASTM D 1970 and TAS 103-95 standards.
MFM Building Products, Coshocton, OH Circle 50 mfmbp.com
Formaldehyde-free insulation Formaldehyde-free Cavity-SHIELD is an NFPA 13-compliant, fi berglass batt insulation for concealed spaces in multifamily buildings. The product provides an alternative solution to sprinklers in the interstitial space. The fi berglass batts are a noncombustible insulation product made up of long, resilient glass fi bers bonded with thermosetting resin. The batts are designed for use in concealed spaces between fl oors, serving as a passive fi re solution for limiting potential fl ame spread between and through fl oors.
Johns Manville, Denver Circle 51 jm.com
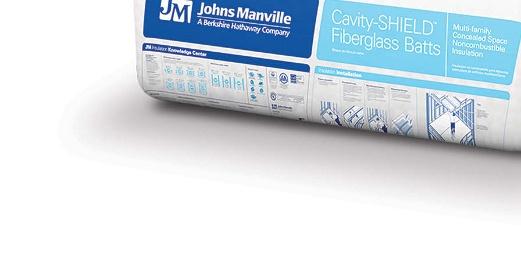

Drainable wrap Drainable wrap uses a layer of multi-directional polypropylene fi bers that diverts bulk water from exterior wall cavities, creating a highly effi cient drainage gap that sheds more bulk water than traditional house wraps. The wrap includes with a lifetime-limited warranty and meets code requirements for drainage effi ciency.
TYPAR, Old Hickory, TN Circle 52 typar.com
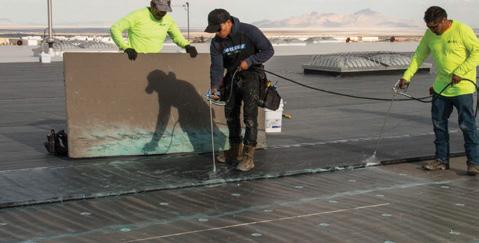
Adhesive/primer for EPDM membrane CAV-GRIP III low-VOC adhesive/primer can now be used to bond Sure-Seal, Sure-Tough, and Sure-White EPDM to horizontal substrates for warranty terms to and including 20-year, 90-mph designs. The product can be applied in temperatures as low as 25 F. With a fast tack time of less than 5 min., the product can be applied with a spray gun.
Carlisle SynTec Systems. Carlisle, PA Circle 53 carlislesyntec.com
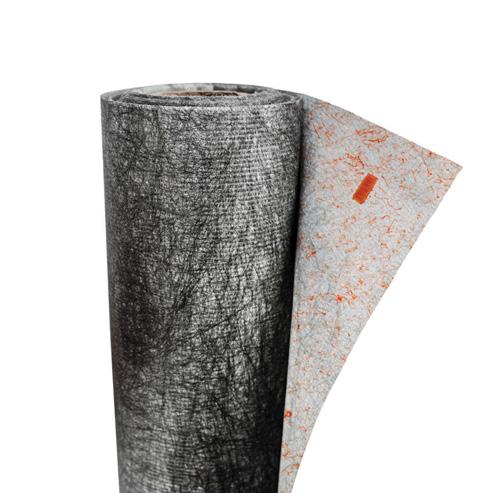
800.PAC.CLAD pac-clad.com
Circle 250
Mater Dei High School, Santa Ana, CA, is the largest non-public school west of Chicago. An old 1-million-Btu boiler was replaced with six Noritz tankless water heaters.


High School Embraces Multi-Unit Tankless System
Replacing a malfunctioning boiler with six tankless water heaters meets hot-water needs effi ciently and affordably at a California school.
Mater Dei High School, Santa Ana, CA, opened its doors in 1950 on a foundation of Catholic values and academic excellence. Today, with 2,100 students enrolled, it is the largest non-public school west of Chicago. Its acclaimed athletic program boasts several alumni who have gone on to play in the NFL, the NBA, and MLB. Like any institution, Mater Dei’s success depends on the quality of its people and facilities. So when an old, 1-million-Btu boiler began malfunctioning and placing the hot-water needs of the entire school in jeopardy, officials knew they needed to act. “We had been experiencing perennial problems with the boiler over several years, but it seemed to be getting worse and worse,” explained Steve Ritter, executive director of facilities at Mater Dei.
The school called on James Motis, owner of Prevent Backflow Plumbing, East Anaheim, CA, to solve its water-heating problem. A 30-year industry veteran, Motis specializes in commercial projects, and his customers include Subway, Panda Express, and the Natural History Museum of Los Angeles. Motis had already dealt with multiple service calls for the boiler. Its heat exchanger was wearing out, and a replacement was no longer available on the market. The boiler had reached the end of its life, and it was time to replace it.
MOVING TOWARD TANKLESS The disadvantages of the boiler were clear. It was large and bulky, which made it nearly inaccessible for regular maintenance. Ineffi cient operation meant it fi red even when hot water wasn’t needed in order to keep the stored water at setpoint temperature. Perhaps worst of all, it represented a single point of failure—the school was completely dependent on it for all hot water needs.
Initially, Motis and the school considered replacing the old boiler with two boilers. Here, at least, two units provided a limited level of redundancy, but the problems with the storage tank and inefficient operation would have continued. As a result, Motis considered a
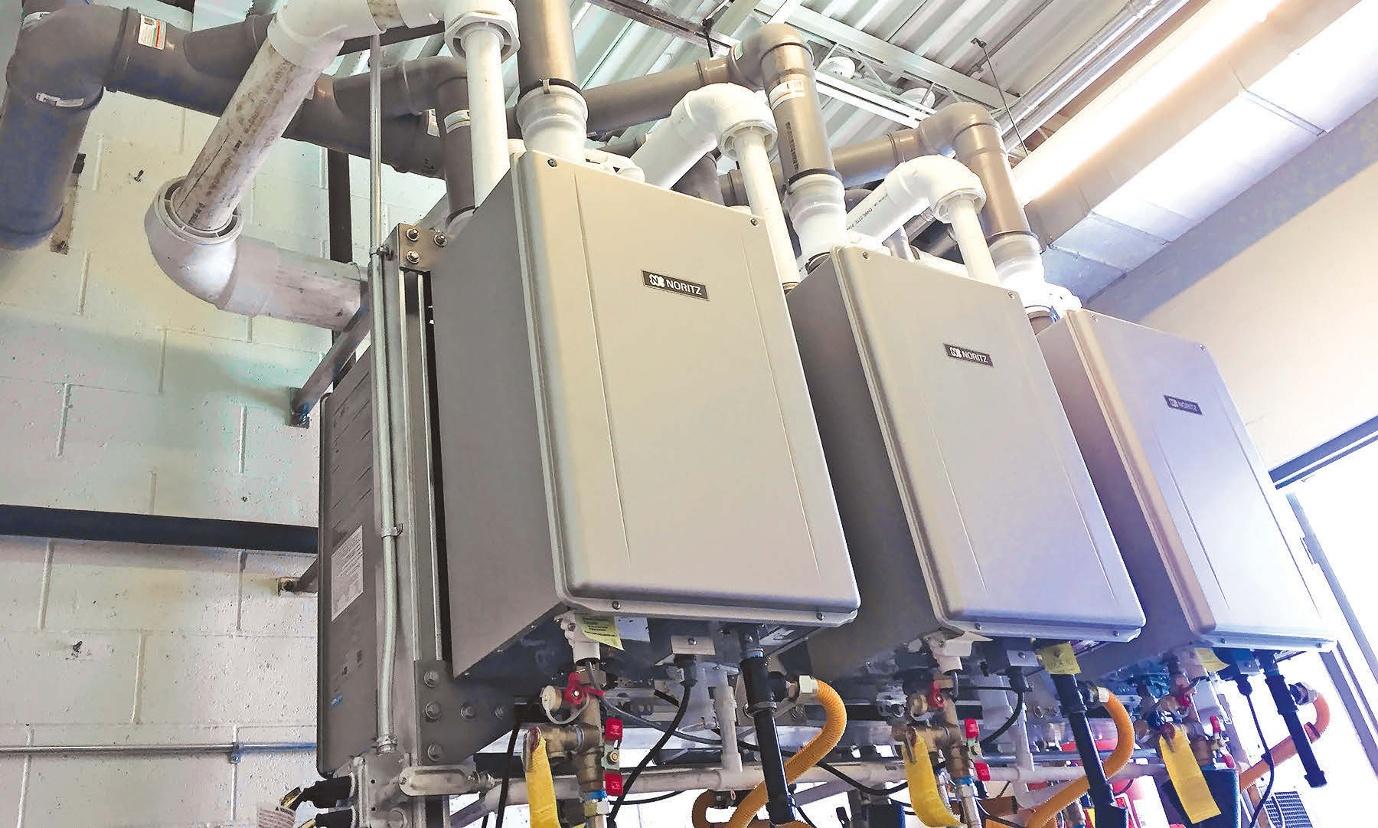
The tankless system provides redundancy of operation, efficient performance, compact design, and simple serviceability. second option: replacing the old boiler with several tankless water heaters from Noritz America Corp., Fountain Valley, CA, which he had successfully installed in more than a dozen other applications and with which he felt very comfortable. “Installing six tankless water heaters banked together in a rack system would have cost roughly the same as putting in two new boilers,” explained Motis. “The advantages, however, would have been their redundancy of operation, efficient performance, compact design, and simple serviceability.”
Ritter was convinced by Motis’ confidence. “The on-demand tankless system sounded extremely energy-efficient and a perfect fit for our hot water needs,” he said.
There was one problem. When the need surfaced in late 2017, Noritz did not yet have units certified for common venting—its NCC199CDV commercial tankless water heaters, designed expressly for that purpose, were due to release in January 2018.
Motis and school administrators insisted on common venting for the time and labor savings it would allow. “Being able to vent a system of water heaters through one common pipe eliminates the need for multiple roof penetrations and the leak prevention concerns that accompany them,” explained Motis. Common venting also allows fewer support hangars and a cleaner aesthetic for the completed project.
Since the new common-vent-capable units were only a few months away from release, Motis decided to postpone the installation. During the interim, he connected a Noritz NR111 tankless water heater he had in-shop to a 600-gal. storage tank at the school to provide hot water. “This makeshift install held out as long as it needed to, and I received no hot-water complaints from the school,” he recalled.
MULTI-SYSTEM ADVANTAGES With the 2018 release of the NCC199CDV unit, there was a new delay. With school in session, installation had to wait until March, when the school would be closed for the Easter holiday.
This gave Motis about one week to complete the installation, which included connecting six tankless water heaters into a banked system before making the final water connections. Noritz offered the option of prefabricating the units for Motis, saving him between three and four days of labor.
Prior to the installation, Noritz technicians connected the six water heaters on a custom-engineered rack and pre-sized the gas and water supply lines. The system was also designed for flexible transport and installation on the job site. “I really liked that they left both ends of the rack open because it allowed me to set it wherever I wanted on the jobsite,” said Motis.
There are several advantages to having a multi-system tankless setup. The units provide redundancy of operation. If one happens to go offline and needs to be serviced, the remaining units split the Btu demand to maintain the setpoint temperature. This capability keeps hot-water-reliant operations running, even if one or more units need servicing. If all remaining heaters have reached maximum demand, then the flow rate will be reduced slightly to lower the Btu input and maintain the setpoint temperature.