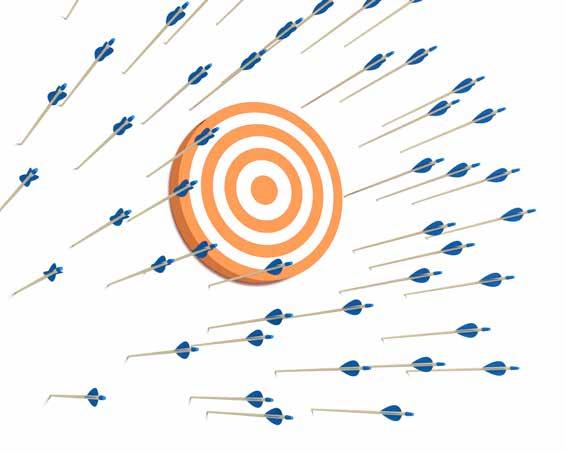
33 minute read
Fluid Power Faux Pas: Our Top Five Hydraulic System Mistakes Tips on avoiding costly hose, coupling, and tubing missteps
TOP 5 HYDRAULIC SYSTEM MISTAKES
By Cindy Cookson, Vice President of Hydraulics Global Product Line Management, Gates Corporation
With decades of experience in hydraulics, my Gates colleagues and I, especially our application engineers, have seen a lot when it comes to hose, coupling, and tubing solutions. At one end of the spectrum, we’ve been impressed, even inspired, by the ingenuity and creative problem-solving applied by end users. But at the other end of the spectrum, we’ve witnessed errors that make us cringe when we see them repeated in the field. To help everyone in our industry avoid these costly missteps, our friends at Fluid Power Journal asked us to share our top five hydraulic-system mistakes and some thoughts how to avoid them.
1
Forgetting about safety
When working with hydraulic systems day in and day out, some users become complacent about safety. Or even worse, technicians new to hydraulics may see a hose and mistakenly consider it to be the equivalent of a garden hose. In high-pressure hydraulics, mistakes can lead to critical injuries or even death, so it’s important to never take a hydraulic system for granted. Here are some critical safety reminders about hydraulic systems and hose assemblies: • Never touch a pressurized hydraulic hose. Rubbing your hand along a hose as a leakdetection technique, for instance, is just asking for trouble. • Similar to electrical systems, hydraulic systems can be energized even when the system appears to be “off.” Therefore, always depressurize a hydraulic system prior to handling or replacing any system components. • When replacing a hydraulic assembly, always ensure the replacement assembly can meet the system performance requirements, including working pressure, temperature, and fluid being conveyed. • For hydraulic hand tools, never carry the hand tool by the hose.
This can lead to pinching and pinholes. • For line-of-sight hydraulic lines in which an operator is working near the pressurized hydraulic assembly, use lineof-sight sleeving to protect the operator in the case of hose or assembly failures.
2
Relying on ‘what we’ve always used’
Hose and coupling standards for hydraulic systems have evolved over time. System pressures have increased, and the loads on hydraulic systems are increasingly dynamic. Meanwhile, materials science and process technologies have improved the capabilities of hydraulic hose and coupling assemblies.
Relying on “what we’ve always used” misses out on innovation and improvements in hydraulic hoses and couplings. But it could also mean compromising the safety of a hydraulic system. Hose and coupling selections should be made based on system requirements and not just on a hose construction. We often hear, “I need a two-wire braid hose,” or “my system needs a four-spiral hose.” But as OEMs have transitioned to isobaric hose ratings and hose manufacturers have innovated to deliver flexibility and weight savings in hydraulic hoses, referring to a hose by its construction is a risky move. Instead, when selecting hoses and couplings, follow system requirements for working pressure, temperature, and fluid compatibility.
The STAMPED method reminds users of the considerations for selecting a hose for a specific application. Here’s a brief explanation of the STAMPED acronym: • Size – Determine what ID hose is required for fluid flow. A hose that is too large reduces system performance due to increased pressure loss and excessive system heat from excessive fluid turbulence. • Temperature – The hose must be capable of withstanding
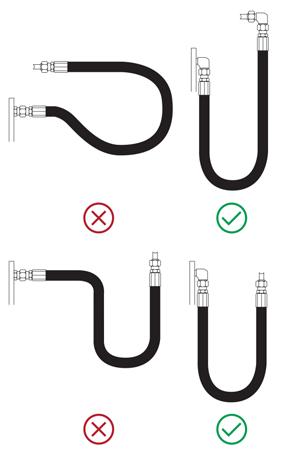
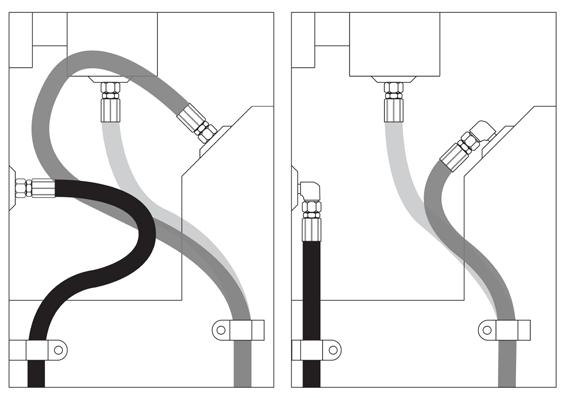
the system’s minimum and maximum fluid and ambient temperatures. • Application – How and where the hose assembly will be used. • Material/Media – The hose tube, cover, and couplings must be compatible with the fluid being conveyed. • Pressure – Published hose working pressure must equal or exceed the normal system pressure, including pressure spikes. • Ends – Identify the termination and threads needed for the system to define the proper couplings and adapters. • Delivery – Determine the hose size needed to deliver the required fluid volume without losing pressure or adding unnecessary weight or bulk.
Also consider requirements for how the hose and assembly are physically provided to the end application, including the date required, special packaging, labeling, or certifications.
3
Poor system routings
Hose assembly routings are a critical component of hydraulic system performance, both in an OE application and when replacing hoses. Poor routings can lead to, at best, an under-performing hydraulic system with less system pressure than expected; or at worse, faulty routing leading to costly downtime, with the worst-case scenario being unsafe working conditions. Application engineering experts can diagnose a hydraulic system and recommend routings or system changes to improve performance, and these consultations usually reduce hydraulic system costs (figure 1).
Because hoses are flexible, they are often chosen instead of rigid tubes. But that doesn’t mean hoses have unlimited flexibility. Common issues arise when hoses must bend – particularly bends near the coupling. WRONG RIGHT
Figure 1: Avoid bends near the coupling.
WRONG RIGHT
WRONG RIGHT
Figure 2: Use angled adapters or alternative couplings.
Optimized hose routings will avoid hose bends near the coupling by using angled adapters or alternative coupling options to alleviate hose flex requirements. If a bend radius is below the recommendation for that particular hose, get creative with angled adapters. Revisit your coupling selection to avoid sharp bends (figure 2).
Proper routings also mitigate hose abrasion, whether against other hoses or against machine components. Return lines are another component that can be problematic. Although the lines are typically low pressure and a necessary component to return fluid to a reservoir, they are often the last component considered
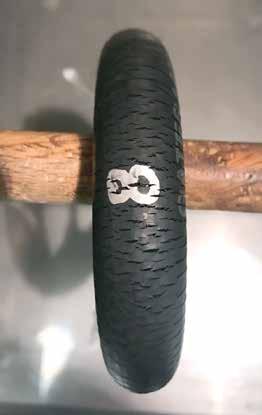
Figure 3: Cover cracks caused by ozone.
when designing a system. To mitigate the risks of challenging routings, Gates makes Multi Master GMV MegaFlex, a flexible, corrugated hose design that has a tighter minimum-bend radius. Finally, hose routings can minimize the likelihood of leaks in a hydraulic system with proper termination selection. Avoid stacking adapters to minimize system cost and the risk of system leaks.
4
Ignoring signs of wear
Hydraulic assembly inspection should be included in any preventive maintenance schedule. These inspections should monitor for signs of wear, including cover damage like cracking and abrasion. Ideally, the system design reduces the likelihood of damage, but when damage reaches the hose reinforcement, replace the assembly.
Cover cracks can be caused by several issues. Exposure to extreme heat, particularly in engine compartments, can cause the exterior cover of the hose to become brittle and crack (figure 3). Exposure to ozone, either from the sun or from high electrical charges, such as in welding equipment applications, can cause microcracks to appear on the surface of the hose. This is similar to the weathering seen in tire sidewalls. Ozone damage typically appears first on the exterior of hose bends, where the rubber compounds see their highest stresses. Once these cracks reach the hose reinforcement, the reinforcement is compromised because of potential damage from moisture and debris. This damage can be mitigated by protecting hoses from high electrical exposure and by choosing hoses with materials resistant to ozone.
Cover abrasion is a constant challenge, particularly in congested hydraulic systems where it is difficult to isolate one hose from others or the machine frame in dynamic applications. The most obvious way to mitigate abrasion damage is to choose hose covers that are specially formulated with abrasion resistance. Specialized nitrile rubber compounds offer a midgrade level of abrasion resistance, and extreme resistance to abrasion can be realized with a hose cover made of ultrahigh molecular-weight polyethylene film. It is also possible to assemble the hose in an abrasion-resistant sleeve or hose guard, but this option considerably increases assembly costs and can complicate hose installation in the application. (Continued on page 8)
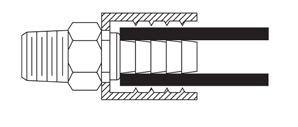

(Continued from page 7) In addition to selecting abrasion-resistant hose covers or accessories, the hose routing can also have an impact on hose abrasion. Use clamps to support long hose runs or to keep hoses away from moving parts, taking special care to allow for volumetric expansion. Hoses that bend around a portion of the machine frame should be assembled with enough length to avoid rubbing over a machine corner. And it’s worth noting that hoses should never be clamped to the machine frame, which could restrict expansion in the curves when the hose is pressurized (figures 4 and 5).

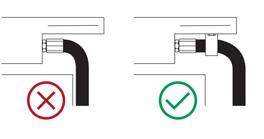
5
Proper assembly
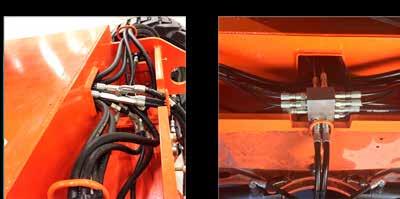
A user can procure the most premium and highest-performing hoses and couplings in the world, but if they’re not assembled correctly, they’ll never realize the value. Proper assembly has several criteria: a qualified hose-coupling interface, assembly by a trained technician, and a verified crimp diameter.
A qualified hose-coupling interface results from verifying that the hose and coupling work together. The verification is more than just crimping to a certain crimp diameter; it should be verified by burst and impulse testing across a range of crimp diameters to account for hose and coupling manufacturing variation as well as crimper and die tolerances. The testing should mimic the intended application, particularly the temperature. A hose-coupling interface may work well at standard 100°C (212°F) operations and then not perform at elevated temperatures above 120°C (248°F). Further, all hoses are not the same. Even though hoses from different manufacturers may meet the same performance criteria, the properties of the compound affect the robustness of the hose-coupling interface. Also, the thickness of the rubber materials and the placement of the reinforcement WRONG RIGHT
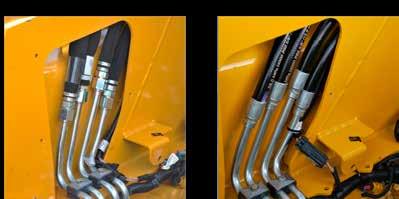
Figure 4: Use clamps to prevent abrasion damage.
NO PRESSURE
HIGH PRESSURE
Figure 5: Allow for volumetric expansion in hydraulic hoses. WRONG
RIGHT
Figure 6: Cross-section of the hose-coupling interface.
Figure 7: Crimp diameter measurements with standard calipers (top) and notched calipers (bottom).
material can change the crimp dimensions. Likewise, couplings from different manufacturers are not necessarily equivalent. They may be made from different grades of steel, different material hardness, and include features such as serrations that are dimensionally different and may significantly impact the quality of the hose-coupling interface. Even the radius or heights of these features can significantly impact assembly performance (figure 6).
A trained assembly technician is also critical to the assembly process. She or he must be trained to select the proper hose and couplings, cut the hose to the correct length, remove debris and contaminants from inside the hose, ensure full coupling insertion onto the hose, select the appropriate crimper setting, and place the assembly properly in the crimper dies. And the technician must do it all safely!
Finally, after the assembly has been made, the crimp diameter on each end of the assembly must be verified for proper crimping. This measurement is often performed with calipers and compared to a qualified crimp diameter range (figure 7). Some systems also use a go/no-go gauge to verify the crimp by reviewing either the crimp diameter or the stem collapse.
Smart crimpers are gaining popularity in the market. They make operator training and quality assembly easier by mistake-proofing various steps in the assembly process. Smart crimpers, such as Gates’ GC20 Cortex crimper, typically include the crimp settings in an onboard computer to eliminate the need to reference the crimp setting and program the crimper.
New technology and materials are advancing the capabilities of hydraulic hoses and couplings, as well as hydraulic systems overall. As hydraulic systems become more complex, proper hose routing keeps the system running efficiently, both in OE and replacement applications. Baseline training in hydraulics can support safe operations and provide reminders on system inspections. Finally, hose and coupling manufacturers often provide recommendations and training on proper hose assembly. Staying up to date on these innovations and recommendations is well worth the effort, as it can promote a fluid power system’s safe operation, improve its performance, and reduce downtime.
CASE STUDY: OPTIMIZING HOSE ROUTINGS
X X X X X X X X X X X X X X X X X X X X X X X X X X X X X X X X X X X X X X X X X X X X X X X X X X X X X X X X X X X X X X X X X X X X X X X X X X X X X X X X X X X X X X X X X X X X X X X X X X X X X X X X X X X X X X X X X X X X X X X X X X X X X X X X X X X X X X X X X X X X X X X X X X X X X X X X X X X X X X X X X X X X X X X X X X X X X X X X X X X X X X X X X X X X X X X X X X X X X X X X X X X X X X X X X X X X X X X X X X X X X X X X X X X X X X X X X X X X X X X X X X X X X X X X X X X X X X X X X X X X X X X X X X X X X X X X X X X X X X X X X X X X X X X X X X X X X X X X X X X X X X X X X X X X X X X X X X X X X X X X X X X X X X X X X X X X X X X X X X X X X X X X Two case studies by Gates product application engineers demonstrate the value of optimized system-hose routings. In the first X X X X case, a customer was having difficulty routing hoses through a channel in the rear drive. Upon further inspection, Gates engineers found a few opportunities: X X X X X X X X X X X X
What Engineers Observed Optimized Solution X X X X X X X X
Tee grouping created Replace tees with a manifold. X X X X X X X X challenges routing hoses Manifold design provided fixed points X X X X through the channel. of reference for routing and improved X X X X X X X X
Bundled tees created abrasion concerns. aesthetics on the machine. It also eliminated abrasion concerns from bundled tees. X X X X X X X X X X X X X X X X
X X X X
Connections at the same point were difficult to install. Gates QuickLok connections minimized leaks and enabled fast and easy X X X X X X X X X X X X assembly. X X X X X X X X
X X X X The before-and-after photos show a cleaner system with improved perX X X X X X X X formance and fewer leak points. X X X X X X X X In a second case, a customer had issues with hydraulic fluid leaks at a X X X X hose-tube connection point. The Gates engineer located the root cause of X X X X X X X X the leakage issue: a bundle of hose-tube connections that were difficult X X X X X X X X to get wrenches on caused installation challenges and system leaks. The solution was crimp-on hose-tube connections that eliminated the leaks and reduced the number of SKUs.
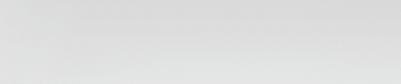
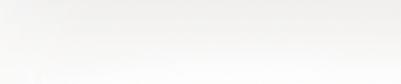
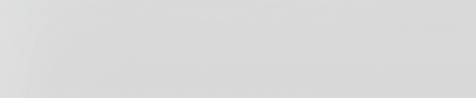



Pandemic Blamed for Drop in Fluid Power Exports Last Year
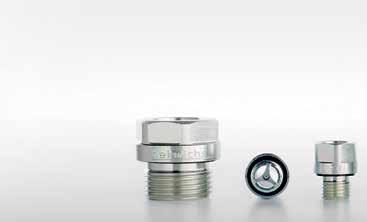

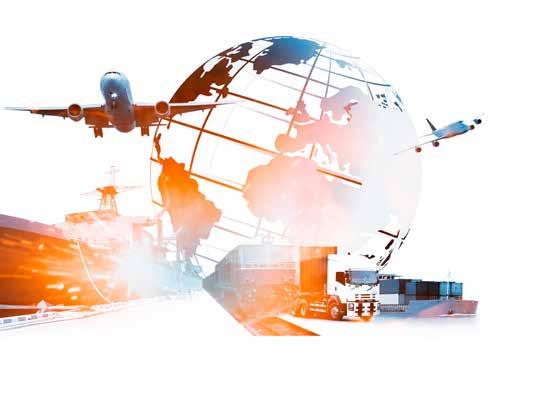
Fluid Power Journal staff report
»U.S. FLUID POWER product exports totaled $5.6 billion in 2020, a double-digit drop from 2019, the National Fluid Power Association reported.
U.S. fluid power exports declined nearly $1 billion, more than 14%, as a result of numerous challenges, including a recessionary economy brought on by the COVID-19 pandemic, a Feb. 25 NFPA report said. An uncertain foreign trade environment due to unstable trade policies, including unpredictable sanctions and wavering tariffs, was another factor in the export decline, according to the report.
The top 10 trading partners for U.S. fluid power exports remained consistent even through the pandemic, the report said. Those 10 trading partners accounted for 72% of fluid power exports, while 180 other countries traded for the remaining 28% of exports, according to the report. More than half of fluid power exports, 55%, were traded with the industry’s top five partners: Mexico, Canada, China, Germany, and the U.K., the report noted.
Fluid power product rankings saw little change throughout the pandemic. The top five products, totaling 61% of U.S. exports, were hydraulic valves, hydraulic actuators, rotary hydraulic pumps, pneumatic valves, and reciprocating hydraulic pumps, the report said.
For more detailed information, NFPA members can visit https://nfpahub.com/stats/ info-category/international-fluid-power-data.
robust compact reliable
The ‘heavy-duty’ solution for demanding applications. Double cushioned glass against vibrations. Sealed against the housing via integrated formring. Available from M 10x1 and up!
HN OSG | OIL LEVEL SIGHT GLASS
Special solution for special demands
It’s our turn. heinrichs-usa.com
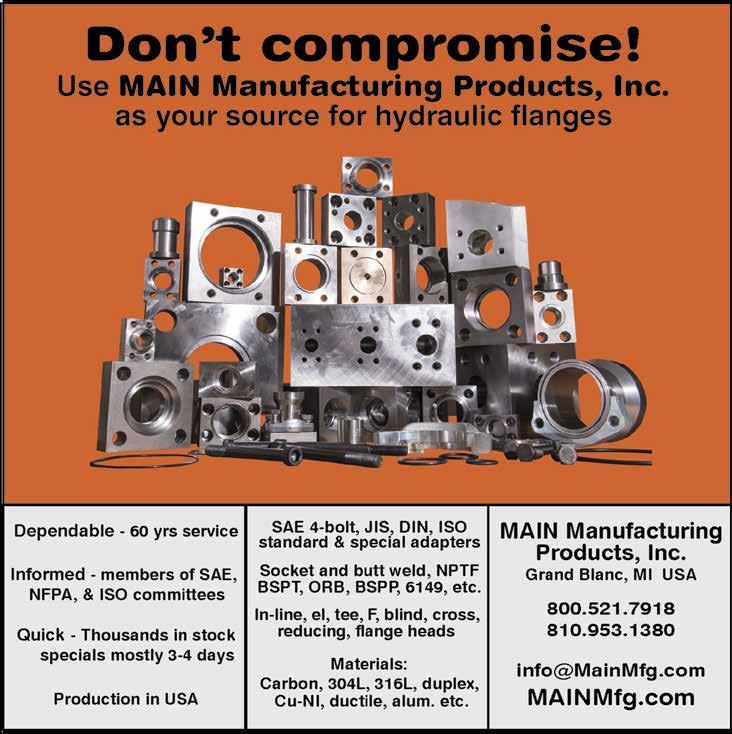
CELEBRATING 60 YEARS
»THE INTERNATIONAL Fluid Power Society expects to release an updated mobile hydraulic mechanic certification by the end of the year.
The certification is designed for individuals who fabricate, assemble, test, maintain, and repair systems and components. The mechanic should understand hydraulic symbols, read system schematics, and be skilled in using hand tools, power tools, micrometers, and testing equipment. HITACHI FLANGELOCKTM The upgraded MHM Study Manual compiles all the information necessary to pass both the written (knowledge) and job performance (practical ability) certification tests.AND CAP KITS AVAILABLE
Improvements and updates in the new MHM Study Manual include: • • Principles of operation, explained for commonly found components within a mobile hydraulic system – pumps, valves, actuators, and accessories. Color-coded cutaway illustrations of hydraulic components to aid in under» IFPS IS ACCEPTING nominations for the 2021 Fluid Power Hall of Fame awards. The Hall of Fame acknowledges Part number Part description Applicable machines Number of parts Weight (kg) SWINGFLGLCK2062 Swing hose FlangeLockTM kit EX3600, EX5600, EX8000 16 x 2062U - red FlangeLockTM 6.7 SWINGCAP2062 Swing circuit cap kit EX3600, EX5600, EX8000 16 x 2062 - cap 4.5 standing operation. individuals who have made significant contributions to fluid • Updated symbology is ISO 1219 standard compliant. TRAVELFLGLCK2462 power technology and dedicated their careers to the industry.Travel hose FlangeLockTM kit EX3600, EX5600, EX8000 16 x 2462U - purple FlangeLockTM 7.7 • Expanded content on troubleshooting includes decision-tree aids.TRAVELCAP2462 Anyone can nominate one living and one deceased indi-Travel circuit cap kit EX3600, EX5600, EX8000 16 x 2462 - cap 6.4 • • Detailed content on pressure, flow, and directional control valves. Improved graphics throughout and real-life photos assist visualization. FRONTATTFLGLCK326162 vidual. The nominee must have 25 or more years of service in the fluid power industry. Living nominees will be asked Front attachment FlangeLockTM kit EX3600, EX5600, EX8000 14 x 3262U - black FlangeLockTM 4 x 3261U - black & silver FlangeLockTM 8.9 • Basic hydraulic calculations useful in troubleshooting. FRONTATTCAP326162 to complete an application. A panel of judges will select Front attachment cap kit EX3600, EX5600, EX8000 14 x 3262 - cap 4 x 3261 - cap 9.5 • • Safety tips. Basic principles of electrohydraulic control – open loop and closed loop. BOOMARCHFLGLCK3262 the inductees, who will be announced on Fluid Power Pro fessionals' Day, June 19. Boom arch hose FlangeLockTM kit EX3600, EX5600, EX8000 20 x 3262U - black FlangeLockTM 9.9 • Electrohydraulic valves. BOOMARCHCAP3262 Nominations are being accepted until April 15 and can be Boom arch hose cap kit EX3600, EX5600, EX8000 20 x 3262 - cap 11.3 • Sensors used in electrohydraulic systems. CONTAMINATION CONTROL made at www.fluidpowerhalloffame.org.

THE ULTIMATE CONTAMINATION CONTROL TOOL
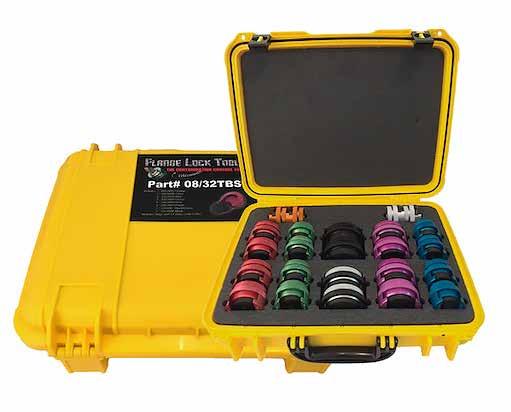
Routine and scheduled maintenance of hydraulic systems are vital to getting the most out of your Hitachi Mining Excavator. While maintenance plays the largest role in the prevention of unnecessary machine downtime, it can also expose the hydraulic system to high levels of contamination rapidly decreasing component longevity. The importance of contamination control is sometimes Stop the Mess overlooked when performing maintenance due to incorrect practices being used. THE FLANGELOCK™ TOOL AND CIRCUIT BLANKING CAPS The FlangeLock™ tool and caps are the ultimate contamination control tools for protecting your hydraulic system. The FlangeLock™ allows for the simple sealing of open hydraulic flanges without tools while the caps can be bolted in place of a flange connection. Easy on, easy off, they offer a leak-proof solution to hydraulic systems and environmental cleanliness. FlangeLock™ tools and caps stop the mess.
The FlangeLock™ Tool is the ultimate contamination control tool for protecting your hydraulic systems. It allows for the simple sealing of open SAE code 61, 62 HITACHI MAKING CONTAMINATION CONTROL EASY & CAT-Style hydraulic flanges without tools. Constructed from lightweight aluminum. Hitachi have packaged FlangeLock™ tool and caps specifically for Hitachi mining excavators. The Hitachi customised kits make sure no matter which component routine maintenance is being performed on, you will always have the exact Easy on, easy off. Offers a leakproof solution to hydraulic system and environmental number of FlangeLocks™* and caps to help reduce contamination. cleanliness. FlangeLock™ Tools stop the mess!*Note: FlangeLocks™ are not to be used under pressure
SAVE TIME SAVE MONEY SAVE LABOR SAVE OIL
This product is Patented, other Patents pending. • • • No tools required No expensive hardware needed No more rags stuffed into hoses • One hand installation • Eliminate hydraulic oil spills & clean up • Quick installation & ease of usage Call you local Hitachi Muswellbrook representative or the branch on 02 6541 6300 for more information. • No more messy plastic caps • Safe for personnel & environment • The ultimate contamination control tool • Industry acclaimed
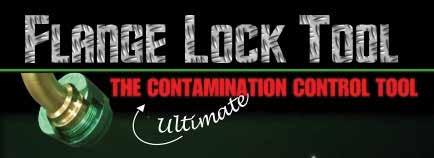
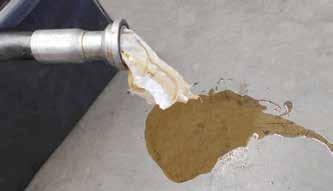
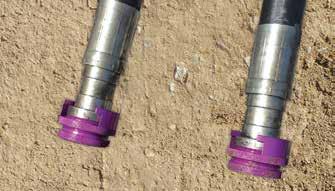
For more information, call 203-861-9400 or email sales@flangelock.com. www.flangelock.com
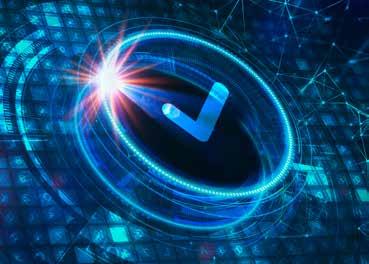
January 2021 Newly Certified Professionals
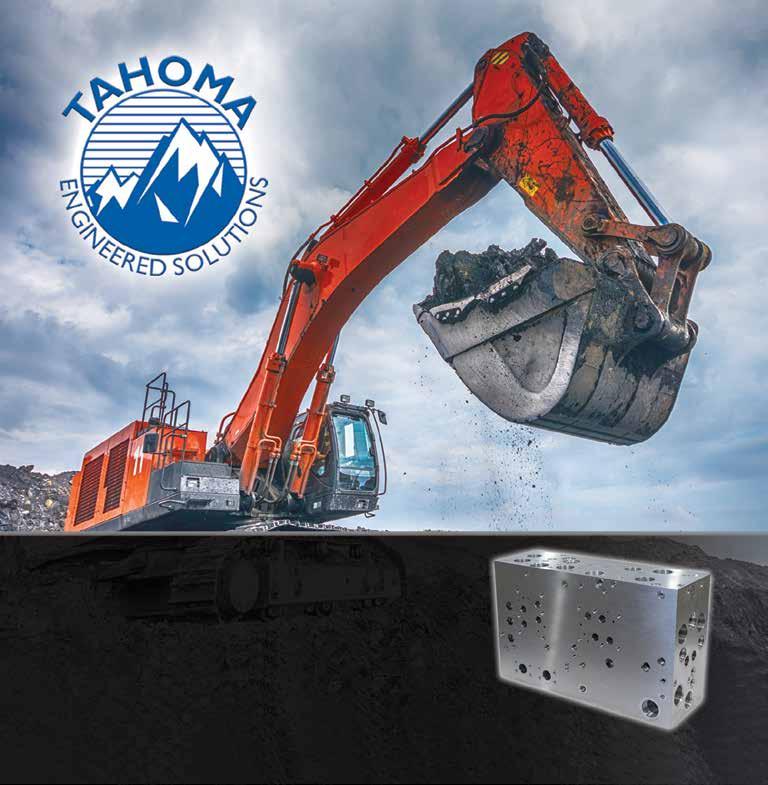
CONNECTOR & CONDUCTOR
Robert Bertenshaw, The Boeing Company Alex Ng, The Boeing Company John Osko, The Boeing Company Jonathan Summers, The Boeing Company Chris Wilkie, The Boeing Company
ELECTRONIC CONTROLS SPECIALIST John Bills
SPECIALIST
holds HS and PS Certifications
John Bills
HYDRAULIC SPECIALIST
Nathan Bariel, The Boeing Company Kevin Dugan, Gates Corporation Jesse Holmes, CERES Jonathyn Lamont, Curry Fluid Power
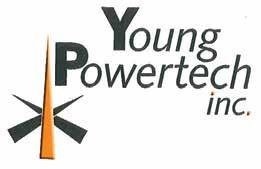
MOBILE HYDRAULIC MECHANIC
Ryan Bisarra, Altec Industries, Inc. Ivan Bojoruez, Southern California Edison Corey Boynton, Cleveland Electric Illuminating Tyson Dahlgrin, Altec Industries, Inc. Michael Gudehus, Southern California Edison Jason Harper, Southern California Edison Cory Heath, Altec Industries, Inc. Fuasalli Iose, Southern California Edison Sean Mahannah, Southern California Edison John Mathews, Altec Industries, Inc. Robert Nava, Altec Industries, Inc. David Navarro, Altec Industries, Inc. Carlos Pelaez, Altec Industries, Inc. Brett Roeder, Altec Industries, Inc. Alexander Shelley, Southern California Edison Francisco Tabullo, Southern California Edison Clinton Tinsley, Altec Industries, Inc. John Weber, Altec Industries, Inc.
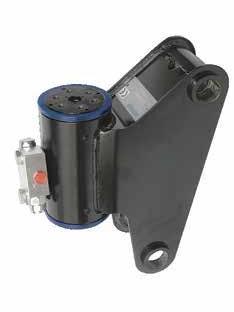
Precision Machining for Quality Hydraulics
Contact us today 419.496.0964, ext. 203 Sales@TahomaEngineeredSolutions.com ISO 9001:2015 532 County Road 1600 • Ashland, Ohio 44805
delivers solutions
Helical Hydraulic Rotary Actuators
GENERAL DATA
• Torque output from 45 LB-Ft to 44.000 LB-FT • Rotation up to 720 degrees • Cantilever mount • Straddle mount • Special design available
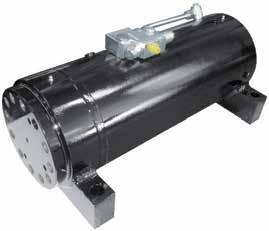
Contact Us 3060 Plaza Dr. #108 • Garnet Valley, PA 19060 Telephone: 610-558-0760 • E-mail: info@youngpowertech.com www.youngpowertech.com
Spring Meeting Dates Changed
CELEBRATING 60 YEARS
»THE INTERNATIONAL Fluid Power Society’s in-person spring meeting, previously scheduled May 4-7, has been rescheduled and will take place May 3-6 at the Embassy Suites San Antonio Riverwalk Downtown in San Antonio, Texas.
IFPS set a technical workshop for the meeting:
Maximizing the Use of PowerPoint and PDF Files Thursday, May 6, 8 a.m. - 2 p.m. includes lunch
Discover your inner designer during Dan Helgerson’s deep dive into the underutilized tools of PowerPoint. Learn how to spice up your slide show by adding animation, motion paths, morphs, and how to work with graphic reproduction. You’ll also learn how to link and bookmark in PDF files. This is a hands-on workshop, where attendees will be “doing” as Dan “teaches.” Register by visiting ifps.org or call 856-424-8998. SCHEDULE OF EVENTS
Monday, May 3 2:00 PM - 4:00 PM New Board Member Orientation* 6:30 PM - 11:00 PM Board of Directors Dinner* Tuesday, May 4 8:00 AM - 9:00 AM Strategic Planning Committee Meeting 9:00 AM - 11:00 AM Education Committee Meeting 11:00 AM - 12:00 PM Membership Committee Meeting 12:00 PM - 12:30 PM Hosted Lunch 12:30 PM - 1:30 PM Membership Committee Meeting (cont’d) 1:30 PM - 5:00 PM Certification Committee Meeting 6:00 PM - 9:00 PM Dinner Wednesday, May 5 8:00 AM - 10:30 AM Marketing Committee Meeting 10:30 AM - 12:00 PM Finance Committee Meeting 12:00 PM - 12:45 PM Hosted Lunch 1:00 PM - 2:30 PM Board of Directors Meeting 2:30 PM - 3:00 PM Strategic Planning Committee Meeting 3:30 PM - 5:00 PM Riverwalk Boat Tour 6:00 PM - 9:30 PM Reception & Trivia Night Thursday, May 6 8:00 AM - 2:00 PM Technical Workshop & Box Lunch * invitation only
OUR HOSES & EQUIPMENT HELP KEEP YOU AND YOUR PRODUCTS MOVING!
• High Quality Hose & Couplings • Inventory & Fast Response • Crimping Equipment • Crimp Spec. Software • E-Commerce

Jason Industrial well known for its Industrial Hose business has expanded to offer Hydraulic Hose, Couplings and Equipment. As you have come to know, we are all about high quality and service. Our Nationwide Distribution Centers have stock and are ready to ship.
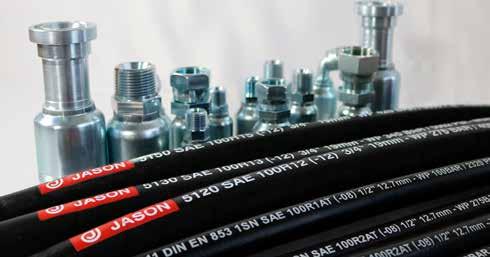
www.JasonIndustrial.com | 630.752.0600

A New Road to Hydraulic Specialist Certification
»IFPS RELEASED THE hydraulic specialist (HS) certification test, designed to be comprehensive, in 2017. The test benchmarks competencies showing that, as a fluid power specialist, you are at the top of your craft, whether you’re in sales, engineering, or system designing.
After reviewing the design, layout, and content of the HS Study Manual, the IFPS certification committee decided to update and better streamline the manual by: • rewording complex topics for easier comprehension; • rewriting the equation formulas and subsequent text describing how to compute complex formulas for ease of calculation; • carefully rewriting some outcomes to provide the necessary information to prepare for the test and provide industry best practices paramount to our industry; and • adding “bar” whenever pressure units are used to reflect the industry’s more common use of both metric units of pressure (bar and
Pascal).
Preparation is the key to a successful outcome. For those who were unsuccessful the first time around, don’t give up! You can find the streamlined study manual in your IFPS account under downloadable products.
IFPS wants you to succeed. There are several ways to prepare. Visit ifps.org to access these resources: • Master the online and study manual pretests. • Access recorded web seminar outcome presentations. • Consider a paid one-year access to the HS interactive study manual. • Form a study group – an excellent way to share strengths and knowledge. • Use our animated circuits for a visual understanding of schematics. • Certification review training classes (see page 15).
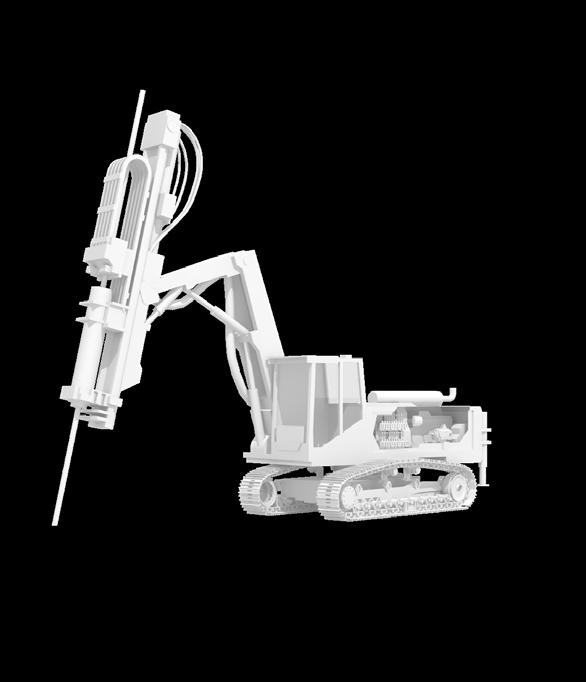
IFPS CERTIFICATION
Joining IFPS and gaining my CFPHS has truly helped round out my fluid power knowledge and create an excellent foundation for personal growth. The greatest benefit has been the ability to apply those skills across multiple industries and in widely varying applications, giving me the confidence to deliver the best solution to my clients for the job at hand. Ben Cusack, CFPHS, OneHydraulics Engineering Manager
Smart Hydraulics. Easy Business.
Precise, Flexible and Safe
Load-holding valves type CLHV
Versatile and Flexible
Mobile controller type ESX
Efficient, Reliable and Durable
Variable displacement axial piston pump type V30D
Industry Leading Performance
Proportional directional spool valve PSL-CAN
HAWE Hydraulik manufactures the highest quality hydraulic components, constructed to minimize space and maximize product durability for the mobile, industrial and oilfield markets.
Partner with HAWE to always have the right solution!
We are Partners.
www.hawe.com | info@haweusa.com | 704-509-1599
Field Sales and Operations opportunities available now. Visit the HAWE Job Market online to apply today.
Certification Testing Locations
Individuals wishing to take any IFPS written certification tests can select from convenient locations across the United States and Canada. IFPS is able to offer these locations through its affiliation with The Consortium of College Testing Centers provided by National College Testing Association.
Contact headquarters if you do not see a location near you. Every effort will be made to accommodate your needs.
If your test was postponed due to the pandemic, please contact headquarters so that we may reschedule.
TENTATIVE TESTING DATES FOR ALL LOCATIONS:
May 2021
Tuesday 5/4 • Thursday 5/20
June 2021
Tuesday 6/1 • Thursday 6/24
July 2021
Tuesday 7/13 • Thursday 7/29
August 2021
Tuesday 8/3 • Thursday 8/26
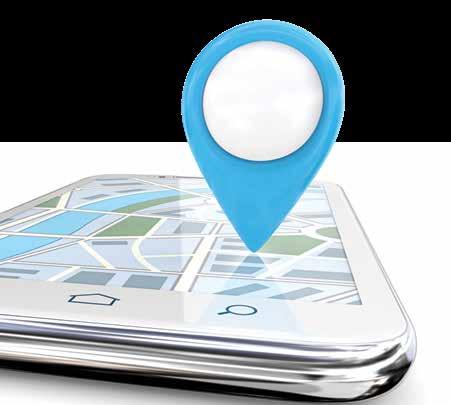
ALABAMA Auburn, AL Birmingham, AL Calera, AL Decatur, AL Huntsville, AL Jacksonville, AL Mobile, AL Montgomery, AL Normal, AL Tuscaloosa, AL
ALASKA Anchorage, AK Fairbanks, AK
ARIZONA Flagstaff, AZ Glendale, AZ Mesa, AZ Phoenix, AZ Prescott, AZ Scottsdale, AZ Sierra Vista, AZ Tempe, AZ Thatcher, AZ Tucson, AZ Yuma, AZ
ARKANSAS Bentonville, AR Hot Springs, AR Little Rock, AR
CALIFORNIA Aptos, CA Arcata, CA Bakersfield, CA Dixon, CA Encinitas, CA Fresno, CA Irvine, CA Marysville, CA Riverside, CA Salinas, CA San Diego, CA San Jose, CA San Luis Obispo, CA Santa Ana, CA Santa Maria, CA Santa Rosa, CA Tustin, CA Yucaipa, CA COLORADO Aurora, CO Boulder, CO Springs, CO Denver, CO Durango, CO Ft. Collins, CO Greeley, CO Lakewood, CO Littleton, CO Pueblo, CO
DELAWARE Dover, DE Georgetown, DE Newark, DE
FLORIDA Avon Park, FL Boca Raton, FL Cocoa, FL Davie, FL Daytona Beach, FL Fort Pierce, FL Ft. Myers, FL Gainesville, FL Jacksonville, FL Miami Gardens, FL Milton, FL New Port Richey, FL Ocala, FL Orlando, FL Panama City, FL Pembroke Pines, FL Pensacola, FL Plant City, FL Riviera Beach, FL Sanford, FL Tallahassee, FL Tampa, FL West Palm Beach, FL Wildwood, FL Winter Haven, FL
GEORGIA Albany, GA Athens, GA Atlanta, GA Carrollton, GA Columbus, GA Dahlonega, GA Dublin, GA Dunwoody, GA Forest Park, GA Lawrenceville, GA Morrow, GA Oakwood, GA Savannah, GA Statesboro, GA Tifton, GA Valdosta, GA
HAWAII Laie, HI
IDAHO Boise, ID Coeur d ‘Alene, ID Idaho Falls, ID Lewiston, ID Moscow, ID Nampa, ID Rexburg, ID Twin Falls, ID
ILLINOIS Carbondale, IL Carterville, IL Champaign, IL Decatur, IL Edwardsville, IL Glen Ellyn, IL Joliet, IL Malta, IL Normal, IL Peoria, IL Schaumburg, IL Springfield, IL University Park, IL INDIANA Bloomington, IN Columbus, IN Evansville, IN Fort Wayne, IN Gary, IN Indianapolis, IN Kokomo, IN Lafayette, IN Lawrenceburg, IN Madison, IN Muncie, IN New Albany, IN Richmond, IN Sellersburg, IN South Bend, IN Terre Haute, IN
IOWA Ames, IA Cedar Rapids, IA Iowa City, IA Ottumwa, IA Sioux City, IA Waterloo, IA
KANSAS Kansas City, KS Lawrence, KS Manhattan, KS Wichita, KS
KENTUCKY Ashland, KY Bowling Green, KY Erlanger, KY Highland Heights, KY Louisville, KY Morehead, KY LOUISIANA Bossier City, LA Lafayette, LA Monroe, LA Natchitoches, LA New Orleans, LA Shreveport, LA Thibodaux, LA
MARYLAND Arnold, MD Bel Air, MD College Park, MD Frederick, MD Hagerstown, MD La Plata, MD Westminster, MD Woodlawn, MD Wye Mills, MD MASSACHUSETTS Boston, MA Bridgewater, MA Danvers, MA Haverhill, MA Holyoke, MA Shrewsbury, MA MICHIGAN Ann Arbor, MI Big Rapids, MI Chesterfield, MI Dearborn, MI Dowagiac, MI East Lansing, MI Flint, MI Grand Rapids, MI Kalamazoo, MI Lansing, MI Livonia, MI Mount Pleasant, MI Sault Ste. Marie, M Troy, MI University Center, MI Warren, MI
MINNESOTA Alexandria, MN Brooklyn Park, MN Duluth, MN Eden Prairie, MN Granite Falls, MN Mankato, MN
MISSISSIPPI Goodman, MS Jackson, MS Mississippi State, MS Raymond, MS University, MS MISSOURI Berkley, MO Cape Girardeau, MO Columbia, MO Cottleville, MO Joplin, MO Kansas City, MO Kirksville, MO Park Hills, MO Poplar Bluff, MO Rolla, MO Sedalia, MO Springfield, MO St. Joseph, MO St. Louis, MO Warrensburg, MO MONTANA Bozeman, MT Missoula, MT
NEBRASKA Lincoln, NE North Platte, NE Omaha, NE
NEVADA Henderson, NV Las Vegas, NV North Las Vegas, NV Winnemucca, NV NEW JERSEY Branchburg, NJ Cherry Hill, NJ Lincroft, NJ Sewell, NJ Toms River, NJ West Windsor, NJ
NEW MEXICO Albuquerque, NM Clovis, NM Farmington, NM Portales, NM Santa Fe, NM
NEW YORK Alfred, NY Brooklyn, NY Buffalo, NY Garden City, NY New York, NY Rochester, NY Syracuse, NY NORTH CAROLINA Apex, NC Asheville, NC Boone, NC Charlotte, NC China Grove, NC Durham, NC Fayetteville, NC Greenville, NC Jamestown, NC Misenheimer, NC Mount Airy, NC Pembroke, NC Raleigh, NC Wilmington, NC NORTH DAKOTA Bismarck, ND
OHIO Akron, OH Cincinnati, OH Cleveland, OH Columbus, OH Fairfield, OH Findlay, OH Kirtland, OH Lima, OH Maumee, OH Newark, OH North Royalton, OH Rio Grande, OH Toledo, OH Warren, OH Youngstown, OH OKLAHOMA Altus, OK Bethany, OK Edmond, OK Norman, OK Oklahoma City, OK Tonkawa, OK Tulsa, OK
OREGON Bend, OR Coos Bay, OR Eugene, OR Gresham, OR Klamath Falls, OR Medford, OR Oregon City, OR Portland, OR White City, OR PENNSYLVANIA Bloomsburg, PA Blue Bell, PA Gettysburg, PA Harrisburg, PA Lancaster, PA Newtown, PA Philadelphia, PA Pittsburgh, PA Wilkes-Barre, PA York, PA SOUTH CAROLINA Beaufort, SC Charleston, SC Columbia, SC Conway, SC Graniteville, SC Greenville, SC Greenwood, SC Orangeburg, SC Rock Hill, SC Spartanburg, SC TENNESSEE Blountville, TN Clarksville, TN Collegedale, TN Gallatin, TN Johnson City, TN Knoxville, TN Memphis, TN Morristown, TN Murfreesboro, TN Nashville, TN
TEXAS Abilene, TX Arlington, TX Austin, TX Beaumont, TX Brownsville, TX Commerce, TX Corpus Christi, TX Dallas, TX Denison, TX El Paso, TX Houston, TX Huntsville, TX Laredo, TX Lubbock, TX Lufkin, TX Mesquite, TX San Antonio, TX Victoria, TX Waxahachie, TX Weatherford, TX Wichita Falls, TX
UTAH Cedar City, UT Kaysville, UT Logan, UT Ogden, UT Orem, UT Salt Lake City, UT VIRGINIA Daleville, VA Fredericksburg, VA Lynchburg, VA Manassas, VA Norfolk, VA Roanoke, VA Salem, VA Staunton, VA Suffolk, VA Virginia Beach, VA Wytheville, VA WASHINGTON Auburn, WA Bellingham, WA Bremerton, WA Ellensburg, WA Ephrata, WA Olympia, WA Pasco, WA Rockingham, WA Seattle, WA Shoreline, WA Spokane, WA WEST VIRGINIA Ona, WV
WISCONSIN La Crosse, WI Milwaukee, WI Mukwonago, WI WYOMING Casper, WY Laramie, WY Torrington, WY CANADA ALBERTA Calgary, AB Edmonton, AB Fort McMurray, AB Lethbridge, AB Lloydminster, AB Olds, AB Red Deer, AB
BRITISH COLUMBIA Abbotsford, BC Burnaby, BC Castlegar, BC Delta, BC Kamloops, BC Nanaimo, BC Prince George, BC Richmond, BC Surrey, BC Vancouver, BC Victoria, BC
CELEBRATING 60 YEARS
MANITOBA Brandon, MB Winnipeg, MB NEW BRUNSWICK Bathurst, NB Moncton, NB
NEWFOUNDLAND AND LABRADOR St. John’s, NL
NOVA SCOTIA Halifax, NS
ONTARIO Brockville, ON Hamilton, ON London, ON Milton, ON Mississauga, ON Niagara-on-the-Lake, ON North Bay, ON North York, ON Ottawa, ON Toronto, ON Welland, ON Windsor, ON
QUEBEC Côte Saint-Luc, QB Montreal, QB
SASKATCHEWAN Melfort, SK Moose Jaw, SK Nipawin, SK Prince Albert, SK Saskatoon, SK
YUKON TERRITORY Whitehorse, YU
UNITED KINGDOM Elgin, UK
GHAZNI Kingdom of Bahrain, GHA Thomasville, GHA
EGYPT Cairo, EG
JORDAN Amman, JOR
NEW ZEALAND Taradale, NZ
CFPAI Certified Fluid Power Accredited Instructor CFPAJPP Certified Fluid Power Authorized Job Performance Proctor
CFPAJPPCC Certified Fluid Power Authorized Job Performance Proctor Connector & Conductor
CFPE Certified Fluid Power Engineer CFPS Certified Fluid Power Specialist (Must Obtain CFPHS & CFPPS) CFPHS Certified Fluid Power Hydraulic Specialist CFPPS Certified Fluid Power Pneumatic Specialist CFPECS Certified Fluid Power Electronic Controls Specialist CFPMT Certified Fluid Power Master Technician (Must Obtain CFPIHT, CFPMHT, & CFPPT) CFPIHT Certified Fluid Power Industrial Hydraulic Technician CFPMHT Certified Fluid Power Mobile Hydraulic Technician CFPPT Certified Fluid Power Pneumatic Technician
CFPMM Certified Fluid Power Master Mechanic (Must Obtain CFPIHM, CFPMHM, & CFPPM) CFPIHM Certified Fluid Power Industrial Hydraulic Mechanic CFPMHM Certified Fluid Power Mobile Hydraulic Mechanic CFPPM Certified Fluid Power Pneumatic Mechanic
CFPMIH Certified Fluid Power Master of Industrial Hydraulics (Must Obtain CFPIHM, CFPIHT, & CFPCC) CFPMMH Certified Fluid Power Master of Mobile Hydraulics (Must Obtain CFPMHM, CFPMHT, & CFPCC) CFPMIP Certified Fluid Power Master of Industrial Pneumatics (Must Obtain CFPPM, CFPPT, & CFPCC) CFPCC Certified Fluid Power Connector & Conductor
CFPSD Fluid Power System Designer CFPMEC (In Development) Mobile Electronic Controls
CFPIEC (In Development) Industrial Electronic Controls

Tentative Certification Review Training
IFPS offers onsite review training for small groups of at least 10 persons. An IFPS accredited instructor visits your company to conduct the review. Contact kpollander@ifps.org for details of the scheduled onsite reviews listed below.
HYDRAULIC SPECIALIST CERTIFICATION REVIEW September 13-16, 2021 - Fairfield, OH - CFC Industrial Training | Written test: September 16, 2021
PNEUMATIC SPECIALIST July 27-29, 2021 - Fairfield, OH - CFC Industrial Training | Written test: July 29, 2021
ELECTRONIC CONTROLS CERTIFICATION REVIEW August 9-12, 2021 - Fairfield, OH - CFC Industrial Training | Written test: August 12, 2021
CONNECTOR & CONDUCTOR CERTIFICATION REVIEW May 18-19, 2021 - Fairfield, OH - CFC Industrial Training | Written and JP test: May 20, 2021 November 16-17, 2021 - Fairfield, OH - CFC Industrial Training | Written and JP test: November 18, 2021
MOBILE HYDRAULIC MECHANIC CERTIFICATION REVIEW Online Mobile Hydraulic Mechanic Certification Review (for written test) offered through info@cfcindustrialtraining.com. This course takes you through all chapters of the MHM Study Manual (6.5 hours) and every outcome to prepare you for the written MHM test. Members receive 20% off. (Test fees are additional - separate registration required.) April 13-15, 2021 - Fairfield, OH - CFC Industrial Training | Written and JP test: April 16, 2021 August 30 - September 1, 2021 - Fairfield, OH - CFC Industrial Training | Written and JP test: September 2, 2021
INDUSTRIAL HYDRAULIC MECHANIC CERTIFICATION June 14 - 16, 2021 - Fairfield, OH - CFC Industrial Training | Written and JP test: June 17, 2021
INDUSTRIAL HYDRAULIC TECHNICIAN CERTIFICATION REVIEW TRAINING Call for dates. Phone: 513-874-3225 - CFC Industrial Training, Fairfield, Ohio
MOBILE HYDRAULIC TECHNICIAN CERTIFICATION REVIEW TRAINING Call for dates. Phone: 513-874-3225 - CFC Industrial Training, Fairfield, Ohio
PNEUMATIC TECHNICIAN and PNEUMATIC MECHANIC CERTIFICATION REVIEW TRAINING Call for dates. Phone: 513-874-3225 - CFC Industrial Training, Fairfield, Ohio
JOB PERFORMANCE TRAINING Online Job Performance Review - CFC Industrial Training offers online JP Reviews which includes stations 1-6 of the IFPS mechanic and technician job performance tests. Members may e-mail askus@ifps.org for a 20% coupon code off the list price or get the code in our Members Only area for the entire IFPS Job Performance Review; test not included.
LIVE DISTANCE LEARNING JOB PERFORMANCE STATION REVIEW E-mail info@cfcindustrialtraining.com for information.