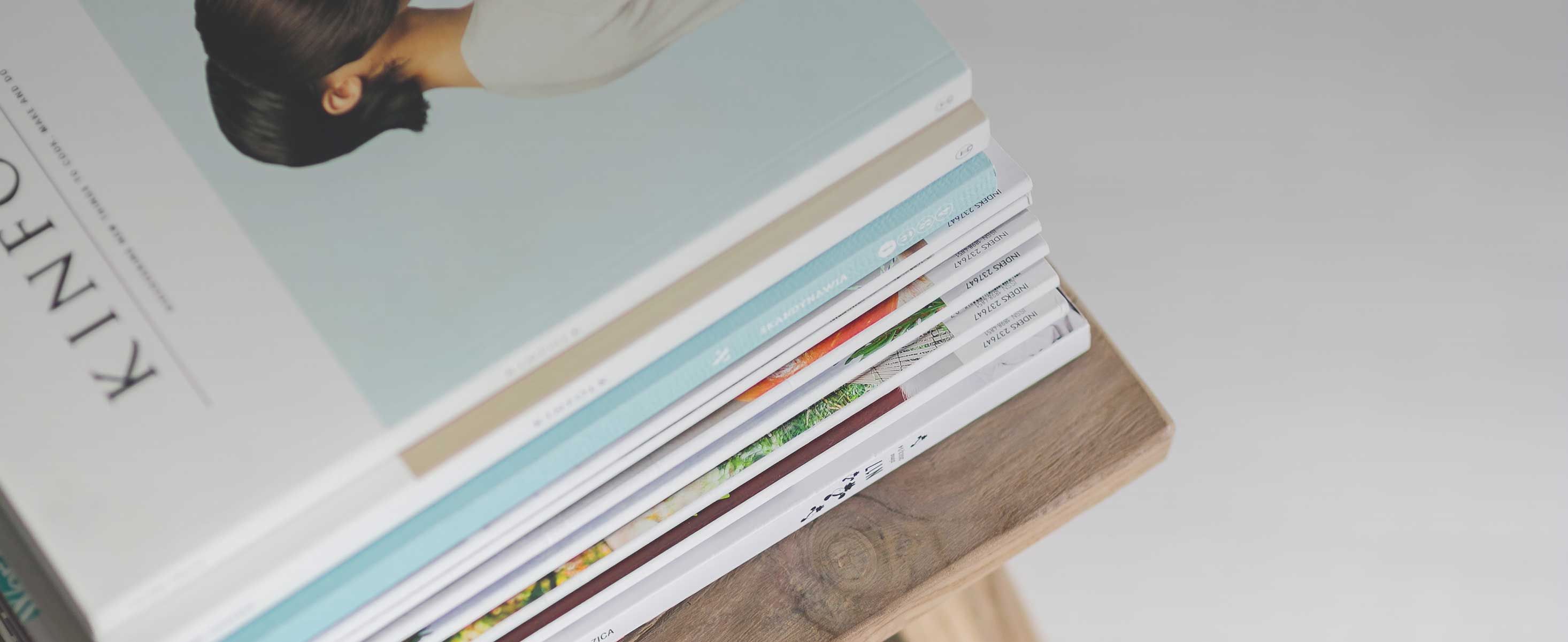
2 minute read
WHY ACCUMULATORS FAIL
There are a number of reasons why a bladder or diaphragm in an accumulator typically fails.
The most common reason is that the compression ratio is exceeded. The compression ratio is determined by dividing the maximum system pressure by the precharge pressure. Typically, a compression ratio of less than 4:1 is acceptable for a bladder-type accumulator and 6:1 for a diaphragm accumulator. Maintaining a proper compression ratio is necessary to ensure that excessive flexing of the bladder or diaphragm doesn’t occur.
Another common failure is due to incorrect precharge pressure. It is necessary that the precharge pressure be less than the system minimum operating pressure. If the bladder-style accumulator was precharged to a higher pressure than manufacturer specifications, the bladder may fail. Under normal operation, the bladder is compressed in the shell by hydraulic oil and only expands to rest against the anti-extrusion poppet valve in the bottom of the accumulator when the system is off. Higher-than-specified precharge pressures can cause the bladder to pound against the poppet valve in the bottom of the accumulator when system pressure drops but is still within the operating range of the machine. This makes the bladder fail where it is pushed against the anti-extrusion poppet valve. Hydraulic fluid leaking into the gas side of an accumulator effectively reduces the working volume of the accumulator.
Another possible failure with rapid cycling that fully discharges the accumulator is that the bladder can get pinched under the poppet valve as shown in figure 1. This may also occur if the precharge occurs too rapidly.
High oil temperature may also cause the bladder or diaphragm to prematurely fail, as the polymers used in the construction of a bladder or diaphragm have reduced life expectancy at elevated temperatures. It is also important to understand that when precharging the bladder or diaphragm, it is necessary to perform this slowly, as rapidly expanding gas will cause the temperature to decrease rapidly and may subject the polymers to brittle fracture due to the extreme cold.
A leak in the bladder will cause the gas precharge to escape into the hydraulic system. This may result in a sponginess in the actuators. It can also allow hydraulic fluid to enter the bladder. A pinhole leak on the side of the bladder is difficult to diagnose. The bladder may effectively seal the hole when the hydraulic side pressure is low but expose the hole when the hydraulic pressure is increased and the gas compresses, moving the bladder away from the accumulator wall.
In a piston-style accumulator, the dynamic seal wear allows the gas to escape and permits hydraulic fluid to migrate into the gas chamber. As shown in figure 2, the hydraulic fluid in the gas chamber reduces the effective working volume of the accumulator. •
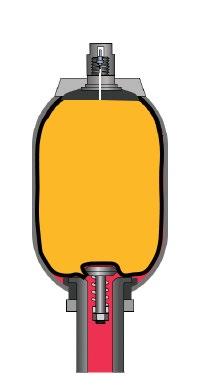
Test Your Skills
1.
A higher-than-specified precharge pressure in a bladder-style accumulator: a. is recommended so it doesn’t have to be checked as often. b. can cause the bladder to be damaged by pounding against the poppet valve. c. drops as the fluid heats up. d. results in greater fluid storage during operation. e. seals any pinhole leaks on the side of the bladder.
See page 54 for the solutions.
By Andy Peakcock,