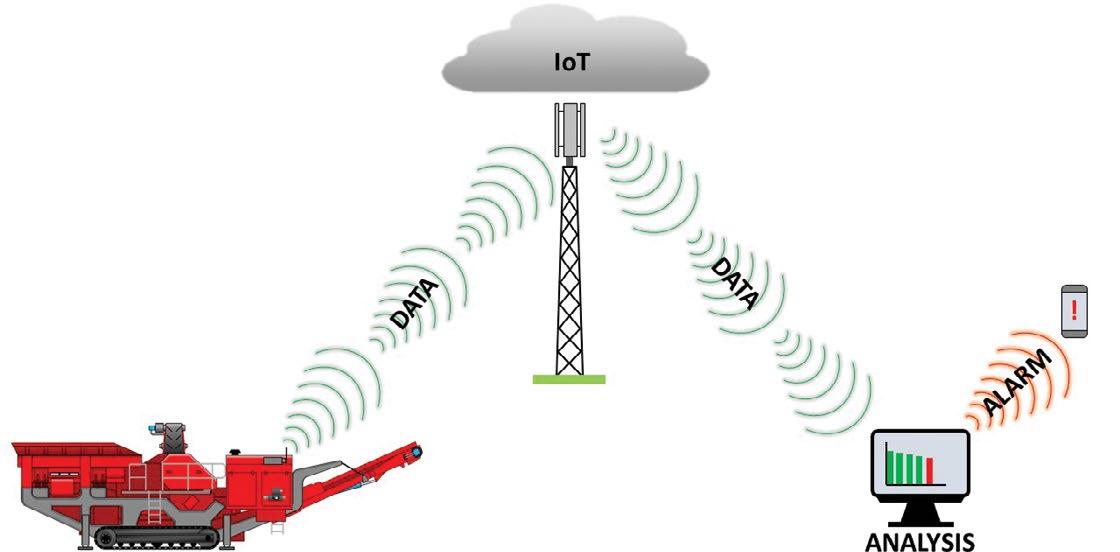
12 minute read
solution partner
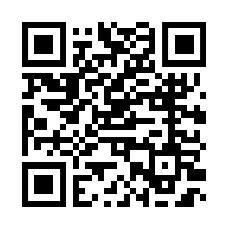
Condition monitoring and maintenance
For pumps and motors that operate for long periods of time, continuously monitoring their performance can provide an early warning of a potentially costly failure. Webtec’s new CTA flow monitor has been designed for this purpose and can be installed either in the pump outlet line to monitor pump flow rate or in the supply line to a conveyor motor for example.
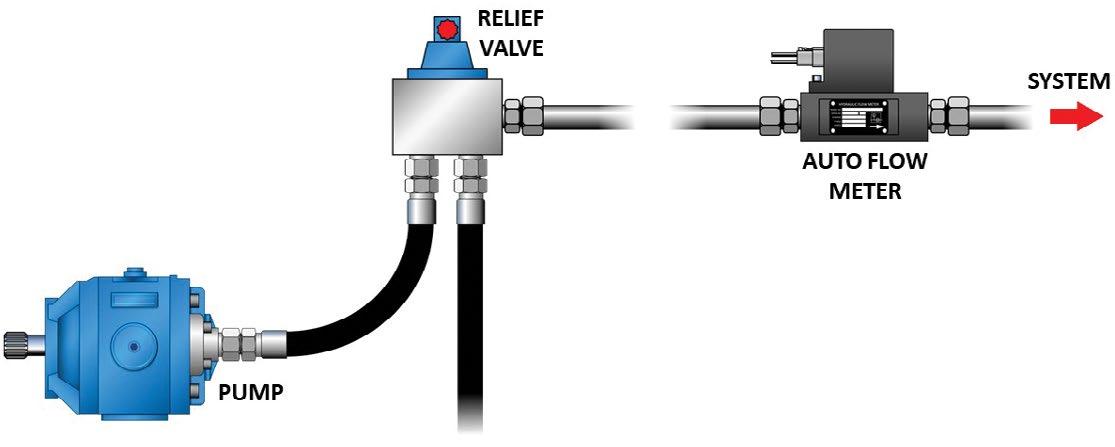
Excavator mounted solutions
For short-term tasks such as demolition work, where the task involved does not warrant the use of a dedicated machine, crushing attachments are often used that can be mounted onto an excavator boom and used to process smaller quantities of material.
Auto flow meter monitoring pump output flow.
By comparing the pump or motor flow rate with its rotational speed, a rapid assessment can be made of the component’s state of wear and action can be taken before a catastrophic failure occurs. A particularly useful feature of the CTA flow monitor is that its output can be observed remotely via a machine’s telematic system. For autonomous vehicles or machinery that is not constantly supervised by operators, a data link can be established via the cloud to provide an early warning of an impending component failure, thus saving the potential cost and time wastage of a catastrophic failure.
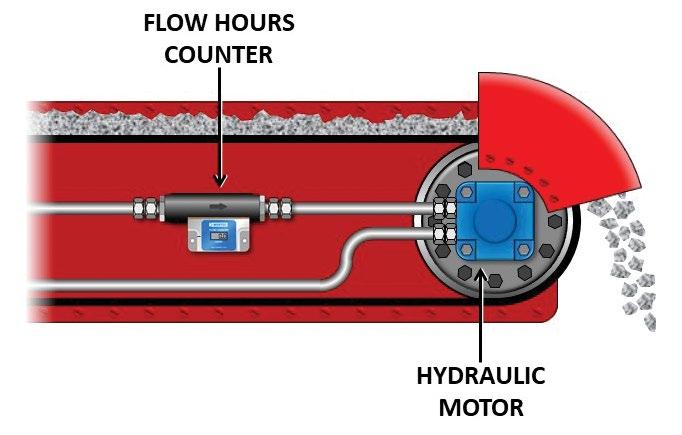
Webtec’s DHM Series hydraulic multimeter can be an invaluable tool for system troubleshooting and optimizing the setup of attachments such as crusher buckets. An integral part of the installation of this equipment is making sure the excavator is setup correctly for the bucket to do its work. If the excavator isn’t set properly, then the bucket won’t function to specification. The hydraulic multimeter enables the measurement of flow, pressure, peak pressure, temperature, hydraulic power, and pump volumetric efficiency. As part of a predictive maintenance program, measuring a pump’s volumetric efficiency by determining its loss of flow with increasing pressure is one of the best ways of assessing the pump’s condition. The in-built loading valve of the hydraulic multimeter means that this measurement can be simply carried out independently of the machine operation. The unit can then transfer data wirelessly for further analysis or the recording of performance history.
Also useful for system troubleshooting is the versatile HPM7000 Series portable data logger, which, by connecting to suitable sensors, can monitor such properties as pressure, flow, temperature, frequencies, speeds, and fluid contamination. This base model can be extended by the use of plug-in input modules to extend the number of CAN bus channels that can be monitored or for interfacing with analogue sensors using voltage or current outputs. The unit has a variety of different modes with the ability to data log 16 million measured values per test at a variable interval sample rate as short as 1ms and with a total possible storage size of 12GB.
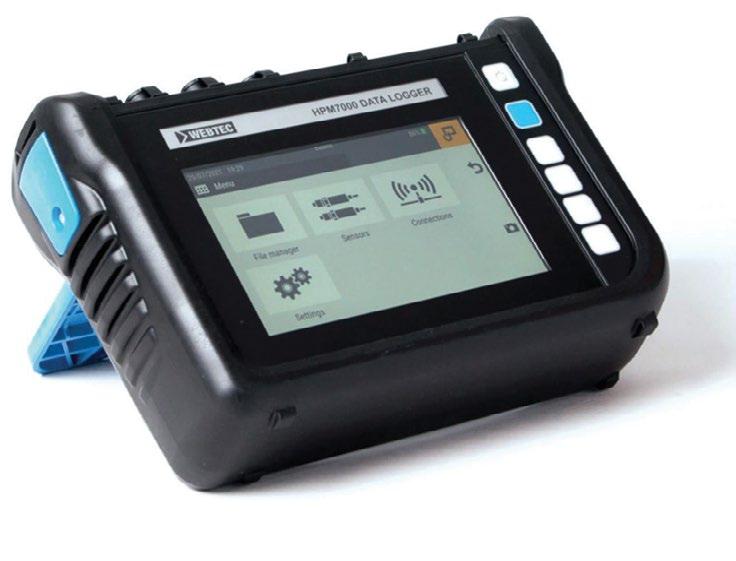
Many leading OEMs in the crushing and screening industry have come to rely on Webtec’s wellproven products owing to their performance and reliability while operating under the harshest of conditions found in this industry. •
A total pump failure, for example, not only results in lost production while the pump is being replaced, it may require a considerable amount of time and effort to flush the system of contamination to avoid subsequent failures.
The RFS 200 flow hours counter is another new device used with a preventive maintenance program. Installed in the input or output line of critical hydraulic components, it monitors their actual usage time, thus enabling routine maintenance to take place when the component is approaching the end of its useful life. Compared to monitoring engine run time, the flow monitor can record individual component usage in applications where not all machine functions operate continuously.
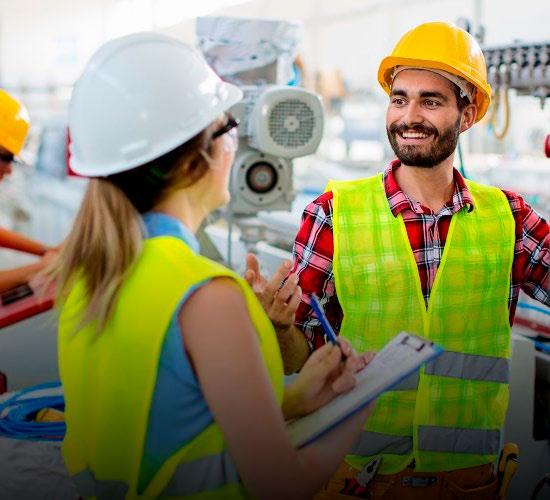
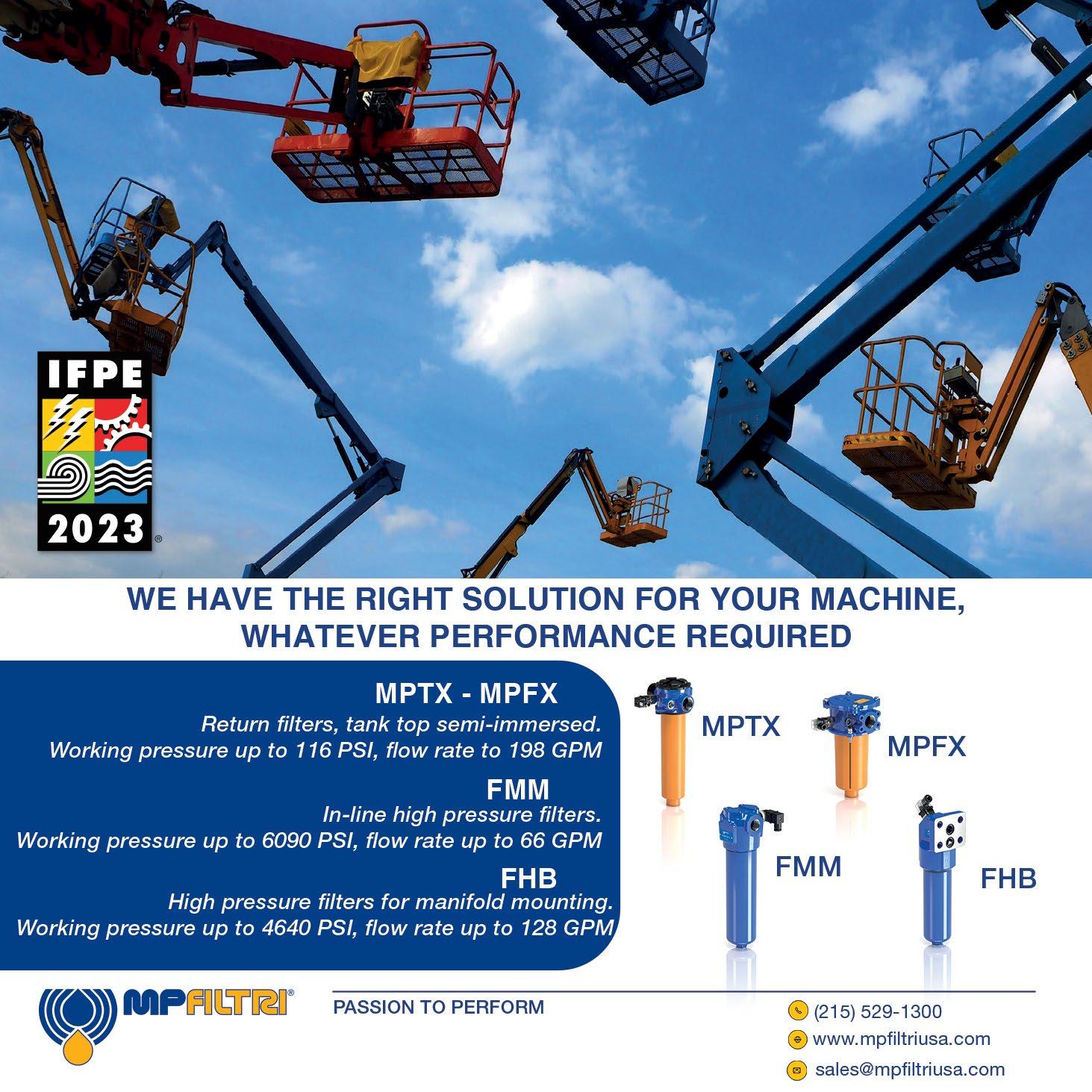
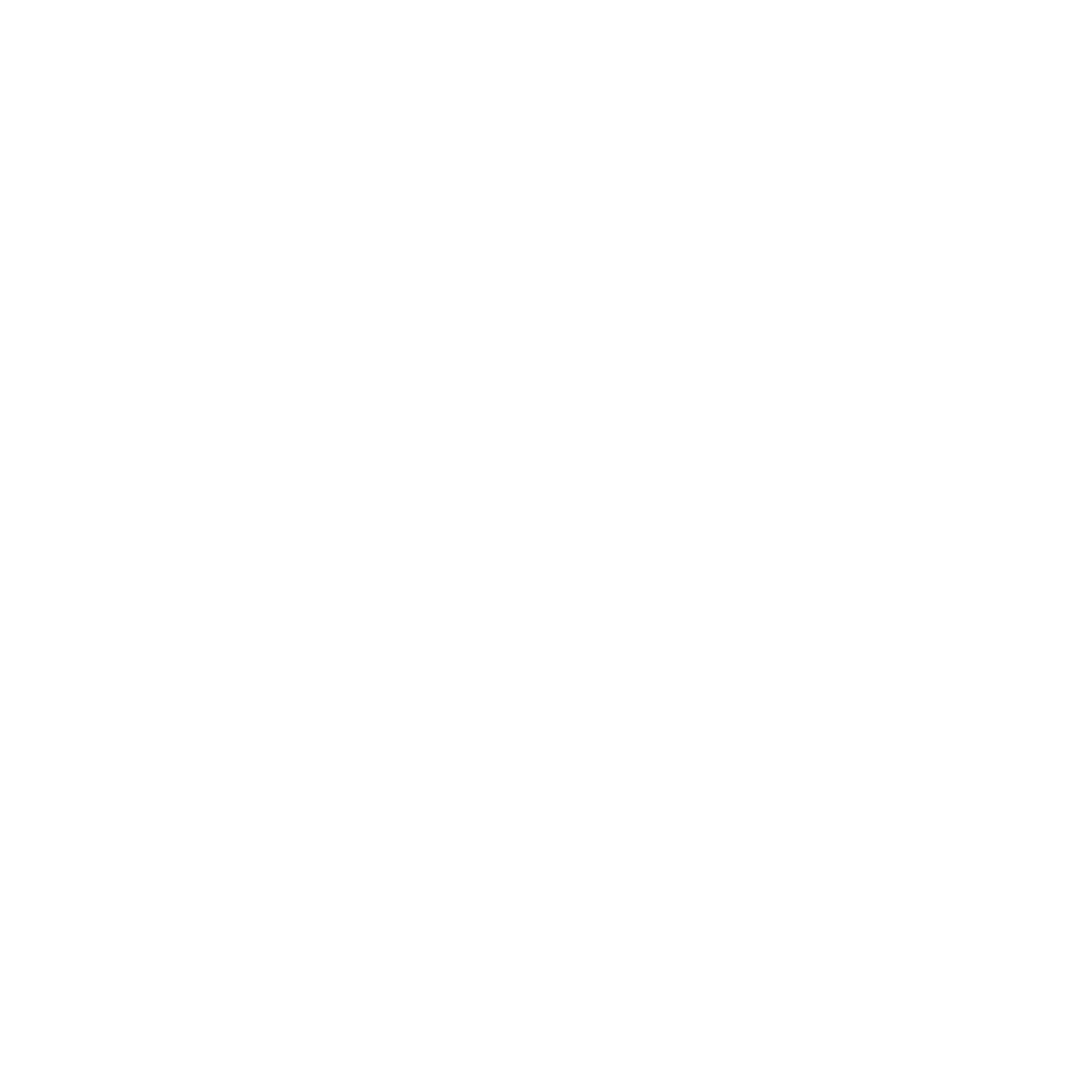
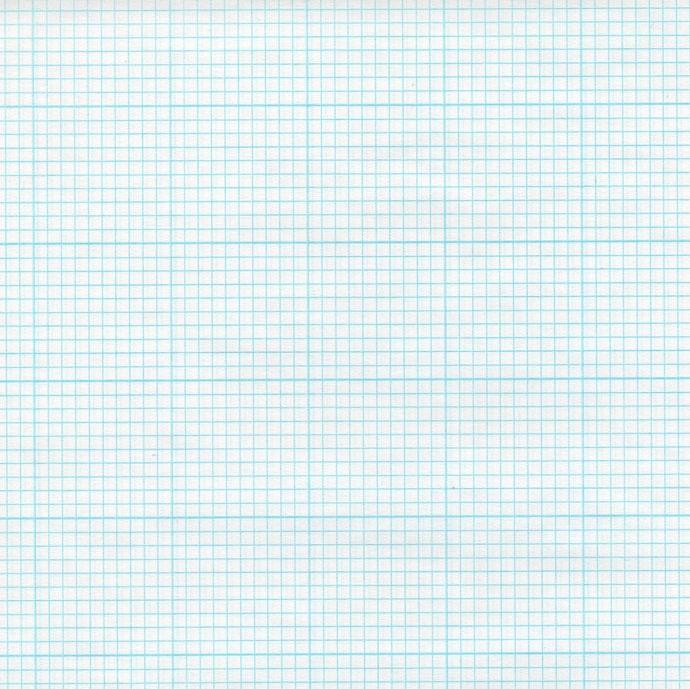
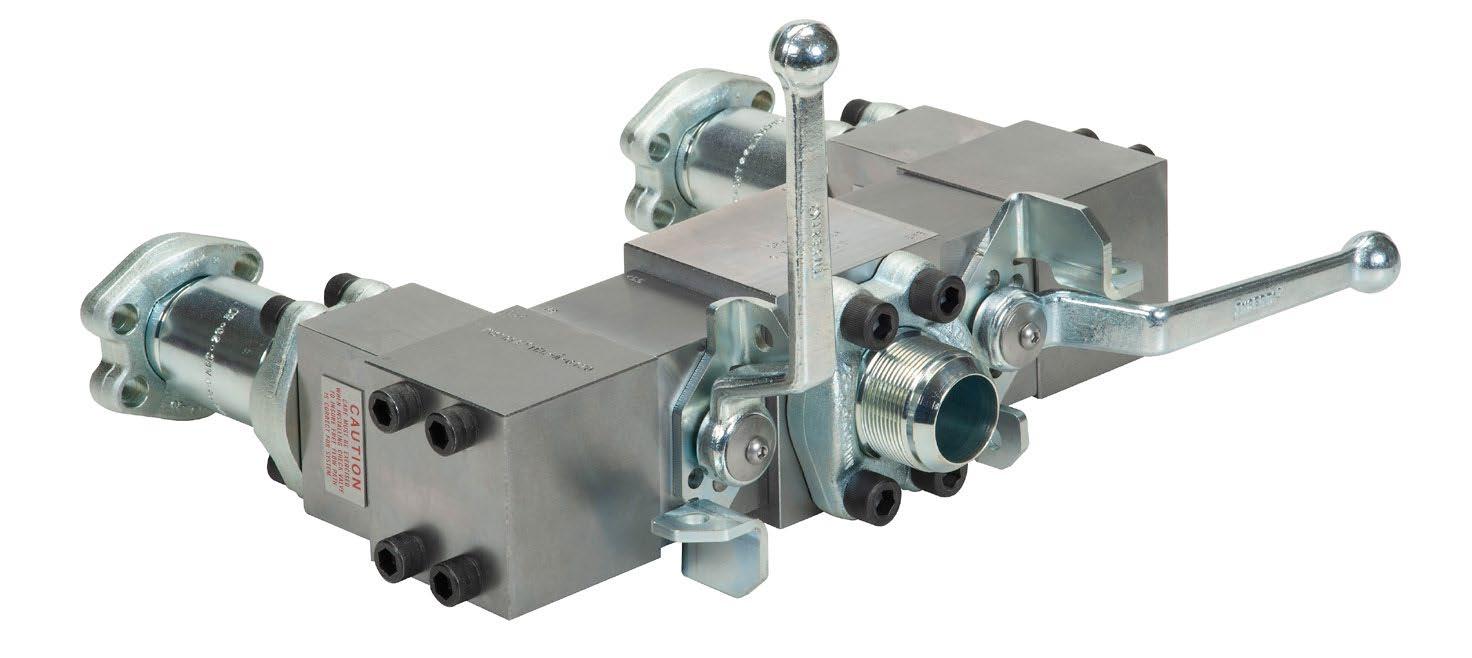
Surround Sensing for Mobile Machines
By Enrique Busquets, Director, Product Area Mobile Electronics and Electrification,
Worksite safety – protecting operators and equipment from collision and damage – has always been a high priority for the off-highway industry. Whether at construction sites, agricultural fields, or road-building locations, keeping personnel safe from dangerous accidents and reducing machine damage from collisions has been the focus of many different kinds of efforts and investments.
Worker safety training and well-established, properly followed worksite safety procedures will always have an important role in these efforts. However, there is a significant opportunity for mobile machine builders to design features and capabilities into their machines that can enhance their safe operation.
To satisfy these goals, mobile machine builders are beginning to incorporate a range of new surround sensor technologies designed specifically to improve collision avoidance capabilities and enhance operator focus and situation awareness. This technology is being made available in modular, integrated platforms that include radar, ultrasonic, and camera components that can be software-integrated, making it easier for machine builders to integrate within their existing machine platforms.
Status of surround sensing
Until recently, there had been limited investment by machine builders in the use of available surround sensing technology to improve the level of “situational awareness” crucial to improve jobsite safety. In agricultural applications, machine builders have been adding backup cameras to allow them to reverse a tractor more easily or combine and hitch to a piece of equipment.
In general the kinds of sensing technology now widely used in passenger and commercial on-road vehicles to provide driver alerts and collision avoidance capabilities have not been extensively exploited. This is, in part, due to the need to “ruggedize” these electronics for use in machines operating in more demanding environments and in equipment that typically generates higher levels of vibration that can rapidly degrade electronics.
The value of surround sensing is providing operators with a new array of sensory information about the risks and obstacles, both fixed and moving, that they could encounter operating their equipment. One of the challenges associated with introducing vision systems, radar, and ultrasonics into mobile machines is the greater complexity of their operating environments, relative to commercial and passenger vehicles.
Compared to straightforward roads, driveways, and parking lots, risk conditions on a construction site or vegetable field can pop up randomly, which makes seeing the next risk more difficult.
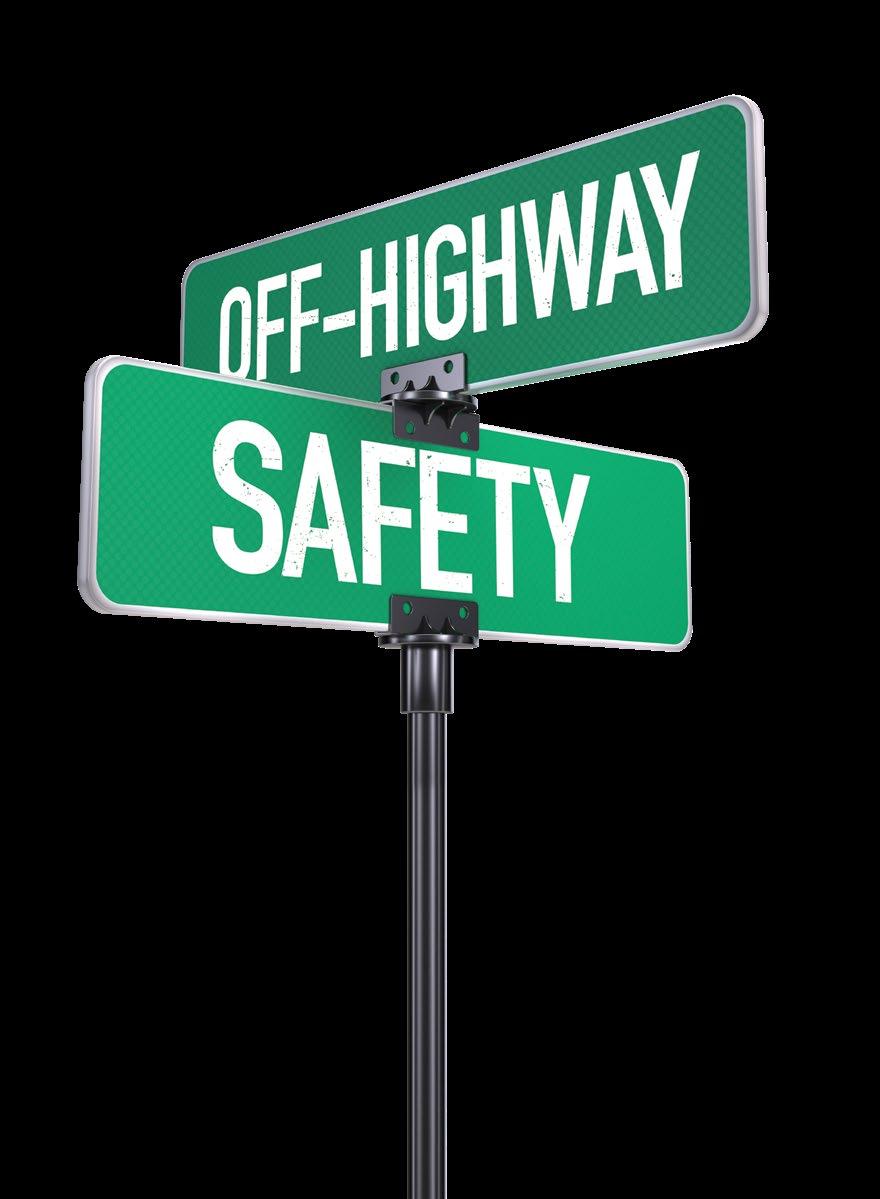
The new surround sensing technologies need to be carefully selected and integrated into a given machine, based on that machine’s functions and the characteristics of its operating environment. So while each off-highway application is unique, there are three common principles that can be used to guide which types of sensory systems to use and how to integrate them into the machine.
Collision avoidance. Collision avoidance is the most easily recognized surround sensing capability. To varying degrees, cameras, ultrasonic sensors, and radar can all contribute to warning an operator of the imminent risk of collision and either alert them quickly enough to stop or change course, or automatically halt the vehicle.
Accomplishing some of these goals, including automatic stopping, will require integrating the surround sensing inputs into the overall vehicle operation; it may also call for more sophisticated controller hardware and software, as well as making sure that an off-highway vehicle’s CANbus network can support the added data from the sensors.
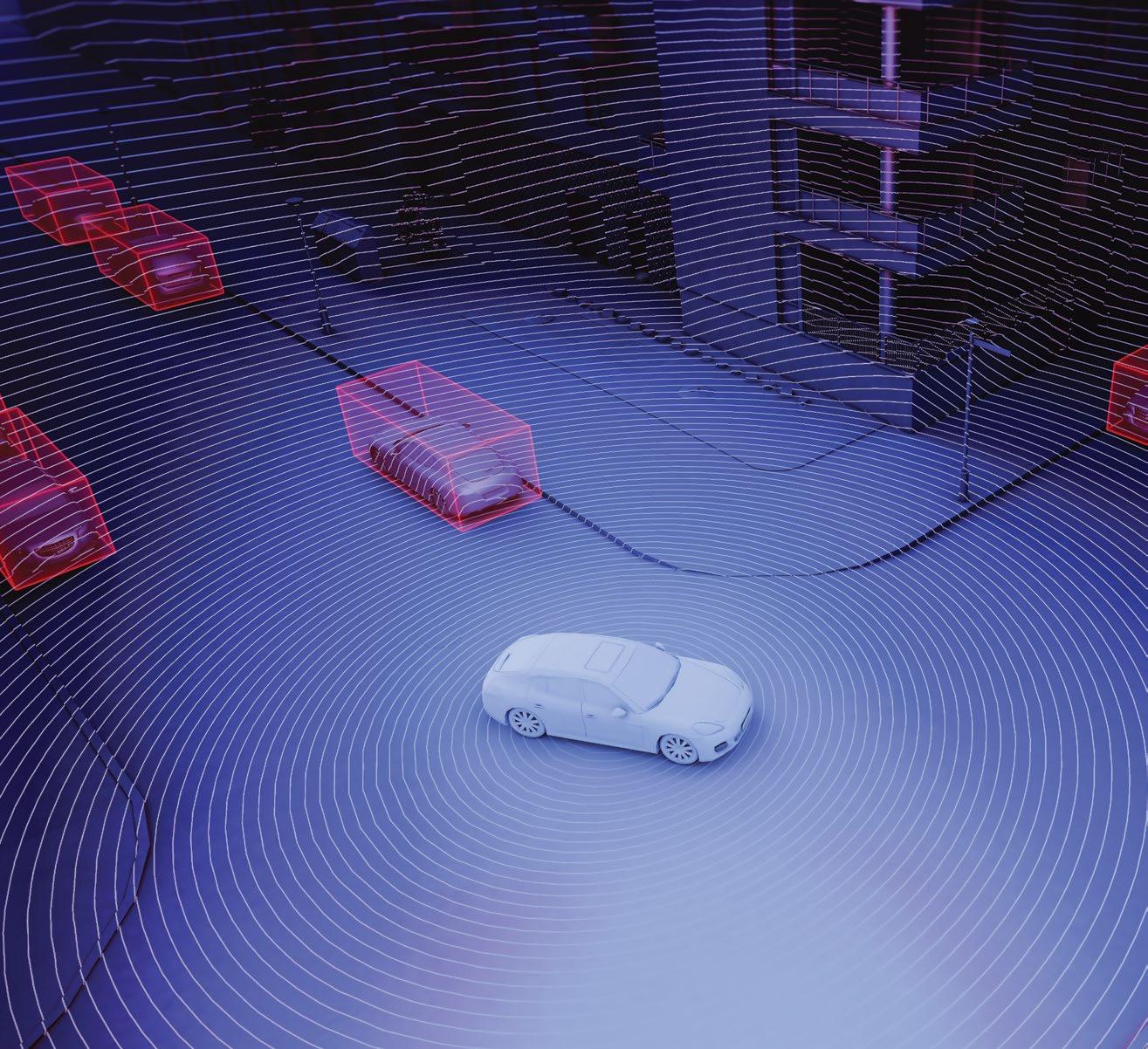
Focus on the job. Experienced equipment operators are typically well-trained in situational awareness. But it does demand, to a certain extent, that their attention be somewhat divided. A forklift operator pulling skids of material from shelves in a large warehouse has to simultaneously manage the skid removal task and constantly double-check that the backup space is safe and unimpeded.
Self-explanatory operator assistance. One of the advantages of this new generation of mobile machine sensors is that, combined with the more advanced controllers and software now routinely used on off-highway equipment, operators can be supplied with information that is literally self-explanatory. For example, video combined with ultrasonic sensors can be utilized with specialized operator cab displays to indicate which obstacles in the path of travel have a lower or higher risk of collision.
Leading technology suppliers like Bosch Rexroth are now offering these sensor portfolios in modular packages. They can also supply key insights into the right sensors, or combination of sensors, and will provide the greatest enhancement to operator safety and reduction of worksite accidents and collisions.
Each mobile machine, and the operating environment it is engineered for, presents unique working conditions and application requirements that can help determine the appropriate surround sensing technologies for a given application.
Multicamera vision systems
As noted earlier, camera systems are not yet widespread options for off-highway equipment. There is a new range of camera systems now available that have been adapted from passenger and commercial vehicles, and improved to provide long-term performance in the more demanding off-highway applications.
There are now multicamera systems that provide high-quality imaging with other features that make them a powerful tool to keep operators fully aware of surrounding conditions. After all, our strongest and most fast-acting sense is our vision.
These multicamera systems have high-resolution imaging of 1200 x 800 pixels. They also come with a specialized controller/CPU that provides best-in-class stitching together of the images, as well as zoom functions and the ability to add graphical overlays.
These more advanced features make multicamera systems, with their ability to provide a 360-degree view of conditions, a more effective tool for improving safety. The new systems take into account operating characteristics such as vehicle speed, steering angle, and drive direction to continuously stitch together a coherent image. They also feature detailed guidance on where to position the cameras on each vehicle’s exterior for the most effective coverage.
Ultrasonic sensors for mobile machines
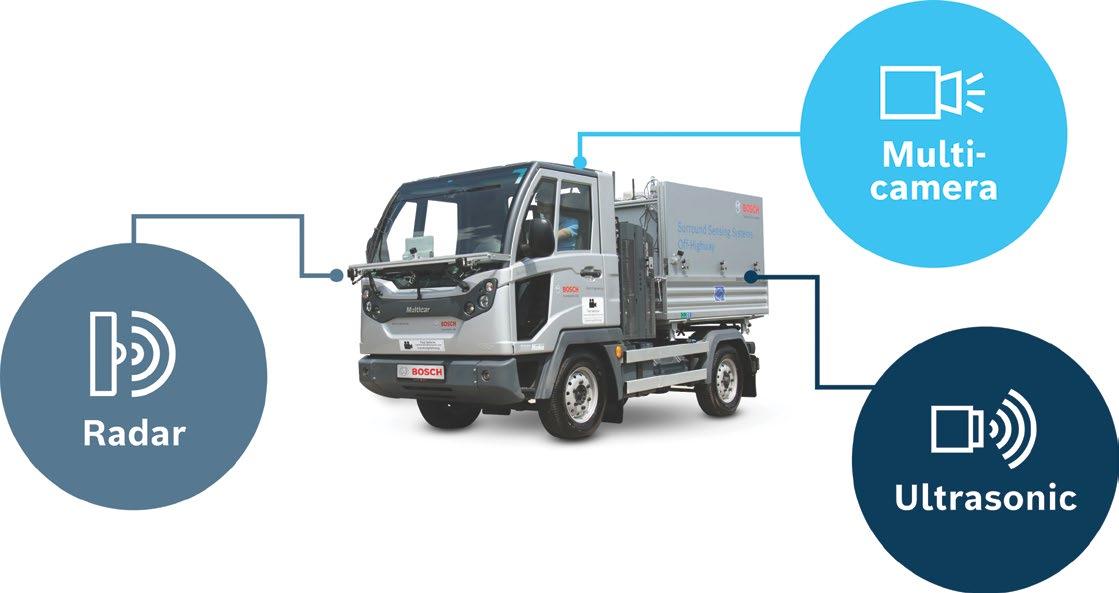
Ultrasonics can provide highly valuable short-range operating conditions. These sensors have been adapted from the latest generation of automotive sensors, with configurations that can range from one to 12 sensors, depending on the size of the machine and its typical operating environment.
The software has been created to achieve measurement rates of up to 120 milliseconds. In the kinds of sensors now available, ultrasonics provide an accurate description of static or moving objects and obstacles as close as 15 centimeters to 5 meters away, depending on the signal resolution.
Applications in which ultrasonics makes the most sense are those with tighter operating environments and many static and moving obstacles, like skid steer loaders on construction sites. A key aspect to assess of these ultrasonic platforms is how they generate and process signals from multiple sensors.
Some systems will actuate all the ultrasonic sensors at the same time. But this runs the risk of generating false positives or negatives and other noise that can impact the quality of the sensing. More advanced systems trigger the sensors in precisely controlled sequences and process the ultrasonic echoes rapidly to capture a much more accurate portrait of the surrounding system.
In some more advanced applications, the ultrasonic data can be overlaid on the 360-degree video inputs, with colored graphics indicating which obstacles are closer and of higher risk.
Radar for fast-moving machines
While ultrasonics can provide obstacle data from close-at-hand objects, there is a significant role that radar can supply for situational awareness and surround sensing. Radar is most useful for detecting objects farther off than ultrasonics, and it can detect risks while a vehicle is in rapid movement.
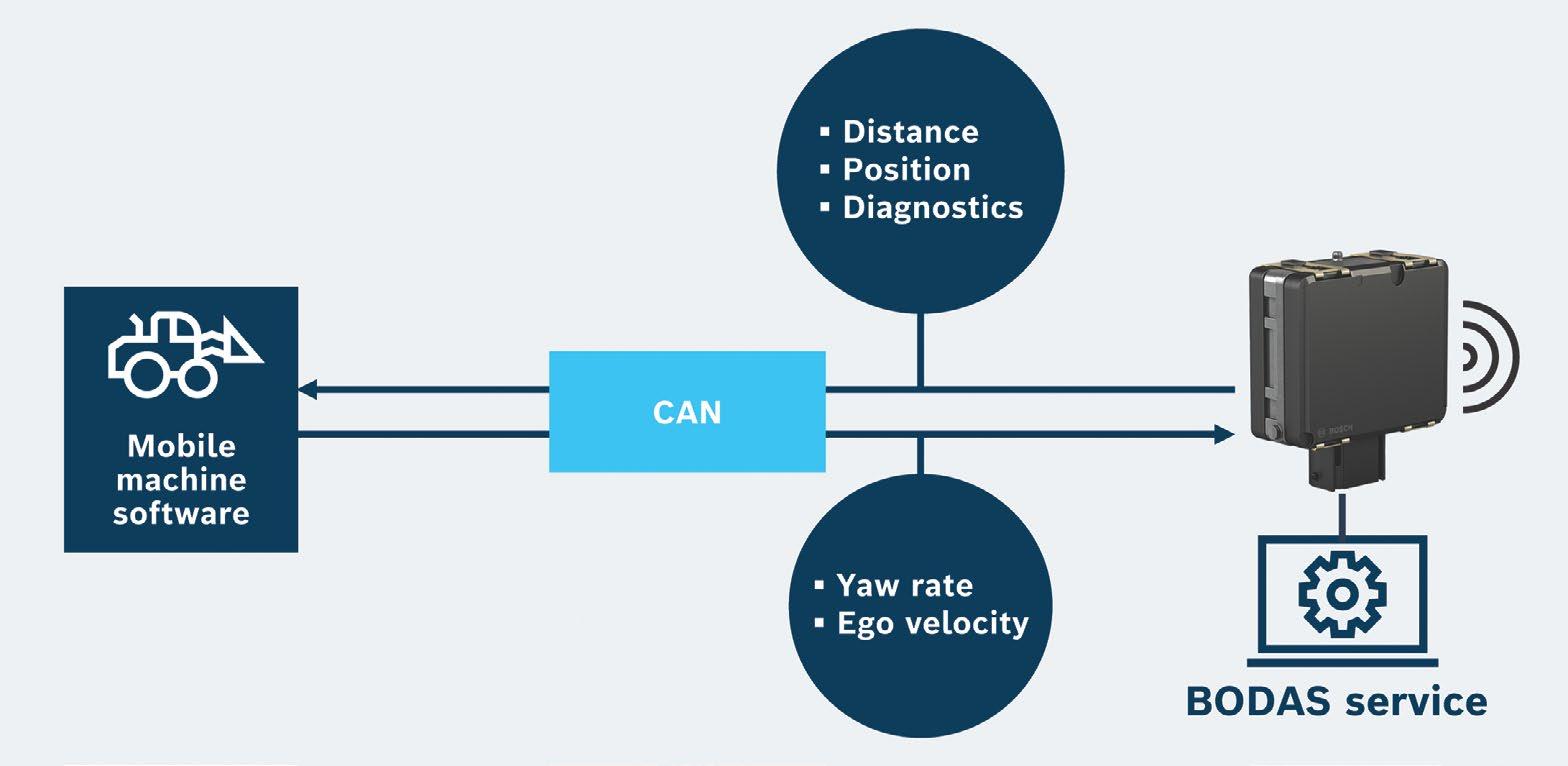
There is a wide range of construction and agricultural equipment that also has to travel significant distances on roads at speeds up to 40 kilometers per hour. Radar-based collision avoidance systems offer the highest degree of safety for these vehicles when they need to operate on the roads.
The radar systems being offered by leading suppliers feature both near- and far-range integrated antennas and ground-detection filters, and can detect and track up to 40 objects simultaneously.
Since each mobile machine has unique operating characteristics, there may not be a need to have all three kinds of surround sensing technology – cameras, ultrasonics, and radar – incorporated into one piece of equipment. However, many widely used machines could benefit from all three.
Wheel loaders used on construction sites often drive at high speeds from one part of a site to another or to another. At the same time, a wheel loader’s work often involves them in tight situations where ultrasonics play a more valuable role.
And in these wheel loaders, the operator cab is typically mounted high on the machine because the operator needs a 360-degree view of the surroundings. Additional multicamera displays augment the view. Combined with the potential for graphic overlays of the ultrasonic sensors, their ability to focus on the job and have self-explanatory data on risks can improve safety and reduce the risk of accident.
New generation of sensors
To make the best use of this technology, mobile machine builders who consider the potential advantages of the new generation of surround sensors will need to assess how to modify the design and engineering of their systems.
First they’ll need an intelligent assessment of which of sensor packages make the most effective contribution to safety, based on a machine’s dimensions, operating conditions, and demands on the operator.
Machine designs may need to be modified with expert guidance. Mounting brackets and wiring harnesses must be carefully selected, with particular care about exactly where cameras or ultrasonic sensors are placed to provide the most effective system performance.
Modifications to HMI displays may also be needed so video can be easily integrated. There will also need to be an assessment of controller capabilities and communications backbone. In the case of high-quality video, Ethernet-based connectivity may be needed on the machine.
The right high-performance surround sensing technology offers the potential to significantly enhance safety on the jobsite and out in the field. It can reduce operator stress with assistance systems that make it easier to keep them situationally aware of risks around them.
The systems have now been optimized and ruggedized for the off-highway machine environment, offering a new suite of tools to improve safety, reduce the risk of accidents and equipment damage and ultimately help off-highway operations run more smoothly. •
Ashcroft S1 OEM Pressure Transducer: High Quality, Economical and Built to Last
Get reliable pressure measurements with an economical transducer for demanding OEM applications. The Ashcroft® S1 OEM pressure transducer is designed to meet the requirements of mobile hydraulic, off road vehicle, construction equipment, performance racing, agriculture, and refrigeration applications.
The S1 is constructed for high-volume manufacturing, allowing Ashcroft to offer a high-quality transducer at a cost-effective price with quick lead times to meet OEM needs. Its features include:
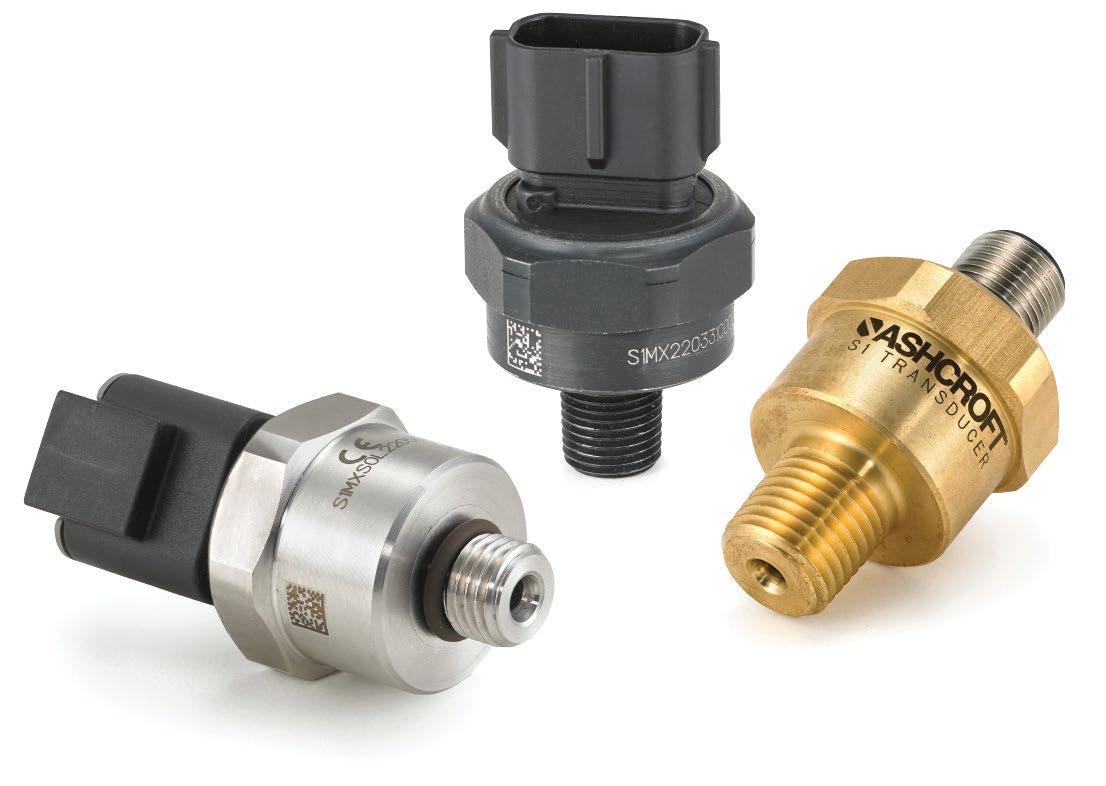
• Reliability: Field-proven, all stainless-steel thin film CVD-based sensor technology for exceptional cycle life and repeatability, and pressure ranges that span from vacuum up to 10,000 psi
• High vibration and shock resistance: CVD sensor with added vibrationresistant technology includes a cushioning media applied to wire bonds and points susceptible to high vibration for increased protection
• TruAccuracy™ performance: Ensures rated accuracy out of the box, so it’s ready for installation with no additional calibration adjustments required
• Protection: IP65 or IP67 levels of ingress protection (depending on electrical connection used) and the ability to operate in temperatures from -40°F to 257°F (-40°C to 125°C)
• Flexible construction: Wide range of process connections, electrical connections, outputs and pressure ranges along with fitting materials to meet your needs
1
QUICK: MAIN has a large and diverse inventory, including specials for same day shipping. MAIN’s US production facility, specialized manufacturing processes, and large raw material inventory allow your custom non-stock parts to be shipped in days. 2
INFORMED: MAIN’s engineers are active on ISO and SAE committees. They are available to assist you with your flange needs, call 800.521.7918, e-mail to info@MAINmfg.com or fax 810.953.1385.
3
DEPENDABLE: MAIN has 60 years of experience in designing, developing, manufacturing and distributing quality hydraulic flanges and components.
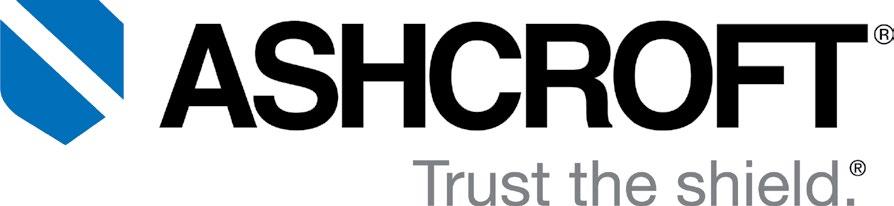
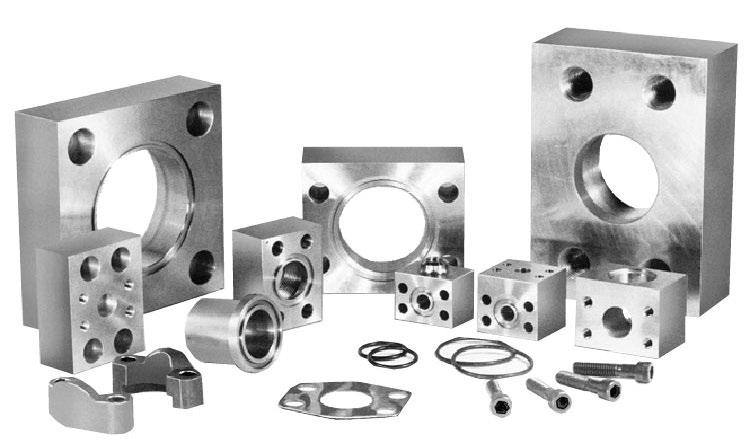
Grand Blanc, MI 800.521.7918; FAX: 810.953.1385
E-mail: info@mainmfg.com
Web: www. mainmfg.com/fpj
UC-CSS-230V-AK
Our 230v Air Knife allows you to shrink a Clean Seal Capsule onto a hose, tube, or pipe assembly in under one second. A single pass through the Air Knife is all that is needed to fully seal single or multiple assemblies. A Magnetic puck ensures that the capsule is held on properly, allowing for easy capsule sealing on 45° or 90° fittings. A large 110mm Air Knife opening allows for sealing fittings up to 3”.
Main benefits of the UC-CSS-230V-AK and Clean Seal Capsules include:
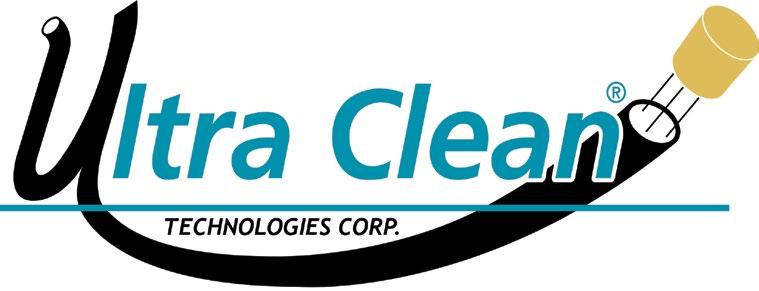
• Save time by sealing multiple assemblies in under one second.
• Eliminate excessive Injection molded cap and plug inventory.
• Clean Seal Capsules stay on until you're ready to remove them with the built in tear strip.
• Eliminate re-contamination during transportation and storage.
• Provide a tamper-proof seal of hose and tube assemblies.
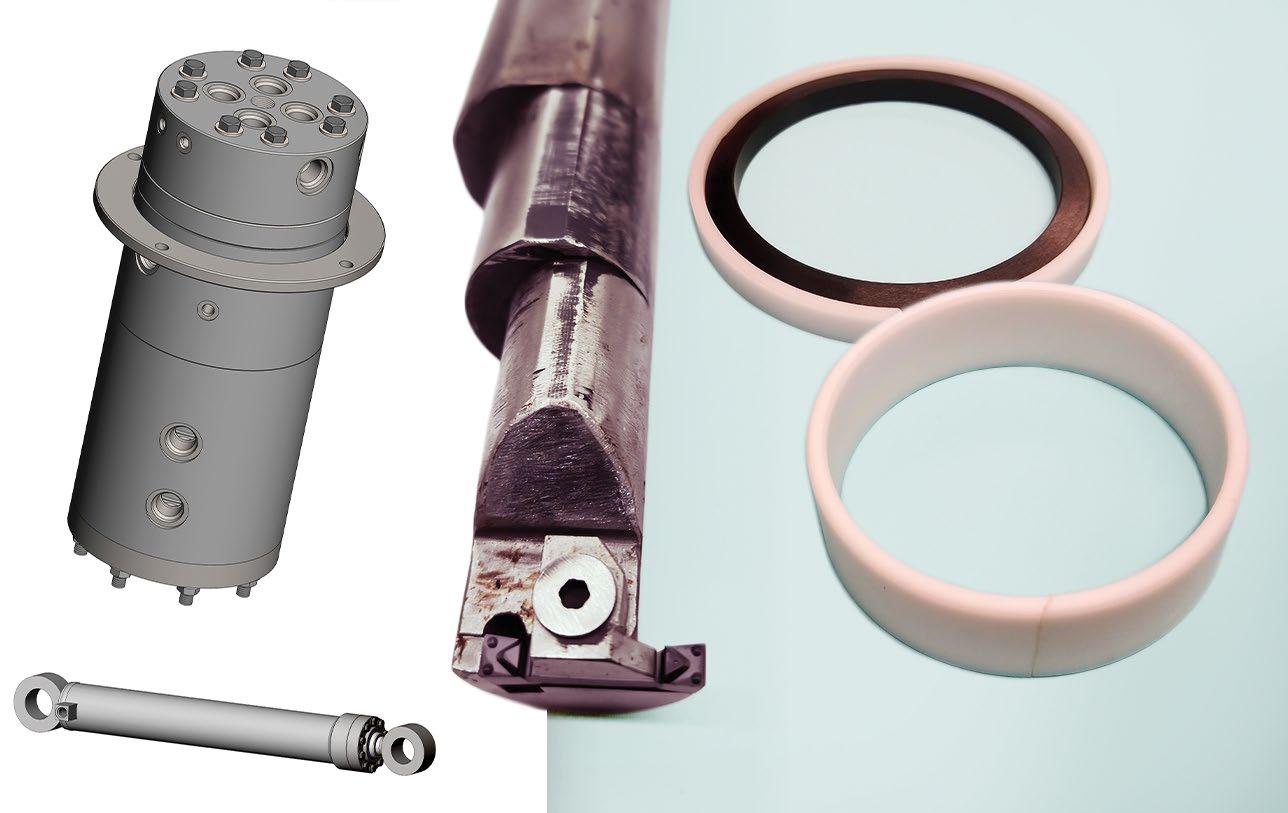
StepLock Piston Seals
These seals are designed for 7,000 psi working pressure and pressure spikes to 20,000 psi.
Lap Cut Wear Rings
Replace glass filled wear rings with precision machined POM wear rings that are lap cut to improve the life of all hydraulic system components, and to reduce breakage from pressure spikes.
6,000 psi Cylinders
We offer Attachment cylinders for shorter stroke applications that see higher work induced compressive forces, and the long stroke cylinders that are designed for longer stroke applications that see higher work induced tension forces.
6,000 psi Rotary Unions
Our 6,000 psi rotary unions are made to order. These can be built with most common port sizes, have 1 or more passages in and out, and a center port for electrical.
Our newest product is Manchester replacement ID grooving inserts, in steel cutting grade. These are used with our stepped boring bar, which can fit into bores of 1.181” up to 2.16” deep, bores of 1.475” up to 3.55” deep, and bores of 1.831 up to 5” deep with a maximum groove depth of .315”.
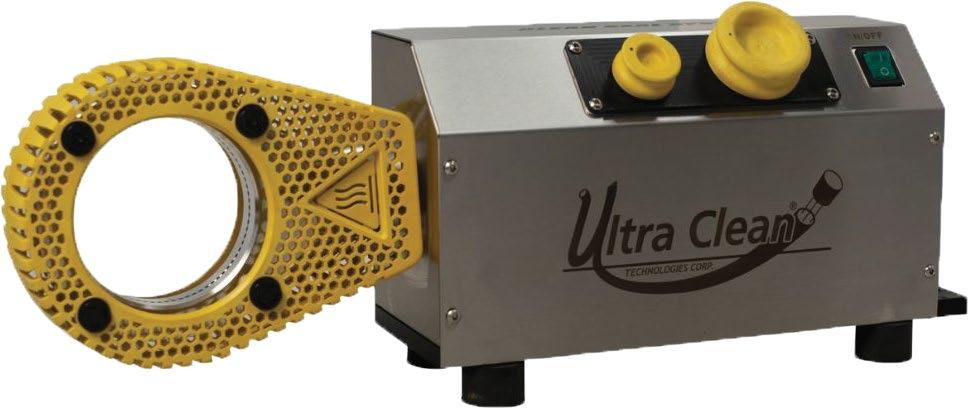