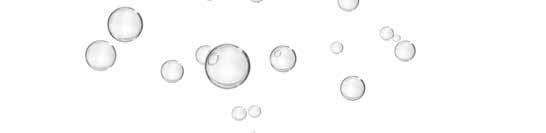
33 minute read
Cover Story
ELIMINATING WATER contamination

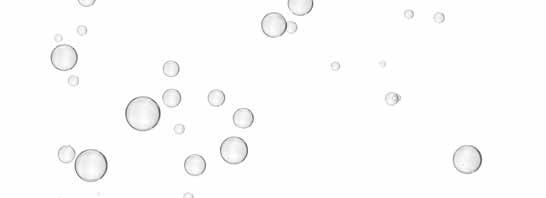

IN AIR SYSTEMS
By Michael Schapoehler, Product Technology Manager, Airline Hydraulics Corp.
In the dog days of summer, people often say, “It’s not the heat, it’s the humidity.” This is true – on a hot day, it’s often the humidity that makes us suffer most. Unfortunately, pneumatic machinery also suffers from an increased likelihood of water in its air lines.
How water forms in air lines
One of the most prominent triggers for excess water in pneumatic air lines is an increase in temperature. When temperatures rise, water evaporates and increases humidity, meaning there is a higher amount of water particles in the air. Since pneumatics rely on this air, it’s not surprising that systems release a significant amount of water during the hotter months. In fact, a 25-horsepower compressor can release more than 18 gallons of water in one day during the summer.
Another trigger for excess water in an air line is fluctuation in air temperature. If the air temperature drops lower than its dew point (the atmospheric temperature at which water droplets can condense), water vapor condenses to form water. At this point, the relative humidity has essentially reached 100%. A typical example of this phenomenon is when, on a hot day, droplets form on a glass with cold drink.
The same thing happens in pneumatic systems. Temperature fluctuations in day-to-day operations, or throughout the system itself, could potentially cause a similar “dew” to form within the system. If the air is carrying water vapor and goes from hot to cold within the line, vapor will condense to form water that will likely accumulate throughout the system.
It is a natural occurrence for water to be present in the air and fluctuate between its gas and liquid states. So why is it so harmful to pneumatic processes and machinery?
Why water must be removed
Even a small amount of water within a pneumatic air line can result in big issues. Here are a few problems that occur when excess moisture goes unchecked. Loss of component lubrication. Pneumatic components are prelubricated at the factory. Water in a compressed air system compromises this lubrication and even has the potential to wash it away entirely. Unfortunately, many components rely on this lubrication to function correctly; without it, they are subject to premature wear and failure. It does not take much water to wash away the lubrication from smaller valves typically found in pneumatic systems. Within these components, rubber seals are prone to swelling, stiffening, and deterioration when subject to moisture.

Bacterial growth. This moisture can also lead to the growth of bacteria and microorganisms in pipes and components. Some of these organisms can survive and multiply in higher temperature ranges, such as 45°C to 90°C (113°F to 194°F); others need lower temperatures, ranging from 25°C to 40°C (77°F to 104°F). However, the one thing they all need is moisture. Pneumatic lines can become breeding grounds for bacteria and mold that can gunk up components and cause health and safety concerns. Pipe scale and rust. Moisture also wreaks havoc on piping through the formation of pipe scale and rust. This buildup accumulates to decrease the pipe’s interior surface area, which increases the pressure loss as air passes through and reduces the system’s overall performance. Over time, the pipe scale and rust detach from the piping, traveling through the pneumatic system and causing further issues.
Pneumatic components are intricate, precise, and relied on to make a pneumatic system run properly. When components become clogged with debris, a machine cannot operate at full capacity and may even
A tiny valve can quickly become clogged with corrosion, rust, or pipe scale from water in an air line, leaving small components vulnerable to premature failure.
fail completely. It may require shutdown to assess which component is failing and to then replace that component.
Poor air quality for important processes.
When compressed air is used directly in a product or process, it’s even more critical to remove moisture and its byproducts like bacteria, rust, and debris. In the simple process of cleaning parts and products using a blowgun, for example, a moist blast of air could carry rust, mold, and bacteria.
Another process sensitive to the effects of water, bacteria, and particulate is a paint booth. Paint is precisely mixed with other chemicals to provide an aesthetic and protective coating to a product. If the pressurized air used to apply this finish is compromised, the impurities adversely affect its color, adherence, and quality. The painted item would be less protected from the elements and possibly suffer from premature wear. These are just two common processes that suffer from poor air quality, but there are many more depending on the application and industry. Increased costs. For original equipment manufacturers and machine builders, it’s costly to assume the end user will have clean, dry air flowing through the system. This assumption often results in premature wear and breakdown of the machine, which leads to increased time and resources to travel to the facilities, troubleshoot, and service the machines.
End users need clean and dry air because they rely on the machine to operate without problems; their income often depends on it. At best, water damage will cause unplanned work stoppages to replace damaged components. At worst, it creates long downtimes to troubleshoot, source and purchase components, or get the machine serviced. If portions of the final product come into contact with moisture and debris from compressed air, latent damage and quality issues can occur. These scenarios all lead to reduced profits, which is especially harmful to businesses running off thin margins.
Removing water
Here are a few best practices to decrease or prevent moisture accumulation. Drain the air compressor. Air compressor tanks often contain a drain at the bottom so that collected water can be released. Be sure to drain the tank after each use of the air compressor to prevent a consistent buildup of water. Drain the air compressor regularly, especially during the hotter months. If the air compressor is continuously under high demand, empty the tank frequently. Create consistent temperatures. Pay attention to differences in temperatures within the system. Water vapors turn into liquid water when passing from a warmer to a colder area. Knowing this, design a pneumatic system to avoid these temperature changes.
For example, air compressors are noisy, so designers may put them outside or in a non-temperature-controlled room away from the rest of the system. During the hotter months, that compressor delivers

hot compressed air to cold indoor areas. This setup is a recipe for condensation since warm air is running through cool pipes. By placing the air compressor in a similarly temperature-controlled room, the condensation may significantly reduce. Choose pipe material wisely. As noted earlier, water wreaks havoc on air piping and creates rust and scale. Carefully select pipe material to reduce these risks. Some materials, such as steel, are prone to rust and scale. (Continued on page 14)
EVERY Part Matters!
PENINSULAR® CYLINDER CO.






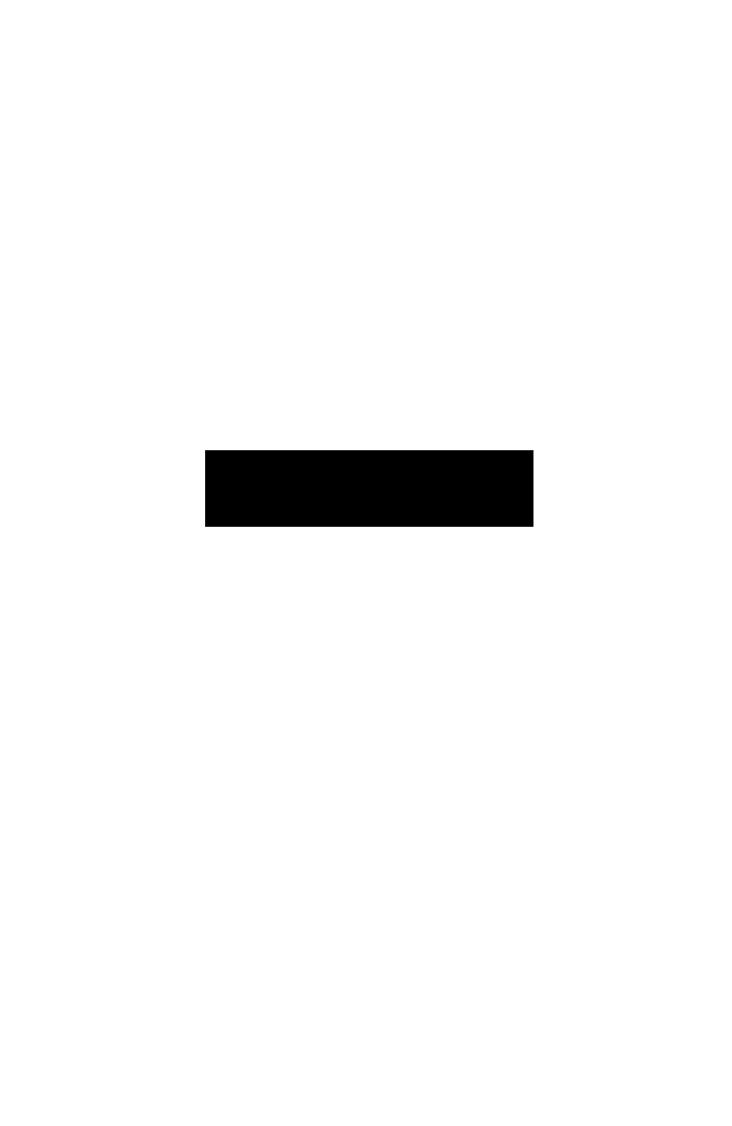

Hydraulic • Air • Custom Cylinders
Let’s Talk Cylinders 800-526-7968 www.peninsularcylinders.com
(Continued from page 13) Other materials, such as marine-grade aluminum pipes, are more resistant to rust and help prevent oxidation-based contamination. Implementing a piping system with cleaner interior surfaces decreases issues related to moisture buildup and increases smooth, laminar airflow. Adjust piping direction. As water vapor condenses and becomes liquid, it typically collects and pools at the bottom of the pipe. One way to prevent this water from entering the rest of the system is to adjust where other pipes connect to the main line. Connecting these pipes to the top of the air line instead of the bottom, where the water collects, is likely to provide dryer air into the rest of the system. This method does not eliminate water but helps minimize damage that could occur further down the line.
Products to remove water from air lines
If those best-practices aren’t applicable to a system or aren’t enough to prevent water accumulation, some products in the marketplace can help remove excess water.
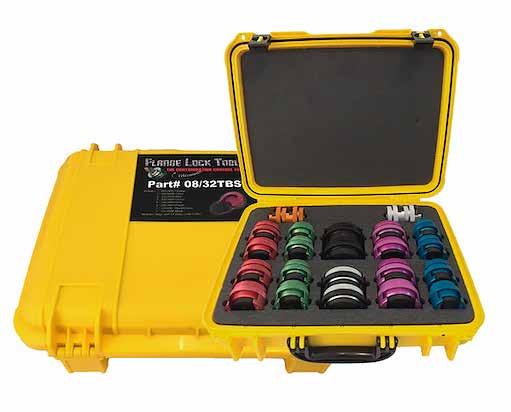
THE ULTIMATE CONTAMINATION CONTROL TOOL
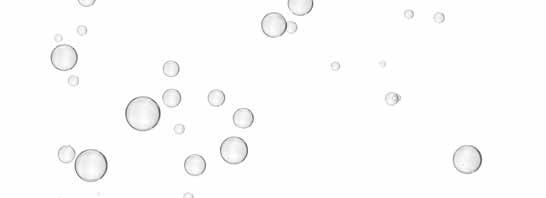
by SMC works well if the system has high
air flow. The AW30 uses a cyclone-effect to

spin the air at high speeds, forcing the water
and debris to the sides of the unit, where it becomes separated and drains out the bottom. This cyclone-effect does require a high amount of air pressure, so if this pressure is lacking, consider a different solution, and larger ones can serve as mainline filters. for removing water from air lines. SWINGFLGLCK2062 Swing hose FlangeLockTM kit Air dryers. Air dryers are another option SWINGCAP2062 Swing circuit cap kit for keeping water out of pipes. Air dryers throughout its air lines. Air dryers exist for TRAVELCAP2462 Travel circuit cap kit water spots from air tools, and liquid coming FRONTATTCAP326162 Front attachment cap kit it is significantly cooled down, which turns the water vapor into liquid water that goes into a water-trap. Then the cold air heats back to room temperature, resulting in
dryer air. A refrigerated air dryer works like a dehumidifier.
such as a water separator. Water separators. Water separators come in a vapor in the lines. The vapor then turns to liquid and sticks to the contents until they are HITACHI FLANGELOCKTM range of sizes to remove water from pneumatic lines. Smaller ones are good for point-of-use, cleaned out. With any air dryer, it’s essential to make sure the air pressure and capacity fit AND CAP KITS AVAILABLE They are one of the most economical options Part number Part description
Desiccant air dryers use absorptive materials, such as silica gel, to absorb the water can help a large facility experiencing water TRAVELFLGLCK2462 Travel hose FlangeLockTM kit
the compressor. Water in pneumatic air lines causes many Applicable machines Number of parts Weight (kg)
issues that can affect a business’s efficiency EX3600, EX5600, EX8000 16 x 2062U - red FlangeLockTM 6.7 and bottom line. Implementing these EX3600, EX5600, EX8000 16 x 2062 - cap 4.5 can help achieve clean and dry air during EX3600, EX5600, EX8000 16 x 2462U - purple FlangeLockTM 7.7
more significant water removal issues, such as widespread rusting and corrosion of lines, FRONTATTFLGLCK326162 Front attachment FlangeLockTM kit cost-effective best practices and products
from hoses and lines. There are two types of air dryers – desic BOOMARCHFLGLCK3262 Boom arch hose FlangeLockTM kit cant and refrigerated. For refrigerated dryers, BOOMARCHCAP3262 Boom arch hose cap kit every season, including the hot and humid EX3600, EX5600, EX8000 16 x 2462 - cap 6.4
months. For help determining which solution is most useful, consult with a professional EX3600, EX5600, EX8000 14 x 3262U - black FlangeLockTM 4 x 3261U - black & silver FlangeLockTM 8.9 to determine the best option for a system’s EX3600, EX5600, EX8000 14 x 3262 - cap 4 x 3261 - cap 9.5 water removal needs. EX3600, EX5600, EX8000 20 x 3262U - black FlangeLockTM 9.9
EX3600, EX5600, EX8000 20 x 3262 - cap 11.3
water condenses through the use of cooling CONTAMINATION CONTROL Routine and scheduled maintenance of hydraulic systems are vital to getting the most out of your Hitachi Mining Excavator. While maintenance plays the largest role in the prevention of unnecessary machine downtime, it can also expose the hydraulic system to high levels of contamination rapidly decreasing component longevity. The importance of contamination control is sometimes
Stop the Mess overlooked when performing maintenance due to incorrect practices being used. THE FLANGELOCK™ TOOL AND CIRCUIT BLANKING CAPS The FlangeLock™ tool and caps are the ultimate contamination control tools for protecting your hydraulic system. The FlangeLock™ allows for the simple sealing of open hydraulic flanges without tools while the caps can be bolted in place of a flange connection. Easy on, easy off, they offer a leak-proof solution to hydraulic systems and environmental cleanliness. FlangeLock™ tools and caps stop the mess.
The FlangeLock™ Tool is the ultimate contamination control tool for protecting your hydraulic systems. It allows for the simple sealing of open SAE code 61, 62 HITACHI MAKING CONTAMINATION CONTROL EASY & CAT-Style hydraulic flanges without tools. Constructed from lightweight aluminum. Hitachi have packaged FlangeLock™ tool and caps specifically for Hitachi mining excavators. The Hitachi customised kits make sure no matter which component routine maintenance is being performed on, you will always have the exact Easy on, easy off. Offers a leakproof solution to hydraulic system and environmental number of FlangeLocks™* and caps to help reduce contamination.

cleanliness. FlangeLock™ Tools stop the mess!*Note: FlangeLocks™ are not to be used under pressure
SAVE TIME SAVE MONEY SAVE LABOR SAVE OIL
This product is Patented, other Patents pending.

• • • No tools required No expensive hardware needed No more rags stuffed into hoses • One hand installation • Eliminate hydraulic oil spills & clean up • Quick installation & ease of usage Call you local Hitachi Muswellbrook representative or the branch on 02 6541 6300 for more information. • No more messy plastic caps • Safe for personnel & environment • The ultimate contamination control tool • Industry acclaimed
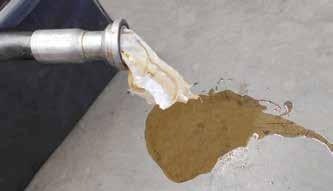
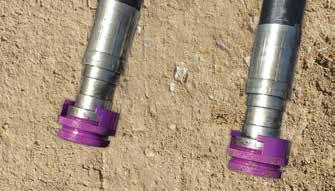
For more information, call 203-861-9400 or email sales@flangelock.com. www.flangelock.com
1000 PSI Nitrogen Pre-Charge
FC-1 FC-2
Sol. 1A Sol. 1B
Set at 2150 PSI
0-3000 PSI
Robert Sheaf has more than 45 years troubleshooting, training, and consulting in the fluid power field. Email rjsheaf@cfc-solar.com or visit his website at www. cfcindustrialtraining.com.
EM 20
Set at 2000 PSI
Solution to
October 2020 problem: Electric Motor Blowing Overloads
Overloads on electric motors are sized to protect the motor. Overloads are caused either by excessive mechanical, flow, or pressure problems. The technician noticed that every time the failure happened, the pressure gauge bottomed out at 3,000 psi (207 bar). The 7½ HP motor with a pump delivering 10 gpm (38 lpm) reached maximum amperage at about 1000 psi (69 bar). When solenoid A is shifted, it opened the pilotoperated check to lower the basket. The flow requirement is very low and the pump is supposed to compensate, providing only the flow required at compensated pressure. We found that the pump compensator was sticking, causing the pump to act like a fixed-volume pump. We also found the safety relief screwed all the way into its maximum of 3,200 psi (221 bar). We confirmed that it was the pump by adjusting the relief to 1,000 psi (69 bar), and the maximum 20-amp rating was not exceeded.
New Problem Cylinder Speed Increases on a Forming Press
By Robert Sheaf, CFPAI/AJPP, CFPE, CFPS, CFPECS, CFPMT, CFPMIP, CFPMMH, CFPMIH, CFPMM, CFC Industrial Training
»A FORMING PRESS had a 3-inch cylinder that increased its extension speed even when no one adjusted the meter-out flow control on the cylinder’s rod side. The customer asked us to check the accumulator’s nitrogen precharge to see if it was low. They knew that lowering the precharge pressure resulted in storing more oil in the accumulator. So they thought the nitrogen gas was leaking off, and they did not have charging equipment with gauges to check it.
We told them they could check it by running the hydraulic pump until the system pressure reached 2,000 psi (138 bar), and then shut the pump down. We told them to slightly open the accumulator valve that dumps oil back to the tank and watch the gauge pressure as it slowly drops off. The pressure reading just before it suddenly drops to 0 psi would be awfully close to the gas precharge pressure. To their surprise, the pressure reading was close to the required 1,000 psi (69 bar).
The customer did not know what to do. Do you?
Automation · Controls · Process
Airline Components for Clean, Dry, Air

A complete line of Filters, Regulators, Lubricators as well as combination units to meet every need. Mainline Filters and Moisture Removal filters also available
Air Dryers
SMC Corporation of America 800-762-7621 www.smcusa.com

Web Marketplace

Emerson.com/ InnovationRoadshow

Access the latest innovations to elevate your operations
Emerson’s unique roadshow experience creates the opportunity to connect with industry experts and the latest product advancements in digital transformation, machine automation and safety.
Connect with us to discover new ways to optimize operational efficiency, improve sustainability and reduce manufacturing costs.
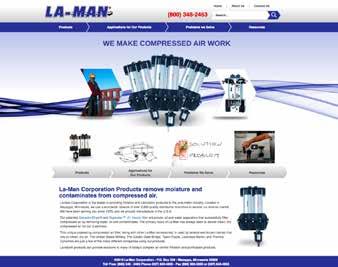
www.laman.com
La-Man Corporation is a leading manufacturer of compressed air filtration products. With over 30 years of experience, we truly understand the importance of protecting valuable machinery, tools, and finished products from dirty, wet, contaminated air. La-Man’s line of products include the patented Extractor Dryer, .01 micron filter, as well as, LA-MAN-Air Breathing Systems™, SuperStar™ Membrane Dryers, and the Refrigerated Extractor/Dryer.
PO BOX 328 • Mazeppa, MN 55956 800-348-2463

www.mainmanufacturing.com
Main's website provides quick access to the 120 page catalog that includes popular styles of MAIN Manufacturing’s extensive offering of carbon and stainless Hydraulic Flanges and Components – ready for immediate shipment. Metric ordering information, weld specs, and dimensional information included. The “Quick Reference Guide” helps specify less popular items often stocked or quickly manufactured (generally 3-4 days) at our US plant. “Create-AFlange” offers more parts than the catalog — by picture. If it’s not here, or for questions, E-mails may be sent to get your answer quickly.
1-800-521-7918 info@mainmfg.com

www.texcelhydraulics.com
At Texcel, our cutting-edge line of hydraulic hose and fittings is not just a product division. It’s a promise of superior service, quality, technical support and availability. We’ve built our company on impeccable customer service. Let us know how we can make a difference for your business.

4444 Homestead Road • Houston, Texas 77028 (800) 231-7116 • sales@texcelrubber.com
CELEBRATING 60 YEARS
IFPS Charts 2021 Projects
»IFPS HELD ITS 2020 annual meeting virtually on Sept. 25. The board of directors approved a number of projects by the education, marketing, membership and certification committees for 2021: • The upgraded Mobile Hydraulic Mechanic certification is in its final stages of development. Areas of the MHM Study Manual that were added and improved include: » Principles of operation explained for commonly found components within a mobile hydraulic system – pumps, valves, actuators, and accessories » Color-coded cutaway illustrations of hydraulic components to aid in understanding operation » Symbology updated to conform to ISO 1219 standard » Expanded content on troubleshooting to include decision-tree aids » Detailed content on pressure, flow, and directional control valves » Improved graphics throughout and many real-life photos to assist in visualization » Basic hydraulic calculations useful in troubleshooting » Safety tips » Basic principles of electrohydraulic control – open loop and closed loop » Electrohydraulic valves » Sensors used in electrohydraulic systems Mentorship Program – A subcommittee will explore mentorship opportunities and the creation of a mentorship program. Nontechnical Associate Certification – A subcommittee will begin writing a study manual for a nonspecialist certification for those who communicate fluid power information such as product part numbers, standard options, promotions, and available services. The Fluid Power Associate certification requires a written test. This certification will be geared toward inside sales, customer service, parts personnel, clerical and support staff, and
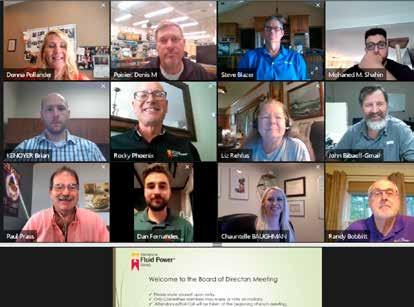

entry level positions. The subcommittee is seeking active certified professionals for technical writing. Fluid Power Symbols Library – A subcommittee will investigate offering the fluid power symbols library to our members.
To become involved in a committee or shortterm subcommittee, contact akayser@ifps.org.
New!

FLAT FACE DESIGN “TVF” SERIES QUICK DISCONNECT
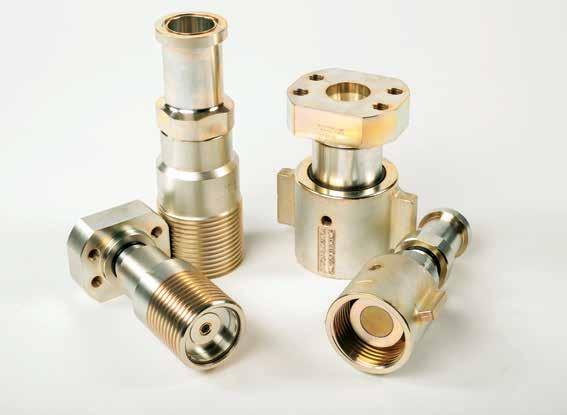
• Up to 6,000 PSI Operating Pressure—Coupled or Uncoupled • Full 4:1 Safety Factor • Superior Flow Characteristics—Minimal Pressure Drop • RoHS Compliant Plating • Multiple Port Options—Female NPTF, Female SAE O-Ring, Female BSPP, Code 61 & 62 Flange Port/Head
P.O. Box 6479, Fort Worth, TX 76115 V. 817/923-1965 www.hydraulicsinc.com
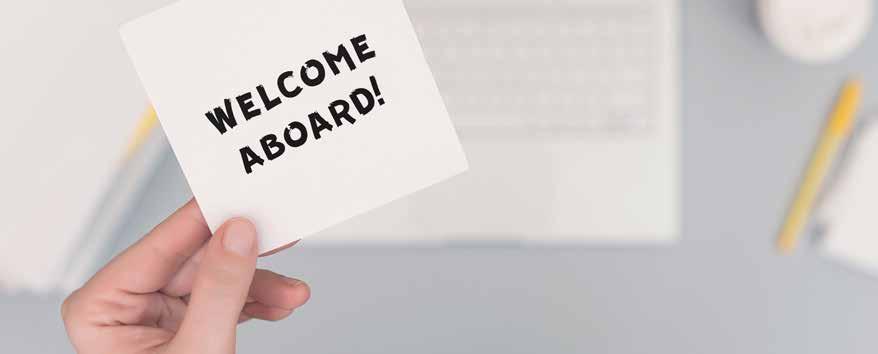
CELEBRATING 60 YEARS
IFPS Announces 2021 Officers
»THE INTERNATIONAL
Fluid Power Society is pleased to announce that Rocky Phoenix, CFPMMH, was elected 2021 president and chair during the IFPS annual meeting. Rocky is the 61st president of IFPS and will take office along with the 2021 board of directors in January.
Rocky served as IFPS membership vice president and is a member of the Fluid Power Hall of Fame selection committee. He has been involved in the fluid power industry for 15 years with Open Loop Energy, Winnemucca, Nevada, working in the mining industry. Rocky is a graduate of North Seattle College, where he earned an associate’s degree in industrial drafting and design. His previous work experience includes many years in the motorcycle and automotive industries. He is an active private pilot.
“I am both excited and honored to be elected president by the IFPS membership for 2021,” Rocky said. “I anticipate a progressive and exciting time ahead for our membership, even in this unique and trying time in our history. I look forward to the progress we will make going forward working with the most knowledgeable and passionate membership I know of in any industry.”
First Vice President: Denis Poirier, Jr., CFPAI/AJPP, CFPHS, CFPIHM, CFPCC – Eaton Corporation Immediate Past President: Jeff Kenney, CFPIHM, CFPMHM, CFPMHT – Dover Hydraulics South Treasurer: Jeff Hodges, CFPAI/AJPP, CFPMHM – Altec Industries Vice President Certification: James O’Halek, CFPAI/AJPP, CFPMIP, CMPMM – The Boeing Company Vice President Marketing and Public Relations: Scott Sardina, PE, CFPAI, CFPHS – Waterclock Engineering Vice President Education: Randy Bobbitt, CFPAI, CFPHS – Danfoss Power Solutions Vice President Membership: John Bibaeff, PE, CFPE, CFPAI, CFPS
Jon Rhodes, CFPAI, CFPS, CFPECS – CFC Industrial Training Steve Bogush, CFPAI/AJPP, CFPHS, CFPIHM – Poclain Hydraulics
Stephen Blazer, CFPE, CFPS, CFPMHM, CFPIHT, CFPMHT – Altec Industries Chauntelle Baughman, CFPHS – OneHydraulics Cary Boozer, PE, CFPE – Motion Industries Lisa DeBenedetto, CFPS – GS Global Resources Daniel Fernandes, CFPECS, CFPS – Sun Hydraulics Brandon Gustafson, PE, CFPE, CFPS, CFPIHT, CFPMHM – Graco Garrett Hoisington, CFPAI/AJPP, CFPS, CFPMHM – Open Loop Energy Brian Kenoyer, CFPHS – Five Landis Corp. Mohaned Shahin, CFPS – Parker Hannifin Randy Smith, CFPHS – Northrop Grumman Corp.
Ex-officio – Donna Pollander, ACA, Executive Director Elizabeth Rehfus, CFPE, CFPS Paul Prass, Fluid Power Journal Robert Sheaf, CFPAI/AJPP, CFC Industrial Training
Special thanks to outgoing past president Timothy White, CFPAI/AJPP, CFPS, CFPECS, CFPMIH, CFPMMH, CFPMIP, CFPMT, CFPMM, of The Boeing Company, and outgoing vice president of education Kenneth Dulinski, CFPAI/ AJPP, CFPECS, CFPHS, CFPMIH, CFMMH, CFPMT, of Macomb Community College, as they complete their tenures on the IFPS board. Their many years of service, commitment, and expertise helped steer the society in its mission. TALKING ABOUT IFPS
How and why did you get involved in IFPS, and what have you gained personally and professionally?
Years ago, I noticed the certification initials on a colleague’s business card. Recently I was reminded that if I only look at a problem from one perspective, my potential solutions are limited. Only looking within my own industry wasn’t using the full potential of fluid power. So I chose to get involved in IFPS to broaden my knowledge base.
John Bibaeff Jr. PE, CFPE, CFPAI, CFPS
I am a strong proponent of lifelong learning. Whether it is through certification, technical training, or academia, continual education is a key part in maintaining relevancy in the workplace. As a professional trainer, certification sends a clear message to those within the industry that a neutral third party has validated my baseline skill sets, both as an instructor and hydraulics professional.
Denis M. Poirier Jr. CFPAI/AJPP, CFPHS, CFPIHM
I became involved in IFPS so that I can help others get the same feeling of accomplishment that I received years earlier. This was my way of giving back to the industry.
Robert Post, CFPHS
»WHILE THE NATION was hunkered down during quarantine, Tom Blansett, CFPAI, Dan Helgerson, CFPAI, and Ernie Parker, CFPAI, were busy conducting free biweekly online study groups. These recorded presentations are available to IFPS members and are especially helpful to those preparing for a certification test. Visit ifps.org/web-seminars to register and view the presentations and others on safety, pneumatics, actuators, hydraulic valves, electrohydraulics, contamination control, pumps, and more. Registration is free for members.
HYDRAULIC SPECIALIST STUDY MANUAL WEB SEMINARS
Outcome 1.2.3: Understand the application of valves – Part 1 Outcome 1.2.3: Understand the application of valves – Part 2
ACCREDITED INSTRUCTOR AUTHORIZED JOB PERFORMANCE PROCTOR AUTHORIZED JOB PERFORMANCE CC PROCTOR
Mark Fiore, Rio Controls & Hydraulics Michael O’Connor, Northwestern Michigan College Bradley Wagner, Manitowoc Crane Group
CONDUCTOR & CONECTOR (CC)
Michael Butler, The Boeing Company Nicholas Danielson, The Boeing Company Nicholas Hoffman, The Boeing Company Keith Houser, The Boeing Company Jason Moore, The Boeing Company
HYDRAULIC SPECIALIST (HS)
Matthew Lilyquist, Altec Industries, Inc. Rudy O’Brien, Altec Industries, Inc.
MOBILE HYDRAULIC MECHANIC (MHM)
Shawn Atcher, Altec Industries, Inc. Jesse Bartholomew, Altec Industries, Inc. Eric Brady, Altec Industries, Inc. Gregory Burnette, AEP Charles Collins, Altec Industries, Inc. Kameron Connell, Crossroads Mobile Maintenance Outcome 2.2.3: Understanding the principles of levers Outcome 3.1.4: Calculate the thrust for a toggle mechanism Outcome 3.1.5: Calculate the hydraulic pressure to support jib boom loads Outcome 3.4.3: Understand the application of logic elements (cartridge valves) Outcome 3.5.1: Calculate the capacity of a reservoir using volume requirements Outcome 3.5.2: Understand the limitations of the reservoir for fluid conditioning Outcome 3.6.1: Understand the difference between isothermal and adiabatic conditions Outcome 3.6.2: Understand the purposes of the accumulator Outcome 3.9: Specify heat exchangers Tyler Coppage, Altec Industries, Inc. Seth Cossey, Altec Industries, Inc. Ryan Cristofaro, Altec Industries, Inc. Marc Czulewicz, Altec Industries, Inc. Myron Dennis, Altec Industries, Inc. James Depratter, Altec Industries, Inc. Jessy Frisk, Altec Industries, Inc. Daniel Gulley, Altec Industries, Inc. Joshua Holmes, Crossroads Mobile Maintenance Tyler James, Altec Industries, Inc. Gilbert Kessler, Altec Industries, Inc. Kevin Lonsway, AEP William Lucas, Altec Industries, Inc. Robert McCoy, Altec Industries, Inc. Justin McCrabb, Crossroads Mobile Maintenance Robert Merrow, Altec Industries, Inc. Jason Mishler, Crossroads Mobile Maintenance Tucker Moss, Altec Industries, Inc. Aaron Moussette, Tip Top Aroborists Richard O’Brien, Crossroads Mobile Maintenance John Paholsky, AEP Mark Peavley, Altec Industries, Inc. Randall Riggs, Altec Industries, Inc. Colt Seaver, Altec Industries, Inc.
PNEUMATIC SPECIALIST STUDY MANUAL WEB SEMINARS
Outcome 1.9: Understand supply side air preparation Outcome 3.12: Understand moisture control Outcome 3.19: Understanding critical flow velocity and sonic conductance Outcome 2.3: Understanding moving loads with friction and incline factors Outcome 3.10: Size and select vacuum pads Outcome 3.18: Calculate the kinetic energy required to stop a load with a shock absorber Outcome 4.3: Familiarization with ladder logic diagrams
CERTIFICATION EMPOWERS
August 2020 Newly Certified Professionals
Ben Wagener, Altec Industries, Inc.
CONFIDENCE

Before I earned my certification, I thought I knew fluid power design. After earning my certification, I know that I know Fluid Power.
Marti Wendel, CFPAI, CFPE, CFPS
Clifford Shamblin, AEP Dirk Sims, Crossroads Mobile Maintenance Ryan Stinde, Altec Industries, Inc. Carl Stone, Altec Industries, Inc. Michael Sullivan, AEP Devon Warman, Altec Industries, Inc. Geoffrey Watson, Altec Industries, Inc. Jack Whalen, Crossroads Mobile Maintenance
Certification Testing Locations
CELEBRATING 60 YEARS
Individuals wishing to take any IFPS written certification tests can select from convenient locations across the United States and Canada. IFPS is able to offer these locations through its affiliation with The Consortium of College Testing Centers provided by National College Testing Association.
Contact headquarters if you do not see a location near you. Every effort will be made to accommodate your needs.
If your test was postponed due to the pandemic, please contact headquarters so that we may reschedule.
TENTATIVE TESTING DATES FOR ALL LOCATIONS:
December 2020
Tuesday 12/1 • Thursday 12/17
January 2021
Tuesday 1/12 • Thursday 1/28
February 2021
Tuesday 2/2 • Thursday 2/25

March 2021
Tuesday 3/2 • Thursday 3/25
ALABAMA Auburn, AL Birmingham, AL Calera, AL Decatur, AL Huntsville, AL Jacksonville, AL Mobile, AL Montgomery, AL Normal, AL Tuscaloosa, AL
ALASKA Anchorage, AK Fairbanks, AK
ARIZONA Flagstaff, AZ Glendale, AZ Mesa, AZ Phoenix, AZ Prescott, AZ Scottsdale, AZ Sierra Vista, AZ Tempe, AZ Thatcher, AZ Tucson, AZ Yuma, AZ
ARKANSAS Bentonville, AR Hot Springs, AR Little Rock, AR
CALIFORNIA Aptos, CA Arcata, CA Bakersfield, CA Dixon, CA Encinitas, CA Fresno, CA Irvine, CA Marysville, CA Riverside, CA Salinas, CA San Diego, CA San Jose, CA San Luis Obispo, CA Santa Ana, CA Santa Maria, CA Santa Rosa, CA Tustin, CA Yucaipa, CA COLORADO Aurora, CO Boulder, CO Springs, CO Denver, CO Durango, CO Ft. Collins, CO Greeley, CO Lakewood, CO Littleton, CO Pueblo, CO
DELAWARE Dover, DE Georgetown, DE Newark, DE
FLORIDA Avon Park, FL Boca Raton, FL Cocoa, FL Davie, FL Daytona Beach, FL Fort Pierce, FL Ft. Myers, FL Gainesville, FL Jacksonville, FL Miami Gardens, FL Milton, FL New Port Richey, FL Ocala, FL Orlando, FL Panama City, FL Pembroke Pines, FL Pensacola, FL Plant City, FL Riviera Beach, FL Sanford, FL Tallahassee, FL Tampa, FL West Palm Beach, FL Wildwood, FL Winter Haven, FL
GEORGIA Albany, GA Athens, GA Atlanta, GA Carrollton, GA Columbus, GA Dahlonega, GA Dublin, GA Dunwoody, GA Forest Park, GA Lawrenceville, GA Morrow, GA Oakwood, GA Savannah, GA Statesboro, GA Tifton, GA Valdosta, GA
HAWAII Laie, HI
IDAHO Boise, ID Coeur d ‘Alene, ID Idaho Falls, ID Lewiston, ID Moscow, ID Nampa, ID Rexburg, ID Twin Falls, ID
ILLINOIS Carbondale, IL Carterville, IL Champaign, IL Decatur, IL Edwardsville, IL Glen Ellyn, IL Joliet, IL Malta, IL Normal, IL Peoria, IL Schaumburg, IL Springfield, IL University Park, IL INDIANA Bloomington, IN Columbus, IN Evansville, IN Fort Wayne, IN Gary, IN Indianapolis, IN Kokomo, IN Lafayette, IN Lawrenceburg, IN Madison, IN Muncie, IN New Albany, IN Richmond, IN Sellersburg, IN South Bend, IN Terre Haute, IN
IOWA Ames, IA Cedar Rapids, IA Iowa City, IA Ottumwa, IA Sioux City, IA Waterloo, IA
KANSAS Kansas City, KS Lawrence, KS Manhattan, KS Wichita, KS
KENTUCKY Ashland, KY Bowling Green, KY Erlanger, KY Highland Heights, KY Louisville, KY Morehead, KY LOUISIANA Bossier City, LA Lafayette, LA Monroe, LA Natchitoches, LA New Orleans, LA Shreveport, LA Thibodaux, LA
MARYLAND Arnold, MD Bel Air, MD College Park, MD Frederick, MD Hagerstown, MD La Plata, MD Westminster, MD Woodlawn, MD Wye Mills, MD MASSACHUSETTS Boston, MA Bridgewater, MA Danvers, MA Haverhill, MA Holyoke, MA Shrewsbury, MA MICHIGAN Ann Arbor, MI Big Rapids, MI Chesterfield, MI Dearborn, MI Dowagiac, MI East Lansing, MI Flint, MI Grand Rapids, MI Kalamazoo, MI Lansing, MI Livonia, MI Mount Pleasant, MI Sault Ste. Marie, M Troy, MI University Center, MI Warren, MI
MINNESOTA Alexandria, MN Brooklyn Park, MN Duluth, MN Eden Prairie, MN Granite Falls, MN Mankato, MN
MISSISSIPPI Goodman, MS Jackson, MS Mississippi State, MS Raymond, MS University, MS MISSOURI Berkley, MO Cape Girardeau, MO Columbia, MO Cottleville, MO Joplin, MO Kansas City, MO Kirksville, MO Park Hills, MO Poplar Bluff, MO Rolla, MO Sedalia, MO Springfield, MO St. Joseph, MO St. Louis, MO Warrensburg, MO MONTANA Bozeman, MT Missoula, MT
NEBRASKA Lincoln, NE North Platte, NE Omaha, NE
NEVADA Henderson, NV Las Vegas, NV North Las Vegas, NV Winnemucca, NV NEW JERSEY Branchburg, NJ Cherry Hill, NJ Lincroft, NJ Sewell, NJ Toms River, NJ West Windsor, NJ
NEW MEXICO Albuquerque, NM Clovis, NM Farmington, NM Portales, NM Santa Fe, NM
NEW YORK Alfred, NY Brooklyn, NY Buffalo, NY Garden City, NY New York, NY Rochester, NY Syracuse, NY NORTH CAROLINA Apex, NC Asheville, NC Boone, NC Charlotte, NC China Grove, NC Durham, NC Fayetteville, NC Greenville, NC Jamestown, NC Misenheimer, NC Mount Airy, NC Pembroke, NC Raleigh, NC Wilmington, NC NORTH DAKOTA Bismarck, ND
OHIO Akron, OH Cincinnati, OH Cleveland, OH Columbus, OH Fairfield, OH Findlay, OH Kirtland, OH Lima, OH Maumee, OH Newark, OH North Royalton, OH Rio Grande, OH Toledo, OH Warren, OH Youngstown, OH OKLAHOMA Altus, OK Bethany, OK Edmond, OK Norman, OK Oklahoma City, OK Tonkawa, OK Tulsa, OK
OREGON Bend, OR Coos Bay, OR Eugene, OR Gresham, OR Klamath Falls, OR Medford, OR Oregon City, OR Portland, OR White City, OR PENNSYLVANIA Bloomsburg, PA Blue Bell, PA Gettysburg, PA Harrisburg, PA Lancaster, PA Newtown, PA Philadelphia, PA Pittsburgh, PA Wilkes-Barre, PA York, PA SOUTH CAROLINA Beaufort, SC Charleston, SC Columbia, SC Conway, SC Graniteville, SC Greenville, SC Greenwood, SC Orangeburg, SC Rock Hill, SC Spartanburg, SC TENNESSEE Blountville, TN Clarksville, TN Collegedale, TN Gallatin, TN Johnson City, TN Knoxville, TN Memphis, TN Morristown, TN Murfreesboro, TN Nashville, TN
TEXAS Abilene, TX Arlington, TX Austin, TX Beaumont, TX Brownsville, TX Commerce, TX Corpus Christi, TX Dallas, TX Denison, TX El Paso, TX Houston, TX Huntsville, TX Laredo, TX Lubbock, TX Lufkin, TX Mesquite, TX San Antonio, TX Victoria, TX Waxahachie, TX Weatherford, TX Wichita Falls, TX
UTAH Cedar City, UT Kaysville, UT Logan, UT Ogden, UT Orem, UT Salt Lake City, UT VIRGINIA Daleville, VA Fredericksburg, VA Lynchburg, VA Manassas, VA Norfolk, VA Roanoke, VA Salem, VA Staunton, VA Suffolk, VA Virginia Beach, VA Wytheville, VA WASHINGTON Auburn, WA Bellingham, WA Bremerton, WA Ellensburg, WA Ephrata, WA Olympia, WA Pasco, WA Rockingham, WA Seattle, WA Shoreline, WA Spokane, WA WEST VIRGINIA Ona, WV
WISCONSIN La Crosse, WI Milwaukee, WI Mukwonago, WI WYOMING Casper, WY Laramie, WY Torrington, WY CANADA ALBERTA Calgary, AB Edmonton, AB Fort McMurray, AB Lethbridge, AB Lloydminster, AB Olds, AB Red Deer, AB
BRITISH COLUMBIA Abbotsford, BC Burnaby, BC Castlegar, BC Delta, BC Kamloops, BC Nanaimo, BC Prince George, BC Richmond, BC Surrey, BC Vancouver, BC Victoria, BC
MANITOBA Brandon, MB Winnipeg, MB NEW BRUNSWICK Bathurst, NB Moncton, NB
NEWFOUNDLAND AND LABRADOR St. John’s, NL
NOVA SCOTIA Halifax, NS
ONTARIO Brockville, ON Hamilton, ON London, ON Milton, ON Mississauga, ON Niagara-on-the-Lake, ON North Bay, ON North York, ON Ottawa, ON Toronto, ON Welland, ON Windsor, ON
QUEBEC Côte Saint-Luc, QB Montreal, QB SASKATCHEWAN Melfort, SK Moose Jaw, SK Nipawin, SK Prince Albert, SK Saskatoon, SK
YUKON TERRITORY Whitehorse, YU
UNITED KINGDOM Elgin, UK
GHAZNI Kingdom of Bahrain, GHA Thomasville, GHA
EGYPT Cairo, EG
JORDAN Amman, JOR
NEW ZEALAND Taradale, NZ
CFPAI Certified Fluid Power Accredited Instructor CFPAJPP Certified Fluid Power Authorized Job Performance Proctor
CFPAJPPCC Certified Fluid Power Authorized Job Performance Proctor Connector & Conductor
CFPE Certified Fluid Power Engineer CFPS Certified Fluid Power Specialist (Must Obtain CFPHS & CFPPS) CFPHS Certified Fluid Power Hydraulic Specialist CFPPS Certified Fluid Power Pneumatic Specialist CFPECS Certified Fluid Power Electronic Controls Specialist CFPMT Certified Fluid Power Master Technician (Must Obtain CFPIHT, CFPMHT, & CFPPT) CFPIHT Certified Fluid Power Industrial Hydraulic Technician CFPMHT Certified Fluid Power Mobile Hydraulic Technician CFPPT Certified Fluid Power Pneumatic Technician
CFPMM Certified Fluid Power Master Mechanic (Must Obtain CFPIHM, CFPMHM, & CFPPM) CFPIHM Certified Fluid Power Industrial Hydraulic Mechanic CFPMHM Certified Fluid Power Mobile Hydraulic Mechanic CFPPM Certified Fluid Power Pneumatic Mechanic
CFPMIH Certified Fluid Power Master of Industrial Hydraulics (Must Obtain CFPIHM, CFPIHT, & CFPCC) CFPMMH Certified Fluid Power Master of Mobile Hydraulics (Must Obtain CFPMHM, CFPMHT, & CFPCC) CFPMIP Certified Fluid Power Master of Industrial Pneumatics (Must Obtain CFPPM, CFPPT, & CFPCC) CFPCC Certified Fluid Power Connector & Conductor
CFPSD Fluid Power System Designer CFPMEC (In Development) Mobile Electronic Controls
CFPIEC (In Development) Industrial Electronic Controls
Tentative Certification Review Training
In-house Review Training – an IFPS Accredited Instructor will come to your company (minimum 10 individuals)
HYDRAULIC SPECIALIST (HS) CERTIFICATION REVIEW
Onsite review training for small groups – contact kpollander@ifps.org for details
March 23-26, 2021 - Fairfield, OH - CFC Industrial Training | Written test: March 26, 2021 September 13-16, 2021 - Fairfield, OH - CFC Industrial Training | Written test: September 16, 2021
PNEUMATIC SPECIALIST (PS)
Onsite review training for small groups – contact kpollander@ifps.org for details
December 14-16, 2020 - Fairfield, OH - CFC Industrial Training | Written test: December 17, 2020 July 27-29, 2021 - Fairfield, OH - CFC Industrial Training | Written test: July 29, 2021
ELECTRONIC CONTROLS (ECS) CERTIFICATION REVIEW
Onsite review training for small groups – contact kpollander@ifps.org for details
August 9-12, 2021 - Fairfield, OH - CFC Industrial Training | Written test: August 12, 2021
CONNECTOR & CONDUCTOR (CC) CERTIFICATION REVIEW
Onsite review training for small groups – contact kpollander@ifps.org for details
May 18-19, 2021 - Fairfield, OH - CFC Industrial Training | Written and JP test: May 20, 2021 November 16-17, 2021 - Fairfield, OH - CFC Industrial Training | Written and JP test: November 18, 2021
MOBILE HYDRAULIC MECHANIC (MHM) CERTIFICATION REVIEW
Onsite review training for small groups – contact kpollander@ifps.org for details
Online Mobile Hydraulic Mechanic Certification Review (for written test) offered through info@cfcindustrialtraining.com. This course takes you through all chapters of the MHM Study Manual (6.5 hours) and every outcome to prepare you for the written MHM test. Members receive 20% off. (Test fees are additional - separate registration required.) April 13-15, 2021 - Fairfield, OH - CFC Industrial Training | Written and JP test: April 16, 2021 August 30 - September 1, 2021 - Fairfield, OH - CFC Industrial Training | Written and JP test: September 2, 2021
INDUSTRIAL HYDRAULIC MECHANIC (IHM) CERTIFICATION
Onsite review training for small groups – contact kpollander@ifps.org for details
June 14 - 16, 2021 - Fairfield, OH - CFC Industrial Training | Written and JP test: June 17, 2021
INDUSTRIAL HYDRAULIC TECHNICIAN (IHT) CERTIFICATION REVIEW TRAINING
Onsite review training for small groups – contact kpollander@ifps.org for details
Call for dates. Phone: 513-874-3225 - CFC Industrial Training, Fairfield, Ohio
MOBILE HYDRAULIC TECHNICIAN (MHT) CERTIFICATION REVIEW TRAINING
Onsite review training for small groups – contact kpollander@ifps.org for details
Call for dates. Phone: 513-874-3225 - CFC Industrial Training, Fairfield, Ohio
PNEUMATIC TECHNICIAN (PT) and PNEUMATIC MECHANIC CERTIFICATION REVIEW TRAINING
Onsite review training for small groups – contact kpollander@ifps.org for details
Call for dates. Phone: 513-874-3225 - CFC Industrial Training, Fairfield, Ohio
JOB PERFORMANCE (JP) TRAINING
Onsite review training for small groups – contact kpollander@ifps.org for details
Online Job Performance Review - CFC Industrial Training offers online JP Reviews which includes stations 1-6 of the IFPS mechanic and technician job performance tests. Members may e-mail askus@ifps.org for a 20% coupon code off the list price or get the code in our Members Only area for the entire IFPS Job Performance Review; test not included.
LIVE DISTANCE LEARNING JOB PERFORMANCE STATION REVIEW
Onsite review training for small groups – contact kpollander@ifps.org for details
E-mail info@cfcindustrialtraining.com for information.