
9 minute read
Designers as the Hub of Collaboration
MODERN MEDICINE
DESIGNERS AS THE HUB OF COLLABORATION
Working for Medtronic, the world’s largest medical device company, we are driven by a noble mission: “Alleviate pain, restore health, and extend life.” Although this mission statement is simple and elegant, the reality of achieving these goals through the medical device product development process is not. Stating the obvious, developing medical devices is an incredibly complex process. While every industry has its intricacies and all companies have their organizational challenges, the design and development of a new medical device, specifically at large corporations, is among the most complex. Through their work, medical device designers break down the barriers these complexities present.
A Multifaceted Environment At Medtronic, we innovate in many ways, but primarily by creating new ways to harness the properties of technology, be they electrical, thermal, chemical, mechanical or digital, to treat or diagnose medical conditions. To sufficiently leverage these technologies, we require the input of individuals with deep expertise in all of these technical fields. We also rely on experts who are up to date with medicine’s continuously evolving understanding of how the human body functions. Even for the biological mechanisms we do understand, few specialists beyond medical doctors and researchers have the necessary comprehensive knowledge to be able to aid in developing a new medical device.
An understanding of technology and physiology is not all we need to make an innovative medical device. We are still left wondering how someone will incorporate this new product in their work (doctors, nurses, techs) or their life (patients, caregivers). While we do know who our target users are, our ability to connect with them in order to gather input to refine our devices is limited by the nature of healthcare privacy, user prevalence, proximity and availability.
This is the environment in which every medical device is developed. Further complicating the process are barriers that arise relative to the business of healthcare, the legality of intellectual property and the gauntlet of country-specific regulatory bodies. Whether you are a small startup or a company of tens of thousands across the globe, these are the realities of developing a medical device.
To succeed in our mission as a company, every project team must rely on the deep expertise of the individual contributors who often—by nature of their roles—have narrow focuses. However, for a project to be successful, these deep experts must collaborate to see the big picture. Without collaboration, it is impossible to see how small decisions can lead to products that may function but fail to meet the needs and expectations of our customers.
A Unique Role for Designers Designers are uniquely positioned to facilitate the necessary level of collaboration among the various clinical, technical and business contributors. We have found that applying the traditional design methods used by industrial designers for decades to the medical device development process brings user experience and meaningful outcomes to the forefront. By clearly understanding the context of use and user motivations, rapidly exploring ideas that focus on interactions and outcomes and creating clear and concise communication tools, designers provide a hub for the various workstreams to come together and explore how we as a collective work to achieve our mission.
There is a common Venn diagram with three circles
that shows a successful product at the confluence of viability, feasibility and desirability (below). At a medical device company, the designer must understand not only the needs of the user (the desirability group) but also the needs and limitations of the other stakeholders so that a realistic and profitable solution can be achieved. At a large medical device company, a multitude of groups make up the three circles.
In our reality, that simple Venn diagram is much more involved (next page). For example: Viability stakeholders may include marketing, finance, operations, sourcing, distributions and localization. Feasibility stakeholders may include mechanical, electrical, systems, material and chemical engineering, software and regulatory. Desirability stakeholders may include patients, family/caregivers, nurses, cardiologists, surgeons, hospital administrators and field staff. This means that a medical designer must have a much wider and deeper knowledge of the product space than may be required in other fields of design.
Where other designers may have more personal responsibility and control over the definition of the end product, medical designers need to collaborate with the aforementioned project team experts to realize a successful product. Therefore, it is a core responsibility of a designer to build and share an empathetic understanding of who the user is and what they need from the product.
At a large medical device company, project teams can range from 50 to 300 people. Designers are uniquely positioned to communicate to large project teams because of their ability to create visualizations and deliver actionable insights. These visualizations can create a clear sense of empathy and understanding among the team. Communicating effectively to every team member requires our designers to visually and verbally tell the user’s story in a clear way through multiple formats. For example, some team members will respond well to presentations. Others may have more success understanding a deliverable they can keep and review over time. Some of the most powerful tools for creating an empathetic understanding of the user for project teams are user personas and workflow storyboards created by the designers.
Understanding who the user is, what their needs are, and the needs and limitations of other project team stakeholders are critically important for ensuring that design progresses in the correct direction. This knowledge helps to define the sandbox that medical designers can play in when creating concepts and seeking solutions that reach the desired output while staying inside the constraints of the project. However, this is merely the beginning of the development process. A medical designer is then responsible for ideating, prototyping and testing through a user-centered approach. It is important that they collaborate and communicate with the project team every step of the way.
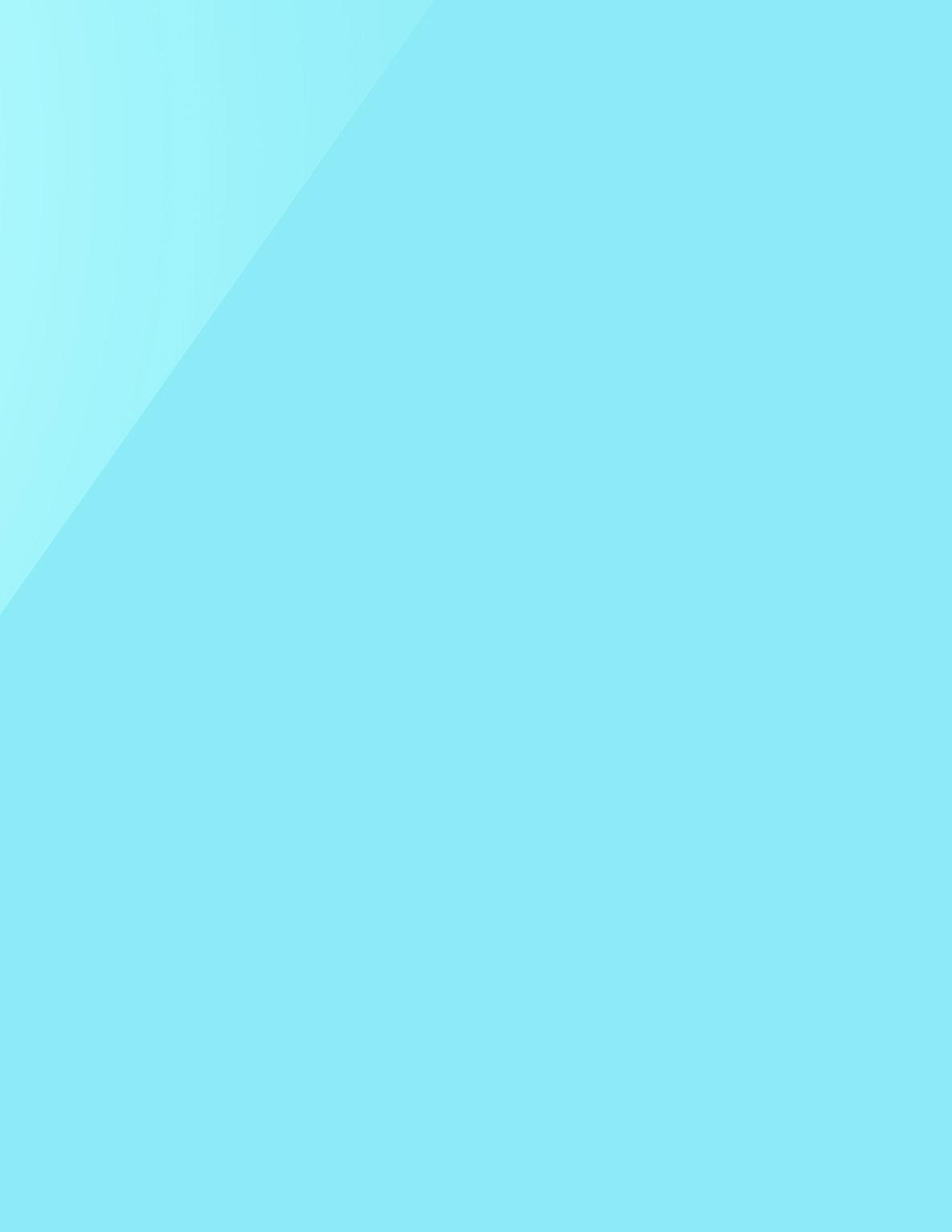
Progressing the Design At a large medical device company, design is best driven by data, not by any one person’s preference. Therefore, field testing serves as evidence that a project is moving in the right direction or, if users are struggling with the concepts put in front of them, that a change needs to be made. This usually means that medical device designers need to build a regular cadence of testing and learn efficient ways to connect with user groups. However, recruiting users to test with, whether they are patients or clinicians, can be a challenge, especially when a user group is small and/or their free time is limited. Building relationships with field staff and recruiting firms can be key to making the needed connections with real users so that testing can be completed. Coming back to collaboration, these visits are not the domain of the designer alone. When possible, great value to the project can come from the involvement of nondesigner project team members. When they observe real end users, they become another advocate for the end user’s needs. This understanding enables them to see how their decisions impact the product’s user experience.
One more aspect that makes the medical designer’s job unique is the focus on safety. The medical designer
Viability
Successful Product
Desirability Feasibility
A standard design thinking Venn diagram.
MODERN MEDICINE
Finance
Marketing Operations Sourcing
Distribution
Localization
Successful Product
Patients Mechanical
Caregivers Electrical
Nurses
Cardiologists
Hospital Admin.

Field Staff Systems
Material
Chemical
Software
A modified design thinking Venn diagram for a large medical device company.
must always be aware of the tasks that are related to safety and work to mitigate the risks that could lead to patient or clinician harm. At the end of the project, the team needs to be able to show that they have identified all the risks involved in using the system, developed mitigations for any risks that could not be eliminated from the system, and tested the system with real end users in realistic scenarios to provide evidence that the safety risks have been mitigated as much as possible. Identifying and implementing the appropriate method for managing risk requires further collaboration across the project team. This can be a challenging and timeconsuming aspect of the job, but it is critically important to meeting user needs.
Knowing we have made the safest possible and most desirable solution for our end users creates a great deal of pride and satisfaction in the end product. The medical designer uses traditional design skills and techniques to build understanding across the diverse set of stakeholders involved in the creation of new medical products. They need to build a robust level of knowledge within technical and physiological fields to be able to understand the constraints of their projects. As designers apply the human-centered design process in this big and complex environment, we routinely find ourselves facilitating meaningful collaboration, increasing the chance we will deliver a great product that accommodates our complex technical constraints while satisfying our business goal of commercial success.
—Stephen Nelson, IDSA, and Danny Gelfman stephen.m.nelson@medtronic.com danny.m.gelfman@medtronic.com
Stephen Nelson is an industrial designer on the Human Factors & User Experience team at Medtronic. He is passionate about building medical systems that improve the experience for patients and clinicians.
Danny Gelfman is the senior principal solutions designer in the Innovation Lab at Medtronic where he uses human-centered design to lead advanced concept development of new healthcare products and services.
CALL F R EDUCATION PAPERS INTERNATIONAL DESIGN CONFERENCE September 14-16, 2020 Seattle, WA
For peer review, publication, and presentation at the 2020 IDSA Education Symposium
Theme: DESIGN EXCHANGE Deadline: June 1, 2020 Submit Online: internationaldesignconference.com/education-symposium
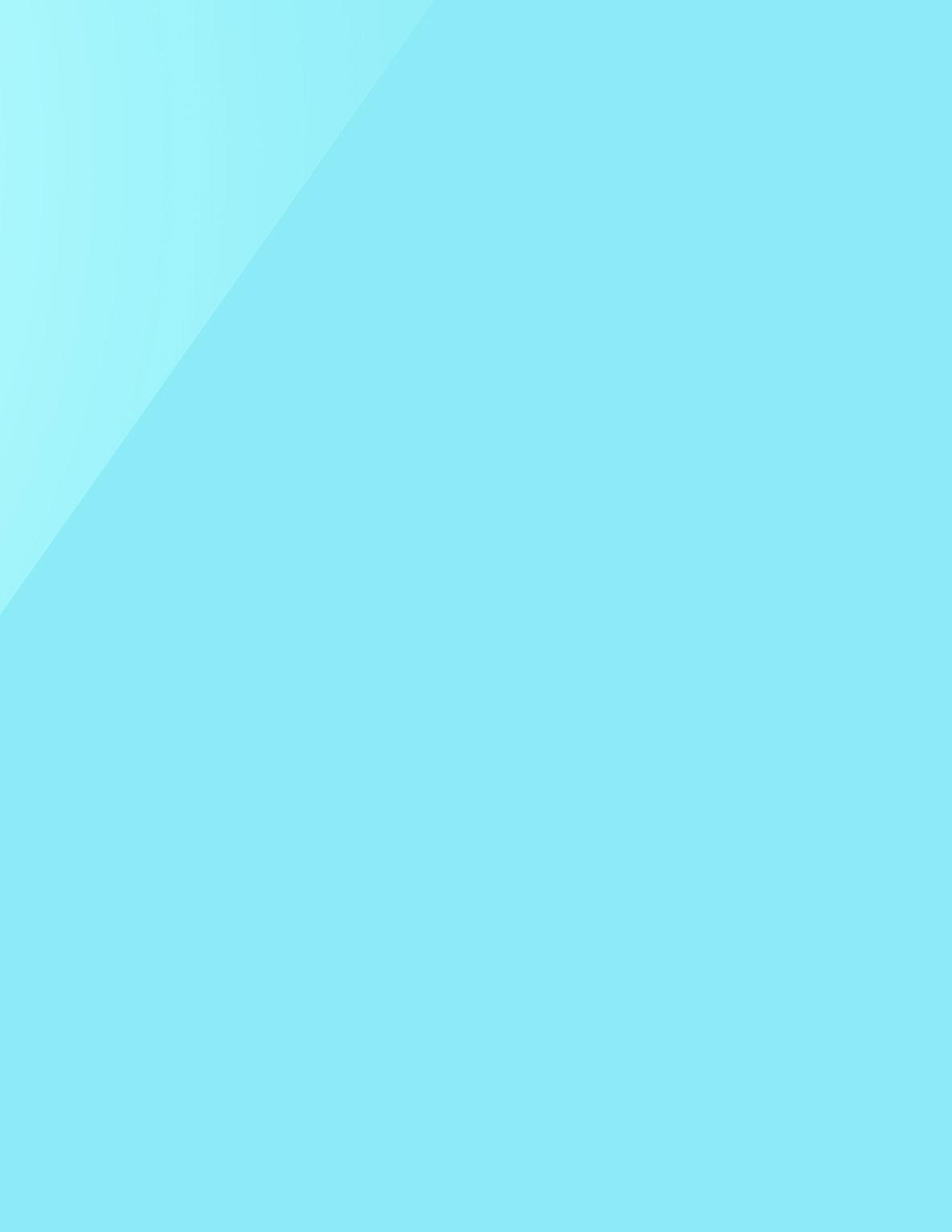
Design education often operates in the realm of the theoretical, where deadlines are self-imposed and outcomes are not always of practical consequence. Its goal is to acquire knowledge, skills, and habits of mind and to practice the application of these to solve meaningful problems via a deliberate iterative process. In design education, tools and methods are constantly evolving and being refined; however, the bulk of these advances in knowledge seem to rarely reach the professional community.
On the other hand, design practice largely operates in the realm of the practical, with a fixed calendar and a strong focus on pragmatic considerations, including budgets and billable time. Designs are realized in the real world and go on to have long-term implications in the way we live, work, and play. Economic pressures ensure that there is increasingly less time for theoretical inquiry and applied research.
As we enter into the fourth industrial revolution, the work of the designer is rapidly changing. How can practitioners and academic institutions better collaborate to ensure that the design community has a hand in shaping the fourth industrial revolution, rather than allowing it to shape us? The coming economic, ecological, and social changes urgently necessitate a meaningful conversation between design educators and design practitioners.
DESIGN EXCHANGE seeks to nurture this spirit of collaboration and invites participants to come together as a community and LISTEN with EMPATHY, as we propose innovative and meaningful changes in the ways we learn, teach, apply, adapt, and perceive across the academic-practice divide. Our shared goal is to EXCHANGE lessons learned, best practices, case studies, research, and future outlooks.