
9 minute read
Preparing for an Interconnected Future
MODERN MEDICINE
PREPARING FOR AN INTERCONNECTED FUTURE
Designing medical devices is unique. A good design requires a blend of safety, usability and aesthetics. Surges in device and contextual complexity, including the omnipresent role of technology and performancebased reimbursement, continue to evolve this domain. The increasing scale of device manufacturers and a resulting portfolio effect have also altered the demands on industrial designers.
As device manufacturers grow through acquisition and organic innovation, industrial designers work within increasingly diverse product development teams and must evolve to thrive. Additional competencies for industrial designers in the medical domain include systems thinking, risk management, user interface (UI) development and user experience (UX) design. Further, as with many technologydriven domains, industrial designers must have proficient soft skills to excel as cross-functional partners.
Industrial design practitioners and educators need to adapt to this new normal. To do so, we need to think critically about our role in the development process, advance our hard skills and elevate our soft skills. Turning the tools and methods for capturing user needs and design inputs inward is a good first step.
Diversity in Products and People In-house industrial design teams now face the challenges that once defined external consultants exclusively (e.g., a wide variety in project scope and ever-changing domains). Essentially, the role of industrial design has expanded as device manufacturers aim to support procedures end-toend with complete product portfolios, known as the portfolio effect. Industrial designers work on products ranging from handheld tools and capital equipment to graphical user interfaces.
This expansion in product diversity has occurred for good reason. It allows systematic solutions benefiting the patient, the user and the device manufacturer. Advantages of the portfolio effect include a cohesive user experience, increased safety and an ability to offer broader cost discounts. Beyond expanding the range of project contributions, the portfolio effect has also increased the interconnections industrial designers have with other research and development disciplines.
Device manufacturers employ diverse teams with every discipline found in a research university catalog, including roles common to product development and those exclusive to medical device design. Traditional stakeholders (e.g., mechanical engineering and marketing) are primary partners for industrial designers, but the mix of cross-disciplinary interaction is changing. Systems engineering, software engineering, and research and technology groups play an ever-increasing part day to day. These disciplines have been integrated in the development process historically, but the degree to which industrial designers interact with these stakeholders has intensified. The ubiquitous nature of technology and the portfolio effect are driving this shift.
The rise of the hybrid usability specialist/human factors engineer/industrial designer magnifies the need for better cross-disciplinary interaction. Successful industrial designers appreciate cross-disciplinary perspectives and work in tandem with partners to develop design solutions. Strengthening our partnerships with other disciplines is a huge opportunity to advance the industrial design profession. These partnerships will also accelerate industrial design into the fourth industrial revolution (e.g., artificial intelligence, internet of things, augmented/mixed/virtual reality, quantum computing).
A Complex Responsibility While the technology evolution in the healthcare ecosystem builds momentum, one underlying constraint is constant: The human body is the most complex system a designer will encounter. It is complicated because it is variable— no human body is alike. This complexity, found in both the exterior and interior of the body, is exclusive to medical device design. Thus, creating a straightforward design solution that accommodates this variability is immensely challenging.
Implantable, indwelling and percutaneous products offer unique design constraints. These devices must consider the internal anatomy of the patient, a less familiar (because it is less accessible) problem space. Additionally, product solutions must last for years, if not decades. Often, these solutions involve working with a predefined legacy technology or delivery mechanism, and any revision to existing approaches is perceived as added risk. Moreover, these design constrains lead to the misconception that substantive design changes, and thus contributions from industrial designers, are out of scope or are limited. This misconception is common within engineering disciplines, as well as among some industrial designers. Arguably, there are opportunities beyond the handle, or more broadly, the design of the handle’s exterior plastic housing.
If the perception is that industrial designers are the handle people, then that is all industrial designers will be tasked with or asked to contribute. Instead, we need to shift ourselves to a higher system-level or interaction-level focus (e.g., consider the handle a part of a system that provides tactile and positional feedback that is necessary to build user trust and efficacy). We must be systematic thinkers relative to our role in development. The scope of industrial design should be as diverse and interconnected as the products we work on. It is important to define discrete problems and craft solid deliverables, but we should not lose sight of the broader system perspective. Industrial designers can influence the ecosystem, the workflow and the technology. If we do not adopt this mindset, industrial design will be pigeonholed.
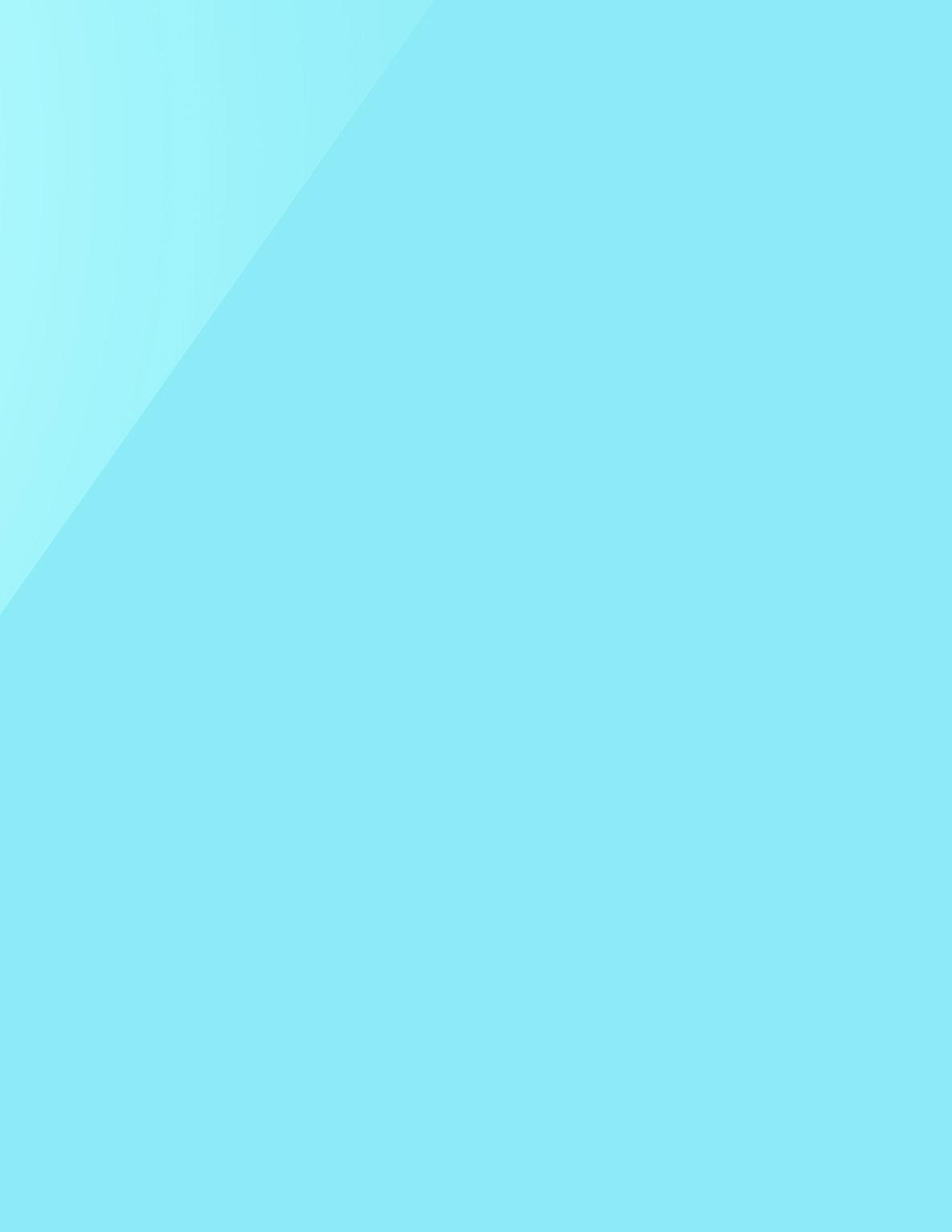
The Hard Skills Written communication is vitally important. Today’s medical device projects require succinct, yet comprehensive design deliverables to satisfy regulatory bodies and communicate design requirements to cross-functional partners. However, design education curriculums traditionally do not require rigorous documentation of design methodology, limiting the exposure of industrial designers to expository writing. Also, the drive toward internship-ready portfolios does not involve discussion of risk management, user interface design documents, version control or good file name hygiene when building design asset databases. These factors are vital when working under design controls in regulated industries, as is the case with medical device design.
The necessity of UI/UX deliverables creates a gap between the design education curriculum and industry practice. This is exasperated by how outnumbered industrial designers are in practice (easily 10:1 for each engineering discipline). Since industrial designers cannot be desk-side to oversee the implementation of every pixel or review the curvature of every fillet, we must build rapport and trust with our counterparts, which begins with effective documentation. Expanding the rigor of design education is a logical fix to this industry-academe gap. The latter constraint is more problematic. Building trust is hard. A good first step is ensuring cross-functional alignment.
MODERN MEDICINE
User Needs
Design Input
Verification
Validation
Design Process
Review
Design Output
Medical Device
The FDA’s waterfall process for the design of medical devices, from Design Control Guidance for Medical Device Manufacturers, 1997.

Look Inward before Working Outward Most medical device companies research users, but few take the time to reexamine their internal processes once standard operating procedures are in place. The design of medical devices requires subject matter experts, and design teams relish the chance to talk to users and observe their behavior. Likewise, the design research toolbox can improve our cross-functional interactions. Treating our counterparts as subject matter experts of their own disciplines supplies rich opportunities for engagement. We should analyze our interactions using the proven tools at our fingertips: qualitative interviews, communication framework diagrams and value-stream mapping.
Rather than getting frustrated that an engineer did not implement a widget as intended, design research methods can uncover where the error occurred and why. Was there a misalignment in organizational priorities, a gap in documentation or a simple miscommunication, or was a technical constraint ignored in the design specification? Introspective analysis of our cross-functional interactions can answer these tough questions.
Nested within the Design Control Guidance for Medical Device Manufacturers, 1997 issued by the U.S. Food and Drug Administration (FDA) is a diagram outlining a waterfall process for the design of medical devices (above). The process starts with user needs and cascades to the design input phase. This flows on to the final medical device with a few other stops along the way. The first two phases set up a program for success. Understanding the users, tasks, goals and use environments is an essential step. Additionally, the FDA asks teams to question assumptions and continually review the outputs of each phase. This process also applies to better understanding our cross-functional partners and ourselves.
The upside to self-reflection and cross-functional inquiry is not confined to medical product development. Nevertheless, the portfolio effect, diverse teams and complex responsibilities position those in the field to gain the most from the effort. Turning the tools and methods for capturing user needs and design inputs inward will help industrial designers build more meaningful partnerships and prepare the profession for an interconnected future. It does not hurt to regularly check-in and challenge our assumptions either.
—M. Robert Garfield mrobert.garfield@abbott.com
M. Robert “Bobby” Garfield is a senior human factors engineer and industrial designer within Abbott’s Electrophysiology and Heart Failure Division in St. Paul, MN.
SIDEBAR RESEARCH METHODS FOR CROSS-FUNCTIONAL INQUIRY
There are multiple generative and expository methods in the design research toolbox. Each method plays a unique role in the product development process. Design research methods can also be used for self-reflection and cross-functionally inquiry. Qualitative interviews, communication framework diagrams and value-stream mapping are particularly helpful in understanding team dynamics and improving collaboration.
Qualitative interviews are a means of gathering detailed information about a person’s experiences and beliefs. They are the first step in understanding our counterparts. Interviews can be highly prescriptive or more open ended. Semi-structured approaches are a nice balance. A simple interview guide allows for in-depth dialog that stays on topic. A qualitative approach provides more depth than surveys because interviewees can share their perspective in narrative form with added context. Transcription, coding and other analysis turn conversations into meaningful datasets. To maximize the utility of qualitative interviews, frame the discussion in a way that guides the conversation without leading the responses. For example, to better understand team interaction, do not ask, What are the biggest ways the industrial design department aids/hinders your department? A better approach would be to have a counterpart describe their role and then define the role of industrial designers in the development process. This subtle adjustment can uncover novel insights without tipping your hand. The feedback from qualitative interviews is meaningful on its own and can be used as inputs to other research methods.
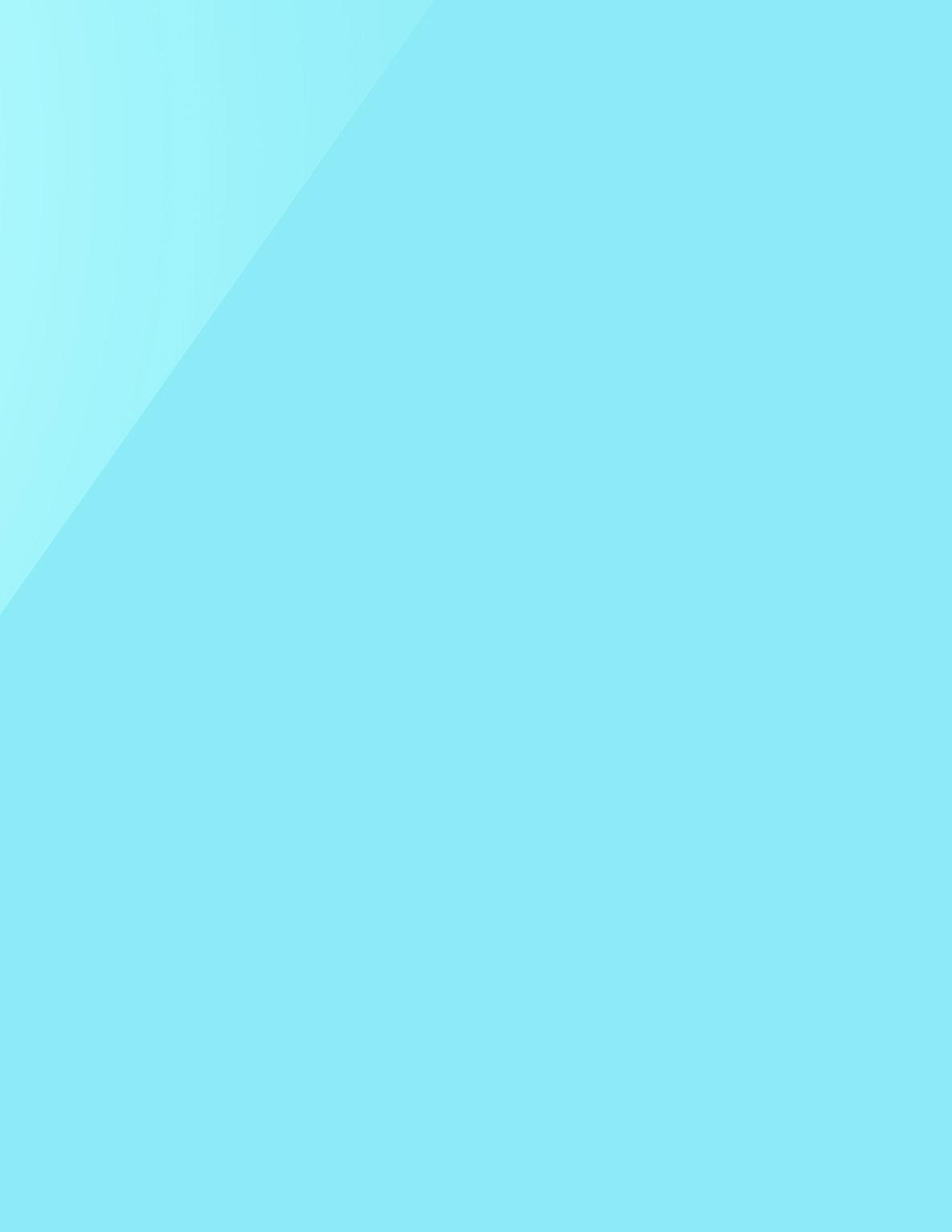
Communication framework diagrams visualize and characterize team communication in complex settings. They are constructed based on research about the flow of information between personnel. Data analysis involves the use of coding schemes to categorize modes of interaction, including verbal and nonverbal paths. Research queries can extend to communication preferences, frequency and topic. A product development inquiry might ask, How often and by what means does the industrial design team communicate with systems engineering (and vice versa)? The construction of communication framework diagrams can elicit problems in crossfunctional interaction. By exploring team communication patterns, it is easy to expose areas of opportunity and improve the flow of data during development.
Value-stream mapping is a method of documenting processes and flow. Adaptations of the method are often employed to identify touchpoints and key stakeholder values. The practice can be applied at different scales, including the flow of data, materials and people through an ecosystem. Its use to analyze the development process of a whole company, a single project or an individual deliverable is particularly helpful in strengthening cross-functional partnerships. The exercise identifies operational issues and ensures that outputs and measures are tailored to the audience. It also uncovers responsibility overlaps and gaps. For example, a value-stream map of a development process might help reveal that mechanical engineers enjoy working with industrial designers since the partnership reduces their responsibility for exploring surface geometry, whereas software engineers find the partnership a burden due to gaps in the flow of information.