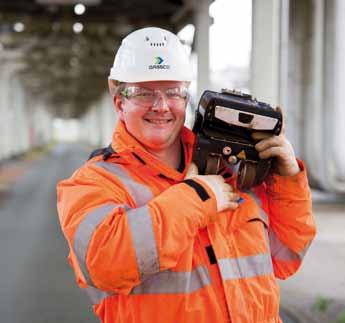
6 minute read
Robotic solutions enhance safety and reduce costs
Robo tic solutio ns enhance safety and r educ e co sts
Development and implementation of robotic solutions is a high focus area within Gassco’s R&D activities which is yielding valuable results. By Britt Aarhus, Lisbet Kallevik and Håkon Hilmar Ferkingstad
There has been rapid development in the field of robotic solutions in recent years and their deployment in the oil, gas and petrochemical industry is increasing. Applications range from subsea systems that are remotely operated to devices and drones for topside and onshore use.
Robotic solutions have particular potential for visual inspection and light maintenance tasks such as cleaning and painting, where they can provide significant advantages over traditional methods. These advantages include the ability to work 24/7 and to operate in hazardous, harsh and dirty environ
ments, which have placed robotics in an ideal position to be an integral part of the inspection and maintenance strategies for various types of assets.
A core focus for Gassco’s robotics development has been internal inspection of pressure vessels. The most important driver for this development is enhanced health and safety. By using robotics solutions, one reduces the need for entry of a human inspector in the pressure vessels. In addition, there is a significant cost saving potential, and new and better ways to document the condition of the pressure vessel.
c Håkon Hilmar Ferkingstad holding a Bike to demonstrate its compactness and portability.
Developing the technology
Since 2012, Gassco has been involved in several research and development projects for robotic solutions, of which one was the European Union co-funded Petrobot project. This ran from 2012 to 2016 and involved the development of robotic solutions for internal inspection of storage tanks and pressure vessels (see, petrobotproject.eu/).
In 2016, two exciting solutions for internal inspection of pressure vessels developed in the Petrobot project were used for the first time on a Gassco operated asset. The Bike, a small fourwheel magnetic crawler, is a flexible platform for inspection in confined spaces. The second solution, the Snakearm, is a four-metre-long robotic arm with unique visual inspection capabilities. The results from the first use of these two devices showed that such solutions can provide a safer, more complete and cost-efficient inspection compared to the use of entry by an inspector. It has been demonstrated that there can be significant cost savings through a reduced number of work tasks and man-hours for preparation, inspection and return to operation.
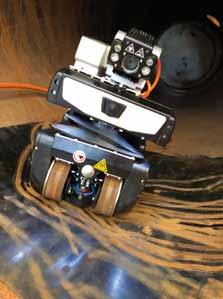
Since 2016, the Bike and the Snakearm have been further developed, tested and used for several internal inspections of pressure vessels in Norway with good results. This has been done through strong collabor
z Using a Bike to perform a visual inspection inside a pressure vessel. v A Snakearm entering a pressure vessel. ation with robot developers (GE Inspection Robotics, OC Robotics) and the technical service providers at our assets in Norway (Equinor and Shell).
During this development period, we have learned that it is not only important to concentrate on the technical solution, the robustness and capabilities of the robot, it is also essential to pay attention to the human factors and the interaction between machine and human.
To be able to achieve results there are three equally important factors: First the robotic solution, which is the tool; Secondly the operator who controls the robotic solution; and Thirdly the inspector who evaluates the findings.
While all three factors contribute to

success, a fourth factor – the need to create a good interaction between them – is probably the most important. When it comes to evaluating defects, a robotic solution will not be able to compete with an experienced inspector.
In September 2019, together with the technical service provider, Shell, we performed six inspections of pressure vessels using robotic solutions at the Nyhamna process plant in Norway. Even though at times we experienced bad weather conditions with heavy rain and wind, combined with other technical challenges, we managed to do all the planned inspections and achieved excellent results. This was thanks to great teamwork, good planning and creative problem solving (see this link to a video from Nyhamna, youtu.be/L5fflOtVrl8).
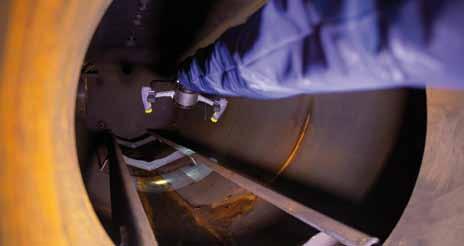
A range of tools can be attached to the robotic solutions depending on the application required, in this case cameras and lighting on the Snakearm.
Benefits of innovation
The objectives for the oil, gas and petrochemical industry from implementing robotic solutions for pressure vessel inspections are to minimise the exposure of personnel to potentially hazardous conditions, reduce downtime and save resources. Up to 98% of the total cost for internal inspection of pressure vessels with the use of entry by an inspector is related to the preparation work to allow human entry and the after-work to put the pressure vessel back into operation. The inspection work itself accounts only for about 2% of the total cost.
Based on the archived results from tests and preformed inspections the cost and time saving with the use of a robotic solution compared to ordinary inspection with entry of an inspector is estimated to be 75% (up to NOK 1 million or $110,000 per pressure vessel). However, the most important benefit is enhanced health and safety by reducing the need for human entry.
The focus in early implementation of robotic solutions has been the “low hanging fruit”, that is easy accessible and clean pressure vessels. However, we have also seen opportunities where the potential for risk reduction, cost and time saving are significantly greater than in the first use cases we have focused on till now.
Valuable collaboration
For Gassco the key to success in the development and implementation of robotic solutions has been the close and valuable collaboration with all involved parties. Our end users, the inspectors and operational personnel from our assets have been involved from the start and we have also been very transparent and shared our results and experience from tests and use with the robotics developers.
This open innovation approach where everyone gains value and can influence the development and implementation has been a high focus for us and has created greater value and faster implementation for the robotic solutions.
The way forward
Based on the experience and results achieved through research projects in the past and now the first use of robotic solutions on our assets, we see that use of robotic solutions can reduce risk and cost and give added value through building expertise within robotics and generating associated opportunities.
For Gassco the focus going forward will be to operationalise and deploy robotic solutions nearing the end of their development phase, which are ready to be used in an asset. Through this, we hope to contribute to fast tracking the deployment of robotic inspection solutions in the oil, gas and petrochemical industry. In addition, the results and experience from testing and implementation will be a vital part of future development when Gassco plans to extend the use of robotic solutions. We have several exciting new concepts and uses in the development pipeline such as crawlers and Snakearms for equipment with small entries (down to two inches) and extended use of drones for piping inspections.
Britt Aarhus, Lisbet Kallevik and Håkon Hilmar Ferkingstad work for Gassco AS as, respectively, Chief Innovation Officer, Communication Manager and Principal Engineer Asset Technology. Britt Aarhus is also a member of IGU’s R&D and Innovation Committee.