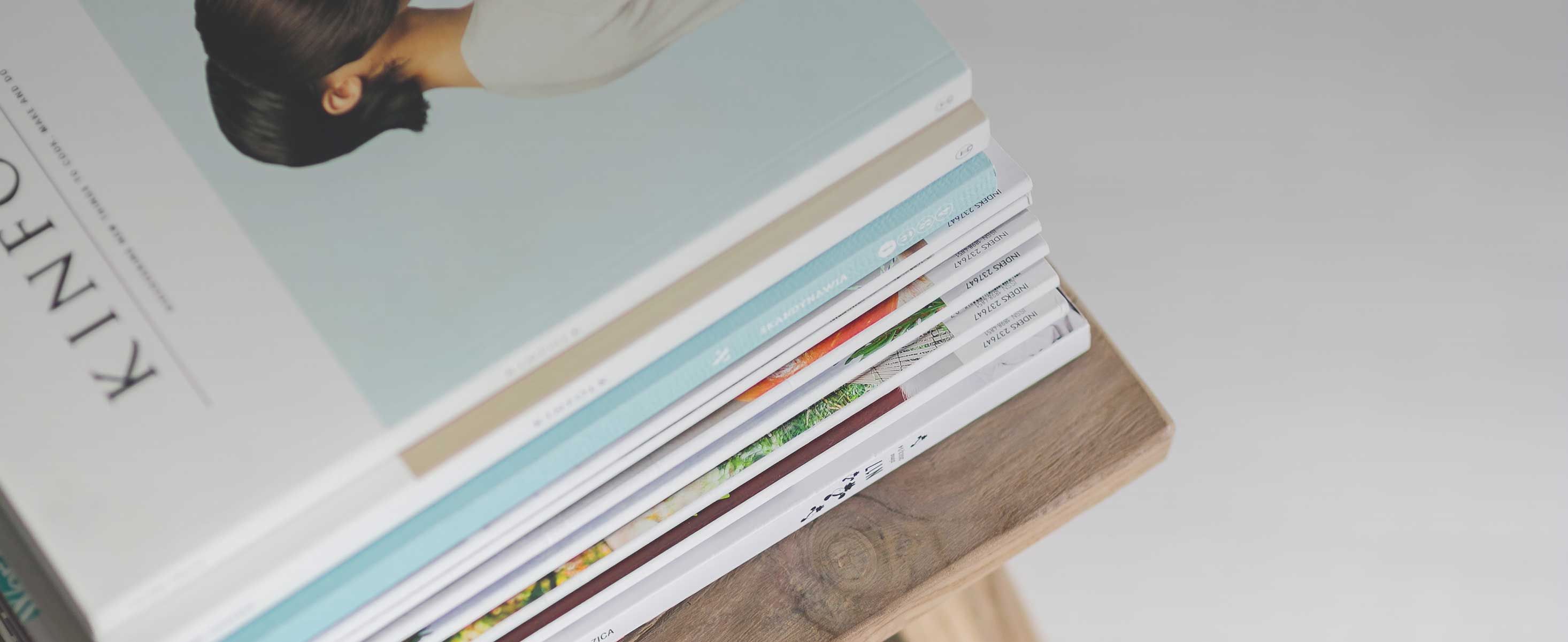
1 minute read
International Journal for Research in Applied Science & Engineering Technology (IJRASET)
from A Review on Basalt Fiber and Basalt Fiber Reinforced Polymer Composites Advancement and Industrial
by IJRASET
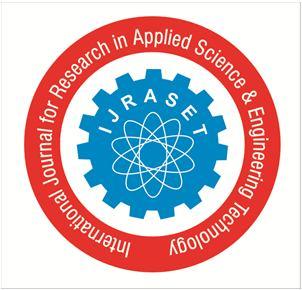
ISSN: 2321-9653; IC Value: 45.98; SJ Impact Factor: 7.538
Advertisement
Volume 11 Issue IV Apr 2023- Available at www.ijraset.com
0, 0.5, 1, 1.5 vol%
Glass transition temperature (Tg) rises with MWCNT content up to 1.5 vol% and is observed to fall with increasing MWCNT concentration.
Increase in elastic modulus and strength. Because of aggregation and CNT waviness, experimental results fell short of theoretical expectations.
Composites using CNT reinforcement significantly improve the effectiveness of the
Covalent bonding and nanoparticle dispersion boost stress transmission across interface when CNT surfaces are modified. Crack deflection and fracture reinforcement in the fiber direction. propagation pinning are two toughening mechanisms that are activated by the addition of CNT. MWCNT, when added in modest amounts to epoxy, lowers agglomeration and debonding.
BFC/ Gr/SiO2 composites have a 58.5% higher friction coefficient than BFC composites, and fillers significantly reduce wear rate at higher loads.
Pure BFC exhibits fiber pull-out and debonding between the fiber and matrix, whereas the inclusion of fillers results in little fiber breakage and minimal fiber pullout.
[45]
GnPs/Epoxy composites: 0.1 to 2 wt%
GnPs/Basalt/epoxy composites: 0.07, to 0.41 wt%.
GnPs/Epoxy composites: With increasing filler loading, AC conductivity, dielectric permittivity, and dielectric loss all rise.
The use of fillers improves the composites' mechanical characteristics. The optimal strength and modulus values are obtained when the filler content is 0.07% by weight.
When up to 1 weight percent of GnPs were added to Epoxy composites, they were uniformly distributed within the matrix. However, the addition of fillers led to their clustering, forming conductive pathways within the material. GnPs may evenly scatter in a matrix at low filler loadings, but when filler loading reaches 0.24 weight percent, agglomeration starts to occur.
[118]
Coating cycle from 1 to 10%
Due to a reduction in resistance with an increase in CNT concentration, electrical conductivity for atwo-cycle
Flexural strength and modulus both rise withthe number of dip cycles; for two dip
MWCNTs were discovered to be firmly coated through
[119]