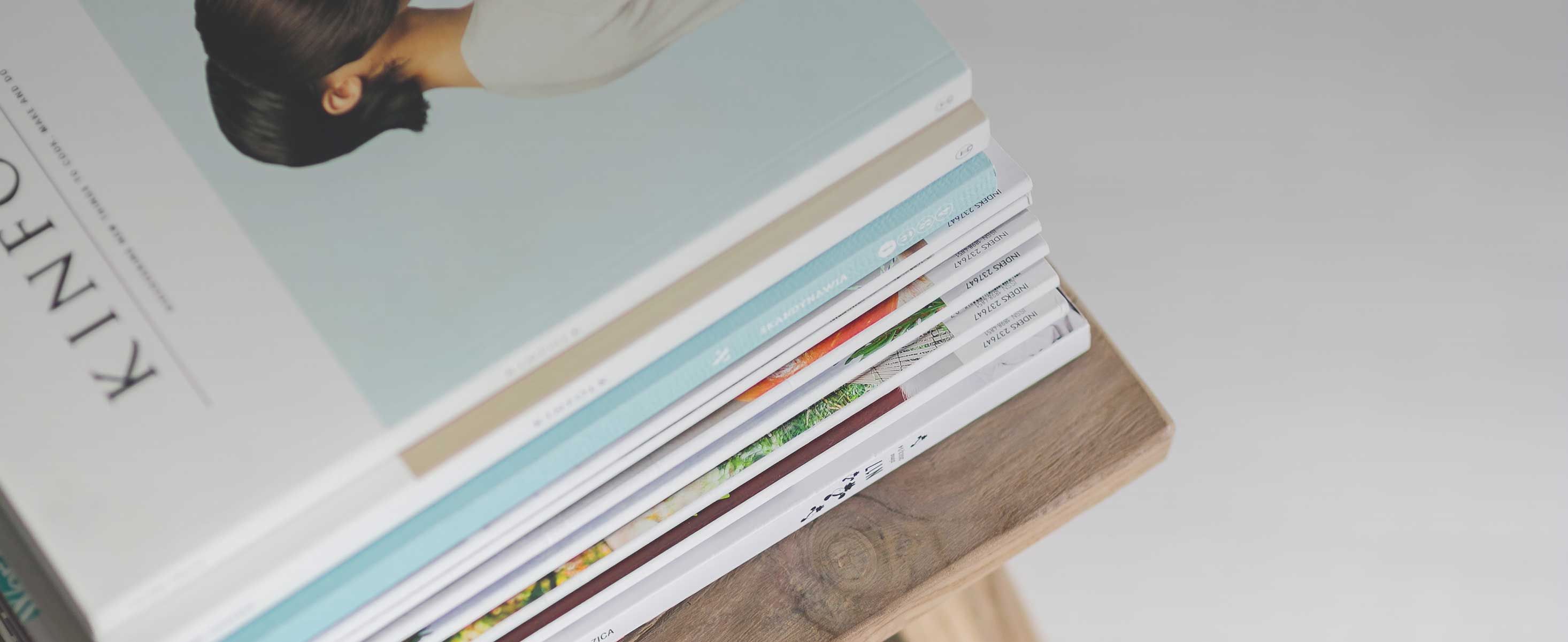
3 minute read
Beneficios
Beneficios de un circuito neumático conectado
Claramente, se puede obtener una gran cantidad de conocimiento al habilitar la conectividad para varios componentes en un circuito neumático. Y recopilar esta información puede tener beneficios de gran alcance para una operación de fabricación en su conjunto. Si bien existen muchos beneficios de este tipo, este documento solo profundizará en algunos:
» Eficiencia Mejorada: Con un esfuerzo comparativamente pequeño, los fabricantes pueden automatizar y monitorear de manera más eficiente la función de sus sistemas neumáticos. Por ejemplo, la conectividad puede ayudar a monitorear el consumo de aire comprimido, identificar posibles ineficiencias, como fugas, que representan aproximadamente el 20 % del consumo total de aire, y reducir tanto los costos de energía como la huella de carbono.
» Incluso un pequeño cambio, como la adición de un sensor de línea de aire para monitorear la presión operativa, puede tener un impacto positivo en las operaciones. Al configurarlo para que brinde una notificación cuando la presión cae por debajo de cierto valor, los ingenieros pueden saber exactamente cuándo un sistema no está funcionando con eficiencia y tomar medidas para solucionar el problema, como cambiar el filtro o reparar una fuga.
» Establecer la conectividad tampoco tiene por qué ser difícil. Con algunos métodos, puede llevar mucho tiempo instalar o poner en marcha un componente conectado, así como establecer manualmente los parámetros del sensor. Sin embargo, esto no es cierto para todos los sensores y dispositivos conectados. Por ejemplo, una tecnología, como IO-Link, solo tiene que estar enchufada para estar lista para usar, y permite a los usuarios configurar y poner en marcha el equipo conectado rápidamente al leer y cambiar los parámetros del dispositivo desde el archivo de descripción del dispositivo IO, a través del software de control del sistema. En el caso de IO-Link, la configuración de la máquina también es mucho más rápida debido a la conexión “punto a punto” independiente del fabricante que permite una integración perfecta con todos los sistemas Fieldbus/Ethernet establecidos.
» Productividad Optimizada: La conectividad también puede mejorar significativamente el rendimiento de un circuito. Las métricas operativas y de rendimiento se pueden monitorear de forma remota, ya que los sensores y otros dispositivos conectados envían datos en tiempo real. Estos datos proporcionan información sobre cómo funciona todo el sistema, tanto como partes individuales como en su conjunto. Esa información permite a los usuarios hacer ajustes para que todo el sistema funcione mejor, por ejemplo, manteniendo la presión de aire que optimiza el uso de energía para la productividad deseada. Tener datos relacionados con las operaciones a nivel de campo brinda la capacidad de tomar mejores decisiones a nivel operativo con respecto a la mejor manera de maximizar la productividad.
» Tiempo de Inactividad Reducido: Los datos de los sensores pueden facilitar el mantenimiento predictivo y planificado, notificando a los gerentes de mantenimiento sobre la reparación o el mantenimiento necesarios antes de que un problema se vuelva urgente o detenga la producción. Por ejemplo, al monitorear los recuentos de ciclos y los niveles de producción a lo largo del tiempo, es posible estimar la vida útil del actuador y predecir el final de su vida útil, lo que permite su reemplazo antes de que falle.
La transferencia de datos en tiempo real y los diagnósticos continuos hacen que el estado de salud de cada dispositivo sea más visible para los usuarios. Los errores, como roturas de cables o cortocircuitos, se detectan inmediatamente, lo que permite subsanarlos mucho más rápido y reducir cualquier tiempo de inactividad asociado. Se puede acceder a estos datos de diagnóstico incluso durante el funcionamiento.
Si un componente falla, los sensores pueden ayudar a identificar las posibles fuentes de la falla para facilitar el diagnóstico y la reparación del problema. Por lo tanto, cuando un sistema está fuera de servicio por mantenimiento, no toma tanto tiempo, ahorrando a los fabricantes no solo tiempo, sino también dinero.
Además, el acceso a los datos de todo el circuito neumático, en lugar de un solo punto de datos, ofrece una visión más completa de cómo funciona el circuito. Como resultado, los ingenieros pueden brindar un soporte técnico más cohesivo. Y con un sistema como IO-Link, incluso el reemplazo de sensores se simplifica cuando ocurren fallas: su parametrización automática significa que los usuarios solo tienen que conectar el nuevo dispositivo para importar la configuración de parámetros, de modo que todo pueda ponerse en marcha más rápido.
Conéctate al futuro con Norgren
Si bien agregar conectividad a los circuitos neumáticos puede parecer desalentador, los beneficios de hacerlo (proporcionar eficiencia y productividad de fabricación, al tiempo que reduce el tiempo de inactividad y los costos generales) hacen que valga la pena. Conectarse con los expertos para desarrollar su solución puede ayudarte a aprovechar al máximo el proceso. Con una larga historia de control de movimiento y tecnología de fluidos, Norgren puede guiar tu transición a la neumática inteligente, ofreciendo una cartera de productos para completar todo, desde un circuito neumático básico hasta un sistema neumático conectado habilitado para IO-Link. No importa por dónde empieces, ya sea con un solo sensor o con un circuito completamente conectado, la actualización de tus sistemas neumáticos es una manera invaluable de asegurarte de estar bien posicionado para manejar los desafíos de fabricación en los años venideros.