
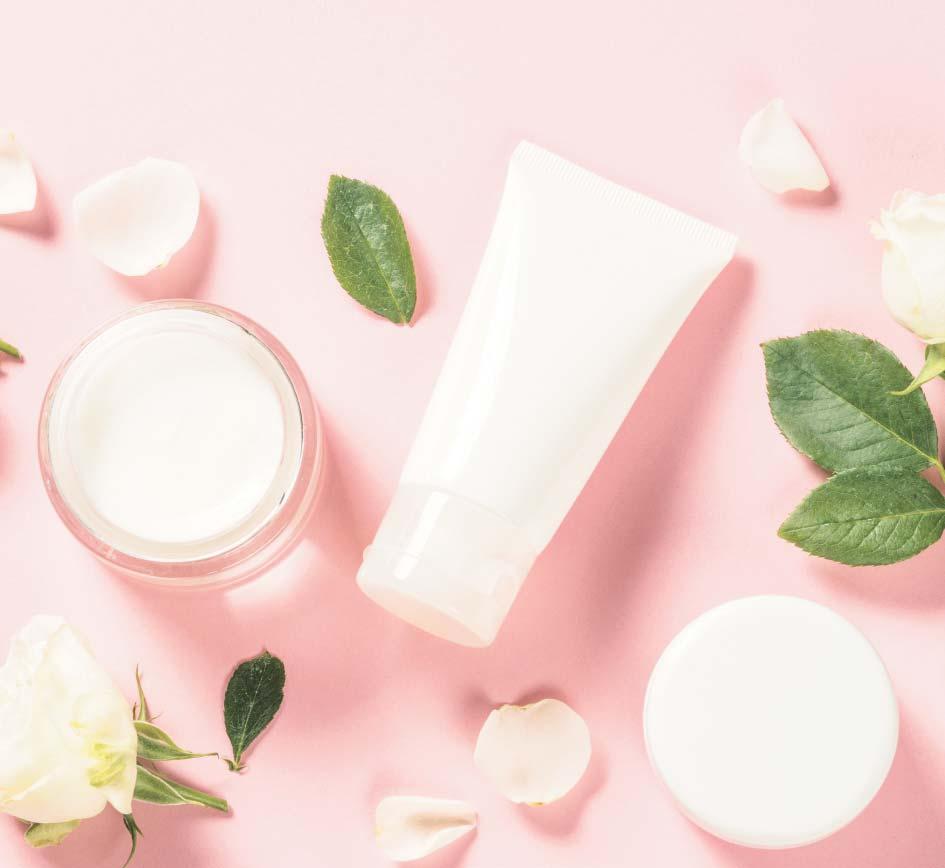
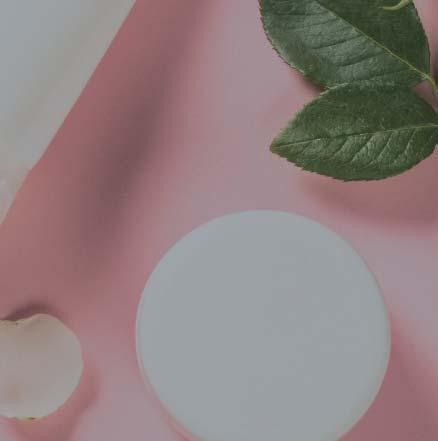
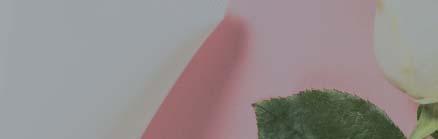

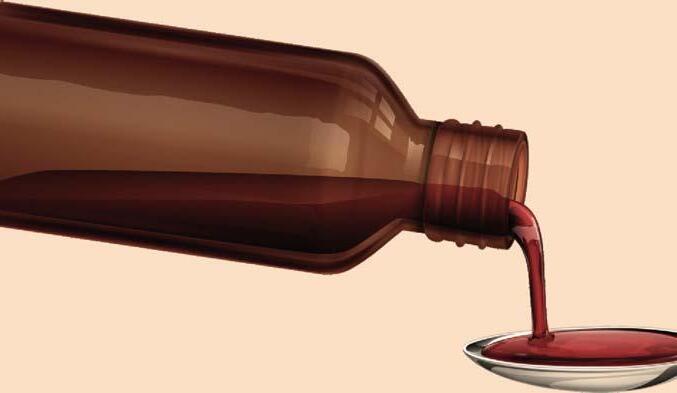

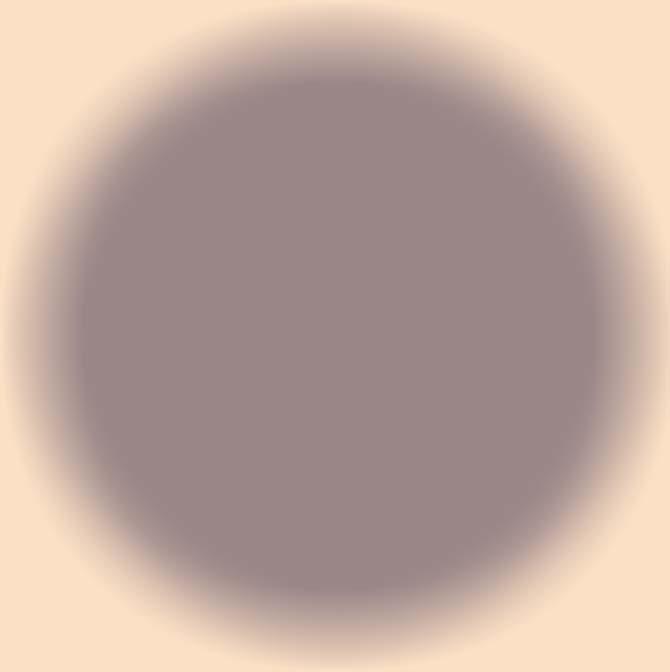
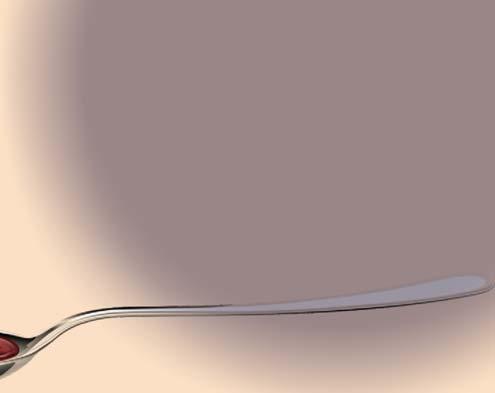
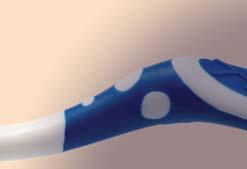

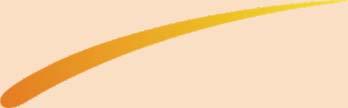
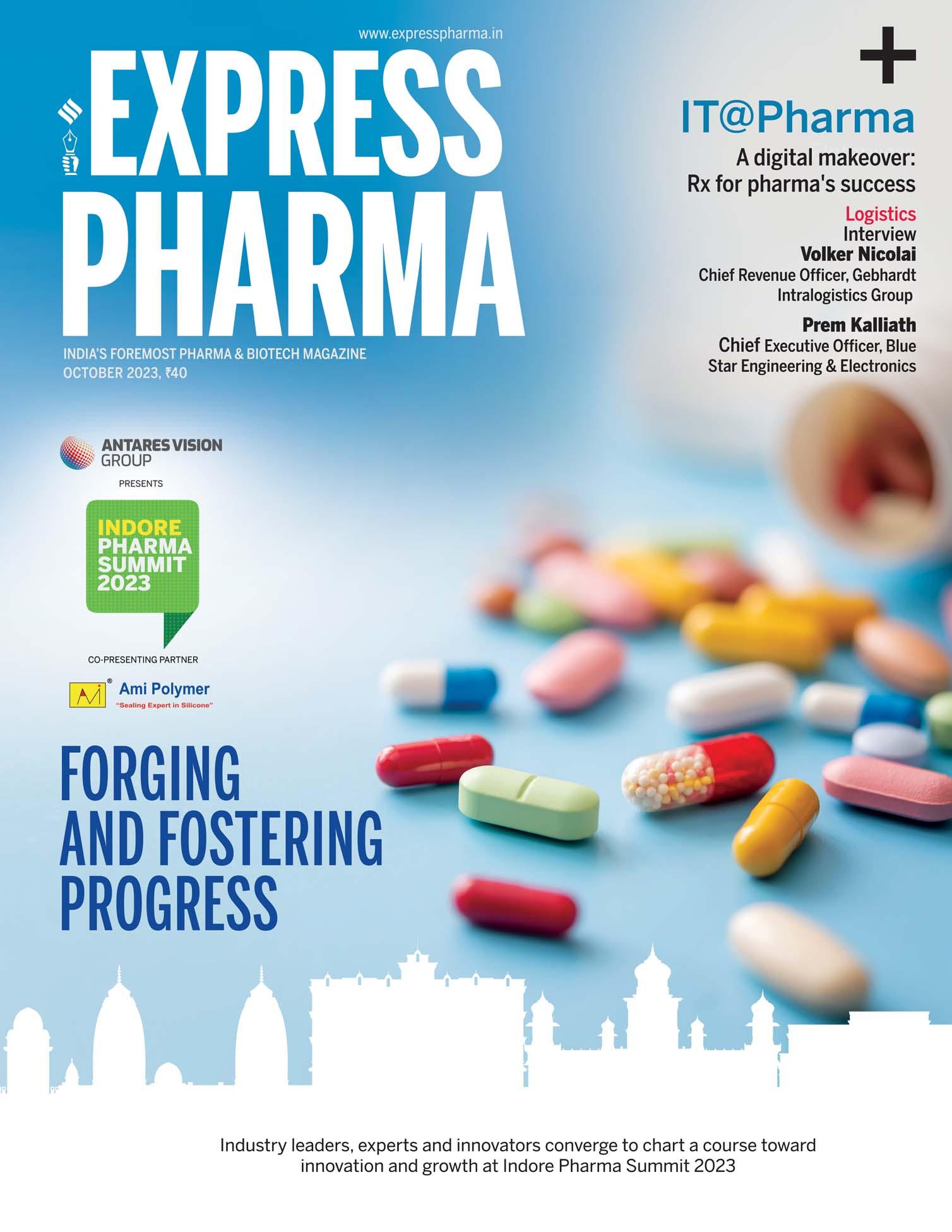

QbCon® 1
QbCon® 1
Material flow from raw material to dried granules in a truly continuous process
Fully automatic filter cleaning during the drying process with unprecedented consistency
Uniform pellet transport from feeding to discharge
Very short residence time and narrow residence time distribution
Easy scale-up for new product development
Chairman of the Board
ViveckGoenka
Sr.Vice President-BPD
Neil Viegas
Vice President-BPD
Harit Mohanty
Editor
Viveka Roychowdhury*
Editorial Team
Lakshmipriya Nair
Kalyani Sharma
DESIGN
Art Director
Pravin Temble
Senior Designer
Rekha Bisht
Senior Artist
Rakesh Sharma
Marketing Team
Rajesh Bhatkal
Ashish Rampure
Debnarayan Dutta
Production Co-ordinator
DhananjayNidre
Scheduling & Coordination
Pushkar Waralikar
CIRCULATION
Mohan Varadkar
Industryleaders,experts and innovators converged to chart a course toward innovation and growth at Indore Pharma Summit 2023 | P28
P18: INTERVIEW
PREM KALLIATH CEO,BLUE STAR ENGINEERING & ELECTRONICS
VOLKER NICOLAI CHIEFREVENUE OFFICER, GEBHARDT INTRALOGISTICS GROUP GMBH
22 PHARMALABORATORYEQUIPMENT: GROWTH, CHALLENGES AND TRENDS IN INDIA IT@PHARMA
15 EXPRESS PHARMA TO HOSTSIKKIM PHARMASUMMIT 2023 IN OCTOBER
42 ADIGITAL MAKEOVER: RX FOR PHARMA'S SUCCESS
400021. Editor: Viveka Roychowdhury.* (Editorial & Administrative Offices: Mafatlal Centre,7th floor,Ramnath Goenka Marg,Nariman Point,Mumbai 400021)
* Responsible for selection of news under the PRB Act.Copyright © 2017.The Indian Express (P) Ltd.All rights reserved throughout the world. Reproduction in anymanner,electronic or otherwise,in whole or in part,without prior written permission is prohibited.
Glenmark Pharma’s 75 per cent stake sale in its API arm to Nirma, and the possibility of the biggest shake up in pharma rankings, as Cipla’s promoters mull a sell out, kept the pharma sector in simmer mode all through September.
Both deals are symptomatic of India Pharma Inc today. The exit of Cipla’s Hamied family from the driver’s seat will mark the end of an era. In my brief stint as editor of Ciplog, Cipla’s house journal, in the early 1990ties, and continuing as a journalist covering the pharma beat, I watched from the sidelines as Dr Y K Hamied championed low cost generics on the ‘patients over patents’ premise.
India’s pharma sector is clearly once again in consolidation mode. But while the big names are in the news, we could also see a similar consolidation among pharma MSMEs which might not hit the headlines. Besides the usual reasons (lack of interest/acumen from the GenNext of these pharma promoters, etc, proposed revisions to India’s pharma Good Manufacturing Practices (GMPs) in Schedule M could make or break MSME pharma units. The tightening noose of regulatory scrutiny could turn out to be a major driver for sellouts in the MSME sector over the next few months. While laggards managed to slip under the radar of global scrutiny, India’s Central Drugs Standard Control Organisation (CDSCO) now seems to be in crackdown mode.
In a follow up to Union Health Minister Mansukh Mandaviya’s statement in early August that pharma companies with an annual turnover of over Rs 250 crore will have to mandatorily adopt GMP standards within six months, and those with a turnover of less than Rs 250 crore would get six months more, the CDSCO has partnered with industry associations like Indian Drug Manufacturers' Association (IDMA), as well as drug inspectors via the All India Drugs Control Officers' Confederation (AIDCOC) to conduct online and offline awareness workshops, walking the participants through the proposed changes that will be part of the updated Schedule M. These workshops are set to continue over the next few months.
The comparison between the existing Schedule M and the draft upgraded version (as outlined in the presentation given by Dr Eswara Reddy, JDCI, CDSCO at one of these webinars) would require considerable expenditure and time. For instance, sanitation has been expanded from covering only
workers and manufacturing premises to cover ‘personnel, premises, equipment/apparatus, production materials and containers.’ Similarly, validations would extend beyond just the manufacturing processes, testing and cleaning to now include ‘premises, utilities and equipment’.
Another concern for smaller players is that the updated Schedule M will bring in mandatory annual audits of their approved suppliers, including raw material and packaging material suppliers. Currently, the frequency of such audits are left up to the manufacturer and are conducted on specific occasions, for instance, after product recalls or inspections by licensing authorities. This update ensures safer medicines, as it would prevent the use of suppliers who do not have the license for pharma-grade materials. This is clearly linked to instances of Made in India cough syrups found to contain high levels of the toxic diethylene glycol (DEG). However, annual audits would add to the documentation and administrative cost of doing business, especially painful for the MSME sector.
Product recalls would now need to be reported to the licensing authority, specifying a comprehensive system for prompt and effective recalls. Beyond reporting serious adverse drug reactions to the licensing authority, the draft updated Schedule M requires companies to have a pharmacovigilance system in place, and faulty manufacture, product deterioration and serious quality problems will need to be reported to the licensing authority.
Will such changes be too exhaustive to implement? Will CDSCO give industry more time for implementation? These are legitimate concerns. Let’s hope that these workshops are taken more seriously this time around and manufacturers implement the updated Schedule M in the right spirit. Given that pharma companies have previously complained that there was a mismatch between the states’ and center’s reading of these rules, with some state regulators being more benign than others, one hopes that these workshops will also result in more consistency in the interpretation and implementation of the rules across all jurisdictions.
VIVEKA ROYCHOWDHURY, Editor viveka.r@expressindia.com viveka.roy3@gmail.comWhile the big names are in the news,we could see a similar consolidation among pharma MSMEs which might not hit the headlines
Sikkim
Over the past few years, Sikkim has transformed into a bustling pharma hub with expansion prospects and a favourable business environment.
The combined efforts of the state government and the businesses themselves promote innovation in the life sciences sector of the state and enhance its global positioning, as well as advance a sustainable approach to pharma development in the area. Be it drug discovery, process innovation, or research collaborations, Sikkim's ecosystem encourages meaningful collaborations and boosts competitiveness. However, there are several measures needed to optimise its growth potential.
Therefore, Express Pharma is organising the fifth edition of the Sikkim Pharma Summit on October 13, 2023, at
the Hotel Mayfair, Gangtok.
Sikkim Pharma Summit 2023, under the theme, 'Volume to Value Leadership: Opportunities and Challenges for India Pharma Inc' will provide the opportunity for professionals in the pharma sector to come together and exchange ideas on the most recent trends, challenges, and opportunities in the industry. It will offer an opportunity to network and learn, meet policymakers, explore business opportunities, and stay up-to-date with the latest industry trends and developments.
Topics to be discussed
◆ Pharma leaders of tomorrow: Traits and tickets to play
◆ Balancing sustainability and progress: Sikkim's approach to pharma
◆ Global market access and evolving regulatory landscape
◆ Innovations in drug discovery and development
◆ Creating a futureready workforce
◆ Digital transformation in pharma
◆ Building robust and resilient supply chains
◆ Evolution and revolutions in pharma packaging
● Strategic location and connectivity: Sikkim's well-connected road networks and proximityto keycities make it an accessible location for the supplychain
● Government incentives and support: The State government has introduced a range of incentives and support mechanisms to attract pharma companies
● Clinical trials: The growing healthcare infrastructure in Sikkim presents opportunities for pharma companies to conduct clinical trials in diverse patient populations.
● Research collaborations: Sikkim's educational institutions and research centres can facilitate partnerships and collaborations between pharma companies and academia.
● Skilled workforce: Sikkim has been investing in education and skill development, cultivating a skilled workforce that can cater to the needs of the life sciences
● Sustainable and eco-friendlyapproach: The region’s commitment to eco-friendly practices resonates with the pharma industry's growing emphasis on sustainability
Q A Q A
Schott Glass India: Extractables are components of the container closure system (all packaging materials) that are released during a certain stress test procedure (e.g. aggressive solvents, exaggerated conditions of time and temperature). Leachables are components of the container closure system that are migrating into the drug formulation during usual production process and storage. The amount of E & L coming from the material is dependent on a lot of different factors like the material itself (glass or plastic; Type I or Type III glass), the converting process, pH value of the drug formulation, ionic strength of the formulation, closure system, sterilization methods, temperatures during processing and storage, secondary packaging, and many more. Due to this high amount of diverse parameters only the owner of the finished product (the Pharmaceutical company) is able and obliged to perform E & L studies on their products. These studies are done as stability studies (Extractables studies, accelerated aging studies, durability studies) to evaluate the quality and the compatibility of the packaging material.
Schott Glass India : Certain organic materials can interact with the drugs or alter the inner surface of the glass packaging. In some case e.g. the meniscus of the solution would appear more flat than without any organic materials. These particular containers are then rejected in the filling line due to improper filling even if they are properly filled. BSE bears the risk for the Creutzfeld-Jakob disease. These are only a few of the reasons why this information is requested by regulatories. For the production of glass temperatures of around 1600°C are needed. At this temperature all organic substances like BSE, Pthalates and others are decomposed. Also bacteria and other living organisms cannot survive these temperatures. When the tubing comes out of the melting tank it is absolutely pure and clean and free of any organic material.
For more information contact:
santosh.jadhav@schott.com
Pharma Summit 2023 will provide the opportunity for professionals in the pharma sector to come together and exchange ideas on the most recent trends,challenges,and opportunities in the industry
Blue Star Engineering & Electronics recently announced a partnership with Gebhardt Intralogistics Group of Germany,for warehouse automation solutions.In a freewheeling conversation, Viveka Roychowdhury asks Prem Kalliath, CEO,Blue Star Engineering & Electronics and Volker Nicolai, Chief Revenue Officer,Gebhardt Intralogistics Group GmbH why this is the right time to consider such warehouse automation solutions,and why pharma companies need to move from a product centric to a solution centric approach.Edited excerpts from the interaction
Mr Kalliath, what are the business drivers for such warehouse automation solutions for pharma companies in India?
Mr Prem Kalliath: The pharma industry in India has many components in its value chain, from the large API to formulation to specialty manufacturers, etc. All of them require automation, but different kinds of automation, depending on the kind of load they need to deal with, in terms of tonnage, number of SKUs and the number of destinations between all of them. These three factors will have implications in the way you store, pack and distribute your packages.
One of the specific requirements we thought we should approach Gebhardt to work with us, is the need to have a whole basket of solutions relevant for different players and for the same player at different points in time. That's where we believe this partnership is unique.
We have something which works well for the API maker, we have something which works well for the formulation manufacturer, and also for the specialty manufacturer, which are across the chain. All the people who are getting into more direct to retailer, direct
to consumer will have requirements for things like automating their fulfillment centers, automating their distribution centers, etc.
Thus, this partnership is unique because it gives us a whole range of industry relevant solutions, while being compliant with all pharma requirements of regulation, traceability, etc. And in partnership with us, we can provide solutions which meet the requirements and also do it in a responsive, implementable and costeffective manner.
Mr Nicolai, can you share your experience of using such warehouse automation solutions globally in the pharma sector?
Volker Nicolai: Of course, we’ve had different global projects for our warehouse automation solutions in the pharma sector. Distribution and traceability are one of the main drivers for customers.
If you have an end-of-line packaging, full cartons can be traced to the palletising unit. It is then automatically taken by a robot, for example, and while the robot picks it up, it passes a barcode reader just to make sure that it is placed on the right pallet. Thus, traceability was one of the main drivers in the production area.
The second driver was on the distribution side. So, one is of course quality, traceability and then the other is volume. We have many online pharmacies in Europe, where you can buy even prescription medicine online. It is much more non prescription or healthcare/beauty products, where e-commerce gets more essential and creates volumes. You cannot do it anymore with manual procedures. With volumes, the effectiveness of such solutions comes in.
India is considered a price sensitive market and the pharma industry is price controlled, so they cannot
pass on too much of the price of implementing these technologies to their customers. How expensive are they compared to what they're using now or if they're not automating it? What is the return on
investment (RoI) and how fast can the client see RoI?
Nicolai: Usually I think, in Europe, it's sometimes an ROI of two to four years.
And in the India context?
Kalliath: I think in the
Indian context, too it will be similar. But I want to put it differently, I think one is in terms of a return on investment.
Secondly, in terms of (warehousing automation solutions being) a necessity
for the supply chain. I think almost everyone believes in the extent of change that ecommerce with epharmacies is bringing in. And of course, many companies also want to experiment. For companies
to meet their ambition to stay in touch with their consumers, to stay as close as possible with their retailers, it then becomes a necessity for doing it.
So, while the economics of it (implementing automation warehousing solutions) will be attractive, I think what's more important is that your right to play in this market requires you to have a degree of sophistication and automation.
In addition, the whole regulatory framework requires you to have this. If you look at it, from a business ROI point of view, rather than a pure financial ROI perspective, I think the returns will be very attractive.
What about the data that a pharma company or an epharmacy might gather from these automated solutions? Does Gebhard or Blue Star have solutions which help pharma companies and their customers gain insights from this data?
Kalliath: Within any automated solution that you have, we will get data on which products were how frequently purchased, by which customer. In fact, most of this is available with companies even now.
Companies can today even trace back to where it came from, especially from a
quality standpoint. But these solutions allow you to do it with the ease and speed at which you want to be able to do it.
And secondly, when you have all of these solutions, it will require an integration with a warehouse management or warehouse control, and finally, a distribution system as well. The end-to-end availability of information can help companies plan their supply chain networks much better, know what plan to service, which market, etc. All of this information will be available. And I'm sure many companies have already started doing it. It just enables the process and expedites a way in which they can move in that direction.
So, like you said, many pharma companies are already on this path. What is the USP of the Blue Star and Gebhardt partnership?
And what does each one bring to the table, in comparison to what is already available?
Kalliath: While forging this partnership, that was something which was uppermost in our minds. I think, with very few exceptions, most people come to the market with a product focused approach. Whereas we come with a pure solution focused approach.
So whichever company you may be, large, medium or small, we will have a solution which is tailored to the requirements. And that is, I think what we Blue Star and Gebhardt, together bring to the table: our ability to change or choose the right solution, depending on the requirement of the customer. Rather than being predisposed to what is available with a specific manufacturer or product supplier.
I think that is the biggest difference that we bring to the table. And both of us have the same mindset. Because I think the advantage that we have and the reason why we work with Gebhardt is the kind of range of product offerings that they have, and the expertise across industry, including pharma. I think that's where we collectively believe we have something which is working well and can be used to differentiate in the market. We are in early conversations with a few companies. I'm sure we will gain traction over the next few months.
So, Mr Nicolai, when you look at the India pharma market and the global pharma markets that you're already serving, where do you think your solution will need to really be customised for India conditions? We have to see what is the right level of automation.
The level of automation in Europe might be higher than in India. And then the second thing is the software processes, which need to be adapted.
We don't know about regulations here in India, besides FDA and GMP. But of course, Blue Star will be able to find this out, if they don't know it already.
And the next thing is, of course, the entire implementation of the project. Project management in Europe is different. And of course, this cannot be a European company. For every successful project, you have to have an essential project management team, which runs the project in an effective way, communicates with partners and therefore we are pretty much sure that our partnership with Blue Star is ideal.
What do you estimate will be the project implementation time because implementing any new systems does take time, training, etc.?
Kalliath: Absolutely. Based on our experience, any of these projects will take anywhere between 12 to 18 months to implement. And that's the normal timeframe. From when you sign up for an order, to actually having a system implemented and delivering the results that you expect, the entire cycle
I think the pharma industry is particularly well poised to benefit from the automation solutions that are on offer.They are an adopter of automation solutions,but the way they have adopted it typically tends to be a little more product centric rather than solution centric.And that's not really what we bring to the table
can take anywhere between 12 to 18 months, and sometimes even longer. I think that's where the project management capability, which Nicolai was referring to, becomes very critical and important. And in addition to the
expectations, as well as global standards and becomes cost effective in the Indian context. That's really what we're looking at. I think the pharma industry is particularly well poised to benefit from the automation solutions that are
on offer. They are an adopter of automation solutions, but the way they have adopted it typically tends to be a little more product centric rather than solution centric. And that's not really what we bring to the table. Because we have a
knowledge of the market, we have a whole range of solutions that we can offer. And I think we have the openness to consider various models in which it can work which meets the requirements from all dimensions: cost, quality,
implementation timeframe and flexibility. I think that's really what a partnership between Blue Star and Gebhardt collectively brings to the table.
viveka.r@expressindia.com
viveka.ory3@gmail.com
project management, I think what we are also doing is trying to see which part of the systems can be localised and indigenised. That will be a very important part that we play as we go forward and help customers to realise better ROI, if that's the way they want to be looking at it.
There is good engineering capability in India, there is a developing ecosystem, and with our knowledge of the engineering of the product and the available supply chain, I think together, we can come up with a solution which meets all the
EXPRESS PHARMA 21
October 2023
While the economics of it (implementing automation warehousing solutions) will be attractive,I think what's more important is that your right to play in this market requires you to have a degree of sophistication and automation
Amit Sehgal,Managing Director,Avantor India outlines how the pharma lab equipment sector in India is experiencing robust growth,driven by increased investments in healthcare,R&D infrastructure,and government initiatives.Emerging trends like digitalisation and technological advancements are also shaping the industry's future
Across the world, amongst the many key areas of development, laboratory equipment, instrumentation, and consumables play a critical role in the growth of the pharma sector. According to a market report, the size of laboratory equipment services market is estimated to reach $22.1 billion by 2027, growing at a CAGR of 11.1 per cent during the forecast period 2022-2027. Furthermore, the Asia-Pacific region has the fastest CAGR rate over the forecast period due to factors like increased clinical trials by key players in the developing economies of the Asia-Pacific region. [1]
In India, the laboratory equipment market is primarily driven by factors such as increased investments in the healthcare sector, growing awareness about health-related issues as demand for new and enhanced drugs increase, growing expenditure in enhancing the R&D infrastructure in pharma and healthcare with pharma companies doubling down on establishing innovative labs are fueling the demand further. Pharma giants outsourcing their manufacturing to Indian companies have added to the growth.
Also, more investments are being made in R&D of developing and manufacturing best-inclass lab tools and apparatus by the equipment manufacturers, propelled by growing need to diagnose lifestyle diseases that are increasing rapidly.
The country’s lab equipment market is also experiencing growth as the government takes various steps to make the pharma, life sciences, and healthcare industry more resilient and to become a hub for global research and develop-
ment initiatives. These include measures such as increased funding for life sciences, expansion of clinical capabilities, and growing academic-industry collaborations. For instance, according to industry research reports, in April 2020, the Department of Biotechnology
announced that about 16 companies were granted funds to boost their R&D for the development of drugs and vaccines to speed up the process with an aim to tackle the Covid-19 infection. [2]
Initiatives such as Production-Linked Incentive (PLI) Scheme to drive domestic manu-
facturing of key starting materials (KSMs)/drug intermediates and active pharmaceutical ingredients (APIs) within the country is another influencing factor that is giving strong impetus to the lab equipment manufacturers to ramp up their processes and operations across the supply chain.
India graduates a tremendous number of science and engineering students, so that there is a broad pool of laboratories in the country to draw from. Recently, University Grant Commission [3] instructed all higher education institutions (HEIs) to register their grant and research project approval requirements with the aim to fast-track the functioning of pharma and R&D agencies. This would enable the public and private varsities to get faster approvals for their research, increase transparency, and ease the accessibility of research funds to scholars for buying lab instruments and equipment. With expedited approvals process, the demand for lab equipment will see a higher uptick.
The market’s growth depend on the need for achieving keener accuracy in diagnosis with advanced laboratory apparatus, reduced downtime, effectively meeting all quality control standards and cost-effectiveness. Here, companies such as Avantor, a life sciences leader, can play a pivotal role. Avantor’s broad portfolio is used in virtually every stage of the most important research, development and production activities in the industries it serves. The company offers everything from high purity products, equipment and
instrumentation to services optimising scientific workflows.
Moreover, the added advantage of availability of cheaper and larger base of skilled workforce is prompting the government and investors to encourage new vendors to establish highquality, innovation laboratories in the country to help promote this sector.
Support in the form of investments from public and private sectors, initiatives under the ‘Make in India’ and reduced dependence on import of superior equipment from international markets are all coming together to help the domestic lab equipment manufacturers. Avantor has tied up with few local players to offer basic equipment under this initiative.
In today’s digital era, technology has become the key enabler in accelerating digital transformations across the industry spectrum and the same holds true for lab equipment services segment as well. Implementation of emerging technologies such as Artificial Intelligence (AI), Internet of Things (IoT), process automation, predictive analytics, and mixed reality, amongst others, are helping expand production and efficiency in lab equipment manufacturing, procurement, and management.
Increasingly, digital lab solutions are being developed to help enhance every critical stage of lab management and support digitisation throughout the lab ecosystem. Solutions covering aspects of inventory, chemical, and equipment management are being adopted to help monitor, manage, and automate timeconsuming tasks and processes. Doing so, the lab scientists, re-
Support in the form of investments from public and private sectors,initiatives under the ‘Make in India’and reduced dependence on import of superior equipment from international markets are all coming together to help the domestic lab equipment manufacturers
searchers, and experts can focus more on their core tasks instead of spending productive time dealing with non-core work.
Also, lab automation plays a vital role in accelerating science across biopharma discovery involving high throughput genomic and cell biology assays, agricultural & food, and medical research.
Products including self-testing kits and portable equipment like miniaturised centrifuges have also gained importance with the development in nanotechnology and miniaturisation, point-of-care testing. They are expected to boost growth in the general lab equipment manufacturing market in the future.
Equipment manufacturers will continue to make higher investments in new technologies and equipment for laboratory process optimisation, integrated automation for key data insights, as well as intellectual property protection. We would see greater demand for sophisticated and cutting-edge lab equipment and instruments such as DNA amplifiers, spectroscopy, and immunoassay analysers, to name a few, to help in bringing in higher efficacies, improve time-to-market and reduce costs in various processes including drug discovery, testing and analysis, production, and marketing. This is likely to continue to rise in coming times, backed by increased demand for improved features, including sustainability, automation, data integrity and portability. For instance, Avantor Science offer its customers in life sciences industry cloud-based, proprietary digital solutions that help manage their day-to-day operational, regulatory, and data- and metrics-based insights to optimise their workflows and create results.
Today, India is known for its potential as a global hub for drug manufacturing, and in fact, powered by lab manufacturers has built a strong standing as a global research centre.
As the healthcare and pharma industry continues to evolve and grow, its ripple effect in terms of technological innovations, investments, digitalisation
across the supply chains, and changing consumer behaviors are creating new opportunities in areas such as drug discovery, research & development, and API manufacturing, and in fact, across the entire value chain. All this has a direct and indirect impact on the growth of lab equip-
ment and services segment too. As our pharma and healthcare industry continues to cater to the growing demands for better healthcare solutions in the country, both public as well as private players across segments, including lab equipment manufacturers need to focus more deeply to-
wards establishing sustainable, future-ready development and expansion strategies to provide the best-in-class products and services for a better, healthier, and safer tomorrow.
References
[1] https://www.industryarc.com
/Report/16800/laboratory-equipment-services-market.html
[2] https://www.expresspharma.in /equipping-progress/
[3] https://timesofindia.indiatimes. com/education/news/biorrap-toreduce-wait-period-for-scholars-topurchase-lab-equipment/articleshow/97225008.cms
In an industry where compliance is non-negotiable and operational efficiency is paramount, pharma companies are taking a proactive approach. Moving beyond the limitations of BPA, the industry is embracing Process Excellence Applications (PEA) to tackle regulatory challenges and supercharge productivity. This article delves into the transformative journey from business process application to excellence, highlighting the factors.
Understanding Business Process Application
BPA involves using technology to automate and streamline an organisation's repetitive, rule-based tasks and workflows. By eliminating manual interventions, BPA reduces errors, accelerates processes, and frees up valuable human resources for strategic decision-making and high-value activities.
BPAin pharma: Enhancing efficiencyand compliance
In the pharmaceutical industry, where stringent regulations and quality control are paramount, BPA becomes a gamechanger. From research and development to manufacturing, distribution, and post-market surveillance, BPA optimises processes, minimises errors, and ensures compliance with regulatory standards. Here are some notable benefits of BPA in the pharma sector:
◆ Efficiency: BPA reduces manual interventions, leading to faster processes, reduced cycle times, and increased productivity.
◆ Accuracy: Automation minimises errors, ensuring data integrity and product quality.
◆ Compliance: BPA helps
maintain compliance with stringent regulatory standards, reducing the risk of non-compliance penalties.
◆ Resource optimisation:
Organisations can allocate human resources to more strategic activities by automating repetitive tasks.
◆ Data-driven insights: BPA
generates data that can be analysed for insights, enabling continuous process improvement.
However, it's reshaping the
pharma industry by combining technological advancements with regulatory compliance.
Software solutions like Learning Management Systems (LMS), Document Management Systems (DMS), Electronic Batch Records (EBR), Quality Management Systems (QMS), and more are pivotal in automating processes toward a future of streamlined operations and sustained success.
Fewsoftware solutions for BPAin pharma
◆ LMS: Training and skill development are vital in the pharmaceutical sector. LMS software automates training by providing a centralised platform for creating, delivering, and tracking training programs. It ensures that employees are up-to-date with the latest regulations, procedures, and industry standards, contributing to enhanced compliance and quality.
◆ DMS: Accurate document management is crucial in a highly regulated industry like pharma. DMS software offers a centralised repository for storing, organising, and managing documents, such as Standard Operating Procedures (SOPs), batch records, regulatory submissions, and more. Automation within DMS ensures version control, easy retrieval, and timely approvals, all while maintaining data integrity.
◆ EBR: EBR software automates batch record creation, management, and review. It replaces paper-based processes, reducing the risk of errors, ensuring consistency, and expediting the review and approval cycles. EBR enhances traceability, making it easier to identify deviations and maintain
BPAis a transformative approach the pharma industry can leverage to drive operational excellence,enhance product quality,and ensure regulatory compliance.The industry can achieve Business Process Excellence (BPE) by automating critical processes across various domains,improving efficiency,and supporting better decision-making and innovation
compliance.
◆ QMS: QMS software automates quality assurance processes, including deviations, Corrective and Preventive Actions (CAPA), change controls, and audits. It provides real-time visibility into quality-related activities, enabling timely responses and minimising risks of non-compliance.
Integrating various software solutions within a pharmaceutical organisation's ecosystem creates a harmonious digital environment that fosters efficiency, accuracy, and collaboration. The interconnectedness of these systems ensures a seamless flow of data and information across departments, minimising errors and enabling swift decision-making.
LMS
◆ Integration with other software: LMS can seamlessly automate employee onboarding and training assignments based on roles.
◆ Integration with compliance tracking: LMS can be linked with compliance tracking software to ensure that training requirements align with regulatory standards.
◆ Impact on regulatory observations: Properly trained employees are better equipped to follow regulatory guidelines, reducing the risk of non-compliance observations.
DMS
◆ Integration with other software: DMS can integrate with enterprise applications such as ERP and CRM to ensure the organisation's most up-to-date documents are available.
◆ Version control integration: Linking DMS with workflow tools helps document review and approvals, ensuring the correct versions are used.
◆ Impact on regulatory observations: Access to accurate, current documents promotes adherence to regulatory requirements, minimising observations during audits.
EBR
◆ Integration with manufacturing systems: EBR software can be integrated to capture real-time data directly from production processes.
◆ Linking to quality control: Integration with QMS allows deviations or quality issues
identified during production to be addressed in the same system.
◆ Impact on regulatory observations: Real-time data capture and direct linkage to quality processes minimise errors and enhance compliance, reducing observations.
QMS
◆ Integration with EBR and LIMS: Integrating QMS with EBR and Laboratory Information Management Systems (LIMS) ensures a closed-loop quality control process.
◆ Linking to CAPA management: Integration with CAPA
management systems enables swift action on identified issues.
◆ Impact on regulatory observations: QMS integration enhances traceability and facilitates the timely resolution of quality-related concerns, mitigating observations.
BPA is a transformative approach the pharma industry can leverage to drive operational excellence, enhance product quality, and ensure regulatory compliance. The industry can achieve Business Process Excellence (BPE) by automating critical processes across various domains, improving efficiency, and supporting better decision-making and innovation. Let's delve into how BPA can drive excellence in these crucial domains:
1. Quality control (QC) planning: BPA enables a proactive approach to quality by automating and optimising QC planning processes. Through BPA, pharmaceutical companies can streamline the scheduling of tests, sampling, and analysis, ensuring adherence to strict quality standards. Automation facilitates real-time monitoring of QC activities, alerts for deviations, and data-driven decisionmaking. By integrating BPA into QC planning, organisations can reduce human errors, ensure consistent compliance, and enhance product quality.
2. Capacity planning: Capacity planning is vital for efficiently meeting market demands while avoiding resource wastage.
BPA transforms this process by automating data collection on
production output, resource availability, and demand forecasts. Advanced analytics within BPA systems analyse this data to predict future capacity requirements, allowing for proactive adjustments. This integration ensures optimal resource allocation, minimises production bottlenecks, and enables responsive decisionmaking.
3. Anytime Product Quality Review (APQR): APQR is a regulatory requirement demanding a comprehensive product quality assessment over time. BPA simplifies this process by automating data aggregation from various sources, such as manufacturing records, quality control data, and adverse event reports. Automated analytics tools identify trends, deviations, and insights, facilitating APQR report generation. BPA not only ensures compliance but also drives continuous improvement through actionable data.
4. Skill evaluation and training: BPA empowers skill evaluation and training processes by automating training program management, skill assessments, and compliance tracking. Learning Management
❒ Express Pharma accepts editorial material for regular columns and from pre-approved contributors / columnists.
❒ Express Pharma has a strict non-tolerance policy of plagiarism and will blacklist all authors found to have used/refered to previously published material in any form,without giving due credit in the industryaccepted format.All authors have to declare that the article/column is an original piece of work and if not, they will bear the onus of taking permission for re-publishing in Express Pharma.
❒ Express Pharma's prime audience is senior management and pharma professionals in the industry.Editorial material addressing this audience would be given preference.
❒ The articles should cover technology and policy trends and business related discussions.
❒ Articles for columns should talk about concepts or trends without being too company or product specific.
❒ Article length for regular columns: Between 12001500 words.These should be accompanied by diagrams,illustrations,tables and photographs, wherever relevant.
❒ We welcome information on new products and services introduced by your organisation for our various sections: Pharma Ally (News,Products,Value
Add),Pharma Packaging and Pharma Technology Review sections.Related photographs and brochures must accompany the information.
❒ Besides the regular columns,each issue will have a special focus on a specific topic of relevance to the Indian market.
❒ In e-mail communications,avoid large document attachments (above 1MB) as far as possible.
❒ Articles may be edited for brevity,style,and relevance.
❒ Do specify name,designation,company name, department and e-mail address for feedback,in the article.
❒ We encourage authors to send their photograph. Preferably in colour,postcard size and with a good contrast.
Email your contribution to: The Editor, Express Pharma, Business Publications Division,The Indian Express (P) Ltd, Mafatlal Centre,7th floor,Ramnath Goenka Marg, Nariman Point,Mumbai 400021 viveka.r@expressindia.com viveka.roy3@gmail.com
Software (LMS) powered by BPA streamlines onboarding, skill development, and training assignments. Automation ensures employees are equipped with the latest knowledge and competencies, fostering a culture of excellence and expertise.
5. Quality metrics management: BPA is crucial in capturing, analysing, and managing quality metrics. Automated systems collect data from various stages of the manufacturing process, transforming it into actionable insights. BPAenabled Quality Management Software (QMS) enables realtime monitoring of deviations, Corrective and Preventive Actions (CAPA), and change controls. This integration facilitates prompt responses to quality-related issues, reducing risks and optimising product quality.
Arriving at business process excellence
◆ Assessment and alignment: Begin by assessing existing processes and identifying areas that can benefit from BPA. Ensure that automation aligns with regulatory requirements and industry best practices.
◆ BPA solution selection: Choose BPA systems tailored to the pharmaceutical industry's unique needs. Look for features such as process modeling, integration capabilities, real-time monitoring, and advanced analytics.
◆ Workflow design and integration: Design automated workflows encompassing the entire QC planning, capacity planning, APQR, skill evaluation, and quality metrics processes.
◆ Data integration: Integrate data sources such as laboratory
information management systems, manufacturing equipment, and historical production data to create a unified data repository.
◆ Real-time monitoring and analytics: Implement BPA systems offering real-time monitoring and analytics capabilities to detect deviations, trends, and opportunities for improvement.
◆ Change management and training: Facilitate a smooth transition by training employees on the benefits and functionalities of automated processes. Encourage collaboration and adaptability.
◆ Continuous improvement: Regularly assess BPA-enabled processes, using data insights to optimise workflows, enhance compliance, and improve overall performance.
The pharma industry can elevate its operational efficiency,
regulatory compliance, and product quality by harnessing the power of Business Process Application in QC planning, capacity planning, APQR, skill evaluation, and quality metrics. BPA's integration fosters a culture of continuous improvement, empowering organisations to achieve Business Process Excellence and provide patients with safe, effective, and reliable pharmaceutical products.
In the dynamic realm of the pharma industry, the imperative for adherence to rigorous compliance standards and the pursuit of unrivaled operational efficiency converge. Within this landscape, pharma companies are transcending the boundaries of conventional Business Process Applications (BPA) and
embracing the monumental potential of Process Excellence Systems (PES). This strategic shift is not only addressing intricate regulatory challenges but is also fueling an unparalleled surge in productivity.
The path to achieving excellence is paved with careful planning, smart integration, and a commitment to improving. This journey has several steps, like analysing, aligning, choosing solutions, designing workflows, integrating, training users, implementing, keeping track, and ensuring compliance. Each step works together like a well-coordinated orchestra to help pharmaceutical companies reach the peak of Process Excellence. As pharma entities continue to embrace the potential of automation, they chart a course toward excellence that is as unwavering as it is transformative.
Industry leaders,experts and innovators converged to chart a course toward innovation and growth at Indore Pharma Summit 2023
Indore, with its strategic location, well-developed economic zones and industrial centres, skilled workforce can emerge as a big pharma hub andsignificantly accelerate the growth of the sector and of the economy. The city, with its conducive environment is well-positioned to add value and volume to pharma products.
Therefore, Express Pharma, organised the maiden edition of the "Indore Pharma Summit" on August 25, 2023, at the Sayaji Hotel, Indore.
IndorePharma Summit 2023 provides an opportunity for professionals in the pharma sector to come together and exchange ideas on the most recent trends, challenges, and opportunities in the industry. It also offered an opportunity to network, learn, access policymakers, explore business opportunities, and stay up-to-date with the latest industry trends and developments.
This article examines the major takeaways and learnings shared by the experts during the event.
Sandeep Raktate, Executive VP-International Operations, Cipla spoke on ‘Trends and Disruption Redefining Pharma Landscape,’ and provided valuable insights into the challenges and opportunities facing the pharma industry today.
Raktate pointed out that the industry faces numerous challenges such as the impact of the COVID-19 pandemic, patent expiries, regulatory hurdles, and continuous price erosion in the generics market. Rising input costs, cold chain losses, cybersecurity threats etc are also threats to be tackled. Then, he spoke on the potential of disruptive technologies to mitigate most of these challenges and alter critical functions in pharma, especially manufacturing. He
pointed out that technologies such as automation, AI and data analytics are transforming how medicines are produced, enhancing efficiency and reducing costs.
In a rapidly changing pharma landscape, the session underscored the need for adaptation and innova tion. Disruptive technologies hold the promise of improving manufacturing processes and
Digital technologies can help to mitigate challenges and optimise opportunities in pharma.We should move towards touch less factories and data-driven decision making
Sandeep Raktate Executive VP, Head International Operations and Central Manufacturing, Cipla
Digitalisation in pharma betters operational efficiency,reduces risk of human errors,improves quality and ensures transparency.Thus,it is a key enabler of compliance
Manickam Perumal Site Quality Head, Lupin, Pithampur
drug development, but they also necessitate a digital transformation across the industry. The challenges must be met with resilience and strategic planning. To thrive in this evolving landscape, companies must embrace change, invest in technology, and prioritise sustainability and quality. The insights shared during this session offer a roadmap for the industry
to navigate these challenges and emerge stronger and more resilient in the years ahead.
Indore Pharma Summit 2023 saw several thought leadership session. In one of them, Shaunak J Dave, MD & CEO,
Antares Vision Group (India) spoke on how India Pharma Inc needs to move from volume to value leadership, shifting focus to quality in healthcare outcomes, cost-effective innovation and patient-centric care. Citing Chandrayan Mission as an example, he pointed out that India can lead in cost-effective innovation in pharma too, provided the right mindset and strategies are adopted. He advocated the industry to imbibe and implement learnings from other industries to build an ecosystem that prioritises value-driven healthcare solutions.
Agility, forward thinking, continuous learning, environment consciousness, etc were some of the other qualities that he stressed upon as India Pharma Inc traverses its journey towards volume leadership. A key takeaway form his session was that the healthcare landscape is constantly evolving, so being agile enables pharma companies to quickly adapt to these changes.
Dave also gave a brief on the solutions offered by Antares Vision to aid digital transformation in pharma companies across functions like R&D, manufacturing and supply chain.
His session underscored that adopting volume to value leadership is essential for India Pharma Inc to remain competitive, enhance its global standing, address healthcare challenges, comply with evolving regulations, achieve sustainable growth, and ultimately provide better healthcare solutions for patients in India and around the world.
Manickam Perumal, Site Quality Head, Lupin, Pithampur, in his presentation on ‘Regulatory compliance in the digital age’, focused on the industry’s significant transformation in the digital age, with
Innovation,agility,cost effectiveness and growth mindset will be key to drive sustained progress in India’s pharma industry
Shaunak J Dave MD & CEO, Antares Vision Group (India)
the adoption of technologies such as data analytics, artificial intelligence, and blockchain. He said that these technologies can also ensure regulatory digital tools and real-time data aids in monitoring drug safety and efficacy as well. Likewise, industry needs to leverage and optimise digital documentation and electronic recordkeeping to enable Good Manufacturing Practices (GMP) and other regulatory standards, streamlining processes and reducing the risk of errors.
He went on to give exam- crucial functions in the operations automation such predictive analytics and tech-
production processes and improve product quality and operational efficiency in the modern pharma manufacturing landscape. Similarly, laboratory automation systems like LIMS reduces the risk of human errors, enhances the efficiency and reliability of quality control processes, and ensures seamless and accurate data management in scientific research and analysis. A quality system integrated with enterprise applications like QAMS, eDMS, SAP, eLogs, and eBMR, promote transparent and results-oriented data analysis within an
Workingtemperaturerange:-90°CtoRT
+919900674407|info@srico-labworld.com|www.srico-labworld.com
Disruptive technologies hold the promise of improving manufacturing processes and drug development,but they also necessitate a digital transformation across the industry.The challenges must be met with resilience and strategic planning.To thrive in this evolving landscape,companies must embrace change, invest in technology and prioritise sustainability and quality
challenges that hinder digital transformation such as resistance to change, legacy systems and practices, lack of adequate skills and training among employees, need for substantial investments in technology and infrastructure, data privacy and cybersecurity concerns etc. He also advised that successful digital transformation requires a holistic approach and a cultural shift enabled by strong leadership support, adaptable infrastructure, improved process capabilities, alignment with customer and regulatory expectations, and a flexibile business models.
A key take away from his session was that digital solutions can improve compliance and facilitate agile response to compliance issues, thereby ensuring that pharma products meet the highest quality and safety standards in this age.
Amit Chawla, Director of McW Healthcare and National Secretary/Vice Chairman of Federation of Pharma Entrepreneurs (FOPE) MP Chapter, addressed the critical topic of "Opportunities and Challenges for MSME (Micro, Small, and Medium Enterprises) Pharma at Indore Pharma Summit 2023. This session shed light on the potential of MSMEs in the pharma sector, with a particular focus on Indore.
Emphasising that Indore is a budding pharma hub with its strategic location, supportive infrastructure, and conducive business environment, he opined that the city can metamorphose into a pivotal centre for this industry. However, making quality paramount will be fundamental to the progress of Indore's pharma MSMEs. He underscored that while growth is essential, it should not come at the expense of compromising on product quality and safety. Maintaining high-qual-
ity standards is not only crucial for consumer health but also for establishing a reputation of trust within the industry.
He also encouraged the pharma industry to take proactive measures and invest in advanced manufacturing technologies, implement stringent quality control processes, and foster a culture of continuous improve-
Indore has the potential to be a key pharma hub.Pharma MSMEs are also contributing to this hub’s growth. Quality will be the key to progress of Indore’s pharma MSME.The industry should proactively take steps to ensure highest quality
Amit Chawla Director,McWHealthcare, National Secretary/Vice Chairman,FOPE- MPChapterCollaboration is key in the digital age.Pharma companies must foster collaborations with start ups and other partners to stay ahead of the curve
Anurag Chauhan
Digital Lead, Cipla
Ashift from volume to value requires pharma companies to focus on patient-centricity, cost effectiveness,as well as process and product efficiency, among other factors to position themselves for long term success
Umesh Gupta
VP& Site Head - Operations, Glenmark Pharmaceuticals
ment to enhance the competitiveness of Indore's pharma MSMEs and boost their sustainability. Thus, this session offered valuable insights into the opportunities and challenges facing MSMEs in the pharma sector, and was a valuable reminder that achieving sustainable growth in the pharma sector requires a commitment to excellence.
Chawla also provided a
roadmap for MSMEs in the pharma industry to thrive by prioritising quality, innovation, and continuous improvement.
Anurag Chauhan, Digital Lead, Cipla spoke on the digital disruption in pharma and said that the pharma sector is undergoing a major transfor-
mation due to digital disruption. This shift is fundamentally altering the sector’s operational dynamics. He delved into the cutting-edge technologies that are propelling this disruption and spoke on strategies for pharma firms to remain competitive in the digital era.
Elaborating on how embracing technology and harnessing digital channels, can help companies streamline their operations, enhance efficiency, and elevate overall patient experience, emerging technologies like artificial intelligence, blockchain, Internet of Things (IoT), and Big Data Analytics are acting as catalysts for change in the pharma industry. These innovations have the potential to revolutionise critical areas, ultimately leading to improved outcomes and heightened efficiency.
He also pointed out that AI, in particular, has emerged as a frontrunner in this digital transformation, influencing the pharma value chain, including drug discovery, clinical trials, precision medicine, supply chain management, quality control, predictive maintenance, process optimisation, and regulatory compliance.
His session also underscored the importance of collaboration in the digital age. He said that pharma enterprises must actively cultivate partnerships with startups and other collaborators to foster inn ovation and maintain a competitive edge.
Similarly, he also pointed out the criticality of effective talent management in the digital age. He emphasised that pharma companies must actively attract and retain toptier talent equipped with digital skills and capabilities. By nurturing a culture of continuous learning and innovation, these companies can cultivate a workforce that is agile, adaptable, and primed to embrace the opportunities brought about by digital disruption.
Umesh Gupta, VP & Site Head – Operations, Glenmark
Pharmaceuticalsspoke an interesting topic, 'A roadmap for value-driven, sciencebased hybrid business approach' at Indore Pharma Summit 2023.
He started his session by highlighting that the pharma industry is undergoing a shift from volume to value, and while this transformation is not without its challenges, it can improve patient outcomes, control costs, and enable long-term success.
He emphasised that to successfully navigate this land-
scape, pharma companies must identify the "tickets to play" including product quality and process compliance, regulatory credibility, a sound business strategy, cost competitiveness, and supply consistency and reliability and a talent pool equipped with the right tools and processes.
Admitting that implementing large-scale changes in the pharma industry is not easy
due to organisational and behavioral challenges, he advised the industry to shift from a reactive approach to a proactive one. He pointed out that the reactive mode is characterised by instability in production and process failures, inadequate technical risk analysis and resource allocation, unpredictable supply situations and recalls, etc.
Conversely, a proactive ap-
proach involves establishment of efficient processes and robust products, predictive analysis and maintenance, implementing life cycle management and building a stable supply chain for business growth. He also explained how MS&T can help companies to build and sustain a proactive approach.
He concluded that the journey from volume to value
in the pharma industry is imperative and transitioning from reactive to proactive approaches; companies can position themselves for sustained growth in an evolving landscape.
The maiden Indore Pharma Summit proved to be a valuable platform for industry professionals to come together and discuss a wide range of critical topics, from regulatory compliance to quality leadership. The event facilitated the exchange of ideas, the exploration of innovative solutions, and the identification of strategies for success in the pharma sector.
Digital solutions can improve compliance and facilitate agile response to compliance issues, thereby ensuring that pharma products meet the highest quality and safety standards in this age.
The Indore Pharma Summit 2023 featured a series of sessions and presentations focused on products and solutions furthering advancements in the life sciences industry.Asummary of those sessions from the event
Yadnesh Sanzgiry's presentation highlighted the role of digitalisation and disruptive technologies. He also underscored the impact of technology on pharma manufacturing and production. He pointed out that pharma companies, recognising the potential of IoT, AI, and digital technologies, are making substantial investments to enhance efficiency and quality.
He introduced DIAMIND Factory by Antares Vision India and informed that it is a comprehensive solution aimed at leveraging digitalisation to optimise manufacturing processes. It offers a central platform to connect machinery and extract data for analysis. The idea behind DIAMINDisation is to connect manufacturing machines to the DIAMIND tool, facilitating seamless col-
Dhairy Sharma, Technical Sales, Cilicant, delivered an informative presentation at the Indore Pharma Summit 2023, highlighting the pivotal role that packaging plays in the drug development. His presentation centered on active packaging and its role in preserving the quality and extending the shelf life of pharma products.
Sharma emphasised that active packaging goes be-
At the Indore Pharma Summit 2023, Aman Sharma, Sales Development Manager at SCIEX, emphasised the critical role of identifying and eliminating nitrosamines in pharma products to safeguard patient health. Nitrosamines, as impurities in medications, pose a significant health risk. Regulatory bodies such as the FDA have implemented strict guidelines and testing requirements to detect and mitigate nitrosamine contamination in pharma products. He also showcased SCIEX's solu-
lection and organisation of data. This data is then transformed into actionable insights through visual dashboards that focus on specific Key Performance Indicators (KPIs).
He also informed that the DIAMIND factory solution is paperless, shareable, scalable and modular; facilitates analysis; enables decision based on data driven facts; provides quick return of investments; and supports operational excellence, lean manufacturing process and total productive maintenance.
yond mere containment and protection. It actively interacts with the contents to maintain their integrity and efficacy. He also illustrated how innovative solutions by Cilicant can significantly benefit pharma companies by safeguarding their products.
His presentation spotlighted Accuflip, a humidity regulator provided by Cilicant. He informed that this specialised technology plays a crucial role in maintaining the ideal moisture levels within capsules, preventing them from becoming too dry or overly moist. This control over humidity is vital for ensuring the stability, effectiveness, and efficiency of pharma products.
In conclusion, Dhairy Sharma's presentation assured that Cilicant's active packaging solutions align with the industry's evolving needs and regulations, ensuring that pharma companies can maintain the highest standards of product quality and safety.
tions as a leader in analytical technology, for nitrosamine detection and quantification. He also informed that NDSRI are quantifiable using LC-MSMS and SCIEX has the right solutions for the same. He stressed that with the right analytical machinery, SCIEX contributes to realising the full potential of pharma and ultimately improving human health by ensuring the safety and quality of medications in the market.
At the Indore Pharma Summit 2023, Prabhat Balyan, Manager-Business Development at Ami Polymer, shed light on the pivotal role of polymer solutions in the drug manufacturing process. He elaborated on the diverse applications of tubing and hoses in the life sciences sector, and accentuated the importance of tailoring these solutions to meet the
During his presentation on "Empowering Pharma Compliance: Exploring Cutting-edge Solutions," Rohit Chakravorty, Application Manager- Life Sciences: APAC, from Veolia WTS Analytical Instruments, provided insights into his company and its innovative solutions. Specifically, he spotlighted the Sievers product line and informed that it has played a significant role in Total Organic Carbon
Meenu Bansal, Field Marketing Expert, Merck Life Sciences, delivered a presentation focusing on Merck's product, Milli-Q. Her presentation illuminated how Milli-Q Lab Water portfolio is relevant to pharmaceuticals, clinical laboratories, academia, industrial settings, research institutions, and government laboratories.
Bansal emphasised the versatility of the Milli-Q system and informed that it can be tailored to meet the specific water purification needs of each application. She informed that by offering tailored solutions, Merck ensures that customers receive an effective water purification system suited for their unique purposes.
Her presentation also highlighted how water dis-
unique requirements of different pharma products. Balyan also underscored how precision-engineered polymeric products can help pharma companies to adhere to stringent regulatory standards, ensuring both safety and efficacy.
He concluded his presentation by conveying Ami Polymer's commitment to partnering with the pharma industry to provide tailored polymer solutions that align with their specific drug manufacturing needs. He said that by offering specialized and compliant polymer solutions, Ami Polymer contributes to the pharma sector's ability to manufacture high-quality and regulatory-compliant medications.
(TOC) analytical instrumentation for the past 25 years. Chakravorty emphasised the importance of compliance in the pharma industry, and highlighted that Sievers ensures compliance across all four critical water parameters, conductivity, TOC, endotoxin, and bioburden. Compliance in these areas is essential to guarantee the safety and quality of pharma products.
The focus of his presentation was Sievers Eclipse, a solution designed to enhance Bacterial Endotoxin testing in terms of compliance, consistency, and environmental consciousness. Chakravorty delved into the innovative features and advantages that the Sievers Eclipse brings to the pharma industry.
He concluded that the Sievers Eclipse, with its advanced features and advantages, presents a significant leap forward in bacterial endotoxin testing, contributing to the pharma industry's mission of ensuring product safety and regulatory compliance.
pensing is optimised by Milli-Q systems to provide high-quality purified and ultrapure water consistently. This consistency is essential for laboratories and facilities in various industries, as it ensures a reliable and uninterrupted supply of pure water, which is fundamental for experiments, processes, and analyses that demand the highest water quality standards.
In summary, Meenu Bansal's presentation shed light on Merck Life Sciences' commitment to delivering top-tier water purification solutions through the Milli-Q Lab Water portfolio. The Milli-Q system's reliability, adaptability, and ability to provide consistently high-quality water underscore its significance in life sciences.
As pharma industry undergoes a digital renaissance,industry leaders share insights on the pivotal role of technology in navigating complexities from supply chain uncertainties and field force management,to sustainability and shop floor automation in reshaping the future of pharma
The pharma sector is slowly shedding its image as a digital laggard.
The jolt from the COVID pandemic saw many companies hasten their digital transformation journey. Many of the early birds are tasting the low-hanging fruits of these forays. But a lot still needs to be done to truly catch up with other sectors.
So what are the best practices and learnings of these pharma digital torchbearers?
Express Pharma, IPA, AWS and SAP conducted a Thought Leadership Forum on the importance of Maximising Value from Digital Transformation in the pharma industry. We summarise some key takeaways from this interaction.
The storyso far…
Setting the context, the keynote address by Dr Sudarshan Jain, Chairman, IPA gave an overview of various aspects of the pharma industry, including security in cloud applications, vendor performance, supply chain uncertainties, and digitalisation of the field force. He emphasised the importance of investing in secure environments for enterprise applications and aligning procurement policies with vendor quality and performance. He also highlighted the need to build alternatives within the supply chain to mitigate uncertainties and enable the field force through intelligent recommendations.
Touching on embedding technologies like intelligent process automation and AI within business processes and discussing the challenges and changes in the Indian pharma sector, Jain spoke about the importance of leveraging technology, sustainability, demand forecasting, and supply chain control towers is also emphasised. He suggested adopting practices from other indus-
tries, reinventing sales and operations planning, and focusing on digital tools and analytics.
He concluded by expressing his
Suresh
Dhaval
desire to collaborate for betterrun pharma organisations and improved patient outcomes.
Next, Sudakshina Ghosh, Sr.
Director SAP Customer Advisory Practice, Rohit Sinha, Principal BD, AWS and Sanjeev Joshi, Partner, PWC gave
their insights on how digital transformation is imperative for the life sciences industry.
Calling it the ‘power of three’ Sinha highlighted how the partnership between SAP, AWS and PWC resulted in a perfect platform of innovation, which will give life sciences companies deep insights into where they can be, where they want to be, and how can they get there.
Commenting on how the digital journey of pharma companies has accelerated particularly post-pandemic, Joshi spoke about how each partner had solutions for different facets of this journey, be it across the vendor ecosystem, pharma operations or the customer interface. He emphasised that having a digital strategy, the right roadmap, the right products and the implementation partner is the key to success.
The three speakers jointly addressed points related to security, vendor performance, supply chain uncertainties, and digitalisation of the field force. The focus is on ensuring security as applications move to the cloud, with investments being made to run enterprise applications in secure environments with disaster recovery management infrastructure.
Rounding off the session, Ghosh mentioned the importance of aligning procurement policies with vendor quality and performance, and the need to build alternatives within the supply chain to mitigate uncertainties. Additionally, there is an emphasis on enabling the field force through intelligent recommendations to streamline sales processes. She also briefly touched on how technologies like intelligent process automation and generative AI are getting increasingly embedded applications to deliver better business process execution.
Invest in secure environments for enterprise applications and align procurement policies with vendor quality and performance.There is a need to build alternatives within the supply chain to mitigate uncertainties and enable the field force through intelligent recommendations
Dr Sudarshan Jain Chairman, IPA
JB Pharma's focus area of digitisation continues to be automation and process optimisation,using data to get good insights,create value by increasing efficiency of capital,operational efficiencies which would help increase revenues
Bhise CIO, JB Pharmaceuticals
As much as technology interventions are required,I think there are more process and people interventions required.So a lot of chain management and capability building is where investments are being made
Pandya CIO, Piramal Enterprises
Ghosh also discussed how SAP is leveraging Chat GPTbased capabilities to expand incident reporting capabilities within EHS and asset maintenance processes. She highlighted the use of visual character recognition and language models to create incident reports, propose solutions, and make changes to future processes via continuous monitoring. Emphasising that these capabilities are being delivered today, she showcased how these AI-driven process innovations can be easily consumed by leveraging simple API constructs. She also mentioned the importance of language models for companies with global operations to ensure consistent incident reporting.
With this context, the session segued into the first panel discussion, moderated by Viveka Roychowdhury, Editor, Express Pharma , with pharma CIOs and CFOs sharing their learnings on and highlighting specific areas where they have maximised the value of digital transformation.
Salesforce optimisation: Expanding on his learnings
Suresh Bhise, CIO, JB Pharmaceuticals said the focus area of digitisation in his company continues to be automation and process optimisation, using data to get good insights, create value by increasing efficiency of capital, operational efficiencies which would help increase revenues. “We want to grow gradually on this, create value, show deliveries from the IT side to the business, and go closer to the business,” said Bhise.
Giving an example, he recounted how in the sales area, J B Pharma has created applications that have enabled the sales team to meet their targets, plan their doctor visits, utilise time spent waiting at doctor clinics to train themselves via e-learning modules, as well as pass on real-time data from chemists and distributors via apps back to the corporate team, which can then analyse the data to ensure production, marketing etc are in sync.
Advancements in technology have made the lives of supply chain professionals easier,with tools like artificial intelligence assisting in demand forecasting and inventory allocation
Sreenivas Rao NandigamSupply chain departments need to adopt online deliveries,engage with doctors and patients through influencers,and expand distribution to midtowns and rural areas
Shop floor automation: For Dhaval Pandya, CIO, Piramal Enterprises the focus is on increasing productivity, getting more out of investments already made and targeting the systems of engagement. In his opinion, the adoption of digitisation is much faster in these areas, with better results in the least amount of time. Hence supply chain, finance, and HR tend to become the target for intelligent automation.
“Change is painful,” reasoned Pandya. “Digitalisation is painful for the people going through it but if you see the results, then you want to be part of that process.”
Bringing in experience from his past assignment in the airports sector, Hemal Shah, Head-IT, Aristo Pharma reminded how the Covid pandemic forced all sectors to accelerate their digital journeys.
“Companies don't have any opportunity if they are not automating, learning or adapting,” concluded Shah.
Covid pandemic forced all sectors to accelerate their digital journeys. Companies don't have any opportunity if they are not automating,learning or adapting
Hemal
ShahHead-IT, Aristo Pharma
Finance function has to deal with millions of complex transactions like pricing validation of returned goods in strategic markets like the US.By deploying analytical tools we could derive meaningful insights,playing a very significant role in the decision-making process
Finance: Speaking about how analytics can help derive value out of digitisation Lalit Kumar Singal, CFO, Macleods Pharmaceuticals recounted the finance function has to deal with millions of complex transactions like pricing validation of returned goods in strategic markets like the US. “By deploying analytical tools we could derive meaningful insights, playing a very significant role in the decision-making process,” explained Singal.
Areas of concern
Lalit
Kumar Singal CFO, Macleods PharmaceuticalsData Security: Commenting on the multiple ways life sciences companies can leverage data to not only come up with new drugs, but also different dosage forms, delivery mechanisms, and which ends up in delivering patient outcomes, Ghosh cautioned that “pharma companies have to invest a lot more in securitising the data.” Shah of Aristo Pharma agreed, commenting that “unless we adopt secure ecosystems, it'll be very difficult for us to take the automation journey forward.”
Training: Pandya of Piramal Enterprises raised another concern saying, “As much as
technology interventions are required, I think there are more process and people interventions required. So a lot of chain management and capability building is where invest-
ments are being made…The weakest link continues to remain the people. Unless and until you are training your people well enough, then the technological investments in these
areas will start showing the benefits.”
Reinventing the pharma supply chain: With many challenges and changes in the Indian pharma sector over the
past few years, Rahul Altekar, Director, Supply Chain Solutions, SAP asked supply chain chiefs how they are coping with the complexities and trends impacting the pharma supply
chain, given that each company had to contend with both domestic and international markets, as well as the differences between branded generics and generics OTC etc.
Sun Pharma explained that from a supply chain perspective, demand planning is easier in the Indian market due to its streamlined nature, while the US market poses different challenges. Advancements in technology have made the lives of supply chain professionals easier, with tools like artificial intelligence assisting in demand forecasting and inventory allocation.
While acknowledging that the pharma industry has been a late adopter of technology, he noted that regulators and other extraneous factors make technology adoption slower. Even so, Rao said that “in the past three years, there has been an increased eagerness to adopt technology in non-core areas, such as finance and support functions.”
Given the challenges of processes like continuous manufacturing in the pharma industry, he emphasised the importance of utilising these advancements to improve efficiency.
Changing customer demands: Altekar drew attention to the changing profile of pharma customers, and asked leaders how they are dealing with the customer demands pressurising the supply chain.
Confirming this trend, Prakash Gupta, President, Global Supply Chain, Wockhardt said, “We learn a lot from the consumer.” He narrated how patients/consumers are today more informed, opinionated, and digitally inclined. They expect teleconsultations, digital prescriptions, home deliveries within hours, and lower costs.
To address these demands, Gupta said the supply chain department needs to adopt online deliveries, engage with doctors and patients through influencers, and expand distribution to midtowns and rural areas.
In this section, the speaker discusses the changing landscape of the pharma industry, highlighting the shift towards online distribution and faster delivery times.
Altekar compared the
Security is a key concern as applications move to the cloud. Investments in secure environments and disaster recovery management infrastructure is pivotal
Aligning procurement policies with vendor qualityand performance is crucial
Training and capabilitybuilding for employees are vital alongside technology interventions
AI and machine learning,is helping with demand forecasting,inventoryallocation,and overall supplychain management
The SoPs in pharma need reinvention with digital tools to optimise cost and efforts
Life sciences industrymust benchmarkagainst other industries and adopt best practices for digital transformation
Regulatorypressures and compliance requirements are impacting technologyadoption
pharma industry to a quickservice restaurant, where customers expect to receive their orders in one hour!
Gupta also mentioned the upcoming online trade revolution in India, which he believes will happen within the next five years, rather than 10.
The need for speed: Drawing on his experience across sectors and pharma clients, Ashit Saxena, Partner - PWC highlighted that the pharma industry now has to be faster in everything that they do, whether it is R&D, procurement or supply chain.
Unfortunately, the supply chain as a whole function is viewed as a cost. Thus from a supply chain management perspective, Saxena emphasised the need for faster processes, lower costs, while maintaining high-quality standards and safety. He stressed the importance of doing things better and improving efficiency throughout the supply chain.
Additionally, “while pharma companies need to do things faster, better, cheaper, they also need to think of sustainability within the supply chain,” cautioned Saxena. For instance, he highlighted the need to responsibly dispose of chemicals and packaging materials, while exploring circularity in the supply chain.
Tech beyond IT: Beyond the role of technology, such as AI and machine learning, in improving processes and effi-
ciency, Saxena encouraged pharma companies to understand emerging trends in technology and leverage them to be faster, better, and cheaper. For example, 3D printing spare parts and using variables to contact supervisors in maintenance.
Reducing time to service: Altekar asked how pharma supply chain heads were dealing with another imperative: the importance of reducing time to service. Comparing it to other industries like automotive and consumer and personal consumer packaged goods (CPG) where freezing durations are much shorter.
Wockhardt’s Gupta narrated how they have managed the challenges of demand forecasting and production in the pharma industry and succeeded in reducing the production cycle from 30 days to seven days, by implementing changes such as multi-sourcing and collaboration with suppliers to increase flexibility.
He also highlighted the importance of communication and interaction between the business teams and manufacturing teams to adjust production based on real-time demand. Summing up, Gupta said they are making efforts to improve agility and inventory management to meet customer expectations for timely deliveries.
Saxena described the efforts made by a pharma client to build a supply chain control tower to improve visibility and
real-time decision-making, which resulted in agility and reduction in production frozen time.
Throwing up cross-industry examples, Saxena suggested that the pharma industry should benchmark itself against other industries and adopt practices from them. While he acknowledged that regulatory pressures may sometimes contribute to inefficiencies within the sector, he specifically mentioned the example of aviation where engine failure during flight is not acceptable, drawing a parallel to critical machines in API plants.
Similarly, Saxena narrated how the pharma sector could look to the consumer goods industry, to improve its supply chain. He mentioned the concept of just-in-time (JIT) inventory, visibility with suppliers and customers, and better forecasting.
He also emphasised the need for understanding the cost of machine stoppages and the potential for supplier consolidation and highlighted the importance of continuously improving and looking outwards for inspiration to become a more efficient and effective industry.
Altekar summed up, emphasising the importance of locating flexibilities and exploiting them while respecting rigidities and compliances to become more like a consumer packaged goods (CPG) company.
Sun Pharma’s Rao believes that it is now time to reinvent the Sales and Operations Planning (S&OP) process in the pharma industry. He explained that in the past, inefficiencies were tolerated because the industry was profitable, but now with shrinking margins and increased customer demands, there is a need for greater efficiency.
He suggested that digital tools can play a crucial role in digitising the process and creating a business case to demonstrate the value they can bring. He emphasised the importance of making a hard pitch and showing how these tools can save both effort and money. Additionally, he mentioned that in his company, the responsibility for the S&OP meetings lies with a neutral department called the strategy and analytics cell, highlighting the need for an independent view on demand and supply balancing.
Discussing the importance of the S&OP, he stated that it should be an independent entity under the MD's or CEO's office. Noting that in India, the focus is mainly on demand and supply balancing, and topics like analytics and return goods are not widely discussed, Rao emphasised the need for the Indian pharma sector to have the right mindset and culture to adopt S&OP and create effective organisations.
To sum up, current digital transformation trends in the pharma industry span the increasing role of process automation in improving manufacturing efficiency, digitalisation's impact on field force engagement, and the importance of vendor management and supply chain planning.
There is also a need for selfreflection and honesty in assessing technology adoption. There also needs to be an emphasis on the importance of people and process changes alongside technology in driving better predictability and delivering positive health outcomes for patients.
Nowavailable!
Best-in-classosmolalityperformance, designedwithyouinmind.
HIGHLIGHTEDFEATURES:
Offersthewidestrangeofosmolalitytesting(0–4000mOsm/kgH2O)
Supports21CFRpart11,GMPandEUAnnex11compliance
MeetsPharmacopeiaosmolalitytestingguidelines
3Leveluseraccessandpasswordprotection
Storage:unlimiteddatastorageforaccess
Audittrail:Preserveunlimitedresultsandevents
Databasebackup,protectsyourdatawithautomaticormanualbackup
No.127,BussaUdyogBhavan,TokershiJivrajRoad,SewriWest,Mumbai-400015, Maharashtra,Landline:+91022-24166630Mobile:+919833286615
Sekhar Surabhi,CEO,Caliber Technologies shares the journey of the company as an enterprise software solution provider with a strong focus on the pharma sector.He also speaks on Caliber's commitment to innovation,the impact of their flagship product CaliberLIMS,and the company’s vision for the future of pharma manufacturing,in an interview with Express Pharma
Could you tell us about Caliber Technologies' growth journey?
It has been a remarkable journey of 22 years being a leading enterprise software solution provider to the global regulated industries, including pharma. Over the past two decades, we've been dedicated to pioneering innovation and digital transformation in the industry. Our commitment to delivering cutting-edge software solutions has allowed us to establish a strong presence worldwide, partnering with pharmaceutical companies to enhance their operational efficiency and compliance.
We consider our clients as essential collaborators, and their feedback shapes our solutions. This collaborative approach has kept our product offerings at the forefront of industry needs. Two decades ago, the Indian pharma industry relied heavily on the manual processes and paper documentation. We are proud that through relentless learning and innovation in Quality Management, Manufacturing, Laboratory Solutions, and Data & Insights, we've enabled our customers to ensuring top-quality with our world-class portfolio, with absolutely no paper dependency.
Our global footprint has expanded significantly during this journey. Today, we serve pharmaceutical companies of all sizes, from emerging biotech startups to established MNCs. Our solutions have been deployed in diverse regions, adapting to local regulatory frameworks and unique industry challenges.
Caliber has been at the forefront of innovation for pharma digital transformation. Could you share some examples of how your company is contributing to the industry's growth?
Certainly. Caliber has been a leader in developing solutions that address critical industry needs. For instance, our flagship product, CaliberLIMS, was the first LIMS in India to be built on emerging Web
Technology at that time, which offered phenomenal savings on validation and maintenance, giving the best ROI in the industry. We went on to build India’s first 100% paperless laboratory, almost a decade ago. We did this at a time when most competitors were still offering only partial digitalization on aging technology. Caliber’s growth engine has been innovation and collaboration with our customers.
We were also one of the first companies to offer the revolutionary Anytime PQR. This is our award-winning offering which brings down monthslong effort to just minutes. Our investment in Data Sciences is leading to transformative solutions like ‘Continuous Process Verification’ (CPV) and quality metrics. We are constantly working on new inn ovations. There are a few exciting offerings in the pipeline which we will be announcing soon, which I am confident the industry will see as disruptive and game changing.
Your flagship product, CaliberLIMS, is globally recognized in the industry. How has this system revolutionized laboratory operations, and what benefits has it brought to pharmaceutical quality?
CaliberLIMS has been a game changer for our customers’ laboratory operations. Being the first in the industry to implement 100% paperless lab solution, it makes me proud to offer a robust, comprehensive LIMS which is helping the industry be future-ready. It is
also the first LIMS in the world to offer a QR-code enabled glassware management module. CaliberLIMS is well appreciated for its wide functional coverage and depth through comprehensiveness. CaliberLIMS has 16+ modules and each module has been carefully designed to help users get the best value from it. Still, we continue to learn every day to make the product more powerful to ensure the success and future-readiness of our customers. I am also excited to release the next version of CaliberLIMS soon, which is designed to be scalable and adaptable to evolving technological needs, meeting future needs of industry from a regulatory perspective and efficiency perspective.
Let’s talk about the industry’s needs. Regulatory environments can vary greatly across different countries. How does Caliber help companies navigate the complexities of changing global regulatory requirements?
This is an exciting subject for me! Navigating global regulatory frameworks is indeed complex, but it's a challenge we've embraced. We are ahead of the game when it comes to foreseeing the regulatory needs that the industry is facing.
We have our eyes on the regulatory developments, and we are proactively building up ourselves to help our customers address them. For example, Anytime PQR is a system that came from Caliber first. We are also now offering a
robust tool for continued process verification. We also have another robust system which will be released soon that I am sure will be well received by our customers, it addresses some crucial upcoming regulatory needs.
Not just in our products, but even in implementation approach, we are ensuring to stay ahead. We have been at the forefront of adopting the CSA (Computer System Assurance) approach for all our implementations. Thanks to the upcoming regulatory changes, this is speeding up the time to go live for our customers.
As a part of my commitment to giving back to the pharma community I serve as board member on ISPE, which gives me opportunity to share our knowledge as well learn from the industry thought leaders.
How do you envision the future of pharmaceutical manufacturing, considering aspects like data analytics and real-time quality monitoring?
The future of pharmaceutical manufacturing is exciting and dynamic. Data analytics and real-time quality monitoring will play a pivotal role, and of course, so will AI & ML. However, all of this is possible only with a strong source data. Only when every data point is digitalized using the right systems and tools, can such data be
used for analytics, predictions, and further inn ovations. This is where IQM – Integrated Quality Management – comes in. This has been our big vision all along. I anticipate increased reliance on data-driven decision-making, predictive analytics, and real-time monitoring for pharma manufacturing. We ensure to build this into every product individually, and our entire product suite.
Our CaliberBRM (Batch Record Management) software, for example, tracks every step of the manufacturing process in real-time. These systems collect data on process parameters/variables such as temperature, pressure, and chemical compositions during production. In case of any deviations from predefined parameters, alerts are generated, and corrective actions can be taken immediately.
Similarly, EPIQ QMS, our integrated Quality Manage-
ment Software Solution accumulates a vast dataset of historical production information. This data can be used for predictive analytics. For example, the system might identify that certain deviations in temperature at a particular stage of production are correlated with a higher likelihood of impurities in the final product. Armed with this insight, the manufacturing team can proactively adjust the process parameters to prevent such deviations.
When you put this together, identify and monitor “Critical Quality Attributes” “Critical Material attributes” and “Critical Process attributes”, and customers are empowered to build analytics and predictive analytics with data coming from these robust systems. This foundation is crucial to build consistent quality and reducing wastage. The future of pharmaceutical manufactur-
ing is shaped by data analytics and real-time quality monitoring and Caliber is at the forefront of it.
Looking ahead to the next decade, what disruptive technologies or shifts do you anticipate will have the most profound impact on the global pharmaceutical landscape, and how is Caliber positioned to capitalize on these changes?
Healthcare is becoming a priority across the globe, one of the biggest challenges going forward would be manufacturing high quality medicines at low cost without interruption to the supply chain. Of course, technologies like AI, blockchain, and advanced analytics will significantly impact the pharmaceutical landscape to make the quality consistent and operations efficient. But, as I said earlier, the foundation should be laid first, and it needs to be done right now. Caliber is well-positioned to
capitalize on these changes by continuing to develop solutions that harness the power of these technologies to improve efficiency, compliance, and patient outcomes. As a company, we are always game for sharing our knowledge and helping the industry in their digitalization process.
As the CEO of Caliber Technologies, what strategies do you believe are crucial for fostering a culture of continuous learning, adaptability, and innovation within your organization?
For us, inn ovation is at the heart of everything. Innovation happens when people feel comfortable making mistakes and learning from them. That is the culture I am focused on nurturing. Fostering a culture of continuous learning and innovation is paramount. We encourage our teams to embrace change, seek out new knowledge, and collaborate openly. We promote cross-functional collaboration with our Work Together, Win Together (WTWT) initiatives, and celebrate innovative thinking. By staying agile and open to new ideas, we can drive positive change both within our organization and for our clients in the pharmaceutical industry. I personally spend significant amount of time with my innovation team, to constantly look into what would help the industry to deliver safer medicines.
The future of pharma manufacturing is exciting and dynamic.Data analytics and real-time quality monitoring will play a pivotal role,and of course,so will AI and ML.However,all of this is possible only with a strong source data.Only when every data point is digitalised using the right systems and tools,can such data be used for analytics, predictions,and further innovations
PROSOLV® SMCC makes it possible to manufacture multi unit particulate systems (MUPS) like products with ease.It is a problem solver,whenever tablets with good hardness need to be manufactured at lower compression force for compression sensitive products
The hardness of pharmaceutical products carries significant information about the characteristics of ingredients and processing conditions during manufacturing, which may be critical in discriminating pharmaceutical products. Most of pharmaceutical tablets are made by compaction of powder blends using a rotary tablet press. For a given blend, the hardness strongly depends on tablet porosity after the compaction process. This porosity is inversely proportional to the maximum applied force. As seen in Figure 1, the hardnessporosity relation is highly nonlinear and it is well described by an exponential law1
are comparable cellulose polymers of similar molecular weights, polydispersity, particle size, porosity, and crystallinity, the principal difference being a changed
develop between MCC & SIO2 during PROSOLV® SMCC manufacturing. Silicon dioxide simply adheres to the surface of microcrystalline cellulose. Single particles or small agglomerates of silicon dioxide
particles in the initial stage of densification. Increased strength of tablets is most probably a consequence of intersurface interactions of SiO2 and MCC. Silicification improves flowability, lubricity,
3) The size and weight of individual tablets are decreased, which increases patients’ compliance.2
PROSOLV® SMCC possesses further advantages such as decreasing the
Also, analysis of hardness data can provide information about other process parameters and components such as wet and dry granulation conditions, particle size distribution, type of equipment, speed of compaction and pre-compaction forces among others.
Correlation of PROSOLV® SMCC with MCC
PROSOLV® SMCC and MCC
(more rough) topography of the surface of MCC particles.
The specific surface of PROSOLV® SMCC is as much as five times larger due to the higher specific surface area of adsorbed colloidal silicon dioxide.
No new covalent bonds
are uniformly distributed on the whole surface of MCC (particle size of silicon dioxide ranges about 15 nm). This high de -agglomeration of silicon dioxide contrasts with a dry physical mixture of MCC with silicon dioxide, which contains large agglomerates of silicon dioxide. Silicon dioxide slightly facilitates the transport of
and compactability. The tensile strength of compacts of PROSOLV® SMCC is greater than of the respective MCC.
Tablets manufactured from PROSOLV® SMCC
1) Exhibit higher tablet hardness at lower compression force
2) Are relatively easier to coat
hygroscopicity of the active ingredient leading to increased stability of tablets. Due to a decreased size, higher compressibility, and better flow properties make the blend less sensitive to the rate of tableting; a higher output of tablets in one batch can be achieved, which makes their manufacture substantially cheaper. The
in which optimal compaction and decent floware required
PROSOLV® SMCC 90 Formulas in which a balance of flowand compaction are required
PROSOLV® SMCC HD 90
PROSOLV® SMCC 90 LM
toughness and ductility of compacts of PROSOLV® SMCC are greater than those for MCC: the toughness is approximately 60% greater in compacts of PROSOLV® SMCC than MCC, which represents a considerable increase in the binding capability of PROSOLV® SMCC and which may be reflected by a larger “carrying capacity” for this material. In contrast to routinely used PROSOLV® SMCC,
Formulas in which optimal flowand consolidation are required.This grade shows the best disintegration time
Equivalent to PROSOLV® SMCC 90 with lower moisture content (<3%)
the high-density grades like PROSOLV® SMCC HD 90 shows further improvement in flow properties and lesser sensitivity to the rate of tableting.2
PROSOLV® in hardness improvement
Tablets are generally produced by in die compaction, which consists of filling a die with granules, compression between two rigid punches and ejection
from the die. The strength of the tablets is dependent on the state of densification of the powder, which is given by the applied force. Hardness of tablet is a measure of the breaking force or mechanical integrity of tablets.3
Case study
PROSOLV® SMCC: High Dose, Low Bulk Density Active Case Study
The drug in study was having a high dose requiring high dose loading. The low bulk density of drug resulted poor flow and low compactability. This resulted in extremely soft and fragile tablets with over 30 % breakage during the coating process.
PROSOLV® SMCC is 30–50% percent more compactible than MCC (Fig 3). Therefore, the same hardness
as observed with MCC tablets can be achieved with less compaction force. This results in more porous tablets which enables faster disintegration and more complete drug dissolution.
PROSOLV® SMCC makes it possible to manufacture MUPS (multi unit particulate sytems) like products with ease. It provides required cushioning effect and protects the pellets from getting ruptured. To sum up PROSOLV® SMCC grades are problem solver, whenever tablets with good hardness needs to be manufactured at lower compression force for compression sensitive products.
1) Alberto Cuitiño. Acumen Biopharma. Hardness Testing of Pharmaceutical Tablets
2) Jitka, M, Petra N, (2007) A study of compacts of the properties of compacts from Silicified Microcrystalline celluloses Drug Development and Industrial Pharmacy, 33:775–781
3) https://www.jrspharma.com /pharma_en/products/excipients/prosolv®-smcc.php
Pharma India
Email id: Suyesh.kale@ jrsindia.com
Abstract
Continuous wet granulation and drying have long been a hot topic in pharmaceutical research and development (R&D) and industry. However, there is no truly continuous fluid-bed dryer on the market that is suitable for a long process time and that meets the quality requirements described in the present article. This article outlines the experimental testing on a new R&D system (QbCon®1) for truly continuous granulation and drying. Special attention is paid to the dryer and the resulting granules.
The results show that very narrow and reproducible residence time distributions are achieved in the dryer, which leads to uniform drying of the granules of different size classes. The process delivers consistent quality regarding moisture and particle size of the granules over several hours. When changing the conveying speed of the granules in the dryer while maintaining all other parameters, it was possible to describe the limits for a fixed process/formulation combination, which depends mainly on the depth of the fluid bed.
The possibility to follow the process in-line, makes the QbCon®1, with its innovative drying process, an ideal device for the introduction of continuous wet granulation.
Introduction
The FDA Guidance on Process Analytical Technologies (PAT) and the ICH Guidelines on pharmaceutical development, quality-related risk management and quality systems have given the concept of continuous pharmaceutical manufacturing a major boost. The pharmaceutical industry expects many advantages from the implementation of continuous manufacturing processes. The possibility to monitor a production process more
closely by means of PAT and thereby constantly produce high quality products is the key aspect of these ideas and entails many other advantages such as higher patient safety, lower costs, better process understanding and enhanced process control, to name but a few. It is intrinsic to continuous processes that, to a certain extent, they require only longer production times instead of a scale-up, but since all developments start in the laboratory, there is a need for space-saving equipment in laboratory size, which is also suitable for the smallest
throughputs.
Granulation and granule drying also play a major role in continuous manufacturing, since the reasons for granulation (improved flowability, prevention of segregation, dust reduction, etc.) are not necessarily eliminated by continuous manufacturing. However, there is currently no continuous dryer on the market that can meet the quality requirements of pharmaceutical production. First of all, a short residence time of the granules in the dryer with a narrow residence time distribution is essential to be able to remove
defective products in a targeted manner without having to discard a large portion of the batch, which would be the case with a high degree of back-mixing. Furthermore, narrow residence time distributions simplify the traceability of material in the continuous process, making it easier and less complex to trace finished tablets back to the raw materials or to subsequently trace raw materials to the finished tablet. Further important quality requirements for a dryer are even, reproducible drying of all granules – especially of different sizes – over the entire process duration, a small process chamber to keep the volume in the drying process as low as possible and, in particular, a long service life of the exhaust air filters without having to interrupt the drying process or even replace the filters.
There are several semicontinuous or quasi-continuous dryers (with several drying chambers working in parallel) for granules on the market, but none of them meets all the quality requirements mentioned above. In addition, semi-continuous dryers cannot deliver the promised benefit of reducing waste products that do not meet specifications to the extent of a fully continuous dryer. Due to the high volume of material that remains in different chambers of the semi-continuous drying process, it is not possible to discard specific partial quantities. On the contrary, entire partial batches must be discarded in case of doubt due to the high degree of (back-)mixing.
Materials
A powder mixture (proportions: 80/17/3) consisting of alactose monohydrate (Granulac 200, Meggle, Wasserburg, Germany), microcrystalline cellulose (Avicel PH 101, FMC
BioPolymer, Philadelphia, PA, USA) and povidone (Kollidon 30, BASF, Ludwigshafen, Germany) was used for granulation. Purified water was used as granulation liquid.
The blue, water-soluble dye FD&C Blue No.1 (BASF) was used to assess the residence time distribution of the granules in the dryer.
Manufacture of the granules / System description QbCon® 1 The three powders were mixed in a laboratory mixer (LM 40, L. B. Bohle, Germany) at a speed of 15 rpm. Granules were produced in a fully continuous process.
QbCon® 1 (Figure 1) is a system with fully-integrated software and unit operations consisting of different components by L. B. Bohle (liquid feeding, wet granulation, drying, automatization) and Gericke (powder feeding).
Feeding of powder and liquid, wet granulation and drying are possible in one fully continuous process step without interruptions. The entire process is controlled and monitored via a touch panel. The nominal throughput of the system is 0.5-2.5 kg/h, but can significantly deviate upwards, for example if high-density material is used, the moisture required for granulation is low or the desired residual moisture is in a higher range. In the present tests, the powder mixture described above was filled into the gravimetric powder feeder (GZD150.12 special, Gericke, Switzerland) and dosed at a rate of 1 kg/h into the first zone of the QbCon® 1 twin-screw granulator. The granulation liquid was fed into the second zone of the granulator via a high-pressure pump using a nozzle with an internal diameter of 0.25 mm. The liquid feed rate was controlled by a Coriolis flow meter at 4 g/min resulting in a granule moisture content of 24 %. In a twin-screw granulation
process powder and liquid are continuously fed onto two corotating screws. Both components are continuously conveyed, mixed and sheared to produce granules that leave the granulator at the end. For an example and overview of the granulator process zone, please see Fig. 2. The twin screw granulator of the QbCon® 1, whose screws have a diameter of 25 mm and a length of 20 x diameter, was operated at a screw speed of 50 1/min. The screw configuration consisted for the most part of double flighted conveying elements. After the liquid feeding, a kneading element consisting of five individual discs with an offset angle of 45° was used, which supports the even distribution of liquid in the granules. The kneading element was 25mm long. Shortly before the outlet, another kneading zone with the same length and the same offset angle was inserted.
Wet granules leave the twin-screw granulator and land on the distributor plate of the continuous dryer via a direct connection, where they are immediately subjected to hot air and conveyed in the direction of the outlet by a vibration excitation. Fluidisation of the granules through the air and vibration is extremely low, just enough for horizontal conveying. The supply air temperature and the supply air volume during the tests was 80 °C and 20 Nm3/h respectively.
The conveying of the granules and the air flow are independently adjustable, so that the drying effect of the granules can be controlled via the air flow, the supply air temperature and the conveying speed. The filter surface for the exhaust air is permanently kept free by means of a cleaning process that is based on a new principle. Thus, for the first time, a continuous granulation without interrupting the process is possible. The dry granules leave the QbCon® 1 via a pneumatically operated valve and can be further analysed and processed. A prepared mechanical interface for a NIR probe or any other similar probe also allows in-
line quality determination and thus control of the process based on quality (e.g. moisture, active ingredient content or product temperature) of the granules.
The residual moisture of the granules was determined based on the loss on drying of the collected samples (approx.
3 g). For this purpose, an ana-
lytical moisture analyser (HR73 Halogen Moisture Analyzer, Mettler Toledo, Columbus, Ohio, USA) was used at a drying temperature of 105 °C. The abort criterion was a mass loss of < 1 mg within 60 seconds. The analyses were performed in triplicate foreach sample.
During one test, the dry granules were divided into four size classes using test
sieves of sizes 1.4 mm, 1.0 mm and 0.5 mm in order to test the uniformity of drying within the various sieve fractions.
Granule size distribution
A photo-optical analyser (CPA 2-1, Haver und Boecker, Germany) was used to investigate the granule size distribution. A sample of dried granules collected over ten seconds was fed into the measuring zone via an automatically controlled vibrating feeder, in which a line scan camera determines the granule size and automatically transmits it to the connected software for processing. For the evaluation the 10%, 50% and 90% size quantiles of the Q3 distribution were used.
Residence time distributions
The residence time distribution of the granules in the continuous dryer was measured using ExtruVis 3 (ExtruVis, Germany). The device consists of an industrial camera, a ring light for constant illumination of the room to be recorded and a special software for evaluating the data. During the process, a pulse of moist granules that had previously been dyed with a blue dye was manually fed into the inlet of the continuous dryer. The coloured granules moved together with the white granules towards the outlet. The ExtruVis camera was placed directly in front of the outlet to record the distribution of the coloured granules within the white granules. The connected software calculates a density distribution of the residence time as a function of time (E (t)) based on the colour intensity at the outlet. A detailed. A measuring frequency of approx. 20 images per second allowed a reliable in-line determination of the residence time distribution in the dryer. The mean residence time of the granules in the dryer is calculated by halving the area under the residence time curve.
The main focus of this study is on the drying process of QbCon®1. Initially, a long-term
test was carried out using the process data described above, in which samples were taken at regular intervals over a period of 2.5 hours, which were examined under various quality aspects.
Thereafter, the drying conditions were varied by changing the conveying speed of the granules in the dryer while maintaining all other process and formulation parameters. The purpose was to investigate the process limits of the dryer for the underlying conditions depending on the residence time.
It was generally observed that the continuous granulation and drying tests could be carried out without interrupting or disturbing the process. The critical process parameters of feeding, granulation and drying were consistent over the entire test period. Particularly noticeable was that the exhaust filters were covered with only a small portion of the fines content of the granules. This low coverage can be explained by the extremely low fluidisation of the granules in the dryer. Therefore, the cleaning interval of the product filters has been reduced to 20 minutes. The filters could be cleaned completely without any product residues during cleaning.
Residual moisture is a critical quality attribute for dried granules. Highly fluctuating values and too high residual moisture contents can lead to irregularities in downstream processes, e.g. smearing of sieve surfaces, variations in tablet content or difficulties with the continuous feeding of granules. The residual moisture of the produced granules after continuous drying over a test period of 2.5 hours is shown in Fig. 3. The raw material had an initial moisture content of 1.28%. The residual moisture of the granules fluctuated between 1.02% and 1.38% during the test and averaged 1.21 ± 0.11%. This scattering around the mean value is acceptable for residual moisture measurement by means of LOD and can be regarded as
very low. With regard to the moisture content of the dried granules, a consistent and reproducible result could be obtained, which is of utmost importance for a continuous process. The drying was so effective and efficient that some of the granules showed a moisture content which was below that of the raw material. This can be of great importance for moisture-sensitive products. If the residual moisture is considered too low, it is possible to adapt the process to shorter drying times (= residence times), lower temperatures and air flow rates in order to achieve higher residual moisture contents.
In addition to residual moisture, a consistent granule size distribution is important for further processing of the granules. The 10, 50 and 90% quantiles of the granule size distributions are shown in Fig. 4. Again, the continuous granulation and drying process leads to consistent granule sizes, which is mainly due to the low fluctuations in the 10% quantile (mean value: 298 μm) and in the median granule size (mean value: 726 μm). Fluctuations in the 90% quantile are typical for twin-screw granulation and are the highest in absolute terms within these tests, but really the smallest with a relative standard deviation of 6%. Thus, the fluctuations in the 90% quantile (mean value: 1805 μ m) are acceptable. In addition, the oversized granules are usually classified after the drying step in order to obtain a nar rower size distribution.
The residence time of the granules in the dryer defines the time in which the moist granules are exposed to the drying air flow. A constant residence time distribution is therefore of utmost importance for consistent drying results. Even though residual moisture and granule sizes indicate a constant residence time, a detailed investigation of the residence time behaviour in the continuous dryer is of great interest, both for upscaling to larger systems and for discharge concepts for faulty material in fully continu-
ous processes. Therefore, the distribution of the residence time of the granules in the dryer at the beginning, middle and end of the endurance test is shown in Fig. 5. It is not surprising that the curves are almost congruent, as the results discussed above have already indicated this. The mean resi-
dence time for the three tests was 57, 61 and 63 seconds, which is very short for continuous drying. The fact that such low residual moisture is still maintained, demonstrates the effective flow of the drying air through the granules. Not only the mean residence time, but also the width of the residence
time distribution is an important parameter that characterizes the conveying and blending behaviour of a system. The small width of the measured distributions is ideal for a continuous dryer. The aim must be to move all granules through the dryer at the same speed in order to achieve a similar drying performance. Wide residence time distributions can lead to different moisture content within a sample. The curves are almost axis-symmetrical, which indicates very low backmixing in the dryer.
Due to these considerations, the uniformity of the drying process within a sample must be tested. Optically, the observations did not reveal any differences between the conveying speed of coarse and fine particles. Fig. 6 shows the residual moisture of granules of different sizes from the same sample, which show only very small differences. Only the granules of the largest fraction have a slightly higher moisture content, which is common with fluid-bed drying and is of no greater significance within the scope shown here.
In order to further characterize the QbCon® 1 and to test the limits for the present formulation and throughput, the conveying speed of the granules was increased or decreased by adjusting the vibration feeder. This results in different granule bed heights in the dryer and residence time distributions varying in length and width, which are shown in Fig. 7. The mean residence times vary between 49 and 229 seconds and the curves show a high degree of symmetry. The residence time distribution with the longest mean residence time is particularly striking. The long-time interval between the first and last occurrence of coloured granules in the residence time experiment suggests that the granules of a sample are unlikely to become uniformly dry. This is illustrated by Fig. 8, where the residual moisture of the granules is displayed as a function of the mean residence time. With the mean residence time increasing from 49 to 148
seconds, the residual moisture of the granules drops from 1.37 to 0.65%. However, if the mean residence time is increased to 229 seconds and the residence time curve is widened at the same time, the residual moisture will increase again. In addition, the values scatter very widely with a relative standard deviation of > 41%. If the residence time is too long, the bed thickness of the granules in the dryer increases, resulting in a poorer and less even flow through the granules. These two influencing parameters are of utmost importance when designing the desired process.
A new system for the continuous production and drying of granules on a laboratory scale was experimentally investigated. The present tests have shown the great potential of this novel drying process which uses a fluid bed. Thanks to a very short residence time and a narrow residence time distribution, constant, continuous drying of the granules was achieved even among the different size classes, and the particle size distributions were also constant over the process time. Such results are so far unique in the field of continuous wet granulation and demonstrate the superiority of the present system over known processes. On the basis of different conveying speeds of the granules in the dryer, it was possible to determine the process limits for a given formulation and a given throughput – simply based on the residence times and residual moisture content. The height of the granule bed proved to be a critical parameter to be controlled. The possibility to follow the process in-line, makes the QbCon®1, with its innovative drying process, an ideal device for the introduction of continuous wet granulation within companies.
Due to the crucial necessity and its direct impact on human health and welfare, pharma is probably the most important and critical sector among others. As a consequence of which, it becomes essential to store pharmaceuticals, vaccines, laboratory samples or units of blood at the right temperatures to ensure that they remain effective and that quality is maintained. Another reason for the pharma division to ensure safety measures & controlled environment is stringent regulations and inspection of the facilities. This elementary need for climate control can only be ensured with right data monitoring systems. Testo being a market leader in testing & measurement sector provides the best in class data loggers and data monitoring systems for the pharma division.
Pharma goods must be stored well in every situation as any deviation in the ambient temperature or humidity values may lead to deteriorated quality of the product. Testodata loggers can be used to test the optimum conditions for specific products or surroundings. Temperature & humidity data loggers are often used in pharma industries to monitor the conditions in which drugs, medicines, vaccines are kept. Not only storage, but during the transit of goods, testo transport data loggers are useful to measure the transport conditions. The range of data loggers is very extensive. A temperature & humidity logger such as 174 T guarantees continuous monitoring in a storage or warehouse. Also, data loggers with multi channels for connecting external sensors & thermocouples, like testo 176 are available for ensuring secured work process in labs.
These data loggers are also critical for production quality assurance where the temperature
has to be frequently checked at various points in production processes. Using thermocouple probes, data loggers can also
record data in the kinds of extreme temperature ranges. The probe's fast response also contributes in the validation
processes and quality standard optimisation in QA units & clean room applications. These instruments are the most convenient and pocket friendly solution for all pharma application areas.
The testo Saveris 2 WiFi data logger system is the simple, flexible and reliable solution to humidity and temperature monitoring in cold storage area like blood banks. This innovative monitoring system is ideal for high product quality & eliminates manual work of reading out or documenting measurement data. With a secure online storage of all readings in Testo Cloud the data can be managed and analyzed online by the user via smart phone, tablet or PC anywhere and anytime. In case of crises and deviations, it is provided with an alarm by e-mail, or optionally by SMS.
Another important and crucial application of a pharma industry involvesvalidation of sterilisation and freeze-drying processes. Not only that, validating cleaning and disinfecting equipment is equally necessary. In order to allow a seamless operating procedure, the validation process and the documentation work must be as efficient and smooth as possible which could be easily achieved with testo 190 data logger solution that has innovative data loggers for temperature & humidity, smart software and accessories.
Testo offerings are majorly related to the data security along
with comprehensive analysis & evaluation of all the recorded measurement data. Testo data loggers ensure continuous monitoring of temperature and relative humidity of pharma products during production, storage or transit of goods. Real time data monitoring is important for the quality of pharma goods and also enables the supplier to improve the life of the goods. Transportation trucks, warehouses, cold rooms etc. can now be remotely monitored via Testo data loggers & data monitoring systems. Testo's data loggers are EN 12830 and 21 CFR Part 11 compliant which ensure complete documentation of parameters, be it humidity, temperature or absolute pressure. They come with professional software where the data recorded cannot be modified and the audits can be easily complied with.
Testo also has an established state-of-the-art NABL accredited service & calibration LAB in accordance with the standardISO/IEC 17025:2017, that takes care of the after sales support locally from Pune. Testo service & calibration facility is highly cost effective as it delivers international standards very conveniently within a week’s time. Instruments of any brand/make can be calibrated and serviced locally maintaining necessary standards.
The accredited parameters include humidity, pressure, absolute pressure, contact type temperature, non-contact type temperature (Infra Red Thermometer, Thermal Imager). In fact, ours is the first and only lab in India to get NABL Accreditation for dew point temperature as well.
For more details, login to our website www.testo.com or write back to us on info@testo.in
Good Manufacturing Practice guidelines are continuously revised to consider technological changes and current practices in pharmaceutical manufacturing.
Process validation is a key requirement of all regulations.
The weighing experts from METTLER TOLEDO help you design weighing processes, qualify weighing equipment and continuously monitor it to ensure reliable product quality and avoid unpleasant surprises during audits.
Process validation contributes significantly to ensuring drug quality, but it also places a heavy burden on pharmaceutical manufacturers. It requires significant effort and resources that result in additional costs.
Pharma production, and the validation of such a process, is a complex task that needs to consider many aspects, including weighing. Weighing has a significant impact on quality, both in production and in the laboratory. Therefore, weighing equipment must be qualified and critical weighing processes need to be validated.
Weighing occurs at various stages of the pharma manufacturing process. Nowadays, scales are built into complex machinery, such as filling machines or reactors. They also can be connected to human machine interfaces (HMIs) or computers running software
that guides operators through production processes. Initially, scales are used in material receiving to verify incoming or outgoing components and reconcile inventory. Next, scales and balances are found in dispensing areas to weigh components according to predefined formulations. Then, scales are used when checking for com-
pleteness or monitoring production yield. Finally, weight based quality control confirms the weight of tablets using the principle of mass uniformity or vial fill level is qualified using statistical quality control (SQC) software. In quality control labs, balances belong to the most widely used equipment for standard preparation, assays and impurity profiles.
Weighing processes are critical to high-quality products and the performance of the scale is a Critical Process Parameter (CPP).
Process validation contributes significantly to ensuring drug quality. Since Weighing has a significant impact on quality, weighing equipment must be qualified and critical weighing processes need to be validated. METLLER TOLEDO's Good Weighing Practice™ (GWP®) provides outstanding support in three main stages- weighing process validation, equipment qualification & continuous process verification.
About METTLER TOLEDO
METTLER TOLEDO is a
leading global supplier of precision instruments and services. The Company is the world’s largest manufacturer and marketer of weighing instruments for use in laboratory, industrial and food retailing applications. METTLER TOLEDO also holds top-three market positions in several related analytical instruments and is a leading provider of automated chemistry systems used in drug and chemical compound discovery and development. In addition, the company is the world’s largest manufacturer and marketer of metal detection and other end-ofline inspection systems used in production and packaging and holds a leading position in certain process analytics applications. Additional information about METTLER TOLEDO can be found at www.mt.com
For more information
Link: www.mt.com/ GWPVerification
Call us on Toll Free -1800 22 8884 / 1800 10 28460 or Email- sales.sales@mt.com
The weighing experts from METTLER TOLEDO help you design weighing processes,qualify weighing equipment and continuously monitor it to ensure reliable product quality and avoid unpleasant surprises during audits
Designedfornutraceutical& pharmaceuticalapplications