SEPTEMBER 2023,` 40
WhyX-rayinspection is a viable quality assurance solution for pharma products
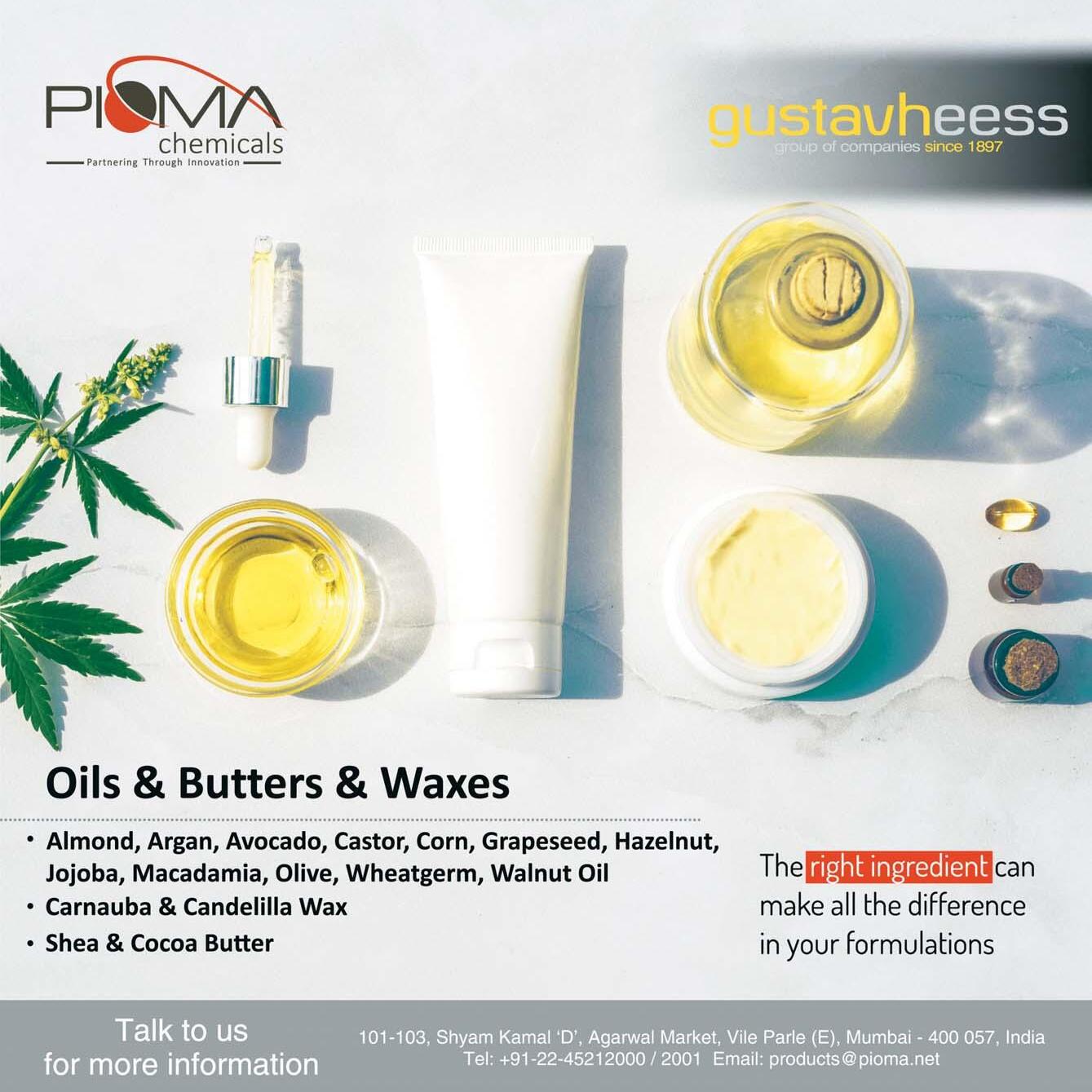
Generative AI with Google Lens to detect counterfeits in pharma
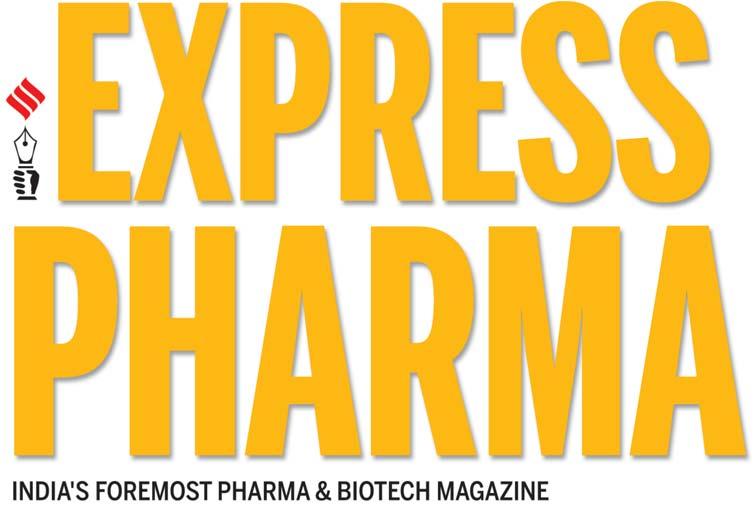
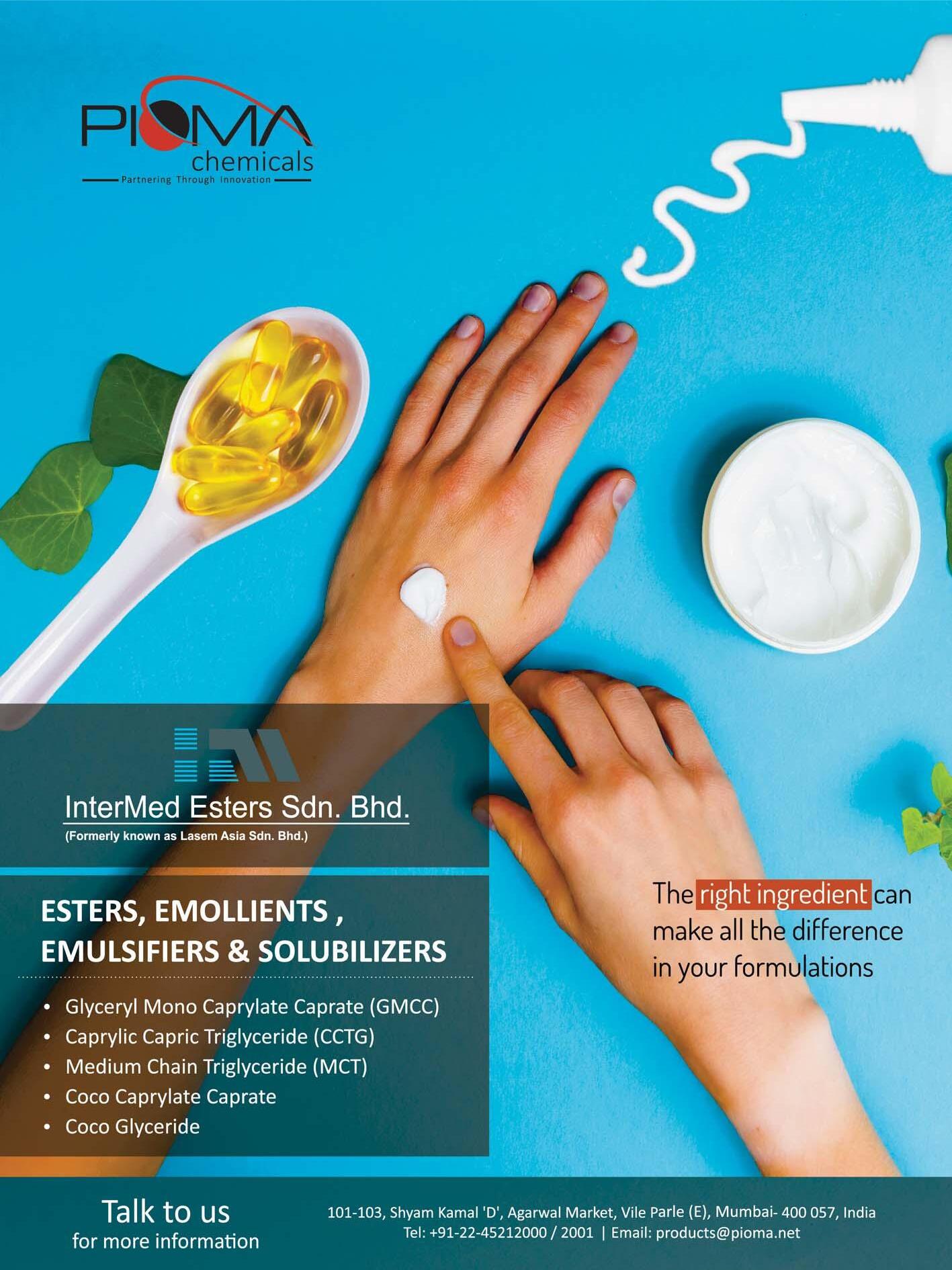
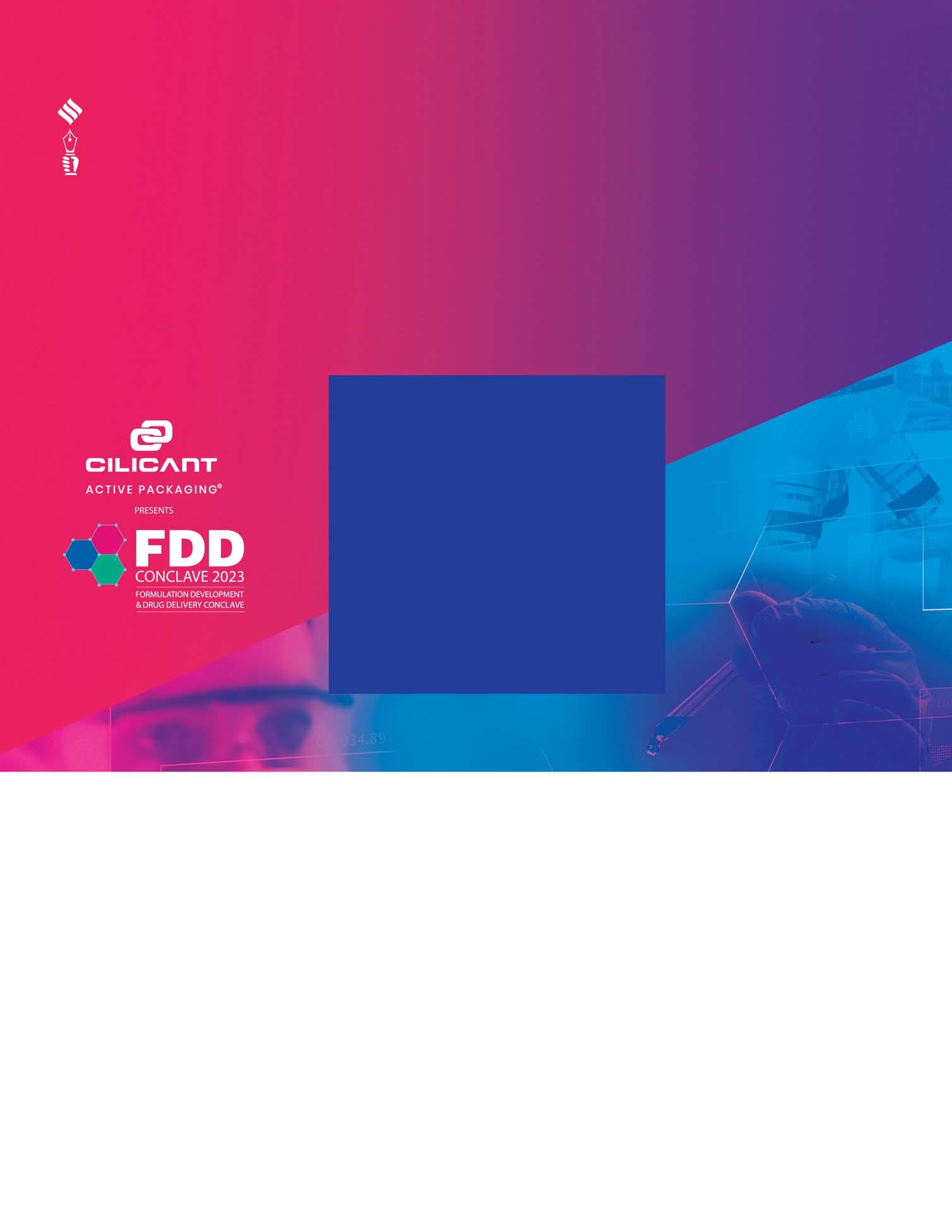



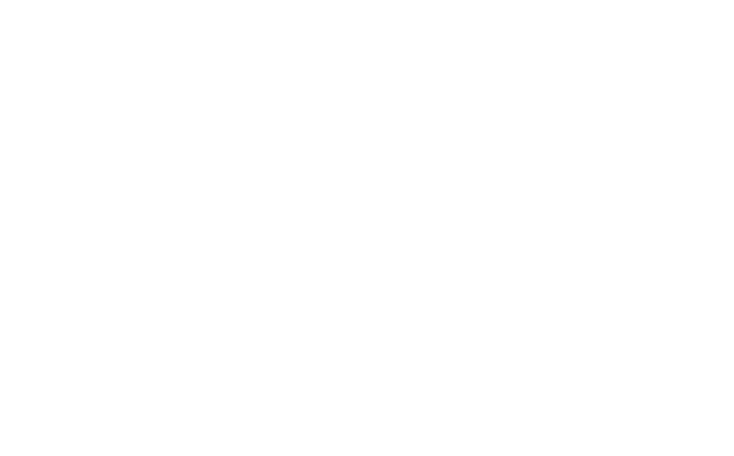
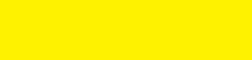

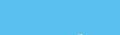


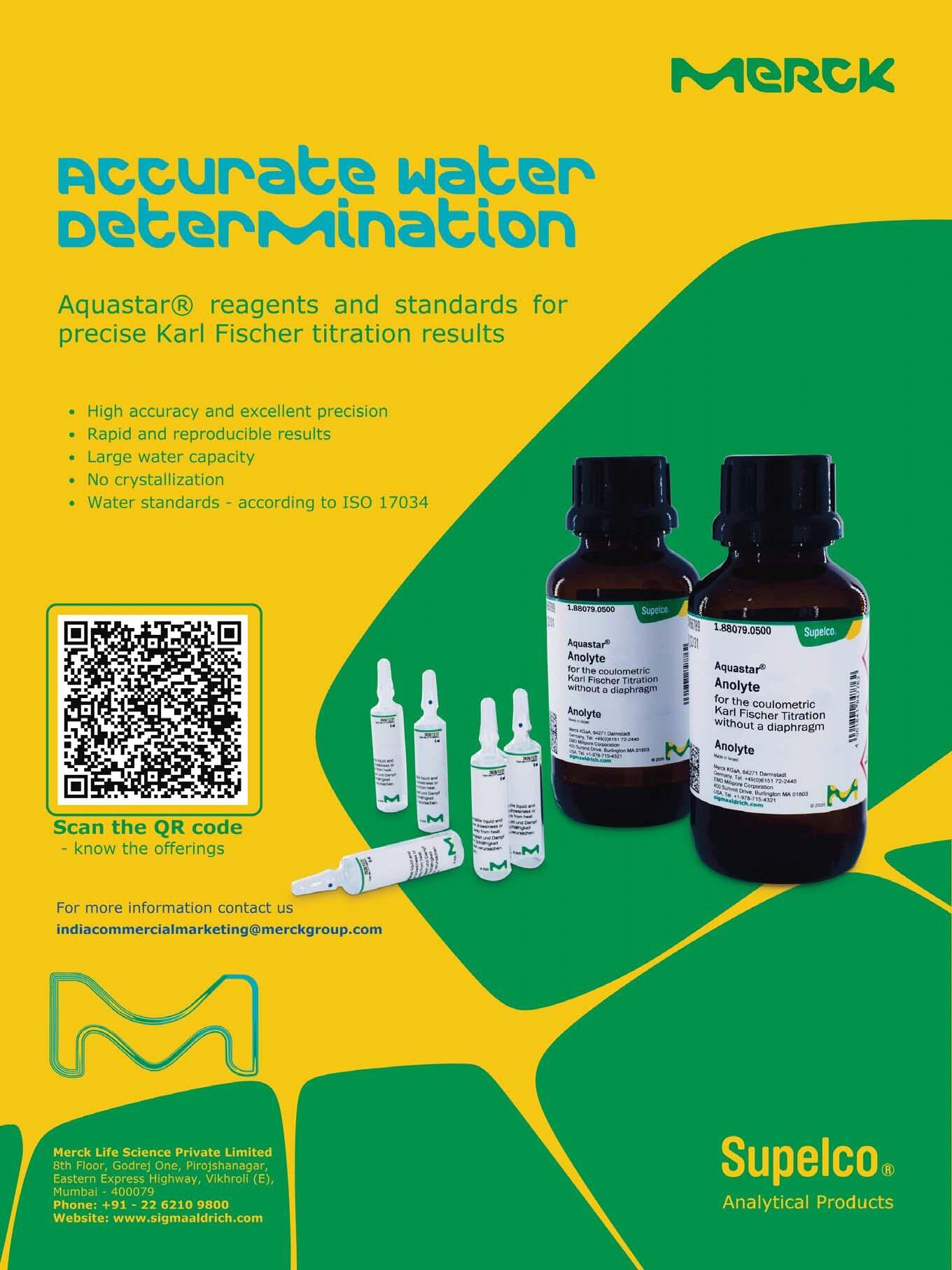
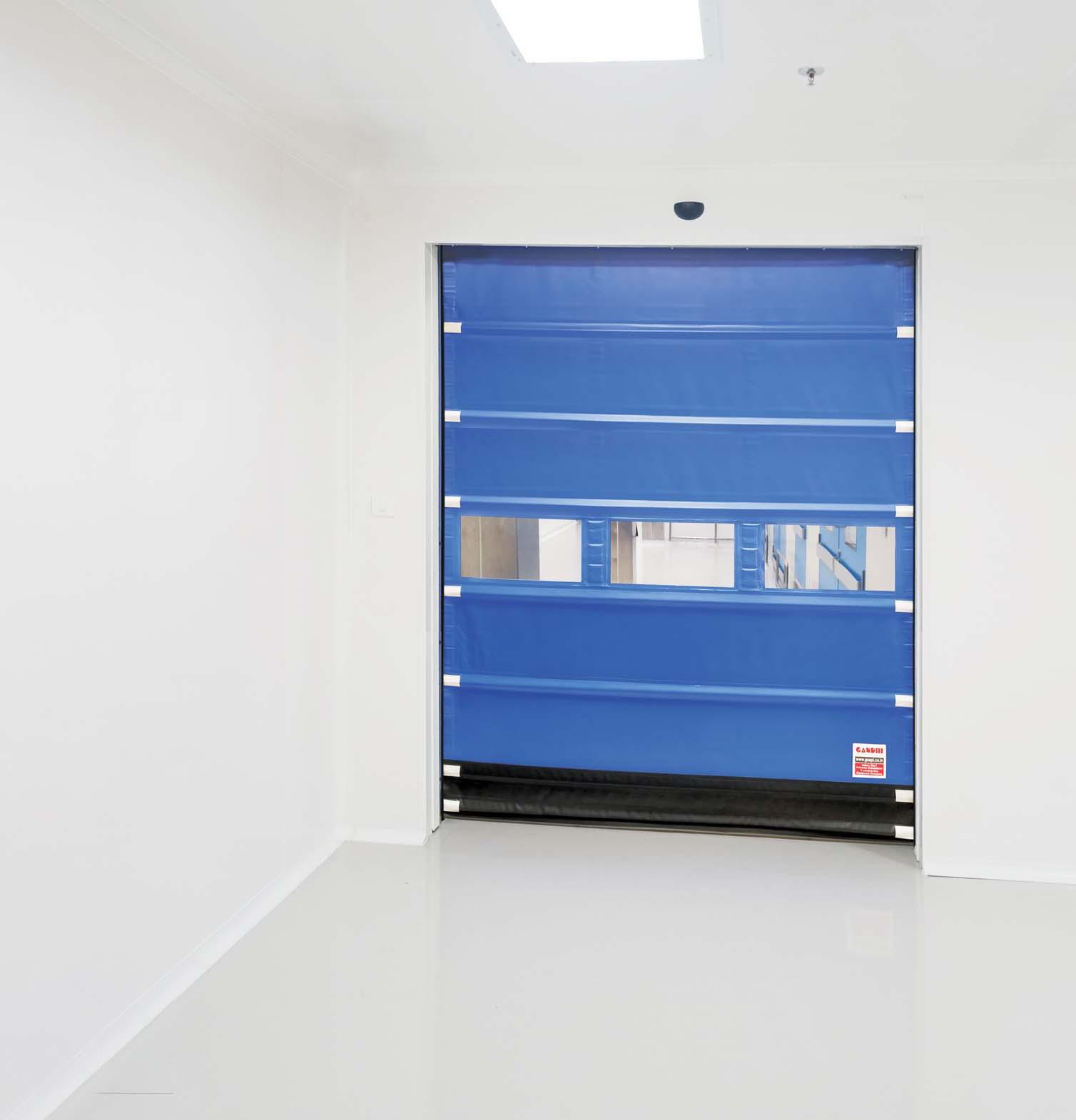
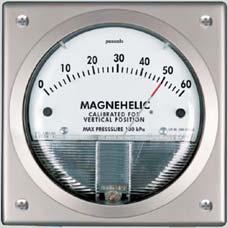
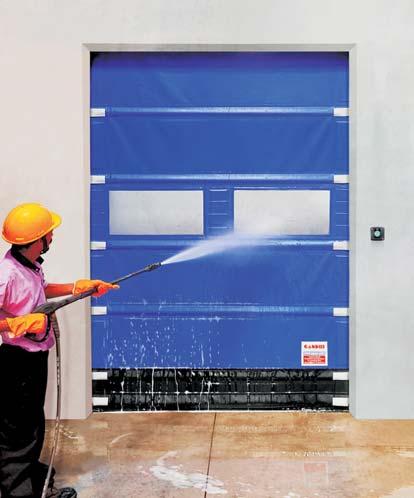
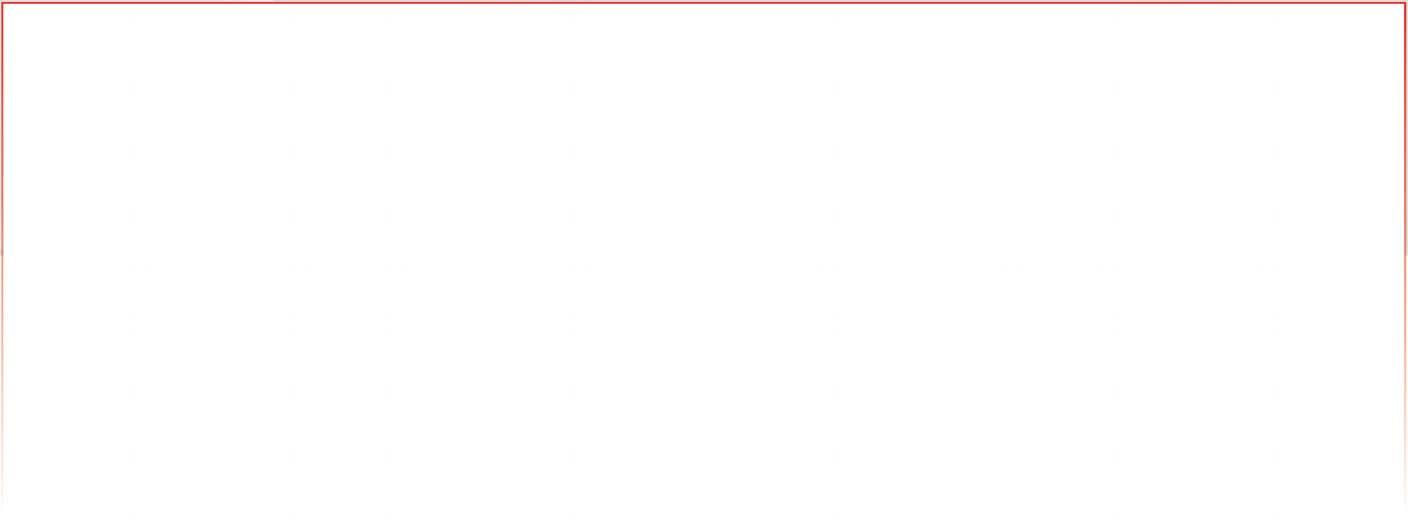
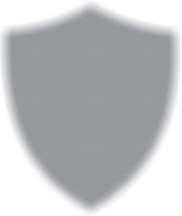
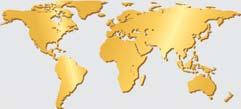
SEPTEMBER 2023,` 40
WhyX-rayinspection is a viable quality assurance solution for pharma products
Generative AI with Google Lens to detect counterfeits in pharma
Whatevercontainerformatyouneed–withmorethan130yearsof experience andzerodefectqualityapproachSCHOTTTypeImiddle borosilicateglassFIOLAX®helpsyoutosucceed. Benefitfromsafesupply,highestreliability,andpremiumquality. schott.com/fiolax
Withlatestdevelopmentsinallowableadjustmentsforbothisocraticandgradient compendialmethodsofUSP,IndustriesfollowingUSPguidelines,nowcanmodernize theHPLCmethodstoaddresstheorganizationalgoals,fastermethodsforfaster release,reducedextraworkofrevalidationofmethods,reducesolventconsumption forbetter&safelabenvironmentandreducedpersamplecost.
Scanthecodetoaccessanexclusiveinfographicguide.
Seema Singh, Ajay Kumar Dantuluri and Vijaya Kumar Jujare, Ashland Speciality Ingredients explain the various features and advantages of Natrosol™ 250 HEC and inform that it finds application as a tablet binder,a sustained-release polymer,a suspension aid,a film former in aqueous film coating,and a viscosifier in syrups
Natrosol™ 250 hydroxyethylcellulose (HEC) is a nonionic, water-soluble polymer that is commonly utilized in medicinal formulations due to its ability to provide thickening and viscosity-modifying properties.
Natrosol™ 250 HEC
Natrosol™ 250 HEC belongs to the cellulose ether family. Unlike sodium CMC, because it is nonionic, it is more resistant to pH changes and its solution quality is unaffected by high concentrations of other solutes such as salts, mild acids, and alkaline substances. Unlike HPC and HPMC, HEC remains soluble in both cold and hot water and does not precipitate from aqueous solutions at high temperatures. Natrosol™ 250 HEC pharm is soluble in both cold and hot water and does not gel or precipitate when heated to the boiling point of water. It is however partially soluble in some solvents, usually those that are miscible with water (for example, ethanol or water mixture), or those that contain polar groups (for example, glycerin and propylene glycol at a temperature around 550C to 600C). HEC is a cellulose ether polymer that is produced by the reaction of cellulose with ethylene oxide, this reaction results in the introduction of hydroxyethyl groups (-CH2CH2OH) along the cellulose chain.
HEC and the rate of addition to the water. In general, the lower viscosity grades are more easily dissolved than the higher viscosity grades.
To facilitate the preparation of Natrosol™ 250 HEC solutions, Ashland (the manufacturer) suggests several methods:
Adding the Natrosol™ 250 HEC
1. Slowly into the vortex of vigorously agitated water. This method involves adding the polymer slowly to the water while agitating the solution to prevent lump formation. The agitation should continue until all
GRADES AND TYPICALPROPERTIES FOR NATROSOL™ 250 HYDROXYETHYLCELLULOSE
water without lump formation.
Natrosol™ 250 HEC finds application as a tablet binder, a sustained-release polymer, a suspension aid, a film former in aqueous film coating, and a viscosifier in syrups.
Although Natrosol™ 250 HEC is more resistant to microbiological degradation than are natural gums and colloids, it is recommended that a preservative be added if solutions are to be stored.
Benefits of Natrosol™ 250 hydroxyethylcellulose in oral liquid applications
1) Viscosity: Non-Newtonian fluids, including polymer solutions and many pharmaceutical formulations like syrups, dispersions, emulsions, gels, and creams, exhibit variable viscosities depending on the applied shear. Shear-thinning liquids are characterized by decreasing viscosity with increasing shear rate. Natrosol™ 250 HEC solutions exemplify shear-thinning materials. Natrosol™ 250 HEC finds extensive use in modifying the viscosity of solutions, dispersions, and emulsions. By selecting the appropriate grade and concentration, a wide range of viscosities can be achieved.
250 HECis temperature-dependent, with an increase in viscosity upon cooling and a decrease upon heating. Unlike certain other cellulose ethers such as methylcellulose, HPMC, or HPC, Natrosol™ 250 HEC does not demonstrate a cloud point or gelation point. Consequently, HEC solutions can be boiled without experiencing precipitation or gelation problems.
5) Effect of pH: Being non-ionic, Natrosol™ 250 HEC solutions demonstrate relatively good stability within a pH range of 2 to 12, with minimal impact on viscosity. However, the solutions exhibit the highest viscosity stability within the pH range of 6.5 to 8.0. Below a pH of 3, solutions become less stable and may experience a reduction in viscosity due to acid hydrolysis.
Application of natrosol™ 250 pharm HEC in oral liquid formulations
Oral solutions are liquid preparations in which the API and other excipients are dissolved in suitable solvent system, consisting of water. Oral solutions containing high concentration of sucrose or other sugars traditionally have been defined as syrups. There is an increasing trend to replace sucrose in whole and in part with other substances because of its glycogenic and cariogenic properties. Cellulose ethers like Natrosol™ 250 HEC are non-glycogenic, because they're not hydrolyzed and absorbed into the bloodstream. Subsequently, when dissolved, they form a syrup-like vehicle for medications intended for use by diabetic patients and others whose diet must be restricted to non-glycogenic substances. The viscosity resulting from the use of these cellulose derivatives is much like that of a sucrose syrup. The addition of one or more artificial sweeteners usually produces an excellent imitation of a traditional syrup.
*Brookfield LV viscosity at 25°C, mPa·s, according to the Ashland method **EP viscosity label based on the EP viscosity method. EP viscosity range 75 – 140% of the value stated on the label (NF viscosity range 50 – 150% of the value stated on the label). Natrosol™ 250 HEC meet the monograph requirements of the United States National Formulary (NF) and the European Pharmacopoeia (Ph. Eur.).
Properties of Natrosol™ 250 HEC
Natrosol™ 250 HEC are supplied as offwhite, granular or fine powders that, when dissolved in water, give clear, smooth, nonthixotropic solutions. However, like many water-soluble polymers, the particles of HEC tend to clump or form lumps when first mixed with water. This tendency for the particles to agglomerate is known as lumping and can affect the rate at which the polymer dissolves.
The degree of lumping that occurs during the dissolution process depends on various factors, such as the viscosity grade of the
the swollen or gelatinized particles are dissolved, resulting in a smooth solution.
2. Pre-wetting Natrosol™ 250 HEC with a water-miscible organic liquid, such as ethyl alcohol, propylene glycol, or glycerin before adding it to the water. This method can improve the solution rate by effectively separating the particles of Natrosol™ 250 HEC, preventing lump formation.
3. Blending Natrosol™ 250 HEC with other dry components in the formulation can also improve the solution rate. This method separates the particles of Natrosol™ 250 HEC, allowing the solution to be added to
2) Effect of concentration: Aqueous solutions of Natrosol™ 250 HECexhibit increasing viscosity as function of increasing concentration and molecular weight. The rate of increase in the viscosity is dependent on the Molecular Weight, with higher molecular weight grades showing steeper increasing viscosity compared to lower molecular weight grades with the similar change in the concentration.
3) Effect of shear rate: Aqueous solutions of Natrosol™ 250 HECexhibits shear-thinning behavior, reducing viscosity as shear rate increases. This feature enhances formulation stability and facilitates easier application. All grades of Natrosol™ 250 HEC exhibit similar flow behavior, with varying degrees of viscosity change with shear rate based on molecular weight.
4) Effect of temperature: The viscosity of aqueous solutions containing Natrosol™
In summary,Natrosol™ 250 HEC offers several advantages as a viscosifier in oral liquid formulations
Non-glycogenic properties of Natrosol™ 250 HEC make it an ideal rheology modifier for preparing syrup-like vehicles for medications, particularly for diabetic patients and individuals with dietary restrictions on glycogenic substances.
The choice of Natrosol™ 250 HEC grade and concentration allows for customization of the desired rheology profile in the formulation.
Artificial sweeteners and / or cyclodextrins can be added to optimize taste, providing an imitation of a sugar syrup. Preservatives are necessary for sugar-free syrups containing Natrosol™ 250 HEC.
SEEMA SINGH Regional Marketing Manager –Pharma (APAC) AJAY KUMAR DANTULURI Technical Manager - Pharrma (ROA) VIJAYA KUMAR JUJARE Staff scientist, Formulation (ROA)Chairman of the Board
ViveckGoenka
Sr.Vice President-BPD
Neil Viegas
Vice President-BPD
Harit Mohanty
Editor
Viveka Roychowdhury*
Editorial Team
Lakshmipriya Nair
Kalyani Sharma
DESIGN
Art Director
Pravin Temble
Senior Designer
Rekha Bisht
Senior Artist
Rakesh Sharma
Marketing Team
Rajesh Bhatkal
Ashish Rampure
Debnarayan Dutta
Production Co-ordinator
DhananjayNidre
Scheduling & Coordination
Pushkar Waralikar
CIRCULATION
Mohan Varadkar
P17: INTERVIEW
Pg
21 WHYX-RAY INSPECTION IS A VIABLE QUALITY ASSURANCE SOLUTION FOR PHARMA PRODUCTS
26
47 IS INDIACAPABLE OFENSURING EQUITABLE ACCESS TO BIOPHARMACEUTICALS?
Regd.With RNI No.MAHENG/2005/21398.Postal Regd.No.MCS/164/2022 - 24.Printed and Published byVaidehi Thakar on behalf of The Indian Express (P) Limited and Printed at The Indian Express Press,Plot No.EL-208,TTC Industrial Area,Mahape,Navi Mumbai-400710 and Published at Mafatlal Centre,7th floor,Ramnath Goenka Marg,Nariman Point,Mumbai 400021.
Editor: Viveka Roychowdhury.* (Editorial & Administrative Offices: Mafatlal Centre,7th floor,Ramnath Goenka Marg,Nariman Point,Mumbai 400021)
* Responsible for selection of news under the PRB Act.Copyright © 2017.The Indian Express (P) Ltd.All rights reserved throughout the world. Reproduction in anymanner,electronic or otherwise,in whole or in part,without prior written permission is prohibited.
Even as the National Medical Commission Registered Medical Practitioner (Professional Conduct) Regulations, 2023, is held in abeyance till further notice, it has strengthened the call for quality medicines. Let us examine the possible impact on the pharma sector.
Speaking for most doctors, the Indian Medical Association (IMA) compared the National Medical Commission’s (NMC) push towards promotion of generics as “running trains without tracks’’, reasoning that not all generic medicines are of the same quality as their branded counterparts.
In contrast to the IMA’s stance, the Alliance of Doctors for Ethical Healthcare (ADEH) has put out a statement urging the NMC to reverse its decision to put the directive in abeyance. Their suggested solution: issue a “fresh, improved directive mandating doctors to write prescriptions in generic name only with the company name in the bracket if any RMP desires to”.
The ADEH statement points out that as generic names are used during the training of doctors in pharmacology and all clinical subjects, they should be allowed to continue to write prescriptions in generic names until the government can assure through concrete evidence that all medicines available in the market are of standard quality. In the absence of such reliable assurance, doctors have to rely on the company’s reputation, his/her individual experiences as well as of fellow doctors.
The ADEH statement also suggests that within five years, there should be a move towards a situation in which all medicines in India are of standard quality, whatever may be the manufacturing company. To monitor the progress towards this end, ADEH suggests that National Drug Surveys should be carried out based on representative samples of medicines in the retail market. Once this goal is achieved, all brand names should be gradually done away with.
They also urged the government to ban all irrational Fixed Dose Combinations (FDC) that constitute around 40 per cent of the retail market in India compared to seven per cent in World Health Organisation’s Essential Medicine List. Writing generics in prescriptions, the ADEH stated, becomes a huge challenge if irrational FDCs with multiple ingredients are to be prescribed using generic names.
What do these recommendations mean for the pharma sector in India? Spanning companies of all sizes, the sector is only as strong as its weakest link. Smaller
pharma companies do not always have the finances to put quality systems in place, yet contribute to affordability and access. Should the government crack down hard on quality, most MSME pharma companies are likely to fold up. Not only will this be a loss of livelihoods, it might impact medicine prices.
A crackdown on quality seems inevitable. Even though GMP norms are officially in place, recent global criticism on pharma quality triggered by children’s deaths linked to cough syrups made in India, have shown that implementation is patchy to say the least. In early August, Union Health Minister Mansukh Mandaviya announced new timelines for adoption of GMP norms. Pharma companies with an annual turnover of over Rs 250 crore have within six months, those with a turnover of less than Rs 250 crore have six months more to adopt GMP norms, else may be penalised. Will the GMP laggards fall in line this time?
Also, pharma companies might need to lay off their armies of medical representatives (MRs) if doctors cannot prescribe brands. While some part of this salesforce might be needed to shift build rapport with the pharmacy-distributor side, it's fair to say that the NMC regulations will change the rules of pharma marketing.
The NMC’s regulations prohibit doctors and their families from accepting gifts, fully-paid trips to medical conferences, etc. These restrictions are already part of the Uniform Code for Pharmaceuticals Marketing Practices (UCPMP) which are supposed to be followed by all pharma companies, as all major pharma associations have accepted this code. Inspite of periodic attempts to make it mandatory, the UCPMP has stayed voluntary.
Will NMC’s attempt to shift the onus on the receiver (rather than the giver) make a difference? There are already reports of doctor associations finding loopholes in the NMC’s regulations. For instance, in the case of medical conferences, the association is free to accept sponsorship from pharma companies but not individual doctors.
The NMC diktat has resurrected important debates on the loopholes in pharma manufacturing and marketing. It is high time these weak links are addressed and fixed once and for all.
VIVEKA ROYCHOWDHURY, Editor viveka.r@expressindia.com viveka.roy3@gmail.comSpanning companies of all sizes,the sector is only as strong as its weakest link
Analysing the increased M&A and investment activity across India’s API, formulations and nutraceutical ingredients, driven by domestic consolidation and inbound global investor interest
Subhakanta
Bal ,MD, Rothschild & Co tells Viveka Roychowdhury that he is highly confident to grow meaningfully in the next two to three years
As one of the world’s largest independent financial groups, with more than 200 years of global expertise, how important a market is India to Rothschild & Co's overall business, in terms of revenue share (or percentage growth in revenue share)?
Rothschild & Co is one of the largest independent financial advisory firms globally with over 1,500 professionals on the ground in 58 locations across 42 countries. During 2021 and 2022, the firm successfully advised on over 1,000 M&A
EXPRESS PHARMA 17
Schott Glass India: Borosilicate glasses usually have a very good heat resistance. After converting they go through the annealing oven at around 600°C without changing the chemical composition. In the filling process, the temperature of around 300°C is easily bearable for them even if they are standing there for a few hours. The point is not so much the temperature itself but rather the temperature difference if they are exposed to heat and cold at the same time (temperature shock resistance). Here the strength depends on the the Coefficient of Thermal Expansion (CTE). The lower the CTE is, the higher is the temperature shock resistance. E.g. a FIOLAX(R) container (CTE of 4.9) with a wall thickness of 1.0 mm can bear a temperature difference of almost 200°C. A soda-lime container (CTE of around 9) with a wall thickness of 1.0 mm e.g. can only bear temperatures around 100°C. This is important for the lyophilization process where the glass is frozen inside and at the same time heated from the bottom. It should be kept in mind that this relates to a container without any defects on the glass surface. Any defect lowers the resistance. The temperature shock resistance can be influenced by the wall thickness. As glass is a quite bad heat conductor the temperature shock resistance increases with decreasing wall thickness.
deals globally, which makes us the most active global advisor by volume of transactions. India has been essential to the firm’s global strategy for over 20 years. With a team of 25+ bankers and advising on an average of 12-14 transactions every year, we are one of the country’s largest pure play global M&A and financial advisory firms.
Our business in India has grown significantly over the last five years, both in terms of banker strength and revenues. Our focus on pure-play M&A and financial advisory service offering, strong global sector expertise coupled with experienced local bankers, and longevity of senior bankers within the firm in India is certainly paying off, evidenced by the rising share of repeat business from our existing clients. Given
how our business in India has shaped over the last five years, we are highly confident to grow meaningfully in the next two to three years.
What's been the engagement levels with India's healthcare and pharma sectors, in terms of growth in value/volume of deals transacted as a percentage of Rothschild & Co’s global business?
Healthcare is an important and growing market at a global level. With a global team of c.100 bankers dedicated to the sector, Rothschild & Co has advised on over 170 transactions in the healthcare sector globally in the last three years. It is also a globally interconnected sector, especially in pharma and medical devices, which leads to a large volume of
Schott Glass India : The Coefficient of Thermal Expansion is a measure how much the glass expands and shrinks in volume when it is heated and cooled down again. The smaller the CTE the less is the movement. Pure quartz glass e.g. has a CTE of below 1 · 106/K. The CTE is a consequence of the chemical composition of the glass. The higher the amount of Alkali (Na, K) and Alkaline earth (Ca, Mg, Ba) metals in the glass is, the higher is also the CTE. Among the Borosilicate glasses there are basically three groups: The group of 3.3 CTE glasses. That is where Boro8330TM is located. Then we have the group of around 5.0 CTE glasses, where FIOLAX(R) belongs to. And at last there is the group of 7.0 CTE glasses, mainly produced and used in China. Apart from indicating the quality of the glass the CTE is also quite important for temperature applications. Especially for freeze-drying applications glasses with CTE of 3.3 or 5.0 are highly recommended. During freezing and heating the temperature difference can be quite high so that breakage due to temperature shock can occur. And this comes easier for 7.0 expansion or soda-lime glasses than for 3.3 and 5.0 CTE glasses.
For more information contact: santosh.jadhav@schott.com
Pharma B2B has witnessed consistent M&Aactivity,especially in the Active Pharmaceutical Ingredient (API) segment.
The industry continues to be fragmented, providing the opportunity for consolidation
cross-border activity for us. We have scaled up our healthcare sector franchise in India over the last few years and are now regarded as among the top two global firms in the healthcare sector in India, having advised on over 15 transactions in the last seven years. Some of the healthcare sector transactions we have advised in India include the sale of 20 per cent stake in Piramal Pharma to Carlyle, sale of Medreich to Meiji Seika Pharma, Intas Pharma’s acquisition of Actavis UK & Ireland, fund raise from Temasek by Integrace Health, sale of Oaknet Healthcare to Eris Lifesciences, TPG Growth’s investment in Solara Active Pharma and sale of majority stake in Symbiotec Pharmalab.
We continue to be busy in the sector, advising currently on multiple transactions across pharma, MedTech and healthcare services. We have advised a diversified set of clients in the healthcare sector in India, with our client base comprising large Indian generics majors, private equity (PE) funds and familyowned firms. In general, across sectors, we have had extensive experience in advising family owned/founded firms, which comes naturally to us, given our own heritage as a familyowned firm.
Quite a few pharma promoters in India are divesting stakes, as the next generation is not interested in taking forward their legacy in the same sector. As an investment banking and advisory firm, which are the segments most attractive for such deals and strategic investors like PE/VCs?
We have seen strong deal activity across multiple segments within the healthcare sector in India.
Not surprisingly, a lot of activity has been in the pharma sector, across multiple sub segments including domestic formulations, API/CDMO and nutraceutical ingredients. In
the domestic formulations segment, we have seen a healthy level of activity from strategics as well as PE funds. Trade activity has been driven by a desire to enhance market share, plug specific whitespaces from a therapy area standpoint and
accelerate beyond organic growth. Pharma B2B has witnessed consistent M&A activity, especially in the Active Pharmaceutical Ingredient (API) segment. The industry continues to be fragmented, providing the opportunity for consolidation.
PE activity has been led by funds seeking platform investments and subsequent bolt-on acquisitions to acquire capabilities and scale up. Trade activity has been primarily driven by a desire to expand in high growth segments such as HPAPI,
oncology, peptides and injectables.
Nutraceutical ingredient segment has also had recent deal activity, such as Novozymes’ acquisition of a majority stake in Synergia Life Sciences and TA Associates’ investment in OmniActive
Health Technologies. The space is witnessing interest from global strategics as well as PE funds on the back of strong growth driven by rising consumer awareness and a shift towards preventive care. This segment is also witnessing strong inbound interest with overseas companies looking to acquire assets in India to access niche/high growth product portfolios, expand their manufacturing base and benefit from revenue synergies.
We have seen quite a few M&As /deals centered around Active Pharmaceuticals Ingredients (APIs) manufacturers as investors look to secure the global pharma chain to avoid the disruptions seen during the Covid pandemic. By when will we see the results of such moves?
There is more focus on APIs now post-Covid. Several regions/countries have historically relied on China for bulk drugs/APIs. Given the supply chain disruptions faced during Covid, there is a greater realisation of the need to diversify the supply chain and avoid over reliance on one country/source. In certain product categories, China is likely to continue to be the major source/supplier, given the vast capacities (and consequently cost efficiency) built over time. This would be especially relevant in high
volume intermediates/APIs, where cost is a key consideration and having large scale capacities helps drive costs of production down (i.e., benefit from economies of scale).
However, in categories which are either high value/niche or considered critical, we are witnessing a desire on the part of customers to diversify the supply chain outside of China i.e., China + 1 strategy. Outside of China, India and Italy are two of the major API manufacturing hubs, which are expected to further fuel the demand for APIs from India. We expect such supply chain diversification moves to take time to show results, given the gestation period involved in setting up large capacities and building/developing the ecosystem required to have local production at a meaningful scale.
What are the trends driving M&As in the domestic formulations space in India and how is it likely to evolve going forward?
There has been a strong wave of M&A activity in the Indian domestic formulations space. Large Indian domestic companies are doubling down on the Indian market driven by a desire to enhance presence, plug specific whitespaces from a therapy area standpoint and accelerate beyond organic growth. Some key deals
include Torrent Pharma’s acquisition of Curatio Healthcare, Eris Lifesciences’ acquisition of Oaknet Healthcare and Mankind Pharma’s acquisition of Panacea Biotech’s domestic formulation brands. Several strategic transactions have been in the form of brand acquisitions to fill specific portfolio gaps and strengthen specific divisions. Most large Indian pharma companies enjoy a healthy balance sheet, providing the ammunition to fund inorganic growth. This coupled with the fact that there are limited avenues for inorganic capital deployment (with similar risk-reward dynamics) implies that domestic M&A activity is expected to continue going forward.
Several larger domestic companies are looking to focus on core portfolios and sharpen capital/resource allocation decisions. This in turn has also resulted in companies divesting select non-core brands, a trend that is likely to continue.
There has also been a fair amount of PE activity in the Indian domestic formulations space, including Advent’s acquisition of Bharat Serums and Vaccines, KKR’s acquisition of a controlling stake in J.B. Chemicals & Pharmaceuticals and True North’s acquisition of Glenmark Pharmaceuticals’ orthopaedic and pain
management business. This trend is expected to continue as some local companies look to sell, driven by a lack of succession considerations or as some of the larger companies look to restructure/shed non-core portfolios.
Given uncertain macroeconomic trends, increasing pricing pressures, escalating regulatory overhang due to quality concerns shadowing even the bigger Indian pharma companies, what's been the track record of M&A in the healthcare/pharma ingredients sector (globally versus India) and how do we expect it to evolve over the next few years?
Pharma B2B has been an area with consistent M&A activity, especially in the API segment driven by PE funds and corporates. The industry has been and continues to be fragmented, providing consolidation opportunities. The industry continues to benefit from a structural move from customers to increasingly outsource manufacturing activities and shift towards an asset-light business model driven by cost pressure, the desire to migrate from a fixed to a variable cost structure and supply chain complexity.
In addition, there has been a growing share of mid and
small pharma companies in the late-stage pipeline, which bodes well for continued growth in outsourcing, as several mid and small pharma companies rely on outsourcing to meet their manufacturing requirements. Also, there seems to be rising demand from customers for integrated service offerings, which would further drive consolidators to fill gaps in service offerings through acquisitions. China + 1 strategy could also drive inbound activity with overseas companies looking to acquire assets, especially those with strong regulatory track record, meaningful regulated markets exposure and presence in high-growth and niche areas.
As you rightly said, there is clearly a greater focus on compliance and regulatory track record. Given the increase in regulatory scrutiny and the spate of OAIs (Official Action Indicated) issued by USFDA over the last few years, investors and acquirers are increasingly emphasizing regulatory compliance/track record. Based on our experience, we believe a strong regulatory/compliance track record, especially with US and European regulators has clearly evolved into a “must have” for most investors.
viveka.r@expressindia.com
viveka.roy3@gmail.com
Mike Pipe,Head of Global Sales & Product Management, Mettler-Toledo Safeline X-ray, explains why x-ray inspection should be an invaluable asset in the pharma industry, providing manufacturers with comprehensive and accurate quality checks while dispelling concerns about its impact on products
We are all aware that the pharma industry operates within a highly regulated environment, where upholding product safety and quality is paramount. Manufacturers invest significant resources in validation processes to meet regulatory requirements. One technology solution to complete quality assurance checks in the pharma sector is product inspection. While many manufacturers rely on systems like vision inspection and metal detection, the use of x-ray inspection is gaining recognition as an additional tool for quality assurance. To understand the benefits of x-ray inspection, we must first look at its
functionalities, then address the misconceptions. In this article, we will explore why x-ray inspection should be an invaluable asset in the pharma industry, providing manufacturers with comprehensive and accurate quality checks while dispelling concerns about its impact on products.
The primary function of x-ray inspection is contaminant detection of a wide range of foreign bodies including metal, glass, mineral stone and highdensity plastics. Simultaneously, x-ray systems perform valuable in-line quality checks including counting components, identify missing or broken products, monitoring fill levels, checking for damaged packaging and detecting agglomerates such as flavour and powder lumps.
To understand the benefits of x-ray inspection, we must first address the misconceptions. Pharma manufacturers often express concerns about the potential impact of x-ray inspection on their products. However, studies have consistently shown that the quantity and energy of x-rays used during product inspection are minimal, and the duration of exposure is extremely brief. For example, tablets undergoing x-ray inspection are typically exposed to low-energy xrays for less than 0.2 seconds. In comparison, the dose of background radiation that pharma products receive while on the shelf, in transit or during consumer ownership is significantly higher than the levels delivered by an end-ofproduction line x-ray inspection system.
The US Food and Drug Administration (FDA) acknowledges that the dose levels received by objects passing through an x-ray inspection system are lower than the dose of background radiation received in a single day. Furthermore, and perhaps most crucially, the FDA asserts that there is no known danger in
consuming medicines that have undergone x-ray inspection. 1
Scientific studies have also been conducted to evaluate the effects of x-ray inspection on pharma products. For instance, researchers at the Department of Drug Delivery and Nano Pharmaceutics, Graduate School of Pharmaceutical Sciences, Nagoya City University in Japan conducted a study on the effect of x-rays on the pharmaceutical quality of drug tablets. The study exposed acetaminophen, ioxoprofen and mefenamic acid tablets to varying x-ray doses, ranging from 0.34mGy to 300Gy. These doses were significantly higher than those delivered by typical x-ray inspection systems. The evaluation of sam-
to x-ray radiation for a period of two hours. This extended exposure time was significantly longer than the fraction of a second typically used during industrial x-ray inspection. However, no degradation was observed in either substance after the two-hour exposure period. 3
These scientific studies collectively demonstrate that x-ray inspection at the levels used in pharma manufacturing does not significantly affect the quality or efficacy of the products. While not all formulations have been studied, the low doses of x-ray radiation involved in x-ray inspection systems are well below the levels of naturally occurring background radiation and do not pose a risk to product integrity.
facturers to address these specific concerns and gain confidence in the integrity of their products.
However, it is important to recognise that the extensive scientific studies and regulatory guidelines surrounding xray inspection provide a strong foundation for manufacturers to trust this inspection method. The studies have consistently demonstrated the safety and efficacy of x-ray inspection, and regulatory bodies acknowledge its effectiveness in ensuring product quality and safety.
Utilising the technology of x-ray inspection systems, manufacturers can start to see significant benefits on their production line. It eliminates the need for redundant testing, which can be costly
line, x-ray inspection becomes one of the most versatile and comprehensive inspection tools available to manufacturers. Unlike other inspection methods, x-ray inspection has the capability to inspect a diverse range of products, regardless of their shape or packaging.
One of the significant advantages of x-ray inspection is its ability to penetrate various materials, including metals, glass, high-density plastics and rubber. This capability enables the detection of dense foreign bodies that may contaminate pharmaceutical products. Metal fragments, glass shards or other foreign objects that could compromise product quality and safety can be reliably identified and removed from the production line, p reventing them from reaching the consumers.
ples through formulation tests revealed that exposure to xrays did not affect the pharma quality of the drug tablets. The exposed samples exhibited similar characteristics in dissolution, disintegration and hardness tests as control samples that were not exposed to x-rays. Additionally, when combined with accelerated temperature and humidity tests equivalent to six months of exposure, x-ray exposure did not affect the pharma quality of the samples. This study concluded that x-ray exposure at levels much higher than those encountered during product inspection had no significant effect on the efficacy or other properties of the drug tablets. 2
Another study, conducted by Robert Bosch Packaging Technology and the PHAST Society for Pharmaceutical Quality Standards, exposed model pharma substances, tramadol HCl and nifedipine,
Despite the availability of such comprehensive studies, pharmaceutical manufacturers often prefer to conduct their own tests. This cautious approach can be attributed to the stringent regulatory environment in which they operate. Regulatory bodies worldwide have established guidelines and requirements for pharma manufacturing including the Good Manufacturing Practice (GMP), the Good Distribution Practice (GDP), and manufacturers who want to comply with these regulations while maintaining the highest level of quality assurance.
Some manufacturers may have concerns specific to their products or processes that they believe require additional scrutiny. These concerns may stem from the complexity of the formulation, sensitivity to radiation or unique packaging requirements. Conducting their own tests allows manu-
and time-consuming, allowing manufacturers to streamline their processes and focus on other critical aspects of production. By trusting in the proven capabilities of x-ray inspection systems, manufacturers can benefit from the expertise and experience of the producers of these systems, who have a deep understanding of the technology and its application in the pharma industry.
So where should x-ray inspection technology be used within the production process and what are its benefits?
Traditionally, x-ray inspection in the pharma industry has been primarily used for specific applications, such as verifying the presence of tablets or needles. However, the potential of x-ray inspection extends far beyond these limited applications. When employed at the end of the production
As mentioned at the start of this article, in addition to contaminant detection, x-ray inspection allows for other critical quality checks. It can verify the completeness and integrity of packaged products, detecting missing or damaged items within the packaging. This level of scrutiny is essential in the pharmaceutical industry, where missing components or damaged products can have severe consequences for consumers. For instance, checking the presence of needles in glucose monitoring systems, verifying their functionality is crucial, as a faulty device could have fatal implications for diabetic patients. By detecting and preventing the distribution of defective or compromised products, xray inspection plays a crucial role in upholding a company's brand image and reputation.
One of the notable advantages of x-ray inspection is its versatility. Unlike other inspection methods that may be limited to specific product types or packaging formats, xray inspection can be applied to a wide range of pharmaceutical products, regardless of their shape, size or packaging materials. It is particularly
The US Food and Drug Administration (FDA) acknowledges that the dose levels received by objects passing through an x-ray inspection system are lower than the dose of background radiation received in a single day
beneficial for pharmaceutical manufacturers who commonly use metalised film or aluminium-backed blisters as packaging methods. X-ray inspection systems can effectively inspect products contained within these packaging materials and check their integrity and quality.
By leveraging x-ray inspection technology at the end of the production line, pharmaceutical manufacturers can enhance their quality control processes and minimise the risk of contaminated or defective products reaching the marketplace. The comprehensive nature of x-ray inspection, coupled with its ability to inspect a variety of products and packaging formats, makes it an invaluable tool in upholding product safety and maintaining consumer trust.
Beyond its ability to detect defects, x-ray inspection systems also contribute to compliance with regulations and provide traceability. The data generated by x-ray inspection systems can facilitate compliance with regulatory requirements. Manufacturers can access comprehensive quality data and export it as needed, providing transparency and accountability. X-ray inspection systems enable the creation of individual images of each product, complete with date and time stamps, providing information to support due diligence that quality checks have been completed. The information is easily retrieval thereby facilitating easy tracking. Additionally, the reporting capabilities of x-ray inspection systems allow for detailed shift
and production reports, including the number of rejected items. This level of documentation aids the validation process and ensures that approved settings remain unchanged during production, minimising the risk of errors or deviations.
X-ray inspection plays a crucial role in completing a large range of quality assurance checks without significantly impacting the efficacy or physical properties of pharmaceutical products. The technology offers comprehensive contaminant detection, quality checks, compliance facilitation and traceability, all of which contribute to brand protection and consumer safety. By embracing x-ray inspection as an additional tool in their quality assurance processes, pharma-
ceutical manufacturers can elevate their standards, mitigate risks, and have confidence that high quality products are entering the market. The time has come for the industry to recognise the immense value xray inspection brings and embrace its potential for a safer and more reliable pharma supply chain.
1. Based on an airport security X-ray system, typically of higher dose than an inspection system for pharmaceutical products. From the FDA website: “There are no known adverse effects from eating food, drinking beverages, using medicine, or applying cosmetics that have been irradiated by a cabinet x ray system used for security screening. The radiation dose typically received by objects scanned by a cabinet x-ray system is 1 milli-
rad or less. The average dose rate from background radiation is 360 millirad per year.”
https://www.fda.gov/radiationemitting-products/security-systems/frequen
2. Kazuaki Uehara, Tatsuaki Tagami, Itaru Miyazaki, Norikazu Murata, Yoshifumi Takahashi, Hiroshi Ohkubo & Tetsuya Ozeki (2015) Effect of X-ray exposure on the pharmaceutical quality of drug tablets using X-ray inspection equipment, Drug Development and Industrial Pharmacy, 41:6, 953958, DOI: 10.3109/03639045.2014.917093
3. Martin Vogt, Elke Sternberger-Rutzel, Manuel Birke & Christoph Jacobs (2012) Influence of X-ray radiation as PAT method on the model substances tramadol HCl and nifedipine compared to the influence of UV-Vis radiation, TechnoPharm 2, Nr. 3, 1–12
Counterfeit pharma jeopardise patient safety, infringe on intellectual property rights, and undermine the credibility of the pharma industry. Current methods of combating counterfeits are often time-consuming, expensive, and prone to human error.
The recent government announcement that 300 samples would have QR codes has some restrictions. QR codes can be rendered inoperable by scratching them off using a sharp object or marker. It is useless if the QR codes are broken. What use does the label serve, and who is responsible for making sure the QR code is still working when it changes commercial hands? What assurance is there that counterfeiters who can easily mimic a brand's packaging, name, and logo won't also be able to mimic its QR codes?
A more efficient and accurate solution is required to identify counterfeit drugs and protect public health.
Combining generative AI and image recognition is probably the answer. With the use of Google Lens and Generative Artificial Intelligence (AI) technology, a complex system for assessing photo metadata (Photo Meta Data) on pharma packaging and verifying the authenticity in real time.
I'd want to make a recommendation for pharma companies, government officials, and customers to combine the strength of AI with picture recognition to create a foolproof way to restrict the risks connected with counterfeit drugs.
*In 2018, Google Images introduced some new features to its image search results. Next
to a selected photo, the creator of the image, the credit line, and a copyright notice are immediately displayed. This works by reading the corresponding IPTC photo metadata fields embedded in the image file. On August 31, 2020, this feature was enhanced to also display a licensable badge above an image and a link to the licensing information.
System requirements
a. Generative AI: Implement advanced Generative AI algorithms that analyse visual patterns, text, and packaging features to identify discrepancies between genuine and counterfeit pharma packs.
b. Google lens: Utilise the powerful visual recognition capabilities of Google Lens to capture and interpret codes on the packaging swiftly.
c. Cloud-based database: Establish a cloud-based database containing comprehensive information about authorised pharma products, including packaging details, manufacturing locations, and authorised distributors.
d. Machine learning: Train the system using machine learning techniques to improve
accuracy and adaptability over time.
System workflow
1. Generative AI will be used to create unique invisible image tags for each product (like UID). This can be done by training the AI on a dataset of existing batch numbers, allowing it to generate new, unique invisible image tags on brand logo / brand name that cannot be replicated by counterfeiters
2. These unique image tags will then be printed on the packaging of each pharma product during the manufacturing process. (Covertly on Brand Logo and Brand Name)
3. Google Lens will be used by consumers to scan these image tags. Upon scanning, Google Lens will verify the code against a database of legitimate codes (image tags). If the code matches one in the
database, the product is confirmed as authentic. If not, the product is flagged as potentially counterfeit.
4. In addition, the system can provide detailed product information, such as manufacturing date, batch number, expiry date, etc., to further assure the consumer of the product's authenticity.
Key features and benefits
a. Real-time authentication: The system provides instant verification of pharma packs by scanning image tags using Google Lens and analysing visual patterns with Generative AI. This ensures rapid and accurate identification of counterfeit products.
b. User-friendly interface: Develop a user-friendly mobile application or web portal that allows consumers, healthcare professionals, and regulatory authorities to access the system easily and perform authentication checks.
c. Comprehensive database: Maintain a cloud-based database containing detailed information about authorised pharma products, enabling prompt comparison and verification during scanning.
d. Enhanced traceability:
Enable pharma companies to track their products throughout the supply chain, reducing the risk of counterfeit products entering the market and facilitating targeted recalls if necessary.
e. Regulatory compliance: Support regulatory authorities in enforcing pharma regulations and combating counterfeit drugs by providing them with a reliable tool for inspections and investigations.
f. Consumer empowerment: Empower consumers to verify the authenticity of pharma products before purchasing, thereby increasing trust in the market and reducing the potential harm caused by counterfeit drugs.
Counterfeit pharma products are a growing global concern. By offering a scalable and reliable solution, our business aims to address the needs of pharma manufacturers, regulators, healthcare professionals, and consumers worldwide. The market potential is substantial, with potential revenue streams including licensing the technology to pharma companies, charging fees for database access, and offering premium services for enhanced features.
By harnessing the power of Generative AI with Google Lens for scanning image tags on pharma packs, proposed solution provides an efficient, accurate, and scalable approach to combating counterfeit pharma products. With enhanced authentication capabilities, regulatory compliance support, and empowered consumers, the solution aims to make a significant impact on public health and safety while fostering trust in the pharma industry.
Amaninder Singh Dhillon,Consultant explains how combining generative AI and image recognition can help create a more efficient and accurate solution to
and protect public health
Pharma FR&D leaders and experts come together to envision India Pharma Inc's evolution into an innovation-driven powerhouse and a global pharma leader at FDD Conclave 2023
Organised by Express Pharma, FDD Conclave has emerged as 'the' platform for leaders, experts and veterans of FR&D to come together, confer and converse on the current and future trends in the industry, growth drivers and challenges, as well as form meaningful alliances to fast-track progress.
EXPRESS PHARMA
September 2023
FDD Conclave 2023 also witnessed pharma FR&D leaders delve into the industry's evolution from a generics-centric model to an innovation-driven powerhouse. It was held at Park Hyatt Hyderabad, on July 21-22, 2023. Under the theme, ‘Making India an epicenter for FR&D’, the event explored avenues to
harness India Pharma Inc’s strengths, cultivate new capacities, and navigate a path towards creating innovative and differentiated pharma solutions for the world. The leaders also examined the impact of recent government initiatives, regulations and policies to promote innovation in pharma R&D and help India
secure and sustain a key position in the global pharma R&D landscape.
Thus the conclave sparked transformative discussions and dialogues which can help India Pharma Inc to leverage its established capabilities and accelerate its trajectory towards becoming an innovation-driven industry.
Formulation Delivery and Drug Delivery (FDD) Conclave 2023 witnessed insightful discussions and showcased exciting advancements in pharma FR&D research. Thought provoking and invigorating sessions with an impressive line-up of speakers were part for the event.
The first panel discussion at the event focused on "Fuelling inn ovation in oral solid dosage forms: Opportunities and challenges.”
In this discussion, industry experts delved into the potential for advancements and innovation in oral solid dosage forms. They shared valuable insights to unravel opportunities, and chart strategies that can overcome challenges and pave the way for transformative breakthroughs in this critical area.
The expert panelists in this discussion were Manikandan Ramalingam, Sr VP-R&D, Granules Pharma (Moderator); Dr Subhrangshu Sengupta, VP - R&D - Formulation, IPCA Laboratories; Dr Pirthipal Singh, VP and Head R&D, Tirupati Group; Dr Sandhya Shenoy, AVP R&D, IPCA Laboratories; Dr Ravikumar N, EVP, MSN Laboratories; and Dr Mayur Patel, Head-Formulation Development, APNAR Pharma.
They spoke on the current and future trends and discussed pivotal aspects such as overcoming the obstacles of permeability and stability in the development of oral biologics. The experts pointed out that this roadblock must be surmounted to ensure the progress of this inn ovative avenue of medicine.
The panelists also spoke on the potential of 3D technology to revolutionise pill design by offering customisable shapes, colors, and even tastes, thereby enhancing patient experience. They highlighted that pill burden can be reduced through 3D printing and this presents an opportunity to individualise medications and customize manufacturing processes.
Similarly, they spoke on the advent of digital pills and the complex challenges associated with them. The experts cautioned that while they hold the potential to greatly enhance med-
● Overcoming permeabilityand stabilitychallenges will be keyfor progress in oral biologics.
● 3D printing can provide the desired shape,colour and taste to pills,reduce pill burden,offer personalization,facilitate onsite manufacturing etc
● Digital pills can enable medicine adherence and prevent over dosage.But,fears of privacybreach,cost,lackof proof of concept are challenges to overcome
● Convenience,compliance and cost are the three Cs which are keyfor FR&D scientists.Patient centricityshould be central to all innovations in FR&D
● Paediatric and geriatric polulations require medicines which are palatable,reduce pill burden and side effects and enables patient adherence.
● Novel excipients can help innovate and improve our old formulations and improve their efficiacyand effectiveness
ication adher ence and p revent overdose, concerns regarding privacy breaches, cost-effectiveness and the necessity for robust proof of concept must be addressed to encourage widespread adoption.
They underscored the importance of tailoring pharma innovations to cater to the specific demands of di-
verse patient demographics such as the pediatric and geriatric groups. The panelists also highlighted the potential of novel excipients to rejuvenate and enhance traditional formulations, boosting their efficacy and effectiveness.
They concluded that the driving forces for research and development
scientists lie in the three Cs: convenience, compliance, and cost-effectiveness. However, at the heart of all these scientific endeavours should be an unwavering commitment to patient centricity. Any innovation in pharma must prioritise the needs and well-being of patients to truly make a meaningful impact.
Dhairy Sharma, Technical Sales, CILICANT, took the stage at FDD Conclave 2023 to present on "I nnovation in Active Packaging." He elaborated on the latest advancements in active packaging and showcased ho w they ar e revolutionising the pharma industry by ensuring product stability, extending shelf life, and enhancing patient safety.
Underscoring the importance of smart active packaging solutions, the session shed light on CILICANT's contributions to maintain the quality and integrity of primary packaging through their FREXIL dust-proof canisters and desiccant solutions. Sharma emphasised how this solution resonates with the industry's need for uncompromised product quality.
Sharma informed that CILICANT's FREXIL dust-proof canisters play a pivotal role in safeguarding products from potential contaminants, ensuring that the packaging remains untainted. The presentation spotlighted how CILICANT's solutions - FREXIL type C and type Y desiccants address multiple challenges simultaneously, effectively tackling moisture-related issues and odours.
Attendees gained insights about the importance of a proactive approach to moisture control and odour mitigation. The session also explained how these smart active packaging solutions from CILICANT solutions can elevate their packaging strategies, optimising both quality and customer satisfaction.
FDD Conclave 2023 witnessed presentations on several relevant issues. One of them was on the topic of Form 483, Tablet Compressibility & MCC. Dr Abhijit V Gothoskar, Formulation Expert from Sigachi Industries provided valuable insights into these crucial aspects.
The session focused on the critical issue of tablet failures during manufacturing and the role of excipients in this context. The presentation shed light on the escalating regulatory focus on tablet manufacturing issues and underscored the significance of excipient performance. Dr Gothoskar explained how excipients can mitigate observations in Form 483, ultimately leading to enhanced tablet manufacturing quality.
One of the key takeaways was the emphasis on understanding the
nuanced role of excipients in tablet formulation, especially when regulatory bodies are increasingly scrutinising tablet failures during manufacturing. The session also spotlighted Microcrystalline Cellulose (MCC) as a time-tested, multifunctional tablet excipient. Dr Gothoskar spoke about the significance of MCC in tablet formulation and its versatile properties that contribute to tablet integrity, stability, and overall performance.
He also informed that Sigachi, as a dependable formulation partner and solution provider, can offer valuable expertise and resources to navigate the complexities of tablet formulation. The session gave insights on robust tablet formulation strategies and a proactive approach to regulatory compliance through the right excipients.
FREXILdust proof canisters by CILICANTmaintain the quality of your primary packaging. These innovative solutions eliminates the possibility of dusting,takes care of moisture and odour
Dr Ajay Khopade, VP FR&D, Sun Pharmaceutical Industries spoke on the theme and vision for FDD Conclave 2023, i.e. transforming India into a global epicenter for pharma formulation research and development. His session highlighted that the roadmap to realise this ambitious goal is through a comprehensive sixpoint agenda which included:
◆ Augmenting investment in pharma R&D to create an environment conducive to innovation and drug discovery through multifaceted approaches, including incentivising R&D through grants, fostering collaborative ventures with academic institutions, and attracting clinical trials to expedite the development process.
◆ Acceleration of drug approval processes and clinical trials through transparent processes, a robust regulatory framework, commitment to inter-
national standards and stringent intellectual property (IP) protection.
◆ Investment in human capital through comprehensive training and skill development initiatives to fortify India Pharma Inc’s competitive edge.
◆ Upgraded infrastructure like state-ofthe-art research laboratories and manufacturing facilities with integration of advanced technologies, such as automation and digitalisation, to create an environment conducive to innovation.
◆ Encourage symbiotic collaborations between domestic and international stakeholders to accelerate drug development, and harness the collective expertise of industry players, research institutions, and government bodies.
Thus, Dr Khopade's blueprint underscored that a multifaceted approach is necessary for India to emerge as a focal point for pharma formulation R&D.
Dr Kuldeep Bhokare, DirectorPharmaceutical Process, Romaco, presented on the topic, “Formulation Development with Advanced Fluid Bed Technology.” This session provided insights into the applications of advanced fluid bed technology and its potential to drive breakthroughs in pharma formulation.
Dr Bhokare spoke on formulation development empowered by Fluid Bed Technology and elaborated on the Fluid Bed Technology's distinct mechanisms, which include Top Spray, Bottom Spray, Tangential Spray, and Wurster Column mechanisms.
He explained about Fluid Bed Technology's features such as the Air Flow Bed technology, the ORBITER booster, and the ROTOJET spray nozzle, each contributing to the optimisation of fluidisation and coating processes. He also highlighted how the ORBITER booster, with its special design, facilitates the formation of an air flow bed, controlled air distribution, and a gentle product distribution through a spiral orbital movement. The prolonged air path, enabled by ORBITER, enhances drying efficiency by 25 per cent.
Dr Bhokare also underscored how Fluid Bed Technology has found its application in diverse areas such as MUPS, delayed/enteric release, sustained/modified
release, taste masking, micro-encapsulation, protective coating, stability enhancement, and uniform size granulation, thereby demonstrating its adaptability
and relevance.
In summary, Dr Bhokare's session provided a comprehensive overview of the potential of Fluid Bed Technology to reshape the landscape of formulation development.
Fluid Bed Technology's features like Air Flow Bed technology, ORBITER booster, and ROTOJETspray nozzle,each contribute to the optimisation of fluidisation and coating processes
WonHyun (James) Hwang, Head of Application, Asia and Middle East of Africa Biopharma, Avantor Performance Materials Korea shed light on the influence of Bakerbond Chromatography Resin on the final formulation of biopharma products. The key highlights of the event provided invaluable insights into this critical aspect of the pharma industry.
One of the takeaways was the meticulous approach Avantor takes to ensure regulatory compliance and support.
Hwang emphasised that their BAKERBOND chromatography data range and ligand information are available and included in comprehensive regulatory support files. These files are equipped with methods that facilitate rigorous testing and analysis.
The session also underscored the significance of factors that are often overlooked in formulation development.
Buffer pH and the incorporation of additives emerged as pivotal considerations. Hwang stressed that these variables can exert substantial influence over both product quality and process performance.
Intermediate product control (IPC) took center stage as a key quality control
checkpoint. Hwang explained that IPC serves as a designated measure to ensure
Ravleen Singh Khurana, MDirector, Nitika Pharmaceutical Specialities shared his insights on lubrication in oral solid dosage (OSD) formulations and emphasised the need to tailor lubrication strategies to the unique requirements of each OSD formulation.
He pointed out that each formulation possesses distinct attributes, such as brittleness, plasticity, and viscoelasticity, necessitating a deep understanding of its lubrication needs. A crucial takeaway was that the sensitivity of lubricants varies across formulations and an approach where the chosen lubricant aligns precisely with the formulation's requirements, is key.
He said that the future of lubricants will be based on resolving problems of lubrication, meeting the specific needs through customisation, offering unique
product purity and pH conductivity.
Hwang delved into the realm of process parameters, specifically addressing OBC (order of buffer concentration) and UV cut-off. The event emphasised that these parameters not only hold individual significance but also interact with each other and with process buffers.
In summary, the event illuminated the intricate relationship between Bakerbond Chromatography Resin and final biopharma formulations.
solutions for special products like effervescent tablets, developing coprocessed lubricants, offering natural lubricants for use in the organic, clean label, nutraceutical products, developments in external lubrication process, environmental sustainability and developing novel lubricants.
Khurana also emphasised that Quality by Design principles will steer the way forward. The formulation scientist's role will extend to meticulously selecting lubricants and their grades, fostering robust formulations. Thus, in the years to come, aided by advancements in inprocess monitoring, automated external lubrication, and the development of novel lubricants, formulators will be empowered to design OSD formulations with unprecedented precision, control, and reliability.
BAKERBOND chromatography data range and ligand information are provided in regulatory support files along with methods to test
Day 1 on FDD Conclave witnessed some interesting and intriguing panel discussions. One of them was on "Advancements in vaccine development: New-age FR&D techniques and next-gen delivery systems."
Expert panelists examined how cutting-edge research and formulation techniques are revolutionising vaccine development, leading to enhanced efficacy and broader accessibility during the course of this discussion. They explored next-generation delivery systems and platforms for vaccines, and shed light on their potential to enhance efficacy, safety and accessibility.
The panelists for this session were Dr Ramesh Matur, Sr VP, Head R&D, Biological E (Moderator); Dr Ajay Singh, Head - mRNA Department, Gennova Biopharmaceuticals; Dr Rajender Burki, Associate VP, R&D, Biological E; Dr Tarun Sharma, Sr VP R&D, Auro Vaccines and Dr Rajendra Lingala, VP & Head R&D, Indian Immunologicals.
The panelists shared insights on the intricacies of vaccine formulation and explained how each vaccine is meticulously tailored to combat specific diseases, setting it apart from the formulation of conventional drugs. Talking about various emerging platforms for vaccine development they highlighted the significance of stabilising the mRNA platform to democratise its potential. The experts also underscored that stability is pivotal for broader application of mRNA technology.
The discussion also covered how micro-needle patches are an advantageous method of vaccine delivery and emphasised that these patches hold immense promise, even for individuals with compromised immune systems. While acknowledging the current scalability challenges in commercial manufacturing of micro-needle patches, it was unanimously agreed that substantial progress is on the horizon. The discussion also addressed the need for vaccine design and formulation for individuals with compromised immune systems and looked at combination vaccines as a
● Formulation development of vaccines is different from the formulation development of other drugs.Everyvaccine is customised to a disease
● The wayto democratise the mRNAplatform lies in stabilisation of the formulation
● Micro needle patches are a more advantageous wayof vaccine delivery,even for immuno compromised patients
● Micro needle patches are an evolving area,especiallyin commercial manufacturing.Scalabilityis an issue currentlybut we will see significant progress in future
● Vaccines development approaches need to generate a response even in the immuno-compromised.For instance, combination vaccines can help reduce intake of aluminium in paediatric vaccines
potential solution. This approach aligns with the need to bolster immunogenicity in vulnerable populations, heralding a paradigm shift in vaccine development
strategies.
In conclusion, the discussion explored the distinctive aspects of vaccine formulation and delivery methodolo-
gies. These insights will help shape the trajectory of vaccine research and contribute to enhance global health and well-being.
Manisha Chaudhuri, Senior Technical Application Expert, Merck delved into the challenges inherent in pharma and biological product development and presented a comprehensive overview of cuttingedge solutions aimed at overcoming these obstacles. She highlighted the role of innovative excipients, predictive formulation techniques, and solubility enhancement strategies in reshaping the landscape of drug development.
She spoke on the potential of 3D printing in the production of amorphous solid dosage forms and provided insight into the strides being made in this arena, shedding light on the integration of 3D printing into the drug development process.
Speaking on viscosity reduction platforms, and challenges posed by high viscosity in formulations can impede drug
delivery and efficacy, she underscored the innovation in viscosity reduction strategies and presented novel ap-
proaches to streamline drug administration and enhance therapeutic outcomes. For instance, use of excipient
combinations to reduce protein viscosity efficiently.
Chaudhuri addressed the demand for high-dose formulations and showcased novel formulation methodologies and novel manufacturing technologies to meet the evolving needs of modern pharma and biological product development.
She also delved into the realm of continuous manufacturing and its potential to expedite production, enhance quality control, and optimise resource utilisation. She also accentuated the challenges and innovations in solid dose manufacturing.
Chaudhuri also informed the industry that Merck is building a robust foundation on novel technologies and expanding its capabilities to simulation tools and oral delivery of large molecules.
Vaibhav Datke, Sr ManagerBusiness Development at Ami Polymer gave a presentation on polymeric solutions for the pharma industry and shed light on the pivotal role that polymer solutions play within this sector. The presentation commenced by introducing the audience to Ami Polymer's offerings tailored specifically for the life sciences sector. The speaker also highlighted that the selection of appropriate polymer products holds the key to unlocking heightened productivity, minimised downtime, and improved operational efficiency.
Highlighting that polymers find widespread application in the pharma industry, serving functions ranging from drug formulation and controlled drug release to packaging materials, Datke spoke about on chemical compatibility and the need to match polymer choices with the nature of drugs being used. He elaborated on other factors as
well such as service temperature, sterilisation considerations etc in the choice of polymers. The presentation emphasised the significance of evaluating physical properties such as tensile strength, flex crack resistance, and opacity when choosing polymers for specific formulations, ensuring that the selected materials align with the intended applications.
In conclusion, Vaibhav Datke's presentation emphasised that the choice of polymer solutions within the pharma industry is a strategic move with farreaching consequences for efficiency, productivity, and overall success. Emphasising that the significance of collaborating with strategic partners who provide cutting-edge and dependable polymer solutions, he concluded that Ami Polymer can offer a comprehensive array of polymer solutions tailored to the pharma industry's unique demands.
L-R: Dr Rakesh Bhasin,VP-Formulations,Biocon (Moderator); Dr Sunil Tiwari,President R&D,Hetero Drugs; Dr SajeevChandran,VP-R&D, Lupin; Dr Abir Banerjee,VP-R&D Biotech, Bharat Serums & Vaccines; Dr Khalid Akhter Ansari,Group Head,Formulation Development,Oral solid and Parenteral Dosage Forms,Novartis; Dr Amarender ReddyDonthidi, VP& Head-R&D Injectables and Ophthalmics,Amneal Pharmaceuticals; and Dr VaibhavSihorkar,VP& Head-Developability& Formulations,Sai Life Sciences
Day of FDD Conclave 2023 saw some enlightening discussions and sessions. It commenced with a captivating panel discussion on "Evolutions and Revolutions in Drug Delivery." This discussion highlighted the potential of cutting-edge technologies and breakthroughs that are shaping the future of medicine. An esteemed panel of experts explored the latest advancements in drug delivery hold the key to patient well-being and improved health outcomes. This esteemed panel is composed of leaders and experts in this segment.
The moderator for this session was Dr Rakesh Bhasin, VP-Formulations, Biocon, and the distinguished panelists were Dr Sunil Tiwari, President R&D, Hetero Drugs; Dr Vaibhav Sihorkar, VP & Head- Developability & Formulations, Sai Life Sciences; Dr Sajeev Chandran, VP-R&D, Lupin; Dr Amarender Reddy
● Evolution platform from conventional technologyto controlled drug deliveryto device driven deliveryhas nowreached stage of target delivery
● Patient centricityand compliance are crucial for faster and meaningful evolution
● We need strategies and approaches to eliminate complexities in drug delivery
● Innovation in drug deliveryneeds to be driven bypatient centric therapeutic adherence tools that are market need driven rather than just the technologypush driven innovation
● Scaling up the R&D to production level is important
● We should focus on skilling upcoming researchers with case studies for more meaning innovations
Donthidi, VP & Head - R&D Injectables and Ophthalmics, Amneal Pharmaceuticals; Dr Abir Banerjee, VP-R&D Biotech, Bharat Serums & Vaccines; and Dr Khalid Akhter Ansari, Group Head, Formulation Development, Novartis.
The panel discussion gave an overview on the evolution of drug delivery methods from conventional methods to more precise and targeted delivery
approaches, and showcased the progress and advancements in this sphere. The panelists discussed and examined how device-guided drug delivery has helped improve accuracy. The panel stressed on the importance of keeping the patient central to all improvements in drug delivery. The conversation also revolved around strategies to simplify drug delivery complexities, and empha-
sised the need to create delivery tools and approaches that enable patient adherence to treatments. The experts unanimously agreed that innovation should be about what patients need, rather than just what technology allows. Altogether, the panel discussion showcased how drug delivery techniques are transforming how we administer treatments and revolutionising healthcare.
Sourabh Sobti, Business Development Lead at CEPI, shared his insights on the importance of Investments in vaccine delivery to ensure equitable access to vaccines and safeguard public health.
The session highlighted the need for transformative approaches and effective strategies to address the challenges in vaccine development and delivery. Sobti also spoke about the creation of comprehensive vaccine libraries targeting highrisk pathogens, such as those with pandemic potential to expedite vaccine development in times of crisis. He stressed on the importance of establishing global clinical trial and laboratory networks with predefined processes and protocols to accelerate the generation of clinical evidence concerning the safety and efficacy of vaccines, and foster a more
rapid response to emerging threats.
The session underscored the need to optimise manufacturing processes for
swift initial production and subsequent scaling of vaccines as well. Sobti said that manufacturers should leverage prior ex-
periences in scaling up production to meet heightened demand during pandemics, ensuring timely vaccine availability. He spoke on the importance of constant monitoring of global surveillance and lab networks too. He opined that vigilant surveillance helps in promptly identifying potential alert triggers, enabling swift responses to emerging infectious diseases. Such proactive measures will serve as a cornerstone of preparedness against future pandemics.
In conclusion, the session highlighted proactive approaches to address the challenges associated with increasing vaccine volumes and costs. He discussed strategies that can pave the way for a more resilient and responsive public health ecosystem, poised to effectively combat future pandemics and safeguard global well-being.
The last session at FDD Conclave 2023 was an engaging panel discussion on "Building FR&D Talent in India." This session highlighted the importance of talent building in pharma FR&D to drive advancements in drug development, and ultimately, improve healthcare outcomes for patients worldwide. The experts will also discussed how a well-nurtured talent pool plays a vital role in driving industry growth, staying competitive in a dynamic market, and addressing the ever-evolving challenges in the pharma landscape.
The moderator for this session was Viveka Roychowdhury, Editor of Express Pharma & Express Healthcare and the other esteemed panelists were Makarand Avachat, EVP-Pharma R&D, Lupin; Dr Ashok Omray, Pharma Consultant; Suresh Pareek, Angel Investor (Pharma); Vinod Arora, Principal Advisor, IGMPI and Dr Girish Jain, Pharma Consultant.
The panel discussion emphasised that organisations must empower their employees through upskilling and reskilling initiatives to foster a quality-conscious and futureready talent pool in pharma FR&D. It also highlighted that robust collaborations between industry and academia can help cultivate and retain skilled professionals in pharma research. It underscored that training programs must prioritise quality, focusing on skills crucial for the evolving landscape. The panelists stressed on quality-focused training in India, upgrading the pharma curriculum and incentivising research to nurture adept FR&D talent. The expert panelists also called for industrywide skilling efforts and rec-
Organisations should encourage and enable their employees to upskill and reskill themselves to create quality-conscious and future ready talent in pharma FR&D
We need strong and meaningful collaborations between industryand academia to build and retain talent in pharma research Training and upskilling programs in India for FR&D talent should be quality-oriented,and with a focus on skills which will be pivotal in the future
We need to upgrade pharma curriculum,nurture scientific temperament and attitudes,incentivise research and improve remuneration to build FR&D talent
Skilling and training at industrylevel is key.Pharma companies should build centres for training and skill development to enable talent building in the field of pharma research
While the pharma industryis striving to go from volume to value,we need to revamp pharma education and nurture talent which will enable the industryto grow
ommended that pharma companies should establish dedicated training centers, facilitating talent development.
Moreover, the experts accentuated the need to align pharma education with industry evolution to nurture the
talent essential for propelling the industry's transition from volume to value.
Together, they shared some
very interesting insights on fostering talent and innovation within the pharma research and development landscape.
FDD Leadership Award 2023 lauded 15 R&D leaders and gamechangers for their pivotal contributions and achievements in propelling progress in formulation development and drug delivery
Express Pharma , revived its tradition of honouring the FR&D leaders and hosted the fifth edition of FDD Leadership Awards this year. FDD Leadership Awards 2023, held in conjunction with the FDD Conclave 2023 at Novotel Airport, Hyderabad, celebrated and underscored
EXPRESS PHARMA
September 2023
the exceptional contributions of FR&D scientists in fuelling the pharma industry's progress. Cilicant was the Presenting Partner for the awards.
The event began with an entertaining and hilarious stand-up comedy act that left the audience in splits! The
laughter-filled performance was given by renowned standup comedian Sai Kiran. This act set the tone for the evening and gave a very energetic and enthusiastic start to the awards night.
Next, an address from Viveka Roychowdhury, Editor of Express Pharma high-
lighted the awards' commitment to acknowledging the role of FR&D leaders in the evolving landscape of pharma research and development. She also explained the rigorous selection process of the FDD Leadership Awards.
The awards ceremony that followed was the night's high-
light. FDD Leadership Awards 2023 recognised and honoured the accomplishments of 15 winners spanning three categories – Stalwarts, Leaders, and Rising Stars, in the field of formulation development and drug delivery.
Express Pharma also acknowledged the pivotal role of
Category: Stalwarts
✵ Dr Kishore Deo
✵ Makarand Avachat
✵ Dr Ravikumar N
✵ Subhrangshu Sengupta
Category: Leaders
✵ Dr H B Pushpalatha
✵ Manikandan Ramalingam
✵ Prasanna Kumar J
✵ Preeti Raut
✵ Dr Rajender Burki
Category: Rising Stars
✵ Dr AjaySingh.
✵ Dr Khalid Akhter Ansari
✵ Dr Prigneshkumar Patel
✵ Rajesh Rao
✵ Samarth Kumar
✵ VijayKumar Kuvar
the distinguished jury for FDD Leadership Awards –Vinod Arora, Principal Advisor at the Institute of Good Manufacturing Practices India (IGMPI), Suresh Pareek, Angel Investor (Pharma), Dr Ashok Omray, Pharma Consultant and Dr Girish Jain, Pharma Consultant, in selecting the winners. Their collective expertise ensured that the awards echoed the industry's pursuit of excellence. The jury members also joined Ms Viveka Roychowdhury, Editor, Express Pharma and Manish Jain MD and CEO, Cilicant in presenting the award to the winners.
The event ended on a jubilant note, followed by a networking gala dinner which provided an opportunity for the attendees to connect and exchange ideas.
Express Pharma's FDD Leadership Awards 2023 reaffirmed the industry's commitment to pushing boundaries and fostering innovation in pharma.
By introducing cost-effective drugs for critical illness by leveraging path-breaking manufacturing technologies,India could emerge as the de-facto pharma manufacturing hub and be the harbinger of equitable access for biopharmaceuticals in the country,opines
Dr Himanshu Gadgil, CEO,Enzene Biosciences (a subsidiary of Alkem Laboratories)According to the World Health Organisation (WHO), an estimated two billion people across the world do not have access to essential medicines for life threatening diseases like cancer, AIDS and even autoimmune diseases like Type 1 diabetes. In India, this situation is far more appalling, with an estimated 65 per cent of the population lacking access to potentially life-saving drugs and health-related expenditure constituting about 63 per cent of total out-of-pocket household expenses. In this context, it is important to improve access to essential medicines in our country by taking measures aimed at reducing the cost of drug production, introducing more cost-effective options to expensive biopharma products and improving their distribution and availability across urban and rural centres alike.
An important part of achieving Universal Health Coverage, providing access to affordable and quality-assured essential medicines has been a focal point of the Indian government since the past few decades. In a bid to resolve both physical and financial restrictions inhibiting equitable access to quality medicines, theJan Aushadhischeme was launched in 2008 and envisaged the setting up of dedicatedJanaushadhi Kendras to provide quality generic medicines at capped prices for the general public. This
scheme which was significantly revamped and renamed as thePradhan
Mantri Bhartiya Janausadhi Pariyojana(PMBJP) in 2015, now has 9000+ such centres across the country that stock around 1,800 essential drugs and 285 odd surgical items. To help financially weak citizens gain access to affordable healthcare, thePradhan
Mantri Jan Arogya Yojana (PMJAY) was launched in 2018, providing about 500 million Indians with a ?5 lakh family health insurance cover that include coverage for 1,400 medical procedures as well as critical diseases like prostate cancer. However, despite these efforts, there is still a lot to be done in terms of improving all dimensions of access to medicines, especially the affordability of criti-
cal drugs used to treat serious illnesses and maintaining international-level quality standards while exploring more cost-effective manufacturing and distribution techniques.
Although India is the world’s largest supplier of generic medicines, earning it the sobriquet of being the ‘Pharmacy of the World’, there is a clear need to invest in technologies of the future, pursue fully integrated drug development and innovate disruptive manufacturing processes that can slash the overall cost of production.
Take for example expensive biopharma products like
innovator biologics, which are complex medicines produced using living cells or organisms that are used for precise and targeted treatment of cancer, autoimmune diseases, metabolic disorders and even hormone deficiencies. By developing good manufacturing practice (GMP) plants with continuous manufacturing processes, domestic biotech players can produce quality biologics at lower costs, which in turn can translate into lower medical expenses for lakhs of patients in the country. In fact, this can lay the foundation for a disruptive and affordable manufacturing platform that can bring to market innovative immunotherapy treatments for chronic or life-threatening ailments. Considering that the capitalised R&D cost for launching a new biopharma product has been doubling every ten years, India could even establish itself as a global biopharmaceutical hub by virtue of introducing more efficient process development methods that are eventually scaled up and applied in the manufacturing of such critical biopharma products.
With the passing of the Biologics Price Competition and Innovation (BPCI) Act of 2009, the US Food and Drug Administration (FDA) created a shorter approval path for biological products that are highly similar to already approved biologics. Known as biosimilars, these biopharma
products are highly similar to innovator products and have no clinically meaningful dissimilarities, especially in terms of efficacy, safety or quality. However, due to significantly lower spends on R&D and shorter lead times from development to launch stage, these biosimilars are proving to be more affordable when treating maladies such as rheumatoid arthritis, osteoporosis, colorectal cancer, Type II diabetes and even bone tumours.
Biosimilars possess a significant advantage over innovator drugs as they can transform into superior products by utilising manufacturing technologies that offer inherent reproducibility and increased cost benefits. This enables them to establish themselves as upgraded alternatives. Indian pharma players could play a key role in positioning biosimilars as superior products to costly biologics. What’s more, with many key biologics scheduled to lose patent protection in this decade, Indian pharmaceutical companies ought to seize this opportunity and leverage innovative technologies to introduce quality and way more affordable biosimilars in the domestic as well as global markets. Not only will this precipitate into lower treatment costs and ensure equitable biopharma access for Indian patients, but could also peg Indian pharma companies to become global market leaders in the biosimilars segment and effect a major change in drug pricing standards.
Sterile & Non-Sterile 400mm(16") Sterile & Non-Sterile 300mm(12")
Frame: Tested To Withstand 40 Autoclave Cycles
Sterile 600mm(24") ISO Class 4 &
Lens: Tested To Withstand 35 Autoclave Cycles
Nowavailable!
Best-in-classosmolalityperformance, designedwithyouinmind.
HIGHLIGHTEDFEATURES:
Offersthewidestrangeofosmolalitytesting(0–4000mOsm/kgH2O)
Supports21CFRpart11,GMPandEUAnnex11compliance
MeetsPharmacopeiaosmolalitytestingguidelines
3Leveluseraccessandpasswordprotection
Storage:unlimiteddatastorageforaccess
Audittrail:Preserveunlimitedresultsandevents
Databasebackup,protectsyourdatawithautomaticormanualbackup
No.127,BussaUdyogBhavan,TokershiJivrajRoad,SewriWest,Mumbai-400015, Maharashtra,Landline:+91022-24166630Mobile:+919833286615
L.B.Bohle's BRC series combines high product capacity with minimal material loss.In contrast to competitive hydraulic systems,force generation is purely electromechanical
Dry granulation, also known as roller compaction, has become a widely used granulation technology in recent years. It has a wide range of applications. Powders are compacted between rotating rollers to form a flake.
The flakes are crushed into granules with the desired particle size distribution using a sieve and sieve inserts. The pressed and dried granules are used in various ways in the pharmaceutical industry. Granules can be used as starting materials, intermediates, dosage forms for immediate preparation, and granules for ingestion.
Compared to the starting material, compacted granules have a higher bulk density and a larger particle size. As a result, the granules have better flow properties, which means better processing. Granulation also reduces dust and fines. This results in little or no material loss and low dust exposure. Agglomerates pre-compacted by dry granulation are easier to tablet than powders. All of the properties of compacted granules support the tableting goal of producing a tablet that is as uniform as possible.
Unlike wet granulation, which is a continuous process, dry granulation is a well-established process in the production of solids. Dry granulation is particularly suitable for moisturesensitive pharmaceutical substances. A key advantage of dry granulation is that no energy is required for drying and solvent recovery. This is a decisive argument in favour of dry granulation, especially in times of high energy costs.
Dry granulators are distinguished by the arrangement of the rolls. There are systems with horizontal, vertical, and inclined rolls.
L.B. Bohle (Germany) uses
horizontal rolls for compaction. This arrangement has the advantage that the screws are better ventilated, and the flakes are discharged over a short
distance.
Other features of dry granulators include the width, diameter, and surface finish of the compaction rolls.
The systems also differ in whether the gap is fixed or variable. Dry granulators with a variable gap are preferred. This is the only way to ensure constant pellet porosity at a constant pressing force and thus reproducible flake production. During continuous measurement of the gap distance, a comparison is made between the actual and target values. The goal is to always maintain a parallel gap between the rolls during the process so that the exiting flake has identical properties across the entire width.
In addition, the screw speed is linked to the gap adjustment in a control loop. As a result, when the nip opens, less material is conveyed by the screw into the nip, allowing the nip to close again. The automatic control produces flakes of
defined thickness and porosity. Electromechanical drive
L.B. Bohle's BRC series combines high product capacity with minimal material loss. In contrast to competitive hydraulic systems, force generation is purely electromechanical. This ensures consistent scab characteristics. The electromechanical drive eliminates the disadvantages of hydraulic control, such as aging of the oil and control valves, as well as temperature fluctuations and contamination of the oil. This high-precision process is further supported by the use of force-measuring sensors located inside the force adjustment to directly measure the press force. The results are more accurate than in hydraulic systems where the values are
usually calculated.
The BRC controls the compaction force and flake thickness in a very innovative way, producing uniform compaction of the material over a production range of < 1 - 400 kg/h. At the same time, the ingeniousinnovative machine design facilitates handling and shortens the assembly procedure.
The hygienic design and the standard integrated washing nozzles guarantee an effective WIP process with residue-free removal of the product. In addition, with its functional GMP-compliant design and the possibility of PAT tool implementation, the compactor meets the requirements of the ‘Quality by Design’ concept.
In addition to the compaction force, the size reduction step has a significant influence on the final particle size of the granules. The Bohle Conical Turbo Screen Mill BTS and its screen inserts ensure gentle size reduction of the flakes into granules with the desired particle size distribution - even at high material throughputs. At the same time, each BRC can be converted to an alternative rotary screen BRS in a matter of minutes, allowing it to be flexibly adapted to process and flake requirements.
L.B. Bohle has been producing its BRC range since 2012, and over the years the number of products manufactured with the BRC has increased significantly worldwide, as this granulation method is very economical. Dry pelletizing is a continuous process, achieves high throughput, requires little space and energy, and has the advantage of not requiring granulating fluids and drying equipment.
Roller compaction can be used for a wide range of products. Many generic drugs are dry granulated, such as ibuprofen, metformin, blood pressure medications and antibiotics. Increasingly, new products are being developed using dry granulation from the outset.
Although roller compaction is a continuous manufacturing process suitable for both large and small batch sizes, almost all
products are currently manufactured in batches.
Changeover: Due to its innovative design (ergonomic height, no ladder or framework needed) the changeover is time-saving. Changeovers after cleaning and reassembling can be done in 30 minutes. Competitors’ systems require cleaning and assembly times of up to eight hours. At the BRC only minimum tools are necessary (at roller and scrapper) all other components are designed for tool-less changeover.
A major advantage of roller compactors is their small footprint and flexible integration into the production process.
L.B. Bohle has already installed numerous BRC series machines
in various production scenarios for batch and continuous production. Solutions can be found as stand-alone systems, wall-mounted installations, applications on platforms as well as over several floors, interlinked systems, and containment applications.
Especially in new products the active pharmaceutical ingredients (APIs) are becoming increasingly more potent. In some markets, the segment for highpotency active pharmaceutical ingredients (HPAIs) is growing in the double-digit range, especially driven by oncology medication.
In addition to requirements set by manufacturing guidelines, it is essential that the product is safe for the machine
operator and, of course, for the patient. As a result, L.B. Bohle is faced with new challenges in all toxicity classes in which customers want to use plants and processes.
So, a special version for containment applications for containment level OEB 5 is shown as an example. The containment version includes:
◆ Integrated isolator unit in the compacting unit with corresponding vacuum monitoring
◆ Glove box with safety request for flake removal
◆ Containment port for flake sample collection
◆ Containment port underneath the sieve unit for the removal of granules
◆ Convenient access as no complete isolator unit is installed around the entire compactor
◆ Residue-free removal of prod-
uct with integrated WIP equipment (WIP is also integrated into the standard version).
Just in May, a BRC 100 was sold to India. After a test run at the headquarters in Germany, one of the leading pharmaceutical companies was so convinced by the product that an installation in India was possible in a very short time.
Contact L.B. Bohle’s Indian team for trials in India at its Innovation Center or in Germany.
Contact Parag Radia Director, L.B. Bohle India
p.radia@lbbohle.com +91 987 959 8784
L.B.Bohle has been producing its BRC range since 2012,and over the years the number of products manufactured with the BRC has increased significantly worldwide,as this granulation method is very economical.Dry pelletizing is a continuous process,achieves high throughput,requires little space and energy,and has the advantage of not requiring granulating fluids and drying equipment
When purchasing machines specifically designed to process eye drops, Jubilant Pharma had two requirements: Flexibility and compact design. As a CDMO, Jubilant impresses customers with high efficiency and precise weighing results because ultimately, this leads to higher yields per batch.
For this project, a fourheaded OPTIMA VFVM 10000 was used to implement the specific customer requirements. Jubilant, a CDMO in the ophthalmology industry pays great attention to high performance, high dosing accuracy, and flexibility in terms of varying viscosities and container types. The VFVM10000 offers Jubilant the opportunity to process eye drop bottles in combination with a variety of closure types including preservative free technology.
Jubilant has opted for two filling systems that are permanently installed in the machine. A disposable product path with peristaltic pumps is used as standard. The vertical arrangement of the four peristaltic pumps saves a considerable amount of space.
Since ophthalmic drugs are sometimes viscous, rotary pumps can also be used for dosing viscous products with high precision. Both pump types operate in four-digit versions. The OPTIMA VFVM achieves an output of up to 12,000 containers per hour.
Jubilant uses containers that are consistent in weight. The format-related weights are stored in the checkweigher control system; the gross tare weighing provides efficient 100 per cent fill weight control with no loss of performance. Containers with gross weights outside the defined tolerances are rejected. The metering parameters are continuously adjusted
based on the fill weights registered and analysed by the control system. This ensures consistently high precision filling performance, giving CDMOs like Jubilant “weighty” arguments in its favor.
The production process with the OPTIMA VFVM10000 starts with the sorting of the containers and feeding them into the machine with a centrifuge. The correctly oriented bottles are transferred to the filling and closing station via a star wheel and segment wheel configuration to the linear walking beam transport system.
After the filling process is completed the containers are transferred to the closing station with its specifically designed closing technology, depending on container type. Conventional plastic bottles are fitted with a dropper for dispensing the eye drops. The droppers are transported in a four-lane configuration and inserted into the container with pick & place technology. Optional available: Nitrogen gassing to minimise oxygen in the container.
Twist closure caps are placed via a pre-capping station followed by a final cap torque station.This ensures that always the correct torque force is used and therefore containers are always easy to open. The final torque station also measures removal torque as requested or on a sampling basis.
Once the closing inspection is completed, the finished containers are transferred to a double tray loading configuration at the discharge of the machine. Containers that do not meet the inspection criteria are rejected. The trays, containing only “good” vials, are removed at the end of the line.
During the implementation
phase, Jubilant chose also to process specific types of preservative free OSD technology. The technology consists of flexible bottles and pre-assembled, multi-part closures with integrated droppers and caps. For easy use, OSD caps are opened by tearing off a plastic tab on the cap.
Additional processing of the preservative free OSD technology was made possible and optimised by making design changes to the OPTIMA VFVM. Now, Jubilant Pharma has the flexibility to easily switch between preservative free OSD or conventional screw closures with dedicated
change parts – like a typical format change. For instance, the format parts are located in the bottle feeding centrifuge and the conveyor for the screw caps, erecting the bottles. Sorting, feeding, and pushing the specific OSD closures into the flexible bottles are also carried out by simply using format parts, without time-consuming conversions. A special holder has been developed for pressing in the caps. This ensures stability when pressing the closures into the vials.
Keypoint: On-site service In addition to being compact and flexible, high filling accu-
racy was very important for Jubilant. This was demonstrated in the FAT/SAT with an OEE (Overall Equipment Efficiency) exceeding 90 per cent efficiency. Direct service from a North American subsidiary was another key deciding factor for Jubilant Pharma when awarding the contract. Optima Machinery Corporation has now two locations in the US and the Jubilant account will be handled by Optima Machinery Corporation, Green Bay (WI). One additional challenge was the limited space available at Jubilant’s facility. The VFVM’s compact design with
stacked peristaltic pump dosing system resolves this issue. The system also had to be dismantled and reassembled on site in order to bring it into the production room.
At Jubilant, the OPTIMA VFVM is operated in a Grade B cleanroom environment, therefore the system features Active Open RABS with integrated laminar flow unit above the filling area and additional laminar flow units outside the machine guarding, extending from the door opening zone to the room walls. In total, nine laminar flow modules are operating in the room.
Over the course of the project, the Jubilant Pharma project team had the opportunity to be on site at Optima in Schwäbisch Hall, Germany, for the key milestones such as the mock-up study, the design review, and the machine factory acceptance test (FAT), despite the restrictions during the Covid-19 pandemic. By October 2021, the system passed the customer's site acceptance test (SAT) at Jubilant in Canada. After qualification, it was commissioned for commercial manufacturing projects for pharmaceutical companies in the ophthalmology sector.
METTLER TOLEDO has developed the XPR Automatic Balance,with both automated and manual weighing and dispensing options,which sets the new standard for weighing and dispensing in the laboratory
In analytical R&D or QA/QC laboratories, accurate standard preparation is crucial for the quality of the analytical results, which in turn has an enormous effect on laboratory efficiency. Analytical R&D laboratories are responsible for development, optimisation, and validation of various methods used to analyse their products. Chromatographic techniques like HPLC or GC are commonly applied in analytical R&D and QC labs for identifying, quantifying and purifying the individual components of the mixture. The purity, concentration and composition of these components has a major influence on the quality of the final product, its efficiency, safety, shelf-life, and many other important product features.
To run a chromatographic analysis, many identical samples must be prepared and run through the whole analytical method to see whether the necessary details can be determined. HPLC and GC methods employ the use of known reference substances as standards, to gain traceable results from the evaluation. Therefore, reference standard preparation is a common daily task in most analytical laboratories.
The quality of each analysis largely depends on the quality of the sample and standard preparation, and this in turn on the quality of the dispensing and weighing processes. Any error in this early stage will be propagated downstream in the analysis. Errors caused by deviations from specification – known as out-of-tolerance (OOT) or outof-specification (OOS) errorsand the resulting rework time
and costs should be avoided. OOS investigations are costly and time consuming. Sample preparation is reportedly the most time-consuming, labor-intensive and error-prone part of the workflow, with some 50 per cent of OOS errors attributed to either sample processing steps or human error. Many of these errors can be eliminated by using automation, which reduces the variability in sample preparation. As sample preparation can take up to 60 per cent of the time in an analytical laboratory, the weighing technology needs to deliver accurate and reliable results very quickly.
Solution: XPR Automatic Balance with LabX™ Software
METTLER TOLEDO has developed the XPR Automatic Balance, with both automated and manual weighing and dispensing options, which sets the new standard for weighing and dispensing in the laboratory. It offers intelligent functions, such as automated calculation of amount of solvent required to achieve desired concentration, to support accurate sample and standard solution preparation in an automated way. XPR Automatic Balance con-
nected to LabX software enables standard solution preparation with automatic data processing. Metadata are automatically captured and saved in a centralised database. You can start your digital dosing task with just one click, directly on your balance terminal. LabX guides you step-by-step through your SOP with clear onscreen instructions. All calculations are performed automatically and transcription errors are eliminated. LabX integrates fully with chromatography software and sends your weighing
results directly to where the weight values are required for subsequent chromatographic analyses. In this way, LabX offers a seamless data flow during the entire analysis workflow, guarantees ahigh degree of process security and supports you also with the fulfilment of the FDA ALCOA+ requirements for data integrity.
For more information about METTLER TOLEDO , contect:
www.mt.com/xpr-automatic sales.sales@mt.com
1800 22 8884 & 1800 1028 460
XPR Automatic Balance offers intelligent functions,such as automated calculation of amount of solvent required to achieve desired concentration, to support accurate sample and standard solution preparation in an automated way
Gloves serve more than just the purpose of protecting us from potential health and safety hazards. They play a pivotal role in safeguarding processes against contamination and other risks. The importance of selecting the appropriate nitrile glove for your task cannot be overemphasised. We will delve into the key factors to consider when choosing nitrile gloves and explore how the glove colour also holds significance.
The foundation of wearing suitable gloves lies in understanding your environment and the tasks you'll be undertaking. In environments such as foodservice, cleanrooms, laboratories, and manufacturing, hand protection is not only vital but often mandatory. Laboratory employees and cleanroom workers frequently rely on latex and nitrile exam gloves. Even selecting the right size is crucial to prevent cross-contamination and exposure to hazardous substances.
Interestingly, despite the importance of glove selection, many individuals are not adequately trained in this regard. A senior Scientific Category Leader at Kimberly-Clark Professional notes that the proper choice of gloves is seldom addressed in scientific training. Ill-fitting gloves, whether too loose or too tight, can compromise safety. Gloves that are too big risk being accidentally pulled off, exposing hands to hazardous materials, while overly tight gloves limit dexterity. Alongside proper fit, here are five essential considerations when choosing the right glove:
1.Fit and comfort: Consult
the manufacturer for accurate glove sizing and note features like beaded cuffs that prevent roll-down.
2.Chemical and biohazard protection: Ensure the glove's material and type offer adequate protection against the specific hazardous materials you'll encounter.
3.Tear and puncture protection: Nitrile and latex gloves, meeting ASTM requirements, are recommended for their strength and durability.
4.Dexterity and tactile sensitivity: Gloves with textured fingertips enhance grip on both wet and dry objects.
5.Allergy protection: Nitrile gloves, being latex-free, are an
excellent choice for those with latex allergies.
The world of gloves is surprisingly passionate. People tend to be highly particular about the gloves they use due to the significance of hand protection.
While latex is a familiar material, allergies to latex proteins are common. Nitrile gloves, composed of a synthetic nonallergenic byproduct of oil and latex, have gained popularity as a latex-free alternative. One distinct advantage of nitrile gloves is their tear visibility. Unlike latex gloves, nitrile gloves tear visibly, providing a
clear indication of potential contamination risks.
Gloves must meet rigorous Food and Drug Administration (FDA) standards before they can be sold. Meeting the FDA's minimum requirements for pinholes (AQL 2.5) is crucial for gloves to be considered medical-grade. Furthermore, medical exam gloves undergo a battery of tests before earning the designation of "exam" gloves.
Food service professionals must also ensure their gloves meet FDA standards for safe food handling.
In terms of effectiveness, the color of disposable gloves might have minimal impact, but specific environments may have colour preferences for practical or aesthetic reasons.
1.Cleanroom environments: White gloves are commonly favoured in cleanrooms for their visibility, facilitating the detection of contaminants. Nonetheless, it's important to note that glove color additives might react with cleanroom products and processes.
2.Laboratory settings: Labs often require coloured gloves to differentiate between different lab areas, reducing the risk of cross-contamination.
Selecting the right nitrile glove is a decision that should not be taken lightly. By considering factors like fit, protection, tear resistance, and tactile sensitivity, you can ensure optimal hand safety and efficiency in various working environments. Moreover, staying informed about glove materials, FDA requirements, and color preferences empowers you to make well-informed choices that contribute to a safer and more productive work environment.
Learn more about how Kimberly-Clark Professional® can help with glove selection on: www.kcprofessional.co.in.
Contact
West, North & East India: Bharatkumar Mistri, bharat.mistri@kcc.com, +91 9825053582
South India: Ravi Kumar C., ravikumar.c@kcc.com, +91 9391330669
Selecting the right nitrile glove is a decision that should not be taken lightly.By considering factors like fit,protection,tear resistance,and tactile sensitivity,you can ensure optimal hand safety and efficiency in various working environments
In this study the effect of different lubricants on acetaminophen formulation was studied. Acetaminophen API blended with PROSOLVSMCC HD 90 for 15 min and afterwards blended with sieved lubricants for three minutes.Different lubricants like PRUV,magnesium stearate,stearic acid,and sodium stearate are used
Lubricants are a very important part of the tablet formulation. During the tableting process, powder particles are forced to rearrange under the increasing compression force. Lubricants influence this rearrangement and bonding process depending on their molecular structure. After compression, the tablet has to be ejected by the lower punch of the tablet press. The lubricant is also important in this step of the process because it inhibits sticking between the tablet and the punch, which can lead to damage and stop the machines. Finally, the lubricant influences the dissolution and disintegration times and, thus, the quality attributes of the tablets. Due to their importance in formulating tablets, there are a lot of lubricants on the market. Most of them are characterised by a long fatty acid chain which imparts hydrophobicity to the lubricant. Examples for such commonly used lubricants are magnesium stearate, sodium stearate, stearic acid, and sodium stearyl fumarate (PRUV®). These lubricants were utilised in this study about the influence of lubricants on tableting characteristics [1][2]
In this study the effect of
Tablet Hardness/Compactability
In this studythe effect of different lubricant on tablet hardness was evaluated.
Lubrication efficiency
In this studythe effect of lubrication efficiencyof different lubricants was evaluated.
Observation: The kind of lubricant used had a significant influence on the hardness of the tablets.While tablet lubricated with stearic acid resulted in the highest tablet hardness,those made from magnesium stearate exhibited the lowest hardness.Tablets made from PRUVshows intermediate hardness.
different lubricants on Acetaminophen formulation was studied. Acetaminophen API blended with PROSOLV SMCC HD 90 for 15 minutes and afterwards blended with sieved lubricants for three minutes. Different lubricants like PRUV, Magnesium stearate, stearic acid, and sodium stearate are used. Tablets were compressed to 800 mg tablet weight [3][4] Magnesium stearate is most widely used lubricant in the pharma industry. Hence PRUV® is compared with Magnesium stearate in the following section. [5][6]
PRUV® helps to avoid API
incompatibilities and enhances API stability. With a few exceptions, PRUV® can be applied to any formulation for lubrication, particularly those in which API stability or tablet taste is compromised
Lubricants: PRUV® (Sodium Stearyl Fumarate),Magnesium Stearate,Stearic acid,Sodium stearate).
Observation: As for compactibility,a similar trend observed in the ejection forces.The tablets lubricated with stearic acid showed the highest ejection forces,while magnesium stearate was found on the lower end of the ejection force spectrum.Tablets made with PRUVexhibited the same lowejection forces as compare to magnesium stearate.
due to magnesium stearate. Magnesium cation (Mg2+) is electrophilic, it interacts with the free electrons of an API and forms insoluble salts. This is one of the many causes of API incompatibility with magnesium stearate. [4]
Beyond tablet lubrication properties of PRUV®:
It shows:
◆ Improved API stability
◆ Superior blending properties
◆ Faster disintegration
◆ Faster dissolution times
The choice of lubricant can influence the quality of the tablets as well as the dissolution rates. Since APIs tend to be less water soluble and difficult to compress, choosing the right lubricants continues to become an even more important task.
Most commonly available lubricants are very hydrophobic and thus increase dissolution times significantly. In such cases, a less hydrophobic lubricant can help to decrease the dissolution times well as increase the API release.
PRUV® Sodium StearylThe choice of lubricant can influence the quality of the tablets as well as the dissolution rates.Since APIs tend to be less water soluble and difficult to compress,choosing the right lubricants continues to become an even more important task
In this studythe effect of different lubricant on disintegration time was evaluated.
In this studythe effect of different lubricants on dissolution behavior was evaluated.
Observation: Tablets lubricated with magnesium stearate needed byfar the longest time for disintegration.All other tablets were found to have disintegration times in the same range.
Fumarate complies with Ph.Eur., NF and JPE. It have the ideal particle size and specific surface area to offer a perfect balance between all functionality aspects. It is the preferred choice over magnesium stearate in terms of improving disintegration time and dissolution.
Furthermore, different particle sizes are available, which help to fine tune tablet
formulation resulting in the desired dissolution profiles.
References
1. Jinjiang Li, Yongmei Wu. Lubricants in Pharmaceutical Solid Dosage Forms. Lubricants 2014, 2, 21-43.
2. Sonja Bauhuber, Maria Launer, Gernot warnke.Influence of Different Lubricants on Tableting Characteristics and Dissolution Behavior. Influence of Different Lubricants on
❒ Express Pharma accepts editorial material for regular columns and from pre-approved contributors / columnists.
❒ Express Pharma has a strict non-tolerance policy of plagiarism and will blacklist all authors found to have used/refered to previously published material in any form,without giving due credit in the industry-accepted format.All authors have to declare that the article/column is an original piece of work and if not,they will bear the onus of taking permission for re-publishing in Express Pharma.
❒ Express Pharma's prime audience is senior management and pharma professionals in the industry.Editorial material addressing this audience would be given preference.
❒ The articles should cover technology and policy trends and business related discussions.
❒ Articles for columns should talk about concepts or trends without being too company or product specific.
❒ Article length for regular columns: Between 1200 - 1500 words.These should be accompanied by diagrams,illustrations,tables
Observation: Tablets containing magnesium stearate showed byfar the slowest dissolution rates.Sodium stearate and stearic acid lubricated tablets released the API much faster.The faster drug release was observed for tablets lubricated with PRUV®
Tableting Characteristics and Dissolution Behavior- JRS Pharma
https://www.jrspharma.com/ph arma_en/technicalinfo/brochures/technical-info/lubricants.php
3. Hölzer, A.W, Sjögren, J. Evaluation of sodium stearyl fumarate as a tablet lubricant. Int. J. Pharm.1979, 2, 145–153.
4. JRS Pharma PRUV® | Sodium Stearyl Fumarate- JRS Pharma
https://www.jrspharma.com/ph arma_en/products-services/excipients/lubricants/pruv.php
5. Rowe, R.C., Sheskey, P.J.; Quinn, M.E. (2009) Handbook of Pharmaceutical Excipients. 6th Edition, Pharmaceutical Press, 667-669.
6. Leon Lachman, Herbert A. Lieberman, Joseph L. Kanig. The theory and Practice of Industrial Pharmacy, Varghese publication house, 3rd edition, 1990, 123-144.
QR Code:
Scan the QR code for more details regarding PRUV® from JRS Pharma.
AUTHOR
Prashant Bhangdiya
Business Development Manager – Pharma Rettenmaier India (JRS) Prashant.bhangdiya@jrsindia.com
and photographs,wherever relevant.
❒ We welcome information on new products and services introduced by your organisation for our various sections: Pharma Ally (News, Products,Value Add),Pharma Packaging and Pharma Technology Review sections.Related photographs and brochures must accompany the information.
❒ Besides the regular columns,each issue will have a special focus on a specific topic of relevance to the Indian market.
❒ In e-mail communications,avoid large document attachments (above 1MB) as far as possible.
❒ Articles may be edited for brevity,style,and relevance.
❒ Do specify name,designation,company name,department and e-mail address for feedback,in the article.
❒ We encourage authors to send their photograph.Preferably in colour,postcard size and with a good contrast.
Email your contribution to: The Editor, Express Pharma, Business Publications Division, The Indian Express (P) Ltd, Mafatlal Centre,7th floor, Ramnath Goenka Marg, Nariman Point,Mumbai 400021
viveka.r@expressindia.com
viveka.roy3@gmail.com
Insufficient planning,in the early stages of scale-up,results in an inefficient process at best, or validation failures leading to serious market delays at worst. Using cGMP grade reagents earlier in the transition to large-scale commercial manufacturing makes for a seamless transition — maintaining quality and viability while avoiding additional costs, potential process redevelopment and lost production time.
When you identify suppliers of higher quality reagents ahead of time — chemicals that have been extensively tested and documented — you gain heightened supply chain security and assurance of regulatory compliance. Use cGMP raw materials during development to:
◆ Minimize risk of contamination or aberrant results due to impurities
◆ Provide material traceability to support regulatory compliance.
◆ Eliminate requalification of material due to unavailable grade and quantity of material after transfer
◆ Ensure product consistency that meets intended specifications.
Current Good Manufacturing Practice (cGMP) regulations are set regionally, based on guidelines developed by organizations including the International Conference on Harmonization (ICH)
Pharmaceutical Inspection Convention/Pharmaceutical Inspection Co-operation Scheme (PIC/S), and regulatory agencies. They focus on preventing cross contamination and keeping environmental contaminants out of the product, thereby simultaneously protecting the end user and the product. There is no cGMP certification; they are standards to maintain quality and purity characteristics in pharma development.
The reagents needed for clinical manufacturing must meet additional regulatory and testing requirements to validate sterility, consistency, and efficacy. This includes more quality control testing of initial raw materials, more in-depth documentation to show manufacturing control and validated manufacturing and cleaning processes to minimize risk of
product failure and subsequently, patient safety concerns due to variability or contamination.
KEYCHALLENGES
Lot release testing
◆ Research use only (RUO) raw materials (and equipment) do not include comprehensive—and timeconsuming—QC testing, specifically for endotoxins and particulates leading to patient safety concerns.
Sterility validation
◆ With the change to cGMP products, this is not a ‘one anddone’ test validation; dose audits must be done regularly to prove sterility.
Clinical comparability studies
◆ Time-consuming clinical comparability studies to prove the raw material changes do not alter the final product. By making the change early, you get less chance of variants or atypicals and that validation will fail.
◆ Regulatory and quality systems and history of supporting customers with regulatory submissions.
◆ Quality audits with Rx-360 available to license
◆ Certified ISO9001 and ISO13485 quality systems
◆ Animal origin-free or EMA/410/01 compliant materials
◆ Sterility validation per ANSI/AAMI/ISO11137 (VDmax25)
◆ Sterile barrier shelf-life validation per ANSI/AAMI/
ISO11607
◆ BPOG standardized extractables testing protocol
◆ Endotoxin USP <85> and particulate USP <788> lot release testing
◆ Lot-to-lot consistency and comprehensive supportive testing
◆ Custom specifications and performance characteristics available
Documentation: Lackof documentation support can lead to delays or rejections
Documentation serves as a record that a supplier’s manufacturing facility, processes, and operators are fully qualified. It is not a box to be checked, but should be a systematic approach to acquiring, analyzing, storing, and disseminating information related to products, manufacturing processes, and components (ICHQ10).
KEYCHALLENGES
Process validation
◆ Supporting documentation should be in place for scale-up. If you wait, you lose time in getting necessary documentation.
Traceability
◆ Raw materials at this level must be documented and traceable. This ensures any issues with end product or process can be adequately investigated and ruled out
Certified quality systems
◆ Documentation is not a stand-alone deliverable. These change with the transition from RUO to cGMP, as do corrective/preventative actions and documentation requirements.
WHATWE OFFER
◆ Certificates of Conformance, Quality or Analysis are available with SDS documents online.
◆ Equipment Cleaning and Use Record
◆ Records of Raw Materials, Intermediates, API Labeling and Packaging Materials
◆ Master Production Instructions (Master Production and Control Records)
◆ Batch Production Records (Batch Production and Control Records and Review); our knowledge of regional differences facilitates regulatory compliance
◆ Laboratory Control Records
◆ Supply chain statements
◆ Rigorous documentation of deviations along with root cause analysis and corrective/preventative actions
Supply: Reagents that are unavailable cause disruptive changes and/or stockouts
Collaborative planning, smart forecasting and sales and operation planning are needed to keep your cGMP materials in stock to hit your manufacturing goals. Establishing a comprehensive supply chain strategy, as well as a robust management of change program, as early as possible mitigates risk.
KEYCHALLENGES
WHATWE OFFER
Change management
◆ Change controls become burdensome in full cGMP systems; materials that worked for one workflow may not work for another
Limited raw materials list
◆ Key to build a diverse and large approved raw material parts list ahead of time,
so a stable supply chain is in place with qualified secondary suppliers in case a reagent is discontinued
New production/distribution sites
◆ Moving manufacturing can disrupt a previously secure supply of cGMP reagents; facilities must be certified. Changing the source of supply of critical raw materials requires adherence to formal change control system.
Supplier auditing
◆ A system for evaluating suppliers of critical materials as necessary; all cGMP production materials must be traceable.
WHATWE OFFER
◆ Collaborative planning, forecasting and replenishment (CPFR):we provide service level reports on assurance of supply through our Critical Materials Careteam
◆ A formal Management of Change (MOC) program and change notification services for supply consistency and transparency
◆ Certified global cGMP and
cGDP facilities; with local field-based support on three continents.
◆ Supplier auditing and integrity provides proactive, risk-based audits that enable us to understand the capabilities of new suppliers and collaborate effectively to promptly address CAPA if needed.
◆ Large portfolio of quality premium products and chemicals
Whychoose Avantor®?
Trust chemicals and excipients from Avantor® to help you reach the market faster with new biologics. With our global network of cGMP and cGDP manufacturing facilities, customer-centric quality programs, comprehensive management of change system and in-depth industry expertise, Avantor® can help you improve your production process performance, increase product yield, and comply with regulatory requirements.
Our J.T.Baker® brand of chemicals, founded in 1904,has set the global standard for quality and purity in product manufacturing.
Due to the crucial necessity and its direct impact on human health and welfare, Pharma is probably the most important and critical sector among others. As a consequence of which, it becomes essential to store pharmaceuticals, vaccines, laboratory samples or units of blood at the right temperatures to ensure that they remain effective and that quality is maintained. Another reason for the Pharma division to ensure safety measures & controlled environment is stringent regulations and inspection of the facilities. This elementary need for climate control can only be ensured with right data monitoring systems. Testo being a market leader in testing & measurement sector provides the best in class data loggers and data monitoring systems for the Pharma division.
Pharma goods must be stored well in every situation as any deviation in the ambient temperature or humidity values may lead to deteriorated quality of the product. Testodata loggerscan be used to test the optimum conditions for specific products or surroundings.
Temperature & humidity data loggers are often used in Pharma industries to monitor the conditions in which drugs, medicines, vaccines are kept. Not only storage, but during the transit of goods, testo transport data loggers are useful to measure the transport conditions. The range of data loggers is very extensive. A temperature & humidity logger such as 174 T guarantees continuous monitoring in a storage or warehouse. Also, data loggers with multi channels for connecting external sensors & thermocouples, like testo 176 are available for en-
suring secured work process in labs.
These data loggers are also critical for production quality assurance where the temperature has to be frequently checked at various points in production processes. Using thermocouple probes, data loggers can also record data in the kinds of extreme temperature ranges. The probe's fast response also contributes in the validation processes and quality standard optimization in QA units & clean room applications. These instruments are the most convenient and
pocket friendly solution for all Pharma application areas.
The testo Saveris 2 WiFi data logger system is the simple, flexible and reliable solution to humidity and temperature monitoring in cold storage area like blood banks. This innovative monitoring system is ideal for high product quality & eliminates manual work of reading out or documenting measurement data. With a secure online storage of all readings in Testo Cloud the data can be managed and analyzed online by the user via smart phone, tablet or PC anywhere
and anytime. In case of crises and deviations, it is provided with an alarm by e-mail, or optionally by SMS.
Another important and crucial application of a Pharma industry involvesvalidation ofsterilization and freeze-drying processes. Not only that, validating cleaning and disinfecting equipment is equally necessary. In order to allow a seamless operating procedure, the validation process and the documentation work must be as efficient and smooth as possible which could be easily achieved with testo 190 data logger solution that has inn ovative data loggers for temperature & humidity, smart software and accessories.
Testo offerings are majorly related to the data security along with comprehensive analysis & evaluation of all the recorded measurement data. Testo data
loggers ensure continuous monitoring of temperature and relative humidity of pharmaceutical products during production, storage or transit of goods. Real time data monitoring is important for the quality of Pharma goods and also enables the supplier to improve the life of the goods. Transportation trucks, warehouses, cold rooms etc. can now be remotely monitored via Testo data loggers & data monitoring systems. Our data loggers are EN 12830 and 21 CFR Part 11 compliant which ensure complete documentation of parameters, be it humidity, temperature or absolute pressure. They come with professional software where the data recorded cannot be modified and the audits can be easily complied with.
Testo also has an established state-of-the-art NABL accredited service & calibration LAB in accordance with the standardISO/IEC 17025:2017, that takes care of the after sales support locally from Pune. Testo service & calibration facility is highly cost effective as it delivers international standards very conveniently within a week’s time. Instruments of any brand/make can be calibrated and serviced locally maintaining necessary standards.
The accredited parameters include Humidity, Pressure, Absolute Pressure, Contact Type Temperature, Non-Contact Type Temperature (Infra Red Thermometer, Thermal Imager). In fact, ours is the First and Only Lab in India to get NABL Accreditation for Dew Point Temperature as well.
For more details, login to our website www.testo.com or write back to us on info@testo.in
Enteric coating constitutes a strategy for the modified release of drugs incorporated in orally administered dosage forms whose primary objective is to guarantee the stability of the drug in aggressive stomach conditions and guarantee its release in the digestive tract. Shin-Etsu offers cellulose based enteric polymers which differ in functional substitutions on HPMC backbonehydroxypropyl methylcellulose phthalate (HPMCP), hydroxypropyl methylcellulose acetate succinate (HPMCAS). The chemical structure of HPMCP is a monophthalic acid ester of hypromellose (hydroxypropyl methylcellulose), and the threshold pH value for rapid disintegration of HPMCP can be controlled by varying the phthalyl content. Two types of HPMCP grades with difference in pH-solubilities, HP-55 and HP-50, are available. Additionally, HP-55S, a special type of HP-55, which is distinguished by its higher molecular weight, greater film strength and higher acid resistance properties is available for enteric coating application in MUPS formulations. A suitable grade of HPMCP for a particular purpose should be selected in accordance with each preparation. In this article we would like to focus on application of hypromellose phthalate in rabeprazole delayed release formulation.
The main challenge in the formulation is to prevent rabeprazole degradation upon exposure to acidic environment or moisture. In order to prevent acid degradation of rabeprazole in gastro intestinal tract, tablets should be enteric coated to prevent its exposure to gastric acid.
Formulation
Core tablet of rabeprazole sodium was formulated with incorporation of an alkalizer-light magnesium oxide to maintain alkaline environment around drug. Granulation was performed with low-substituted hydroxypropyl cellulose (L-HPC)
NBD-020 as a disintegrant cum binder using isopropyl alcohol as a granulating fluid. Core tablets of rabeprazole were seal coated with Pharmacoat® 606 (Hypromellose 2910, 6 mPas) to create a barrier between drug and acidic enteric polymer. Further enteric coating was performed with Hypromellose phthalate (HP-50) to optimize the drug release in desired medium. Tablet samples were removed after 8% weight gain for dissolution test. Rabeprazole DR tablets were subjected to dissolution testing as per Indian Pharmacopoeia in 900mL, hydrochloric acid 0.1N for first 2 hours followed by 900mL, phosphate buffer pH 7.4 for next one hour. Impurity profile of related
substance of rabeprazole was also performed. Stability study was conducted for 3 months at 25°C/60%RH and at 40°C/75% RH in HDPE bottle.
Conclusions
Rabeprazole delayed release tablets were developed using HPMCP HP-50 (Hypromellose Phthalate) with recommendation at 8% w/w polymer gain. The formulations as well as
process parameters for the coating process were optimized. The developed formulation exhibited no significant changes in physical parameters, drug release behaviour and impurity profile even after three months stability study.
Note: For more info, please contact us pharmaindia@ setylosein.com or visit https://www.metolose.jp/en/
LISTOFPRODUCTS OFFERED FROM SHIN-ETSU
Shin-Etsu product Generic name Major applications
Nilesh B Mahajan,Technical Manager,Shin-Etsu Chemicals,India informs that his company offers application specific selection of suitable enteric polymers (HPMCPand HPMCAS) and grades TABLET1:
PHARMACOAT® Hypromellose 2910 Film coating,binder,solid dispersion,capsule shell
METOLOSE® Methyl cellulose and Hypromellose Viscositymodifier,binder
METOLOSE® SR Hypromellose 2208
Sustained release matrixtablets
L-HPC Lowsubstituted hydroxypropyl cellulose Binder,disintegrant,anti-capping
HPMCP Hypromellose Phthalate Enteric coating,solid dispersion
SHIN-ETSU AQOAT® Hypromellose Acetate Succinate Enteric coating,solid dispersion
SMART-EX® Co-processed material ODT,MUPS
Gandhi AutomationsIndia’s No.1 Entrance Automation and Loading BayEquipment Company offers High Speed Doors
High Speed Doors designed and manufactured by Gandhi
Automations are sturdy, dependable and are the ideal solution for medium and large entrances. The doors are manufactured with European collaboration and technology with innovative and creative engineering.
Fast moving functional and reliable doors are needed in industrial and commercial contexts. Gandhi designed and manufactured High Speed Doors are versatile and solid
ensuring long-lasting reliability. The modular structure of the curtains, assembled and joined by anodized aluminium extrusions, provides for a wide range of polyester sections available in a variety of colours. Wide, full-width window panels ensure a safer traffic and allow more light in. Their fast and easy replacement, in case of accidental tearing, saves money and time. The alternating metal tubular structure there inserted ensures high wind-resistance.
Prime High Speed Doors are the ideal solution for internal and external entrances and effectively operate in any situation, even when strong winds
are blowing and in rooms with high volume traffic. Sturdy and dependable, Prime is the intelligent door for medium and large entrances.
High Speed Doors for external entrance are equipped with spring steel wind lock in curtain pocket that ensures silent door travel, higher wind loads and curtain stability.
High Speed Door - Prime Reset
It is a unique High Speed SelfRepairing Door with the latest technology that prevents downtime of the door system. In case, the curtain is impacted accidentally it will cause the curtain to move out of the
guides without damage. The movement of the door is designed in such a way it can be recovered with a simple opening and closing operation.
Gandhi Automations manufactures doors of the highest quality that meet the issue for greater flexibility desired by clients. High Speed Self-Repairing Door in PVC is the most suitable solution in the field industries, it lowers the time of transition from one facility to another, avoiding any human error which can cause damage to the High Speed Door and all this can be achieved due to the innovative ANTI CRASH SYSTEM.
Gandhi Automations provides
a world class product with great security.
Below are the features of self-repairing high speed doors offered by Gandhi Automations:-
◆ Flexible and self-repairing door
◆ Functional, safe, quick and resistant
◆ Innovative anti-crash system
◆ Can be equipped with PVC vision windows
◆ Self-lubricating maintenance free guide
◆ Smooth and silent opening and closing
◆ Protects traction unit, enables rapid wiring and safety photocell
◆ Flexible curtain in self-extinguishing material
◆ Self-resetting without intervention
◆ Quickly back to operation
◆ Control panel designed for an intensive continuous service
For further details contact:
Gandhi Automations
Chawda Commercial CentreLink Road, Malad (W) Mumbai – 400064, India
Off: +91 22 66720200 / 66720300(200 Lines)
Fax: +91 22 66720201
Email: sales@geapl.co.in
Website: www.geapl.co.in
Prime High Speed Doors are the ideal solution for internal and external entrances and effectively operate in any situation,even when strong winds are blowing and in rooms with high volume traffic
Virosil Pharma has proved to be effective in controlling aerial bacteria and fungus present in sterile rooms.The area becomes completely sterile within 60 minutes of spraying without causing any irritation to the eyes,nose and skin - unlike conventionally used formulations
In the past years, the pharma and healthcare industry has witnessed tremendous growth and there have been tie-ups with a number of multinationals for production and R&D facilities to be nurtured in India. Organisations are applying for ISO standards and upgrading themselves to the latest norms related to health and hygiene.
Microbial contamination and pollution play a significant role in the pharmaceutical industries. Control of microbes has always been the biggest challenge to these industries. A load of microbes are present in areas such as production, storage/packaging, R&D, Q.A/Q.C., filling etc. They are present everywhere in the air, surface, water, instruments, linens etc.
Hence the disinfectant used should be so precise that it should not only take care of the microbial contamination but also be user and eco-friendly. Virosil Pharma meets all the required standards for the pharmaceutical industry.
Sanosil Biotech, a Mumbaibased company, has launched a range of multipurpose disinfectants which are eco-friendly, chlorine-free and completely biodegradable and have applications in the pharma and healthcare industry as well as in the food processing industry.
It is manufactured in India in technical collaboration with SANOSIL AG of Switzerland.
SANOSIL AG in Switzerland is the patent holder and has joint venture agreements in more than 15 countries such as France, Italy, Spain, Holland, Norway, South Africa, Australia, Saudi Arabia, Oman, the UAE, etc. The product is being used in various countries by reputed institutions and has been thoroughly tested under
strict regulations imposed by European Health bodies.
Virosil Pharma is a multicomponent fumigant and disinfectant. The oxidizing agent used is hydrogen peroxide, which is bonded with stabilizing agents to form a complex solution. A long-lasting effect is ensured by the addition of silver, which acts as a catalyst in trace amounts. The bactericidal effect of silver is based on the fact that the monovalent silver
ion Ag+ binds very firmly to bacterial proteins by a covalent or co-ordinate bond, and thus inactivates or precipitates these.
◆ Its effectiveness against bacteria, viruses, amoebae, fungi and algae; i.e. its extremely wide range of application makes it easy to handle for the end user; i.e. only one product is needed, where so far 2, 3 or various products were necessary.
◆ Owing to the good stability of the product, a long storage
a=samplesfromclass100environmentsshouldnormallyyieldno microbiologicalcontaminants
ADVANTAGES
#Eco- friendly- It is totallybiodegradable since (H2O2) breaks down into water & oxygen
#Chlorine free
#Non-toxic (no irritation to skin or eyes
#No effect on pH
#Non carcinogenic and non mutagenic
#Excellentlyrinseable with no remains
PROPERTIES
#Can easilybe dosed
# Does not foam
# Decomposes into water and oxygen
# It is excellentlyrinseable with no remains
# Treats anyother material with consideration
time can be guaranteed. As the product remains stable at high water/air temperatures, and as its effectiveness is even increased at high temperatures.
◆ Due to its long-term effectiveness and pronounced characteristics to prevent recontamination, this product is perfectly suited for disinfection of drinking water and wells.
◆ Virosil Pharma is ecologically harmless. Its principal constituent - hydrogen peroxide - does not pollute waste wa-
ter, because it breaks down into water and oxygen (H2O and O2), i.e. it produces no noxious by-products.
◆ The two basic substances (H2O2 and Ag) enhance their advantages (*synergism). The bactericidal effect comes into action quicker and more intensively than if either substance was used on its own.
Fumigation is one of the most
important factors associated with pharma industries, it plays a vital role in maintaining the sterility of areas and is directly related to production.
Sanosil Biotech is the first company to pioneer the novel concept of eco-friendly fumigation. The company has great respect for human health and the environment. The CEO, Dev Gupta, an MBA from the Bentley Graduate School of Business, Boston, has been actively marketing the brand nationally. According to Gupta, "Virosil Pharma has simplified the lives of so many people who work in the pharmaceutical industry as they are guaranteed sterility with the minimum risk exposure". As there was a high risk to the staff involved in the use of Formaldehyde/Glutraldehyde for sterilization and disinfection.
Owing to the stringent integrated micro contamination control and biosafety requirements, it is desirable to have micro-contamination control procedures and methods that could be monitored, evaluated and assessed periodically, which are convenient, cost-effective and safe.
A glimpse at the standards put down by various would monitoring agencies would help an individual or an organization help decide on choosing the most appropriate control procedure/methods. The important microbial limits which have been prescribed by various agencies is as follows:
To meet those requirements aerial disinfection (fumigation) with formaldehyde was the most convenient method. With the regulatory having restricted the use of formaldehyde and also putting into place the monitoring levels of formaldehyde after fumigation makes it a procedure with its own limitations.
Formaldehyde is a known carcinogen (IARC & NTP). Formalin is toxic by inhalation, toxic if swallowed, may be fatal if swallowed, causes eye burns, may cause blindness, strong sensitizer, causes irritation to skin, eyes, and respiratory tract. Repeated or prolonged exposure increases the cancer risk.
Eco-friendly,Non-toxic
Room gets sterilized within 1 hour after fumigation
Requires no de-fumigation
Person can be present during fumigation
Highlytoxic
Requires overnight fumigation
Requires de-fumigation
Causes skin,eye irritation even after next dayof fumigation
Virosil Pharma has been a direct alternative to Formalin Fumigation. Virosil Pharma has proved to be effective in controlling aerial bacteria and fungus present in sterile rooms. The area becomes completely sterile within 60 minutes of spraying without causing any irritation to the eyes, nose and skin - unlike conventionally used formulations. Virosil Pharma can even be successfully used in AHU which are responsible for optimal and steady air exchange in production facility, of which the ducts, air shafts, humidificator, filters, etc. are often contaminated with loads of bacterial and bio-films.
The main aim of Virosil Pharma is to increase productivity by cutting down disinfection time while at the same time providing a totally microbe-free environment.
Virosil Pharma is also very effective in disinfection of all critical surfaces that come in contact with pharma products. There is no requirement to rewash equipment and surfaces disinfected with Virosil Pharma since it is H2O2 based and decomposes into water and oxygen.
Virosil Pharma has been tested by several reputed and renowned institutions in India with respect to its disinfection and fumigation applications in Pharmaceutical Industry
Because of all these factors, Virosil Pharma has attained maximum satisfaction of the customers in controlling the microbial contamination in their respective applications. The introduction of an ecofriendly, non-carcinogenic and totally biodegradable versatile product, like Virosil Pharma,
has not only brought an end to the era of conventional biocides but has completely solved the disinfection requirements which these healthcare industries were prone to.
Sanosil Biotech is marketing this disinfectant under the 'Virosil Pharma' brand name and is targeting the entire industrial belt of India. The com-
pany has already set up a distribution and infrastructure network having establishments in Maharashtra, M.P., Hyderabad, Chennai and Delhi.