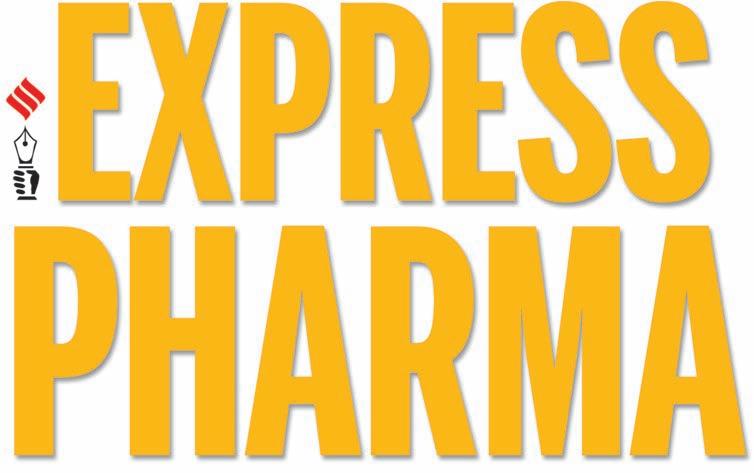
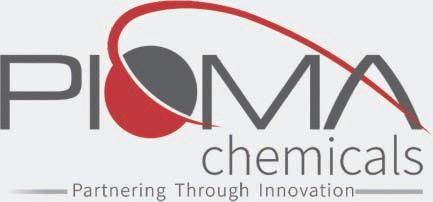
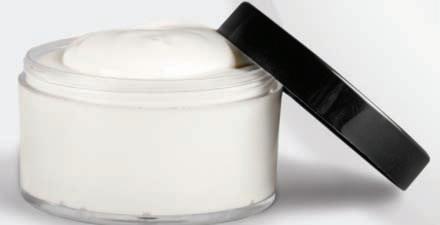
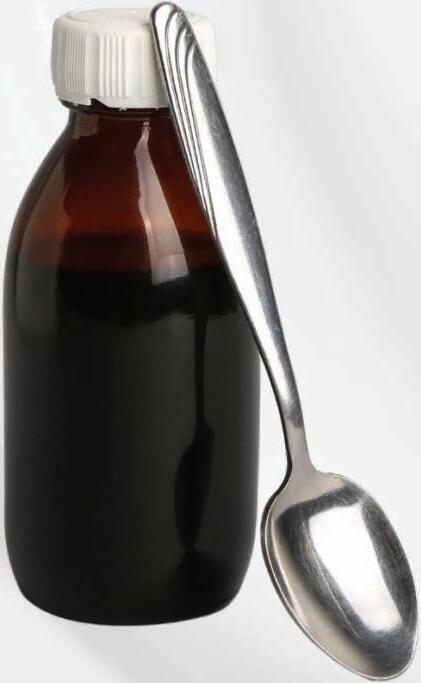
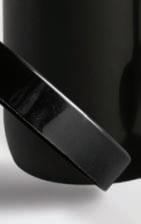
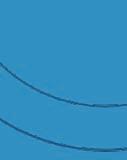

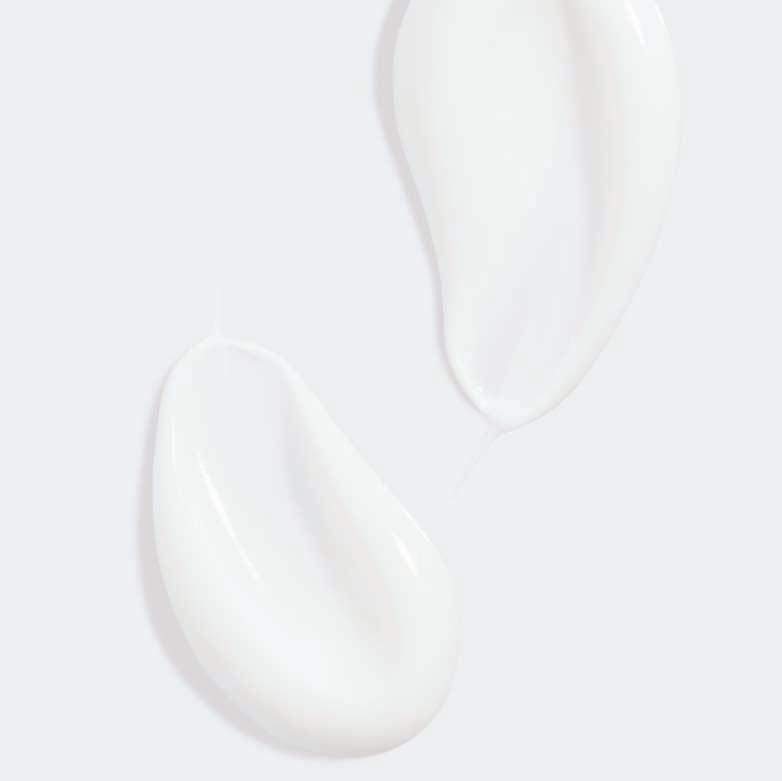
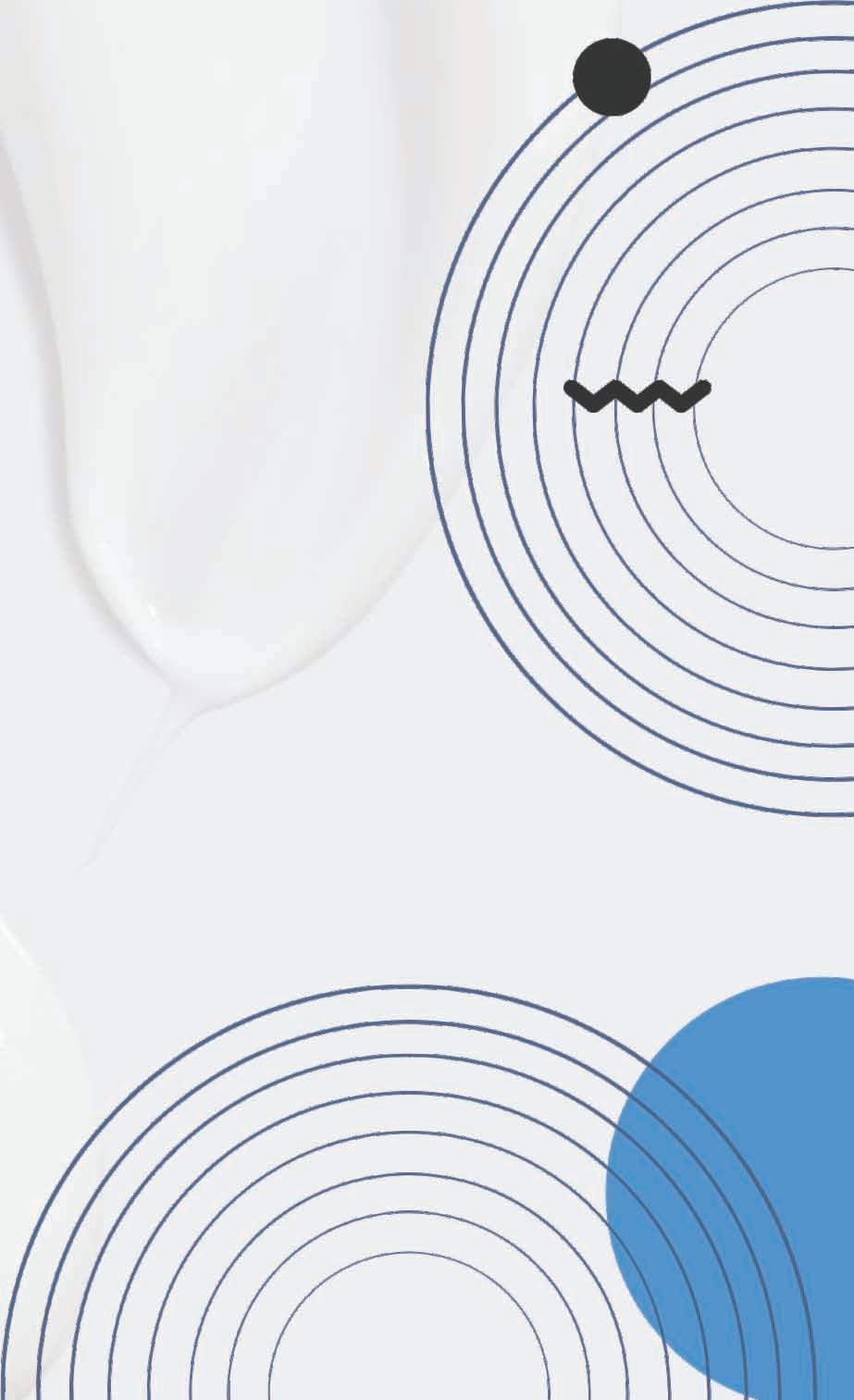
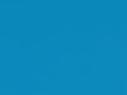
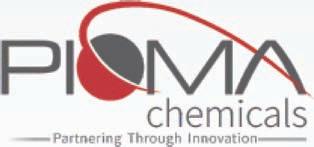
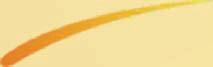

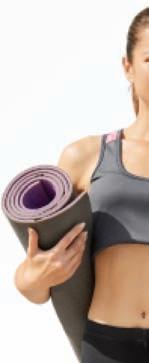
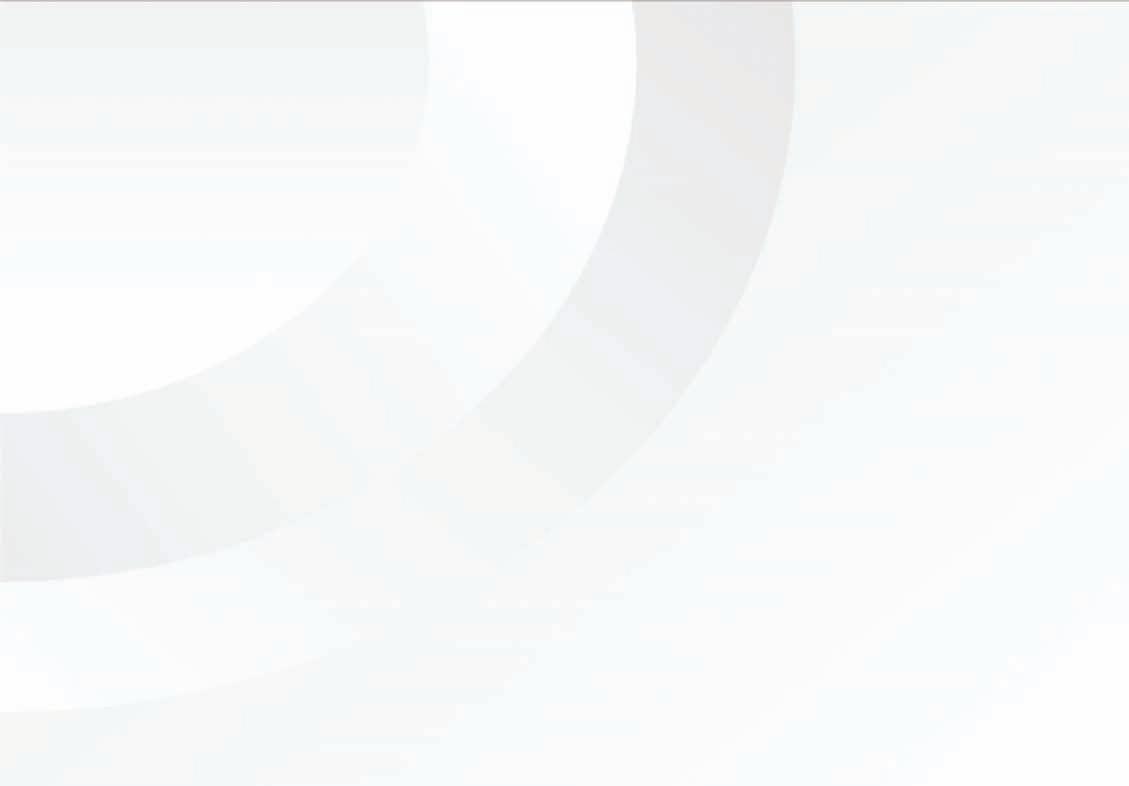
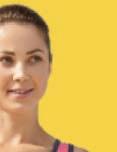
NoBitterAfterTaste
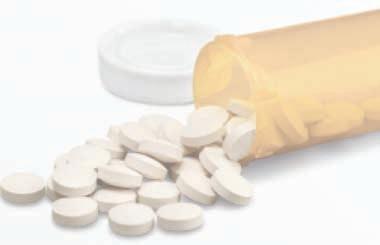


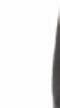
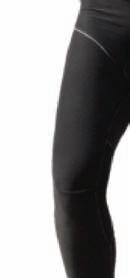
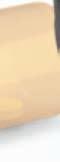
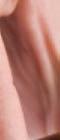
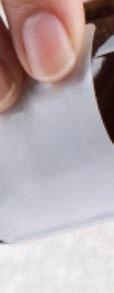
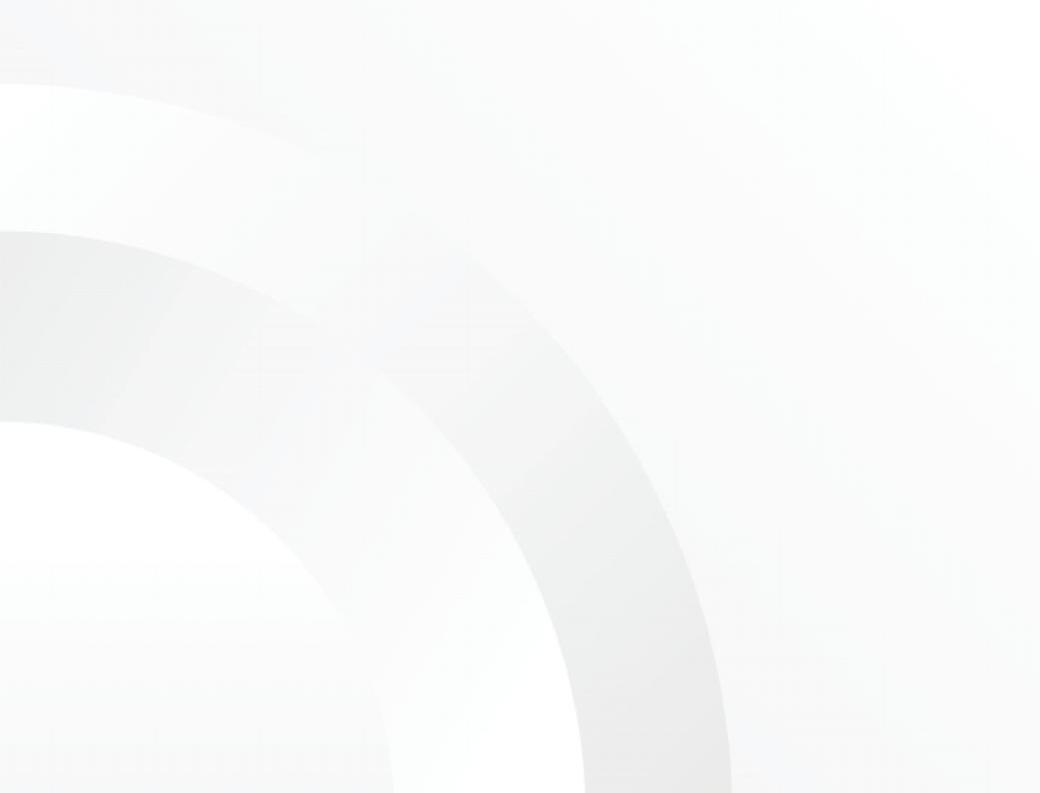
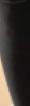

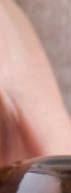
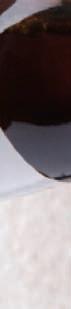
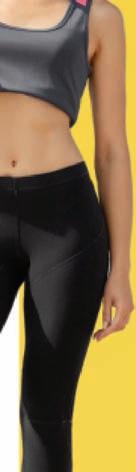
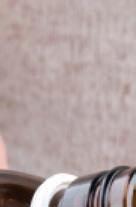








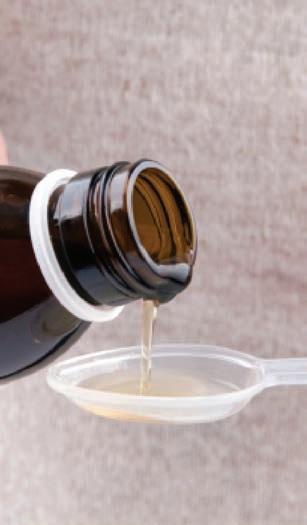
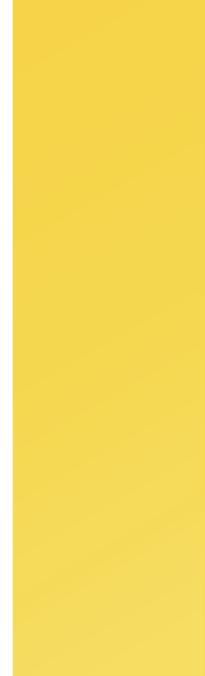
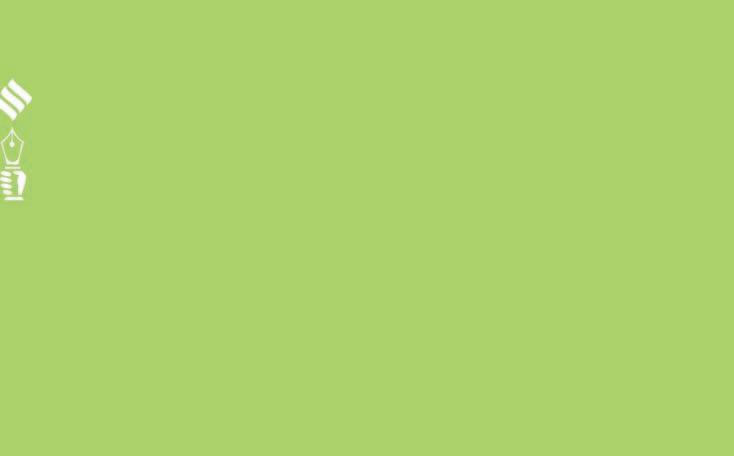
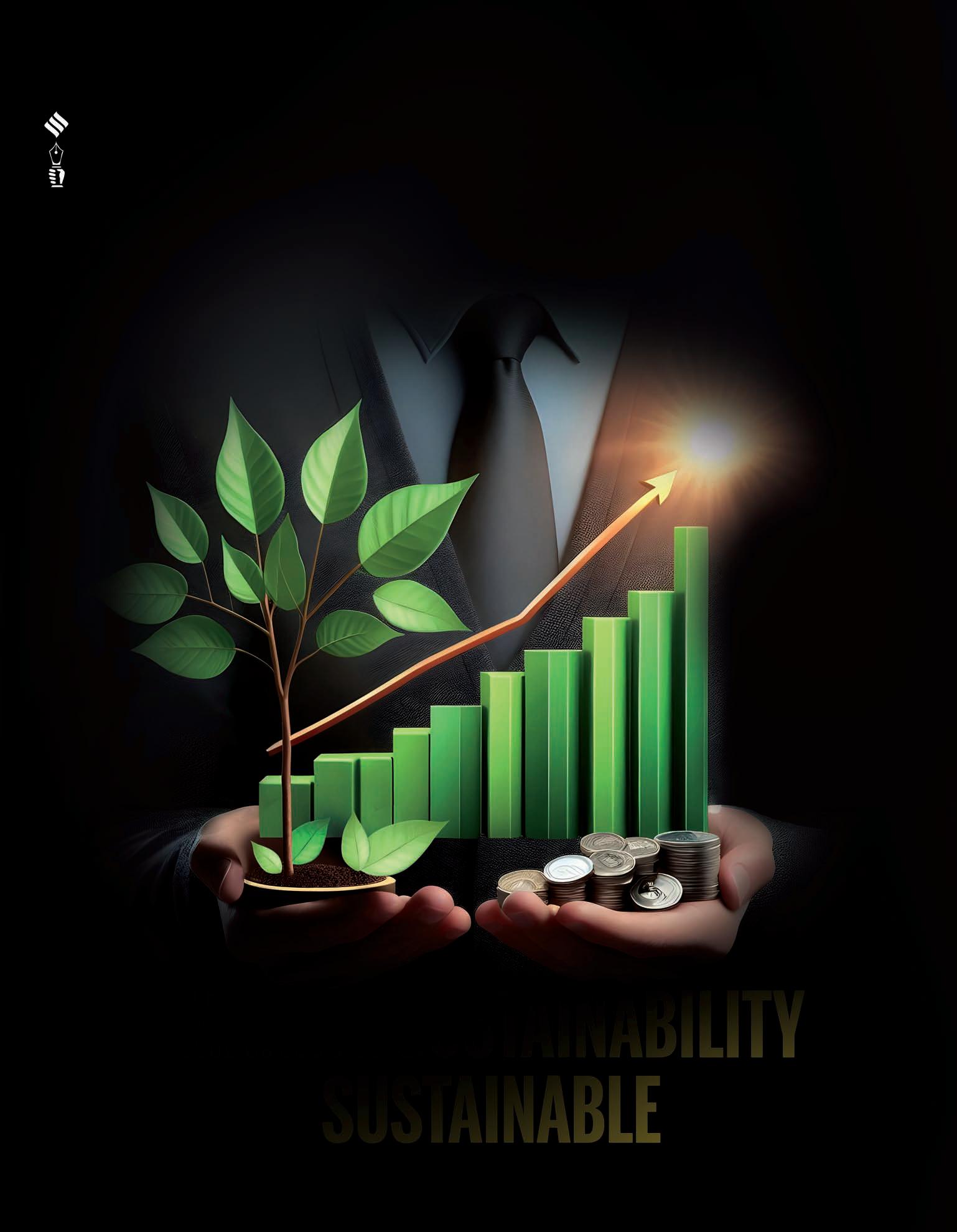
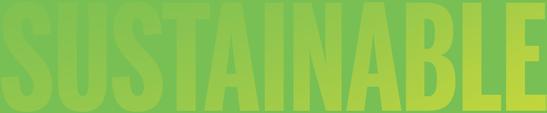

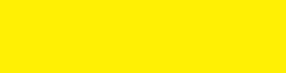

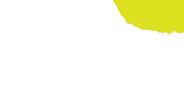

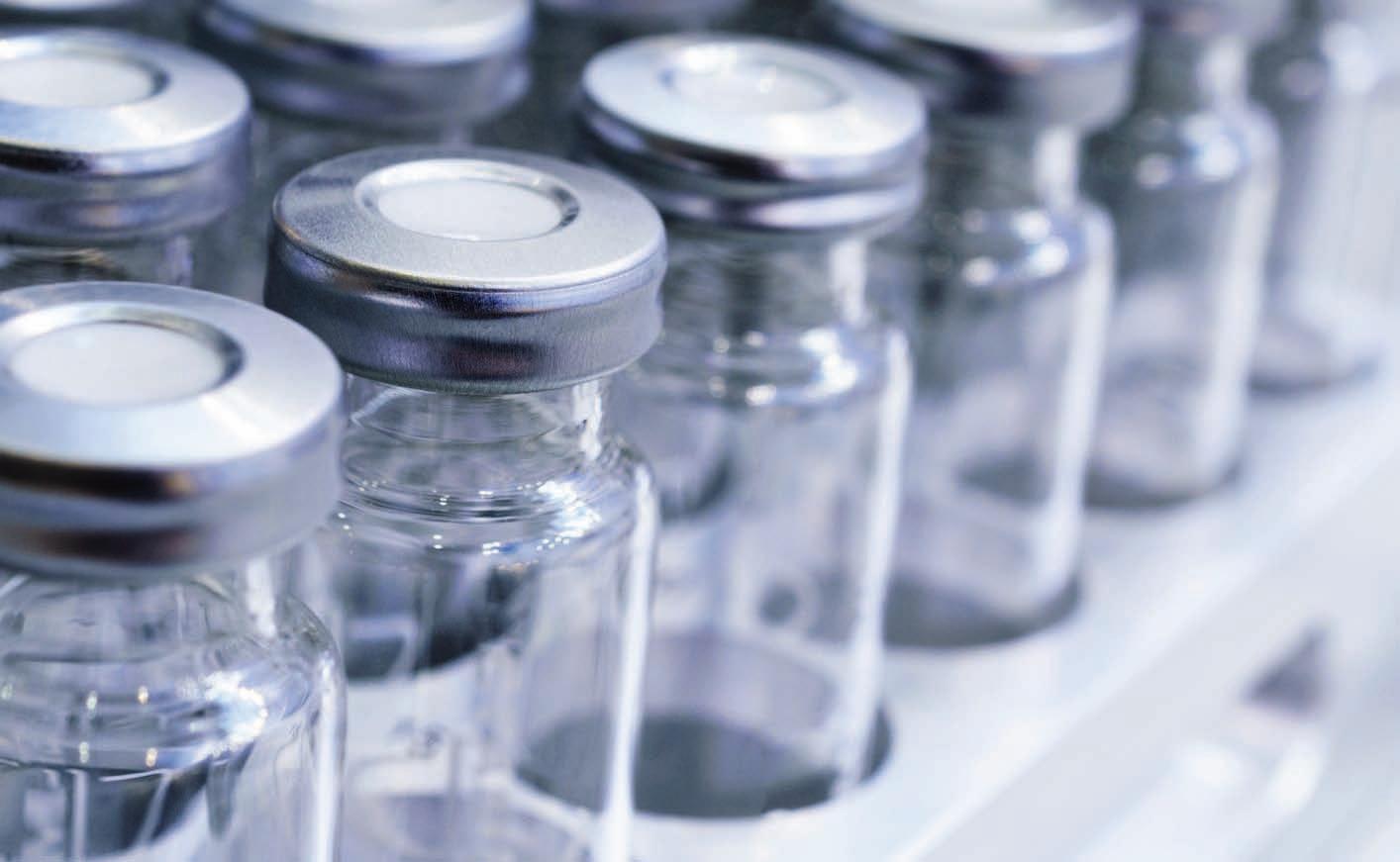
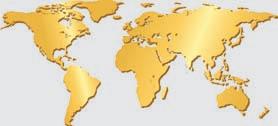
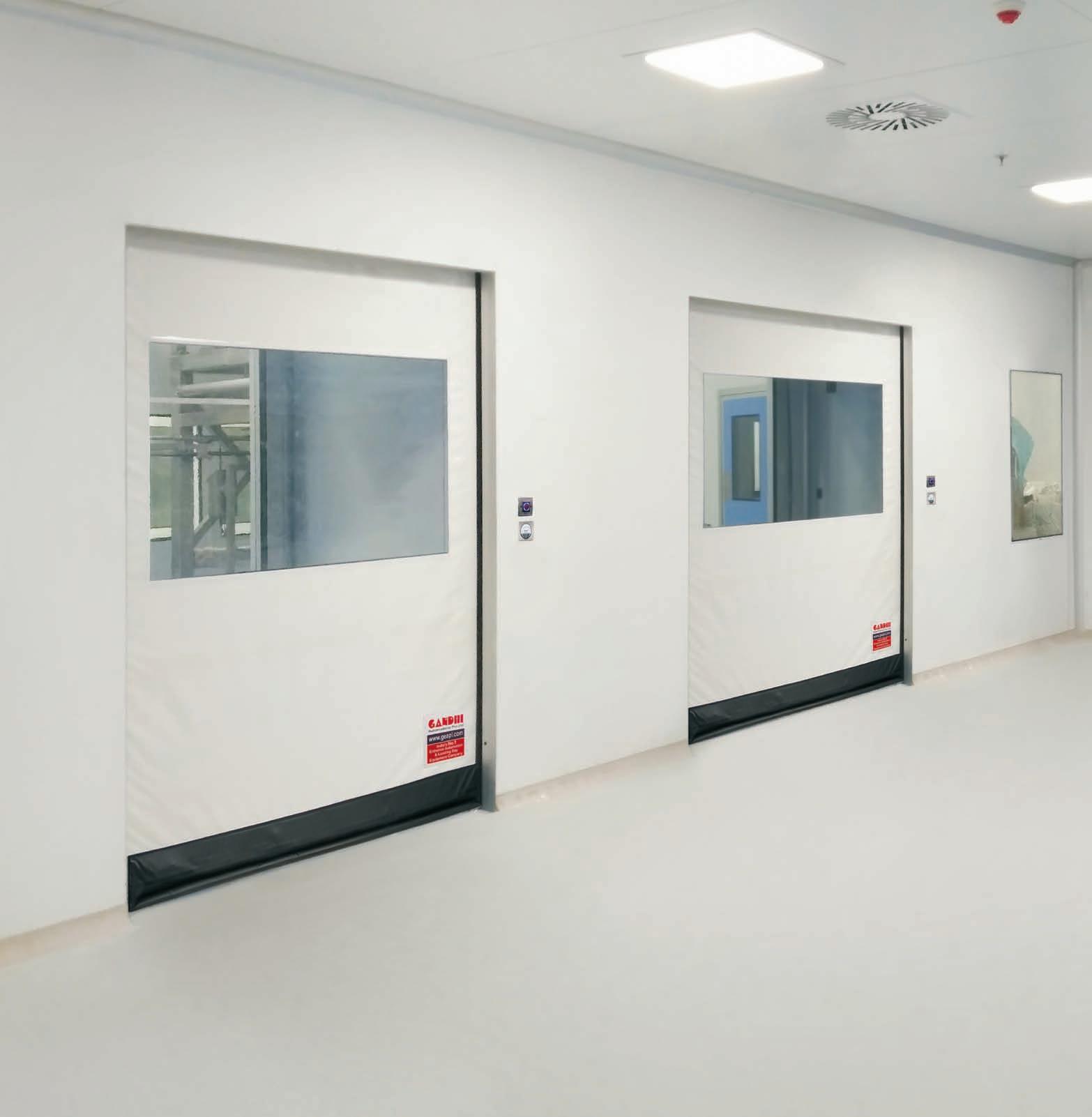
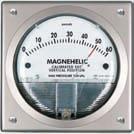

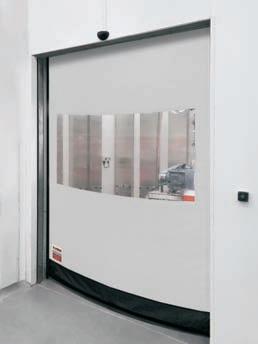
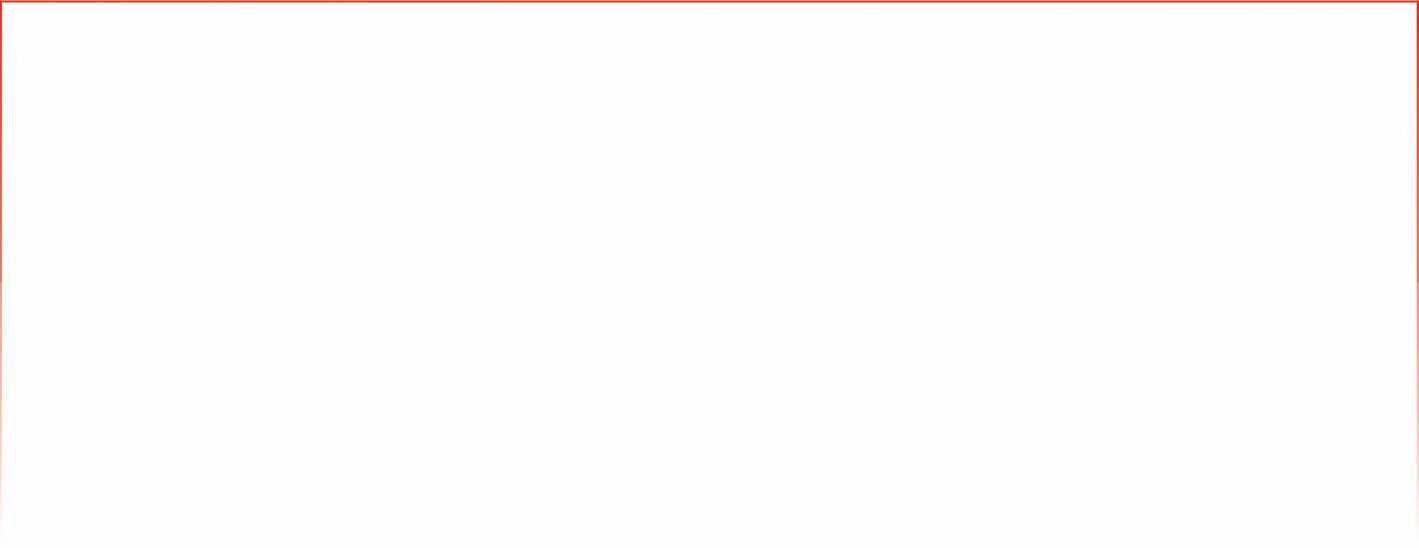
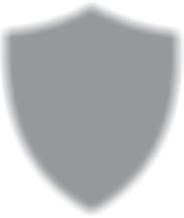
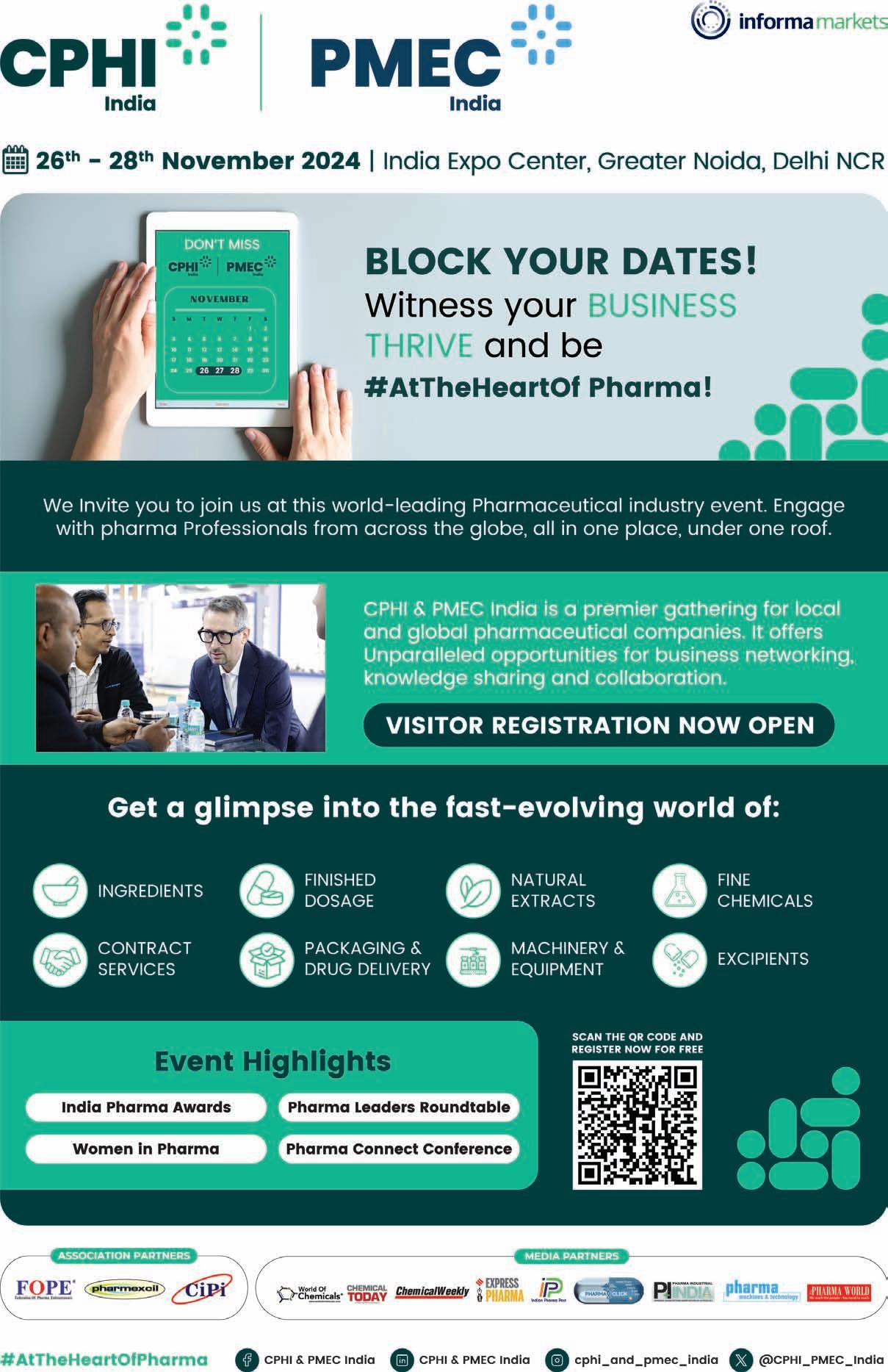
NoBitterAfterTaste
we do.
Delivering a drug when and where it’s needed results in better outcomes for both manufacturers and patients. Ashland is a global leader in excipient technologies for controlled release, film coatings, disintegrants, tablet binding, long acting injectables, and medical devices. We offer products that meet a wide variety of sophisticated needs: klucel™ hpc, viatel™ bioresorbable polymers, vialose™ trehalose, aquarius™ film coating systems, plasdone™ povidone, benecel hpmc, polyplasdone™ crospovidone, natrosol hec, pvpi™ povidone iodine
Learn more about how we can help with your formulations at ashland.com/contact
Chairman of the Board
ViveckGoenka
Sr.Vice President-BPD
Neil Viegas
Vice President-BPD
Harit Mohanty
Editor Viveka Roychowdhury*
Editorial Team
Lakshmipriya Nair
Kalyani Sharma
Kavita Jani
Neha Aathavale
DESIGN
Art Director
Pravin Temble
Senior Designer
Rekha Bisht
Senior Artist
Rakesh Sharma
Marketing Team
Rajesh Bhatkal
Ashish Rampure
Debnarayan Dutta
Production Co-ordinator
DhananjayNidre
Scheduling & Coordination
Pushkar Waralikar
CIRCULATION
Mohan Varadkar
P14 KANISHKDUGGAL COO,ICRI
20 CONTINUOUS MANUFACTURING: TRANSFORMING PHARMA MANUFACTURING
Driven bystringent regulations,rising investor expectations,consumer demand, and operational considerations,MSME pharma companies need to carefully balance their sustainabilitygoals with financial viability
By Viveka Roychowdhury
31 MANUFACTURING THE RIGHTTALENT
35
45 THE FUTURE OF PHARMA LOGISTICS: TRENDS, CHALLENGES,AND OPPORTUNITIES
Regd.With RNI No.MAHENG/2005/21398.Postal Regd.No.MCS/164/2022 - 24.Printed and Published byVaidehi Thakar on behalf of The Indian Express (P) Limited and Printed at The Indian Express Press,Plot No.EL-208,TTC Industrial Area,Mahape,Navi Mumbai-400710 and Published at Mafatlal Centre,7th floor,Ramnath Goenka Marg,Nariman Point,Mumbai 400021.
Editor: Viveka Roychowdhury.* (Editorial & Administrative Offices: Mafatlal Centre,7th floor,Ramnath Goenka Marg,Nariman Point,Mumbai 400021)
* Responsible for selection of news under the PRB Act.Copyright © 2017.The Indian Express (P) Ltd.All rights reserved throughout the world. Reproduction in anymanner,electronic or otherwise,in whole or in part,without prior written permission is prohibited.
Emcure Pharma became one of the first pharma companies to apply for and get some interim relief from the union health ministry's recent prohibition of sale and distribution of fixed dose combinations (“FDC”). Emcure had filed a writ petition before the Delhi High Court seeking the quashing of the August 12, 2024 notification, which prohibited the manufacture for sale and distribution of the company's pain relief FDC of S (+)-Etodolac + paracetamol for human use with immediate effect. Emcure's senior counsel stated before the Delhi High Court that the report of the sub-committee, on the basis of which the ban has been notified, has not been made public till date. The senior counsel also stated that it remains unclear why complete prohibition of the subject matter FDC has been recommended.
The court order shows that Emcure's senior counsel drew the attention of the Delhi High Court to an order dated July 3, 2023 regarding FDCs (Phenytoin + Phenobarbitone Sodium of Lupin) which had been prohibited under similar circumstances. The petition also referred to previous orders dated June 14, 2023 of the same court, which had under similar circumstances, granted interim protection for the drugs already in the distribution network. The June 2023 order specified that while drugs already in the distribution channel shall not be withdrawn, no fresh manufacture of the drug could take place till the next date of hearing. In addition, the order stated that no coercive steps would be taken against the petitioner for the drugs which are already in the distribution channel.
The Delhi HC order dated August 22, 2024 directed that the interim order of June 14, 2023 shall apply to Emcure's drugs which are part of the present writ petitions. The court also directed Emcure to file details of the stock of these banned FDCs as of the order date, within a week. The company also needs to give an affidavit of stock in circulation, within a week. The Union of India was granted four weeks' time to file a counter affidavit. Rejoinder affidavit, if any, needs to be filed before the next date of hearing, which has been listed as January 15, 2025.
The scene seems set for a repeat of previous prohibitions on FDCs, starting from 2016 with 344 FDCs prohibited. After a stay was granted, the matter was referred back to the Drugs Technical Advisory Board (DTAB), which stood by their decision on 328 drugs. The union ministry accepted their recommendation and banned these 328 FDCs in 2018. The next lot of banned FDCs in 2023 too saw similar litigation from several companies.
Pharma associations have gone on record to welcome the recent notification, with Sudarshan Jain, Secretary General, Indian Pharmaceutical Alliance pointing out that the discussion on FDCs is going on over a period of time with recommendation from Kokate committee and Nilima Kshirsagar
Putting the patient first, before granting licences seems the solution
committee. He feels this is a right step in the interest of patients and all aspects have been taken into consideration.
Industry associations are planning to file appeals along similar lines of the Emcure petition, to allow companies to exhaust stocks in the distribution network as well as stocks already manufactured that may be still within company premises. A future plan of action includes associations supporting their members should they contest the notification's premise that their FDCs are purportedly irrational combinations. If companies feel strongly that these are good products, have been in the market for over 30-40 years, and see no reason for a ban, associations will help them make their case.
While it remains to be seen whether more pharma companies challenge the notification, the recent ban revives the discussion on why such purportedly irrational combinations were approved in the first place. Industry discussion groups allude to cases where state licensing authorities took the stance that since individual molecules were licensed, it was fine to pass a combination of licensed molecules.
The gazette notification for each individual banned FDC stated, “There is no therapeutic justification for the ingredients contained in this FDC. The FDC may involve risk to human beings. Hence in the larger public interest, it is necessary to prohibit the manufacture, sale or distribution of this FDC under section 26 A of Drugs and Cosmetics Act 1940. In view of above, any kind of regulation or restriction to allow for any use in patients is not justifiable. Therefore, only prohibition under section 26A is recommended.”
The sentence, 'The FDC may involve risk to human beings' without specifying the reasons / extent and nature, puts the onus on the government to prove that a particular FDC is harmful to patients' health.
Going a step back, should not the authorities have examined whether there were therapeutic benefits of FDCs when licences were applied for? Similarly, should they have not examined whether there is no risk to patients, before they grant a manufacturing licence?
The list of banned FDCs include medicines for common illnesses like cold, fever, antibacterial and antifungal medicines, as well as antibiotics, anti allergy medication, painkillers and multivitamins. Medicines in India can be purchased very easily without a prescription, leading to potential long term misuse of many such irrational combinations. Given this reality, putting the patient first, before granting licences seems the solution.
VIVEKA ROYCHOWDHURY, Editor viveka.r@expressindia.com viveka.roy3@gmail.com
Elevateyourtabletcoating experiencethatofferssuperior protectionwithunmatched quality&innovation.
Kanishk Duggal,COO,ICRI in interaction with Kalyani Sharma emphasises how the availability of a skilled workforce is influencing the growth of clinical research in India and more
How do you perceive India's role in the global clinical research landscape evolving in the next five years?
India is set to become a central player in global clinical research due to its vast and diverse population, costeffective research capabilities, and evolving regulatory environment. Recent data shows a 25 per cent increase in registered clinical trials in India over the past year, positioning the country among the top 10 globally. The Central Drugs Standard Control Organization's new guidelines are streamlining the approval process, further attracting international researchers and sponsors. At ICRI India, we are excited about these developments and are committed to advancing clinical research education to support this growth. India’s expanding role will not only enhance its global standing but also contribute significantly to innovations in healthcare and treatment.
What specific regulatory reforms have significantly impacted clinical research in India, and what further changes are needed?
India has made significant strides in aligning its regulatory framework with international standards, such as those set by the US FDA and EMA. This alignment has made the country more attractive for global clinical trials. The introduction of the New Drugs and Clinical Trials
The adoption of digital tools in the clinical research sector has seen a significant acceleration post-pandemic.The COVID-19 crisis highlighted the need for faster,more efficient,and scalable solutions,leading to a rapid shift towards digital transformation
Rules in 2019 marked a pivotal moment, streamlining the approval process and ensuring higher ethical standards. Additionally, the Indian regulatory authorities have implemented fast-track approval processes for drugs, which has further bolstered the appeal of India as a clinical research hub. However, continued efforts to refine and enhance these regulations, particularly in areas such as patient safety and data transparency, will be necessary to maintain this momentum.
How is the availability of a skilled workforce influencing the growth of clinical research in India, and what measures are being taken to enhance this talent pool?
The availability of a skilled workforce is crucial for the growth of clinical research in India. Our educational programs at ICRI India are designed to address this need by providing comprehensive training in clinical research, pharmacovigilance, and clinical data management.
The landscape is evolving rapidly, with opportunities expanding beyond Contract Research Organizations (CROs) to include IT giants like IQVIA, Wipro, TCS, and Mahindra, each having a life sciences division. Currently, there are over 250,000 job vacancies globally in this sector.
To enhance the talent pool,
we focus on equipping students with practical skills and industry knowledge, ensuring they are wellprepared for these diverse roles. By offering exposure across these three critical areas, we aim to meet the industry’s demand for specialised professionals and support the sector's growth.
How has the adoption of digital tools accelerated in the clinical research sector post-pandemic?
The adoption of digital tools in the clinical research sector has seen a significant acceleration post-pandemic. The COVID-19 crisis highlighted the need for faster, more efficient, and scalable solutions, leading to a rapid shift towards digital transformation. Tools such as electronic data capture (EDC) systems, remote monitoring, and virtual trials have become integral to modern clinical research.
We have integrated these digital advancements into our curriculum, preparing our students to work with cuttingedge technologies. This shift not only streamlines research processes but also enhances data accuracy and participant engagement. As a result, clinical research is becoming more agile, transparent, and capable of addressing complex global health challenges with greater efficiency.
What are the key areas of
investment in building clinical research infrastructure in India?
Investment in clinical research infrastructure in India is focused on several key areas. Advanced technology plays a crucial role, with emphasis on electronic data capture systems, patient management software, and data analytics tools to enhance trial accuracy and efficiency. Upgrading clinical trial sites is equally important, ensuring they meet global standards with state-ofthe-art facilities and resources. Building a skilled workforce is another priority, with investment in education and specialised training programs in clinical research, pharmacovigilance, and data management to address the
Training programs and strategic partnerships are undeniably pivotal in bolstering capacity building within the clinical research domain
skills gap. Strengthening regulatory frameworks to align with international standards also facilitates smoother trial conduct and boosts India’s global competitiveness. Additionally, with the rise of digital tools, investing in infrastructure for remote and virtual trials is becoming increasingly vital. These investments collectively advance India’s position as a leading global hub for clinical
research.
How are training programs and partnerships contributing to capacity building in clinical research?
Training programs and strategic partnerships are undeniably pivotal in bolstering capacity building within the clinical research domain. our comprehensive approach encompasses
clinical research, pharmacovigilance, and clinical data management, providing a robust foundation for nurturing talent.
The burgeoning life sciences landscape has expanded opportunities beyond traditional CROs. IT giants like IQVIA, Wipro, TCS, and Mahindra, among others, have established dedicated life sciences divisions, creating a surge in
demand for specialised professionals. This presents a golden opportunity for skilled individuals to carve out successful careers.
By imparting in-depth knowledge and practical skills, our training programs equip aspiring professionals to excel in this dynamic industry. Moreover, our collaborations with industry leaders foster knowledge exchange, enabling us to stay at the forefront of emerging trends and best practices. Ultimately, these synergistic efforts contribute significantly to the growth of a skilled workforce, thereby strengthening the clinical research ecosystem in India.
Kalyani.sharma@expressindia.com journokalyani@gmail.com
September 2024
www.micronclean.in
DELIVEREDWITHAVERIFIEDANDEASILYACCESSIBLE PROCESSINGHISTORYASSTANDARD
MicroncleanIndiacandeliverdry,cleansterilereadytowearcleanroom garmentsdirectlytoyourpremiseswithaverifiedandeasilyaccessible processinghistory,whichallowsyoutobecompliantwithEUGMPAnnex1. Ifyouareinterestedinintegratingourcleanroomgarmentserviceinto yourcontaminationcontrolstrategy,pleasecontactus.
MicroncleanIndiaPvtLtd PlotNo.24&25|VemagalIndustrialArea Vemagal|Kolar|563102|Karnataka|India T.+917829111150 E.enquiries@micronclean.in
In an exclusive interview with Express Pharma, Zubin Zaveri,Managing Director of Transchem Corporation Pharma Pvt.Ltd.,discusses the company's evolution,market outlook,and investment plans in the Indian pharmaceutical excipients industry
How has Transchem evolved since its inception? What have been the major milestones in this journey?
Transchem started its operations in 1989 by collaborating with BASF. We started as a trader with a turnover of 29 lakhs in 1st year with 3 employees. Since then, we have grown into one of the major Pharma excipients distributors in India and achieved a milestone of 300+ crores in 2023. Since last few years Transchem is growing at CAGR of over 20 per cent. Over the years Transchem has added Elementis, G Sweet, BA’MEK, etc. as Principal partners. We at Transchem believe in “Quality of Quantity” which ensures that the quality standards are maintained. USP of our growth has been quality of service and transparency with both Principals and end customers. In 2022 Transchem was awarded for highest sales in Asia Pacific region by BASF.
How do you see Indian Pharmaceutical excipients market and how do you see the growth of Transchem going forward? What are Transchem’s investment plans considering the current Indian Pharma Excipients Industry?
The Indian pharmaceutical excipient market is growing at a rate of 10–12 per cent annually, which is higher than the global rate of 5–7 per cent. We are witnessing a growing interest in increasing export to developed markets from Indian Pharma manufacturers and hence we at Transchem believe that though there is competition from local and Chinese manufacturers we will grow at a good rate considering the quality of excipients we offer and
principals like BASF we are associated with.
Regarding investment plans, yes, we are open and wiling to invest if right opportunity comes. If you look at the current scenario, India is heavily relying on imports from Europe, US, China, Japan, etc. and that accounts to more than 70 per cent. So, we are open for collaboration if get the right partner who is willing to manufacture excipients in India.
In recent years we have witnessed quite a few acquisitions of Indian distributors by global distributors. What is you view on that and how do you see it impacting Indian Pharma companies?
As we know that Indian Pharma Industry is growing at a good pace, and this is generating the interest from global excipient distributors to increase their presence in India and capitalise on the growth. So, we are seeing lot of acquisitions either to get entry into India or increase the presence. But we see this as a challenge for Indian Pharma manufacturers because lot of money has gone into these acquisitions and there will be margin pressure of global distributors which in turn may increase the cost of excipients to end customers. So, we think these acquisitions may impact Indian Pharma manufacturers as it will increase the cost of their formulations. And that’s where we see the opportunity as we work on a very reasonable
margins and hence are very competitive. So, we are positive of the Transchem’s growth going forward.
What are Trans-Chem's plans for future market expansion or product diversification? What will be your growth strategies, both domestically and globally? How does Transchem plan to leverage Indian Pharma growth and emerging technologies to stay ahead of the curve?
Transchem offers a large basket of excipients for various dosage forms like oral solids, oral liquids, topicals, parenteral, etc. across the different applications like instant & modified formulations, solubilisation, biologics, etc. Indian Pharma is transforming from conventional formulations to concentrate more on specialty medicines, complex generics and expanding into biologics and biosimilars to enhance profitability. At Transchem we have a well-qualified and experienced sales and technical team who have the experience of working in Pharma research. Our team closely follow the industry transformations and work hand in hand with Pharma companies to understand their current and future requirements. So, we are aware of changing industry dynamics and prepared for it.
What is your view on Indian Pharma Industry and why are you so positive about it?
There are quite a few factors which favours India. India has emerged as a global hub for low price and high-quality medicines, thereby rightly making the country the ‘Pharmacy of the World’. The low cost of manufacturing and R&D along with cheap skilled
labour compared to US and Europe makes India a preferred destination. India has the largest number of USFDAcompliant plants outside the US and over 2,000 WHO-GMP approved facilities and supplying to more than 150+ countries worldwide.? Further government policy measures and increasing investments are making the growth conditions more favourable. Up to 100 per cent, FDI has been allowed through automatic route for Greenfield and up to 74 per cent for Brownfield pharmaceuticals projects. The government has launched PLI schemes to boost pharmaceutical manufacturing.
Are there any plans for Transchem to explore new markets or sectors beyond pharma in the near future? We’re witnessing an evolution in India’s pharma sector, and we are focussed to be part of the growth story. The Indian pharmaceutical industry is expected to grow at a CAGR of more than 10 per cent to reach $130 billion by 2030. With a robust base of drug manufacturers and a growing pool of R&D talent, India is a goto market for generics, contract services, coupled with a surge in the biological production of commercial drugs. India Ranks 3rd worldwide for pharmaceutical production by volume and 14th by value. About 20 per cent of the global exports in generic drugs are met by India. Hence considering the future growth in Indian Pharma we are currently focused on Pharma but yes, we are open to explore beyond Pharma and will be interested in collaborating with global manufacturer operating in cosmetics & Nutraceuticals where we see good growth.
Indu Bhushan,CEO & Director,STEERLife highlights how continuous manufacturing make production of pharma products more efficient and offers significant regulatory benefits.He also underscores the importance of technological advancements,regulatory compliance and strategic investments in driving the future of pharma manufacturing
The world massively relies on the developments that continue to take place in the pharma industry to experience an improved quality of life. From producing drugs for rare forms of cancer to generating highly effective vaccinations for various epidemics and pandemics, this industry has always played a pivotal role in safeguarding public health. Its response to COVID19 underscores its potential to effectively address every global health crisis and mitigate longterm health risks associated with them.
The pharma industry has undergone a monumental transformation over the last few years. One of the major factors responsible for its transformative journey has been Process Intensification (PI). Driven by the need to increase efficiency, reduce cost, and improve product quality, it has been at the core of pharma manufacturing. At the moment, it is being majorly applied in bioprocessing and small-molecule drug facilities through Continuous Manufacturing (CM) for rapid development of new therapies and to scale up the production of existing drugs in order to evade a health crisis.
Continuous manufacturing and its benefits
There are three different approaches to continuous manufacturing (CM); fully end-toend continuous, a hybrid of batch and continuous, and individual continuous operations retrofitted in a batch process (mostly for legacy processes). The selection of any of these
approaches is guided by factors such as enterprise readiness, the product itself, processes involved, equipment, relevant regulations, available technology, demand in the market, and volume/value of the product. Irrespective of the approach, integration of CM in the pharma sector results in smaller factories, better process control, and environmental footprints, lower capital input, consistent product quality, modular manufacturing, and lower operating costs.
As per a report by Straits Research, a market research company, the global continuous manufacturing market was valued at $504.25 million in 2022 and is predicted to reach $1,4290.95 million by 2031, registering a CAGR of 12.2 per cent during the forecast period. It also highlights that with more and more manufacturers realising the number of benefits CM holds, there is a noteworthy increase in the investments in the R&D area, further leading to such positive predictions.
Out of many, one huge advantage is how CM renders drug sponsors the ability to rapidly respond to market opportunities. It can seamlessly accommodate scale-up and post-approval changes. For ex-
ample, increases in lot sizes are possible by simply running longer. This can be particularly beneficial during drug shortages and competitive market situations, as manufacturers can acquire additional market share immediately with little to no disruption in operations or product quality.
Along with availing benefits of continuous manufacturing, manufacturers must maintain regulatory compliance to ensure public health safety, build trust, and ethically run the business. They can do so by following the guidelines of the Food and Drug Administration (FDA) and European Medicine
Agency (EMA). Also, to establish a sense of transparency, especially for audits, and adhere to regulatory standards, manufacturers must have a Quality Management System (QMS) in place. This system assists in proper documentation and record-keeping.
However, some manufacturers have been hesitant to adopt CM due to perceptions of increased regulatory risks. They are primarily concerned about potential pre-market delays, greater inspectional scrutiny, and post-market hurdles.
Nonetheless, a recent FDA selfaudit comparing CM to batch manufacturing regulatory outcomes confirmed that manufacturers who submitted CM applications actually “had relatively shorter times to approval and market as compared to similar batch applications…translating to an estimated $171-537 million in early revenue benefit.” In addition, the assessment displayed “no substantial regulatory barriers” for CM applications related to manufacturing process changes or pre-approval inspections.
Over the last decade, companies like Pfizer, Eli Lilly, GlaxoSmithKline, and others have proven CM’s commercial success, which is also indicative of the kind of potential this process holds to drive future trends in pharma manufacturing. Over a half-dozen medicines have already been made by using CM and have been approved in the US.
Along with this, semi-continuous manufacturing is also growing in popularity. This technique combines the elements of both – batch manufac-
turing and continuous manufacturing. As a result, certain stages of the process are operated continuously, while others are carried out in batches. Nonetheless, CM continues to remain a popular choice.
Given the recent technological advancements, regulatory developments, and commercial products, continuous manufacturing is registering noteworthy growth in the pharma industry. Regulators are also pushing CM along with harmonised guidance development to ensure maximum clarity regarding various approaches and concepts associated with it.
But just like the two sides of a coin, along with CM's success and growth rate, the challenges associated with it demand equal attention. Manufacturers are facing economic and workforce capacity challenges associated with CM start-up activities, upfront investment costs, and regulatory uncertainties in certain geographies. Therefore, to successfully implement CM in every pharma manufacturing facility, the key focus should be key investments, advancing scientific and technical knowledge, and additional incentives.
References
1. https://straitsresearch.com/report/continuous-manufacturingmarket
2.https://www.sciencedirect.com /science/article/pii/S03785173220 03337#!
3. https://www.fda.gov/regulatory-information/search-fdaguidance-documents/q13-continuous-manufacturing-drug-substan ces-and-drug-products
⚪ Turnkeyapproachforthecomplete filling linewithisolatorandfreezedryers
⚪ Weconsistentlyalignourprocessesto meettheneedsofourcustomers
⚪ Weassureourcustomerscompetence, safetyandreliability
⚪ OptimaPharmaisanexpert,partner andthehomeforturnkey
OPTIMApharmaGmbH |74523SchwaebischHall|Germany|pharma@optima-packaging.com|www.optima-packaging.com/pharma
OPTIMAIndiaPackagingMachinesPvt.Ltd. |unit110,1stfloor|BrigadeRubix,PlotNo.20|HMTmainroad|Bangalore560013 info-in@optima-packaging.com|Phone:+918046525900|www.optima-packaging.in
Driven by stringent regulations,rising investor expectations,consumer demand,and operational considerations,MSME pharma companies need to carefully balance their sustainability goals with financial viability
By Viveka Roychowdhury
Prime Minister Narendra Modi’s mention of ‘green jobs’ in his Independence Day speech this year re-emphasised his commitment to achieving the Net Zero emissions target by 2070. The question is how will India, arguably the world’s third-largest greenhouse gas emitter, achieve this target, with even the goal of limiting global warming to an increase of no more than 1.5 degrees Celsius (1.5°C) above pre-industrial levels, looking like a steep challenge?
As the market regulator, the Securities and Exchange Board of India (SEBI) has added heft to the net zero target, by expanding the disclosures that listed entities need to make related to Environmental, Social and Governance (ESG) factors.
A SEBI circular dated July 12, 2023 mandates that the top 150 listed entities (by market cap) had to undertake reasonable assurance of Business Responsibility and Sustainability Reporting (BRSR) Core from FY23-24, and this will extend to the top 1000 listed entities by FY26-27. The circular also requires the top 250 listed companies by market cap to disclose BRSR Core information for their value chain in their Annual Reports for FY24-25 on a comply-or-explain basis.
As Ramesh Swaminathan, Executive Director, Global CFO and Head of Corporate Affairs, Lupin points out, the pharma industry’s contribution to the climate crisis comes from its 4.4 per cent share of global CO2 emissions. Although this percentage is lower than that of other industries, without action, emissions are expected to rise. Thus, he points out that the pharma industry has a unique responsibility to take action and promote sustainability. While it needs to reduce its greenhouse gas (GHG) emissions through net-zero strategies, it also needs to address the adverse health effects of the climate crisis by providing affordable medicines.
Listed pharma companies in India have been reporting on their ESG initiatives for the past few years. Quoting from the
Our success in Sustainability within a short period of time is a solid example for companies wanting to start incorporating sustainability in business practices.We at Lupin did our basics right while we integrated sustainability into business operations
Ramesh Swaminathan Executive Director,Global CFO and Head of Corporate Affairs,Lupin
These steps not only reduce environmental impact but also improve operational efficiency,making them attractive to investors who are increasingly looking for companies that prioritise sustainability
Mehul Shah Promoter & Managing Director,Encube Ethicals
Pursuing green certifications,can enhance a company’s credibility and demonstrate a commitment to environmental responsibility,thereby, attracting investors and partners interested in supporting sustainable initiatives
Anil Matai
Director
General,Organisation of Pharmaceutical Producers of India (OPPI)
To further incentivise the sector,the government should introduce green subsidies,tax breaks,and low-interest loans for eco-friendly technologies.Focus on sustainability is fundamental for all organisations and this will contribute to sustainable performance from a longterm perspective
Sudarshan Jain Secretary General,Indian Pharmaceutical Alliance
EY-CII 2024 report ‘How can Sustainability and ESG be the microscope and telescope in the Indian healthcare sector?, Nitesh Mehrotra, Partner, ESG & Sustainability, EY India highlights increasing allocations towards environmental and social initiatives within research and development (R&D) and capital expenditure (capex). 21 per cent of spending is dedicated to environmental and social activities in R&D, showcasing a commitment to innovation and sustainable practices. Equally noteworthy is the allocation of 13 per cent of spending towards environmental and social initiatives within capex, affirming a strategic commitment to infrastructure and operational enhancements for bolstering sustainability performance.
Toeing the green line Larger pharma companies are toeing the SEBI line and are also prominent on global ESG ratings. In December 2023, Dr Reddy’s Laboratories became the first Indian pharma company to earn a place in the Standard & Poor Dow Jones Sustainability World Index (DJSI World) for 2023. Alongside its debut in DJSI World, the company retained its place in the Dow Jones Sustainability Index for Emerging Markets (DJSI EM) for the eighth year in a row. Dr Reddy’s scored 77/100 in the 2023 S&P Global CSA, achieving full scores in Innovation Management, Impact on Access to Healthcare, Climate Risk Management, and Resource Efficiency and Circularity. The company ranked in the top decile percentile and achieved the sixth-highest score out of 347 companies assessed in the pharma industry in the S&P Global CSA. Dr Reddy’s S&P Global ESG score, measuring the company's performance on and management of material ESG risks, opportunities and impact, is 78/ 100. Dr Reddy’s has been awarded ‘Gold Medal’ status by EcoVadis, the global sustainability ratings agency, for its score of 70/100 in its 2023 scorecard.
A Dr Reddy’s spokesperson’s
statement also informed that in 2022, the company’s largest formulations manufacturing facility in Bachupally joined the Global Lighthouse Network (GLN) of the World Economic Forum - a community of over 100 manufacturers that are showing leadership in applying Fourth Industrial Revolution (Industry 4.0 or 4IR) technologies to drive impact in productivity, workforce engagement, sustainability and supply chain resilience. In addition, five of the company’s manufacturing facilities are certified under Indian Green Building Council (IGBC). In FY2024, the company evaluated 26 products through chemistry gate clearance. Through the implementation of 17 cost improvement projects leveraging green chemistry principles, Dr Reddy’s successfully reduced nearly 22 per cent hazardous waste generation in the manufacturing of those products.
Lupin embarked on their sustainability journey four years ago, and made an entry in the S&P Global Sustainability Yearbook 2024, with a notable Corporate Sustainability Assessment (CSA) score of 65/100, and an S&P Global ESG Score of 69. Sun Pharma's CSA and ESG scores were both 68, Cipla's CSA was 67, ESG 70, and Neuland Laboratories had a CSA score of 60 and ESG score of 64. Similarly, Biocon’s S&P Global CSA score was 61, and ESG score was 63, placing it among the Top 10 global biotech companies.
Sudarshan Jain, Secretary General, Indian Pharmaceutical Alliance, which represents large Indian pharma companies, summed up this evolution, saying, “Sustainability is a strategic priority for pharma companies as the sector involves a significant environmental footprint. IPA members are advancing green practices including sustainable supply chains, efficient technologies, carbon neutrality, waste management, and energy and water conservation practices. Financial sustainability, achieved by integrating ESG principles, ensures long-term stability and growth.”
Anil Matai, Director General, Organisation of Pharmaceutical Producers of India (OPPI), which represents India subsidiaries of MNC pharma companies, believes that true
sustainability involves adopting a long-term perspective that prioritises the well-being of both the people and the planet. This entails a dedication to social, environmental, and civic
responsibilities that go well beyond immediate gains. OPPI’s publication titled, Putting the Country First Taking the Country Far, lists the efforts of OPPI member companies.
As an ESG consultant, Sunil Kumar, Director, SIPL also concurs that the pharma sector is increasingly making investments in sustainability, driven by a combination of regulatory
pressures (for instance, regulations like the European Union's Green Deal and the US Securities and Exchange Commission's ESG disclosure requirements are becoming more stringent), investor expectations, consumer demand, and operational considerations.
With +20 clients in the pharma and related intermediate sectors, SIPL has conducted life cycle Assessments (LCAs), and provided ESG solutions and SimaPro software to pharma majors like Novartis, Sun Pharma, Biocon, Ajanta Pharma, Dorf Ketal, Gharda Chemicals, Cardolite Specialty Chemicals, Anupam Rasayan India, SRF, etc.
Giving the equipment manufacturer’s point of view, Shivshankar SR, CEO, ACG Packaging Materials, reiterates that it is important for organisations to proactively set targets and focus on long-term initiatives that will provide value realisation and business transformation towards creating a more sustainable and resilient future. He mentions that within ACG’s business, their adherence to the Science Based Targets initiative (SBTi) through their recently announced strategic partnership with EY Parthenon, underscores their commitment to conscientious corporate stewardship.
Summing up, Shivshankar of ACG Packaging reminds us that the mission to reduce the overall carbon footprint remains a driving principle for the pharma sector, with a focus on making manufacturing ‘contained, continuous and connected’ - optimising raw material use and reducing waste.
Shivshankar singles out large-scale manufacturers who must expedite net zero objectives, thereby effectuating a meaningful reduction in their carbon emissions. While he concedes that embarking on the journey towards decarbonising entire processes will undoubtedly prove overwhelming for many, he reminds us that “ultimately it’s about looking towards the future and trying to understand wide-ranging
stakeholder needs to create long-term and effective solutions.”
MSME pharma sustainabilitypath
But MSME pharma companies are also a huge part of India Pharma Inc. According to the Confederation of Indian Industries (CII), there are around 8,000 small and medium enterprises (SME) units, accounting for about 70 per cent of the total
Transparent reporting of ESG metrics not only enhances investor confidence but also serves as a barometer of a company's resilience and adaptability in a rapidly evolving world.Integrating ESG into investment strategies not only aligns with ethical imperatives but also unlocks opportunities for sustainable growth
Nitesh
Mehrotra Partner,ESG & Sustainability,EYIndia
Government support is crucial for MSMEs to embrace sustainability.Key incentives include financial support, tax benefits,regulatory support,skill development and public procurement preference
Sayooj Thekkevariath,
Partner,Climate Change and Sustainability Services,EYIndia
highly regulated environment.
One of the primary challenges the industry faces is the inherent resource intensity of pharma manufacturing. The production of drugs requires significant amounts of water, energy, and raw materials, which contribute to a substantial carbon footprint. Furthermore, the management of pharma waste, especially active pharma ingredients (APIs), poses significant environmental risks if not handled responsibly. The complexity of global supply chains adds another layer of difficulty in ensuring that sustainability is maintained at every stage of production, explains Shah.
The energy requirement for continuous manufacturing goes down by 50-70 per cent in a few cases.That's very significant as a lower energy requirement translates to not just huge savings but also a huge reduction in the carbon footprint
Indu
Bhushan CEO & Director,STEERLife
number of the pharma units in India.
Forward looking mid size pharma companies have already committed to ESG goals realising that there are multiple benefits beyond compliance.
As Mehul Shah, Promoter & Managing Director, Encube Ethicals puts it, “Sustainability is more than a commitment, it's a path to operational efficiency and long-term value creation.”(https://www.
expresspharma.in/sustainabilityis-more-than-a-commitment-itsa-path-to-operational-efficiencyand-long-term-value-creation/)
Summarising the challenges, Shah points out that with growing awareness of the environmental impact of pharma manufacturing, such as pollution from toxic discharges, pharma companies face the challenge of balancing their sustainability goals with the economic pressures of operating in a
Drawing on his experience as an ESG consultant, Sunil Kumar comments that the sustainability journey for pharmaceutical companies, including smaller and MSME pharma clients, has varied widely depending on their size, resources, and initial practices. However, there are common outcomes and best practices that can guide MSME and smaller pharma companies in their sustainability efforts.
Enumerating some best practices, Sunil Kumar says that for MSME and smaller pharma companies, the way forward involves integrating sustainability into core business strategies and operations. “By starting with manageable changes, leveraging support, setting goals, and fostering a culture of continuous improvement, these companies can achieve significant benefits and contribute positively to environmental and social outcomes. As the industry evolves, ongoing adaptation and commitment to sustainability will be key to longterm success and resilience.”
Enumerating the early steps that MSME pharma companies can consider as they could result in quick gains to encourage more investments in sustainable manufacturing practices, Shah suggests that before making any major changes, the first step should be to optimise what the company has.
Operations can become sustainable if companies can enhance the lifespan and performance of machinery, reduce downtime and minimise resource use. This evaluation helps identify areas where simple optimisations can lead to significant improvements.
For instance, companies can start by improving energy efficiency and result in immediate reductions in energy consumption and costs. Implementing water conservation techniques, such as low-flow fixtures or rainwater harvesting, can reduce water consumption quickly. Companies can also explore the reuse of treated wastewater for non-critical operations like cleaning or cooling systems. Shah reasons that these steps not only reduce environmental impact but also improve operational efficiency, making them attractive to investors who are increasingly looking for companies that prioritise sustainability.
He also singles out ‘green financing’ as another popular avenue for quick gains in sustainability. Simply put, this is a type of loan designed to promote environmentally-friendly activities, encouraging companies to invest in projects that reduce their environmental impact. These loans come with reduced interest rates, providing financial incentives for companies to meet their sustainability goals.
For example, Shah points out that Biocon’s $1.2 billion green loan to fund its purchase of Viatris’ biosimilars business last year, was one of the largest green loans raised by a pharma company in the APAC region. The company agreed to meet certain sustainability targets that helped reduce the cost of the loan.
As EY India’s Mehrotra explains, “Transparent reporting of ESG metrics not only enhances investor confidence but also serves as a barometer of a company's resilience and adaptability in a rapidly evolving world. Integrating ESG into investment strategies not only aligns with ethical imperatives
but also unlocks opportunities for sustainable growth.”
Adding to the suggestions, OPPI’s Matai advocates that educating and training employees on sustainable practices fosters
a culture of sustainability within the organisation, which can have a ripple effect on overall operations. From the investability angle, he agrees that “Pursuing green certifications,
can enhance a company’s credibility and demonstrate a commitment to environmental responsibility, thereby, attracting investors and partners interested in supporting sustainable initiatives.”
Sayooj Thekkevariath, Partner, Climate Change and Sustainability Services at EY India goes further, stating that to make sustainability truly
Highprecision measurementswithmultiple channelsforreliable measurementatsites
Measurementdata memoryfor1million values
Robustmetalhousingand protectionagainstdustand waterjets
Automatedtemperature andhumiditymonitoring withconnectableprobes
Ÿ Easyinstallationsaves timeandeffort
Ÿ Dataaccessibilityfrom anywhereanytimeon
(Choosefromvarioussoftware-basictoCFR21part11compliant,exceptsaveris2)
sustainable in pharma, a holistic approach is essential. This involves adopting circular economy principles like recycling, reusing, and recovering materials which can significantly reduce waste and resource consumption. It also involves leveraging digital technologies for process optimisation, supply chain visibility, and energy management which can enhance efficiency and reduce environmental impact.
Similarly, collaborative partnerships with suppliers, academia, and industry peers can accelerate innovation and knowledge sharing whereas risk management, involving identifying and mitigating environmental risks can prevent costly disruptions and enhance resilience.
However Thekkevariath cautions that companies need to consider a long-term perspective, as viewing sustainability as a long-term investment rather than a cost can drive strategic decision-making.
In terms of early steps leading to quick gains, Thekkevariath opines that to incentivise early investments, the industry can focus on energy efficiency, waste reduction, water conservation and employee engagement.
Lupin’s sustainabilitystory
Swaminathan offers Lupin as an example of achieving success in sustainability within a short period of time. Lupin’s mantra: get the basics right while integrating sustainability into business operations.
Swaminathan touches on five aspects of this journey. Firstly, integrating sustainability into the core business strategy, “ensuring the integration of sustainability practices into the very fabric of our strategy and this accelerated our journey towards becoming a patient-centric sustainability organisation.”
Secondly, Lupin divided the goals into two pillars: aspirational short term ESG SMART goals and long-term Perpetual Commitments. Swaminathan explains that ESG SMART goals have specific targets and timelines, which are monitored
Companies that proactively addressed sustainability and regulatory requirements were better positioned to comply with evolving regulations and avoid potential fines or operational disruptions
Sunil Kumar Director,SIPL
The mission to reduce the overall carbon footprint remains a driving principle for the pharmaceutical sector,with a focus on making manufacturing ‘contained, continuous and connected’- optimising raw material use and reducing waste
Shivshankar S.R CEO,ACG Packaging Materials
Drawing on his experience as an ESG consultant, Sunil Kumar comments that the sustainability journey for pharma companies,including smaller and MSME pharma clients,has varied widely depending on their size,resources,and initial practices.However,there are common outcomes and best practices that can guide MSME and smaller pharma companies in their sustainability efforts
every quarter, whereas the Perpetual Commitments represent the company’s ongoing efforts to improve, track, and report monthly progress.
Thirdly, Lupin links executive pay to ESG goals, with all president-level personnel having ESG goals as their individual goals. Next, taking this down the line, the company integrates sustainability with employees, where every individual thrives and is valued and empowered to
contribute to the business ESG goals.
And fifthly, Lupin involves their supply chain partners,actively engaging with suppliers, partners, and stakeholders to ensure their environmental and social objectives are shared in pursuance of Lupin’s ESG goals. Sharing a few outcomes of this sustainability strategy, Swaminathan mentions that Lupin’s share of renewable fuel in the energy mix increased by
four times, contributing to 33.8 per cent of total energy derived from fuel sources in FY24. The company achieved a 21 per cent reduction in Scope 1 & 2 emissions from the previous year. Looking forward, the company has successfully committed and joined the “Science Based Target Initiatives” which will drive progress towards decarbonisation of the value chain.
On the water stewardship status, in FY24, 44 per cent of
total water withdrawn at Lupin facilities was recycled, and the company’s target is to achieve 50 per cent by 2025.
Giving an example of Lupin's green chemistry skills, Swaminathan explains how the manufacturing of a particular antiviral molecule previously involved a three-step process, which delivered an overall yield of 0.91 per cent with an e-factor of 88 and an atom economy of 35 per cent. Lupin transitioned into a single-step process, delivering a yield of 1.4 per cent along with an E-factor improvement of 90 per cent and an atom economy improvement of 58 per cent.
Pharma companies in India are in a transition phase, as they explore more sustainable manufacturing concepts. However cost remains a key consideration. Equipment makers however argue that while the initial cost to switch to more sustainable options does involve considerable capex, the long-term savings more than make up. Thus advocating short term pain for long term gain.
One such concept is the switch from batch to continuous manufacturing. Indu Bhushan, CEO & Director, STEERLife mentions that many pharma companies in India have shown keen interest to move from batch to continuous manufacturing, particularly for the granulation and blending stages. These large-volume pharma manufacturers are under tremendous competitive pressure and therefore are constantly on the lookout for ways to improve cost efficiency.
To put the cost pressures into perspective, Indu Bhushan says that with products like metformin, paracetamol, and ibuprofen, which are typically manufactured in tons every day, there is a significant energy cost involved. However, while these active pharma ingredients (APIs) are pretty cheap, there is a significant contribution from conversion cost.
For instance, according to
him, a certain amount of API is lost as dust in the manufacturing process. Even if 0.5 per cent is the dust or the material lost in the cleaning process, different kinds of effluent treatments need to be done, adding to the cost.
So how does continuous manufacturing prove to be more sustainable than traditional batch manufacturing?
For one, Indu Bhushan estimates that the energy requirement for continuous manufacturing goes down by 50-70 per cent in a few cases. That's very significant as a lower energy requirement translates to not just huge savings but also a huge reduction in the carbon footprint, reasons Bhushan.
Listing the other advantages, according to Bhushan, continuous manufacturing also generates less effluents than batch processes, where multiple steps and a larger processing surface area translate to cleaning equipment and effluent treatment costs at every part of the process. These costs are reduced in continuous manufacturing systems.
Continuous manufacturing systems have a smaller footprint and therefore need smaller clean room facilities, further cutting down on energy and other utility requirements.
As continuous systems are also automated, there is less chances of human error and therefore less reliance on quality control (QC) as most responses are measured online. And therefore, QC testing, which typically follows every step of the batch process, is not applicable in contiguous manufacturing, reasons Indu Bhushan.
He estimates that the gains would be greater when companies use continuous manufacturing right from the R&D and development stage, going to fullscale commercial manufacturing at a smaller scale.
As he reasons, “Lots of materials are saved during the development (phase) because whatever experience we gain, we (apply) it directly to the commercial scale. In fact, in the initial years of adoption,
companies have used R&D scale equipment even for commercial scale without involving any scale-up or tech transfer. That not only reduces carbon footprint, but the go-to-market
time also significantly reduces because you have all necessary data at one scale. And we are talking about various options available for a scale-up or increasing the batch size.”
On the time to get RoI, Indu Bhushan estimates that it takes between one and a half to two years for a manufacturer to get RoI on continuous manufacturing. Summing up, he mentions
that apart from RoI, continuous manufacturing offers better flexibility in terms of batch size, reduction in energy and effluents leading to better overall sustainability.
…but also more expensive
Indu Bhushan admits that continuous manufacturing is best applied to large volumes, with systems capable of producing 150-200 kg of material per hour, with STEERLife also providing very large commercial scale equipment producing 500 kgs to custom designing a system for one ton per hour line for a client. These systems are typically integrated and require expensive components, like gravimetric feeding and PAT tools, which are required for measuring loss on drying or content or uniformity from time to time. And that makes it more expensive than a batch processor.
Due to the high costs, he has observed two significant differences between how India and the West started adopting continuous manufacturing.
Firstly, in the evolution from batch to continuous manufacturing, while the West is working on end-to-end continuous manufacturing, India’s pharma companies are at a hybrid stage where continuous manufacturing and automation are currently being deployed for stages which are more prone to human error.
Secondly, Indu Bhushan refers to collaborations between
CONTRIBUTOR’S CHECKLIST
equipment manufacturers and contract development and manufacturing organisations (CDMOs) in the US. For example, GEA has collaborated with Hovione for continuous manufacturing of solid orals (continuous tableting). According to him, similar collaborations should happen in India because companies like STEERLife are not just equipment manufacturers, but also provide process solutions, enabling CDMOs which adopt continuous manufacturing to serve global clients.
Agreen government push
IPA’s Jain recommends that to further incentivise the sector, the government should introduce green subsidies, tax breaks, and low-interest loans for eco-friendly technologies. He believes that this will contribute to sustainable performance from a long-term perspective.
Given the financial constraints faced by MSME pharma companies, Thekkevariath also agrees that government support is crucial for MSMEs to embrace sustainability. Key incentives include financial support (like subsidies, grants, and low-interest loans for green technology adoption), tax benefits (tax breaks for in-
❒ Express Pharma accepts editorial material for regular columns and from pre-approved contributors / columnists.
❒ Express Pharma has a strict non-tolerance policy of plagiarism and will blacklist all authors found to have used/refered to previously published material in any form,without giving due credit in the industry-accepted format.All authors have to declare that the article/column is an original piece of work and if not,they will bear the onus of taking permission for re-publishing in Express Pharma.
❒ Express Pharma's prime audience is senior management and pharma professionals in the industry.Editorial material addressing this audience would be given preference.
❒ The articles should cover technology and policy trends and business related discussions.
❒ Articles for columns should talk about concepts or trends without being too company or product specific.
❒ Article length for regular columns: Between 1200 - 1500 words.These should be accompanied by diagrams,illustrations,tables
vestments in sustainable practices and R&D), regulatory support in terms of simplified regulatory processes for environmental compliance and green projects, skill development involving investing in training programmes to build a skilled workforce for sustainable operations and finally, public procurement preference, which involves giving preference to environmentally friendly products in government procurement.
OPPI’s Matai points out that the recently announced Revamped Pharmaceuticals Technology Upgradation Assistance (RPTUAS) Scheme is a significant step in the government's efforts to help upgrade the technological capabilities of our pharma industry and ensure its alignment with the global standards. Eligibility for the PTUAS has been expanded beyond MSMEs to include any pharma manufacturing unit with a turnover of less than Rs 500 crores that requires technology and quality upgradation.
Sunil Kumar also emphasises that policy incentives can help offset the costs associated with compliance and make sustainability upgrades more finan-
cially feasible for MSME pharma companies.
Light at the end of the tunnel?
Given the challenges, Mehrotra from EY India reminds us that the path towards sustainability is not a sprint but a marathon, demanding unwavering commitment and resilience. He believes that by embedding ESG principles into their DNA, Indian pharma can not only mitigate risks but also drive innovation and foster societal well-being. As he puts it, “The green pill beckons and the time to heed its call is now,” referring to R&D efforts that are yielding breakthroughs in sustainable drug delivery systems and biodegradable packaging. Going forward, Lupin’s Swaminathan projects that the company is aspiring to build a 'Transformational Journey in Sustainability'. “Our focus is to empower employees to drive sustainability not only by metrics or setting ESG goals; we are looking at fostering a sense of purpose, community, and urgency. We believe by creating a culture that supports sustainability, organisations can unlock the full potential of their workforce and make a lasting impact on the planet.”
Shivshankar believes that the industry is moving in the right direction, with visible gains already being seen. “We must continue to work collectively to achieve this goal (of reducing overall carbon footprint), ensuring clear communication and complete transparency” is his call to action.
Summarising the many benefits of embracing sustainable practices across production, R&D and supply chains, SIPL’s Sunil Kumar says, “In my opinion, those companies that proactively addressed sustainability and regulatory requirements were better positioned to comply with evolving regulations and avoid potential fines or operational disruptions.”
Thus while larger pharma companies are well on the sustainability path, mid-size and smaller companies can leapfrog early teething problems by exploring the learnings from these front-runners. Adapting and adopting best practices will need to become an urgent imperative to make sustainability part of their strategic growth plans.
viveka.r@expressindia.com viveka.roy3@gmail.com
and photographs,wherever relevant.
❒ We welcome information on new products and services introduced by your organisation for our various sections: Pharma Ally (News, Products,Value Add),Pharma Packaging and Pharma Technology Review sections.Related photographs and brochures must accompany the information.
❒ Besides the regular columns,each issue will have a special focus on a specific topic of relevance to the Indian market.
❒ In e-mail communications,avoid large document attachments (above 1MB) as far as possible.
❒ Articles may be edited for brevity,style,and relevance.
❒ Do specify name,designation,company name,department and e-mail address for feedback,in the article.
❒ We encourage authors to send their photograph.Preferably in colour,postcard size and with a good contrast.
Email your contribution to: The Editor, Express Pharma, Business Publications Division, The Indian Express (P) Ltd, Mafatlal Centre,7th floor, Ramnath Goenka Marg, Nariman Point,Mumbai 400021 viveka.r@expressindia.com viveka.roy3@gmail.com
As pharma manufacturing evolves to meet dynamic market demands,regulatory shifts and technological advancements, Kavita Jani highlights how effective skilling and training stratergies will be crucial to build a resilient and future-ready workforce
Known as the “Pharmacy of the world”, India is a hub for pharma manufacturing and occupies a hefty 20 per cent share in the global generics volume supply by manufacturing 60,000 different generic brands across 60 therapeutic areas. The industry is poised for considerable growth in the near future and is expected to reach $130 billion by 2030 (currently valued at $50 billion) (1).
With an aim to become more value-driven, India’s pharma in-
dustry is looking beyond generics, targeting innovations in drug development. Such ambitious goals will require robust strategies, and to implement those strategies, the pharma industry will require a resilient and future-ready workforce. India Pharma Inc., must therefore focus on optimising and refining its current processes and practices from the bottom up especially, as a sector that contributes greatly to public health and enhances the overall quality of life.
As a core component of the pharma industry, manufacturing and its associated practices need to constantly upgrade and adapt to the industry's changing trends. Minimising human errors, keeping up with the evolving market demands and regulatory landscapes and adapting to technological advancements are the paramount goals for manufacturing. Therefore, the industry needs to focus on upskilling its shop-floor workforce.
An article by CLR titled
“Skill Gap Analysis of Indian Pharmaceutical Sector” informs, that since a majority of the pharma manufacturing units are located in remote regions, not many are willing to relocate to these areas for employment. Therefore, securing and deploying a skilled workforce with highly specialised skills to ensure Good Manufacturing Practices (GMP) and Good Clinical Practices (GCP) becomes challenging.
Fortunately, recognising the imperative for skilled talent, the
industry is working on ways to plug the talent gap through skilling, reskilling and upskilling initiatives. As per a 2024 Employment outlook report by TeamLease, 86 per cent of Healthcare and Pharma employers have shown serious intentions of expanding their workforce driven by ongoing health demands, the surge in digital education and addressing growing industry needs (2).
Let’s look at a few measures that are crucial to nurturing a skilled workforce.
Bridging the industry-academia gap Industry and academic experts agree that industry readiness and job-specific skilling should begin from the academic level. But, they also admit that the current curriculum and teaching approaches need reform to put this into practice. Sumedha Nadkar, Pharmaceutical Consultant and NMIMS - Visiting Faculty Quality & Regulatory Affairs says that internship opportunities are provided to B.Pharm and M.Pharm students by pharmacy colleges. But, pointing out the challenges, she informs “NM College SVPTMhas a non-teaching staff member dedicated to look after placements. Most colleges are not so fortunate and some teaching faculty have to carry out this task while balancing their regular work (syllabus completion/exam paper setting /checking), and preparing for audits like NIRF, and NAAC.” Therefore, this becomes an arduous task.
Nadkar points out, “Rural pharmacy colleges need more attention. Students here lack the basic English communication skills and require direction on career options,” highlighting the need to improve skilling in institutes at the tier-2 and tier-3 levels. Recommending measures to deal with this issue, she says, “The Ministry of Education/ Rural Development/ Science and Technology can collaborate and invite applications from industry consultants and senior management to host sessions and internship programmes.” Simultaneously, Nadkar also stresses adequate training of the faculty, emphasising their lack of exposure to the industry. To aid industry-academia interactions, she suggests hosting student interactions with the alumni, depending on the alumni’s authority and influence in their organisation. Such interactions can also pave the way for internship or employment opportunities.
Explaining the initiatives that the industry must take to bridge the industry-academia gap, Dr Viranchi Shah, National President, IDMA, stated, “Practical training, classroom training, and involvement in cross-functional teams are some basic things that
the pharma industry does. Interacting and engaging with ITIs, pharmacy colleges and other academic institutions is also on the rise, to ensure that the new entrants to the industry are industry-ready. The overall principle is continuous training and engagement at the lowest possible level and continuous interaction with academic institutes.”
Need for apprenticeships
Sumit Kumar, Chief Strategy Officer, TeamLease highlights apprenticeships as a successful
The Ministry of Education/ Rural Development/ Science and Technology can collaborate and invite applications from industry consultants and senior management to host sessions and internship programmes
Sumedha Nadkar
Pharmaceutical Consultant and NMIMS - Visiting Faculty Quality & Regulatory Affairs
Providing on-the-job training alongside formal education,apprenticeships ensures that the workforce is well-prepared to meet future challenges
Sumit Kumar
Chief Strategy Officer, TeamLease Shop floor workers are the most fundamental contributor to the success or failure of any organisation
Dr Viranchi Shah
National President, IDMA
strategy to skill fresh talent for the pharma industry and bridge the industry-academia gap. “Unlike traditional education pathways, apprenticeships provide a unique blend of on-the-job training and theoretical instruction, ensuring that participants develop practical skills that are immediately applicable in the workplace,” says Kumar. This model is especially beneficial in the pharma sector, where roles like bioprocessing technicians, quality control analysts, and regulatory affairs specialists are be-
coming increasingly crucial. Kumar explains how major pharma companies in the UK have implemented apprenticeship programmes as an effective way to nurture a skilled workforce, ensuring that employees are well-trained and abreast with the latest industry practices. This model has proven to be cost-effective, allowing companies to tailor the training to their specific needs, resulting in a highly competent workforce that is ready to contribute to the industry's growth.
We have similar examples on the domestic front as well. For instance, Dr Reddy’s Laboratories’ concept of ‘Self Management Teams’ (SMT). The company informs that the initiative aims to “create an energetic, vibrant workforce capable of handling plant operations seamlessly.” A Dr Reddy’s spokesperson informs, “Since 2001, through SMT, we have trained over 4,500+ youth (10+2 candidates) from economically weaker sections to help them join mainstream professional life. SMT is an initiative aimed at building an agile and empowered workforce, by providing employment opportunities, appropriate education and training/skilling to create a more engaged and flexible workforce whilst providing livelihood opportunities.”
Thus, apprenticeship programmes act as a talent pipeline builder, providing a great model to address niche manpower shortages, and a steady stream of skilled individuals ready to take on the challenges of tomorrow. In India, the pharma sector has witnessed an expansion in apprenticeship programmes as well. According to TeamLease, the apprenticeship engagement in the sector has grown 25 per cent year-on-year in the last two years to reach 22,731 in 2023-24. Kumar says, “These programmes cover a wide range of roles including lab technicians, drug safety analysts, and retail pharmacy chemists, and have been supported by government initiatives such as the Skill India Mission and the National Apprenticeship Promotion Scheme (NAPS).” He emphasises that these programmes aim to not just fill up job vacancies but also aim to build capacity and capability within the life sciences sector.
“Providing on-the-job training alongside formal education apprenticeships ensures that the workforce is well-prepared to meet future challenges, particularly in areas like digital manufacturing, data analytics, and AIdriven drug discovery,” says Kumar.
Upskilling to build competency
The second stage of training is
September 2024
skilling the freshly acquired talent according to their job role and upskilling the long-term workers to enhance their adaptability to the dynamic and developing nature of the industry. Advancing technology, increasingly diverse demands and the changing regulatory landscape demand for the workforce to be adaptable, well-versed with the latest technological advancements, and regulatory compliance.
As per a USFDA Congressional report published in 2020, India stood the lowest among India, the EU, the USA, China and the rest of the world with only 86 per cent of drug facility inspections with acceptable outcomes (3). Moreover, during 2023 and 2024, 35 Indian companies re-
We aim to ensure that our manufacturing teams are not only prepared for current challenges but also equipped to handle future advancements and regulatory shifts in the industry
Rajendra B Chunodkar President – Manufacturing Operations, Lupin
”As a talent pipeline builder,apprenticeship programmes are a great model to address niche manpower shortages,providing a steady stream of skilled individuals ready to take on the challenges of tomorrow”
but also implement methods that can enhance the competency of regulatory compliance to the shop floor workers.
Highlighting the crucial role of the shopfloor workers, Shah says, “Shop floor workers are the most fundamental contributor to the success or failure of any organisation.” Considering that real quality is built by workers, operators and supervisors who work on the shop floor, Shah adds, “The major gap as far as manufacturing operations is concerned is in getting skilled machine operators, and also in skilled people on ground-level QMS implementation.”
With the increasing influence of automation, digitalisation, and the increasingly precise and technologically advanced equip-
Fortuitously, the industry is taking several measures to provide on-the-job training to its employees. Rajendra B Chunodkar, President – Manufacturing Operations, Lupin provides insights into what strategies Lupin implements to ensure its employees are prepared for audits. “We regularly conduct mandatory training sessions on regulatory standards, audit procedures, and the latest guidelines from regulatory bodies such as FDA, EMA, and CDSCO.” He highlights how Gemba walks and internal mock audits aid in simulating real-world scenarios and encourages quick thinking and cross-functional collaboration to ensure that all Lupin’s departments are aligned and prepared for audits and regulatory inspections.
Chunodkar adds, “We have taken a holistic approach to peo-
ple development for shop-floor personnel, including training on 5S Methodology and Six Sigma green belt and black belt training, language training for our shop floor operators, hyper-personalised communication coaching, and gamified learning for SOPs, GMPs, and Audit Interactions, among others.” This ingrains adherence to regulations into their daily operations.
Additionally, as per a 2024 employment outlook report by TeamLease, there’s a growing demand for niche skills in AI, ML, data analytics, and medical coding to derive healthcare insights and contribute to the ongoing transformation in manufacturing, precision medicine and diagnosis (2). These sophisticated tools can help focus on
lean manufacturing practices, reduce waste and improve production efficiency.
Shah explains, “The pharma industry is fast adopting automation and digitalisation, and the involvement of technology in equipment is also increasing. Continuous practical training of the shop floor teams to keep them in pace with the changes is therefore very important.” Therefore, as the pharma sector moves towards digitalisation, leveraging digital technologies to improve productivity, efficiency and innovation becomes increasingly important.
Explaining the methods that Lupin implements, Chunodkar adds, “Our employees receive extensive hands-on training on new technologies, including machinery, software, and automation systems. We also partner with technology providers for
continuous support, updates, and advanced training sessions to keep our teams ahead of the curve.”
Conclusion
Quality control, learning how to operate machinery and the competency of regulatory compliance are some of the governing factors of pharma manufacturing. Given the advancing state of technology, and increasing demand in society for quality medications and treatments leading to a consequential increase in production and evolving regulatory landscapes, the pharma industry must be equipped with a talented and competent workforce, from the ground up. Thus skilling this workforce from its root (i.e.) academia level, and continuing to upskill them as employees is an investment that can guarantee the benefits of an
agile and skilled workforce in the long run.
References
1.https://www.investindia.gov.in/ sector/pharmaceuticals#:~:text= The%20pharmaceutical%20industry%20in%20India%20is%20 currently%20valued%20at%20% 2450,all%20medicine%20in%20t he%20UK.
2. https://group.teamlease.com/ insights/employment-outlook-report-h2-fy24/
3. https://www.fda.gov/newsevents/congressionaltestimony/covid-19-and-beyondoversight-fdas-foreign-drug-man ufacturing-inspection-process06022020
4. https://blog.clrskills.com/skillgap-analysis-of-indian-pharmaceutical-sector/
kavita.jani@expressindia.com kavitanjani@gmail.com
Experts and leaders from the pharma industry congregated to highlight Aurangabad’s role in India’s pharma landscape and discuss issues that are vital for the industry's future growth and success
Express Pharma recently organised the inaugural edition of the Aurangabad Pharma Summit 2024 with a vision—to cocreate an ecosystem that fosters innovation, excellence, and growth within the pharma sector.
It brought industry leaders, innovators, and experts from the city to discuss and explore its rich legacy in manufacturing and industry, and its emergence as a hub of pharma excellence.
Over the course of this summit, experts explored key topics that are critical to the pharma industry’s progress—from advancements in digital technologies to sustainable practices, regulatory challenges, and beyond. These discussions are not just timely but essential as we navigate an era of rapid change and unprecedented challenges.
The event also offered opportunities galore for networking and interaction.
It kickstarted with a lamplighting ceremony and a welcome address from Express Pharma.
L-R: Dr SanjayToshniwal,Central Council Member,PharmacyCouncil of India; Pradipkumar N Patil,VP– Quality,Ajanta Pharma; Dr Prashant Musmade,Data ReliabilityOfficer,GlenmarkPharmaceuticals; Zoher Sihorwala,Senior VP& Head – Global Regulatory Affairs,Wockhardt; Dr Varda Bapat,COO,RVLifesciences; Sumeet Sharma,Sales Director,Cilicant; and Sunil Khera,Ex-President, Wockhardt Americas
Komal Bhavsar, AGM-Business Development, Cilicant, gave a compelling presentation on ‘Innovations in active packaging’ at the Aurangabad Pharma Summit 2024. The session focused on the latest advancements in active packaging technology and their impact on the pharma sector. Bhavsar highlighted how these innovations are crucial in ensuring product stability, extending shelf life, and improving patient safety.
Bhavsar emphasised the growing importance of intelligent active packaging solutions and elaborated on Cilicant's offerings to meet the evolving demands of the industry. The presentation provided an in-depth look into how active packaging not only protects but also interacts with the contents, thereby preserving their efficacy and safety.
Her presentation spotlighted Accuflip, a humidity regulator provided by Cilicant. She informed that this product plays a crucial role in maintaining the
Komal Bhavsar,AGM-Business Development,Cilicant
ideal moisture levels within capsules, preventing them from becoming too dry or overly moist. This control over humidity is vital for ensuring the stability, effectiveness, and efficiency of pharma products.
She also showcased Cilicant's FREXIL dust-proof canisters. Bhavsar explained that these canisters were developed in response to the common issue of dusting associated with activated carbon-based canisters. The FREXIL canisters are designed with a patented technology that not only safeguards pharma products from potential contaminants but also eliminates the dusting problem, which is a critical concern in maintaining the cleanliness and safety of packaging.
The session concluded with valuable insights on adopting Cilicant's smart active packaging solutions to optimise packaging strategies, enhance product quality and improve customer satisfaction.
The first panel discussion at Aurangabad Pharma Summit focused on Aurangabad's contribution to Maharashtra's leadership in the pharma sector.
This discussion was moderated by Dr Prashant Musmade, Data Reliability Officer, Glenmark Pharmaceuticals; Dr Varda Bapat, COO, RV Lifesciences; Anshu Manocha, Site Head (Executive GM), Indoco Remedies; Dr Sanjay Toshniwal, Central Council Member of the Pharmacy Council of India; and Manoj Patil, DGM-Production, Ajanta Pharma were the other other esteemed panelists for this discussion. They shared their insights on the region's strategic importance and future potential.
The moderator steered the conversation through pertinent aspects such as Aurangabad's growing role as a hub for pharma manufacturing and research, and the need for continued investment in infrastructure, talent development, and regulatory support to leverage the city’s true potential. The panelists also dispelled fears among the audience that Aurangabad is losing its position as a pharma hub due to falling investments. They emphasised that the city has attracted significant investments from leading pharma companies due to a favourable business climate.
The availability of skilled manpower in Aurangabad was also underscored as a competitive advantage. Panelists stressed on the importance of developing this talent pool through partnerships with academia to build a future-ready workforce that is aligned with evolving industry requirements. They also highlighted the need for pharma education to evolve and transform to keep pace with changing market demands and technological advancements.
The discussion also addressed how technology has streamlined operations in pharma and enhanced the industry's capacity to meet global standards. Citing examples, they pointed how realtime monitoring of systems and equipment through advanced technology has helped reduce manual errors, ensure better regulatory compliance, and improve product quality.
Robust IPR protection to incentivise innovation, protect against infringe-
Dr
ReliabilityOfficer,GlenmarkPharmaceuticals (Moderator); Dr Varda Bapat,COO,RVLifesciences; Anshu Manocha,Site Head (Executive GM),Indoco Remedies; Dr SanjayToshniwal,Central Council Member,PharmacyCouncil of India, NewDelhi; Manoj Patil,DGM-Production,Ajanta Pharma
◆ Automation and digitalisation in the pharma industryhas ushered real time monitoring of systems and equipment,reduced manual errors,and ensured better regulatorycompliance and qualityof products
◆ Astrong IPR incentivises innovation,protects against infringement,and gives a competitive edge to pharma companies
◆ Aurangabad's skilled manpower,access to critical resources like water and transport,a conducive business climate, favourable government policies make it a keyhub for the pharma sector
◆ Industry-academia collaborations are crucial for the industry's progress.Theywill help create industry-readytalent, encourage innovation,and drive value creation faster and more effectively
◆ Pharma education has to evolve and transform to keep pace with changing market demands and advancements in technologyto create a future-readytalent pool
ment, and provide a competitive edge to pharma companies was also recommended by the expert panel to attract
more investments and foster a culture of innovation.
The panel discussion concluded on an optimistic note and the experts called for sustained efforts to capitalise on Aurangabad’s potential.
Zoher Sihorwala, Senior VP & Head of Regulatory Affairs at Wockhardt gave an inspiring session on ‘Uniting industry leaders for innovation and collaboration’ at Aurangabad Pharma Summit 2024 which explored approaches to foster a collaborative environment in pharma. He emphasised the importance of excellence in one's work and the dignity of labour.
Speaking about the drug development process, he highlighted the need for collaboration at various levels to drive pharma innovation. He cited several industry collaborations including: Wockhardt-Serum Institute partnership for vaccine manufacturing and distribution; Dr Reddy's-Natco collaboration for cancer treatment accessibility; and Bharat Biotech, ICMR, and CDSCO's joint effort in developing a
COVID-19 vaccine etc.
Sharing his perspective on modern leadership, Sihorwala opined that the traditional command-and-control model is outdated and advocated for a synergy-driven approach focusing on empowerment and coaching to foster innovation.
The presentation concluded with Sihorwala advising the attendees to connect the right dots in the right way to drive innovation.
Thus, this insightful presentation emphasised the critical role of collaboration, both within and across organisations, to meet unmet patient needs and tackle global health challenges like pandemics. He highlighted how strategic partnerships can enhance manufacturing capacity, improve product accessibility, and accelerate the development of life-saving treatments.
At the Aurangabad Pharma Summit 2024, Dr Abhijit V Gothoskar, Technical Expert, Sigachi Industries, gave an informative presentation on ‘Tablet compressibility, MCC and techtonic shift.’ His session addressed some pressing challenges in tablet manufacturing, and examined the role of excipients in ensuring tablet quality and regulatory compliance.
Dr Gothoskar highlighted the critical issue of tablet failures during the manufacturing process, a problem that has increasingly come under the scrutiny of regulatory bodies. He pointed out that observations related to these failures, often captured in the FDA's Form 483, can have significant implications for pharma companies. He also spoke about the issue of nitrosamines and explained that choosing the right excipient can be crucial to tackling this issue.
He elaborated on how the strategic selection and use of excipients can lead to more robust tablet formulations, which not only meet regulatory requirements but also ensure product efficacy and patient safety.
The session also addressed how Mi-
Dr Abhijit Gothoskar,Technical Expert,Sigachi Industries
crocrystalline Cellulose (MCC) is a multifunctional and time-tested excipient widely used in tablet formulations. Dr Gothoskar highlighted its versatile properties like excellent compressibility, binding capability, and contribution to tablet integrity and stability. He ex-
plained how MCC's role as an excipient is crucial in overcoming common tablet manufacturing challenges, thereby ensuring consistent quality and performance.
Moreover, Dr Gothoskar emphasised that Sigachi Industries can be a reliable
Excipient performance is rarely understood fully and often underestimated. MCC is the time tested and proven multi-functional exicipient.Sigachi can be a trusted formulation partner and solutions provider
formulation partner for pharma companies. He assured that Sigachi offers high-quality excipients like MCC as well as valuable expertise to help navigate the complexities of tablet formulation.
Pradipkumar Patil, VP – Quality, Ajanta Pharma shared insights on innovations in pharma manufacturing at the Aurangabad Pharma Summit 2024. He highlighted the latest trends and technologies that are transforming pharma production, potentially reducing costs and improving quality.
Focusing on ways to improve pharma production, Patil highlighted key areas of innovation across materials, processes, and equipment.
He addressed innovations in drug formulation, including optimising the size, shape, structure, and solubility to enhance drug effectiveness. He also spoke about coating materials with a focus on controlling drug release, protection against degradation, and more environmentally friendly solutions.
Patil also shared insights on process innovations including the use of laser drilling for controlled-release drugs and the development of dry mixing processes to replace traditional wet granulation methods. He pointed out that these innovations can improve pro-
Pradipkumar Patil,VP– Quality,Ajanta Pharma
ductivity by reducing process time and costs while protecting drugs from degradation. Advancements in pellet and powder coating techniques were also highlighted.
The presentation covered automa-
tion of pharma manufacturing equipment. The expert shared how automation plays a crucial role in modernising and optimising pharma operations, expediting investigation and decision making.
At the Aurangabad Pharma Summit 2024, Hrishikesh Gadve, Assistant Manager – Sales & Marketing, Ami Polymer delivered an insightful presentation on the critical role of polymer solutions in the drug manufacturing process. He shared details about the diverse range of polymeric products offered by Ami Polymer, specifically designed to meet the stringent demands of the pharma and biopharma industries. He emphasised the importance of choosing the right tubing and other polymer-based components to ensure safety, efficacy, and compliance with regulatory standards in the life sciences industry. He also addressed how different types of tubing and hoses are used in the life sciences field, emphasising that various drugs require specific solutions.
During the presentation, Gadve shared information about an array of products, including silicone, TPE, and fluoropolymer tubings, etc. He emphasised that these products are meticu-
Hrishikesh Gadve,Assistant Manager – Sales & Marketing,Ami Polymer
lously developed to ensure they meet international standards and tests, providing the pharma industry with reliable
solutions that uphold the highest standards of safety and efficacy.
Automation plays a crucial role in moderinising and optimising pharma operations, expediting investigation and decision making
The speaker cited examples of modernised tablet compression machines and coating equipment. He stressed on the importance of ensuring all equipment and instruments are 21 CFR Part 11 compliant.
The session provided an overview of how innovat ion is reshaping pharma manufacturing.
AMI Polymer,with its extensive range of polymer and tubing solutions tailored for various pharma processes, is a reliable partner for the pharma industry
Gadve assured the audience that Ami Polymer is working on further enhancing their product offerings to better serve the evolving needs of the pharma industry. In conclusion, he emphasised that Ami Polymer is ready to assist the pharma industry in finding the right polymer solutions for their drug manufacturing needs.
The panel discussion on "Fueling growth and innovation with R&D," held at the Aurangabad Pharma Summit 2024, focused on the critical role of R&D in driving growth and innovation in the pharma sector. The discussion was moderated by Prof Pravin S Wakte, Director, Central Facility for Advanced Research and Training, Dr Babasaheb Ambedkar Marathwada University; while Dinesh Shinde, Associate Director - Formulation Development & Tech Transfer, Wockhardt; Sachin Salampure, Associate Director - CMC & Formulations, VedTechBio; Jitendra Chordiya, Head-Formulation R&D, Harman Finochem; and Sachin Kulkarni, Works Manager, FDC were the other panelists.
The discussion offered several insights on emerging trends, challenges, and strategies in pharma R&D. It expored the growing concern of antimicrobial resistance (AMR), and looked at Aurangabad's role in developing the next generation of antimicrobials. The experts also highlighted the need for continous innovation and robust R&D to tackle AMR effectively.
The panelists also conversed on the impact of emerging technologies like artificial intelligence (AI) and data analytics on pharma R&D. They examined how these technologies are reducing costs, improving decision-making through enhanced data insights, and accelerating innovation. The experts unanimously agreed that integrating AI into R&D processes is not just a trend but an imperative for companies to gain a competitive edge in the rapidly evolving pharma landscape.
They also underscored the importance of optimising and accelerating pharma R&D through strategic investments and meaningful collaborations and called for greater industry-government partnerships. The panelists also pointed out that timely policies could boost R&D outcomes. The potential of public-private partnerships (PPPs) to drive faster development of novel therapies was accentuated as well during the course of the discussion.
The expert panel addressed the importance of building academic centers of excellence and recommended collaboration between academia and industry to foster innovation and ensure creation of industry-ready talent.
There was considerable emphasis on
L-R: Prof Pravin Wakte,Director,Central Facilityfor Advanced Research and Training; Dr Babasaheb Ambedkar Marathwada University (Moderator); Dinesh Shinde,Associate Director - Formulation Development & Tech Transfer,Wockhardt; Sachin Salampure,Associate Director - CMC & Formulations,VedTechBio; Jitendra Chordiya,Head-Formulation R&D,Harman Finochem; Mr Sachin Kulkarni,Works Manager,FDC
◆ AMR is a rapidlygrowing health concern.And,Aurangabad is a major centre developing the next generation of antimicrobials
◆ Emerging technologies like AI and data analytics is transforming pharma R&D byreducing costs,improving decision making through data insights,and accelerating innovation
◆ Accelerating and optimising pharma R&D is a keygoal.This can be done byeffectivelyutilising emerging technologies, strategic investments,meaningful collaborations and timelypolicies from the government
◆ Building academic centres of excellence,PPPs in R&D could usher better and faster R&D outcomes and help develop novel therapies
◆ Driving sustainabilityin pharma R&D is a social and business imperative.Efficient processes,reduced waste,eco friendly rawmaterials,proactive practices like repurposing of drugs can help cultivate a sustainable mindset in pharma R&D
the need for sustainability in pharma R&D as well. The thought leaders discussed how adopting efficient processes, reducing waste, using eco-friendly raw materials, and repurposing existing drugs
can help cultivate a sustainable mindset within the industry. They stressed that sustainability is not only a social responsibility but also a business imperative that can drive long-term success.
The panel concluded with a consensus that Aurangabad, with its strong research capabilities and innovative spirit, is wellpositioned to lead in the next wave of pharma advancements.
In an interview with ExpressPharma, Dr Ankit Varshney,Founder & Director of Bioaltus Pharmaceuticals,discusses Bioaltus Pharmaceuticals' vision,strategic initiatives,and commitment to becoming a global leader in Lifecare through innovation and a robust supply chain
Can you elaborate on your company’s vision? What are the key strategic initiatives that have contributed towards expansion and strengthening of your foothold in the pharma industry?
At Bioaltus Pharmaceuticals, our vision is to be a global leader in providing quality and affordable Lifecare through innovation and an integrated supply chain. We are committed to making healthcare accessible worldwide by investing in R&D, new upcoming OSD Plant, streamlining our supply chain, forming strategic partnerships, ensuring top-tier quality standards, and expanding into new markets. These initiatives fuel our growth and reinforce our dedication to being a global leader in Lifecare.
How do you tailor your products/services to meet the specific needs and demands of different partners and markets?
We understand that each partner and market has unique needs, especially in the thirdparty manufacturing sector. We prioritise flexibility, customisation, and collaboration by developing tailored product formulations, adjusting dosage forms, and ensuring that our packaging aligns with specific market demands. We also adhere to both local and international regulatory standards, enabling our partners to confidently distribute products across diverse regions.
Our scalable manufacturing allows us to meet varying production demands without compromising quality, and our integrated supply chain
ensures timely, cost-effective delivery. By continuously collaborating with our partners, we stay attuned to their evolving needs, offering innovative solutions that support their business goals. To further meet customer expectations, we are expanding our operations with a new plant in Sarigam, Gujarat enhancing our capacity and reinforcing our position as a trusted thirdparty manufacturer in the pharmaceutical industry.
How do you ensure high quality and efficacy of your formulations? Can you tell us about some milestones in the company's journey since inception?
Bioaltus Pharmaceutical's journey is a testament to its commitment to innovation and growth within the pharmaceutical industry. Founded with a vision to address unmet Quality Formulation needs through cutting-edge science, the company began as a small research-focused entity. Early successes in developing Imikro Nano technology in Metformin Combinations for Diabetes attracted patients & doctors for its Small size Tablets, enabling Bioaltus to expand its research and development efforts. Over the years, the company diversified its portfolio, entering areas such as cardiology, nephrology, immunology, neurology and Pain Management. New Dcgi Molecules and regulatory approvals for major drugs marked significant milestones in its evolution from a researchfocused entity to a global commercial pharmaceutical company.
As Bioaltus grew, it
maintained a strong focus on innovation, investing heavily in advanced technologies & New DCGI Molecules like Teneligliptin , Sitagliptin , Sacubitril-Valsartan Etc . Despite facing challenges, the company's resilience allowed it to overcome obstacles and continue its growth trajectory. Recent years have seen further expansion, with new drugs receiving regulatory approval and increased global presence through strategic collaborations. Looking forward, Bioaltus is poised for continued success, with a robust pipeline of new drugs and a commitment to exploring emerging therapeutic areas and technologies, ensuring it remains at the forefront of the pharmaceutical industry.
Can you share more about your key partnerships in the pharma sector and how these collaborations enhance healthcare outcomes? What makes you a preferred partner for pharma companies?
Our key partnerships with leading pharmaceutical companies and research institutions are fundamental to our success and our ability to enhance healthcare outcomes
globally. These collaborations allow us to leverage shared expertise, access cutting-edge research, and bring innovative, cost-effective solutions to the market more efficiently.
Our partners choose Bioaltus because of our unwavering commitment to quality & delivery’s, our ability to customise products to meet specific market needs, and our robust, scalable manufacturing capabilities. We offer end-toend solutions, from product development to distribution, ensuring that our partners can focus on their core strengths while we handle the complexities of manufacturing and regulatory compliance.
What sets us apart as a preferred partner is our proactive approach to understanding the unique challenges of each partner and market. We invest in building long-term relationships based on trust, transparency, and mutual growth. Additionally, our ongoing expansion, including the new plant in Sarigam, Gujarat, demonstrates our commitment to meeting the evolving needs of our partners and ensuring we continue to deliver highquality products on a global scale.
What are your plans for growth in the next 5-10 years?
How do you foresee the evolution of the pharma CDMO industry, and what role do you see your company playing in that future?
Over the next 5-10 years, Bioaltus Pharmaceuticals plans to significantly expand our global footprint by scaling our manufacturing capabilities, entering new international markets, and diversifying our
product portfolio. We foresee the Contract Development and Manufacturing Organisation (CDMO) industry evolving with increased demand for specialised, high-quality, and cost-effective pharmaceutical solutions. As the industry shifts towards more complex and personalised medicines, we aim to be at the forefront, leveraging our innovationdriven approach and integrated supply chain to meet these demands. Additionally, we are investing in Plants as part of our growth strategy, which is needed to fuel our expansion and solidify our position as a global leader in the pharma CDMO sector.
What initiatives do you have in place to foster innovation and continuous improvement within your organisation?
We are committed to fostering innovation and continuous improvement by creating an environment that encourages creativity and collaboration. We promote open communication and idea sharing, regularly conducting brainstorming sessions and workshops to leverage diverse perspectives. Our investment in ongoing training and development ensures our team remains updated on industry trends and technologies. We also prioritise cross-functional collaboration to drive process improvements and innovative product development. By actively seeking feedback from our partners and customers, we adapt our offerings to better serve the market. Through these initiatives, we aim to enhance operational efficiency and drive us toward our vision of becoming a global leader in Lifecare.
Nikhil Agarwal,President,CJ Darcl Logistics explains that the future of pharma logistics is a thrilling frontier shaped by technological advancements,regulatory challenges,and the imperative of sustainability.As the industry transforms,logistics providers must embrace innovative solutions and adapt to shifting demands
India's pharmaceutical industry, renowned as the "Pharmacy of the World", is a cornerstone of global healthcare. Statista forecasts that revenue from the domestic pharma market is set to reach $13.16 billion in 2024. This growth is driven by factors such as increasing healthcare awareness, rising incomes, expanding healthcare infrastructure, and government initiatives to improve healthcare access. Furthermore, India's pharma market size is projected to reach $450 billion by 2047. As of June's report, the Indian pharma market delivered a healthy revenue growth of 8.8 per cent year-on-year.
As the logistics industry undergoes rapid transformation, driven by modern technologies and innovative solutions, the role of logistics in the pharma sector is becoming increasingly critical. This article explores the emerging trends, persistent challenges, and opportunities shaping the future of pharma logistics.
Pharma logistics is a multi-layered ecosystem involving numerous stakeholders, including manufacturers, suppliers, distributors, and end-users. Coordinating these stakeholders throughout the process—from preparing the shipment to final delivery—requires precise endto-end operation. Any disruption can lead to significant financial losses and, more importantly, impact patient safety. A deep understanding of local and regional regulations, along with meticulous planning, is essential.
Digital transformation is enhancing the pharma supply chain in India. The next stage of the industrial revolution, Industry 5. 0, is expected to bring a significant revolution in the way the supply chain operates. Unlike Industry 4. 0, which focuses on automation and smart technologies, Industry 5. 0 aims to facilitate a synergy in human and artificial intelligence. This paradigm shift is especially applicable in the pharma industry since accuracy, respect for the patient, and moral standards are critical in this sector.
A recent survey by GlobalData reveals that there is a significant increase in the companies who are undergoing a digital transformation, 89 per cent of the pharmaceutical companies are now implementing or developing digital innovations. End-to-end visibility has become a vital component of modern pharmaceutical logistics. From the planning stage to final delivery, full visibility ensures that all stakeholders can monitor the shipment's progress in real-time. This visi-
bility is crucial for insurance, quality assurance, and responding to potential disruptions during transit.
Temperature-controlled packaging equipped with advanced technology is now a standard practice in the industry. These packages aids with the longevity of products such as pharma, biologics, vaccines, etc. They are designed to capture real-time data on temperature and other environmental factors, providing valuable insights into the challenges faced at each stage of the shipping journey. The integration of Internet of Things (IoT) and robotics into pharma logistics is another trend gaining momentum. IoT devices monitor various aspects of the shipment, such as temperature, humidity, and location, in real-time. Robotics enhances the efficiency of warehousing operations by automating tasks such as picking, packing, and sorting. Together, these technologies contribute to a more streamlined and reliable supply chain, reducing human error and improving overall efficiency.
Despite technological advancements, pharma logistics still faces several significant challenges. Regulatory compliance is a major hurdle, as logistics providers must navigate a complex and often fragmented regulatory landscape. Non-compliance can lead to delays, fines, and even the destruction of valuable products, making it a critical focus for logistics providers.
Infrastructure limitations are another challenge that cannot be overlooked. In many parts of the world, the logistics infrastructure—particularly for cold storage and transportation—is still developing. This can lead to inefficiencies and higher costs, especially when transporting temperature-sensitive pharma products. Investing in better infrastructure, such as state-ofthe-art warehousing facilities and more reliable transportation networks, is essential for improving the efficiency of the pharma supply chain.
The rise of e-commerce and the growing trend of direct-topatient deliveries, has enhanced last-mile delivery. However, it presents its own set of challenges, often being the most costly and complex component of the logistics chain. In the pharmaceutical industry, lastmile delivery is not a one-sizefits-all model. As the demand for personalised medicine and advanced therapies grows, the challenges associated with lastmile delivery are likely to become even more pronounced.
Despite these challenges, the fu-
ture of pharma logistics is filled with opportunities for growth and innovation. As the pharma sector becomes increasingly competitive, optimising the supply chain is crucial. This involves streamlining processes, reducing cycle times, and improving inventory management. Logistics companies that can offer innovative solutions to enhance supply chain efficiency will be well-positioned for growth. The continued development and implementation of technologies such as robotic process automation (RPA), warehouse automation systems, temperature sensors, RFID tags and predictive modeling offer significant potential for improving the reliability and transparency of the supply chain. As the industry moves towards greater sustainability, logistics providers have the opportunity to adopt eco-friendly practices. This includes reducing the environmental impact of transportation by optimising routes, minimising empty returns, and utilising multimodal transportation.
The future of pharma logistics is a thrilling frontier shaped by technological advancements, regulatory challenges, and the imperative of sustainability. As the industry transforms, logistics providers must embrace innovative solutions and adapt to shifting demands. Seizing the opportunities presented by new technologies and confronting persistent challenges, the pharma logistics sector can ensure the safe, efficient, and sustainable delivery of vital products to those who need them most.
FEATURES
Pharma&LifeScienceExtrusion
Thesmallextruder
Formmastering big challen
-C3PROFILE:CLEAN,CLEVER,COMPACT
-EASYHANDLING,SIMPLE(DIS)ASSEMBLY,GOODCLEANABILITY
-SUITABLEFORTHROUGHPUTSOF50TO1,000G/H
-EASYSCALEUP
-INNOVATIVECOOLING/HEATINGSYSTEM
-HORIZONTALLYSPLITBARRELS
FROMSMALLSCALE
TOLARGESCALE
Seeking solutions to overcome any of the following challenges?
Transform your concept into a market-ready product
Streamline your formulation process
Boost the benefits of your formulations
Integrate cutting-edge ingredients
Align an exciting product with global trends
Whether you need a product that offers a remarkable experience with fewer ingredients or ones that protect our skin microbiota, we are here to support you, every step of the way
We are VIMAL, your reliable ingredient partner with global footprint
*Foracompletelistofscientificresearchandfurtherinformationvisitourwebsiteatwww.pycnogenol.com.Pycnogenol®,Frenchmaritimepinebarkextract, isaregisteredtrademarkofHorphagResearchanditsapplicationsareprotectedbyU.S.patentsandotherinternationalpatents.©2024HorphagResearch.
Nowavailable!
Best-in-classosmolalityperformance, designedwithyouinmind.
HIGHLIGHTEDFEATURES:
Offersthewidestrangeofosmolalitytesting(0–4000mOsm/kgH2O)
Supports21CFRpart11,GMPandEUAnnex11compliance
MeetsPharmacopeiaosmolalitytestingguidelines
3Leveluseraccessandpasswordprotection
Storage:unlimiteddatastorageforaccess
Audittrail:Preserveunlimitedresultsandevents
Databasebackup,protectsyourdatawithautomaticormanualbackup
No.127,BussaUdyogBhavan,TokershiJivrajRoad,SewriWest,Mumbai-400015, Maharashtra,Landline:+91022-24166630Mobile:+919833286615
Romaco Tecpharm has developed a new energy recovery system (ERS) for tablet coaters. This innovative technology reduces thermal energy consumption (steam, hot water, oil or electricity) by up to 50 per cent. Moreover, the temperature of the outlet air is significantly lower. An integrated energy monitor measures all consumption in real time and determines the precise energy saving potential.
Romaco Tecpharm’s new energy re covery system (ERS) enables up to 50 per cent savings in thermal energy consumption during tablet coating. The technology is based on the recovery of waste heat generated during the coating process. A cross-flow plate heat exchanger is integrated into the tablet coater’s air handling unit (AHU) for this purpose. The inlet and outlet air flows in this recuperative system cross in opposite directions without coming into contact. To achieve this, the process air flows via separate air ducts which pass through the orthogonal plates of the ERS. The thermal energy is transmitted through these plates, whose rectangular shape guarantees homogeneous and efficient heat exchange. This innovative form of energy recovery for tablet coaters is protected by a utility model.
The coating process gives rise to intensive energy consumption because the tablets have to be sprayed with liquid coating suspension and dried in parallel. In order to dry the tablet bed, very hot and dry air introduced into the coater drum is guided through it. This causes the coating liquid to evaporate on the surface of the tablets, which are simultaneously coated with the solid particles in the coating
Newenergyrecoverysystem (ERS) from Romaco Tecpharm
The newenergyrecoverysystem (ERS) reduces the thermal energyconsumption of Romaco Tecpharm’s tablet coaters byup to 50 per cent
Newenergyrecoverysystem (ERS) from Romaco Tecpharm
suspension.
However, the temperature of the air saturated with steam drops only slightly at this point. This minor temperature loss inside the drum occurs due to the poor thermal conductivity of the tablets. Very warm, energyladen air flows out continuously as a result throughout the coating process. In most cases, this thermal energy simply goes to waste. For the first time, the energy recovery system developed by Romaco Tecpharm will put an end to intrinsic waste of this kind.
In the following case study, the high-energy outlet air is not merely discharged and wasted, but recirculated at a temperature of 45 to 50°C via the plate heat exchanger of the ERS, where it heats the inlet air.
Before flowing through the energy recovery system, the fresh inlet air first of all has to be dried by being cooled down to about 10°C by a cooling coil, resulting in condensation. With a residual moisture content of about 8g/kg, the inlet air now passes through the orthogonal heat exchanger, where it is heated to between 35 and 40°C. It is then heated further until it reaches the process temperature (approximately 70°C in this example). Thanks to the integrated energy recovery system, the temperature difference to be overcome here is only about 30°C; without an ERS, the difference would be in the region of 60°C, in other words twice as much. In short, the energy recovery system enables up to 50 per cent savings in thermal energy – equivalent to a reduction of some 20 per cent in the tablet coater’s total energy consumption.
The heat exchange additionally means a lower outlet air temperature, so that installing a new tablet coater is far easier. After passing through the energy recovery system, the temperature of
Romaco Tecpharm’s new energy recovery system (ERS) reduces thermal energy consumption by up to 50 per cent during tablet coating,significantly lowering both energy use and manufacturing costs
the outlet air has been reduced by more than 50 per cent. In the example described here, it is emitted into the ambient air at around 20°C instead of 45 to 50°C as before.
The ERS’s enormous energy saving potential is most effective in large production machines, which have a proportionally higher air flow per batch. The absolute amount of thermal energy saved is accordingly higher with high throughputs.
This energy saving is accompanied by lower manufacturing costs – a particularly relevant aspect for standard products that are produced in large quantities and have a comparatively low
sales value. As an energy saving measure, the ERS is especially profitable here.
The energy saving achieved with the ERS can be precisely measured and mapped with the help of the energy monitor. This analysis tool records consumption in real time and determines not only the amount of thermal energy saved but also carbon dioxide emissions from the drum coater. The energy monitor provides robust data for the annual sustainability reports which ar e nowad ays a legal requirement for more and more companies. Energy monitoring is integrated in the tablet coater’s HMI panel and can be supplied as an option.
This innovative energy
recovery system is a landmark development on the road to more sustainability in pharmaceutical production. The ERS is available for all original Romaco Tecpharm equipment and can also be integrated into existing systems if required. In 2019 Romaco Tecpharm took the first step towards more climate-friendly coating processes. The manufacturer’s highly automated drum coaters consume significantly less coating suspension, leading to shorter processing times and lower air flow rates – with benefits for both energy consumption and manufacturing costs. Investments in high-tech solutions are not simply worthwhile from an economic point of view – they are also ecologically sustainable and they ease the burden on humanity and the environment.
In December 2023, Romaco Tecpharm received the LA RAZÓN Award for Innovation and Sustainability in the manufacture of pharmaceutical machinery. This award from the leading Spanish daily newspaper LA RAZÓN honors outstanding entrepreneurial achievements in Catalonia.
For more information on Romaco, visit our website and social media channels: www.romaco.com – Showroom – LinkedIn – YouTube
Romaco is a leading international supplier of processing and packaging equipment specialising in engineering technologies for pharmaceutical products. The Group provides individual machines, lines and turnkey solutions for manufacturing, filling and packing powders, granulates, pellets, tablets, capsules, syringes, liquids and medical devices. The company also serves the food and chemical industries. Through its various technologies, Romaco is committed to sustainable production and to systematically reducing CO2 emissions.
The Romaco Group has its headquarters in Karlsruhe
(Germany) and is part of Truking Technology, a globally operating high-tech enterprise based in Changsha (China). Truking’s core competency is handling and filling pharmaceutical liquids.
Romaco operates from six production sites worldwide, with a broad portfolio comprised of seven established product brands. Noack and Siebler (Karlsruhe, Germany) supply blister, heatsealing and rigid tube filling machines. Macofar (Bologna, Italy) markets technologies for filling sterile and nonsterile powders and liquids. Promatic (also Bologna, Italy) specialises in cartoners, track & trace systems and case packers. Kilian (Cologne, Germany) is a leading manufacturer of tablet presses. Innojet (Steinen, Germany) is in the business of granulating and coating fine solid particles. Tecpharm (Barcelona, Spain) offers tablet coating technologies.
More than 930 highly skilled and committed Romaco employees are dedicated to the development of future product technologies and to the continuous implementation of internal improvement processes. The Romaco Group’s multi-brand system solutions are sold worldwide through nine Sales & Service Centers and a dense network of local agent organisations. Over 12,000 installations delivered by Romaco are currently in use in more than 180 different countries.
Company contact Sanjeev Nimkar Managing Director Romaco India Pvt. Ltd.
Press contact
Unit No. 1005, 1006, 1007, Fenkin 9, Plot no. C5, Road No. 9, Behind Satkar Grande Hotel, Wagle Industrial Estate, Thane(W) 400604
Maharashtra India
Tel. +91 22 69207600
E-mail: india@romaco.com
Nilesh B Mahajan,Technical Manager,Shin-Etsu Chemicals,India informs that his company offers application specific selection of suitable enteric polymers (HPMCPand HPMCAS) and grades
Enteric coating constitutes a strategy for the modified release of drugs incorporated in orally administered dosage forms whose primary objective is to guarantee the stability of the drug in aggressive stomach conditions and guarantee its release in the digestive tract.
By preventing the drug from dissolving into the stomach, an enteric coating may protect the gastric mucosa from the irritating effects of the medication itself and prevent gastric distress or nausea from a drug due to irritation. When the drug reaches the neutral or alkaline environment of the intestine, its active ingredients can then dissolve and become available for absorption into the bloodstream. Enteric coating is also an effective method to obtain targeted drug release such as gastro-resistant drugs.
Polymers used in delayed release (DR) design of dosage forms
Acidic polymers are frequently used as enteric coatings in pharmaceutical practice to delay drug release from oral dosage forms, to protect acid labile drugs from harsh conditions in the stomach, or to protect the stomach from irritation by drugs. In the acidic gastric media, an enteric polymer is protonated and therefore insoluble.
As the pH is raised along the intestine, the polymer gets ionised by deprotonation and becomes
*Viscosityof 10%w/wsolution of methanol and dichloromethane at 20°C
*D50: NMT10μm bylaser diffraction method
**D50: 70-300 μm bylaser diffraction method
Viscosityof all grades is in the range of 2.4-3.6 mPa.s measured in 2%w/waqueous solution of sodium hydroxide at 20°C.
water-soluble. Enteric coatings can be applied to different dosage forms, but they are mostly applied to tablets and pellets filled in capsules.
The following are the general categories of polymers that are used in delayed release drug delivery
Shin-Etsu offers cellulose based enteric polymers which are differ in functional substitution on HPMC backbone
1.Hydroxypropyl methylcellulose phthalate (HPMCP)
HPMCP contains a carboxybenzoyl (phthalyl) group, but its backbone structure is a water soluble polymer (HPMC). The phthalyl group can define the soluble nature of HPMCP, which is insoluble in water due to its hydrophobicity and soluble in weak acid to neutral medium. Additionally, there is no insolubilization during storage.
Key features
◆ Widely used enteric polymer by the pharmaceutical industry since its introduction in the market in 1971 ◆ Soluble in various organic solvents ◆ HPMCP is a
versatile coating material for tablets, pellets, and capsules
◆ Compliant to JP, NF, EP
◆ Various grades are available based on the pH solubility and viscosity
2.Shin-Etsu AQOAT® (Hydroxypropyl methylcellulose acetate succinate,HPMCAS)
Shin-Etsu AQOAT® contains acetyl and succinoyl groups substituted on the HPMC backbone. The acetyl group is hydrophobic and the succinoyl group is hydrophilic. Substitution levels of the acetyl and succinoyl groups in HPMCAS influence the polymer solubility at different pH.
The low ratio of acetyl to succinoyl content (L grade) imparts pH solubility at pH 5.5 and above, while the high ratio of acetyl to succinoyl content (H grade) imparts pH solubility at pH 6.5 and above.
Key features
◆ Widely used enteric polymer by the pharmaceutical industry since its introduction in the market in 1987 ◆ The enteric coating can be performed by aqueous based, solvent based, and dry coating methods ◆ Shin-Etsu AQOAT® (HPMCAS) is a versatile coating material for tablets,
pellets, and capsules
◆ Compliant to JP, NF, EP
◆ Self-affirmed GRAS status
◆ Various grades are available based on the chemical substitution and particle size.
Benefits of HPMCPand Shin-Etsu AQOAT® (HPMCAS):
1.No curing effect
2. Easy to clean after coating
3. HPMCAS is suitable for dietary supplements because of self-affirmed GRAS
4. Application of Shin-Etsu AQOAT® (HPMCAS) in aqueous enteric coating without plasticizer (by ammonia neutralization approach)
5. Suitable for enteric coating of capsules
For more info, please contact pharmaindia@setylosein.com or visit https://www.metolose.jp/en/
ImaDuct Silicone Duct Hose,a high-performance flexible ducting solution from Ami Polymer combines the advantageous properties of silicone with advanced construction techniques to deliver exceptional performance
ImaDuct Silicone Duct
Hose is a high-performance flexible ducting solution offered by Ami Polymer Pvt. Ltd., designed to meet the rigorous demands of various industrial applications. This product combines the advantageous properties of silicone with advanced construction techniques to deliver exceptional performance in challenging environments.
KeyFeatures
◆ Temperature Resistance:
ImaDuct silicone duct hoses are engineered to withstand extreme temperatures. They typically perform efficiently in a wide temperature range, from -60¢XC to +260¢XC (76¢XF to +500¢XF). This makes them suitable for applications involving both very high and very low temperatures.
◆ Flexibility: The hoses are highly flexible, allowing for easy installation in complex or tight spaces. This flexibility also accommodates movements and vibrations in dynamic systems, ensuring reliable performance without kinking or collapsing.
◆ Durability: Silicone material used in ImaDuct hoses is resistant to aging, UV radiation, and ozone, which significantly extends the product¡¦s lifespan. These hoses maintain their integrity and functionality even in harsh outdoor environments.
◆ Chemical Resistance:
ImaDuct hoses offer excellent resistance to a wide range of chemicals, including acids, bases, and solvents. This makes them ideal for use in chemical processing industries where exposure to corrosive substances is common.
niques to ensure optimal performance:
◆ Inner Layer: The inner surface is made from a smooth silicone lining that facilitates easy flow of materials and minimizes friction. This layer is designed to resist the build-up of
◆ Non-Toxic and Non-Reactive: Silicone is an inert material, meaning it does not react with most chemicals or materials. This property is crucial for applications in the food, pharmaceutical, and medical industries where contamination needs to be minimized.
◆ Lightweight: Compared to metal ducting solutions, ImaDuct hoses are much lighter. This reduces the load on supporting structures and makes handling and installation easier.
Construction and Design
ImaDuct silicone duct hoses are constructed using advanced materials and tech-
particulates and ensure clean transport of gases or fluids.
◆ Reinforcement: To provide structural integrity, the hoses are reinforced with layers of fiberglass or polyester fabric. This reinforcement allows the hoses to withstand internal pressures and external mechanical stresses.
◆ Helix Wire: A steel or plastic helix wire is often embedded within the hose structure. This wire provides additional support, maintaining the hose¡¦s shape and preventing collapse under vacuum conditions. It also enhances the hose¡¦s ability to flex without kinking.
◆ Outer Layer: The exterior is coated with a thicker layer of
silicone, which offers protection against abrasion, environmental elements, and mechanical damage. This outer layer ensures the hose can endure rough handling and external impacts.
Applications
ImaDuct silicone duct hoses are versatile and find applications across various industries due to their robust properties:
1. Automotive Industry: Used in air intake systems, turbochargers, and coolant systems, where high-temperature resistance and flexibility are essential.
2. HVAC Systems: Employed in heating, ventilation, and air conditioning systems to move hot or cold air efficiently while withstanding temperature extremes and vibrations.
3. Industrial Processes: Ideal for conveying hot air, gases, or lightweight materials in processes such as plastic molding, chemical manufacturing, and food processing.
4. Aerospace: Used in aircraft ducting systems for hot air and cooling due to their lightweight and high-performance characteristics.
5. Medical and Pharmaceutical: Suitable for environments that require non-toxic, non-reactive materials to prevent contamination and ensure safety.
Major Application as per below:
◆ Automotive ◆ Dryer Hose
◆ Plastic Industry ◆ Air Craft
◆ Brake Ducting ◆ Cap Ventilation ◆ Defroster/Heater Hose ◆ Dry Cleaning ◆ Exhaust Systems ◆ Tractor Pull Exhaust ◆ High Temperature Applications ◆ Rocket Sup-
port Duct ◆ Transmission
Cooling
Maintenance and Care
To maximize the performance and longevity of ImaDuct silicone duct hoses:
◆ Regular Inspection: Conduct routine checks for signs of wear, tears, or any form of damage. Early detection of issues can prevent failures and extend the hose¡¦s service life.
◆ Cleaning: Periodically clean the hoses to prevent buildup of dust, debris, or chemicals that might degrade the material.
◆ Proper Installation: Ensure hoses are installed correctly, avoiding excessive bending or tension that could damage the hose.
◆ Avoid Over-Bending: Follow manufacturer guidelines regarding the minimum bend radius to prevent kinking and ensure smooth operation.
Conclusion
ImaDuct silicone duct hoses by Ami Polymer offer a reliable and efficient solution for demanding industrial applications. Their superior temperature resistance, flexibility, durability, and chemical resistance make them an excellent choice for a wide range of uses, from automotive and aerospace to HVAC and medical industries. Proper maintenance and installation practices will further enhance their performance and longevity, making them a valuable asset in any industrial setup.
Thanks, Vishal Babariya Assit Manager -Sales & Marketing Contact No : +91-9152032308 Email id- vishal.b@amipolymer.com
EMDEX® (Dextrates,NF) is a directly compressible,water-soluble tablet binder and filler.Its Unique composition of 95 % glucose monohydrate and different oligosaccharides derived from starch is monographed under Dextrates in the NF,with use levels ranging from 1 % to 99 %, EMDEX® is designed for a variety of tablets & lactose free applications[4]
Physical Properties [4]
◆ Made from corn starch (GMO free EMDEX® available)
◆ Natural sweet taste of dextrose
◆ Freely & rapidly water-soluble (1000g/L)
Loss on Drying 7.8-9.2 (glucose monohydrate,the assay includes crystal water) Dextrose Equivalent 93 – 99 %
of Solution -105 J/g
◆ Excellent Flowability
◆ Spherical ,Porous particles
◆ Directly compressible fillerbinder
◆ High Bulk density
◆ Narrow particle size distribution
◆ Calorie content- 4.05.0Kcal/gram
EMDEX® Benefits and Applications[5][6]
Benefits:
◆ Superior flow, compaction, and tablet robustness in direct compression applications
◆ Does not require a gliadant,due to superior flow properties
◆ Exhibits excellent mixing properties
◆ Easy to handle- does not stick to punches
◆ Non-dusting
◆ Results in smooth ,shiny tablets
◆ Tablets demonstrate very low friability
◆ Metabolizes fully without osmotic laxative effect
◆ Provides patients with a pleasant, sweet taste and a cool mouth feel
◆ Does not cause dry mouth feel when compared to sugar alcohols
◆ Particle porosity improves EMDEX®solubility and flavor absorption capacity- a key advantage for tablet taste enhancement
◆ Compendial (NF), eliminating regulatory hurdles
◆ Emdex is designed for variety of tablet types and dosage forms:
◆ Chewable tablets
◆ Orodispersible tablets
◆ Effervescents
◆ Sachets
◆ Multilayer tablets
◆ As replacement for lactose
flowability and non-dustiness makes it appropriate to be used as flow improvement aid in sachets and stickpacks.
◆ EMDEX® exhibits narrow particle size distribution with an average particle size of 200 μm.Along with its spherical particle shape and high bulk density,this ensures supreme flow properties.
◆ EMDEX® is a porous material that absorbs fluids, allowing chewable formulation development and manufacture using liquid APIs
◆ The porous structure of the sparay-dried EMDEX® particlesenables excellent content uniformity even for low dose,micronized APIs.
Particle Size d50 (μm) 190-220 130-160
BulkDensity(g/L) 600-700 600-700
Tapped Density(g/L) 700-800 700-800
FlodexIndex(mm) 4 4
Water Solubility(g/L) 1000 220
Powder Characteristics of EMDEX® and spraydried lactose
Compactability
In this study, the effect of different soluble binder on tablet hardness was evaluated.
Observation: The kind of diluent used had a significant influence on the hardness of the tablets. While tablet manufactured with EMDEX® resulted in the highest compactability, those made from glucose and spray-dried lactose exhibited the lowest compactability. Spray drying of EMDEX® as well as the presence of oligosaccharides leads to massive Increase in tablet strength.
Applications:
◆ EMDEX® is 100 % water soluble, it is also perfect for applications in which a good mouth feel or a clear solution is required.
◆ EMDEX® has excellent
for APIs,which are incompatible with reducing sugars.
Comparison of powder characteristics of EMDEX® and spraydried lactose [3]
A comparision of EMDEX® and spray dried lactose with regard to their powder characterstics demonstrated the similarility of the two materials.Both are water soluble,crystallized powders with a porous structure and a spherical particle shape.The particle shape in combination with the high bulk density leads to excellent powder flow of EMDEX® and spray-dried lactose.Further more,both excipients are appropriate for direct compression applications and deform mainly by brittle fracture.
◆ In this study, the effect on Hardness & flowability was evaluated.
EMDEX® is a promising substitute for spray dried
Flowability
In this study, the flowability of different soluble binders was evaluated.
Observation: Due to its high bulk density and spherical particle shape, EMDEX® exhibits excellent flowability.This functional advantage can be utilized in pre form or for flow enhancement in tableting blends and stickpacks.Angle of repose found to be a 300
◆ Oily APIs are readily absorbed by the sponge-like structure of EMDEX®.
◆ Highly suited for veterinary products, who are particularly fond of its pleasant taste.
◆ EMDEX® should not be used
lactose as it has similar powder and tableting properties. Spray –dried lactose is widely used as filler and binder in the pharmaceutical industry, but many adults are not able to digest lactose. Lactose is absorbed from
the gastrointestinal tract once it is hydrolyzed by the enzyme “lactase” into glucose and galactose. Hence, children deficient in “lactase,”are unable to absorb lactose (due to congenital defect or lack of the enzyme) and develop flatulence, diarrhea, gastrointestinal bloating following ingestion of milk due to the build-up of lactic acid, hydrogen, and carbon dioxide. Lactose intolerance in infants and children can lead to prolonged episodes of bloating, diarrhea, dehydration, and metabolic acidosis.Therefore, it is indispensable to provide alternatives to lactose-containing drugs in order to make them suitable for lactose intolerant patients[1][2].
Conclusion:
◆ EMDEX® is a water –soluble filler binder with brittle fracture as the main binding mechansim.
◆ EMDEX® and spray dried lactose show great similarity in terms of particle morphology,bulk density and flowability. EMDEX® was therefore ideally suited as a substitute for spraydried lactose in order to make them suitable for lactose intolerant people.
◆ EMDEX® is well suited for
CONTRIBUTOR’S CHECKLIST
Observation: The flowabilityof DC-grade micro-crystalline cellulose (VIVAPUR® 102) can be further improved byadding increasing amounts of EMDEX®
chewable tablets, effervescent tablets,oro-dispersible tablets, multilayer tablets and sachet kind of formulation.
References:
1. Mattar, R. et al. (2012) Lactose intolerance: diagnosis, genetic, and clinical factors. Clinical and experimental Gastroenterology, 2012:5 113-121.
2. Pawar S, Kumar A (2002) Is-
❒ Express Pharma accepts editorial material for regular columns and from pre-approved contributors / columnists.
❒ Express Pharma has a strict non-tolerance policy of plagiarism and will blacklist all authors found to have used/refered to previously published material in any form,without giving due credit in the industry-accepted format.All authors have to declare that the article/column is an original piece of work and if not,they will bear the onus of taking permission for re-publishing in Express Pharma.
❒ Express Pharma's prime audience is senior management and pharma professionals in the industry.Editorial material addressing this audience would be given preference.
❒ The articles should cover technology and policy trends and business related discussions.
❒ Articles for columns should talk about concepts or trends without being too company or product specific.
sues in the formulation of drugs for oral use in children. Pediatric Drugs 4(6):371–379
3. JRS Pharma The Use of EMDEX® in a Lactose-free Reformulation of Cetirizine Tablets- JRS Pharma https://www.jrspharma.com/ph arma_en/technicalinfo/brochures/technicalinfo/EMDEX.php
4. JRS Pharma EMDEX®
Brochure- JRS Pharma
5. Rowe, R.C., Sheskey, P.J.; Quinn, M.E. (2009) Handbook of Pharmaceutical Excipients. 6th Edition, Pharmaceutical Press, 218-220.
6. Leon Lachman, Herbert A. Lieberman, Joseph L. Kanig. The theory and Practice of Industrial Pharmacy, Varghese publication house, 3rd edition, 1990, 327-330.
❒ Article length for regular columns: Between 12001500 words.These should be accompanied by diagrams,illustrations,tables and photographs, wherever relevant.
❒ We welcome information on new products and services introduced by your organisation for our various sections: Pharma Ally (News,Products,Value Add),Pharma Packaging and Pharma Technology Review sections.Related photographs and brochures must accompany the information.
❒ Besides the regular columns,each issue will have a special focus on a specific topic of relevance to the
Indian market.
QR Code
Scan the QR code for more details regarding EMDEX® from JRS Pharma.
Mr Prashant Bhangdiya Business Development ManagerPharma Rettenmaier India Pvt Ltd Prashant.bhangdiya@jrsindia.com
❒ In e-mail communications,avoid large document attachments (above 1MB) as far as possible.
❒ Articles may be edited for brevity,style,and relevance.
❒ Do specify name,designation,company name, department and e-mail address for feedback,in the article.
❒ We encourage authors to send their photograph. Preferably in colour,postcard size and with a good contrast.
Email your contribution to: The Editor, Express Pharma, Business Publications Division, The Indian Express (P) Ltd, Mafatlal Centre,7th floor, Ramnath Goenka Marg, Nariman Point,Mumbai 400021 viveka.r@expressindia.com,viveka.roy3@gmail.com
Testo data loggers ensure continuous monitoring of temperature and relative humidity of pharma products during production,storage or transit of goods.Real time data monitoring is important for the quality of pharma goods and also enables the supplier to improve the life of the goods
Due to the crucial necessity and its direct impact on human health and welfare, pharma is probably the most important and critical sector among others. As a consequence of which, it becomes essential to store pharma, vaccines, laboratory samples or units of blood at the right temperatures to ensure that they remain effective and that quality is maintained. Another reason for the pharma division to ensure safety measures and controlled environment is stringent regulations and inspection of the facilities. This elementary need for climate control can only be ensured with right data monitoring systems. Testo being a market leader in testing and measurement sector provides the best in class data loggers and data monitoring systems for the pharma division.
Ensuring end to end climate monitoring –Testo Data Loggers
Pharma goods must be stored well in every situation as any deviation in the ambient temperature or humidity values may lead to deteriorated quality of the product. Testodata loggerscan be used to test the optimum conditions for specific products or surroundings. Temperature and humidity data loggers are often used in pharma industries to monitor the conditions in which drugs, medicines, vaccines are kept. Not only storage, but during the transit of goods, testo transport data loggers are useful to measure the transport conditions. The range of data loggers is very extensive. A temperature and humidity logger such as 174 T guarantees continuous monitoring in a storage or warehouse. Also,
data loggers with multi channels for connecting external sensors and thermocouples, like testo 176 are available for ensuring secured work process in labs.
These data loggers are also critical for production quality assurance where the temperature has to be frequently checked at various points in production processes. Using thermocouple probes, data loggers can also record data in the kinds of extreme temperature ranges. The probe's fast response also contributes in the validation processes and quality standard optimisation in QA units and clean room applications. These instruments are the most convenient and pocket friendly solution for all pharma application areas.
Another important and crucial application of a pharma industry involvesvalidation of
sterilisation and freeze-drying processes. Not only that, validating cleaning and disinfecting equipment is equally necessary. In order to allow a seamless operating procedure, the validation process and the documentation work must be as efficient and smooth as possible which could be easily achieved with testo data loggers solution that has innovative data loggers for temperature and humidity, smart software and accessories.
Testo offerings are majorly related to the data security along with comprehensive analysis and evaluation of all the recorded measurement data. Testo data loggers ensure continuous monitoring of temperature and relative humidity of pharma products during pro-
duction, storage or transit of goods. Real time data monitoring is important for the quality of pharma goods and also enables the supplier to improve the life of the goods. Transportation trucks, warehouses, cold rooms etc. can now be remotely monitored via Testo data loggers and data monitoring systems. Testo's data loggers are EN 12830 and 21 CFR Part 11 compliant which ensure complete documentation of parameters, be it humidity, temperature or absolute pressure. They come with professional software where the data recorded cannot be modified and the audits can be easily complied with.
Testo also has an established state-of-the-art NABL accredited service and calibration
LAB in accordance with the standardISO/IEC 17025:2017, that takes care of the after sales support locally from Pune. Testo service and calibration facility is highly cost effective as it delivers international standards very conveniently within a week’s time. Instruments of any brand/make can be calibrated and serviced locally maintaining necessary standards.
The accredited parameters include humidity, pressure, absolute pressure, contact type temperature, non-contact type temperature (infra red thermometer, thermal imager). In fact, Testo has the first and only lab in India to get NABL Accreditation forDew Point Temperature as well.
For more details, login to website www.testo.com or write back to us on info@testo.in
The pH Sensor InPro3100/120/PT100,with its accurate measurement capabilities,reduced maintenance requirements,compatibility with CIPand SIPprocedures,and versatile application, is an invaluable tool for ensuring the quality and consistency of pharma products
In the pharma industry, precision and reliability are crucial for ensuring product quality and compliance with stringent regulatory standards. One of the vital aspects of this precision is accurate pH measurement. Enter the pH Sensor InPro3100/120/PT100, a robust, low-maintenance, and high-accuracy solution designed to meet the demanding needs of bioprocesses in pharma production. This article explores how the InPro3100/120/PT100 sensor can significantly benefit pharma industries.
Reliable and accurate measurement
◆ Key to consistency: Consistent pH measurement is essential in many pharma processes, such as fermentation, buffer preparation, and purification. The InPro3100/120/PT100 offers stable and accurate pH measurements, thanks to its patented Argenthal silver-ion trap reference system. This technology minimises the risk of diaphragm clogging, ensuring uninterrupted and reliable readings even in the presence of complex solutions.
◆ Precision under pressure: The sensor is pressure resistant up to 6 barg (87 psig), making it suitable for various applications within the pharma industry. Its built-in Pt100 temperature sensor ensures that pH readings are compensated for temperature variations, further enhancing measurement accuracy.
Lowmaintenance with gel electrolyte
◆ Reduced downtime: Maintenance can be a significant bottleneck in pharma production. The InPro3100/120/PT100 features a gel-filled electrolyte system that reduces maintenance requirements. This design ensures prolonged sensor life and reduces the need for frequent recalibration and replacement, allowing pharma companies to maintain high productivity levels with minimal downtime.
◆ Long-lasting performance: The gel-filled electrode also provides effective pH measurement for an extended period, ensuring that the sensor remains reliable even in challenging conditions. This translates to cost savings and reduced operational disruptions.
◆ Sterilisation ready: Clean-inplace (CIP) and steam-in-place (SIP) procedures are common in pharma manufacturing to maintain hygiene and prevent contamination. The InPro3100/120/PT100 is designed to withstand these rigor-
ous cleaning and sterilisation processes. Its sterilisable and autoclavable features ensure that the sensor maintains fast and precise pH measurements even after repeated cleaning cycles.
◆ Robust design: The sensor's rugged construction makes it ideal for in-line pH measurements where sensor cleaning and sterilisation are required. This robustness ensures that the sensor performs reliably, even in environments where harsh cleaning agents and high temperatures are involved.
◆ Wide applicability: The InPro3100/120/PT100 is versatile and can be used in various pharma applications, from upstream processes like cell culture and fermentation to downstream processes such as purification and formulation. Its short installation length (120 mm version) makes it optimal for installations with limited space.
◆ Watertight and durable: The sensor's watertight connector and durable design ensure that it can withstand the rigors of bioprocessing environments. This
durability is crucial for maintaining sensor integrity and performance over time.
Conclusion
The pH Sensor InPro3100/120/ PT100 is a robust, reliable, and low-maintenance solution tailored to the demanding needs of the pharma industry. With its accurate measurement capabilities, reduced maintenance requirements, compatibility with CIP and SIP procedures, and versatile application, it is an invaluable tool for ensuring the quality and consistency of pharma products. By incorporating the InPro3100/120/PT100 into their processes, pharma manufacturers can achieve greater efficiency, compliance, and product integrity, ultimately contributing to better patient outcomes.
Additional information about METTLER TOLEDO is available at www.mt.com.
Visit: In-line pH probe and in-line pH sensor for in-line pH measurement (mt.com)
Email: sales.sales@mt.com
Call toll-free: 1800 22 8884 & 1800 1028 460
Reduce time to market with Optima’s turnkey approach – your integrated solution from a single source
Optima Pharma offers customised filling and process solutions for the pharmaceutical and biotech industries. As an integrated system provider, we are the turnkey partner for complete lines, special solutions, and sophisticated standard machines for primary packaging, modular freeze-drying systems and isolator technologies. As part of the Optima Group with around 3,000 experts and 20 global locations, we ensure worldwide availability of services.
How can your newly licensed pharma and biotech
Optima has developed a unique approach that considerably reduces time between your system's design and production start.As a system partner and turnkey provider, Optima delivers completely integrated systems, including filling lines,isolators, and freezedryers
products get to market as quickly as possible? As a manufacturer, Contract Manufacturing Organisation (CMO) or Contract Development and Manufacturing Organisation (CDMO), we know that reducing your time to market is crucial. Meanwhile, you also require increasingly flexible and complex systems. Optima has
developed a unique approach that considerably reduces time between your system's design and production start.
As a system partner and turnkey provider, Optima delivers completely integrated systems, including filling lines, isolators, and freeze-dryers. Optima is your home for turnkey.
The catalyst for your turnkeyproject
Comprehensive Scientific Process Engineering (CSPE) reduces the time-to-market for your turnkey project. How?
CSPE expedites the implementation of your turnkey system using digital engineering, simulation, VHP cycle development, and qualification
KEYBENEFITS OF OPTIMATURNKEY SOLUTIONS
◆ Fastest time-to-market of custom-tailored processing lines
◆ Accelerated production start with comprehensive simulations and VHPcycle development
◆ Integrated solution including filling line, isolator,and freeze-dryer from one partner
◆ Highest safetywith fullytested line at OPTIMA CSPE-Center
◆ Entire life cycle with turnkeyapproach – from conception to production
measures before delivery and an integrated Factory Acceptance Test (iFAT). These measures eliminate unnecessary steps and accelerate production start. Comprehensive turnkey systems in particular launch more quickly, as CSPE includes complete in-house qualification by Optima and makes regulatory audits easier.
“With CSPE, we are switching from an experienced-based model to an integral, datadriven model that leads to continuous imp rovement that is deterministic and no longer random,” says Gerhard Breu, Chairman of the Optima Pharma Division.
At the two CSPE centers in Schwäbisch Hall, filling and closing systems with isolators can be set up and tested with freeze dryers as a fully functional unit under realistic conditions. This considerably reduces the time between installation and the start of production at the customer’s site, as well as from product development to market launch.
Ahigh-performance clean room door is an integral component in ensuring the integrity of these spaces,safeguarding product quality and patient safety
High-speed doors for clean rooms are specialised industrial doors essential for maintaining controlled environments. These doors are engineered to be airtight, creating a reliable barrier between different areas of a facility. Their design ensures durability and minimal maintenance, reducing the frequency of repairs and replacements.
High-speed clean room doors offer a range of critical benefits essential for maintaining stringent environmental control. These doors enhance hygiene by providing an airtight seal that effectively isolates clean room environments, preventing the ingress of dust and other contaminants. This capability is especially crucial in sectors such as pharma, biotechnology, and food production, where maintaining sterility is non-negotiable.
In the pharma and life sciences industries, compliance with rigorous regulatory standards necessitates the manufacture of products within controlled clean room environments. A high-performance clean room door is an integral component in ensuring the integrity of these spaces, safeguarding product quality and patient safety.
Beyond contamination control, these doors are engineered with advanced safety mechanisms, including automated sensors and emergency stop functions, which mitigate the risk of operational hazards. Moreover, high-speed clean room doors are designed to maintain precise overpressure or under pressure conditions within the environment. This is vital for preventing cross-contamination and ensuring that the clean room remains in a state of controlled integrity, even under varying operational demands.
sary for applications such as pharma manufacturing, semiconductor fabrication, food processing, and other highly specialised sectors.
tight integration of the curtain, providing high leak tightness.
◆ Efficient operation: The doors offer high efficiency and low permeability values, compliant with EN 12426 and EN 12427 standards, ensuring < 12 m³/m² h ? 50 PA.
◆ Durable control device enclosure: The control device enclosure is made of StainlessSteel SS 316, ensuring durability and resistance to corrosion.
Prime Clean Reset, Gandhi Automations' high-speed door is designed specifically for clean rooms. This innovative solution is engineered to meet the stringent requirements of controlled environments, ensuring exceptional performance and reliability. Designed with precision to meet the stringent requirements of controlled environments, Prime Clean Reset is the epitome of performance and reliability, ensuring that your clean room operations consistently meet the highest standards of regulatory compliance and product integrity.
Prime Clean Reset is suit-
Given the critical role these doors play in maintaining the purity and safety of highly specialised environments, selecting the appropriate door system is a decision of strategic importance.
able for clean rooms up to ISO Class 5, offering an unparalleled air permeability rate of less than 12 m³/m² h at ? 50 Pa. This ensures that even in the most sensitive environments, the door effectively maintains the critical pressure differentials required to prevent contamination, thereby safeguarding your processes and products.
Engineered with cuttingedge European technology and innovative design principles, Prime Clean Reset offers rapid cycle times for both opening and closing, making it the optimal solution for medium to large entrances in clean room applications. The door's construction is specifically tailored to minimise air leakage and particulate infiltration, ensuring that it supports the rigorous cleanliness standards neces-
With its robust design and reliable performance, Prime Clean Reset seamlessly integrates into your clean room infrastructure, providing a critical barrier that preserves the integrity of controlled environments. Whether you are operating in a pharma, biotechnology, electronics, or defence industry, Prime Clean Reset offers the precision, durability, and compliance needed to maintain your competitive edge in highly regulated markets.
Key features of Gandhi Automations' High-Speed Clean Room Doors include:
◆ Low air permeability: Designed to maintain low air permeability in pressurised rooms with both positive and negative air pressure.
◆ Compact design: The doors are designed to fit inside the columns, with a self-supporting construction that minimises air leakage.
◆ Customisable transparency: They can be equipped with transparent PVC horisontal sections or vision windows for visibility.
◆ Specialised side guides: The special side guides ensure a
These high-speed doors are meticulously engineered to minimise air leakage and maintain strict environmental control, making them indispensable for clean room operations. Their rapid opening and closing operation ensure that the internal facility remains isolated from external conditions, effectively upholding the cleanliness and controlled environment essential for maintaining the integrity of clean rooms.
For further information on our high-speed doors offering, contact:
Gandhi Automations Pvt Ltd. Chawda Commercial CentreLink Road, Malad (W), Mumbai-400064, India.
Off : +91 22 66720200 / 66720300 (200 lines)
Fax : +91 22 66720201
Email : sales@geapl.com
Website : www.geapl.com
B&R Education Network partnered with the Dr.D.Y.Patil Institute of Technology in Pimpri-Pune to organise the Open Automation Challenge 2024.The event paired engineering students with B&R mentors to bring their ideas to reality using the state-of-the-art technologies in the field of automation engineering
At a time when the global manufacturing landscape is more competitive than ever, industry and academia are collaborating to overcome complex new challenges in engineering and at the same time inspire future engineers. The B&R Education Network in India is continuously working as the interface between educational institutions and the automation industry. To help make the next generation of engineers ready for industry, the B&R Education Network partnered with the Dr. D.Y. Patil Institute of Technology in Pimpri-Pune to organise the Open Automation Challenge 2024. The event paired engineering students with B&R mentors to bring their ideas to reality using the state-of-the-art technologies in the field of automation engineering. The event started in June 2024 with over 50 teams across India registering their groundbreaking ideas. Fourteen teams were shortlisted based on their innovative approach and application. The selected teams completed training on B&R's Automation Studio engineering software and other B&R technologies to finally execute their projects and bring their ideas to life.
Understanding the gap
In a fast-paced world, technological transformation leads to better productivity. It is necessary that the engineers of today understand the industry challenges. Today, automation is considered a key element in all manufacturing operations, and the industry expects new recruits to have the required skills in this technology. Moreover, in the era of industrial IoT and Industry 4.0, the evolution of technology is growing rapidly, and the engineering curriculum often struggles to keep pace with it. B&R’s Edu-
During the presentation, he highlighted important topics like industry trends, the changing demands, sustainability and how the B&R Education Network is bridging the gap between industry and educational institutes.
Building the bridge of knowledge
Open Automation Challenge 2024 has seen remarkable milestones with new perspectives and a fresh outlook on the projects built by students
cation Network is a well-structured program of collaboration to improve the industry knowledge of engineering graduates and make them ready for the industrial world. Open Automation Challenge 2024 offered fresh inspiration for the engineering students' innovative minds, encouraging cu-
riosity for creative solutions and courage for big ideas. The emerging engineers explored numerous possibilities, the way automation is changing the world and were intrigued by a presentation delivered by Jhankar Dutta, B&R's Regional Managing Director for Southern and Eastern Asia.
along with their mentor assigned by B&R. The group of students participating in the challenge embarked on a twoweek educational adventure that included project development and training on B&R Automation Studio and related technologies. Their dedication and creativity trans-
formed inn ovative ideas into reality using advanced software and simulation tools. On the final day, each team stepped onto the stage, unveiling their meticulously crafted automation projects before a panel of esteemed judges. The students demonstrated not just technical prowess, but the potential to revolutionise sectors ranging from manufacturing to healthcare and agriculture. The top three teams were selected as winners. The right knowledge is a critically important first step and one of the most effective ways to bridge the gap is to mentor the right way. As the automation industry grows across India with rising expectations and demands, engineers are the pioneers of a bright tomorrow. Beyond competition, the Open Automation Challenge 2024 was a celebration of collaboration and learning.
Open Automation Challenge 2024 event gathered engineering students from all over India: More than 50 teams registered and ultimately 14 teams selected to get the trainings and execute the projects. (Image - B&R)
For more information, visit www.br-automation.com.
THINK COATING THINK INSTACOAT