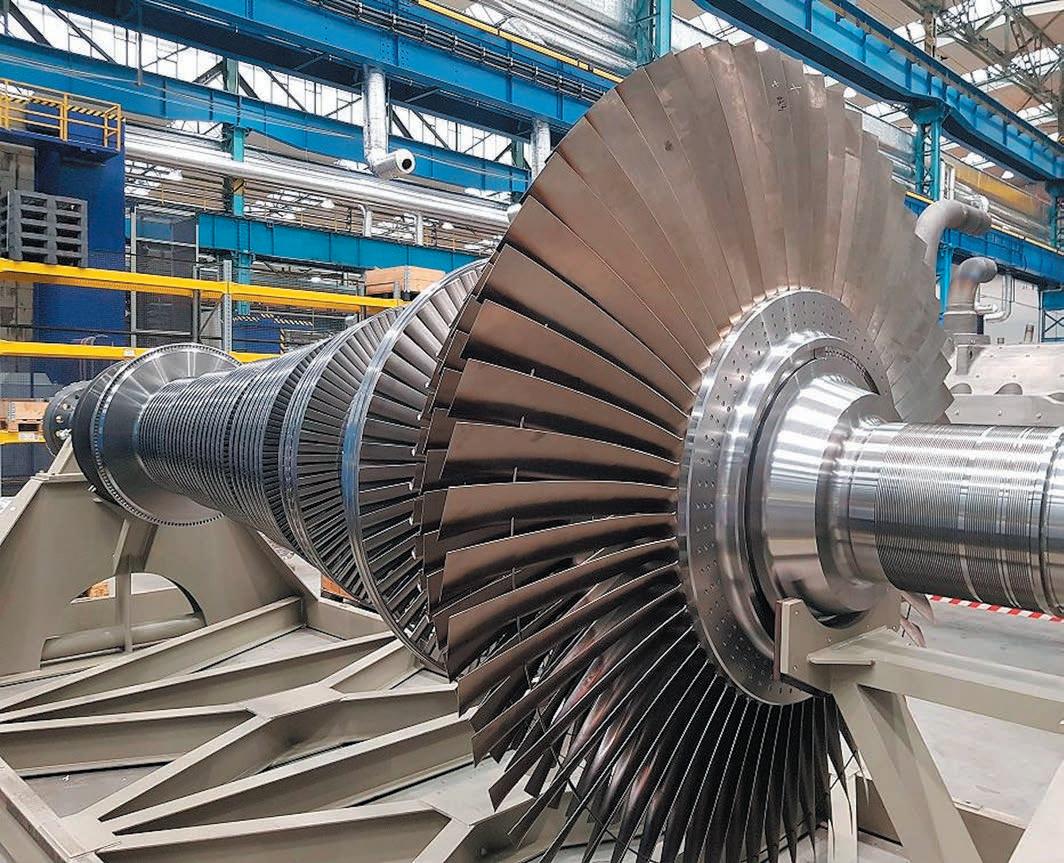
11 minute read
TOPIC MAINTENANCE Soepele vervanging turbine AVR
Soepele vervanging
turbine dankzij veel overleg
Advertisement
Eén van de drie oudste turbines van AVR in Rozenburg is onlangs vervangen door een nieuw exemplaar. Door in de planning rekening te houden met eventuele tegenslagen en dankzij constant overleg, kon het project ruim binnen de planning worden opgeleverd. ‘Het is gelukt om al in november 2021 te testen en meteen op maximaal vermogen te draaien’, aldus Marcel Kooman van AVR.
Jacqueline van Gool
Afvalstroom
Voor wat betreft de grondstoff en – huishoudelijk afval dat niet op één of andere manier gerecycled of verwerkt kan worden – ziet Kooman geen grote veranderingen in samenstelling op korte termijn, maar de samenstelling van het afval verandert wel over langere tijd, zoals het aandeel kunststoff en. ‘Je hebt het over de verwerking van zo'n 1,7 miljoen ton afval in de energiecentrales van onze vestigingen in Rozenburg en Duiven met een behoorlijk wisselende samenstelling per ton. Een groot deel van het afval bestaat uit verpakkingsmateriaal. Wel wordt er meer plastic uit de afvalstroom gehaald. Om dit beter te scheiden hebben we geïnvesteerd in een nieuwe nascheidingsinstallatie.’ Sinds eind vorig jaar draait bij AVR Rozenburg een gloednieuwe turbine. Het nieuwe model is een tegendrukturbine met een maximaal ‘slokvermogen’ van 200 ton stoom per uur. De uitgaande stoom heeft een temperatuur van 130 graden Celsius bij 2,5 bar. Daarnaast levert de nieuwe installatie 22,5 megawatt elektrische energie. Al met al voldoende om tienduizenden huishoudens in Rotterdam te voorzien van elektriciteit en warmte via het warmtenet. De warmtelevering wordt fl exibeler en betrouwbaarder waarmee de positie van AVR is verbeterd.
Oudjes
De nieuwe machine, turbine F, vervangt de oude turbine B. Installatie B was één van de drie eerste turbines van AVR. ‘Bij de oprichting van AVR begin jaren zeventig zijn drie turbines in gebruik genomen, A, B en C’, vertelt Marcel Kooman, projectmanager Strategische Projecten bij AVR. ‘Deze draaien dus al zo’n vijftig jaar. Normaal gesproken gaan dergelijke installaties zo’n twintig tot dertig jaar mee. Onze eerste turbines zijn dus best oudjes.’ In de jaren die volgden, kwam er nog een vierde turbine bij (D) en een biomassa energiecentrale (turbine E). In de loop der tijd zag AVR de vraag naar stadswarmte, stoom en elektriciteit veranderen. ‘In de eerste jaren was het doel om zoveel mogelijk elektrische energie te produceren uit de afvalverbranding. Daarom zijn de installaties C en D condenserende turbines. In deze modellen wordt de stoom bijna tot omgevingstemperatuur afgekoeld en wordt de elektriciteitsproductie maximaal, terwijl er weinig restwarmte overblijft. Maar de afgelopen jaren groeide de vraag naar warmte en stoom voor omringende bedrijven juist.’
Tegendrukturbine
Om economische redenen lag turbine B sinds 2006/2007 stil. Tegelijkertijd onderzocht AVR of het mogelijk was om meer te doen met de restwarmte. Sinds 2015 levert de afvalverwerker warmte aan het Rotterdamse Warmtenet. Vanwege de veranderende marktvraag besloot AVR in 2018 turbine B te vervangen door een nieuwe installatie. ‘Er is toen gekozen voor een tegendrukturbine omdat deze zowel elektriciteit als stoom voor stadswarmte kan leveren. De stoom gaat de turbine in met een druk van ongeveer 27 bar en verlaat de installatie met 2,5 bar en 130 graden Celsius. Dat is ideaal voor stadsverwarming.’ Daarnaast genereert de turbine 22,5 megawatt elektrische energie. De nieuwe installatie kan 200 ton stoom per uur verwerken, maar werkt ook effi ciënt bij lagere capaciteiten, van veertig tot
De nieuwe installatie kan 200 ton stoom per uur verwerken, maar werkt ook efficiënt bij lagere capaciteiten, van veertig tot vijftig ton, afhankelijk van de vraag.
vijftig ton, afhankelijk van de vraag. De verschillende turbines van AVR draaien niet allemaal tegelijk zegt Kooman. ‘Dat wordt afgestemd op de vraag. In de winter is er meer vraag naar warmte voor de stadsverwarming en gebruiken we meer capaciteit van de tegendrukturbines.’
Manoeuvreren
Het vervangen van de turbine verliep volgens Kooman soepel. ‘De grote uitdaging van een dergelijk project is dat je in een bestaande draaiende productie-omgeving moet manoeuvreren. We hebben hiervoor speciale procedures opgesteld en het is vooral belangrijk om veel te communiceren. Bij alle communicatiesessies waren mensen vanuit onze afdeling Strategische Projecten aanwezig, maar ook vanuit productie, onderhoud, techniek, veiligheid en inkoop. In dit soort projecten moet je constant overleg voeren om werkzaamheden op elkaar af te stemmen. Ook bijvoorbeeld voor het aanvragen van vergunningen en dergelijke.’ Het is een dynamische organisatie dus niet al het werk ligt altijd van tevoren vast. Kooman: ‘Je praat over installaties van vijftig jaar oud, daar kan natuurlijk wel eens een storing in zijn. Daarom moet je altijd de vinger aan de pols houden. Denk bijvoorbeeld aan de onderhoudsdienst die onderdelen uit de productielijn moet takelen voor een revisie, terwijl wij tegelijkertijd van plan waren om de turbine in te hijsen. Dan sta je elkaar wel in de weg met je kraan.’
Kundig personeel
Ook het aansluiten van de nieuwe turbine in het bestaande proces was ingewikkeld. ‘Hierbij is het belangrijk dat goed wordt afgestemd welke onderdelen worden bediend, terwijl
de andere installaties blijven draaien en het proces niet wordt onderbroken. Bij de drukken en temperaturen waarbij de machines opereren wil je niet dat er iets mis gaat, dat is erg gevaarlijk. Het is een kwestie van de werkzaamheden goed coördineren, en dat is goed gelukt. Er is geen onvertogen woord gevallen.’ Kooman dankt het goede verloop van zijn project aan de aanwezigheid van kundig personeel. ‘Er zijn binnen ons bedrijf veel techneuten aanwezig die denken in oplossingen. We hebben hier goede mensen aan boord, sommigen hebben al veertig jaar ervaring met deze installaties. Zij zijn hier dagelijks mee bezig en kennen de machines perfect. Dat geldt ook voor de automatisering. De nieuwe turbine is aangesloten op het overkoepelende besturingssysteem, waarmee we al in detail bekend zijn.’ Dat was ook voor de leveranciers een voordeel, weet Kooman. ‘Het is voor hen veel gemakkelijker om te praten met experts over de technische details van een turbine en de automatisering. Dat zorgt ervoor dat het werk sneller kan worden uitgevoerd.’
Inlopen op de planning
Ook is het volgens Kooman belangrijk verantwoordelijkheden neer te leggen bij de technische mensen. ‘Ze vinden het fijn om die verantwoordelijkheid te krijgen en betrokken te worden bij het overlegproces en bij het nemen van beslissingen over onderhoud en productie. Die betrokkenheid zorgt ervoor dat projecten ook op de werkvloer soepel verlopen.’ Natuurlijk waren er ook obstakels in het drie jaar durende project. ‘Er waren kleine vertragingen, bijvoorbeeld door storingen in de andere productielijnen of planningsproblemen
bij de leveranciers. Uiteraard hadden wij ook last van het corona-virus. Dat deed zijn intrede toen we de nieuwe installatie net besteld hadden. We zagen de markt daarop reageren en moesten ons hier flexibel op instellen. Ook had het virus natuurlijk impact op de beschikbaarheid van het personeel.’ Kooman vertelt dat er in de planning van het project rekening is gehouden met deze kleine tegenslagen. ‘Hierdoor konden we zelfs inlopen op de planning. We hadden gepland om de nieuwe turbine uiterlijk in het eerste kwartaal van 2022 op te starten. Het is gelukt om al in november 2021 te testen en meteen op maximaal vermogen te draaien. De installatie is sindsdien continu in bedrijf.’
MARCEL KOOMAN PROJECTMANAGER STRATEGISCHE PROJECTEN AVR Kooman vindt het belangrijk verantwoordelijkheden neer te leggen bij de technische mensen. ‘Betrokkenheid zorgt ervoor dat projecten ook op de werkvloer soepel verlopen.’
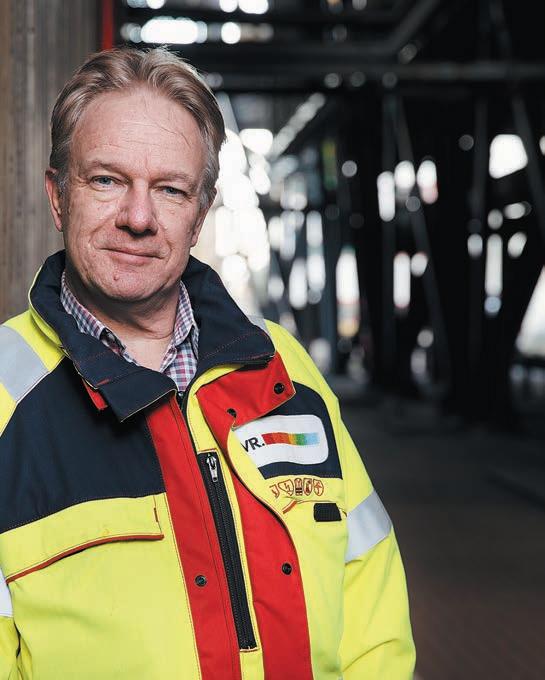
Toekomst
Een apart comité onderzoekt nog wat er moet gebeuren met de andere twee oudjes die bij AVR draaien, turbine A en C. ‘Natuurlijk zijn A en C de meest voor de hand liggende installaties om naar te kijken. Er worden prognoses gemaakt voor de toekomst en daarop worden beslissingen gebaseerd voor wat betreft het turbinepark. De vraag is dan of het rendabel is om ze te reviseren en terug te plaatsen of dat er net als in het geval van turbine B een nieuwe installatie komt. Daar wordt nog over gediscussieerd.’ Interessante ontwikkelingen voor AVR Rozenburg zijn er sowieso voor de toekomst. Zo staat er een nieuwe slakkenband op stapel. Met slakken wordt het restant van het afval bedoeld, dat overblijft na verbranding. De slakkenbanden zorgen voor de afvoer van dit restproduct. Een andere ontwikkeling met het oog op de toekomst is CO2-afvang. Op de AVR-locatie in Duiven draait al een CO2-afvang pilot. Er wordt nu onderzocht of dit navolging kan krijgen in Rozenburg.
Met kleine stappen naar
voorspellend onderhoud
Inmiddels is wel duidelijk welke voordelen de koppeling van informatietechnologie aan operationele techniek kan brengen. Toch lijkt de maakindustrie nog nauwelijks gebruik te maken van de mogelijkheden die industrie 4.0 biedt. Jan Peter Kruiger van MAAK Techniek & Proces vroeg Tiedo Tinga van Universiteit Twente, Jan Post van Rijksuniversiteit Groningen en Chris van den Belt van Ultimo om in een live talkshow de knelpunten boven water te tillen.
Tiedo Tinga is professor dynamisch onderhoud aan de Universiteit Twente en heeft veel ervaring met voorspellend onderhoud bij Defensie. Zelfs in die hightech omgeving is de inzet van kunstmatige intelligentie nog best een uitdaging. ‘Het goede nieuws is dat de assets van Defensie weinig met storingen kampen’, zegt Tinga. ‘Maar dat is tegelijkertijd de uitdaging voor lerende algoritmes. Als je weinig storingen hebt, is het ook lastig om daar patronen in te ontdekken.’ De industrie heeft wat dat betreft meer data beschikbaar. Je kunt eenvoudiger data verzamelen van kritische systemen zoals pompen. Toch lijkt er ook in die omgeving nog niet veel te gebeuren met big data analyse en algoritme-ontwikkeling. Ook daar vormt de datakwaliteit een beperking, stelt Tinga. ‘De procesbesturingssystemen leggen de procesdata wel vast, maar voor conditiebewaking zijn toch andere parameters nodig. We zijn nu aan het verkennen welke data cruciaal zijn voor de uptime van systemen. Zodat je alleen de kritische data hoeft te verzamelen en analyseren. Dat doen we bijvoorbeeld bij de dieselmotoren van marineschepen. Door temperatuursensoren op de lagers te zetten, kan de maintenance engineer verschillen in temperatuur meten bij hoog- en laagvermogen. Als
Jan Peter Kruiger van MAAK is ervan overtuigd dat bedrijven meer waarde uit hun fabriek kunnen halen door efficiënter onderhoud. Kruiger: ‘Zonder het te weten, hebben bedrijven al een schat aan informatie liggen. Het is de kunst juist díe informatie boven water te krijgen, die daadwerkelijk waarde toevoegt aan de productieketen. Bedrijven hebben een onderhoudbeheersysteem (OBS), maar gebruiken slechts een fractie van de mogelijkheden die zo’n systeem biedt. Het vergt ook tijd, kennis en inzicht om zo’n systeem goed in te richten en de data te doorgronden. Maar het levert wel heel veel op als je dat doet. In dat proces biedt de kennis van MAAK echt een meerwaarde. Wij zijn geen OBS-leverancier maar weten wel wat zo’n systeem zou moeten kunnen. Als mediator tussen softwareleverancier en gebruiker kunnen we de processen identificeren, structureren, verbeteren en beheren. Pas als je de juiste data op het juiste moment beschikbaar hebt, kun je datagestuurd optimaliseren. Dan komt het ultieme einddoel in zicht: voorspellend onderhoud. Maar daarvoor zal je dus wel alle tussenstapjes moeten nemen.’ dan de patronen gaan afwijken, kan het systeem tijdig waarschuwen dat de faalkans de limiet overschrijdt en vervanging nodig is.’
Predictive Quality
Jan Post is professor digitale productie aan de Rijksuniversiteit Groningen. Post deed zijn ervaring met industrie 4.0 vooral op bij Philips Drachten, dat met hightech productielijnen consumentenproducten zoals scheerapparaten produceert. ‘In de consumentenmarkt is datacollectie nog een stuk lastiger’, zegt Post. ‘Een industriële pomp gaat soms dertig tot veertig jaar mee en bouwt in die tijd een lange historie op. De productielijnen van Philips moeten vaak om de twee à drie jaar worden aangepast aan nieuwe producten. Dan begin je iedere keer opnieuw met datacollectie. In zo’n omgeving moet je gebruik maken van zowel a priori als a postiori data. Je begint met modellen en stelt die bij naarmate er meer sensordata beschikbaar komt. We onderzoeken binnen de Rijksuniversiteit hoe we die data kunnen fuseren. Daar is veel mee gemoeid omdat er een direct verband is tussen deze procesdata en de productkwaliteit. Bedrijven als Philips maar ook ASML en Tata Steel willen op voorhand de kwaliteit van een product kunnen voorspellen, zodat hun klanten precies krijgen waar ze om gevraagd hebben. Predictive maintenance is
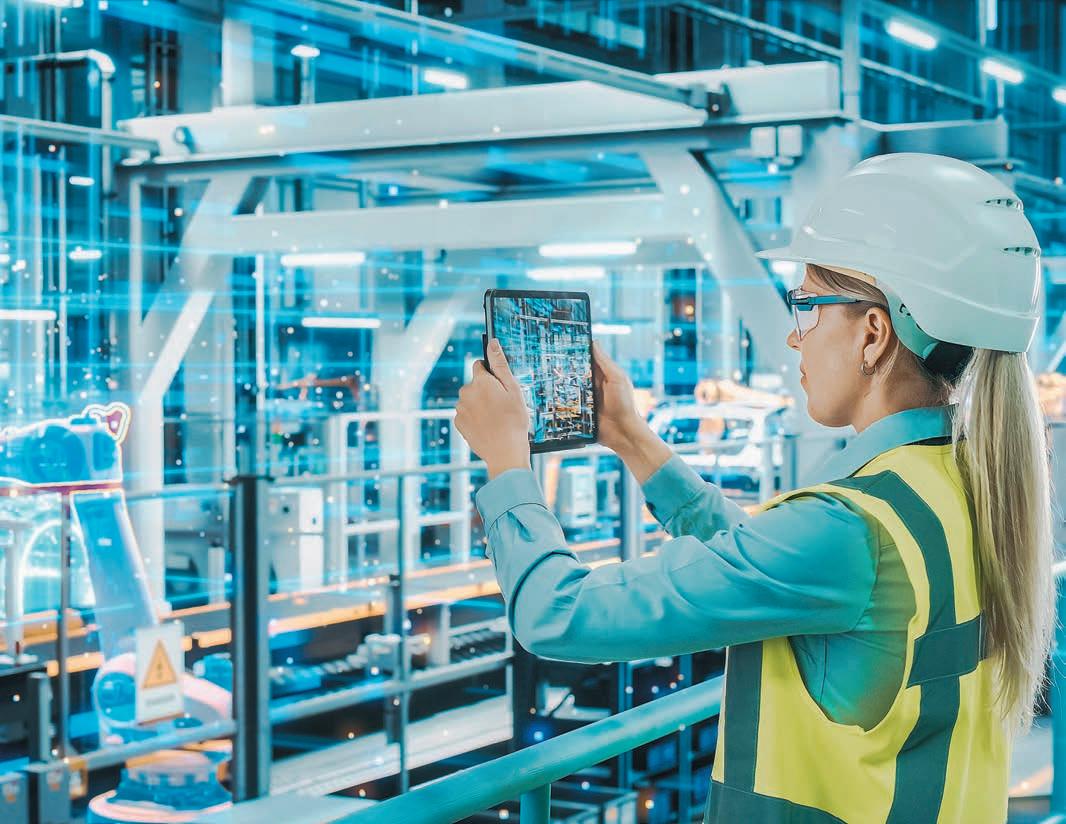
Procesbesturingssystemen leggen de procesdata wel vast, maar voor conditiebewaking zijn toch andere parameters nodig.
daar wel een onderdeel van, maar als je stuurt op predictive quality of zero defects gebruik je de beschikbare data veel efficiënter.’ Philips gaat zelfs zo ver dat het bedrijf ook de data van de leveranciers van bijvoorbeeld staal meenemen in de data-analyses, weet Post. ‘Omdat kwaliteitsverschillen in het staal uiteindelijk ook de kwaliteit van het eindproduct van Philips bepaalt. Hebben ze dit goed onder controle, dan heeft dat ook kostenvoordelen. Bijvoorbeeld omdat je van tevoren weet wanneer je welke reserveonderdelen nodig hebt, maar ook omdat je minder hoeft af te keuren. Door holistisch op kwaliteit te sturen, stuur je ook op alle andere KPI’s.’
Groeimodel
Hoewel de voorbeelden die Tinga en Post schetsen veel vertrouwen geven in de toekomst, werken nog maar weinig bedrijven echt datagestuurd. Dat is ook de conclusie uit een trendonderzoek onder 350 bedrijven van leverancier van onderhoudbeheersoftware Ultimo. ‘Veel bedrijven scoren nog redelijk laag
in het enterprice asset management groeimodel’, vetelt Chris van den Belt van Ultimo. ‘Het percentage correctief onderhoud is bij die bedrijven nog relatief groot. Waar dat aan ligt, is soms moeilijk te doorgronden. Veel heeft te maken met de volwassenheid van de onderhoudsorganisatie, maar ook met budgetten. Bedrijven willen nog wel eens een pilot uitvoeren voor preventief onderhoud, maar het is vervolgens de vraag wie de bredere implementatie betaalt.’
Het is de kunst om alle afdelingen in lijn te krijgen en de kosten en baten af te wegen voor productie, logistiek of bijvoorbeeld magazijnbeheer, stelt Van den Belt. ‘Als je minder storingen hebt, profiteert daar natuurlijk niet alleen de onderhoudsafdeling van.’
Jan Post professor digitale productie Rijksuniversiteit Groningen