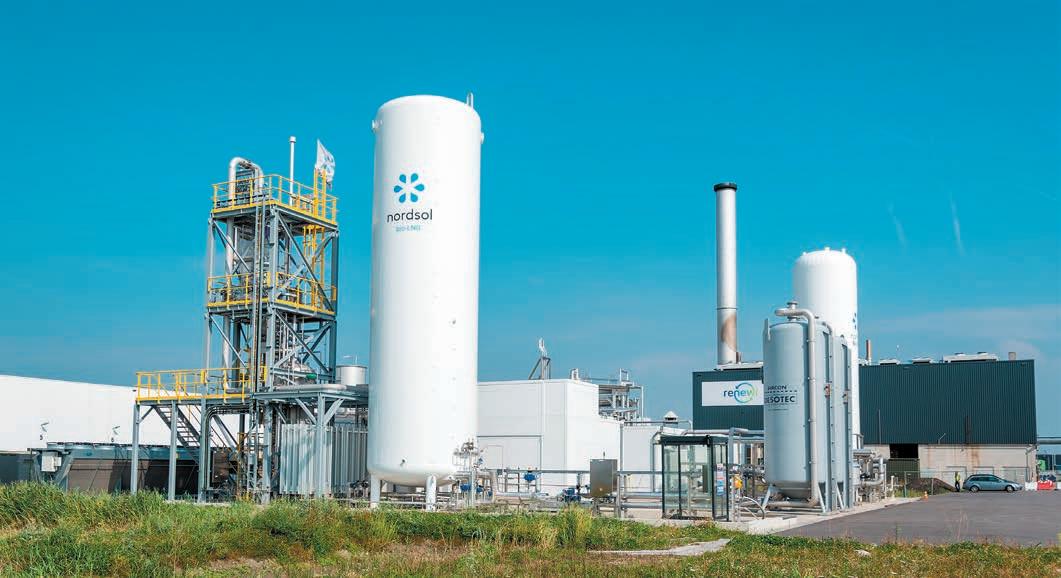
22 minute read
PROJECT Nordsol koppelt twee werelden met bio-LNG
Nordsol koppelt twee werelden met bio-LNG
Van oorsprong is Nordsol een technologiebedrijf. Het ontwikkelde een technologie om op zeer kleine schaal en toch economisch haalbaar bio-LNG te maken. Maar inmiddels is het bedrijf doorgegroeid naar een allround bio-LNG-expert, met stevige ambities.
Advertisement
Liesbeth Schipper
Groengas versus bio-LNG
De beste manier om het zware lange afstand transport te verduurzamen, is door biogas om te zetten in bio-LNG, stelt Van Bossum. ‘Als je in die sector met een volledig groen product komt ten opzichte van diesel, creëer je ontzettend veel groenwaarde. Vergelijk dat met verduurzaming van het aardgasnetwerk. Dan maak je alleen de stap van grijs gas naar groen gas. Wij proberen in een keer de stap van diesel naar bio-LNG te krijgen, met als transitiebrandstof LNG.’ Daarnaast heeft bio-LNG een sociale waarde, vindt Van Bossum. ‘Groengas is een SDE-subsidievariant. Ons model is erop gericht onafhankelijk te zijn van dit soort subsidies.’ En dat kan, want de vraag naar bio-LNG is groot, stelt Van Bossum. ‘De biovariant is nu misschien nog nieuw, maar de infrastructuur rond LNG is al dertig jaar in ontwikkeling. Er zijn inmiddels heel wat vrachtwagens die op LNG rijden en er is ook al een fl ink aantal tankstations in Europa waar LNG kan worden getankt. De markt is er en groeit bovendien hard. Combineer dat met de vraag naar een honderd procent groene variant, dan leidt dit ook fi nancieel tot een betere waardering van bio-LNG ten opzichte van groengas.’ Het doel is om in 2025 meerdere installaties met een totale capaciteit van 25 kiloton bio-LNG operationeel te hebben. De eerste fabriek van Nordsol in Amsterdam, met een capaciteit van ongeveer 3,4 kiloton bio-LNG per jaar, staat er al. Een tweede fabriek in Wilp gaat in 2023 ongeveer 2,4 kiloton bio-LNG per jaar produceren. En zo moeten er nog veel meer installaties volgen. Het concept van de eerste twee fabrieken is ongeveer hetzelfde. In beide gevallen is er een afvalverwerker die biogas levert en een energiebedrijf dat bio-LNG afneemt, met Nordsol als schakel daartussen. ‘Die twee werelden zijn compleet verschillend’, vertelt Léon van Bossum, commercieel directeur van Nordsol. ‘Wij zagen een paar jaar geleden al snel in dat het lastig zou worden onze technologie in zo’n onvolwassen markt te zetten. We moesten die twee werelden met elkaar verbinden, zelf lef tonen en een belangrijke rol als schakel gaan spelen om de bio-LNG-markt in beweging te krijgen.’
Prijsgarantie
Aan de vraag ligt het niet, de energiewereld zit te springen om bio-LNG, stelt Van Bossum. ‘Elektrisch rijden gaat met zwaar lange-afstandtransport niet. Dan ben je een te groot deel van je laadcapaciteit kwijt aan batterijen. Misschien gaat in de toekomst waterstof nog een rol spelen, maar op dit moment is bio-LNG een goed alternatief voor diesel.’ Nordsol stapte daarom eerst naar energiebedrijven toe en vond Shell bereid om als launching customer een lange termijn afnamecontract te garanderen. ‘Shell zag in dat het nodig was om een garantie te geven en ook risico naar zich toe te trekken om op die manier toegang te krijgen tot bio-LNG. Zo kwam de onzekerheid van die nieuwe markt niet bij de biogasproducent te liggen, en ook niet bij ons.’ Vervolgens kon Nordsol met een prijsgarantie naar de biogasproducenten toe, waaronder Renewi. Deze afvalverwerker had lange tijd haar biogas omgezet in elektriciteit, maar het oude subsidieregime voor warmtekrachtkoppeling liep bijna af. Het bedrijf stond voor de keuze: gaan we er groengas van maken of bio-LNG? ‘We gaven aan dat we een lange termijn prijsgarantie kunnen geven, eigenlijk net zoals met de subsidietrajecten. Bovendien namen wij zelf de verantwoordelijkheid voor de technologie. Dit businessmodel zorgde ervoor dat Renewi, Shell en Nordsol bij elkaar zijn gekomen. En dat we de allereerste bio-LNG-plant van Nederland konden realiseren.’
Optimaliseren
De fabriek in Amsterdam is in vijftien maanden gebouwd en werd vorig jaar in oktober opgestart. ‘Natuurlijk kom je met zo’n
De eerste fabriek van Nordsol in Amsterdam heeft een capaciteit van ongeveer 3,4 kiloton bio-LNG per jaar.
eerste plant nog problemen tegen die je moet oplossen, maar het was mooi om te zien dat het proces functioneert. En vooral dat er een hoogwaardige kwaliteit bio-LNG uit komt. Shell heeft bepaalde eisen waar de brandstof aan moet voldoen en we zien dat de kwaliteit daar ver boven ligt.’ Nordsol is het proces nog altijd aan het optimaliseren. ‘Daarvoor hebben we zeer geavanceerde plant information software geïnstalleerd, die gebruikelijk is in de olie- en gasindustrie op heel grote plants.’ Van Bossum lacht: ‘We kunnen daarmee ook op onze kleine postzegel-plant alle data analyseren en dat helpt ons om het proces verder te optimaliseren. Waar kan het nog slimmer, nog efficiënter?’ Die kennis neemt het bedrijf mee naar een tweede project in Wilp. Daar vormt Nordsol eveneens de schakel, in dit geval tussen afvalverwerker Attero en energiebedrijf Titan. Met Titan als lange termijn afnemer van het geproduceerde bio-LNG maakt Nordsol meteen het palet van brandstoffen voor zwaar transport compleet. Want waar Shell zich met de geproduceerde bio-LNG richt op wegtransport, gaat Titan het straks leveren aan de scheepvaart.
Gigantisch grote vergister
Een heel andere insteek krijgt de samenwerking met DBG Bio Energy. Dit bedrijf bouwt in Delfzijl een fabriek die afval uit de papierindustrie gaat omzetten in onder andere bioLNG. Het heeft vertrouwen in de bio-LNG-markt en wil het stuur zelf in handen hebben, stelt Van Bossum. ‘DBG neemt alleen de technologie om biogas om te zetten in bio-LNG bij ons af, en bovendien alle kennis om het project mogelijk te maken. Die kennis hebben we opgedaan omdat we eerder de verantwoordelijkheid hadden genomen voor het eerste project in Amsterdam. En daar kwam heel veel bij kijken, want we waren op allerlei vlakken de eerste: met vergunningen, regelgeving, veiligheidseisen en accijnzen.’ Nordsol is voor DBG Bio Energy dus meer dan alleen een technologieleverancier. ‘Al in het voortraject zijn we nauw betrokken en we helpen ook met regelgeving en de afzet van de bio-LNG. Maar dat doen we dan als partner, niet als medeeigenaar van de installatie.’
DBG Bio Energy mikt naar eigen zeggen op een capaciteit van 15 kiloton bio-LNG per jaar en wil eind 2022 de productie opstarten. ‘Ze gaan in Delfzijl een gigantisch grote vergister plaatsen. Dus dat betekent dat we meerdere installaties naast elkaar moeten zetten om die capaciteit te kunnen leveren. Het grote voordeel van meerdere procestreinen is dat je de beschikbaarheid hoog houdt. Je hebt dan immers redundancy en hoeft niet alles stil te leggen als je een keer onderhoud hebt.’
LÉON VAN BOSSUM COMMERCIEEL DIRECTEUR NORDSOL
Verstoring
Verdere groei voorziet Nordsol voorlopig vooral in Nederland. ‘We willen verantwoord groeien. In eerste instantie richten we

ons daarom op de Nederlandse markt, want er zijn hier veel vergisters en er is ook een sterke vraag naar bio-LNG. Datzelfde zien we overigens ook in Duitsland, dus we zitten daar met sommige projecten ook al in een early phase. Daarnaast kijken we naar België om zelf projecten te ontwikkelen. Maar we zijn eveneens in gesprek met partijen buiten deze drie landen want er is veel interesse voor de technologie. Dat zouden vergelijkbare projecten als met DBG Bio Energy kunnen worden.’ De enige verstoring in het lange termijn groeiproces ziet Van Bossum in Duitsland, waar een aantal partijen centrale vervloeiingsfabrieken bouwt. Deze maken op grote schaal bio-LNG door gas uit het aardgasnet te halen en om te zetten in bio-LNG. Dit gas bestaat voor het overgrote deel uit administratief vergroend aardgas en een klein deel groengas dat op andere plaatsen is geïnjecteerd. Hoewel het geen echte bio-LNG is die ze maken, klopt het op papier wel. ‘Nou is Duitsland een enorm grote markt, dus er is voldoende vraag naar bio-LNG. Maar het is voor ons een verstoring want nu blijven sommige bedrijven die biogas produceren deze ontwikkeling afwachten, terwijl wij eigenlijk willen versnellen.’ Het lijkt een prima manier om snel grote hoeveelheden bioLNG te genereren en zo de markt tot wasdom te brengen, maar Van Bossum heeft moeite met de kromme logica erachter. ‘Wat je eigenlijk met zo’n centrale vervloeiing doet, is dat je eerst biogas opschoont naar 95 tot 97 procent methaan. Vervolgens meng je er stikstof bij om laagcalorisch gas te krijgen en dat injecteer je in het aardgasnetwerk. Op een centrale locatie haal je dan weer gas uit het netwerk om het opnieuw te gaan reinigen. Er zit vocht in, hogere koolwaterstoffen en ook de stikstof moet eruit. En je werkt met aardgas wat vergeleken met biogas best wel een vies complex gas is. Je reinigt dus dubbel en je hebt ingewikkeldere technologie nodig om al die componenten er weer uit te halen.’
Karakteristieken
Gas van goede kwaliteit opschonen, vervuilen en daarna weer opschonen, staat ook haaks op de filosofie van Nordsol. ‘Je wilt de energie in biogas zo efficiënt mogelijk omzetten in een vorm die het meest waardevol is voor de energietransitie. Daarom hebben wij onze technologie juist volledig afgestemd op de specifieke karakteristieken van biogas. Er zijn namelijk grote verschillen tussen biogas en aardgas. Zoals gezegd is de compositie van aardgas vele malen complexer dan die van biogas. Eigenlijk is biogas een veel puurdere gasvorm. Een ander belangrijk verschil is dat biogasproductie per locatie aanzienlijk kleiner in capaciteit is dan aardgasproductie. Bovendien schommelt de capaciteit van een vergister, afhankelijk van welke feedstock er binnen komt. Het is geen stabiele productie, zoals bij een aardgasbron. Ook de economische huishouding is compleet verschillend. Ten opzichte van aardgas is biogas een kostbaar product. Het is zonde om dat te gebruiken als energiebron van je proces, dus energieverliezen willen we absoluut voorkomen.’
Projecten Nordsol
Leverancier biogas: Renewi Afnemer bio-LNG: Shell Locatie: Amsterdam Capaciteit: 3,4 kiloton bio-LNG per jaar In productie: 2021
Leverancier biogas: Attero Afnemer bio-LNG: Titan Locatie: Wilp Capaciteit: 2,4 kiloton bio-LNG per jaar In productie: 2023
Project in ontwikkeling: DBG Bio Energy Locatie: Delfzijl Capaciteit: 15 kiloton bio-LNG per jaar Geplande start productie: eind 2022
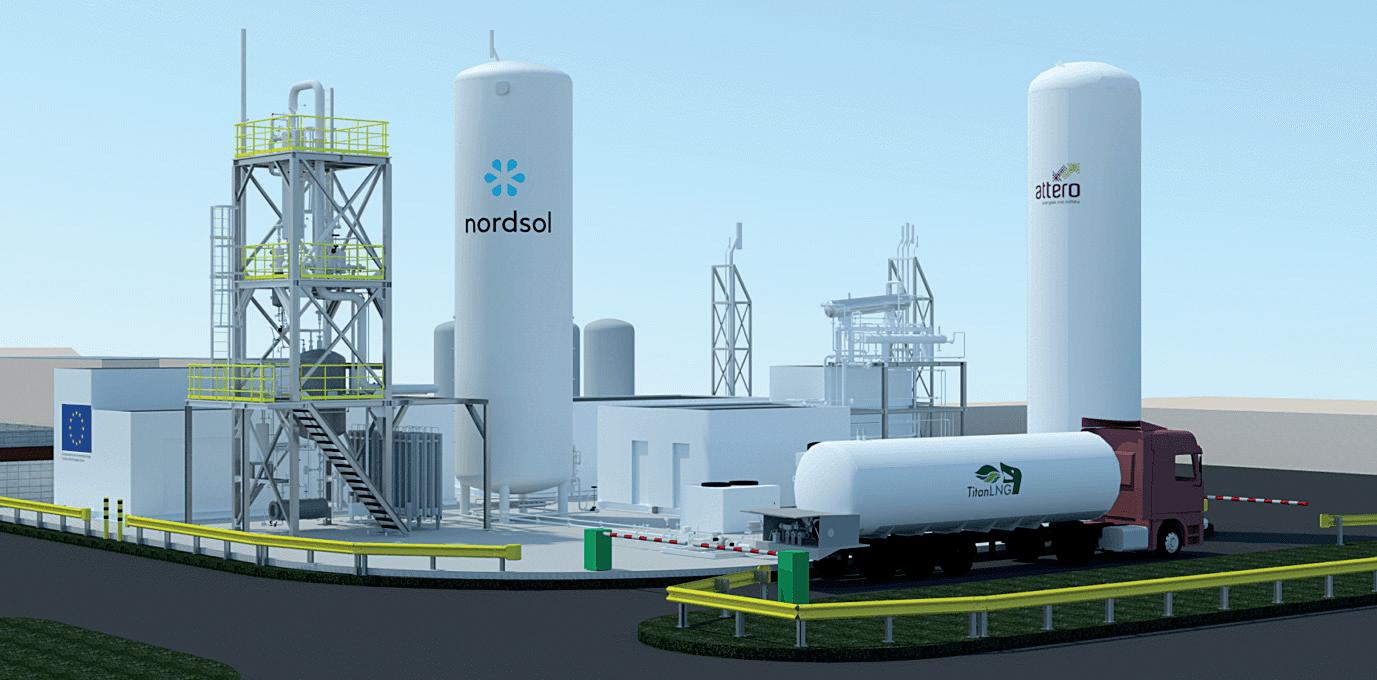
De tweede fabriek van Nordsol in Wilp gaat vanaf 2023 ongeveer 2,4 kiloton bio-LNG per jaar produceren.
Koelmedium
In plaats van domweg de bekende processen in de fossiele industrie te downscalen, heeft Nordsol daarom een proces ontworpen dat helemaal is geoptimaliseerd voor verwerking van ruw biogas uit een vergister. Dit bestaat grof gezegd voor zestig procent uit methaan en veertig procent uit CO2. Een voorbehandeling haalt er nog wat onzuiverheden uit, afhankelijk van wat de feedstock is. Daarna volgt het
hoofdproces: het scheiden van het methaan en de CO2. Dit is dezelfde membraantechnologie die wordt toegepast om groengas te maken. ‘Het verschil is echter dat wij dit opwaarderingsproces heel nauwkeurig kunnen doen. Met onze gepatenteerde technologie kunnen we een heel hoog methaangehalte uit die membraantechniek halen. Waar je normaal gesproken tussen de drie en zeven procent CO2 in het productgas overhoudt, houden wij nog maar een paar honderd ppm aan CO2 over.’ De tweede stap is het vervloeien, waarbij het gas in een warmtewisselaar eerst heel gecontroleerd wordt gekoeld zonder de faseverandering naar een vloeistof. Het gas komt hierdoor in de zogenaamde superkritische fase. ‘Speciaal voor deze stap maken we het methaan tijdens het opwaarderingsproces zo extreem schoon. We willen namelijk voorkomen dat er componenten in het gas zitten die eerder uitvriezen, want dan krijgen we verstoppingen in de warmtewisselaar. Pas na de warmtewisselaar, als we van druk afgaan en het gas flashen, wordt het vloeibaar. Ook daarmee voorkomen we dat er verstoppingen ontstaan en houden we de uptime van de plant zo hoog mogelijk. De afwezigheid van vloeistoffen in de warmtewisselaar zorgt voor het uitblijven van sterke temperatuurgradiënten en dus minder risico van materiaalmoeheid en lekkages.’ Bijzonder is dat Nordsol bij het vervloeien methaan gebruikt als koelmedium. ‘We koelen dus methaan met methaan. Het voordeel daarvan is dat je op die manier dezelfde koelcurves hebt wat resulteert in minder energieverlies. Het is een heel efficiënte manier van koelen en zorgt ervoor dat ons energieverbruik aanzienlijk lager is dan dat van vergelijkbare processen in de markt. Bovendien kunnen we bij schommelende productievolumes het koelmedium gemakkelijk bij- en afschakelen, we produceren het immers zelf. Los daarvan, een van de grote voordelen van het proces is ook dat het een geheel continu proces is, wat leidt tot een continue biogasinname zonder flaring.’
LÉON VAN BOSSUM COMMERCIEEL DIRECTEUR NORDSOL
Keuze
Renewi en inmiddels ook Attero zijn de eerste industriële vergisters die de technologie en het businessmodel van Nordsol hebben omarmd. En Van Bossum verwacht dat andere vergisters zullen volgen. ‘Oorspronkelijk werd alle biogas via een warmtekrachtkoppeling omgezet in elektriciteit. De afgelopen tien jaar is een deel van de vergisters overgestapt op de productie van groengas, dat ze injecteren in het aardgasnet. Maar er zijn ook veel vergisters die nog in het oude subsidieregime van warmtekrachtkoppeling zitten. Die lopen binnen een aantal jaren uit de subsidie en staan net als Renewi voor de keuze: zetten we ons biogas om in groengas of in bioLNG? Dat zijn de partijen waar wij ons het meest op richten.’
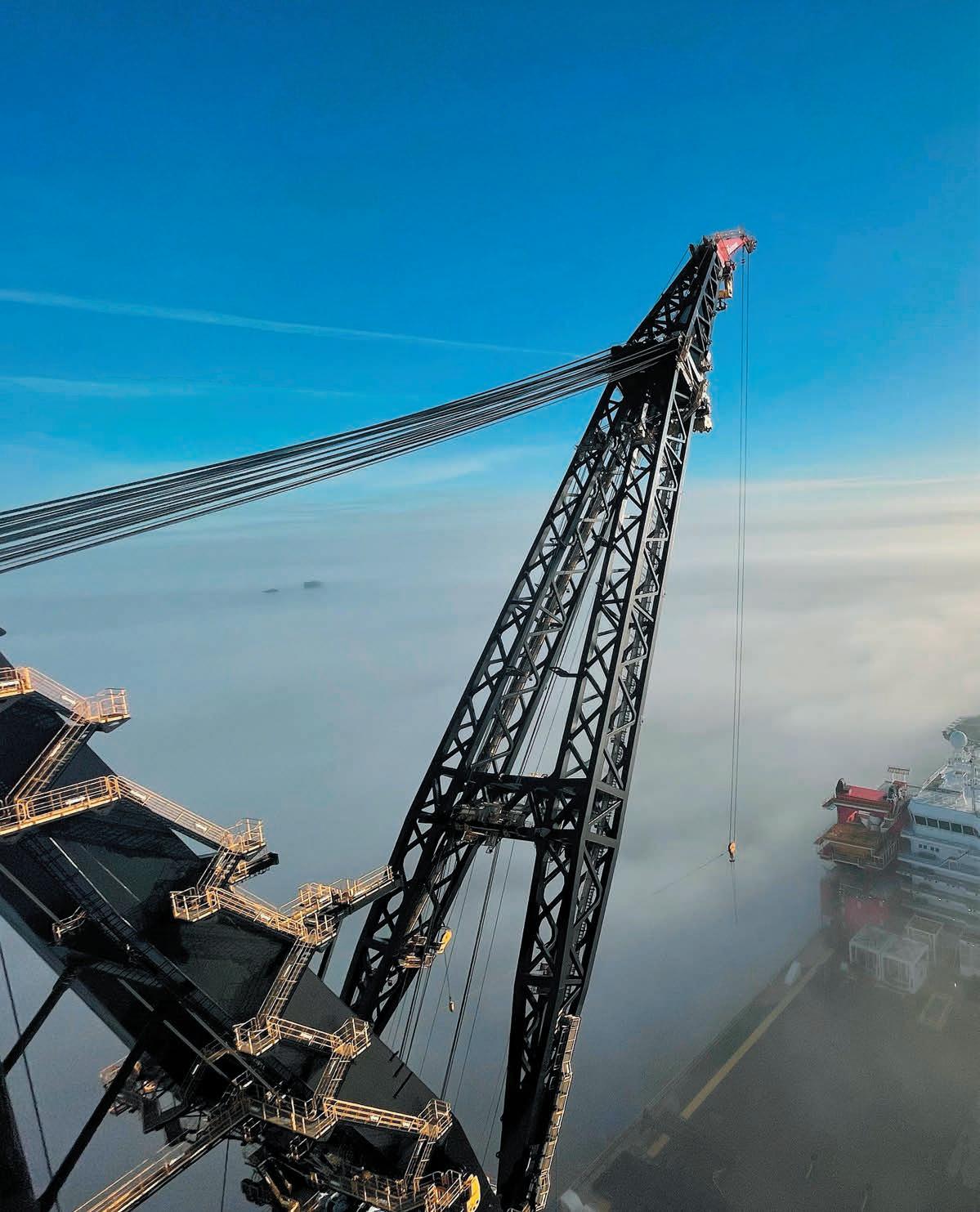
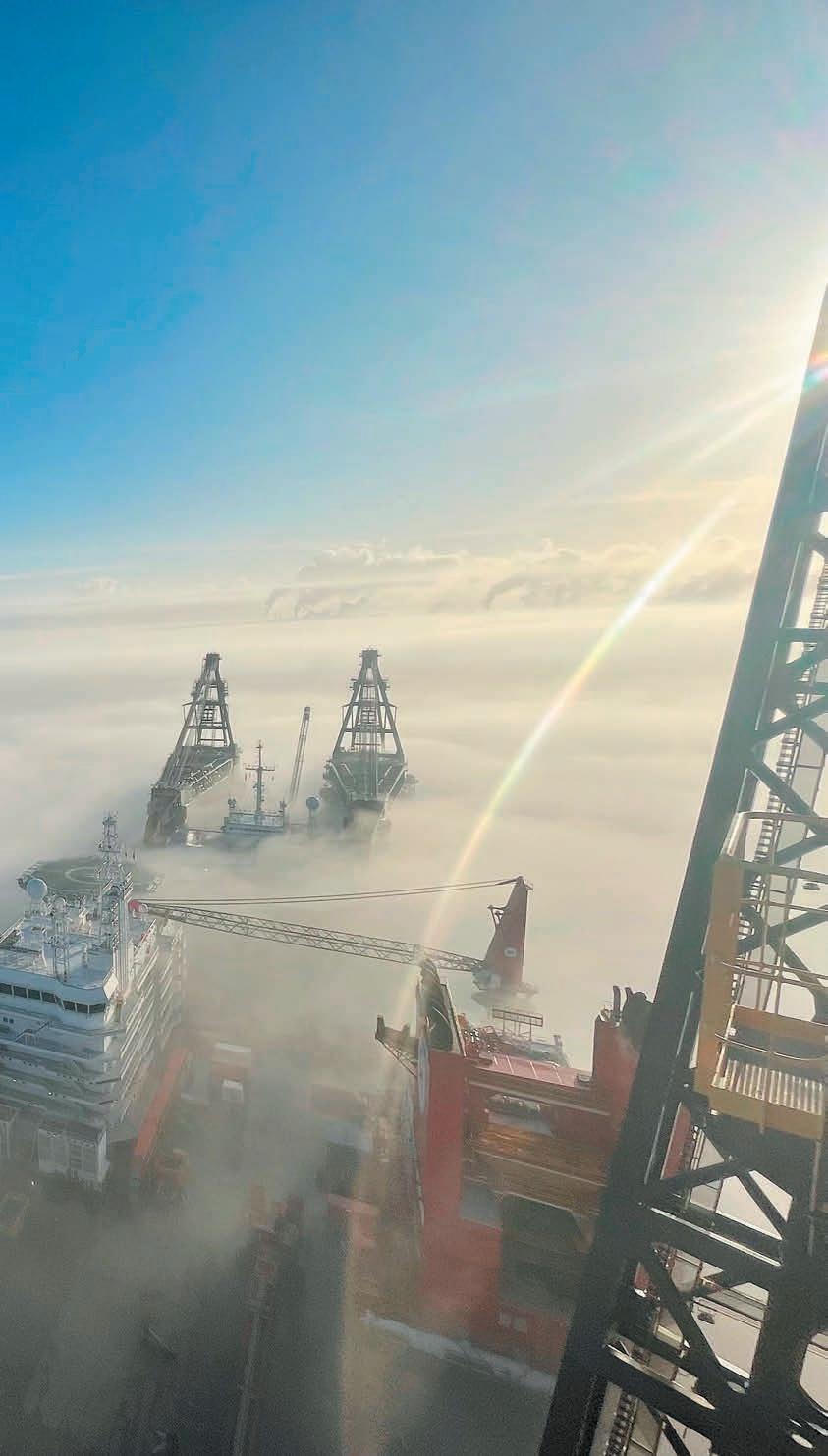
Heerema gaat dit jaar 27 windturbines voor het 257 MW o shore windpark Arcadis Ost I van Parkwind in de
Oostzee installeren. Het bedrijf zet daarvoor Thialf in, maar moet het op één na grootste halfafzinkbare kraanschip ter wereld er wel voor aanpassen. Om van de thuisbasis in de haven van Rotterdam naar de projectlocatie Arcadis Ost te komen, moet Thialf onder de Storebaelt-brug in Denemarken door. De brug verbindt de Deense eilanden Zeeland en Funen en heeft een doorvaarthoogte van 65 meter. Thialf meet echter 105 meter hoog. Het kraanschip ondergaat daarom in Rotterdam een modifi catie. De A-frames hebben al scharnierbare hoeken. Met een speciaal ontworpen systeem kan Heerema de kranen laten zakken en de A-frames opvouwen. In combinatie met ballast kan het kraanschip dan toch de Storebaeltbrug passeren, zonder dat de capaciteit van de kranen is aangetast. Deze kunnen ook straks nog 14.200 ton hijsen.
Stikstof laat sommige planten in natuurgebieden zo hard groeien dat ze andere planten verdrukken en daarmee de biodiversiteit verstoren. Het is dus zaak om stikstof uit afvalwater te verwijderen, zodat de meststof alleen daar terechtkomt waar hij een positieve bijdrage levert. Met dat doel voor ogen besloot een Europees consortium een proefinstallatie te bouwen om stikstof uit reststromen op te werken naar hoogwaardig kunstmest.
Binnen het Europese kennisconsortium N.E.W.B.I.E.S., wat staat voor Nitrogen Extraction from Water By an Innovative Electrochemical System, werkten Evides Industriewater, W&F Technologies, Wetsus en het Catalaanse waterinstituut ICRA samen. Paula van den Brink van Evides Industriewater en Sam Molenaar van W&F Technologies hebben de proef inmiddels afgerond en weten nu veel beter voor welk afvalwater ze elektrodialyse het beste kunnen inzetten. Van den Brink: ‘Er zijn diverse reststromen die stikstof bevatten, zoals digestaat of urine. Normaal gesproken Een techniek waar W&F Technologies al ervaring mee had. Molenaar: ‘De chloor/ alkali-industrie gebruikt al sinds jaar en dag bipolaire elektrodialyse voor het scheiden van zuren en basen uit zout water. W&F Technologies ontwikkelde een asymmetrische bipolaire elektrodialyse die alleen het basische ammoniak extraheert. Het zuur blijft in dat geval gewoon achter in het afvalwater. In veel reststromen bestaat het zuur voornamelijk uit koolzuur. Dit is ideaal, want dit komt dan spontaan als koolzuurgas uit de oplossing bubbelen. Op die manier concentreer je dit gas zonder het echt af te scheiden.’
moet deze stikstof worden verwijderd via nitrificatie en denitrificatie, processtappen in de afvalwaterzuivering, voordat het water kan worden geloosd. Maar als je toch een extra stap moet doen om stikstof te verwijderen, waarom zou je dan niet proberen het als meststof te concentreren? Daarmee creëer je een circulaire meststof waarvoor geen nieuwe grondstoffen nodig zijn.’
Elektrodialyse
De technologie die chemicaliënvrije extractie mogelijk moest maken, was ook al bekend: Bipolaire elektrodialyse.
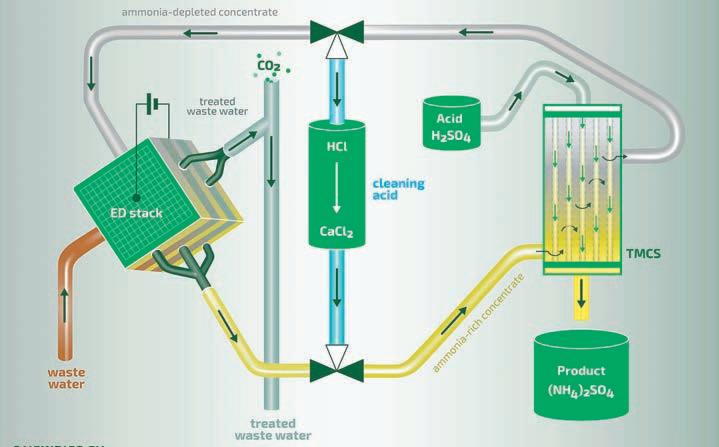
W&F Technologies ontwikkelde een asymmetrische bipolaire elektrodialyse die alleen het basische ammoniak extraheert.
Drie reststromen
Om de werking van het ontwerp te testen, selecteerde het consortium drie reststromen: vergistingsreactiewater oftewel digestaat, urine en tot slot percolaatwater. Van den Brink: ‘Veel waterschappen vergisten hun slib en houden daarna een stikstofrijke deelstroom over. En over stikstofrijke stromen gesproken: urine bevat in verhouding tot andere stoffen de meeste stikstof. Wat betreft stikstofconcentratie is percolaat, het water dat doorsijpelt bij vuilstortplaatsen, juist minder interessant. We wilden deze laatste stroom echter graag onderzoeken omdat elektrodialyse veel voordelen leek te bieden om het redelijk vervuilde water te reinigen. De selectieve scheiding van stikstof zou op
het percolaat een uitkomst kunnen bieden, ware het niet dat het water relatief weinig stikstof bevat in verhouding tot de andere stoffen in het water.’
Stack
De projectpartners bouwden een mobiele kunstmestfabriek in een zeecontainer. Deze fabriek wint vanuit verschillende afvalstromen diverse voedingstoffen terug. Molenaar: ‘De elektrodialyse-stack bestaat uit een stapel afwisselende membranen van twee typen: bipolaire en kation uitwisselmembranen. Deze stapel is ingeklemd tussen twee elektroden. Tussen de membranen door liggen zeefjes die het mogelijk maken water langs de membranen te voeren.’ Door het vervuilde water langs de membranen te laten stromen en tegelijkertijd spanning op de elektroden te zetten, trekken de positieve ionen naar de negatieve elektrode, en de negatieve ionen zullen de neiging hebben naar de positieve pool te trekken. De membranen zorgen er echter voor dat alleen positieve ionen worden doorgelaten. Daardoor ontstaat een ammoniakrijke tweede stroom, waar echter ook nog veel andere zouten in zitten zoals natrium. ‘Om de waardevolle ammoniak over te houden, maken we gebruik van het feit dat ammoniak zeer vluchtig is, en leiden we het daarna nog over een waterafstotend, maar damp-open membraan. Aan de andere kant van dit membraan geleiden we zwavelzuur. De
ammoniak wordt hierin opgenomen waardoor er een zuivere ammoniumsulfaat oplossing ontstaat. Het mooie is dat ammoniumsulfaat een bekende kunstmestvariant is.’
Evides Industriewater ontwikkelt betrouwbare en duurzame wateroplossingen op maat voor de industrie. Daarbij staan het sluiten van de waterkringloop en het verkleinen van de waterfootprint centraal. Met innovatieve processen en technieken wordt (afval)water gezuiverd en worden warmte, nutriënten en andere grondstoffen teruggewonnen.
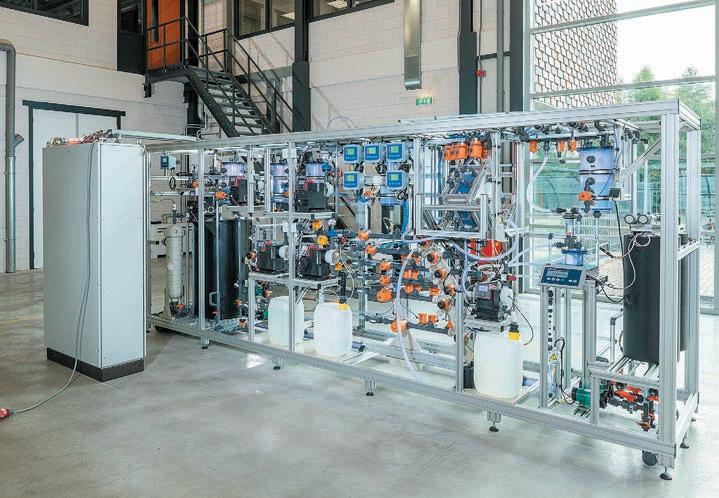
Chemicaliënvrije extractie van stikstof met de procesopstelling van Evides Industriewater, W&F Technologies, Wetsus en het Catalaanse waterinstituut ICRA
Paula van den Brink process engineer Evides Industriewater
Goede onderzoeksresultaten
Tegelijkertijd onderzocht Wetsus nog de mogelijkheid om ammoniak terug te winnen met een vacuümpomp. ‘Daarmee wordt het mogelijk om ammoniakaal water te produceren, wat een veelvoud van toepassingen kent. Variërend van kunstmest tot schoonmaakoplossing of voor het reguleren van de zuurtegraad. Daar is momenteel meer vraag naar dan naar ammoniumsulfaat.’ Beide waterexperts zijn tevreden over de resultaten van het onderzoek, al was het maar om te weten welke configuratie niet werkte. Van den Brink: ‘Evides Industriewater behandelt bijvoorbeeld al percolaatwater, maar we willen natuurlijk graag weten of dit efficiënter kan. Helaas bleek elektrodialyse niet de
gedroomde oplossing, met name omdat er relatief veel zouten en humuszuren in het water zaten opgelost. Dus in plaats van ammoniak haalden we er vooral veel zout uit.’ Opvallend was wel dat de stack nauwelijks hinder ondervond van de zwevende deeltjes in het water. ‘Het doel om ammoniak terug te winnen is dus wel behaald, maar helaas bleek het rendement in verhouding tot het energieverbruik te laag. De afgeleide resultaten kunnen gelukkig nog steeds interessant zijn voor andere stromen. Met name digestaten en condensaatwaters zijn zeer interessant voor stikstofwinning gebleken. Stikstof uit reststromen is daarmee een volwaardige basis voor hoogwaardig kunstmest.’
Sabic verhoogt veiligheidsbewustzijn met escape room
In aanloop naar een turnaround in 2019 trainde Sabic in Bergen op Zoom medewerkers op het gebied van veiligheid in een nagebootste fabriekshal. Inmiddels wordt het Safety Skills Center voor veel meer veiligheidstrainingen gebruikt en is zelfs een (digitale) escape room gebouwd.
Tijdens turnarounds – maar ook bij normale productieprocessen – heeft veiligheid bij Sabic de hoogste prioriteit. ‘Voorlichting aan werknemers via PowerPoint-presentaties, toolbox meetings en dergelijke, beklijft niet altijd’, stelt Judith Beers, senior manager Workforce Development and Continuous Improvement bij Sabic. ‘Veel werknemers hebben een hands-on mentaliteit. Onze visie is dat de leerimpact sterker is als je in een vroeg stadium werknemers in een praktijkruimte met risicovolle situaties confronteert. Dit zorgt ervoor dat je tijdens het echte werk risico’s sneller herkent.’ Het Safety Skills Center – opgezet door Sabic in samenwerking met Symbiosis er meer begrip voor elkaar, bouw je een relatie op en verlaag je de drempel voor het voeren van een dialoog en het geven van feedback.’
– is een grote loods waar medewerkers voortdurend worden getraind om beter samen te werken, en ook veiliger én efficiënter werken. ‘In de diverse compartimenten van de loods trainen we onder meer de Life-Saving Rules. Dit zijn vastgestelde normen om veilig te werken. Het is belangrijk dat je visueel uitlegt of hands on laat ervaren waarom deze grondregels er zijn en wat de gevolgen kunnen zijn als je je er niet aan houdt. Daarnaast is samenwerking tussen contractors en vaste werknemers van verschillende niveaus heel belangrijk. Evenals het zien dat het werk van de één risico’s kan opleveren voor een ander. Door medewerkers in een team te laten samenwerken, ontstaat
Nat pak
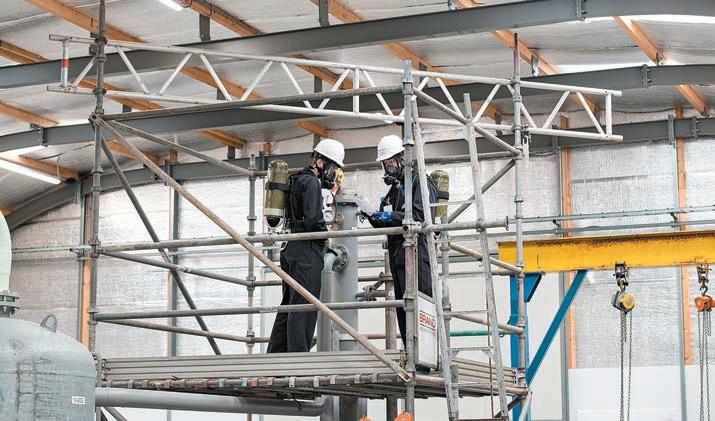
Destijds was de aanleiding van het Safety Skills Center de voorbereiding op een turnaround. Beers: ‘Nu leggen we de focus veel breder. Jonge of net aangestelde werknemers kunnen niet alle handelingen in een draaiende fabriek oefenen, dus simuleren we fabriekssituaties in de loods. Ze krijgen risico’s voor hun kiezen waar ze in de fabriek zelf tijdens normale bedrijfsvoering mogelijk ook mee te maken krijgen. We bouwen daarbij ook booby traps in. Op het eerste gezicht lijkt alles ogenschijnlijk in orde, maar wat zijn mogelijk verborgen risico’s? Het is immers belangrijk dat ze leren om kritisch verder te kijken. Risicoherkenning wordt daarom actief geoefend.’ Voeren ze een opdracht niet goed uit, dan krijgen ze een nat pak. ‘Op deze manier gaat het ook beklijven. Ze voelen er een emotie bij en ervaren dat het niet goed was. Ze hebben misschien een nat pak, maar we vertellen hen erbij dat het in realiteit mogelijk een stof uit de fabriek had kunnen zijn.’
Escape room
Inmiddels bestaat er ook een digitale variant van het Safety Skills Center. ‘
Tijdens de coronapandemie hebben we uit voorzorg met kleinere groepen gewerkt en de afstandsregels in acht genomen’, vertelt Beers. ‘Daarnaast hebben we een digitale 3D escape room gemaakt waarbij het Safety Skills Center is omgetoverd in een LoTo-box (logout-tag-out box, red.). Een team moet een set van acht sleutels verdienen door risico’s te ontdekken en vragen te beantwoorden.’ Zo moeten ze bijvoorbeeld een filmpje bekijken van een operator die op een steiger aan het sleutelen is en regelmatig over zijn hoofd wrijft, zucht, zweet en moppert omdat het sleutelen niet lekker gaat. ‘De vraag is of zij deze man moeten aanspreken om zijn werkzaamheden te stoppen of niet. Aan de hand van het filmpje in combinatie met de bijkomende uitleg moeten de werknemers herkennen dat er sprake is van hittestress, wat gevaarlijk kan zijn.’ Het team dat in de digitale 3D escape room zit, kan met elkaar overleggen wat de beste oplossing is. Wanneer ze vragen juist beantwoorden, ontvangen ze codes die ze nodig hebben om de sleutels te kunnen ontvangen. ‘De escape room heeft ertoe geleid dat we ondanks corona toch heel interactief bepaalde risico’s en situaties onder de aandacht konden brengen en gedrag konden oefenen om het veiligheidsbewustzijn nog verder te verbeteren.’

Op 12, 13 en 14 april 2022 organiseert Easyfairs de beurzen Maintenance en Worksafe in Evenementenhal Gorinchem. De vakbeurzen voor industrieel onderhoud en asset management, en veilig & gezond werken vullen elkaar perfect aan. Met welke innovaties kunnen we assets slimmer en efficiënter maken, incidenten voorkomen en medewerkers motiveren door draagvlak te creëren op de werkvloer? En hoe zetten we die in?
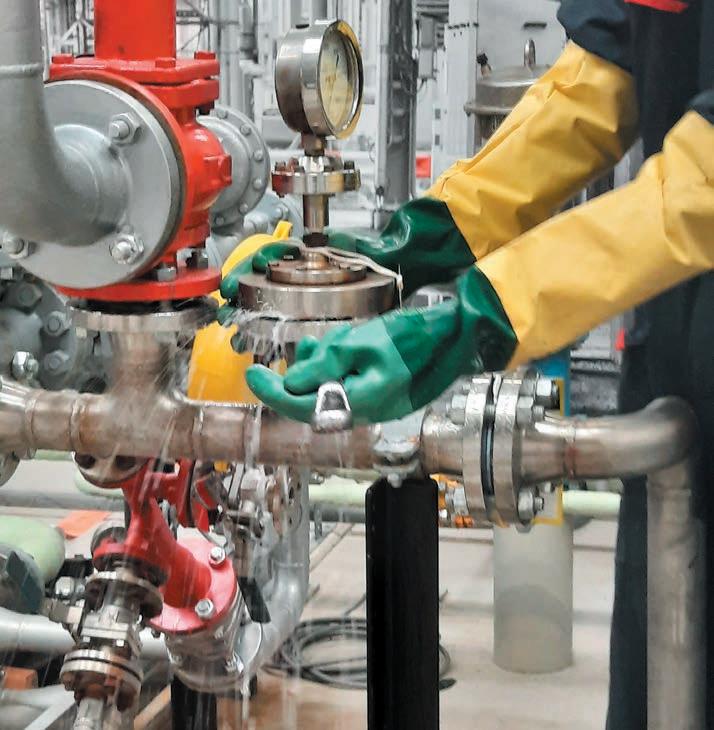
Alles is er op gericht te voorkomen dat in de fabriek fouten worden gemaakt.
Inspiratiebron
Het Safety Skills Center en de escape room zijn slechts deelaspecten naast veel meer veiligheidsprogramma’s. Beers: ‘We merken dat ze verrijkend zijn en andere bedrijven en kennisinstellingen inspireren, die ook met deze benadering aan de slag willen. Alles is er op gericht te voorkomen dat in de fabriek fouten worden gemaakt. Zo kunnen we veiliger werken.’ Toch is blijvend aandacht nodig. ‘Het is belangrijk om de scenario’s en opdrachten regelmatig aan te passen zodat het programma actueel en boeiend blijft. Zo is er onlangs een kleine leiding in de proefinstallatie geplaatst waar nog reststof in kan zitten. Wie niet goed naar de technische tekening kijkt, zal het risico al snel over het hoofd zien, ook al is men zich er inmiddels van bewust dat er booby traps zijn ingebouwd. Belangrijk is daarnaast dat je op verschillende leerniveaus verschillende uitdagingen biedt zodat elke contractor of operator, ongeacht zijn niveau, aandacht blijft houden voor veiligheidsrisico’s.’
Social Learning
De komende tijd zullen er aanvullende fabriekssituaties worden nagebootst. ‘We willen nog meer inzetten op social learning. Een ervaren operator en een jonge operators kunnen bijvoorbeeld in een rustige periode samen naar de praktijkruimte om te oefenen. Dat willen we dit jaar verder vormgeven naast de voorbereidingen voor de volgende turnaround die in 2023 op de planning staat. Het Safety Skills Center laat in elk geval zien dat het leren niet alleen binnen de afdeling opleidingen centraal staat, maar iets is van ons allemaal.’
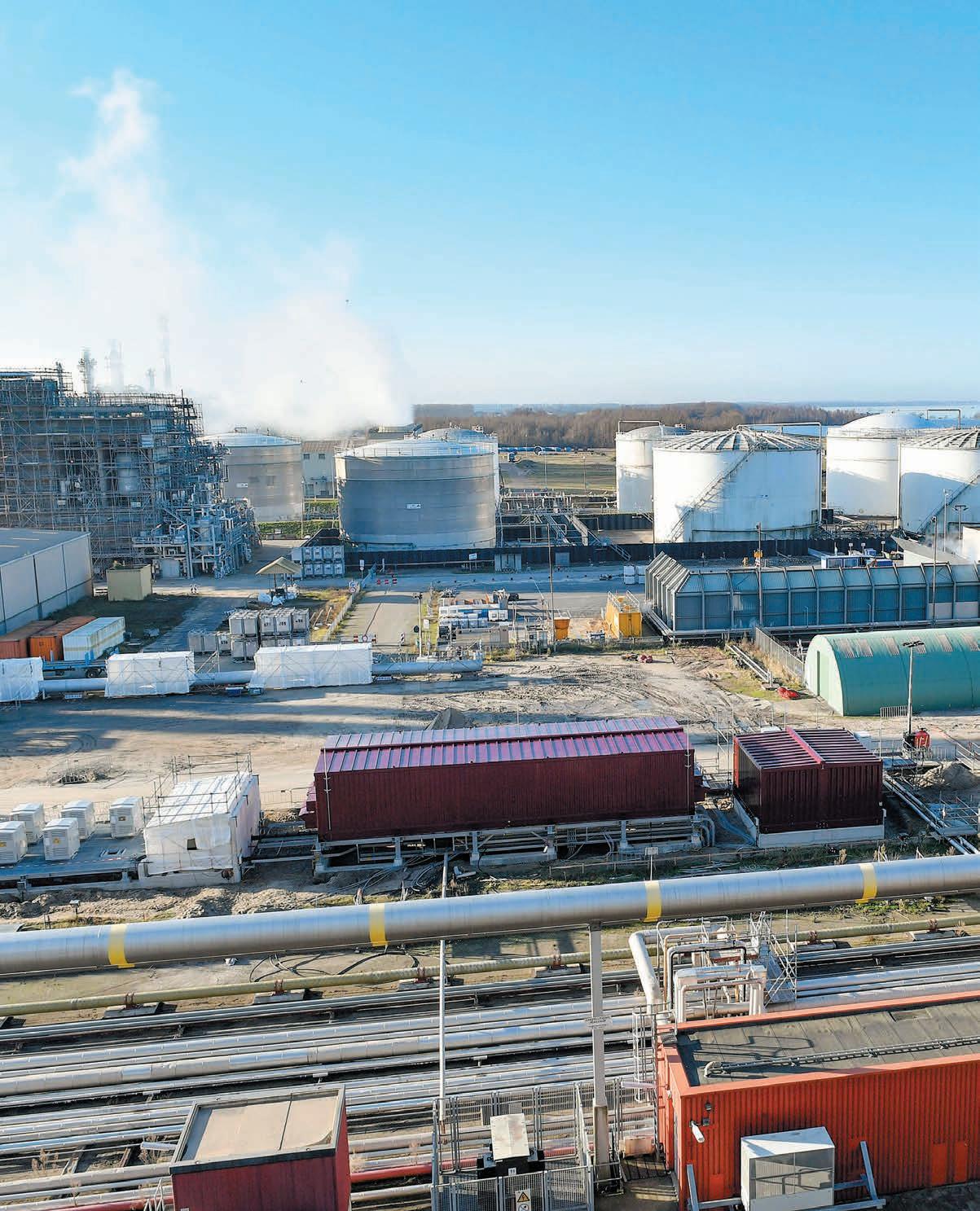

Shell Moerdijk bouwt in het tweede kwartaal van dit jaar een speciale
ringkraan op voor project Skyline. Met dit project vervangt het bedrijf de zestien oudste fornuizen van de kraakinstallatie door acht nieuwe. De ringkraan is nodig om de oude fornuizen veilig uít de fabriek te hijsen en de nieuwe fornuizen veilig ín te hijsen. Samen met Mammoet is Shell al sinds 2017 bezig met het uitwerken van diverse transport- en hijsstudies voor het Skyline project. De ringkraan wordt een van de grootste kranen ter wereld met een hijscapaciteit van 2.000 ton en een contragewicht van 1.600 ton. Hij wordt meer dan honderd meter hoog. De hoofdmast wordt bijna zeventig meter en de kraanarm ruim 45 meter. De componenten van de kraan passen straks in containers, zodat ze gemakkelijk over de gehele wereld te verschepen zijn zonder dat hiervoor speciaal transport nodig is. Daarvoor zijn overigens meer dan honderd containers nodig. Voor de opbouw van de imposante kraan rekent Mammoet vier weken. Een rupskraan gaat deze klus klaren, en deze rupskraan wordt op zijn beurt weer opgebouwd door een grote mobiele kraan. De fundatie voor de ringkraan is inmiddels klaar. Daarvoor waren 72 stuks boorpalen, 60 ton bewapening en 435 kubieke meter beton nodig. De eerste paal voor project Skyline werd in augustus vorig jaar de grond in gedraaid. In totaal zijn er zo’n driehonderd palen nodig.