
6 minute read
Storing power from the wind
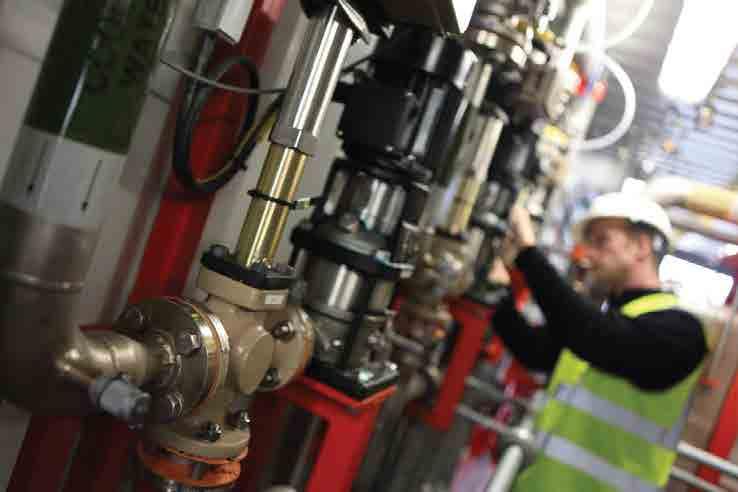

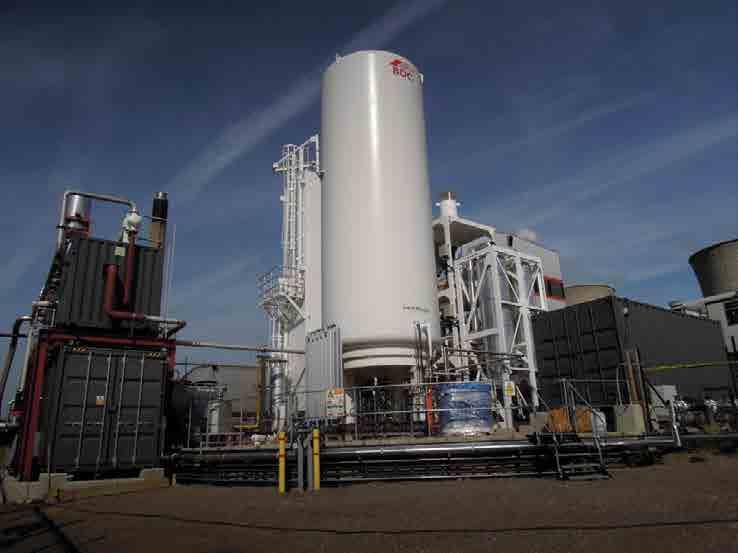
A UK company has developed a novel, large-scale energy storage system.
Over the coming months energy teams from the UK’s Department of Energy and Climate Change through to grid operators and utilities from UK, Europe and further afield are visiting a small site adjoining Scottish & Southern Energy’s biomass power plant on Slough trading estate west of London. They are there to see the world’s first pilot plant of a liquid air energy storage system, owned and operated by Highview Power Storage, a UK energy storage developer. This, they believe, could be the answer to the big problem many power grids are facing – what do we do about wrong-time wind energy?
Highview Power Storage has developed and built a pilot plant of a novel system which uses liquid air as the storage medium. The plant is hosted by Scottish & Southern Energy and connected to the grid. It complies with all the regulations and inspections necessary to be allowed to connect to the grid, just like any other commercial generator.
The system can be scaled to 100MWs/ GWhs of storage, similar to medium scale pumped hydro. But critically liquid air can easily be stored in the same low pressure tanks as used by the LNG industry – it is hundreds of times more energy dense than water (therefore taking up far less space) – and the process does not need large mountains or lakes.
With the dash for green electricity, the deployment of wind farms has outstripped the ability of grids throughout the world to integrate this uncontrollable source of energy. It is now agreed that electricity grids need long duration, large-scale energy storage to support the deployment of renewable but intermittent generation; capturing time-shift wrong time energy.
In the UK last month wind farm operators were paid nearly £3M to switch their wind farms off – and then traditional generators were paid peak prices to turn their high emission gas and oil generators on at periods of high demand. The problem is that, historically, pumped hydro was the solution for large-scale storage; but as demand rapidly increases the geographic constraints of pumped hydro – and its needs for billions of litres of water – are making it unfeasible in many instances.
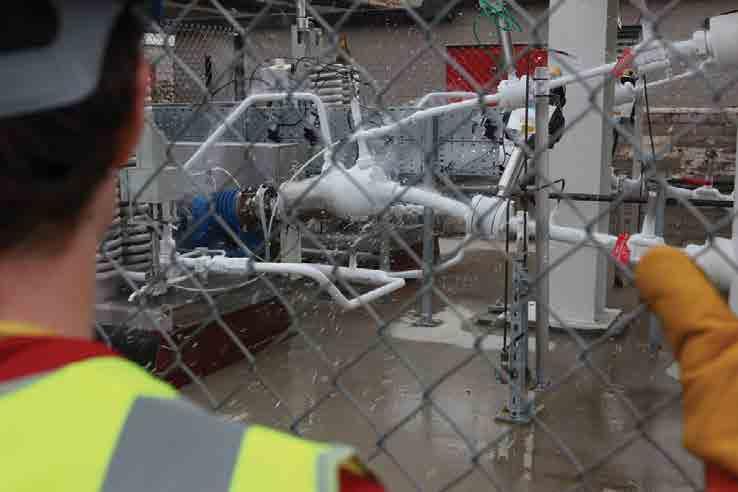
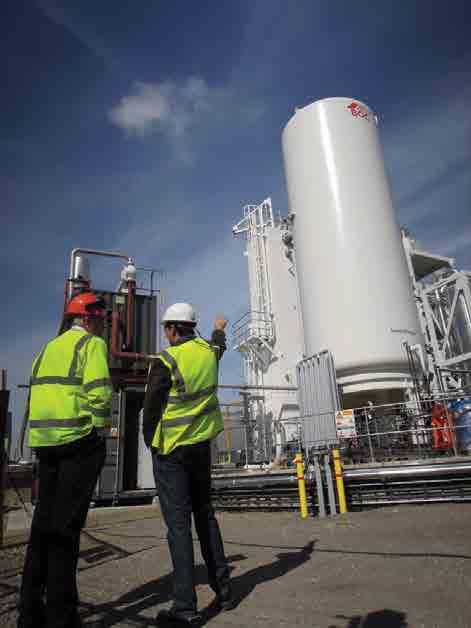
Toby Peters, one of Highview’s founders and developers of the technology (working with a team from the University of Leeds), says, “Whereas many companies were focusing on fast response but relatively small-scale battery technologies, we started out five years ago to develop a system which could deliver affordable, long duration, large-scale energy storage. We identified this as the big gap in the market and today we are now seeing urgent demand for a large-scale solution which can be deployed where pumped hydro is not viable.”
Global problem
In Inner Mongolia this winter, wind farm operators will turn their turbines off every night losing 36GWhs of zero-emission electricity every night as supply exceeds real-time demand. While in the US, reports suggest that approximately 25 TWh of wind energy was curtailed (idled) last year to keep the off-peak grid energy price from frequently going negative. “That,” says Dr David Doty, president of Doty Scientific, reported by Green Tech Media, “is about equal to the energy in 700 million gallons of gasoline just being thrown away. Curtailed wind energy in the US appears likely to exceed 40 TWh in 2011.”
Unlike many new inventions which often then need massive supply chain investment, all the components for large scale plants are from mature supply chains so do not require investment in manufacturing/factories.
Says Peters, “utilities are necessarily conservative and slow to adopt new technology until reliability is rigorously proved over many hours of operation. We wanted to try and remove some of the technology challenge so while our process is novel, all the components are mature and from global suppliers. We do not need to prove that the turbines or compressors can run for 20 years or can be scaled to tens or even hundreds of MWs: they are already in operation.”
With the pilot plant operational, Highview is now looking to move to deployment of a fullscale commercial reference plant with appropriate partners. As Highview CEO Gareth Brett, a veteran of the utility sector, says, “We have a strong technology lead in this massive sector of the storage market, but we do not intend to try to become a manufacturer when we have global supply chains already established for the components populated by major firms with whom we can work.
“This is utility-scale technology. It can be rolled out more quickly and more successfully by – or in partnership with – companies with less constrained access to capital than a small developer and an established international/in-country marketing network. Our role is around the IP and knowledge about how to design and optimise the system for specific market applications.”
Brett has confirmed that the company is having discussions around deploying a first multi-MW plant with potential partners and customers in the UK as well as abroad. n
www.highview-power.com
Cryo Energy System involves four core processes
1. Charge: The system operates by using electrical energy (excess or off-peak) to drive an air liquefier. Similar equipment is widely deployed for the production of bulk liquid LNG, nitrogen, oxygen or argon.
2. Storage: The liquid air is stored in an insulated tank at low pressure, which functions as the energy store. Again, such equipment is widely deployed as bulk liquid LNG, nitrogen, oxygen or argon storage, and millions of tonnes of liquefied gases are commercially stored and transported around the world.
3. Regasification / Power Recovery:
When power is required, liquid air is drawn from the tank and pumped to high pressure. Ambient (or above ambient waste*) heat is applied to the liquid air via heat exchangers resulting in a phase change from liquid air to a high pressure gas which is then used to drive a turbine and generator.
Novelty: Cold Recycling: During the power recovery, very cold gas is exhausted, which is then recycled back into the liquefaction process (stage 1) reducing the energy demands for producing liquid air and thereby increasing the overall round-trip efficiency.
* Added value: Harnessing waste heat (optional).
The introduction of waste heat (including low grade waste heat i.e. sub 100’C) into the power recovery system (stage 3) increases the amount of power which can be extracted. Waste heat is added through heat exchangers rather than direct into the turbine so easily to integrate and manage. Given working fluid is cryogen (-196°C), can use low grade/very low grade waste heat. The systems convert waste heat to power at approx. 40-50% efficiency. i.e. 4 x typical Organic Rankine Cycleprocesses.
The technology is competitive when compared with other commercially used energy storage technologies in terms of capital cost, efficiency, scalability (multi MWs); It produces no harmful emissions.