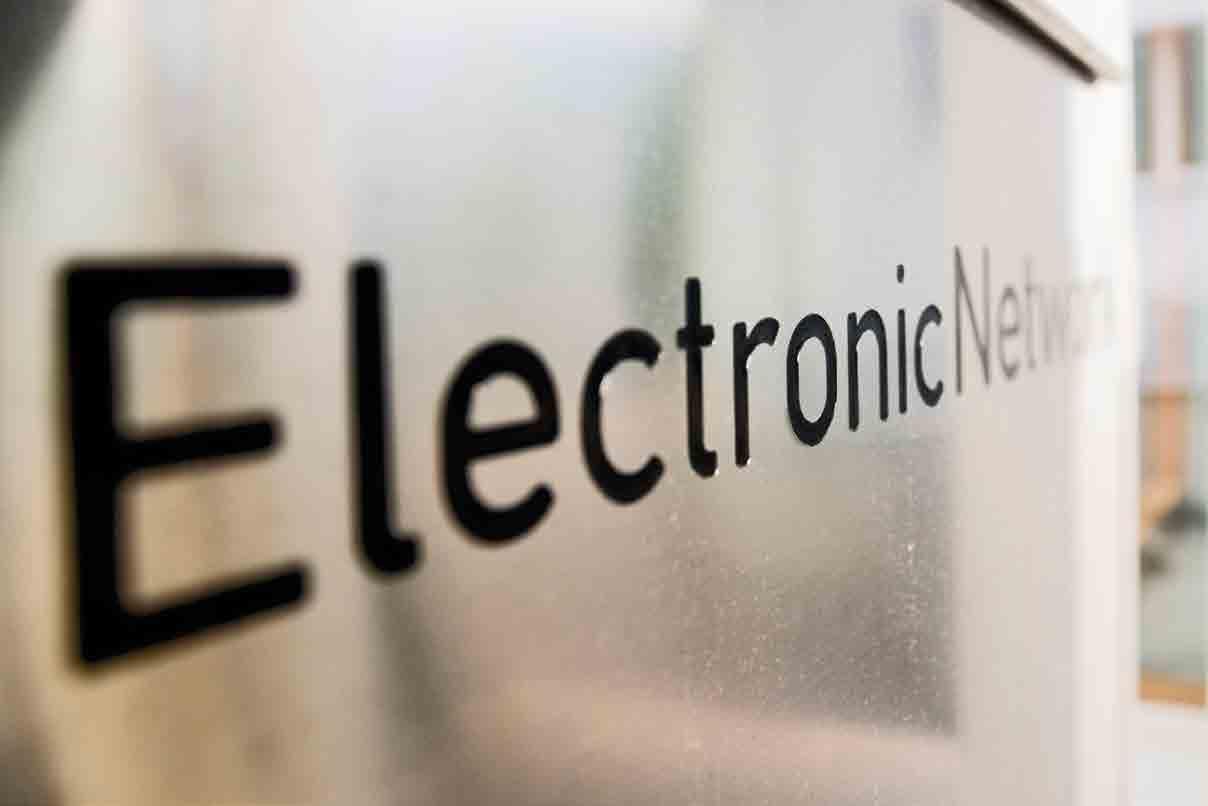
5 minute read
Source of inspiration
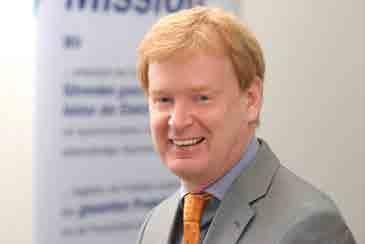
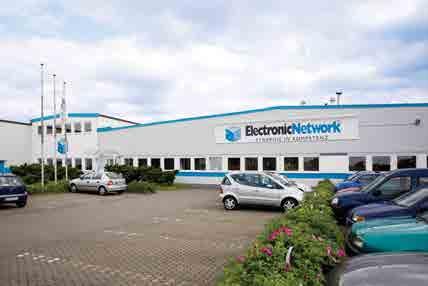
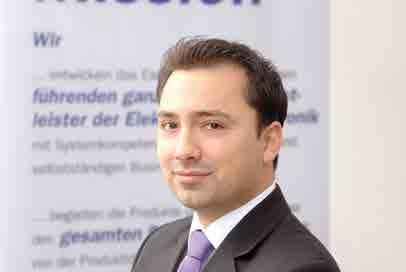
The EN ElectronicNetwork Group is one of Europe’s leading electronic manufacturing service companies. Philip Yorke talked to Klaus Kroesen, the company’s chairman and Fabrizio Tornetta, sales and marketing manager about its broad spectrum of ‘lean’ contract manufacturing services, its innovative approach and about moving into new market segments.
The EN ElectronicNetwork Group is a privately owned company that was founded in Germany in 1999 and quickly established itself as a major player in the European electronic manufacturing services (EMS) industry. The group specialises in fulfilling integrated product manufacturing and implementing new product development services as well as providing logistics concepts on behalf of its customers.
In 2010 the company acquired a manufacturing site in the Czech Republic, which like the other EN sites is providing EM services to multinational companies as well as regional customers. Today the group operates five production sites in Germany and one in the Czech Republic, with advanced plans to build a brand new, dedicated plant in Romania. This is designed to supplement its current volume production and offer greater added value to its customers. Currently ElectronicNetwork AG employs more than 800 people and in 2010 recorded sales of around €150 million.
When it comes to new product development, ElectronicNetwork offers a complete spectrum of services from the creation of the product’s requirement specification to the development of hardware and software. In addition, the company provides layouts tailored to meet the individual approval processes and documentation required. In recent years ElectronicNetwork has built-up significant, in-depth experience in a wide range of core competences. These are based on ARM Cortex A8 processors as well as ARM9-based systems including the creation of embedded software such as Linux.
The company supports its customers in the design process and cross-checks of all product data, which leads to the virtual ‘preproduction’ of any new product. 3D-analysis is also available through the use of CAD tools, which build the electronics into the enclosures before they are manufactured, in order to prevent errors and save both time and money.
Kroesen said, “Our strength lies in our partnerships with our customers and suppliers and we adopt an open company culture
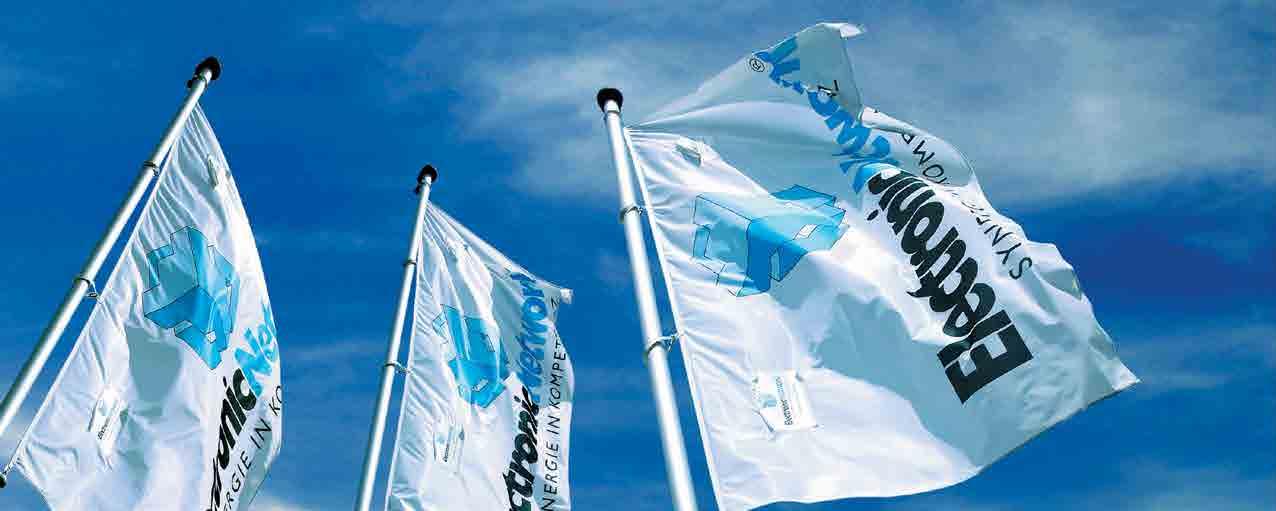
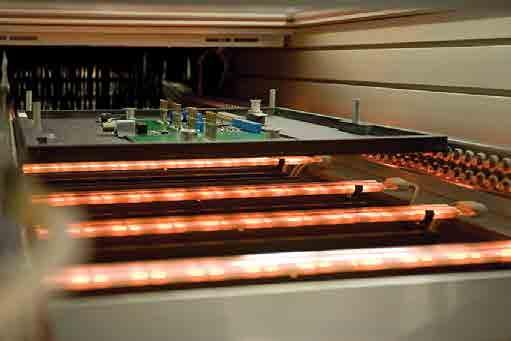
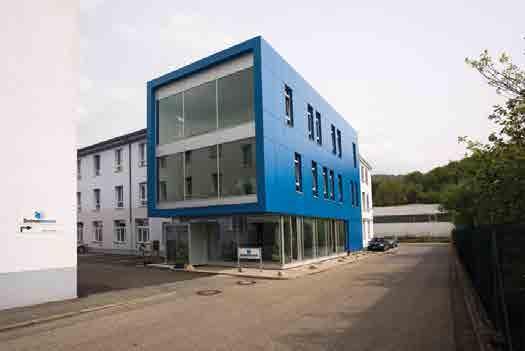
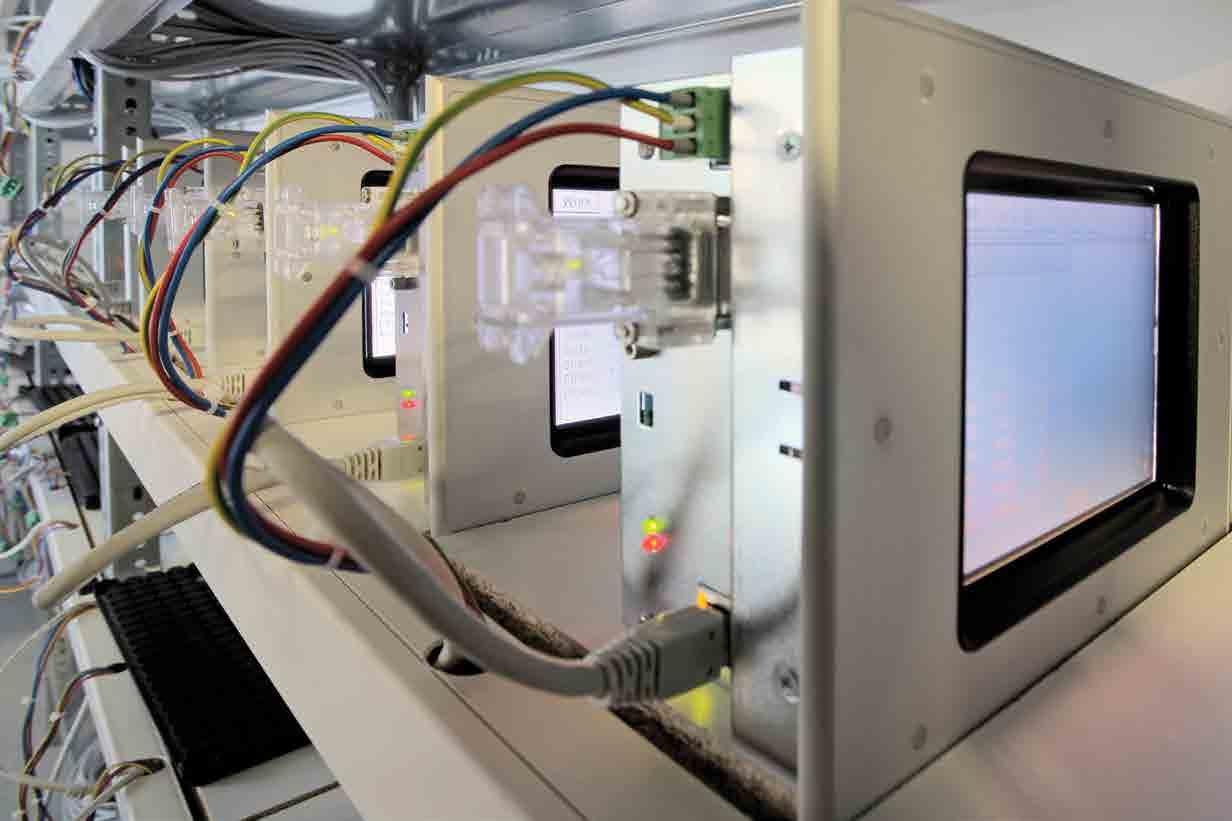

for our mutual advantage. We increase customer benefits through our lean management processes and in-depth expertise, and accompany our customer’s products along the whole product lifecycle from the initial concept to the end of a product’s commercial life. We need to be located as close as possible to our customers, which is why we have invested in a new plant in the Czech Republic. We are manufacturing PCBA boards and systems there as well as complete products including final assemblying.”
Mr Tornetta added, “One of our special competencies is to accompany customers whose products have very long life cycles and use older technology, as happens for example in the railway industry. This is why we are fully certified to ‘IRIS’ – the rail quality assurance standard. We are also very much involved in the automotive industry where big volumes apply and where traceability and strong technical support is very important, and in this field we are a tier-one and tier-two supplier.
We are also very active in the energy and medical equipment sectors, as well as in data processing and telecoms. We like to
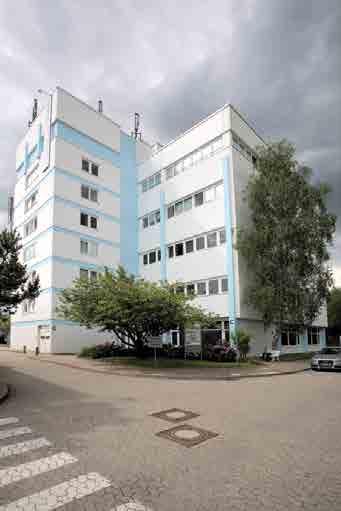

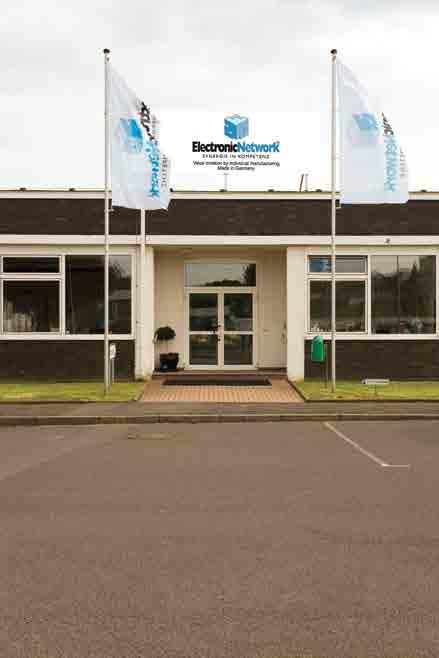
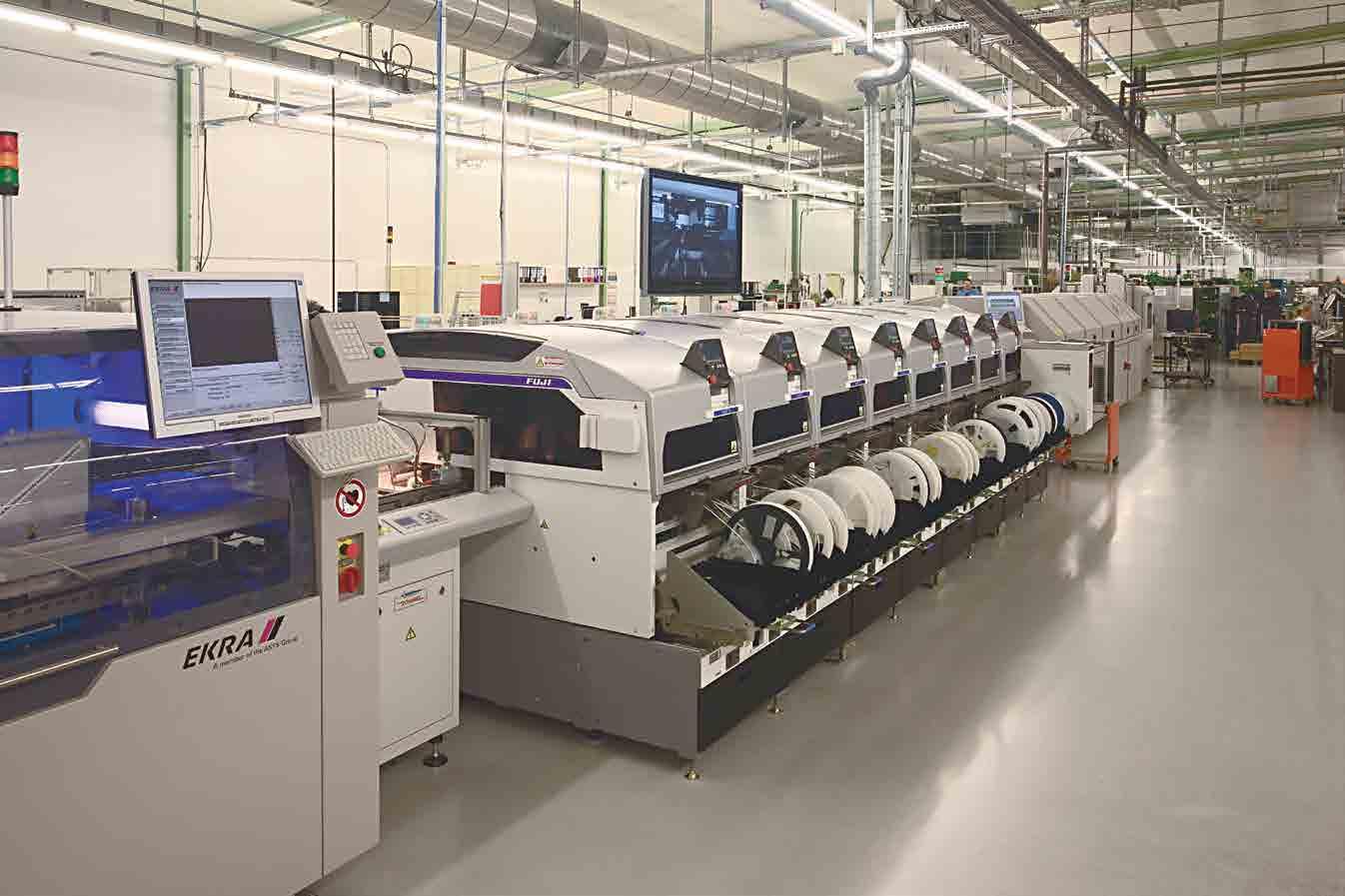
have the possibility of a serious professional relationship that involves us at the early stages of a product’s life cycle, so that we can bring innovative and cost-optimised solutions to the table for the benefit of our customers. Our contribution, as a manufacturer and turn-key systems provider is designed to deliver a faster time to market for our clients’ products in the most costeffective manner.”
Quality and quantity
In order to meet the increasing challenges facing electronics manufacturers and the evolving market conditions, the company operates a comprehensive management system according to ISO 9001, in addition to a fully integrated management system according to ISO 14001. Further certifications obtained at individual locations throughout Europe include ISO/TS 16949 (automotive) and ISO 13485 (medical).
Furthermore, with its network of quality data management and integrated serial number assignment systems, it is possible to guarantee component traceability and the nature of the individual products involved. Kroesen commented, “Recently, EN Electronic Network Hersfeld GmbH successfully passed its re-certification audit for the automotive and medical sectors and this confirms once more the operating efficiency of our company, characterised by our lean management protocols.”
In addition to these important quality standard certifications the company also achieved DIN EN 13980 (ATEX explosion protection directives), as well as the International Railway Industry standard: IRIS, a certification that very few other companies have acquired.
Mr Tornetta added, “Without an integrated and software, supported quality and traceability system, we could for example not fulfil the diverse requirements of the railway or automotive industry. Thanks to the introduction of IRIS for operating companies, the longevity and availability of their railway vehicles has increased and life cycle costs can be evaluated and recognised more clearly.”
It is also worth noting that ElectronicNetwork provides its customers with independent pre-production project teams which are available at all times for consultation and technical support in order to achieve optimal results for its customers. In addition, the strategic volume purchasing of the group ensures that clients benefit from the most competitive prices, even for prototyping new products. The company’s internal test equipment and toolmaking facilities are also designed to improve product flow and to help with the implementation of fully automated or partially automated production lines in an efficient and flexible manner. n
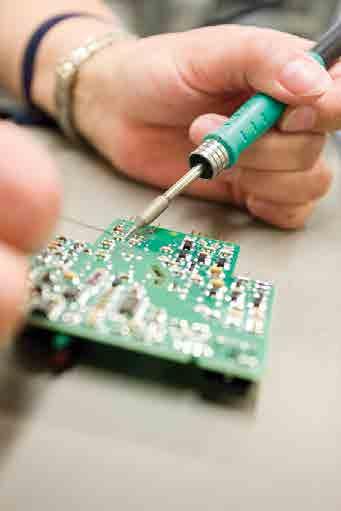