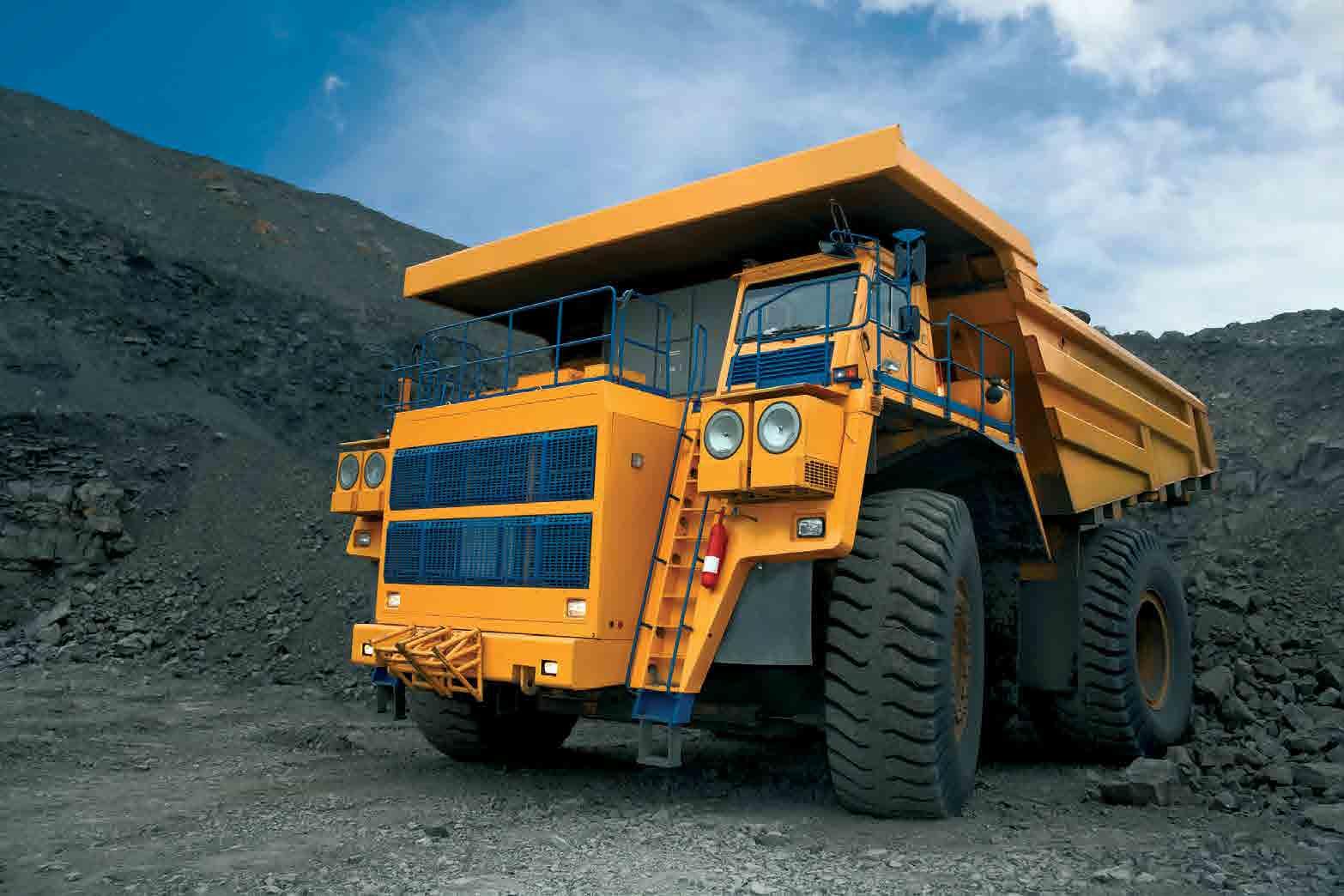
4 minute read
Heavy duty reliability Finnradiator
HEAVY DUTY RELIABILITY
Finnradiator is a market leader in the design and manufacture of radiators for vehicles in the heavy-duty automotive sector. Philip Yorke talked to Juha Partanen, the company’s marketing director about the latest technical advances in radiator technology and the new markets opening up for the company.
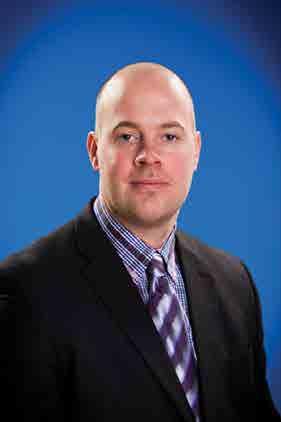
Finnradiator was founded in 1926 in Finland to manufacture radiators for the automobile industry. Over the following years, the company’s focus has been centred on the design and production of various types of radiators for heavy-duty trucks and off-road vehicles.
Finnradiator is the world’s leading expert in the design and production of both copper and aluminium radiators for vehicles devoted to heavy duty environments, such as construction, agriculture and mining, as well as for other off-road heavy-duty applications. The company designs and manufactures customised radiator solutions according to an individual manufacturer’s needs. The radiator assembly can be either of the ‘sandwich’ or ‘combi cooler’ type. Finnradiator is investing heavily in innovative technologies in order to meet the new, challenging EU emission directives. Today the company remains a privately owned family company employing over 300 people.
Setting new standards
Finnradiator has been one of the pioneers in using a new radiator technology known as CuproBraze, which is an amalgamation of copper and brass in the manufacture of radiators designed for heavy duty use. Cores made from copper and brass can remove more heat per unit volumethan any other material system. CuproBraze technology offers exceedingly efficient cooling capacity in a small package. The overall thermal efficiency of a heat exchanger core depends on many factors, such as the thermal conductivity of fins and tubs, the size, shape and thickness of fins and the velocity of air passing through the core. In addition to other major advantages, less fan power is required and so less fan noise is created.
Mr Partanen said, “Our new CuproBraze production lines are the most advanced in the world and whilst most others are using aluminium, we are using copper and brass, which is three times the cost. However, we are involved in the heavy-duty off-road market sectors where price is less of an issue, but where reliability and cooling efficiency are paramount. These are highly specialised areas in which our competitors can’t match our capability or technology. Our in-house R&D department has developed a new copper process technology, which means that instead of separating the brazing process, we can combine it in one step, which means just one operation, thereby saving time, money and further reducing the environmental deficit.
“Our products are at work in some of the world’s largest and most costly vehicles, such as those used in mining, agriculture, construction and military transport. These vehicles must be totally reliable because the cost of down-time is so expensive, and the heat exchanger is a vital component that directly affects many other vital components. Also, when you think of mining vehicles, they are often working in an inaccessible area where repair services may not be available within 1000 kilometres or more.”
Exploiting new markets
Finnradiator’s main markets remain the agricultural sector, with vehicles such as tractors and combine harvesters being the most important. The company’s clients include renowned global brands such as Valtra and Claas. In the mining sector, the company provides products for underground and overground OEM vehicle manufacturers, and in the military sector too, Finnradiator
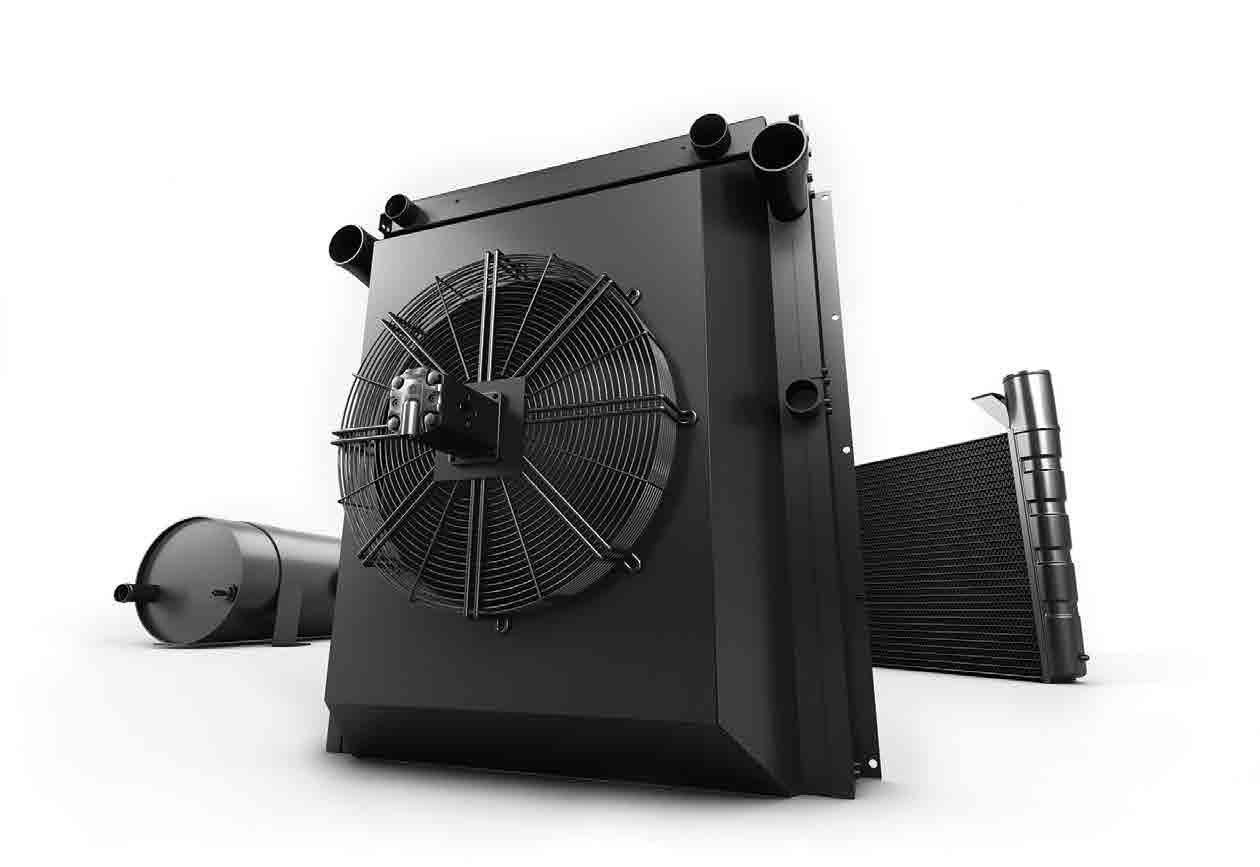

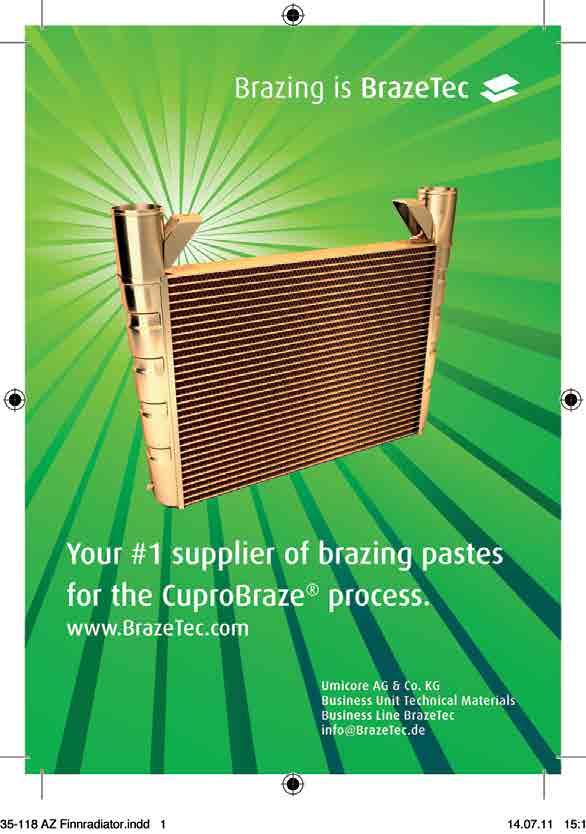
is a major equipment supplier. However, all these sectors, including off-road vehicles, are going to be affected by the very stringent new legislation on emissions from the EU and the USA which come into force in 2014.
This enormous EU and US challenge to OEMs is seen as an opportunity by Finnradiator to expand its sales, as Partenan explains, “The world’s big OEMs are working tirelessly to overcome the severe restrictions on emissions that come into force in a couple of years time. These constraints mean that the gases from the engine must be cleaner when they are emitted than when they entered the engine before combustion. This is an especially difficult challenge for diesel engines which emit more particulate matter than petrol engines. The introduction of new technology into the manufacturing process is all-important and our contribution to this is our highly efficient heat exchanger technology which is superior across the board to traditional heat exchangers and especially at elevated temperature levels.”
Another consideration is that copper and brass are virtually 100 per cent recyclable. Aluminium production on the other hand uses more than twice as much electrical energy compared to copper production (i.e. 54 MWh per tonne of aluminium versus 25 MWh per tonne of copper). Carbon dioxide entering the atmosphere each year could be reduced by as much as one million tonnes by making heat exchangers from copper and brass instead of aluminium. Recently Finnradiator became a member of Cleantech’ Finland, the country’s premier network for the protection of the environment.
Yet another new opportunity for Finnradiator exists in the aftermarket sector where the company has already met with success in Australia, where it has partnered with a local radiator manufacturer involved in the aftermarket sector. In addition, the company has established a sales office in St Petersburg, Russia once more with a local partner to manufacture products for the Russian market. n
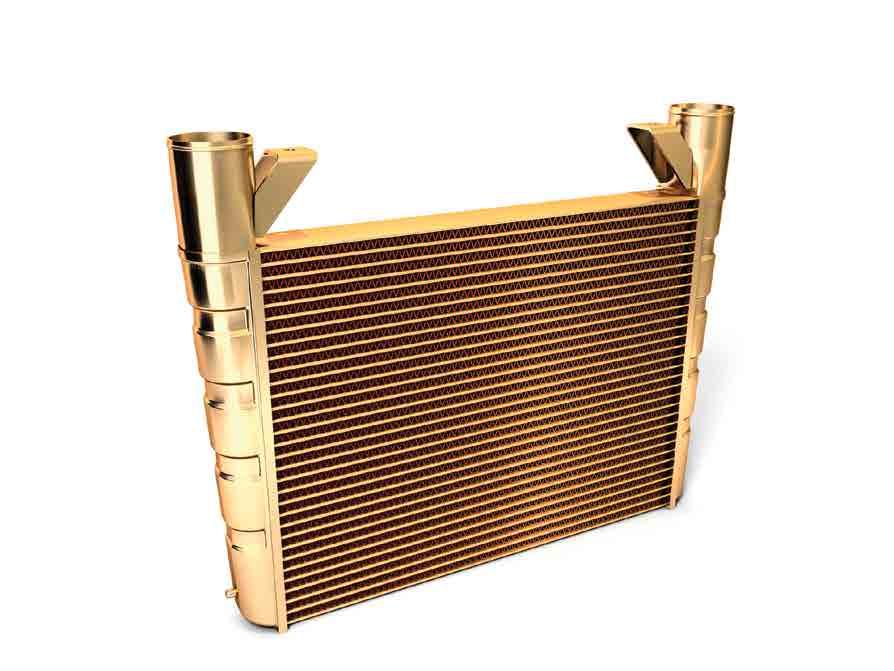