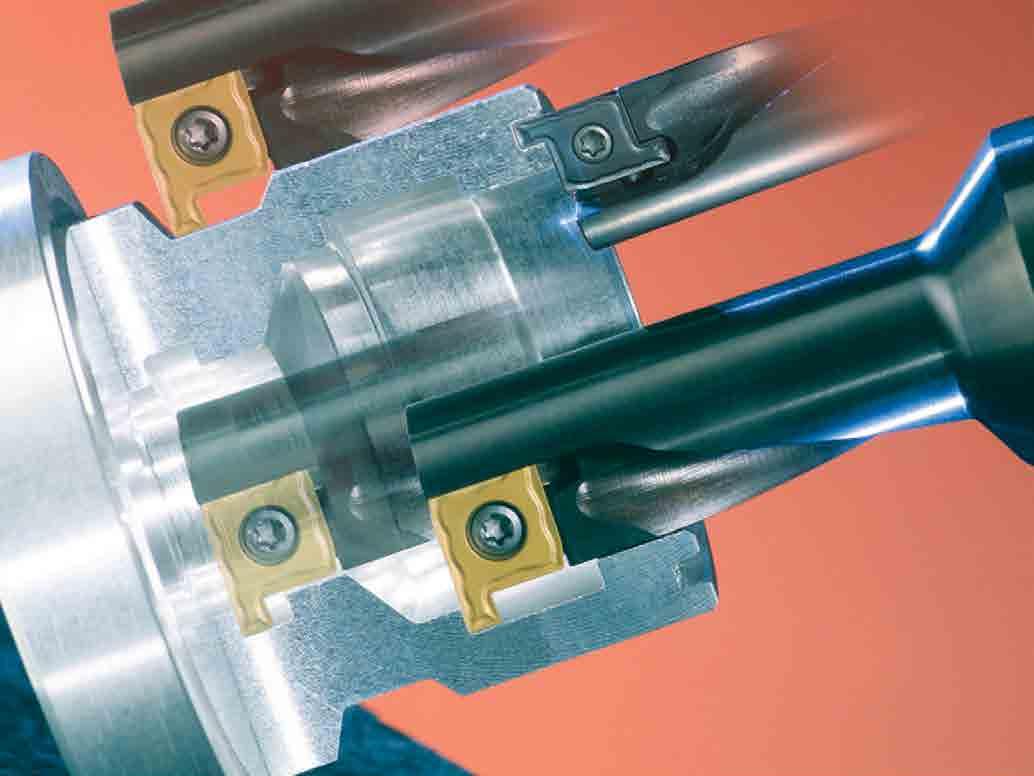
4 minute read
At the cutting edge Ceratizit
AT THE CUTTING EDGE
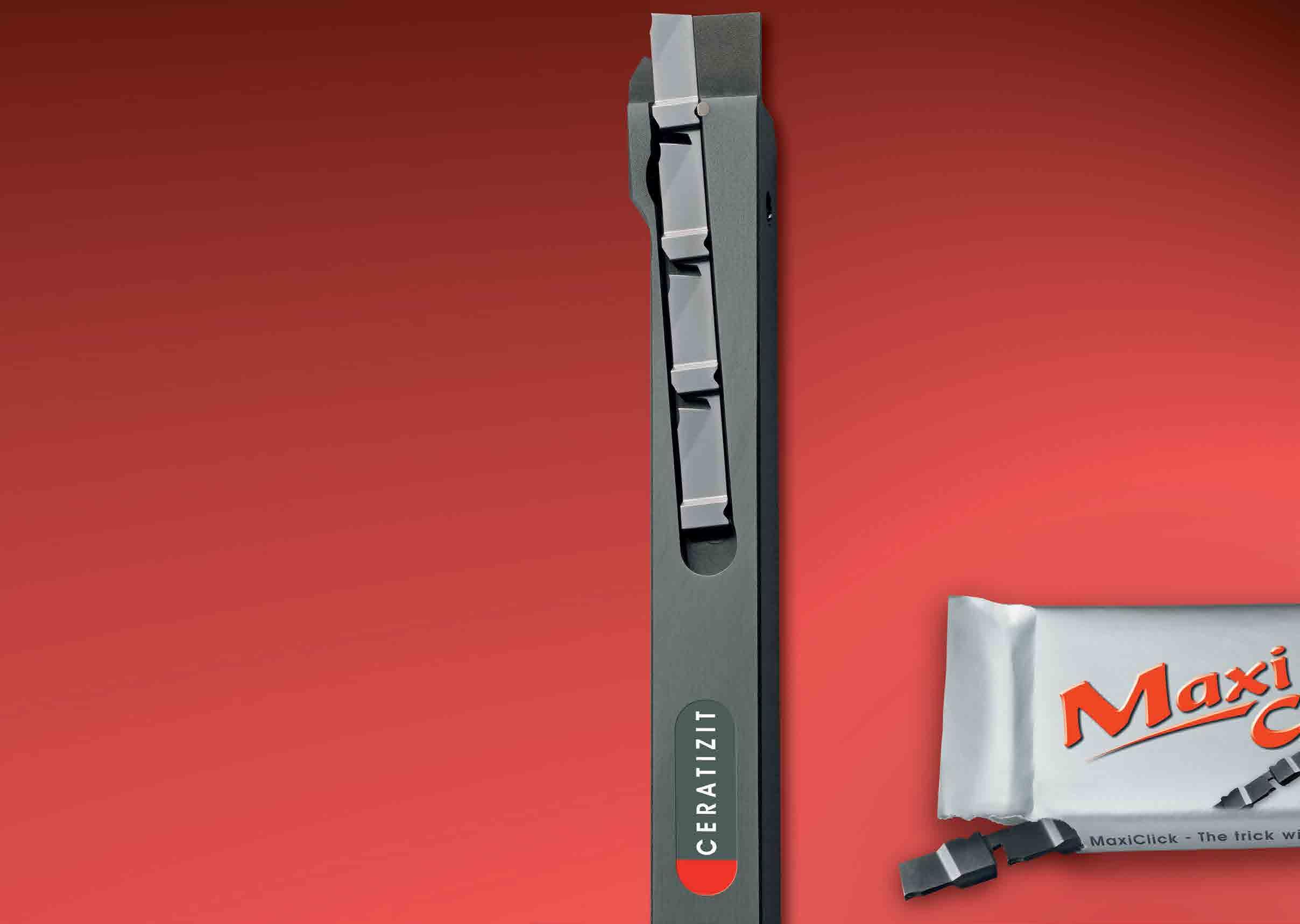
Ceratizit is the world market leader in a number of industry sectors for its unique and innovative hard material products, which include wear parts, cutting tools and carbide rods. Industry Europe looks into its operations to discover the reasons behind its success.
Ceratizit, today a 50 per cent subsidiary of the globally recognised Plansee Group, was established in 2002 as the result of a merger between the two companies Cerametal and Plansee Tizit. As both the companies had common roots and cultural backgrounds, it was felt that a jointventure for the development of carbide as a basis would be mutually beneficial.
The company is based in Mamer, Luxembourg, where its advanced machine park includes a milling centre, lathe centre, horizontal milling unit and vertical milling unit. However, Ceratizit is a global player and also has a large production and sales network stretching across Europe, South America, North America, Asia and North Africa.
Core products
Ceratizit’s impressive range of products is divided into several divisions and sub-divisions, and is designed to meet the needs of today’s state-of-the-art tooling technology. The core product divisions are wear parts, cutting tools, wood machining parts, stone working parts and carbide rods. The wear parts include discs, speciality carbide parts, PCB blanks, knives, nozzles, hobs, cold forming tools and fastening tools.
The cutting tools produced by the company are for applications including drilling, turning, milling, threading and grooving. These are destined for a diverse range of industry sectors, such as automotive, aerospace, rail, tooling, petrochemicals and energy. Products specifically for wood machining include carbide blanks for cutting products such as drill bits or planning blades, and semi-finished products such as blanks for profiling, ground rods and strips.
In addition to this, Ceratizit is one of the world’s leading suppliers of stone working parts, supplying the industry with literally millions of drill tips a year for masonry drills
and hammer drills. Lastly its carbide rod offering covers both standard rods and special rods such as blanks for gun drills of preformed blanks made according to customer specifications.
But it doesn’t end here: Ceratizit also offers a number of additional services to ensure that its clients get the best possible result from its products, and ensure that they choose the right one to meet their specific needs. These services cover online application advice through the company’s E-Techadvisers, tools to calculate exact production parameters as well as WinTool – a modern tooling information system which provides the customer with additional support when they are choosing and applying machine tools.
A new addition
Ceratizit enhanced this range further in July 2011 with the launch of its new carbide hot runner nozzles. These are characterised by their high level of wear resistance and heat

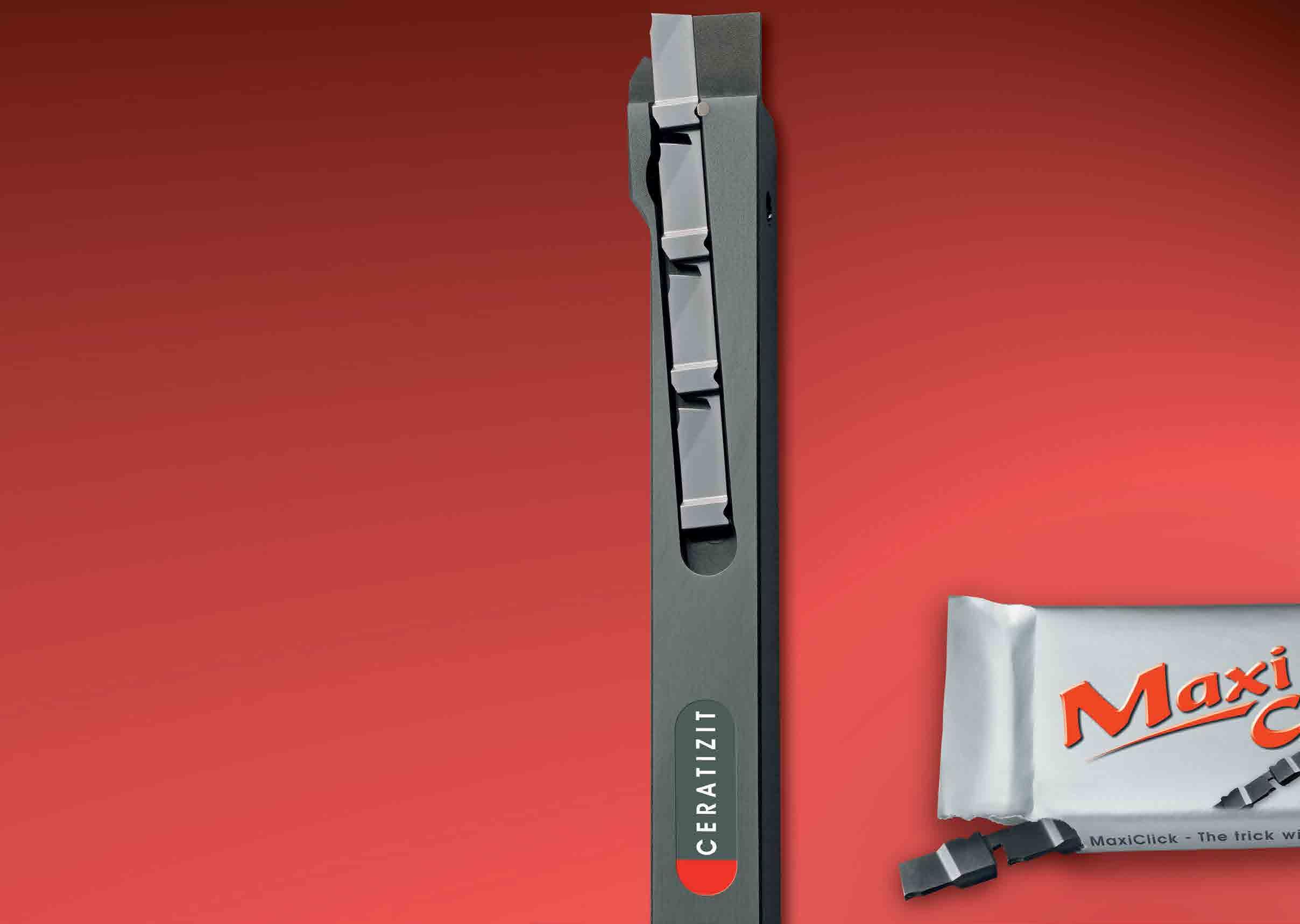
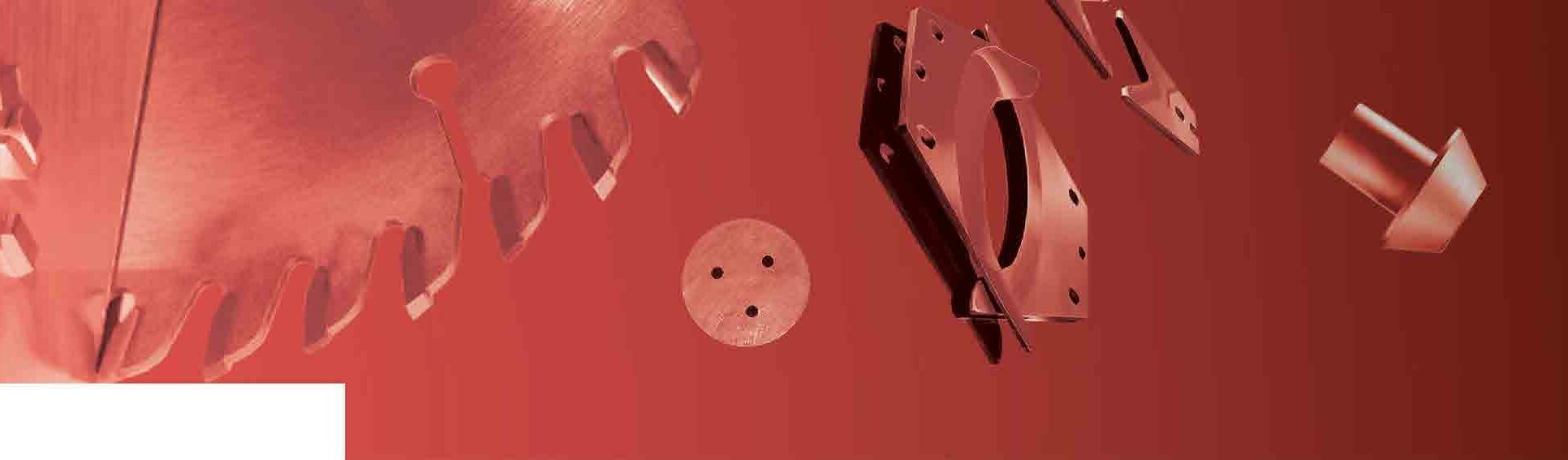
conductivity, and can substantially increase tool life which saves costs for plastics manufacturers. These nozzles can be applied wherever heat conductivity combined with wear resistance, high toughness and resistance to high temperatures are necessary.
Before launching these products on the market, Ceratizit carried out several tests series with various customers. Particularly high results were achieved with glassfibre reinforced plastic materials where wear was patent. For example, tool life was substantially increased which saves costs whilst maintaining consistently high quality. In addition, these new hot runner nozzles are identical in construction to the previous ones available, and can therefore be mounted on existing tooling systems without the user having to invest money in new systems. Equally importantly, Ceratizit can tailor each product to the customers’ requirements, however complicated or precise their needs.
Sonja Stern, product manager for the plastics industry at Ceratizit, commented: “The special thing about Ceratizit is that we do not only offer standard solutions to our customers. We deliver customised tooling solutions, optimised for special requirements. We see ourselves as a
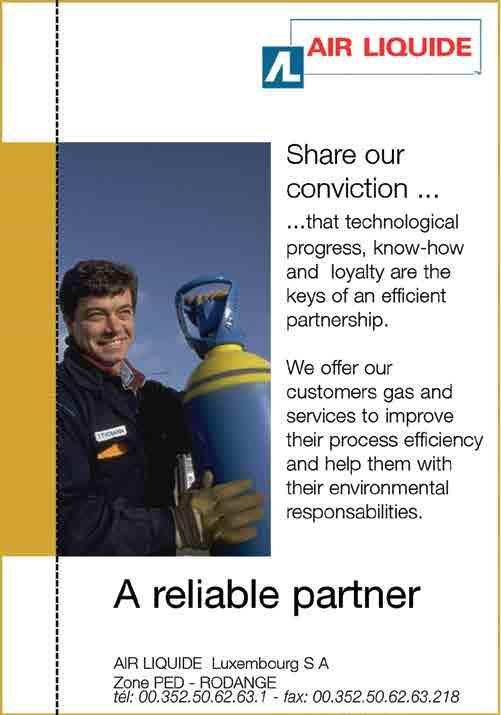
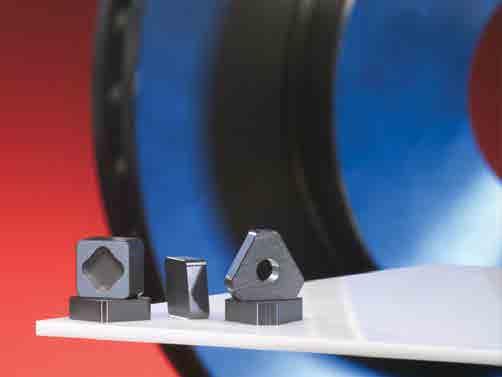
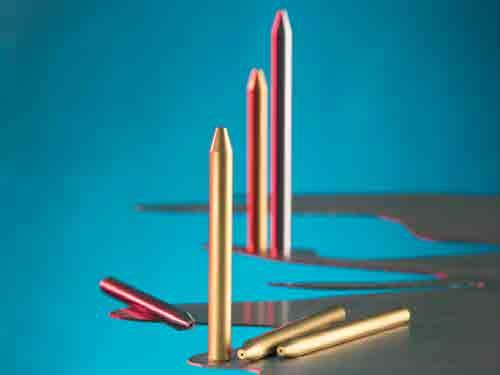
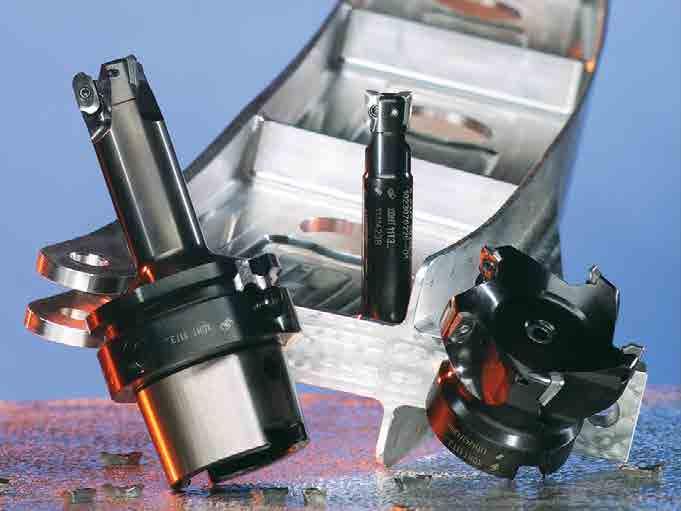
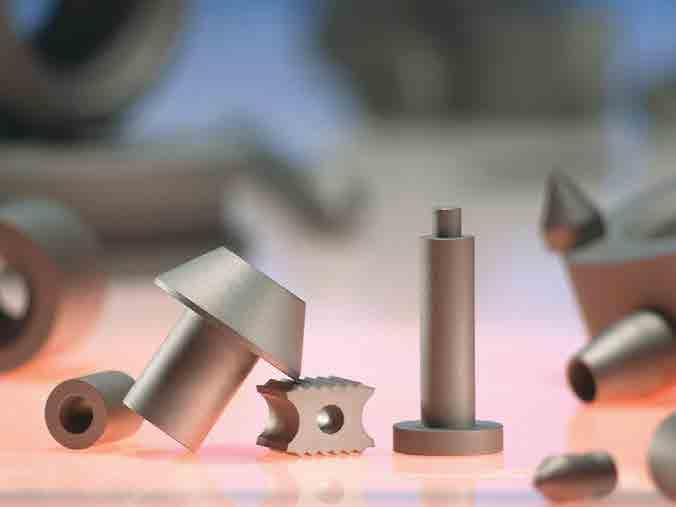
partner to the customer. With our longstanding experience in the field of carbides we create innovative solutions in direct collaboration with the customers. This results in trendsetting carbide product ideas for the plastics industry.”
Consolidation in the USA
In February 2011 Ceratizit announced that it would be centralising its US cutting tool manufacturing operations from Latrobe, Pennsylvania to Warren, Michigan in order, as it said, to “best prepare for the expected economic rebound”.
The forecast for the North American market now looks favourable, so in order to take advantage of this situation and meet the growing demand there Ceratizit will be more than doubling the size of the Warren, Michigan site. Furthermore, it will consolidate its US operations by closing its Latrobe, Pennsylvania location. With this move, it will be consolidating its US operations and realising the synergies of a single location. All the Latrobe facilities – powder operations, hard and soft scrap recycling operations, distribution centre, customer service centre and finance department – will be moved to Warren and all future US growth strategies will now be focused here. n
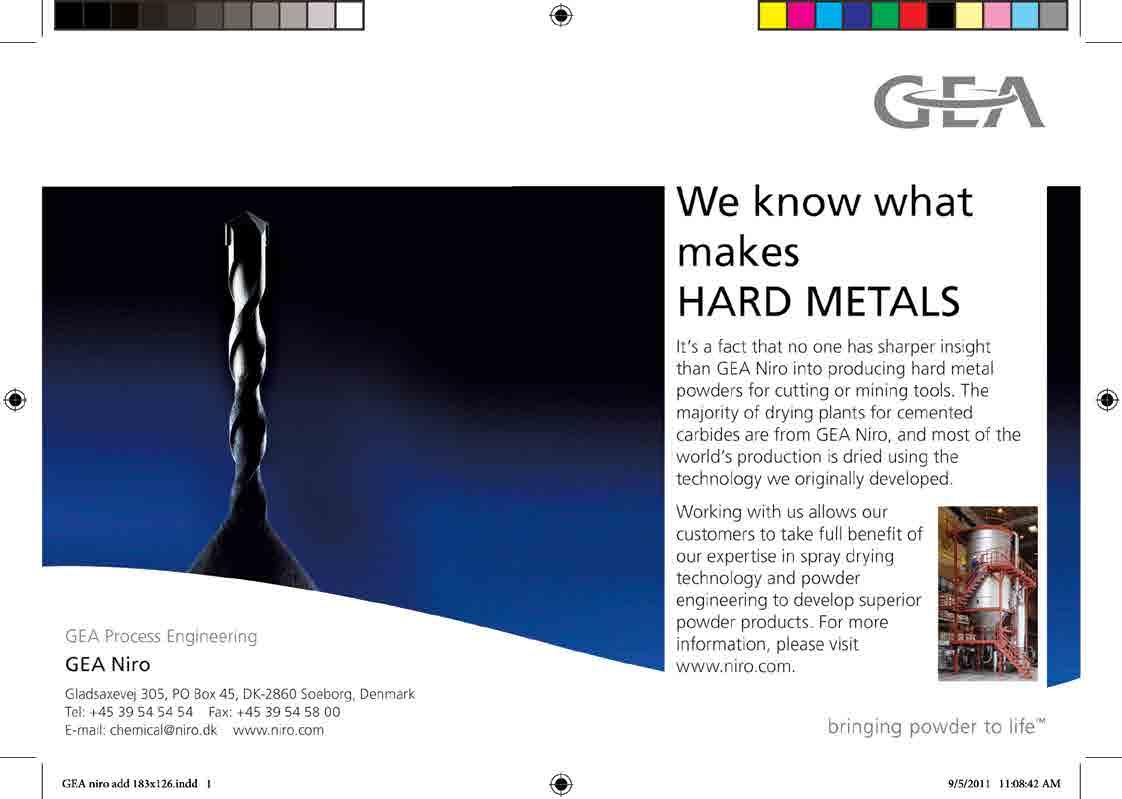