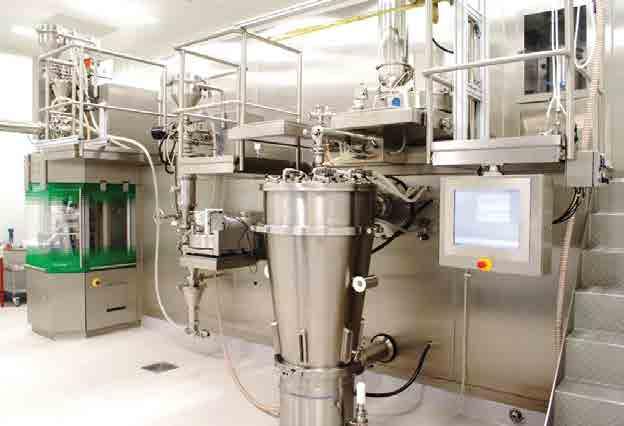
6 minute read
Probing the future GEA Pharma Systems
PROBING THE FUTURE
GEA Pharma Systems is a global leader in the field of pharmaceutical process engineering. Philip Yorke talked to Griet Van Vaerenbergh, GEA Pharma Systems’ marketing manager for Collette products, about the huge potential offered by new global markets and its latest innovative technology.
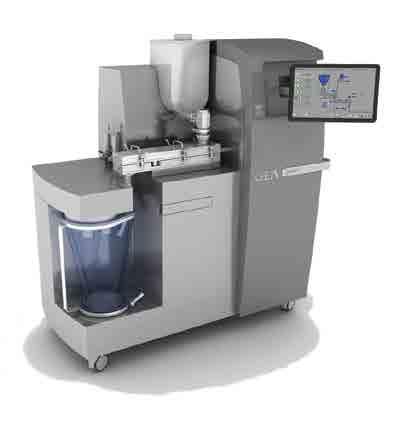
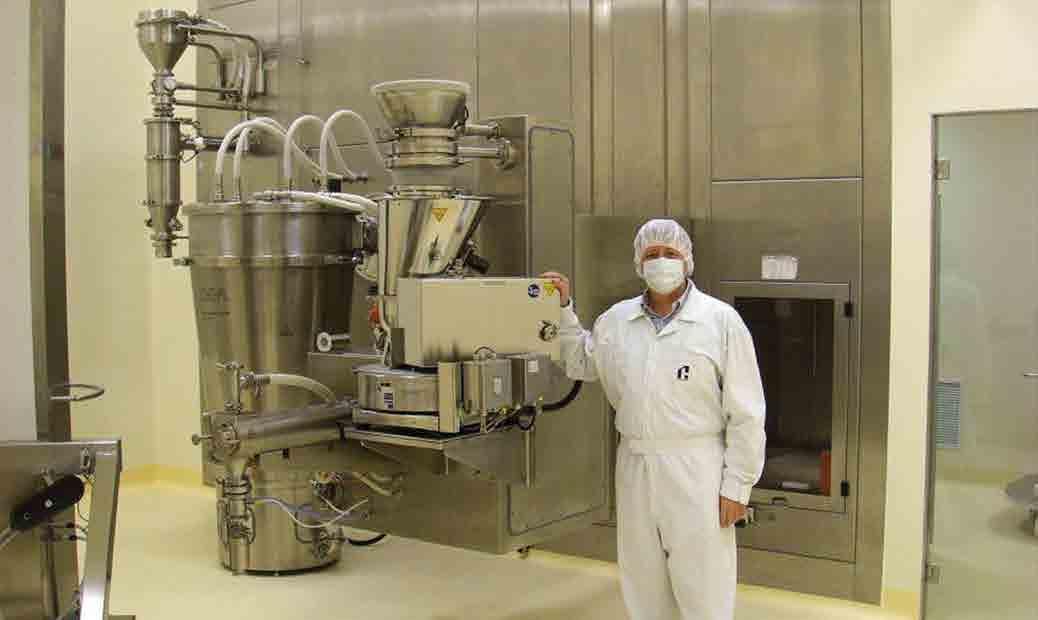
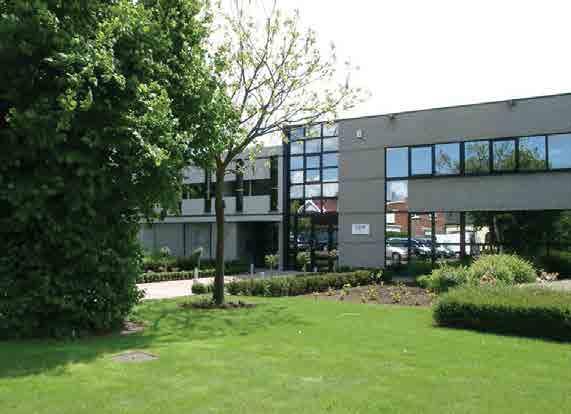
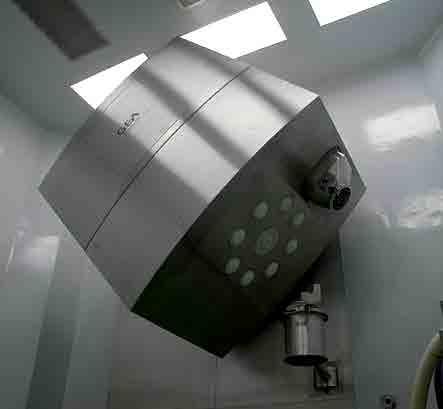
GEA Pharma systems is part of the International GEA Group, which specialises in the provision of systems and process technology for a variety of industries ranging from food and energy, to pharmaceuticals, farm technologies and refrigeration. As an internationally operating technology group, the company focuses on process technology and components for demanding production processes in a variety of end-markets. Currently the group generates 70 per cent of its revenue from the growing food and energy sectors.
The company employs more than 20,000 people worldwide and recorded sales of over €4.4 billion in 2010. In December 2010 the GEA Group was declared the global market and technology leader in its business areas.
One of the group’s fastest-growing business areas is the pharmaceutical, biotechnology and cosmetics sector, placing health and well-being in pole position in the group. Fastmoving demographic developments are turning these markets into major growth sectors. Today in the developed industrial countries, 15 per cent of the population is already over 65 years old, and in the next 20-30 years this proportion will approximately treble. Currently, pharmaceutical manufacturers are investing billions in the improvement of existing products and procedures as well as in new product development. GEA Pharma is able to bring to bear its significant capabilities in this area with growing success.
Fibre optics lighting the way
GEA Pharma’s on going investment in new products has led to some remarkable achievements. The latest of these is its fibre optic probe with fully automated process-interface, known as its Lighthouse Probe™ technology. This globally patented device can be used for real-time monitoring of chemical and pharmaceutical processes and provides in-process window cleaning at any time, as
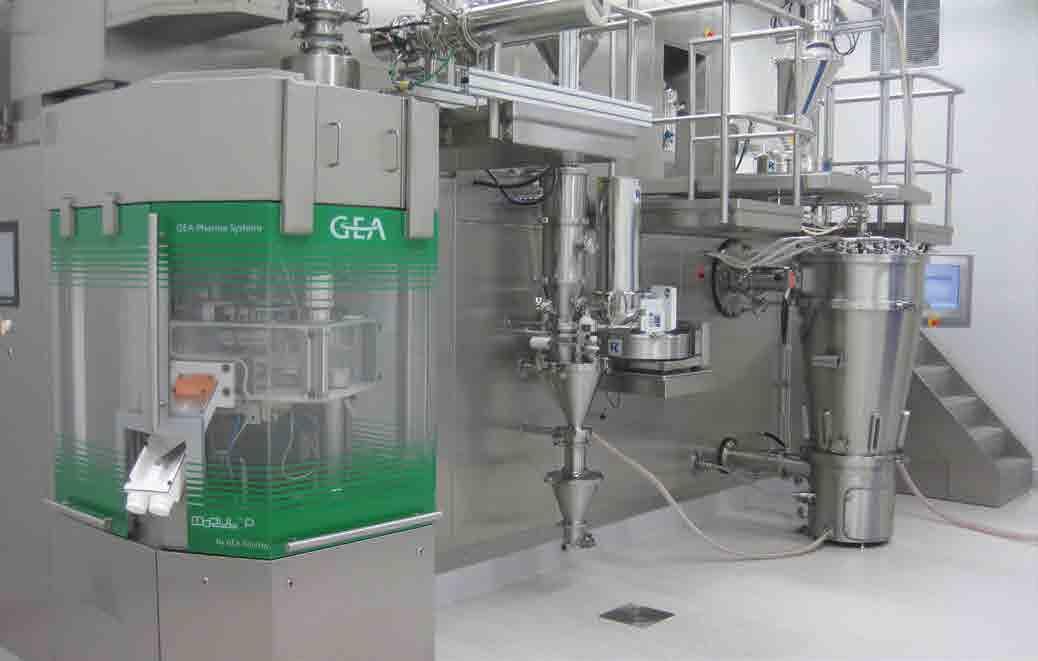
More efficient than ever before
GEA Happel CAIRplus
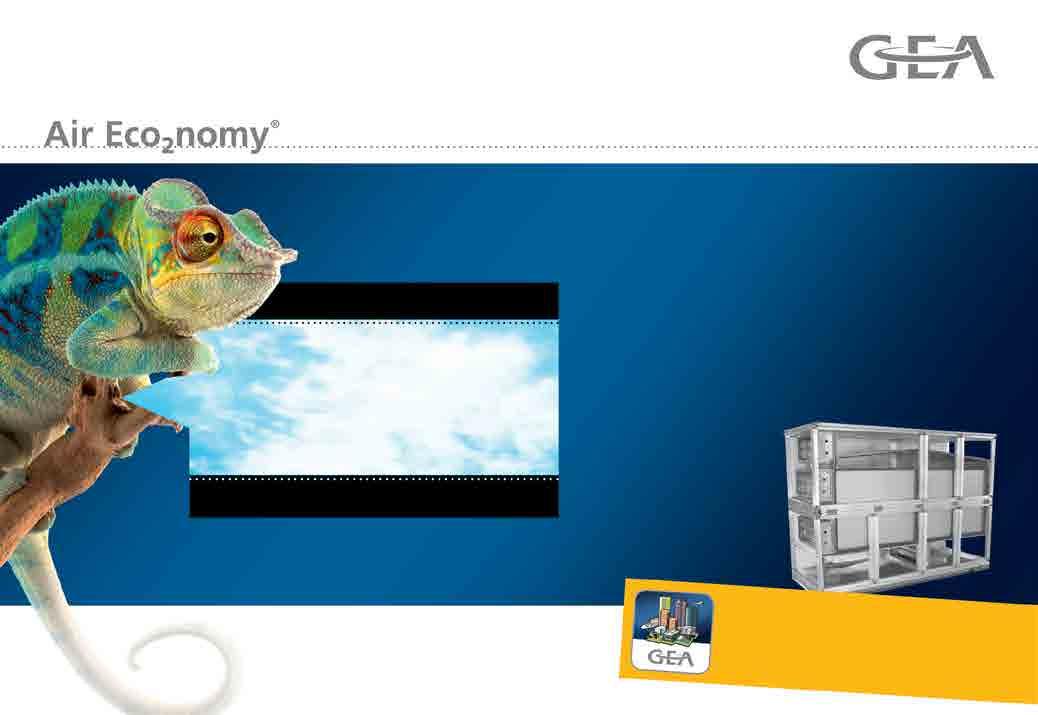
Our most adaptive air handling unit
www.gea-airtreatment.com
A chameleon is the master of adaptation: It makes efficient use of light energy when it is dark, when a chameleon becomes bright - it lowers its body temperature.
GEA Heat Exchangers GEA Air Treatment GmbH
Tel. +49 (0) 23 25/468-00 | info@gea-airtreatment.com Air handling units with adiabatic cooling ECOTWINcool – directly sprinkled, additionally sealed and epoxy coated double plate heat exchanger High cooling capacity through post evaporation on the plate surface Hygienic operation High heat-recovery efficiency up to 0.75 Saves up to 65% cooling energy
Discover the NEW GEA APP for iPad® and iPhone®:GEA Air Eco2nomy City
GEA Happel
GEA Happel Belgium has a long relationship as a distributor for the air handling units with GEA Pharma Systems in Belgium (formerly GEA Courtoy) . It shows how good GEA companies can work together...
In past months GEA Happel developed some customized air handling units with a special electrical heat exchanger and strengthened panels that should resist against high pressure conditions. It is thanks to the capability of our CAIRplus air handling units to develop them completely measured on the needs of GEA Pharma Systems that this order has been executed. More efficient than ever…
well as re-calibration, full CIP (cleaning) of wash housing and seal, and a clear view inside the optic – even under the most difficult conditions.
Mr Van Vaerenbergh said, “Our Lighthouse Probe™ interface system is unique and designed for the implementation of NIR and UV spectro-photometry and fibre optic techniques into production equipment. With its constantly clean observation window capability, manufacturers do not need to disassemble their equipment to maintain optimal monitoring and production efficiency. This device effectively brings to an end the costly errors of the past when random sampling highlighted a production error, often late in the manufacturing process, or even after the batch had been completed. Today we see that pharmaceutical companies are looking towards continuous manufacturing and the online monitoring of processes, which is being driven by continuous European and FDA legislation.”
The integration and automation of fibre optical analyser systems is now possible thanks to GEA’s unique Lighthouse Probe™ technology (LHP). The manual operated, semi, or fully automated LHP is remotely operated to enable its use in sensitive and high-potent processes. Furthermore, it is optimised for a broad spectrum of fibre optic based analytic methods. For full integration with processing equipment, the cleanable LHP system has different options to enable communication with a manufacturer’s existing control systems.
Leading the way in added-value systems
GEA Pharma’s revolutionary Consigma™ continuous high-shear granulation and drying system was launched at the Interpack Pharmaceutical Trade Fair in 2008.
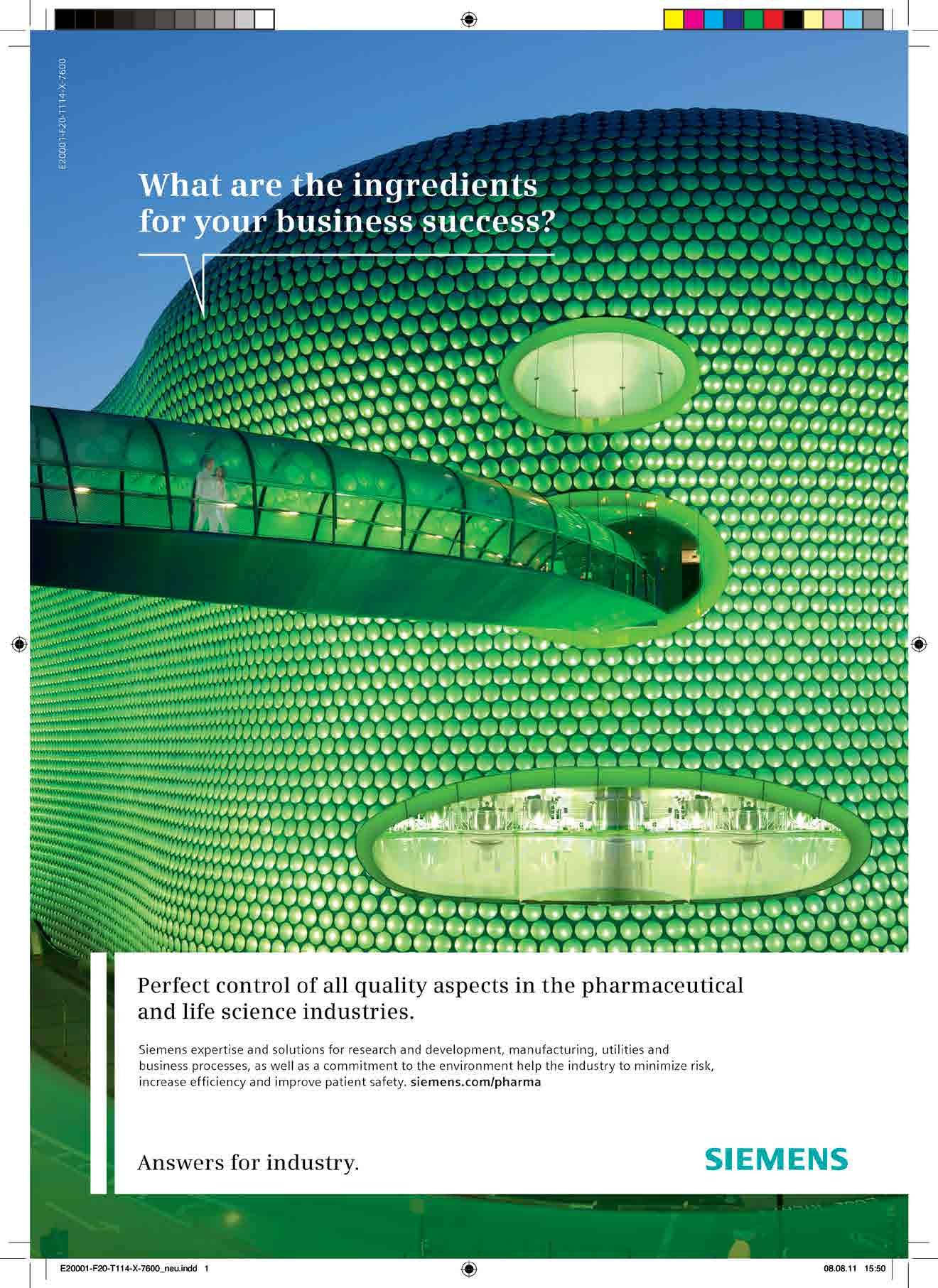
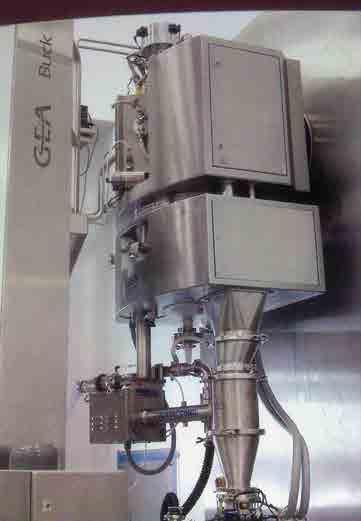
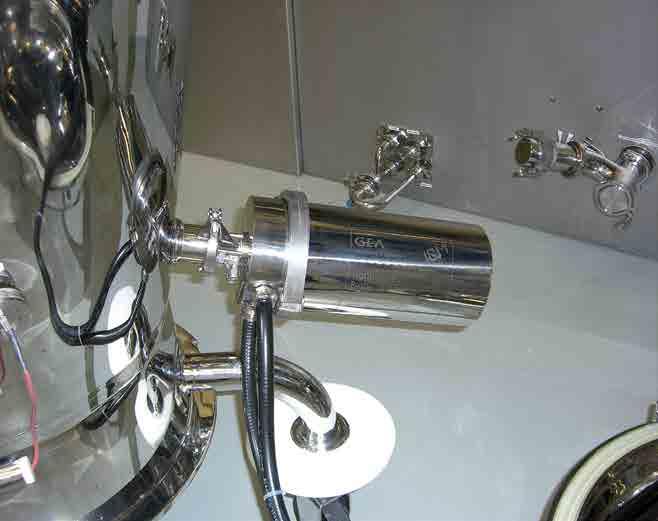
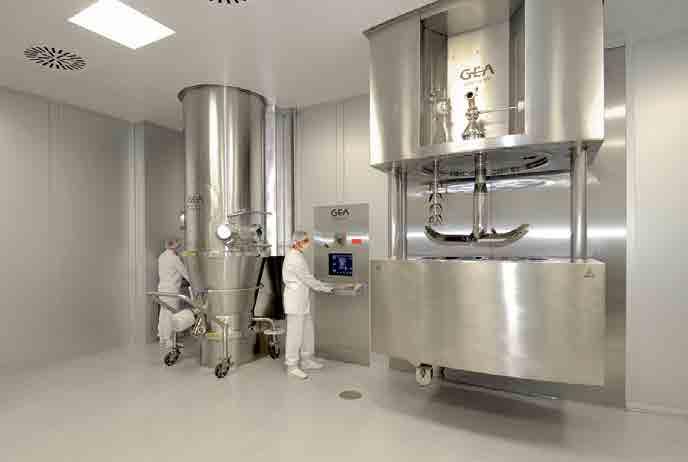

This unique system provides addedvalue benefits through improved quality and maximum flexibility. It has been well received throughout the industry and satisfies the pharmaceutical industry’s demand for continuous production, whilst providing improved quality, flexibility and consistency during manufacturing processes. One Consigma™ device can run 500g in R&D, but can also run clinical trial and launch size, as well as full production batches. This allows manufacturers to reduce development time dramatically and to reduce costs as well as bring new products to market much faster.
Mr Van Vaerenbergh added, “Consigma™ has been a great success for continuous granulation and drying for solid dosage products. It was the first continuous granulation and drying product on the market and sold principally to pharmaceutical companies. Consigma™ offers high-shear granulation combined with segmented fluid bed drying, tableting and coating and is available in a modular construction to fit in every production room.
“The dryer module is based on fluid-bed drying principles and splits the continuous flow of granules in packages of 1.5kg, drying them each in a separate segment of the dryer. In addition, the drying curve of each package is monitored as a fingerprint of the process and controlled to maintain a consistent end- humidity over the whole batch. This drying concept is capable of producing pharmaceutical granules in a continuous manner without the waste involved in start-up and shut-down.
“This year at Interpack, we are showing a new version of this product known as Consigma -1. This is designed specifically to work with very small amounts of product. Process parameters defined on ConsiGma™-1 can transfer one-to-one to the production equipment, again a feature unique to GEA Pharma.”
Advancing single-pot processing
GEA Pharma systems also offer a range of products for single pot processing, which includes models for oncology, hormone and high-containment solid-dosage production, those for organic, solvent-based solid-dosage processing and a model for effervescent production. This is GEA’s UltimaPro™ range which is available in a variety of sizes from 10 to1200 and represents the industry’s benchmark for quality and consistency. GEA Pharma’s single pot processing technology can be tested at the GEA Pharma Systems Process Development Centre in Wommelgem, Belgium. n