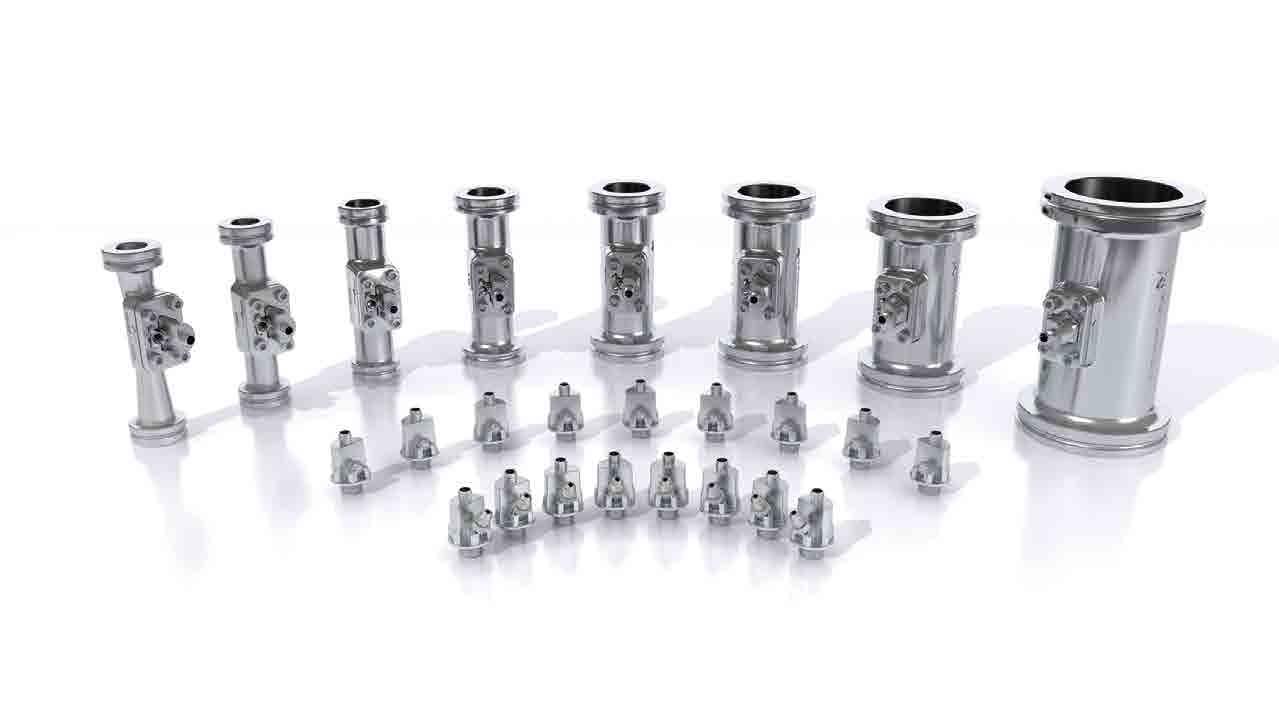
5 minute read
New sensors at the heart of pump efficiency
NEW SENSORS AT THE
HEART OF PUMP EFFICIENCY
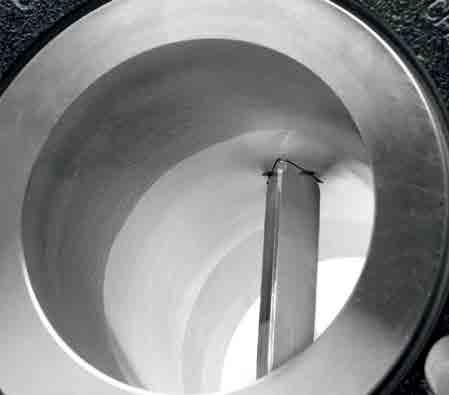

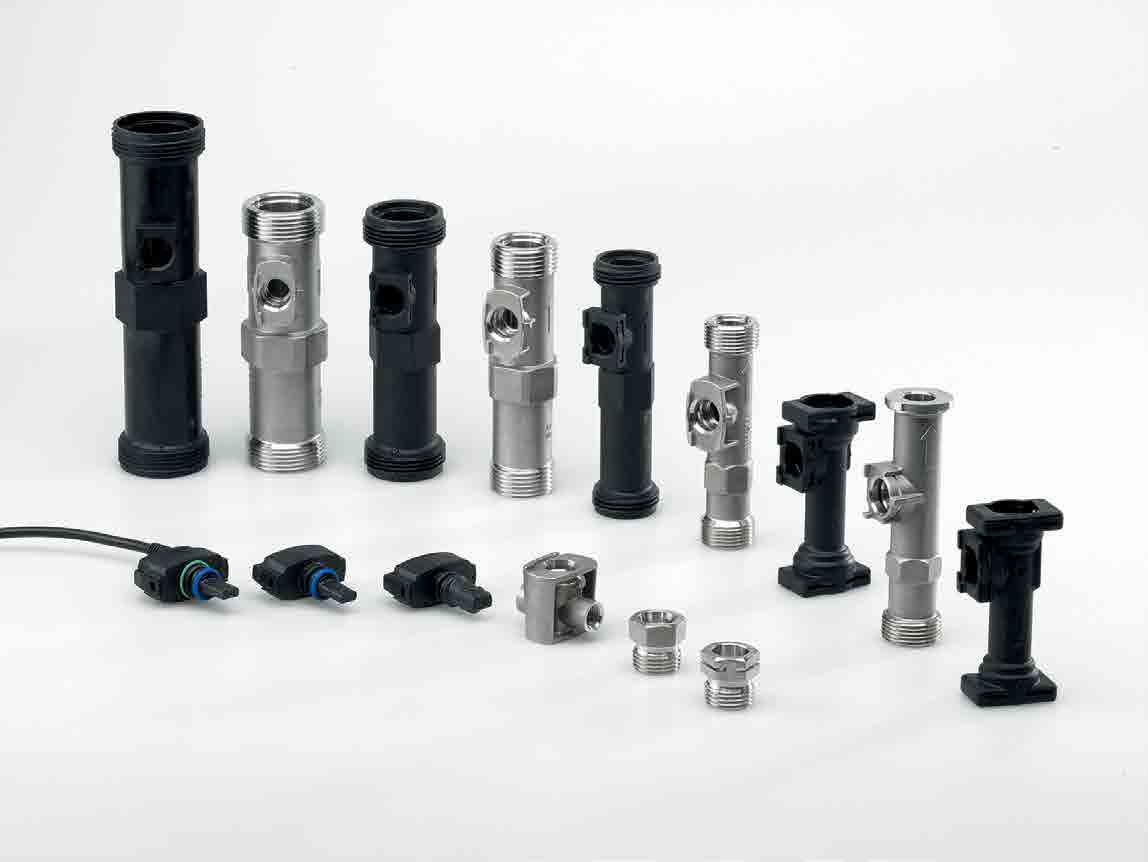
Grundfos is the global leader in circulating pumps and related equipment. Philip Yorke talked to Dr Klaus Kattenhoej, the company’s managing director, about its new sensors division and the strategy behind its formation and innovative range of new pressure sensors.
Grundfos was founded in Denmark in 1945 and is one of the world’s leading manufacturers of circulator pumps for the heating and air conditioning industries, as well as for other key sectors such as water supply, sewage and dosing. Today Grundfos is the world’s largest manufacturer of circulator pumps, with more than a 50 per cent share of the global market. It is inevitable, therefore, that with the ever-increasing demand for greater energy saving and overall efficiency the company has set up a new division to satisfy these significant market challenges. Today the Danish Grundfos Group is present in over 55 countries and has more than 17,500 employees worldwide. In 2011 it recorded sales of more than €2.8 billion. Setting new standards in micro-sensor technology
With one of the biggest dedicated, in-house R&D departments in the industry, Grundfos sensors division has already developed some innovative and ground-breaking new products. The Grundfos Sensor Division produced its first chip for micro-sensors at its state-of-the-art sensor production facilities for semiconductors located at Farum near Copenhagen. This is the very first facility in Denmark to manufacture semiconductors on an industrial scale, and one of the first of its kind in Europe. The new Grundfos semiconductor chip is made from silicon wafers – the favourite material for making sensors being steady-state, which provides the highest quality at the lowest cost – and a proprietary coating originally developed as a Ph.D project at the University of Aarhus before subsequently being patented by Grundfos. This unique coating process makes the chip highly resistant to water as well as other liquids.
Unlike traditional sensors, the Grundfos micro-sensor is so tiny that in principle it can be integrated into even the very smallest pumps and applications on the market. In the short term the production of these micro-chips has been sold internally as well as externally, before being integrated into the bread and butter of the Grundfos business – centrifugal pumps. However, in the longer term the micro-sensors will be made available for many other segments and products, as they are ideal for measur-

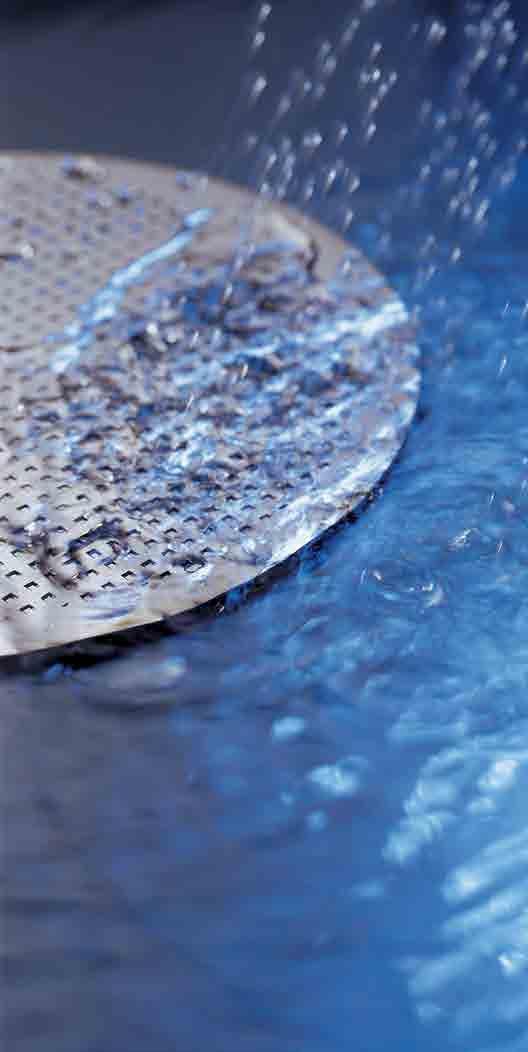
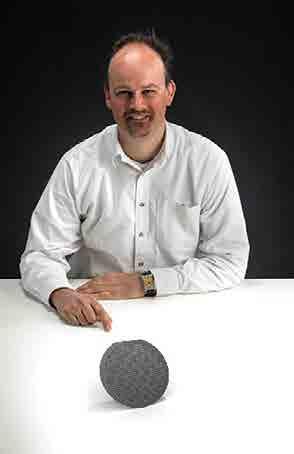
ing pressure, flow and the temperatures of liquids in general.
Kattenhoej said, “We are an entirely new entity and through the steering group, we retain responsibility for all global activities and at the same time take advantage of the Group’s global network in R&D, sales and production. We represent the driving force in this area and our strategy is designed to accelerate sales in this particular sector of our operations. Our strategic goal is to generate sales of more than 600,000 units this year rising to more than 1,000,000 in the next few years to come. In order to help achieve this goal we are setting up distribution channels in Europe, North America and Asia. We plan to have local capacity for assembly and our approach to production is that we start by having local variants and if it becomes big, then we establish manufacturing facilities to meet the growing local demand.”
Kattenhoej added, “We have the competitive edge as a result of our advanced technology, lower packaging costs and our sensors have no moving parts so maintenance is minimal. We work closely with leading Danish universities and German institutes to develop new products and we see our customers not just as clients but as partners, and we help them to develop their products for the global market. We also have a tried and tested system approach so that our customers can save energy and increase efficiency in all their areas of manufacturing. In fact, we are almost at a point where more than half of our products are sold with controls designed to save
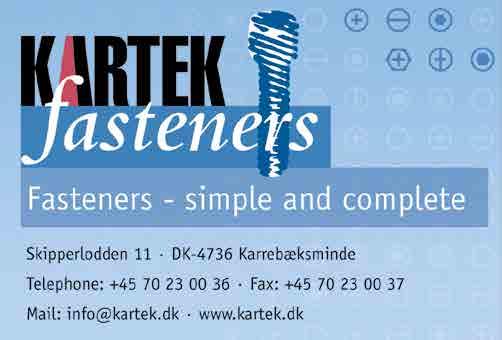
Sand Industries is among the leading suppliers in metalworking and plastics.
We deal with both one-off production, batch production and fully assembled products for customers.
We make everything from prototypes to large series production.
Henning Sand Maskinfabrik A/S Agerskellet 6, 8920 Randers NV Phone: +45 8642 7177 (contact person: Alex Sand) www.sandindustries.dk
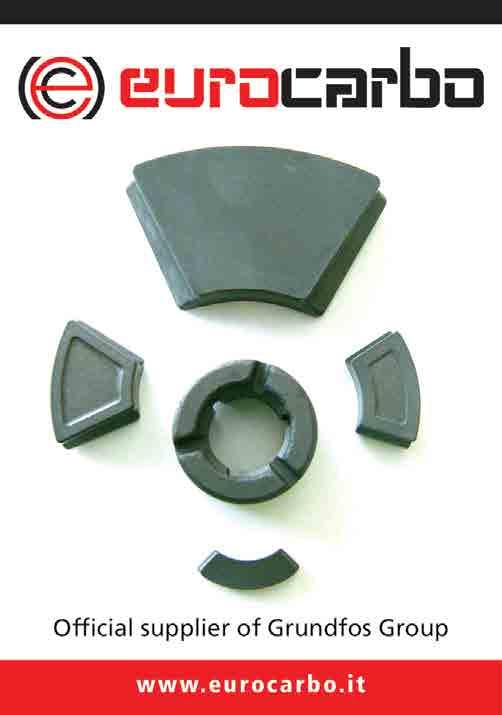
energy. As well as producing energy-saving pumps and sensors for ‘ground-source’ heating systems and thermal solar heating, we also are seeing growth in air-to-water heat pump systems, where the control of the speed of the pump can make a big difference to efficiency and energy saving, which can be displayed to the customer, and we plan to expand from these two key applications for the present time. Temperature control – including chillers – for industry is next.”
Putting sustainability first
Grundfos has always taken its responsibilities very seriously in relation to the environment and believes that although industry is part of the problem, it is also part of the solution. Therefore a global response to climate change will create a greater demand for solutions that will significantly reduce water and energy consumption worldwide. In its position as a global leader in its field, Grundfos is in a unique position to meet these demands with its advanced products, services, partnerships and organisational voice.
Grundfos plans to be part of the ‘sustainable’ solution by focusing on innovation and new product development and applying a broad range of initiatives that will work together to propel it into a more sustainable future. When it comes to producing innovative products and the manufacture of semiconductor chips, the company sees this development as a strategically important basis for sensor integration into the overall Grundfos pump company. Whereas the microchips are produced in clean-room facilities at Farum, the pressure sensors in which the chips are integrated are produced at the Grundfos Electronics headquarters in Bjerringbro, Jutland being the main strip of Denmark stretching up as a peninsula from the borders of Germany going north.
In order to achieve its goals, Grundfos has invested more than €100 million on research and development in the last five years. In addition, the mass production of its sensors has already begun with the company predicting that it will achieve an annual production of over two million pressure sensors before the end of this decade bringing the facilities to the economies of scale they are designed for. Micro Electrical Mechanical Systems / MEMS has already changed the automotive industry fundamentally with more than 150 sensors in the latest German cars providing unseen efficiencies and safety – now the time has come for pumps, heating and cooling systems. n