
7 minute read
Taking non-invasive diagnostic technology further
Nicolay is one of the global market leaders in the development and manufacture of medical device accessories for non-invasive patient monitoring and diagnostic. Philip Yorke talked to Christof Muz, owner and MD of the Nicolay Group, and Jens Hoche the company’s sales and marketing director about its latest investments in plant, new technology and its groundbreaking, innovative new products.
Nicolay was founded in 1964 by the two Nicolay brothers who began by establishing a plastic injection moulding company in Waiblingen, Germany. With the ambition to diversify and grow in 1972 the company invested in a new, modern plant in Nagold, close to its original site. From the beginning the site in Nagold focused on the production of electro-medical accessories. A management buy-out two years later led to a separation of the two business operations, with the plastic injection moulding company in Waiblingen still owned by the Nicolay brothers and the medical accessories business then held by the families Muz and Schwarz.
Nicolay GmbH in Nagold has kept its focus to the medical device accessories market for the past 40 years and has expanded its operation in several steps to reach a total of nearly 10,000 square metres of production space in Nagold today. One remarkable milestone was the establishment of the raw cable manufacturer Sensocab Kabelproduktion GmbH in 1992, on the same site with the same ownership. The two companies form the core of the Nicolay Group and complement one another to the advantage of their customer base, as the differing technological expertise of each of these is combined in the medical cable accessories offered by Nicolay.
Dynamic growth followed and in 2008 another milestone was reached when the Nicolay Group established a new, state-of-theart manufacturing facility in Romania, which today supports the group with another 1500 square metres of production space. In 2009 the group consolidated its board of management with all shares in the Nicolay Group being transferred to the Muz family.
Today Nicolay is a highly successful, vertically integrated manufacturer of medical cables, connectors and cable assemblies that can be customised to suit any individual requirement and specification. Currently the group employs over 400 people
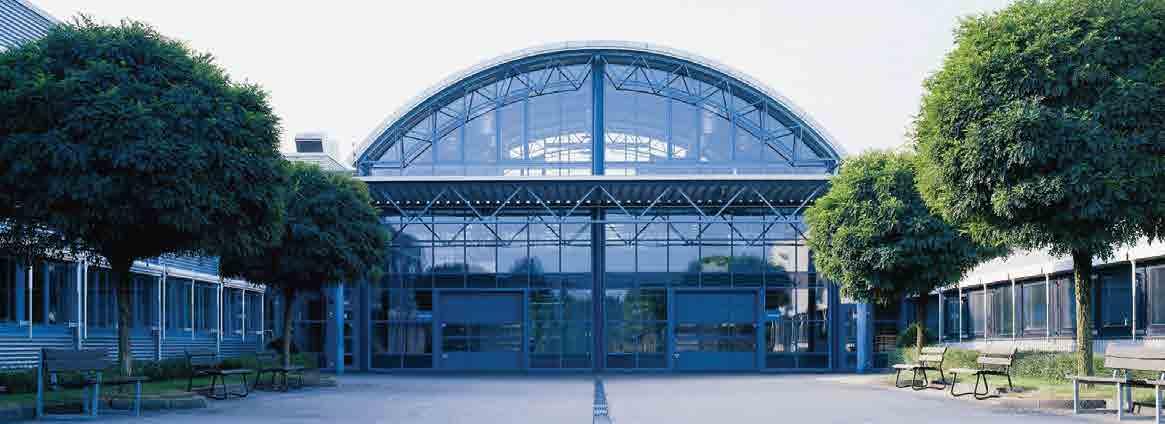
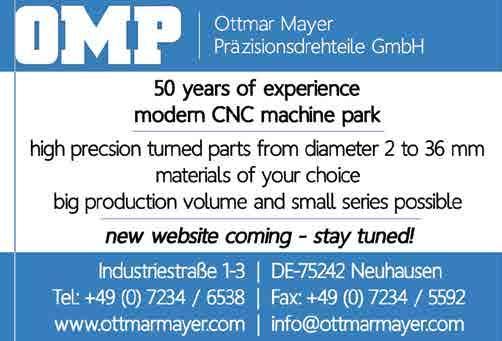
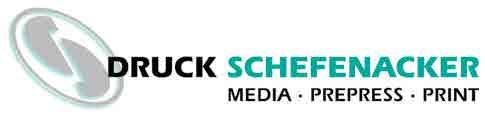
at its three manufacturing sites in Europe and in 2011 recorded sales of more than €35 million.
Continuous investment programme
Since it was founded over 45 years ago, the Nicolay management followed a programme of continuous investment, not only in facilities but also in new technologies as well as in research for the development of new, innovative, noninvasive medical products. The company’s broad portfolio of products includes high quality cable systems, connectors, silicone rubber sealed and packaged electro-mechanical components and sensors such as SpO2 sensors and surgical handles as well as complex modular sub-assemblies, which are custom developed as required in the application.
Recently Nicolay made a major investment in the extension of its facilities in Nagold when it finalised the installation of a new, state-ofthe-art clean room for the manufacture of its latest sterile products. In addition, the company plans to invest an additional €2.5 million in the expansion of its modern cable manufacturing plant. This means supplementing its existing manufacturing site by a further 1,500 square metres of productive manufacturing space with a view to significantly expanding its production capacity and increasing its current product portfolio.
In the development of innovative medical devices, Nicolay is making major progress in a number of key areas, as Muz explained, “Historically we have always placed a high priority on the development of the highest quality, innovative products for reusable applications which are developed to our OEM customer’s specifications. Our portfolio includes three generations of ECG monitoring cable systems, all customisable to different application scenarios from operation room, critical care, wake-up room to ambulance and telemetry applications. We are very proud of the fact that the 2nd generation of these systems was chosen to form the basis of the American National Standard ANSI/AAMI EC53:1995.
“However the requirements do not remain constant. Currently we are involved in the development of our fourth generation of non-invasive products designed for the cardiovascular therapeutic area. This includes the development of a complete new connection system to support the tightened requirements on cleanability of such reusable accessories and also a whole new class of products which are compatible with the reusable products, which we like to name single patient use (SPU) accessories. This class of products will not be a truly disposable product, but will support one patient throughout his hospital treatment, be it one day or one week. The advantage of this product class is the minimisation of the risk of cross-infections from patient to patient, but in addition it also limits the volume of waste, which is a well-known problem with single-use disposable products.
“Nonetheless, we are also involved in the development of disposable products as there are medical applications where only this type of product will work. This is especially true in areas of sterile accessories, which our newly built clean room supports. All R&D for such new developments is con-


ducted in-house in very close cooperation with the OEM concerned. To support this we are a full scope, one-stop shop supplier not only for the manufacture and assembly of products, sub-assemblies and systems, but also for all the services necessary to bring such developments to the market. This includes tool construction, tool making, test development and all necessary verification and validation testing with regards to the requirements of the customer and all relevant medical regulations.”
Muz added, “Unlike our competitors, we are a truly vertically integrated company that is capable of all kinds of thermoplastics and liquid silicone rubber moulding and insert moulding, metal stamping and the customising of our welding, joining and gluing processes in the range of cable assemblies. We also have another major advantage in that none of our competitors presumably can match the depth and breadth of our manufacturing. One reason for this high integration is that we are so exclusively focused on the development of non-invasive medical systems, which led us from the past to the point where we are now. On this path we always prioritise the problem analysis, the wishes and the ideas of our customers, add our knowledge and experience in the development of the best possible application specific solution for our customer. This application centric approach often requires the development of totally new manufacturing technologies, which each time expand our manufacturing capabilities and at the same time result in the best possible solution within each project.
“One of the most exciting developments recently has been our move into a new therapeutic area, that of non-invasive lung function monitoring, where we are developing a complex patient cable for impedance tomography, which involves measuring very small higher frequency signals at the patient’s chest. This required the development of a totally new kind of raw cable combining six tri-axially shielded signal wires in a cable with an overall diameter of only 3.3mm. Each of the double-shielded signal wires has a diameter of only about 60 µm (AWG 42). For this product we also had to develop several new assembly processes to attach up to 12 connection elements to the signal wires on one cable.”
The development of electro-surgical handpieces, is another area where Nicolay has dominated the market through its innovative designs and superior product functionality. These items can be identified by their highly individual design, robustness and long-lifetime service cycle, in a demanding application environment, where hot-steam autoclaving at 138°C is mandatory. Increasing global reach
A large proportion of Nicolay’s non-invasive medical products are exported to its traditional markets in Europe and the USA where its customer base has established markets. However, the company is moving into new global markets in South America, Russia and Asia. Hoche commented,
“With our ability to increase our production capabilities and with the introduction of new, innovative products, we are actively looking at extending our export reach to new global markets such as Brazil, Russia, India, Japan, and Korea. However our main focus for the foreseeable future in addition to the North American market will be Asia, which also mirrors the growth markets for our OEM customers. China is a different question altogether and it is a very different market so at the present time this is not a region on our list of priorities.”
Nicolay’s formula for success continues to deliver exceptional, innovative products that are driving sales and the company forward.
The company’s strategy is based upon its commitment to further organic expansion as well as to the continual introduction of new products targeted to provide optimal efficiency and ergonomics for its OEM customers.
For further information about Nicolay medical products and systems, visit: www.nicolay.de n
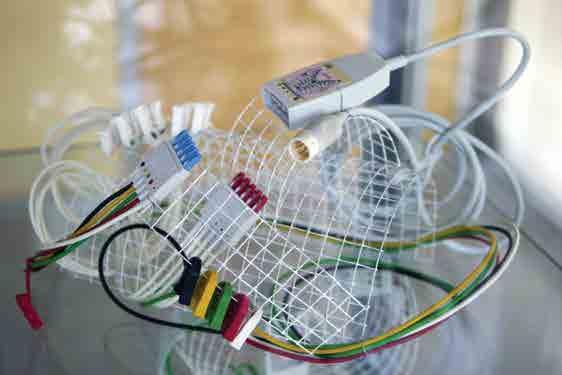
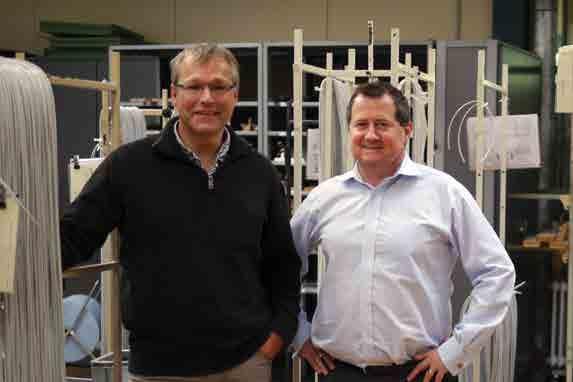