
6 minute read
Nature-inspired innovation
How do you keep a building cool in a hot climate using hardly any energy, or develop a high-speed bullet train that makes hardly any sound? It is the purpose of biomimicry, the examination of nature’s systems to solve very human problems, to find answers to these questions. Victoria Hattersley looks at some of these solutions, and at how PLM (product lifecycle management) tools and 3D technologies can be used to aid the design and manufacturing processes.
The principles of biomimetics are increasingly used in almost every manufacturing sector to develop more environmentally friendly solutions, where they can help product designers with lightweighting, cutting energy use or even developing more efficient ways to use renewable energies.
At the Dassault Systèmes European Customer Forum held in Paris in November 2011, Janine Benyus, author and president of the US-based Biomimicry 3.8 association, discussed the many ways in which biomimetics are changing our interaction with the world. She explained: “Biomimicry is the process of studying nature to find out what it would do to reduce noise, keep things cool, reduce waste etc. – enabling us all to live together on the planet in a sustainable way.”
Taking inspiration from systems which have been tried and tested in nature over millions of years, scientists and technologists are now able to create more ecologically sustainable answers to day-to-day problems. 3D simulation and CAD software programmes, such as those developed by Dassault Systèmes, are just some of the tools which are being used to make these ideas a reality. Modelling from nature
But how exactly can 3D modelling systems help to mimic nature? What can they offer the design team to make their job easier? The programmes offered by Dassault Systèmes alone serve as examples of the huge range of sophisticated tools available to designers now. Its Catia programme allows designers to realise a concept in its entirety using only 3D virtual modelling. What 3D allows a designer to do is test out how a system might appear and what kinds of problems might be encountered in its manufacture. Programmes such as Simulia, meanwhile, give realistic simulations, factoring in every variable, to test how a certain product or concept will perform and react in the real world.
Using 3D and PLM software means problems can be eliminated early in the design phase without the need for costly re-modelling later on. It is also a far more sustainable way of designing because it means that when it comes to manufacturing, only the minimum material necessary need be used. Delmia, meanwhile, is a programme which, following on from the design phase, enables manufacturers to work out the best ways to actually produce using less energy and suppliers, minimising supply logistics and where possible using local manufacturing. This means that not only are its users developing sustainable solutions by mimicking nature’s way of responding to problems, they are also carrying this out in the most environmentally friendly way possible.
Say, for example, you were trying to develop a method of making car components lightweight but still strong enough to withstand any stress. Engineers at Adam Opel Gmbh have been designing engine components with the aid of computer simulation techniques such as CAO (computer-aided optimisation) and SKO (soft kill option), developed by Claus Matthek at the Karlsruhe Research Centre in Germany, which can define the material property of each element of the design and show the simulated effects of adding or removing material.
Prof. Dr. Lothar Harzheim, biomimetics specialist at Adam Opel, explained the principles behind this: “Both CAO and SKO are based on the idea that nature is the ultimate designer and that, consequently, biological load carriers – such as trees and bones – have been optimised during the evolution process. In a
Janine Benyus, president of Biomimicry 3.8
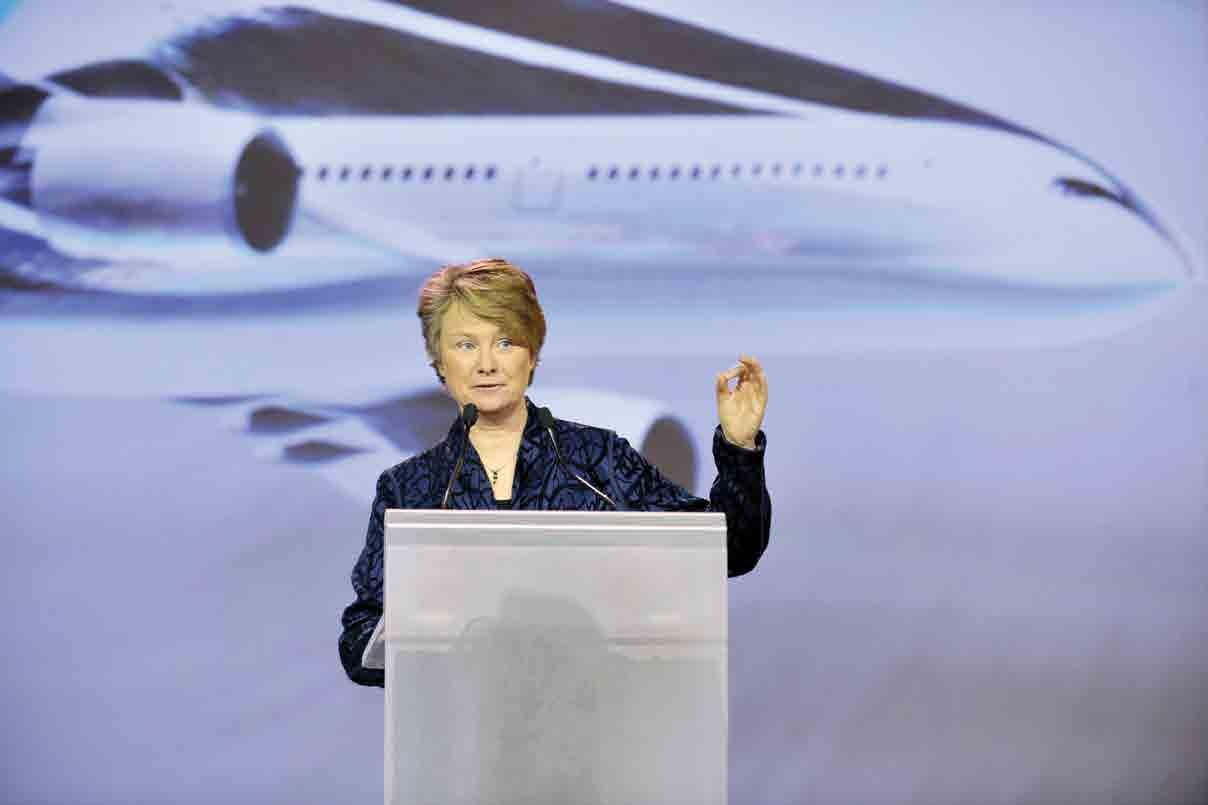
mechanical sense such biological load carriers are nothing other than engineering components. Furthermore, minimum weight is very important for surival, especially for bones. A general underlying adaptive biological growth rule leades to optimised biological structures which can be simulated.
“The SKO method is applied to the inner part of structures which means that materials can be removed and new designs created. The most important SKO enhancement created by Opel is TopShape, which takes manufacturing constraints of cast parts into account and increases the efficiency and optimisation of parts such as brackets and axle components.”
As an example of the success of this methodology, an engine mounting developed by the company using the CAO and SKO methods is 25 per cent lighter and the stresses are 60 per cent smaller than a conventional counterpart. In parts where aluminium could be used instead of steel, the weight reduction culd be as much as 60 per cent.
Biomimicry in action
There are countless other examples of systems that have been developed using principles drawn from nature. In the area of renewable energy, the California Institute of Technology (Caltech) has been studying the behaviour of schooling fish to develop more efficient methods of wind farming. After studying the vortices left behind by fish swimming in a school, researchers at Caltech noticed that some of these rotated clockwise, and some anti-clockwise. This led them to wonder whether alternating the rotation of vertical-axis turbines – which are relatively new additions to the wind energy sector and take up less space because they have no propellers – would improve efficiency. They also noticed that the vortices in fish schools were arranged in a ‘stair’ pattern as opposed to current wind farms which arrange turbines in rows. They believe that staggering the farms in this way may improve efficiency as much as tenfold.
How about high-speed trains which make virtually no noise? The Japanese Shinkansen bullet train, in operation since 2008, was inspired by the example of kingfishers to solve the problem of high-speed trains emitting loud sonic booms when they exit trains tunnels. The design of the kingfisher’s beak allows the bird to dive from the air into the water with minimal energy loss, and the same principle was applied to the front of the train to allow it to exit tunnels almost noiselessly.
The problem of how to inhibit bacterial growth in environments where bacteria pose a health risk, such as hospital surfaces, has been addressed by a partnership between FLEXcon, an innovator in adhesive coating and laminating, and Sharklet technologies, a company which has developed technologies to inhibit bacterial survival and growth. They have developed a protective film, using Sharklet’s core technology inspired by the microbe-resistant properties of sharkskin, to be applied to any germ-prone surfaces to reduce the presence of bacteria. This product is already in use in many healthcare facilities, research laboratories and other settings at risk from bacteria.
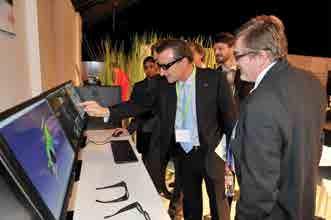
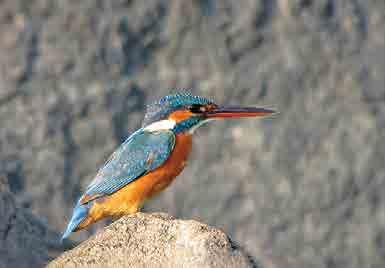
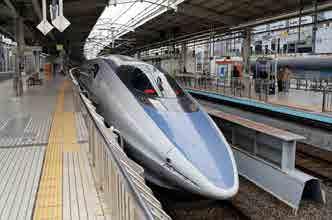
What next?
These are just a few examples of the huge variety of nature-inspired innovations currently in use, and there are of course many new projects in the pipeline. CAD technology is now considered to be a crucial part of this, as John Laux, Digital Design Strategist for Biomimicry 3.8, explained: “Everybody is using some kind of 3D CAD-based software in biomimetics these days. It’s just accepted as the norm.”
In fact, he says, in the future there may well be software developed by companies such as Dassault specifically for these purposes, rather than fitting the work around the standard programmes. “People use traditional CAD programmes for biomimicry currently, but we’re working with vendors to try and find ways to implement more biomimetic features into the CAD software itself. It will actually be about working with the software to integrate those principles so we are trying to work out how you can do this mechanically.”
As has been illustrated above, the principles of biomimetics can, and indeed many would argue should, be integrated into product development for almost any industry sector. “Our goal,” said Janine Benyus, “is moving these kinds of principles into the systems that humans design every day. I would urge manufacturers to invite a biologist to the design table, have them upstream in the design chain, and see what happens.” n