
5 minute read
Profiling performance and precision
The Homag Group is a diverse, global engineering company and the world’s leading manufacturer of machines and plant for the woodworking industry. Philip Yorke looks at how the company has strengthened its market position further with the launch of a new generation of highly efficient and energy-saving precision products.
The Homag Group is famous for its range of iconic, branded products and their contribution to increasing the efficiency of the furniture manufacturing industry. The company offers a wide range of machines and solutions to meet the needs of the most demanding furniture makers and their suppliers. Homag is particularly well-known for its sizing and edgebanding, softforming and postforming machinery, as well as for its stationary CNC machines and complete production line solutions.
Today the Homag Group consists of 14 subsidiary manufacturing companies, 11 of which are located in Germany with a further one in Spain and others established in Brazil and China. In addition, the company has more than 20 sales and technical service companies supporting its global operations, as well as a leading global consultancy company: Schuller Business Solutions.
Continuous performance optimisation
The significant potential for energy savings in terms of consumption was realised at an early stage by Homag, and its commitment to performance optimisation has resulted in some remarkable new products and some innovative technical achievements.
This ongoing drive for enhanced efficiency is exemplified in the new technology package from Homag called ‘ecoPlus’ which is designed to increase productivity and save costs. This new ‘eco’ package encompasses a whole series of innovations, all of which were developed to achieve energy savings of up to 30 per cent or more whilst at the same time significantly reducing operating costs. These new technologies sum up Homag’s approach to sustainability and make production significantly more efficient and more profitable, whilst at the same time offering greater environmental benefits. In addition, Homag focuses on the most efficient deployment of its machines for production optimisation, efficiency and cost-saving.
Examples of this new technology in action can be seen with the latest Brandt Highflex edge banding machine 1880, complemented with ‘ecoPlus’ technology which offers up to a 20 per cent increase in production output with the same energy input. This is in addition to a saving of up to 40 per cent on reduced air consumption due to the use of a dual-circuit compressed air system.
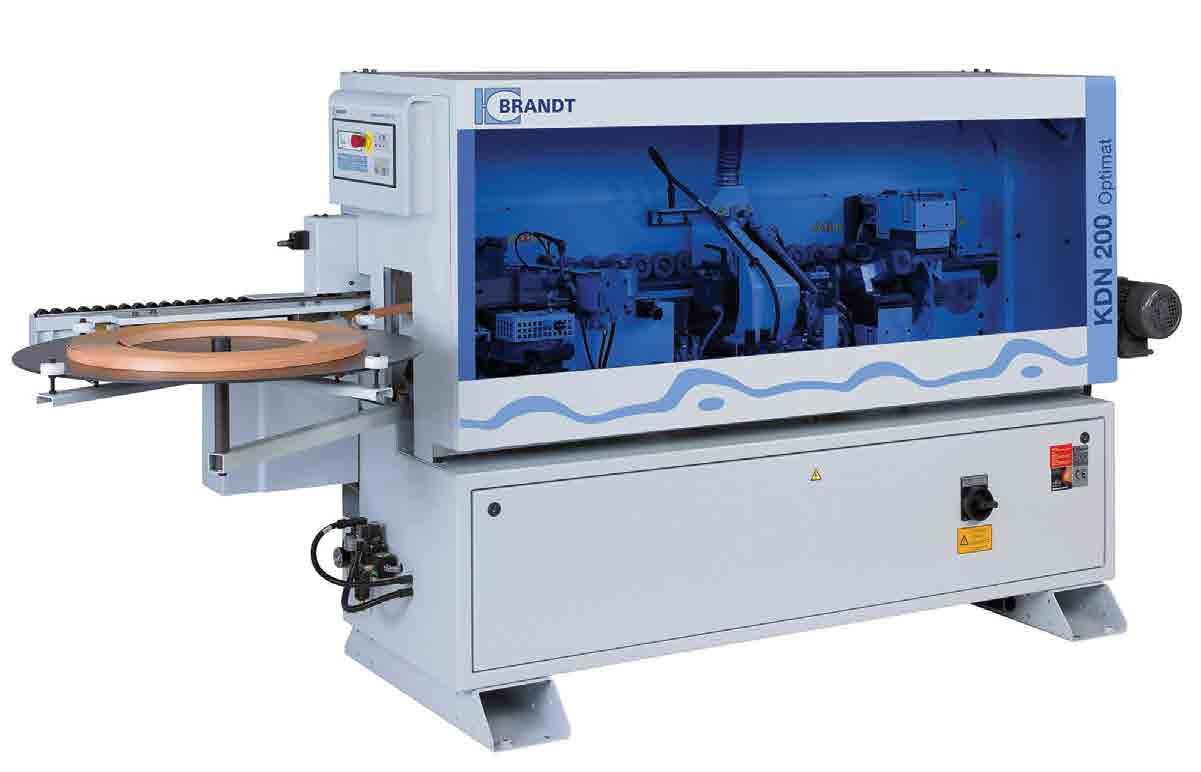
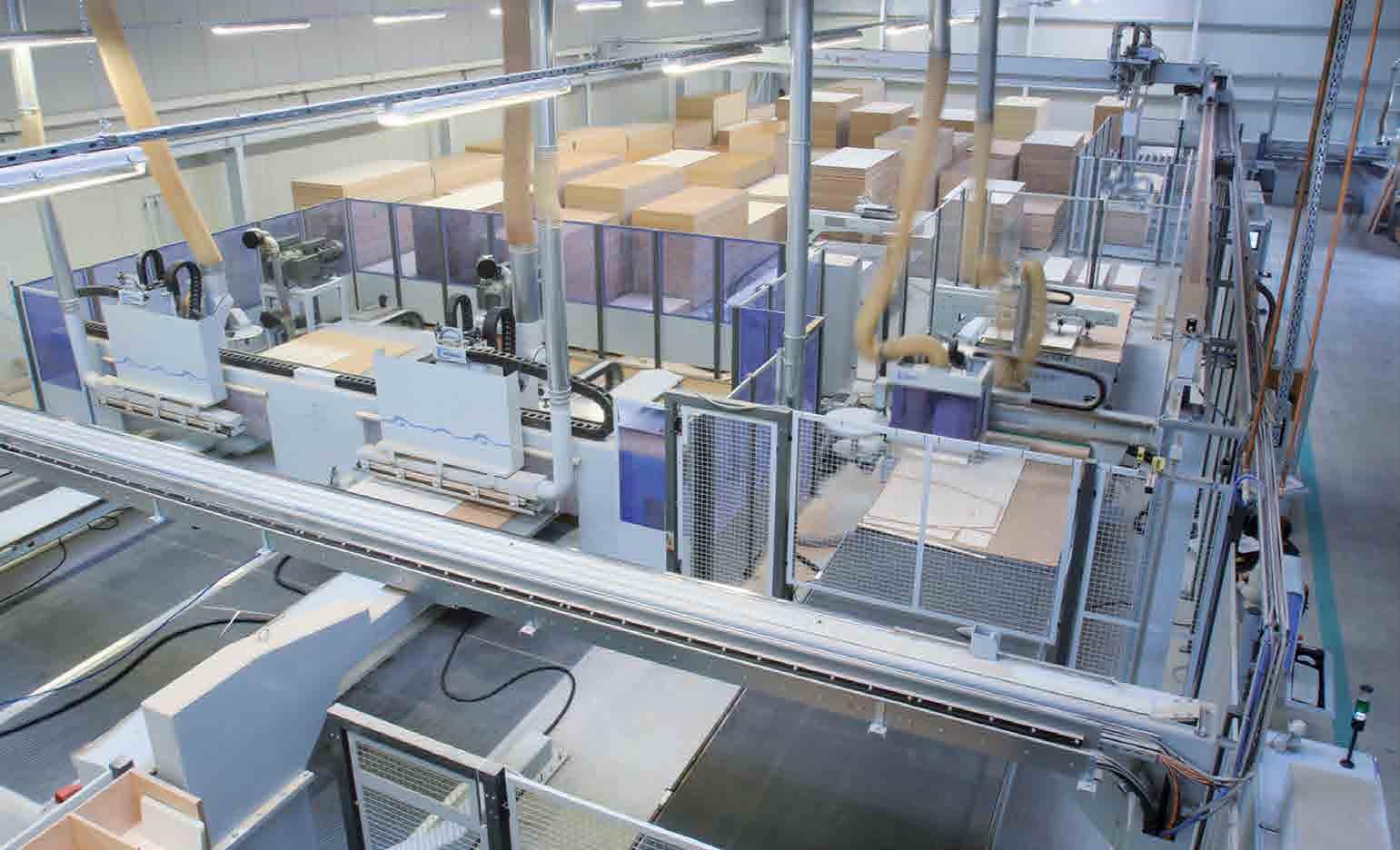

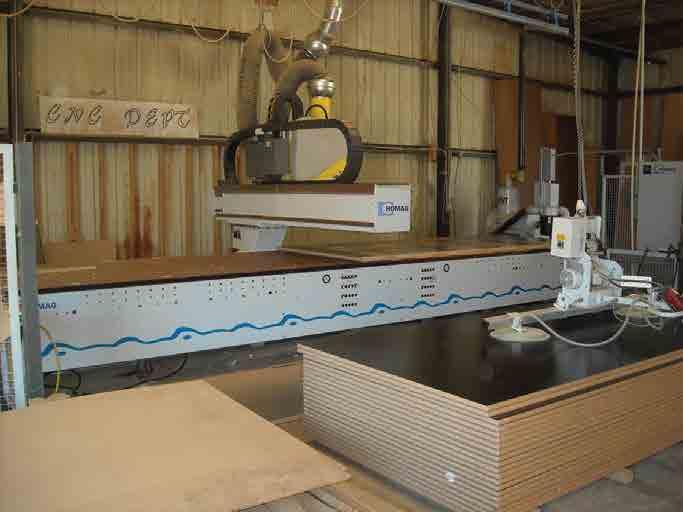
In another recent example, the Homag processing centre BMG 512 has also achieved significant savings with ecoPlus technology achieving energy savings of up to 8160kWh a year through the standby operation alone and up to 5.7t less carbon emission a year. There are also many other examples of how Homag’s ecoPlus technology has been put to work, from applications in extraction technology to its optimisation software packages.
Doo-to-door success
When RIWAG of Switzerland decided to invest in an entirely new door-leaf production plant, it looked no further than the Homag Group for advice and technical support. In fact, the company’s confidence was not misplaced as it decided to commission the Homag Group to supply the complete door leaf plant for them. The result has been that not a single square metre of floor space remains unproductive. Today, the exemplary door-leaf blank manufacturing facility operated by RIWAG Turen AG is an example of everything that a high-tech production plant should be and sets some impressive efficiency milestones along the way.
The all-new production facility is located in Arth, central Switzerland, and has been operational now for two years. It enables RIWAG to produce internal, external, apartment and functional doors in any size and dimension from series as small as batch size one with what was previously an unattainable degree of production flexibility. The company’s owner Aldo Rickenbach said: “Achieving enormous flexibility is only one side of the coin. Doing it economically and to a high standard of quality is another.” The real challenge of this project for Homag was therefore reconciling these two seemingly contradictory requirements.
Quality installation assured
Spalijisten AB is a leading furniture component manufacturer based in southern Sweden and uses an innovative and highly

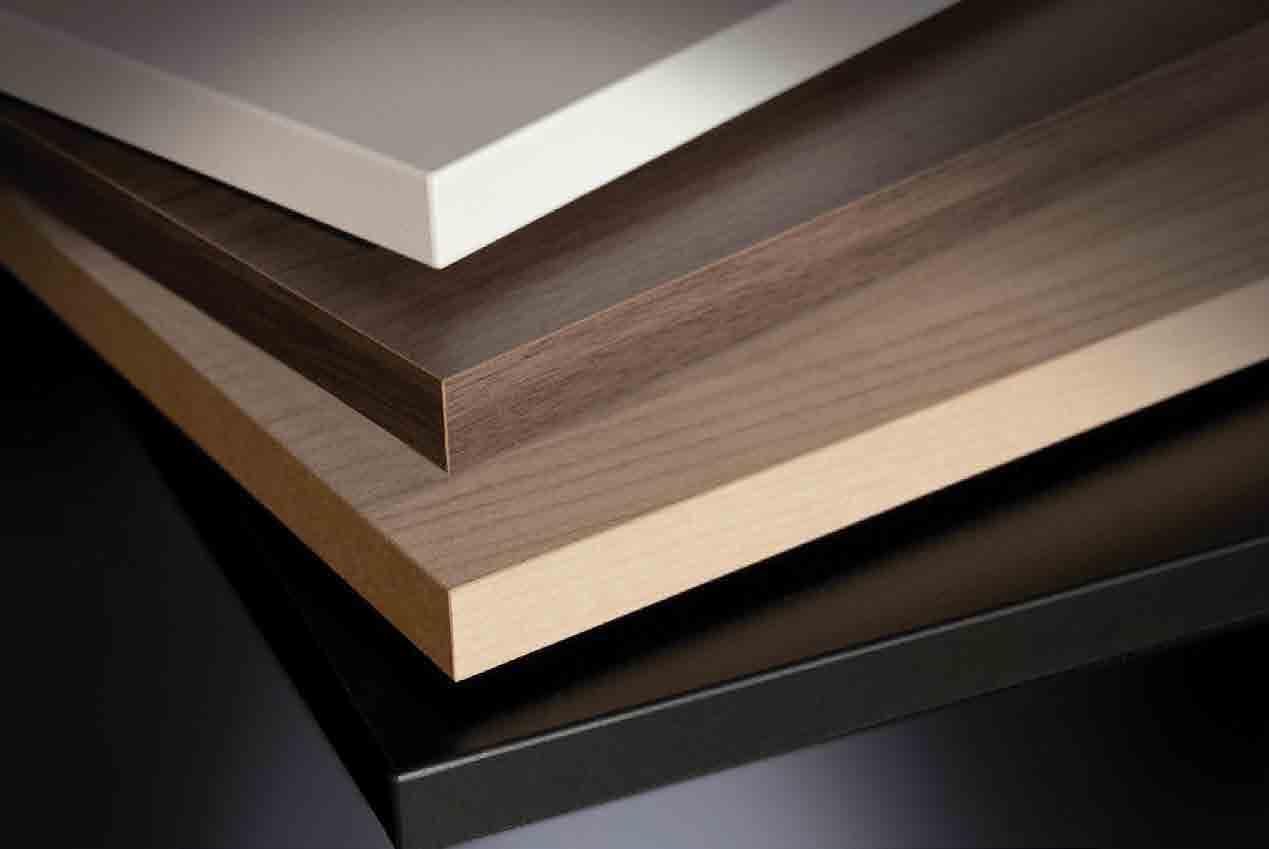
efficient concept recently developed by Homag Engineering. Spalijisten specialises in foil-wrapped furniture components and as part of a major restructuring process was looking for a transverse processing plant that was capable of a highly flexible response to the manufacture of its diverse range of products. At Spalijisten the company’s wrapping process takes place first, followed by the complete processing of all parts in a single work sequence. This is made possible by a fully automatic control program, which executes an automated central plant process led by a Homag PC22 control system. This state-of-the-art plant combines the crosscutting of strips with edging, sizing and drilling, all under the bottom line.
This innovative solution saves two conventional work steps and thereby reduces the investment required whilst increasing efficiency and productivity. “The new processing line clearly demonstrates the benefits achievable when working with the pooled expertise of the Homag Group. The assurance of experienced specialists, which included Bargstedt, Holzma, Weeke and Homag, for each of the individual work steps, was coordinated by Homag, and demonstrated the value of gaining optimal results by relying on a single source,” said a Homag Group spokesman. n
About Murrplastik Systemtechnik GmbH
Since its foundation in 1976, Murrplastik Systemtechnik GmbH has been a pioneer for high-tech plastic products. In 1984 the first open cable drag chain was patented in Oppenweiler. In 1993 Murrplastik Systemtechnik introduced the first cable entry systems. The latest development from the Swabian engineers is the first magnetic cable drag chain. For the first time travel distances are possible without the upper and lower chains touching, meaning there is no wear and tear. Up to now Murrplastik Systemtechnik GmbH has registered over 100 patents. Its products are sold via branches in France, Italy, Switzerland, Spain, USA and China as well as through representatives in Europe, North and South America, Africa, Australia and Asia.