
4 minute read
Precision and flexibility APAG Elektronik
PRECISION AND FLEXIBILITY
APAG Elektronik s.r.o. based in Pardubice in the Czech Republic is a subsidiary of the Swiss APAG Elektronik AG. Its core business is the production of printed circuit boards using the SMT and THT technologies, and the production of electronic systems for the automotive sector. Executive director Ladislav Hrdý spoke to Romana Moares about the history of the company in the Czech Republic and its future prospects.
The company was established as Bohemiatech s.r.o. in 1993 and only three years later APAG Elektronik AG became its biggest customer. In 2007, the company was taken over by the Swiss manufacturer and became its fully owned subsidiary.
APAG Elektronik AG was founded in 1975 to produce and sell electronic measurement and control devices, to major European customers, such as electronic modules for the automotive sector, consumer products, power tools, building automation industries and general industrial applications. Today the company employs 180 staff (50 of which are in product development) and has several operational facilities in Switzerland, the Czech Republic and Hungary.
The Czech subsidiary is based in Pardubice in north-east Bohemia (some 100km from Prague) and operates on a 3000m2 site (of which 1000 m2 are production halls). Despite the recession, it has grown steadily: in 2011 the company employed over 140 people and achieved a turnover of €10.5 million. Forecasts reflect a positive market trend – it is estimated that the figure will rise to €13 million in 2012.

Fast and flexible
In the beginning the company supplied to other sectors, but since it became part of APAG 100 per cent of its components are sold to the automotive industry.
“Prospects in Europe are good,” says Ladislav Hrdý, the executive director of the Czech plant. “We supply to German car manufacturers such as BMW, Audi, Porsche, VW and Bentley which are in excellent shape. On top of that, most of our customers make the upper market end cars, the sales of which are forecast to increase in the next few years. This is our advantage,” he claims, but does not exclude the possibility that in the future his plant will again supply to other sectors as well.
The Czech manufacturer’s competitive advantages include long-term experience in the sector (tier 1 and tier N), a profound knowledge of specifications within the automotive industry, the achievement of ISO/TS 16 949 and ISO 14001 certificates, first-class production technology (SMT, AOI / X-ray lines, a nitrogen atmosphere for wave and reflow soldering). To improve its production process, the company has recently implemented iTAC software for traceability and for production synergy. “We are a relatively small company so we can provide a flexible and fast response to customer requirements,” adds Mr Hrdý.

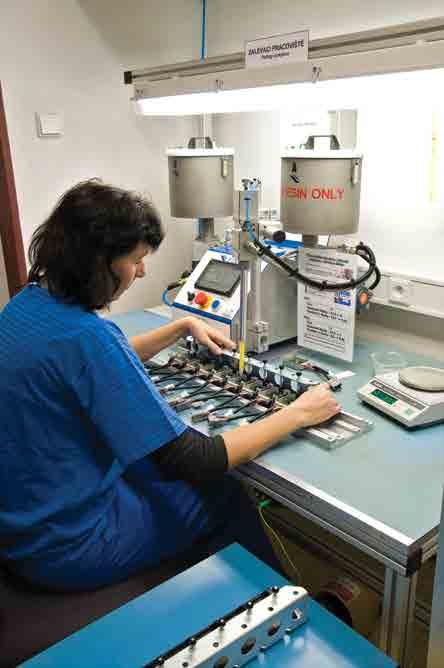
Three product groups
APAG Elektronik s.r.o. focuses on the production and sale of electronic systems developed in its Swiss parent company, but it also manufactures components based on its customers’ product developments (EMS). The electronic systems may be divided into three parts: door handle lighting, supplied mainly to BMW (the company is already making the fourth generation of the product); overhead consoles (Audi) and electronic control units (Porsche, Audi, VW, BMW). This portfolio will remain unchanged for the next few years as the projects run for at least five to ten years, explains Mr Hrdý.
SMD components are printed on two fully automated production lines. The modules are soldered in lead and lead-free processes within a protective nitrogen atmosphere. All printed modules are checked on AOI testers, whilst the soldering of critical parts (e.g. BGA) is checked using X-ray technology. DPS cutting from the panel is done on guillotine-type cutters. If customers require it, the products can be protected by means of silicone against dampness.
Although the company sells some products to the Czech-based Continental, an overwhelming majority of its output goes to its customers abroad, mainly in the EU countries.
Further growth
Over the past five years the company has invested a considerable amount in new technologies and machine upgrades. Airconditioning was introduced to the production hall as well as soldering under a nitrogen atmosphere, and many new machines were purchased to satisfy rising demand. Last year (2011) another massive investment was completed when a second production line was commissioned. Investment in IT improved the production process control.
“Our capacity currently meets the customer demand but this will not be the case for much longer,” says the executive director. “This year we want to increase the production area by another 1000m2 and also extend the warehouse. This is fully in line with the forecasted growth of our customers – the projects are up and running and will be completed regardless of another potential recession, which many fear. We certainly hope that the new investment planned for the next three to four years will secure more work and the future growth of our company,” he concludes. n
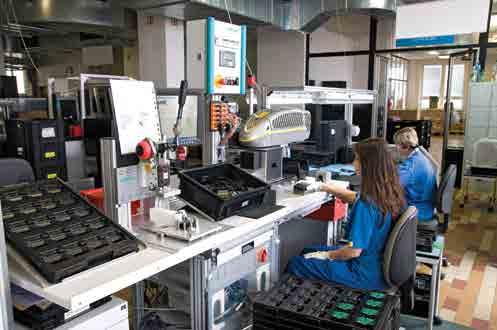