
5 minute read
Perfect casting OMCO
PERFECT CASTING PERFECT CASTING
Headquartered in Aalter, Belgium, OMCO has been manufacturing glass moulds for industry since 1964 and today it is one of the global leaders in its sector. Industry Europe looks at what has made this company such a long-standing success.



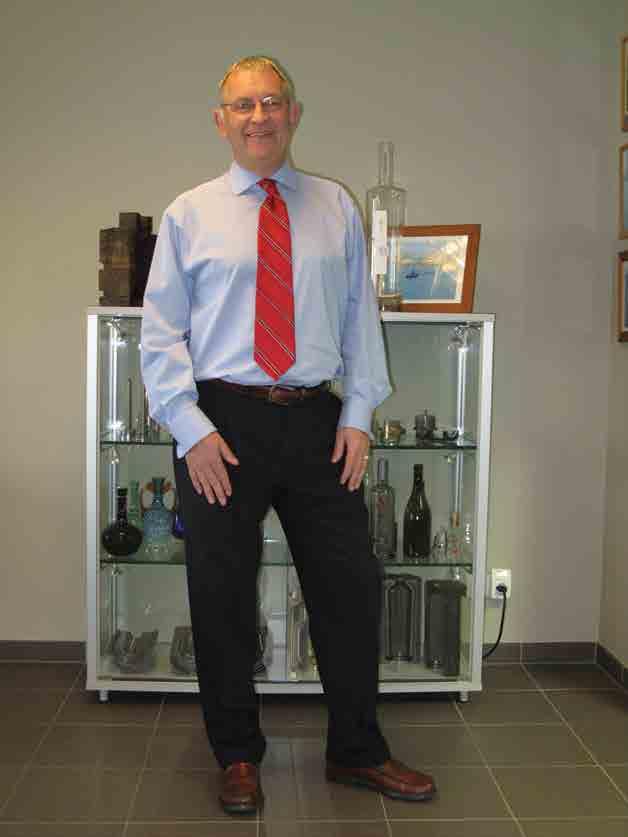
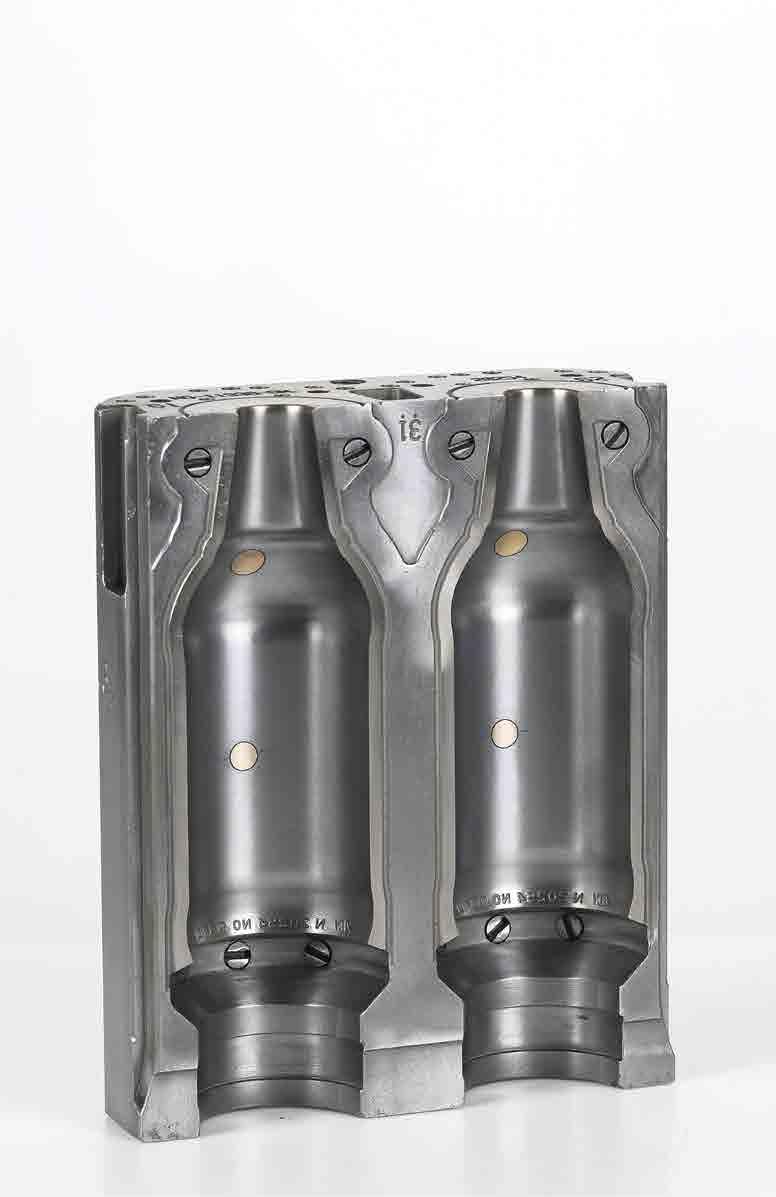

The Omco Group has seven major production facilities in Europe with offices located in all major European countries, including Austria, the UK, Romania and Turkey. In 1970 it acquired a foundry in Hamme, Belgium in order to supply in-house castings to a very high standard in both cast iron and bronze. This is where the biggest company of the group. OMCO International, is still based today. In addition, the company acquired its second foundry in Slovenia in 2001, which specialises in ‘grey casting’ and was purchased to enhance the group’s speciality castings sector.
In 2001 the group expanded with the establishment of OMCO Istanbul, followed by OMCO Romania in 2005 and finally EMCO USA in 2006 to serve the North American market. The group’s glass moulds account for around a third of its overall turnover, but it also offers products such as neckrings, plungers and tableware moulds.
OMCO International and its subsidiaries are part of the BMT Group, which is active in a diverse range of industries. These include the glass mould making division, which is composed of nine companies in eight countries; the industrial gears and transmissions division, which is present in four countries with four companies; the aerospace division with three companies in three countries; and the glass engineering division which includes three companies active in two countries.
Production processes
OMCO’s products for the hollow glass industry consist of specially developed castings in grey and nodular iron and aluminium bronze. Its biggest market is food and beverages although the pharmaceutical sector has also come to be increasingly important. It also serves the cosmetics and tableware markets.
OMCO’s business is built around five key ‘steps’, as it outlines on its website: engineering, foundry, manufacturing, quality assurance and moulds. OMCO has a multinational group of engineers to support its customers throughout the world and uses PRO-E based software systems for product design and programming.
Secondly, its foundry division, OMCO Metals, has locations in Belgium and Slovenia with a flexible supply of its cast iron and aluminium bronze castings. With regards to the third step, manufacturing, the group is equipped with the latest state-of-the-art CNC and robotic machinery. Quality control is the next stage and includes a statistical process control (SPC) on the shop floors as well as a final quality control
after the completion of the production process. Finally, OMCO is able to offer the equipment for any shape of mould its customers might require, using a variety of welding techniques to increase the life of the mould.
Saving energy
Recognising that its clients are looking to reduce their environmental footprints as far as possible, OMCO has been focusing increasingly on developing lighter glass packaging products, which will use less energy in transit. This means thinner glass which is capable of maintaining the same level of strength and product protection. To meet this demand, a few years ago OMCO added a special aluminium bronze mould to its portfolio. In addition to saving energy costs and usage, OMCO is able to manufacture with a great deal of speed and efficiency. Its Individual Sector (IS) can produce over 600 hollow glass products per minute from a single mould, with each mould having the capacity to manufacture up to one million glass containers. The company also applies a nickel coating to protect the edges of the mould so there is no break-away.
Continuous investment programme
The increased pressure for sustainability has meant that there is a great demand for glass products, which are 100 per cent recyclable. This has enabled it to expand at three of its European facilities. Furthermore, last year (2011) it established a new joint venture with Hindustan National Glass (HNG), the leading Indian glass container manufacturer. The two companies have set up mould manufacturing facilities in India under the name OMCO HNG Engineering Ltd. The plant is equipped with a state-of-the-art foundry and CNC machines.
Expansion has also been taking place at OMCO’s Romanian, Croatian and UK production sites. Last year alone it invested over €9 million in new equipment to increase its manufacturing capacity and meet the growing global demand for energy-efficient, recyclable glass containers. n
Messer investing in its customer’s comfort
December last year, Messer Benelux opened its new state-of-the-art filling plant for cylinder gases in Zwijndrecht. In one single weekend we moved from Machelen to Zwijndrecht without having any supply shortages. With a filling capacity around 500.000 cylinders a year for industrial and medical gases, our customer is sure about on time delivery.
Messer, a brand leader in the Benelux, knows that reliable services bring maximum comfort. We worked with our customers on cylinder management and we developed a unique barcode traceability system to find ‘lost’ cylinders. We can now all trace them, no matter who returns them and we deduct the cylinder from the correct customer’s stock.
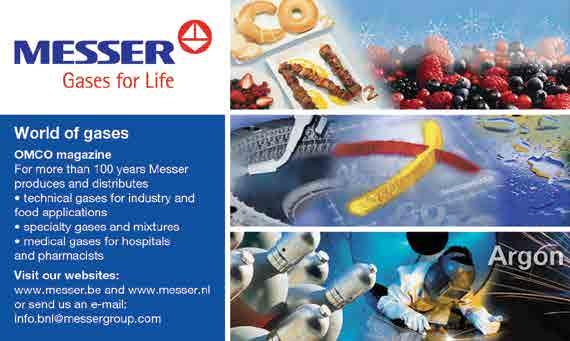

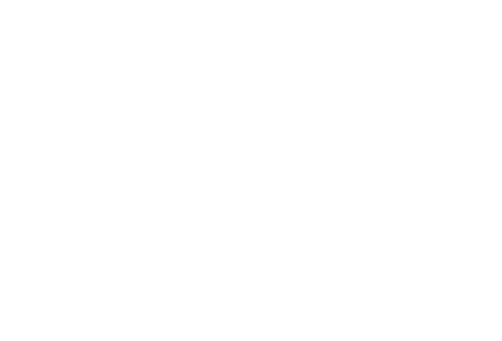
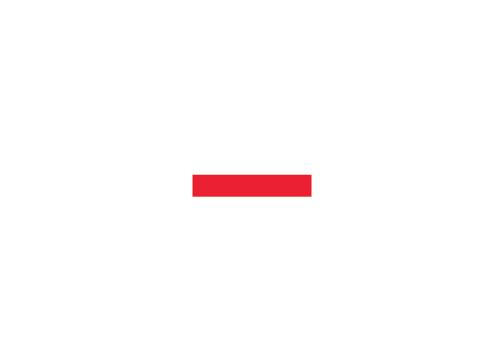
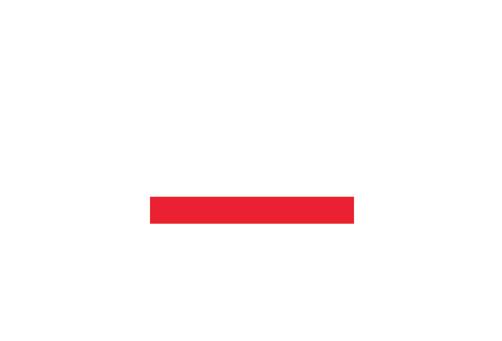
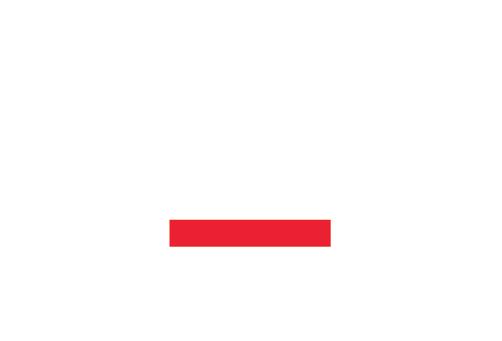

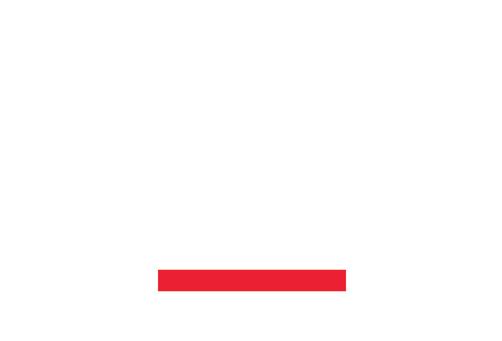