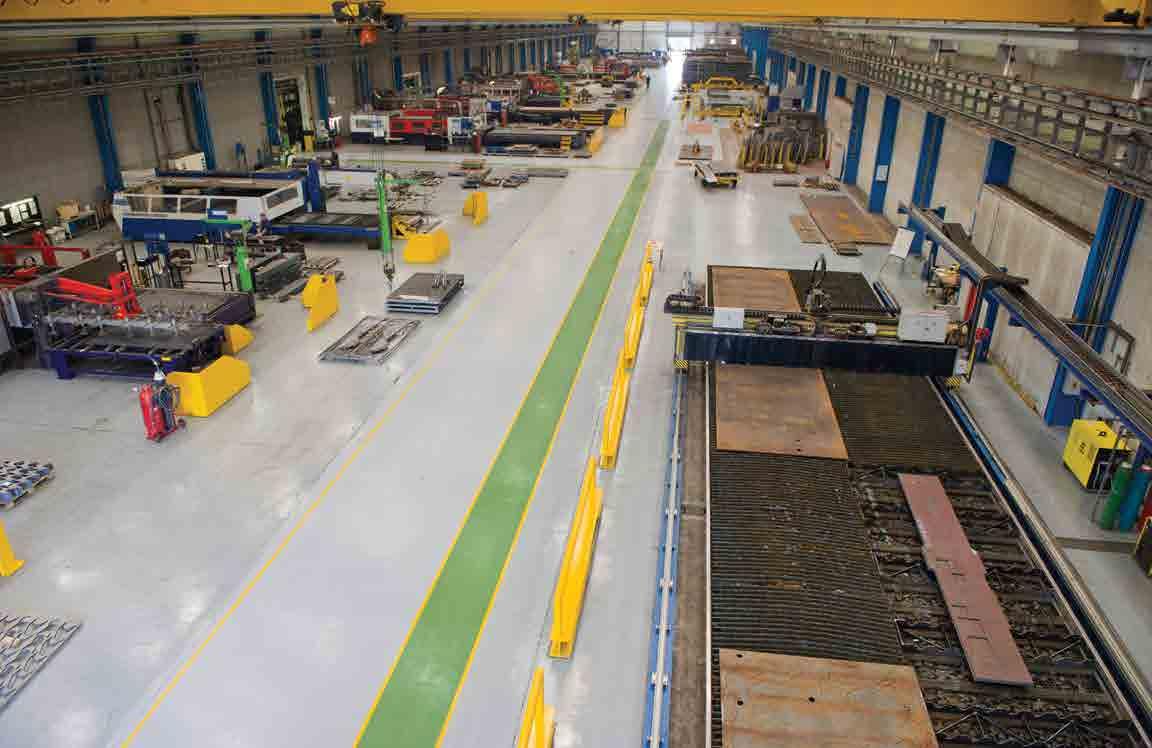
6 minute read
Global reach for design and manufacture
GLOBAL REACH FOR
DESIGN AND MANUFACTURE
Henry Shirman, managing director
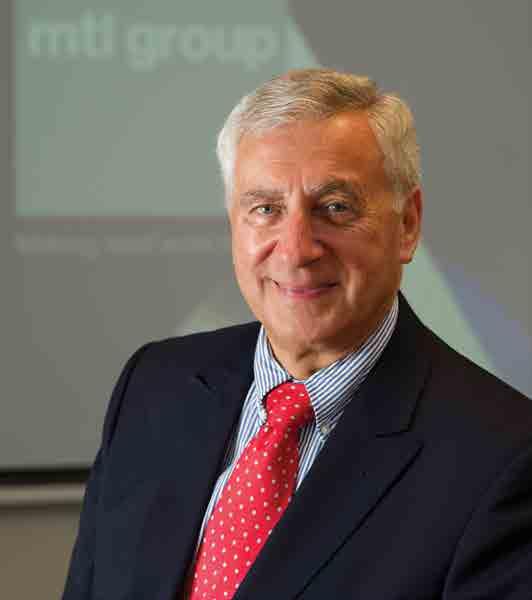

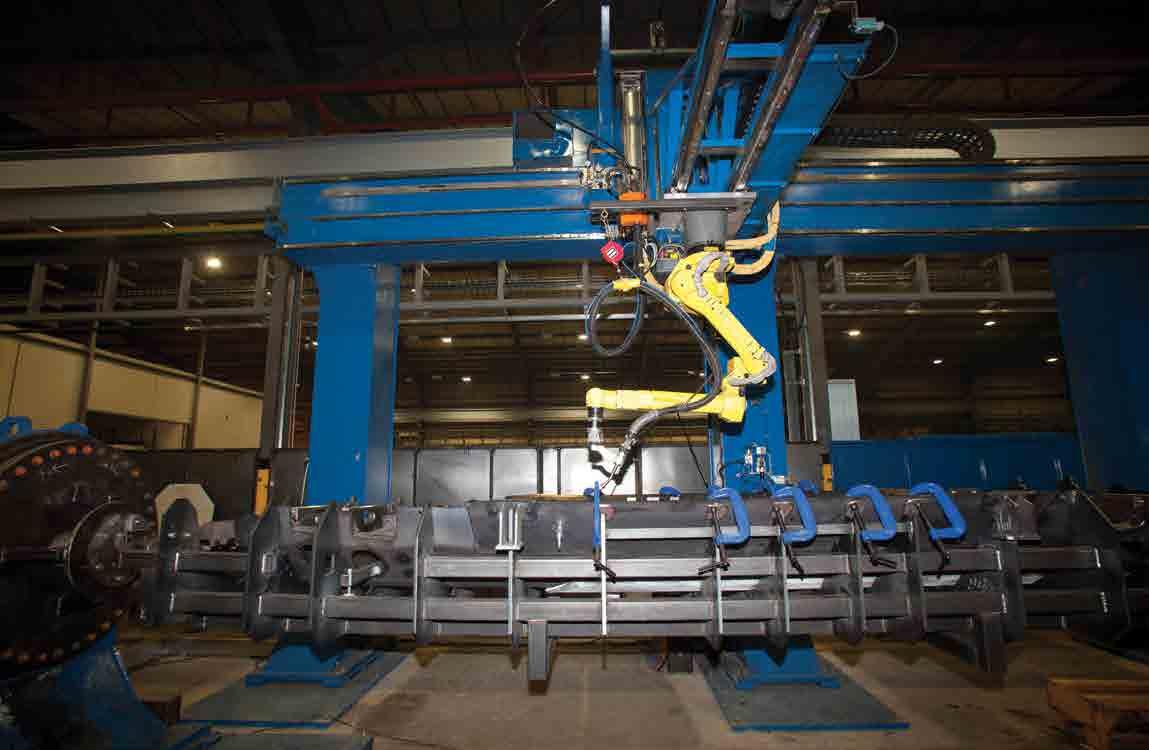
MTL Group is one of the fastest-growing manufacturing companies in Europe. Philip Yorke talked to Dr Henry Shirman, the company’s managing director about its latest technology and move into new market segments.
MTL Group is a leading UK contract manufacturing specialist in the metal sector. Since the company was founded in 1995 it has steadily grown to become the partner of choice for many of the world’s major OEM’s. The company’s head office is based in Rotherham, South Yorkshire, and occupies more than 28,000m2 of manufacturing space set in over 12.4 hectares of private land. At the company’s second major site in the UK at Blyth, Northumberland, dockside fabrication facilities are located in a modern assembly plant where the company is able to produce fabricated metal assemblies of up to 300 tonnes and ship them directly from the deepwater port of Blyth.
The core business sectors that MTL serves include the defence industry, recycling, construction, quarrying and mining equipment, rail and the fast-growing renewable energy industries.
Optimising steel fabrication technology
MTL has invested in eight high-tech laser cutting systems that combined have a capacity of over 1200 hours per week. The company’s wide range of state-of-the-art laser machines means that it is capable of handling every conceivable size and type of job, from carbon steels to aluminium, with around-the-clock working of 24 hours per day, seven days a week. The company’s recently installed Messer laser cutting machine is the largest of its type in the UK and capable of cutting both chamfers and weld preparations of up to +/- 50 degrees, which greatly enhances cutting efficiency and productivity. This in turn significantly reduces costs and lead-times for its customers. The new Messer machine can cut parts up to 20m long and 3.2m wide and up to 25mm thick.
“We have invested more than seven million pounds sterling recently in manufacturing equipment including the latest laser cutting technology, two new plasma cutting machines with large cutting beds and advanced bevel capability,” Dr Shirman said. “In addition, we have installed a robotic plasma tube-cutter which can cut tubes up to 40mm thick. This machine is supporting MTL’s recent success in winning several multi-million-pound contracts in Europe for offshore wind energy farms. This is in addition to installing the world’s most advanced water-jet cutting equipment and processes. Today, water-jet cutting is the fastest growing method of profiling. For example, when cutting armour plate, the material’s properties can be altered by the heat generated in the process, whereas with our water-jet technology there is no heat-affected zone. Furthermore, we have a large press brake, which provides more than 640 tonnes pressure and is serviced by a robot capable of lifting 600kg, which together form the largest installation of its type in the world.”
Taking a closer look at MTL’s advanced water-jet cutting machine, it is a four head, 12m x 3m Bystronic cutter and offers the most advanced and efficient operation of any water-jet cutter available on the market today. This unique machine is capable of cutting exceptionally thick materials of up to 200mm thick. In addition, it is able to cut through the hardest materials including armoured steel used on defence vehicles.
Adding value through Design for Manufacture
MTL’s Design for Manufacture service adds value to its customers’ relationships. MTL’s design and engineering division takes the OEMs concept and makes recommendations that will make the product lighter, stronger or reduce the cost of manufacture. MTL is working closely with several global armoured vehicle manufacturers to improve the design of vehicle floors. In one example the original design of the
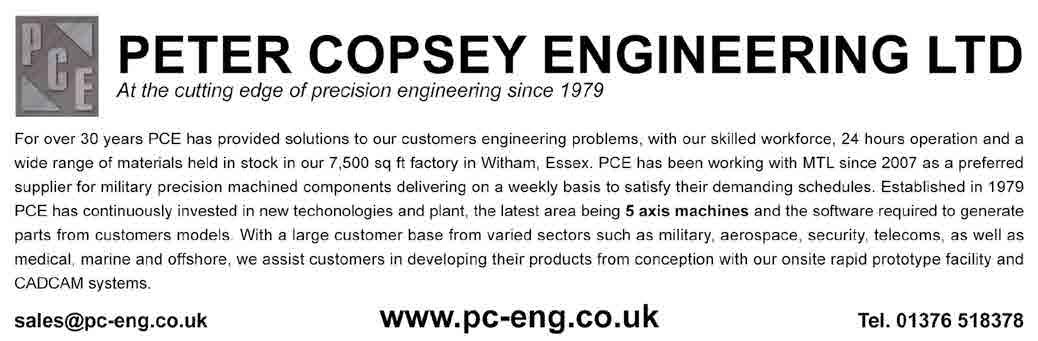

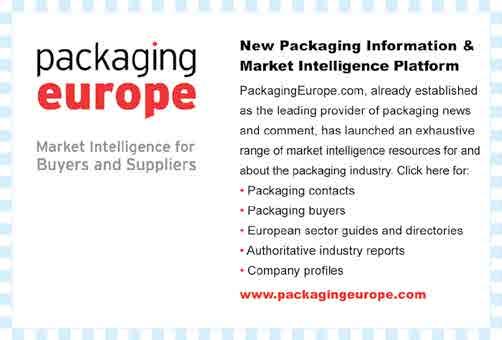
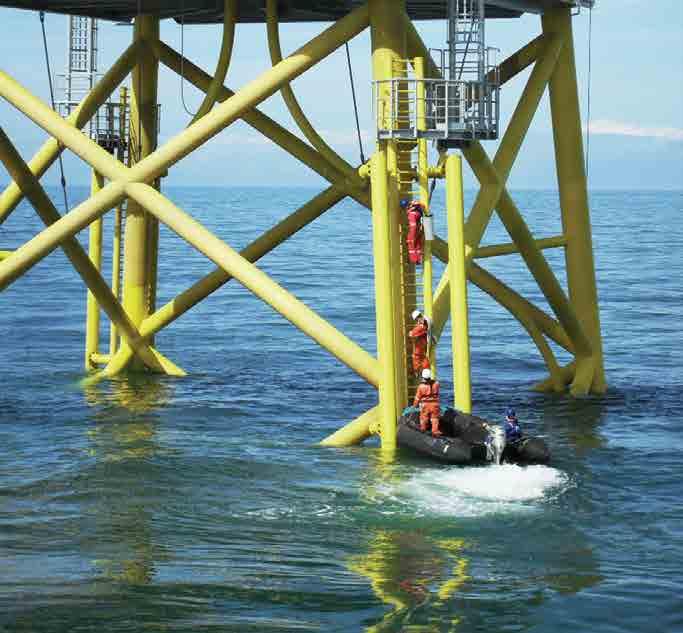
floor was made from 7 pieces and subsequently welded together; MTL’s Design for Manufacture review resulted in the floor being produced in one piece, eliminating the need for welding which reduced the cost whilst increasing the protection level of the armoured vehicle.
Expanding into new geographical market sectors
Traditionally, MTL’s most important market has been Europe. However, today the picture is changing and the company currently exports its products to over 35 countries worldwide. Dr Shirman added: “We are increasing the sales of our exports to the Middle East, the Far East, North America and South Africa. However, our focus is increasingly on the BRIC countries where we see a lot of potential in the future, especially in Brazil. As far as our future growth is concerned, we plan to maintain our strong track record in terms of both organic growth and through acquisitions where the appropriate synergies exist. We also intend to
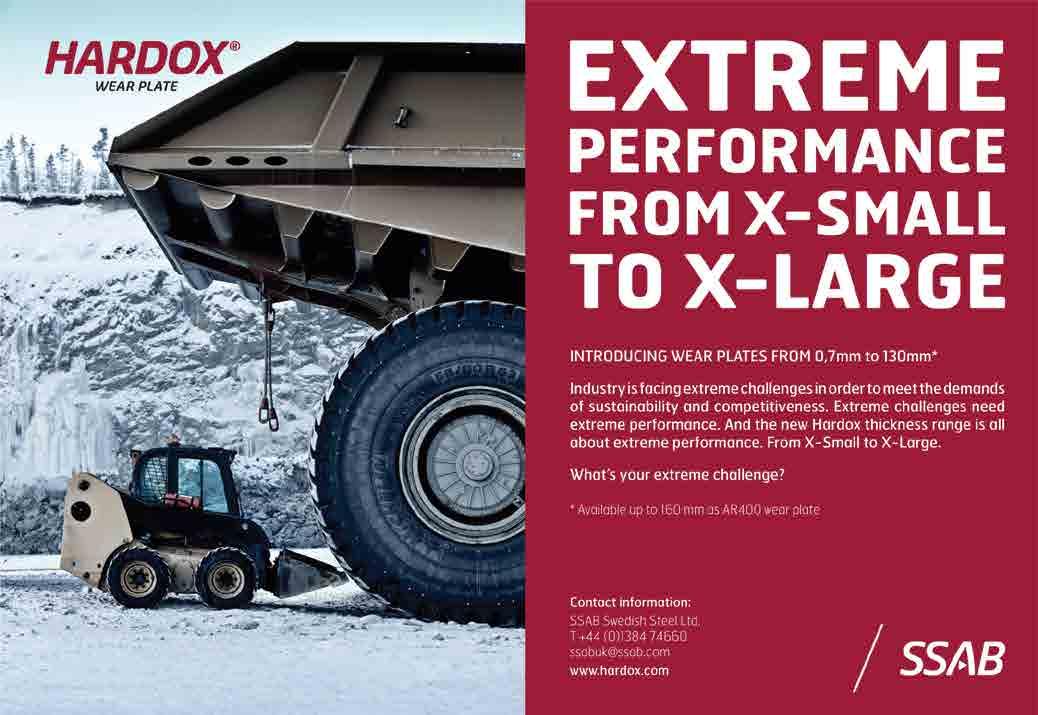
SSAB
SSAB has provided quality materials and service to the MTL Group for over 15 years. SSAB manufacture and supply world leading flat steel products. Hardox® wear plate, the world’s most specified wear resistant steel. Weldox® and Domex® high strength steels, used globally in applications which require increased strength or reduced weight.
Working together, both within the Hardox Wearparts network, and at the design stage with engineers and technicians, SSAB and MTL will continue to focus on ensuring that our customer’s end-products will be lighter, stronger and more sustainable than they would be by using standard materials. N&P Engineering Services Ltd specialise in the service, repair and installation of CNC machines and work in partnership with Ursviken Technology AB, within the UK and Europe. Our goal is to achieve 100% satisfaction, by providing a professional service that meets all our customer’s individual needs.

Visit us at www.np-engineering.co.uk or call us on +44 (0)1590 670850
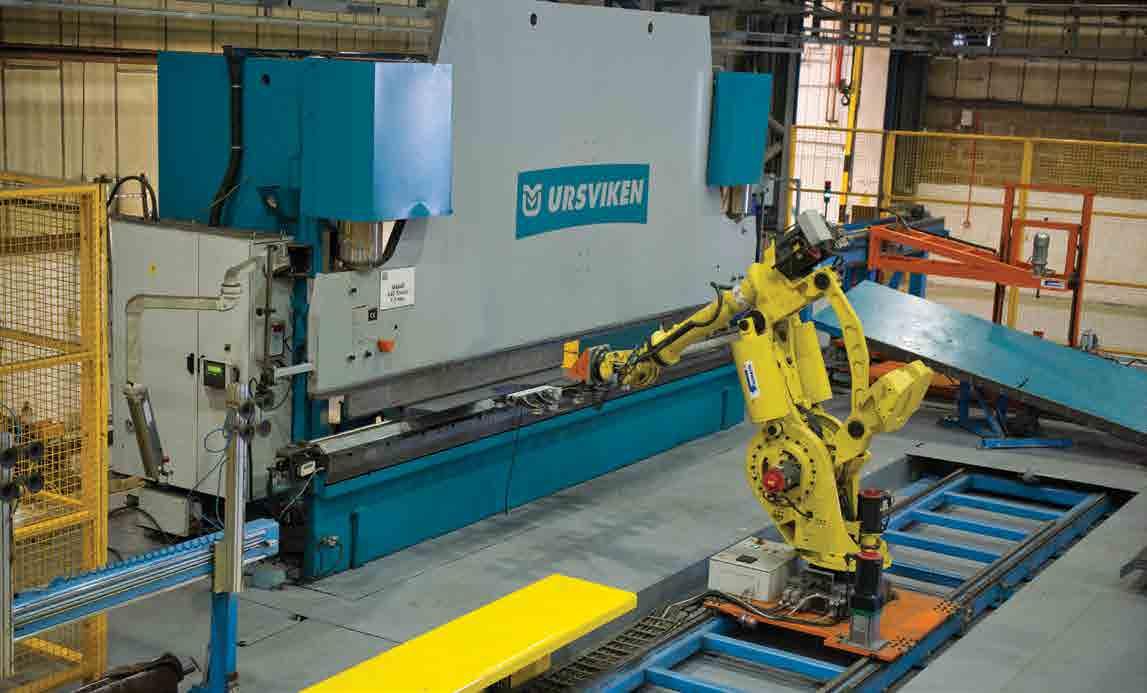
develop our global manufacturing footprint in other world regions. Looking to the future, we have also established our own welder training school and recently hired a further 17 apprentices who will complete a traditional three-year apprenticeship in conjunction with our local technical college.
“Today more than one third of our business comes from the defence sector with the balance evenly spread between the construction, renewable energy, quarrying and mining, recycling and rail industries. We see strong growth in power generation and are targeting the nuclear power and off-shore renewable energy sectors where we are now a global supplier of secondary steelwork.” Advancing armour-plate protection capabilities
As one of the world’s leading armour-plate protection specialists, MTL is pioneering new lightweight solutions for defence ministries. The company showcased its latest add-on armour products, which are branded ‘IMPAS LITE’ and IMPAS ADVANCE” at the AUSA Trade fair in Washington DC in the USA last year. The new IMPAS product stands for ‘Interchangeable Modular Perforated Armour System’ and offers a cost-effective, lightweight alternative solution to composite and ceramic add-on armours, with greater flexibility and better multi-hit outcomes. MTL’s defence sales manager, Simon Hurst said, “IMPAS is an innovative state-of-theart product which is ideal for both RHA and aluminium hulls. One of the key benefits is that the solution provides low-cost, lightweight armour that can be rapidly fitted to any vehicle platform.”
MTL’s armour plate stock is comprehensive and the company holds and processes more than 8000 tonnes of quenched and tempered steel every year. MTL is also one of Europe’s largest stockists and suppliers of armour-plate products. In addition, the MTL Group specialises in the supply of components for blast applications that range from cut and formed parts, up to fully finished fabricated vehicles. n

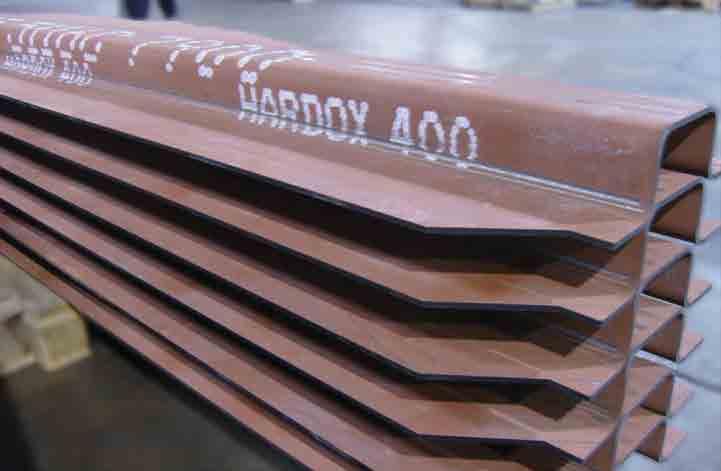