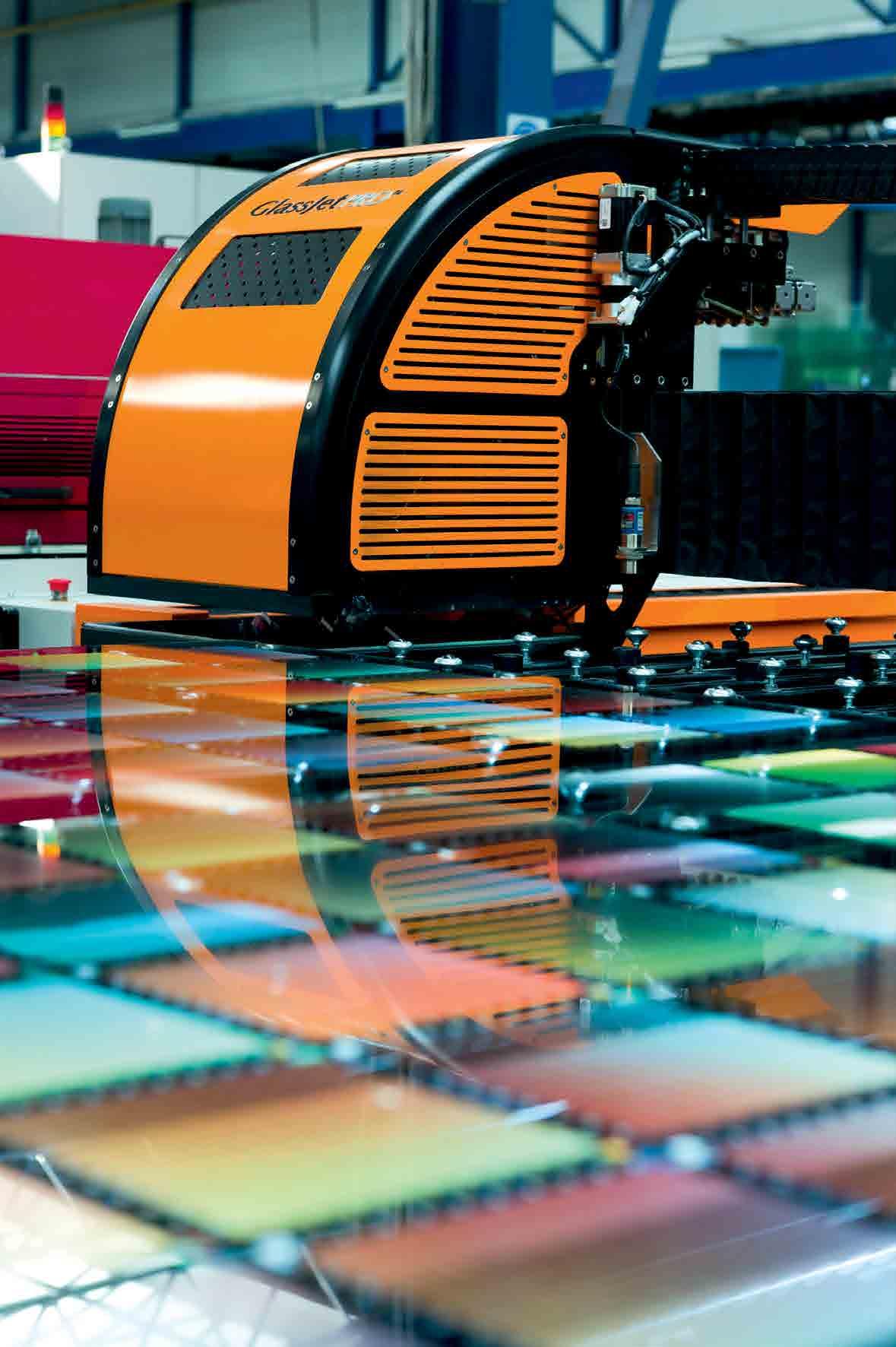
8 minute read
Top class glass PRESS GLASS
TOP CLASS GLASS
The Polish independent company PRESS GLASS is regarded often as Europe’s leading producer of processed glass for the construction industry. The company’s glass is an essential element of many residential and striking public buildings in Poland as well in Scandinavia and other European countries. Joseph Altham spoke to Gerard Plaze, Promotions Manager at PRESS GLASS, to find out about the company’s new products and the investments it is making to expand its newest factory in Poland near Łódź.
Since its foundation in 1991, PRESS GLASS has experienced extraordinarily dynamic growth. Today, there are more than 1500 people working for PRESS GLASS, and the company’s glass can be found in many landmark buildings in Poland including the Intercontinental Hotel in Warsaw and the Sky Tower in Wrocław. Its glass is also found in many buildings in Europe, including the Lietuvos Nergija and Grand Casino in Lithuania, the Department of Defence and Head Office of Public Works Department in Ireland, the Halmstad Arena in Sweden and many others.
The headquarters of PRESS GLASS is located in Nowa Wieś near Częstochowa, in the south of Poland. PRESS GLASS carries out its manufacturing in four highly efficient factories located in Poland with a total area of almost 70,000m2, using up to 15 assembly lines and five toughening furnaces. Its factory in Tychy, near Katowice, specialises in the production of toughened, laminated, machined glass and units for building façades. At its factories in Nowa Wieś and Tczew near Gdańsk, it mostly produces glass units for residential purposes
“This factory, near Gdańsk, was developed in 2004 to bring us closer to our markets in the Scandinavian countries,” stated Mr Plaze. Its newest company factory was built in 2008 in Radomsko near Łódź. PRESS GLASS is now expanding this factory, and, when completed in 2012, the Radomsko production site will be the biggest factory in Europe processing glass for the construction industry, covering an area of 30,000m2. “Our size is important, because it enables us to meet the growing volume and expectations of our clients related to it. But size is only one of the most important considerations, alongside technological supremacy, a wide range of products, Europe-wide certification and individual logistics systems. Ultimately, our size is a reflection of our history and the growth we have achieved by delivering a good service to our customers.” New releases

PRESS GLASS has developed a wide range of products in order to meet the varied needs of the construction industry. The company offers many types of glazed units (glass panes), even up to 3x6m in size, together with 8x6m standard toughened glass which is machined for both the exterior and interior of buildings. PRESS GLASS continues to update its range and has just brought out an improved version of its edge of glass unit, called Premium Edge. “Premium Edge provides the warmest possible insulation and can be used both in residential buildings and for the façades. Premium Edge has three insulating layers and spacer a made of silicone foam. Together with another product, combined stainless steel and the plastic Chromatech Ultra spacerbar, they are a very interesting offer in the Warm Edge category.”
In the last couple of years, PRESS GLASS has introduced several interesting additions to its special glass range. With a state-of-theart Benteler glass laminating line and Scholz autoclave, the company can produce layered panes in-house. “Often the standard offering in laminated glass is quite narrow, based on float glass. This machinery, installed in 2009, allows us to connect different types of glass, such as toughened , ornament or solar control
Premium Toughened glass furnace Heat soak test for toughened glass Sky Tower
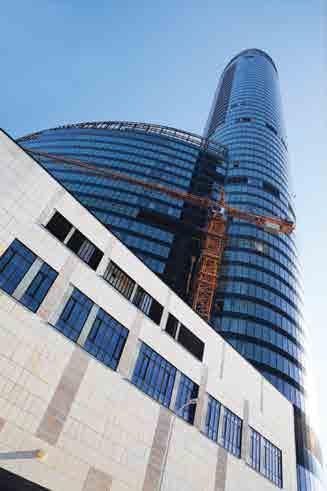
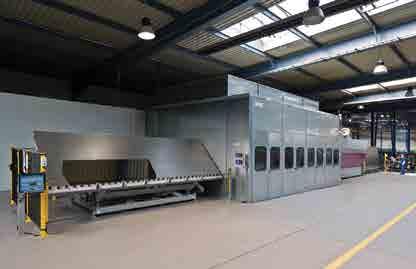


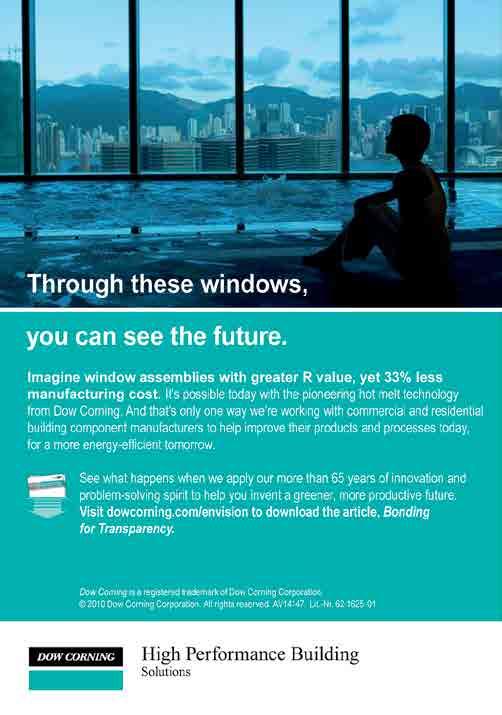
Dow Corning
Dow Corning is collaborating with industry professionals around the world to develop solutions to improve the energy efficiency of buildings, reduce the ecofootprint of construction materials, and improve the health and safety of building occupants. Taking a holistic approach, Dow Corning brings together expertise from across the company to help customers find solutions to a wide range of high performance building challenges. Dow Corning High Performance Building Solutions include proven materials for structural and protective glazing, weatherproofing, insulating glass, window and door fabrication, and building materials protection, as well as innovations for high-efficiency insulation, LED lighting, thermal management systems, and the incorporation of photovoltaic cells and solar panels into building design.
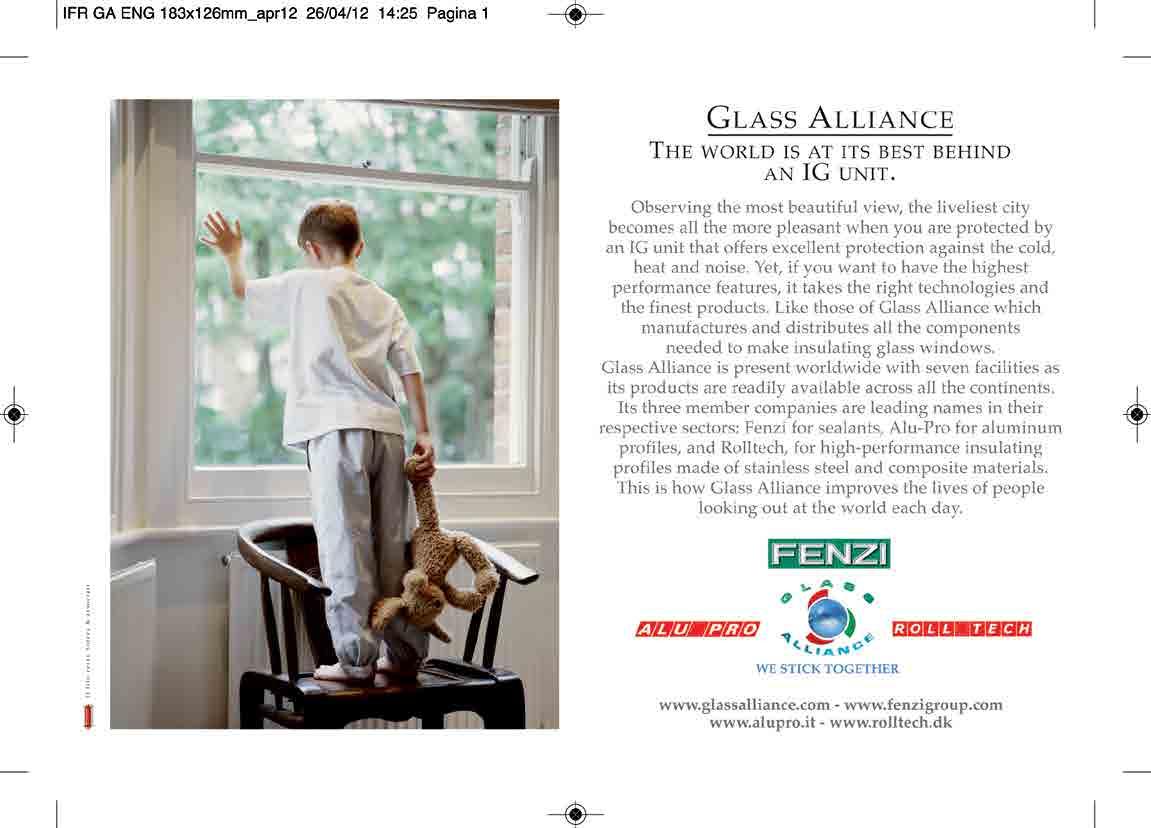

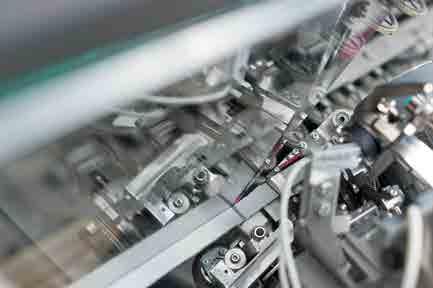
glass to the laminated glass with PVB, sound control and colour foils, for applications including balconies or glass partitions, glass beams, columns or staircases and floors.”
Premium Toughened Glass and Digital Print
While strength and durability are important attributes of the company’s toughened glass, architects also require an attractive visual effect. In 2010, PRESS GLASS therefore introduced its Premium Toughened glass, designed for the façades of buildings. The Premium Toughened glass was developed to avoid the problem of ‘roller waves’, which create a distorted reflection in the glass. The roller wave effect is the result of the way toughened glass was traditionally produced, using rollers in the furnace. To solve this problem, PRESS GLASS makes the glass using a kind of air bag method, on which the glass is positioned at an angle in a furnace. The rollers will then only touch the panel on one cut edge, so that no waviness will be visible once the glass is used on the exterior of a building.
PRESS GLASS also makes glass that can be digitally printed. The company’s Digital Print glass, introduced in 2011, is ideally suited for displaying individually created projects on the internal or external walls of a company’s office. “The process for printing is made in three short steps,” said Mr Plaze. “Once we receive the photo, we can prepare the digital graphic file, then print the image onto the glass and preserve in a toughening furnace. With Digital Print, no additional processes are needed. This avoids extra costs for the customer related to the preparation of printing sieves and ensures the job can be done really quickly.”
Prospects
The new production hall for the factory at Radomsko is scheduled for completion by the summer of 2012. This was a substantial investment decision, particularly in last year’s European economic conditions, but PRESS GLASS believes its confidence is justified. “In this factory we are now installing a continuous toughening furnace. Its main task is to render toughened glass production more efficient and prepare us for big volume orders from both solar and construction branches. Of course, further assembling and machining lines are also scheduled for installation in Radomsko.
“Our main goal is to develop by cooperation with demanding companies and strengthening their brands and market position thanks to fulfilling their requirements.
“We still see possibilities for development in Europe. Scandinavian markets are very important for us, because they are major producers of windows in Europe, and we do our best to serve them perfectly. In Scandinavia and other European countries there is still also a lot of investment in public buildings, which need glass façades. We are able to serve even the biggest ones, as can be seen from our most recently completed project, the Sky Tower in Wrocław, where Premium Toughened glass was used.
“The Polish window producers can also develop thanks to serving new markets in Europe. We make it easier thanks to giving them certification matching national standards of a number of European countries. We also continue to increase our exports to other European countries for windows and façade producers and, thanks to our implementation of new products, we are also serving new client groups such as solar panel producers. We try to be as green as possible in terms of our products and the production technologies we use.” n
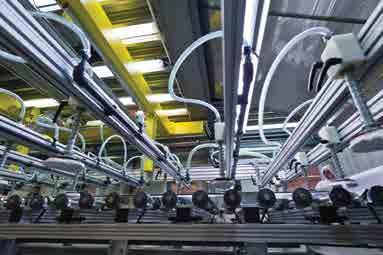
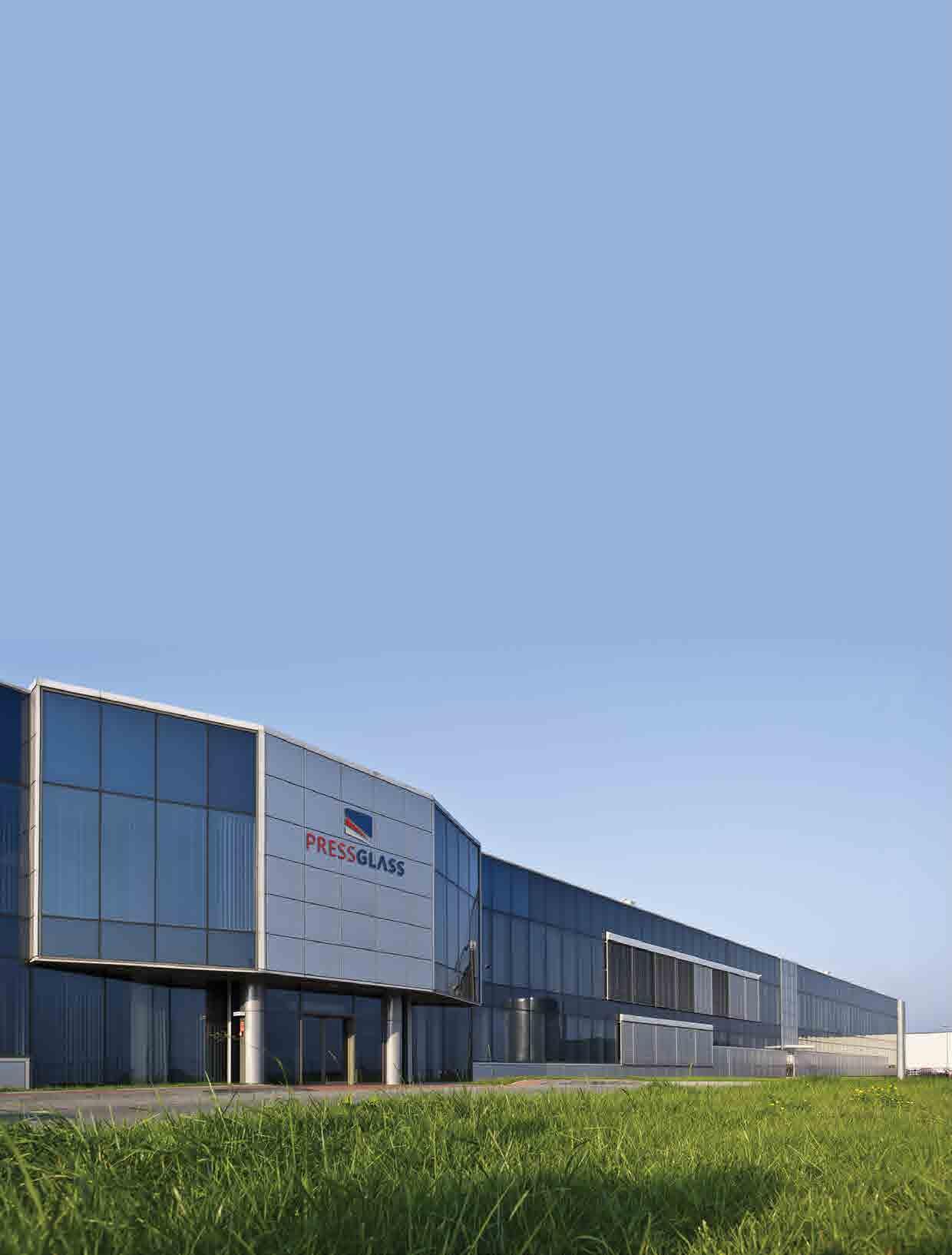
Factory in Radomsko
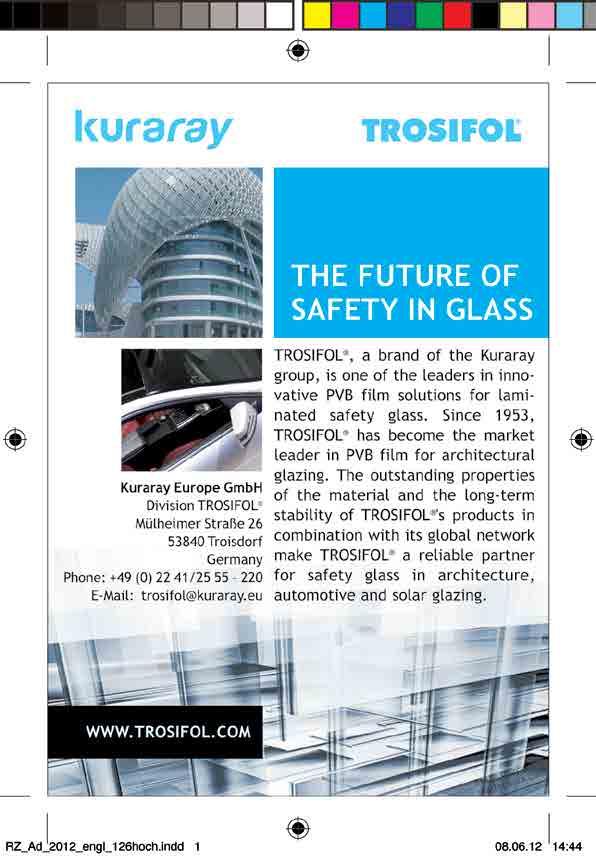
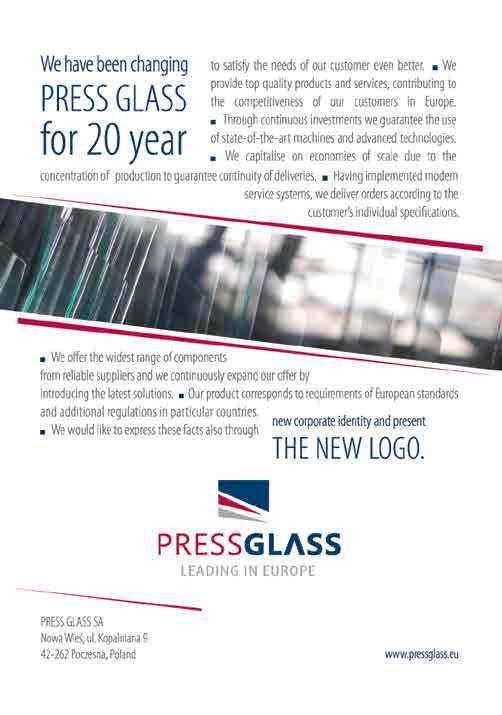
Sikasil® IG-25 HM Plus - Lowest Argon Loss Rates
Argon-filled IG units have not been used in SG facades for many years. Hence structural facades were supposed to be banned for colder climates, due to ever stricter energy saving regulations. With the development of the high-modulus IG secondary edge seal Sikasil® IG-25 HM Plus the glass panes in IG units are very tightly held together. Movements in the butyl layers, caused by temperature and pressure changes, are minimised. As a consequence leakages in the butyl primary seal, the main barriers against argon penetration, are prevented. In tests complying with the European IG standard EN 1279-3 the best test units have proven an annual argon loss rate as low as 0.3%. The maximal limit in the standard is set with 1% per year.
Kuraray
Kuraray Europe’s brand TROSIFOL is one of the leading manufacturers of PVB film for laminated safety glass worldwide. TROSIFOL products are mainly used in applications for automotive and architectural glazing, special TROSIFOL films are used in PV modules.
TROSIFOL operates its headquarters in Troisdorf (Cologne/Germany) and an additional plant in Nishny Novgorod, Russia. There are marketing subsidiaries in the United States, Malaysia, India, China and Ukraine. The Kuraray Europe GmbH namely TROSIFOL congratulates his valued customer Press-Glas on his prominent reference – Sky Tower in Wrocław, the highest building in Poland. We are very happy to supply such a competent company like Press-Glas with our TROSIFOL PVB film.
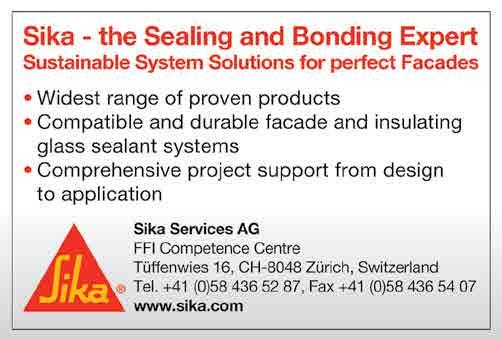