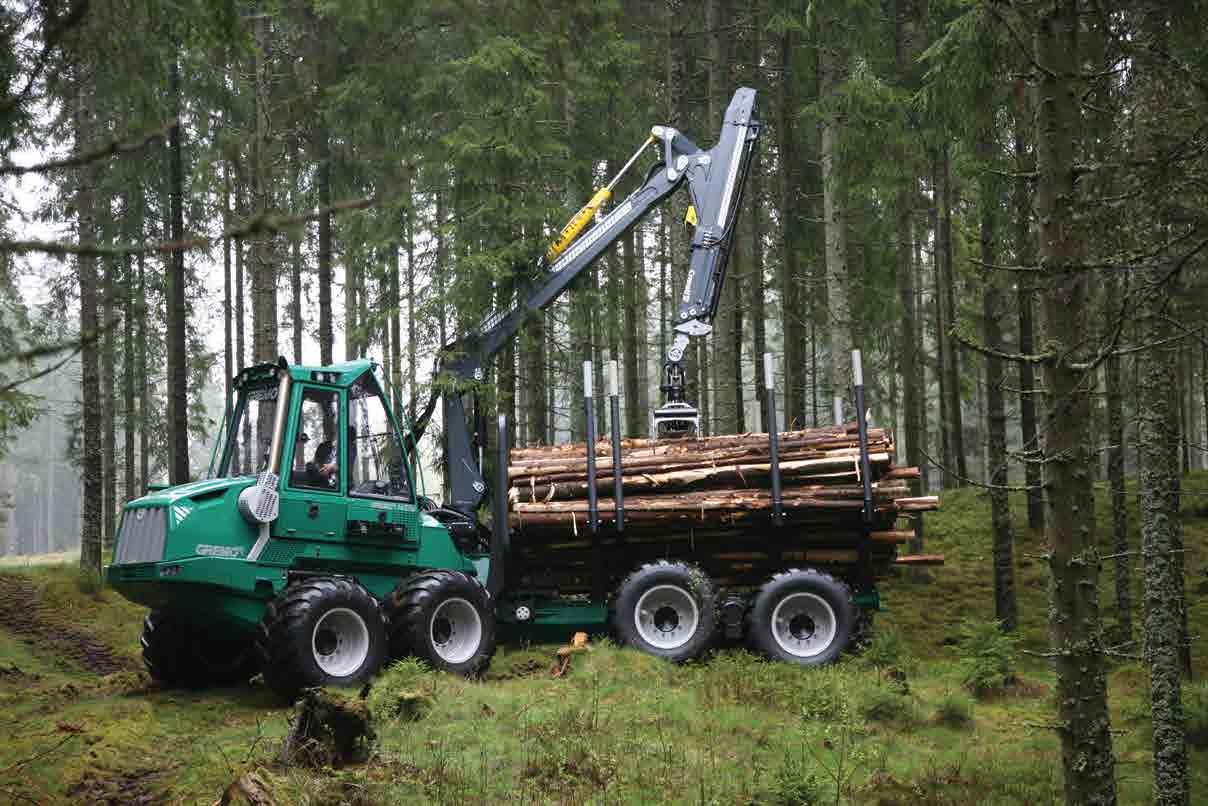
4 minute read
Innovations in high strength steel
‘Forwarder 1450 F’ - Gremo AB - Sweden
The winner of the 2012 SSAB Swedish Steel Prize will be announced on November 15. Four finalists have been nominated for the prize for leading designs in high strength steel. The jury has chosen innovations for the packaging and transportation of metallic scrap, light and sustainable train seats, a truck suspension system, and a forwarder – a light timber transportation vehicle.
The Swedish Steel Prize is awarded for innovative designs made of high strength steels. The prize is intended to inspire, stimulate and disseminate knowledge about high strength steels and the possibilities they offer to develop lighter, safer and more environmentally-friendly products.
“The quality has been consistently high and it has been a difficult task for the jury to select the four nominees. The large number of applications from 26 countries demonstrates the high level of interest in high strength steels,” says jury chairman KG Ramström, chief technical officer, SSAB.
Recycling, which involves the use and transportation of metallic scrap, is extremely important from an environmental perspective. A-ward has designed a flexible and innovative system comprising two units made of high strength steel which compress and pack metallic scrap in containers.
Unsorted scrap is fed in at one end by the equipment and compacted scrap is injected directly into a container in the other, which provides for rapid and efficient loading of scrap. This results in increased profitability.
This is an elegant and innovative system solution for scrap compacting and loading of unsorted scrap in a way which is efficient
Scrap handling system ‘Mi-slide’ - A-Ward Attachments Ltd - New Zealand
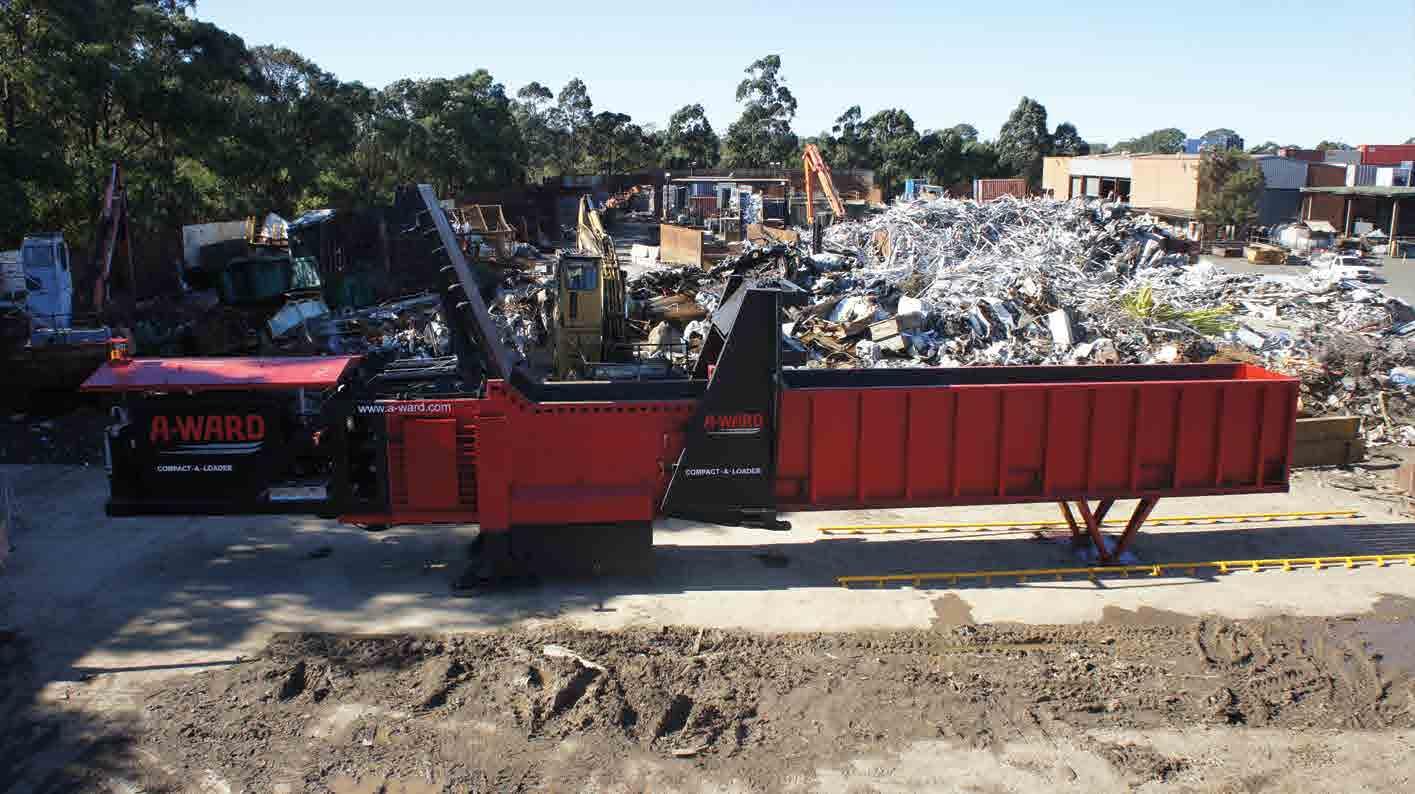
and avoids causing damage to containers. Loading takes place without knocks from falling scrap, which eliminates the risk of buckling and abnormally high wear and tear on the containers.
Hardox 450 and 550 high strength steels have been used in the design.
Light train seats ‘Regio and Regio+’ – Borcad CZ s.r.o – Czech Republic
Borcad, which enjoys a strong position on the market for light train seats, has developed the next generation of train seats through a smart design.
Through optimal use of high strength steel – SSAB’s Docol 1200 M steel – the weight has been reduced by a further 25 per cent. Reduced weight is especially important for commuter trains, which brake and accelerate very often, since it results in lower energy consumption and faster acceleration.
The new design offers improved safety for the head, knee and neck in the event of a collision. The high strength of the steel also provides protection against damage due to vandalism.
Borcad has just secured an order for the new seats for 15 three-carriage trains.
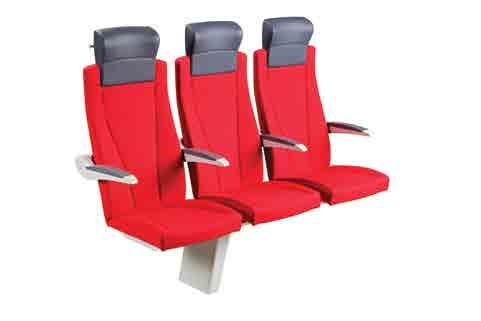
Within the forestry industry, the need for forestry thinning equipment is increasing. A forwarder is a vehicle which transports timber from the logging site to the road. Gremo has produced a carefully conceived and optimised new design which efficiently utilises high strength steel. The 15 per cent reduction in chassis weight leads to lower fuel consumption relative to payload. The forwarder’s chassis has been designed for increased torsional stiffness, thereby improving off-road performance, and the engine’s emission control is in accordance with the most recent EU directives
Manufacturing benefits of the optimised design include approximately 30 per cent lower production costs in the form of fewer steel sections, less welding, and a simpler revolving crane base in the mid-section.
SSAB’s Domex 700, Weldox 700 and Hardox 450 steels are used in this design.
Back axle suspension ‘Twin Y suspension’ – Volvo Group Trucks – USA
Volvo Truck Group has produced a new back axle suspension system which resolves a sustainability problem, while at the same time achieving other benefits. Compared with the previous solution, which most truck manufacturers have been using for decades, the new design leads to a 25 per cent reduction in tyre wear. This reduced tyre wear entails major savings for the end user. Calculations show that the owner saves approximately SEK 200,000 over the life of the vehicle, which in light of US production of 30,000 trucks per year corresponds to SEK 6 billion. This is in addition to lower production costs, increased safety and comfort for the truck driver.
The solution means that a tensile problem (suspension fatigue) has been resolved, at the same time as achieving appreciable improvements in other areas. The design demonstrates that a well-known solution can be improved so much as to have a major impact on the entire application. A patent has been sought for the solution.
The Swedish Steel Prize will be awarded on November 15 at Münchenbryggeriet in Stockholm. The winner will receive an award of SEK 100,000 and a statuette. The prize ceremony will conclude with a two-day event in Sweden at which hundreds of international representatives from the engineering and industrial sectors will participate in plant visits and seminars. SSAB established the Swedish Steel Prize in 1999. n
www.ssab.com