
4 minute read
Clean, lean, power machine Budapest Power Plant
CLEAN, LEAN,
POWER MACHINE
Budapest Power Plant (BERT), a member of the EDF group, is the largest cogeneration power plant company in Hungary. A recent development which aimed at increasing efficiency and protecting the environment enabled the Kelenföld power station to continue to supply the capital’s district heating efficiently in the long term.

BERT operates four plants in Budapest and its past connects closely to the history of the capital. The Újpest, Kelenföld and Kispest plants use combined cycle production technology to provide heating energy and electricity. The fourth plant is the Révész heating plant, which operates hot water boilers to provide a district heating supply. BERT currently provides 60 per cent of the district heating energy demand in Budapest, and supplies 3 per cent of national electricity consumption.
The power station in Kelenföld is one of Hungary’s most distinguished establishments, where energy production began in the 1910s. The plant contains a number of listed buildings which are well maintained ensuring that a piece of industrial building inheritance is preserved for the nation. The antique exterior however hides a modern and environmentally friendly technology due to the many developments completed over several phases in the past years. Mr Zoltan Szabó, project manager at BERT, recalls: “The redevelopment of the Kelenföld power station was quite a bizarre thought at first: Let’s ruin the performance capability of the gas turbine that is actually the ‘soul’ of the power station. How is that?” High efficiency, low emissions
“In order to answer this question, we have to know a little bit more about the firing technology of the gas turbines. The burning of the firing material including natural gas or light oil happens in the gas turbine. In case of traditional firing equipment, the amount of nitrogen oxide that is released during the firing process is reduced by steam injections whilst keeping the firing temperature under control. Because we are talking about significant amount of firing material (41,000 Nm3/h), the amount of steam injected is also significant (40t/h). The injected steam in the gas turbine works to lower efficiency,
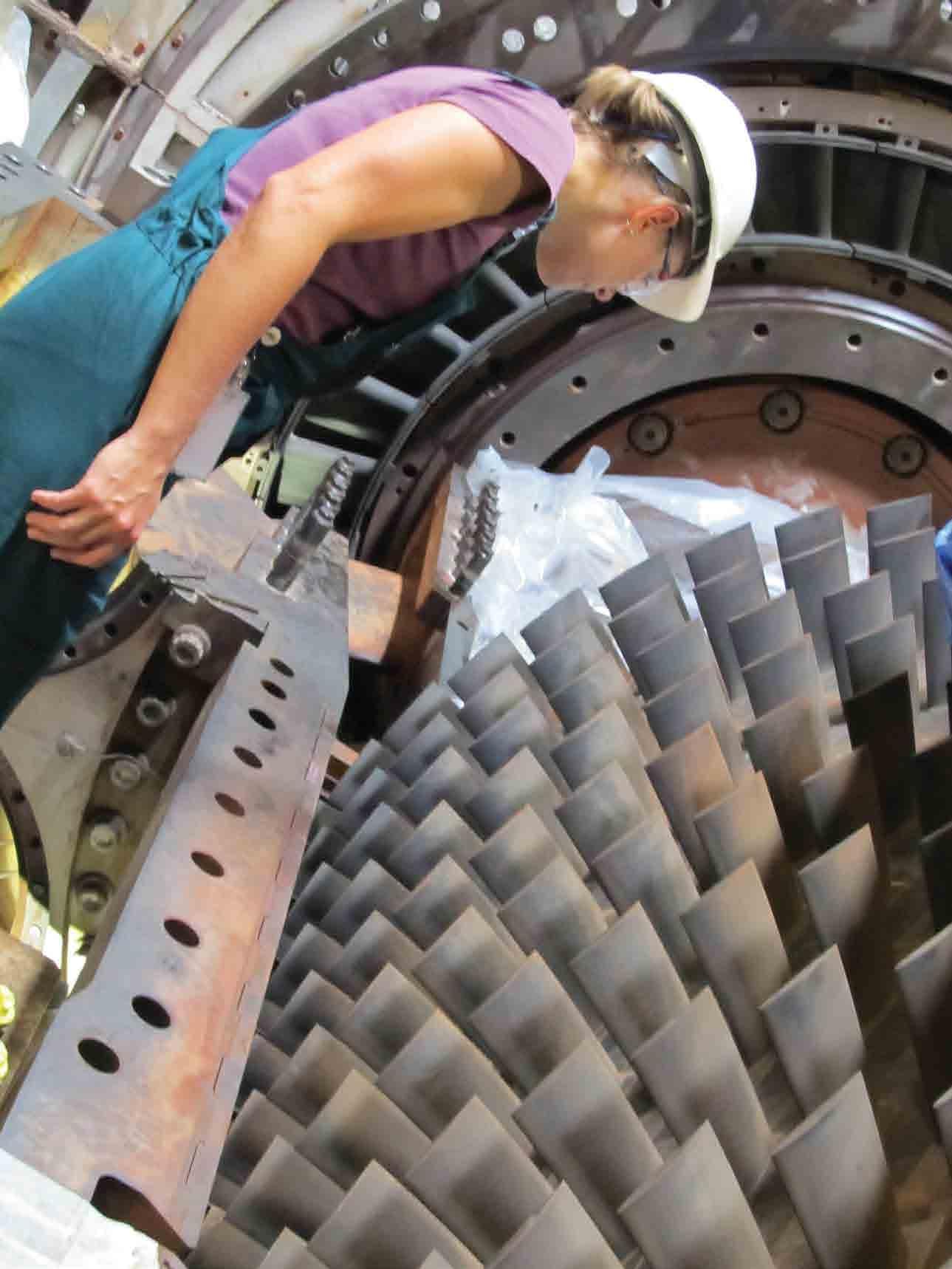
The investment in figures:
The total cost of the investment: €14 million Duration time: 11 months production and 4 months implementation Electric performance increase: 3 per cent CO2 emission reduction: 14 per cent NOx emission reduction: 29 per cent Water use reduction: 150 000 m3/year
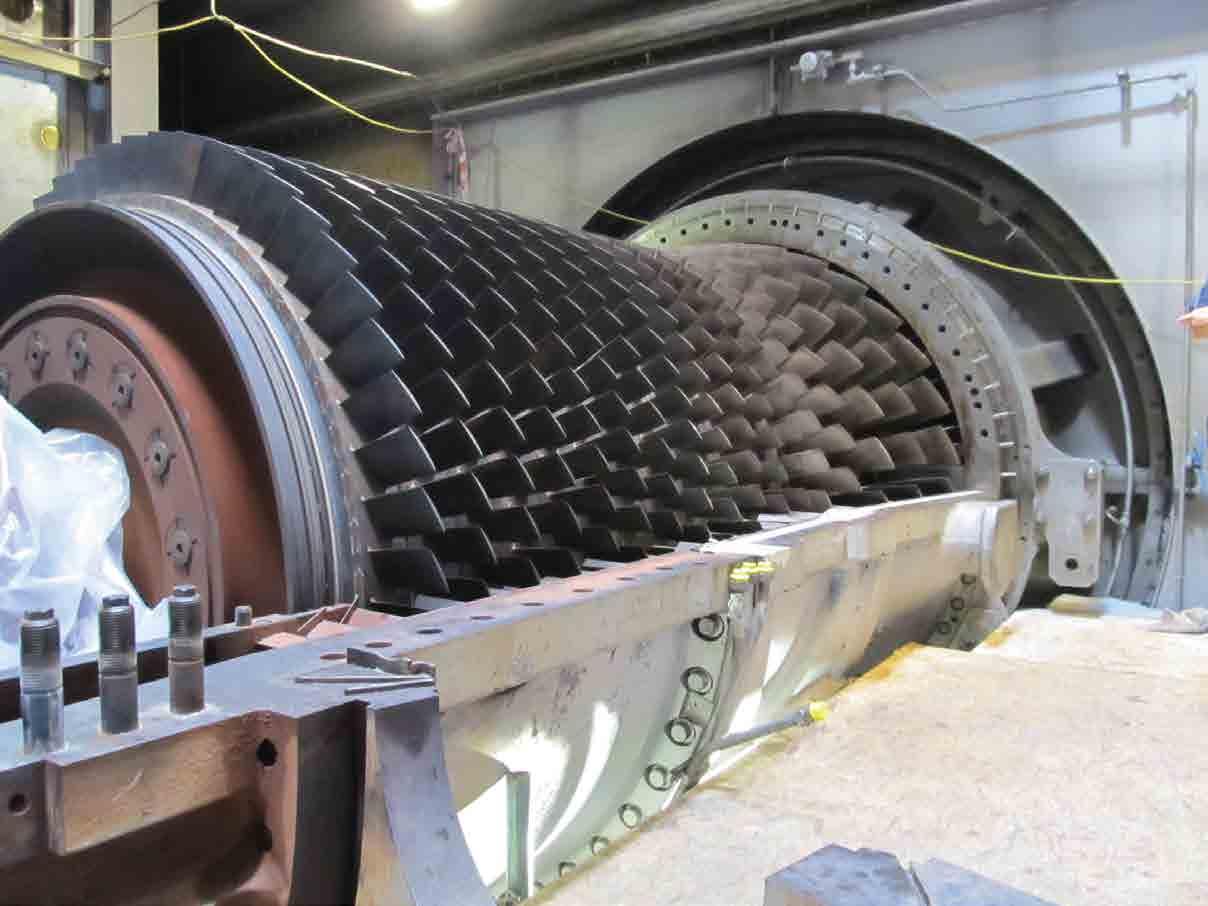
but afterwards, together with the flue gas, it goes to the open air as vapour through the chimney of the heat furnace.
“Today – due to the systematic development process – the dry, low-NOx (DLN) type firing equipment implemented with the necessary geometric requirements and by premixing firing material-air, will be able to keep the NOx and CO2 emission within the limit values. The released steam can work with high efficiency on the steam turbine so that we achieve a positive effect in the power station.
“The results of this are diverse: the electrical and thermic efficiency of the power station increases whilst saving primer energy; the specific harmful material emission reduces significantly; the maintenance cycle of the gas turbine increases resulting in smaller maintenance cost and the flexibility and reliability of the plant also increases.”
The development of the Kelenföld power station was carried out by the company’s own project team following a 1.5 year preparation process. The task to replace the gas turbine firing equipment was delegated to a main contractor, whilst all the complementary jobs including acquiring the necessary permis-
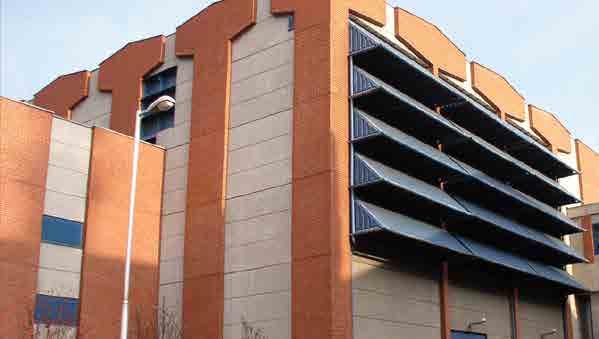
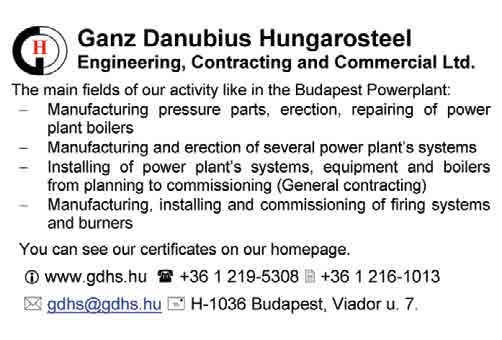
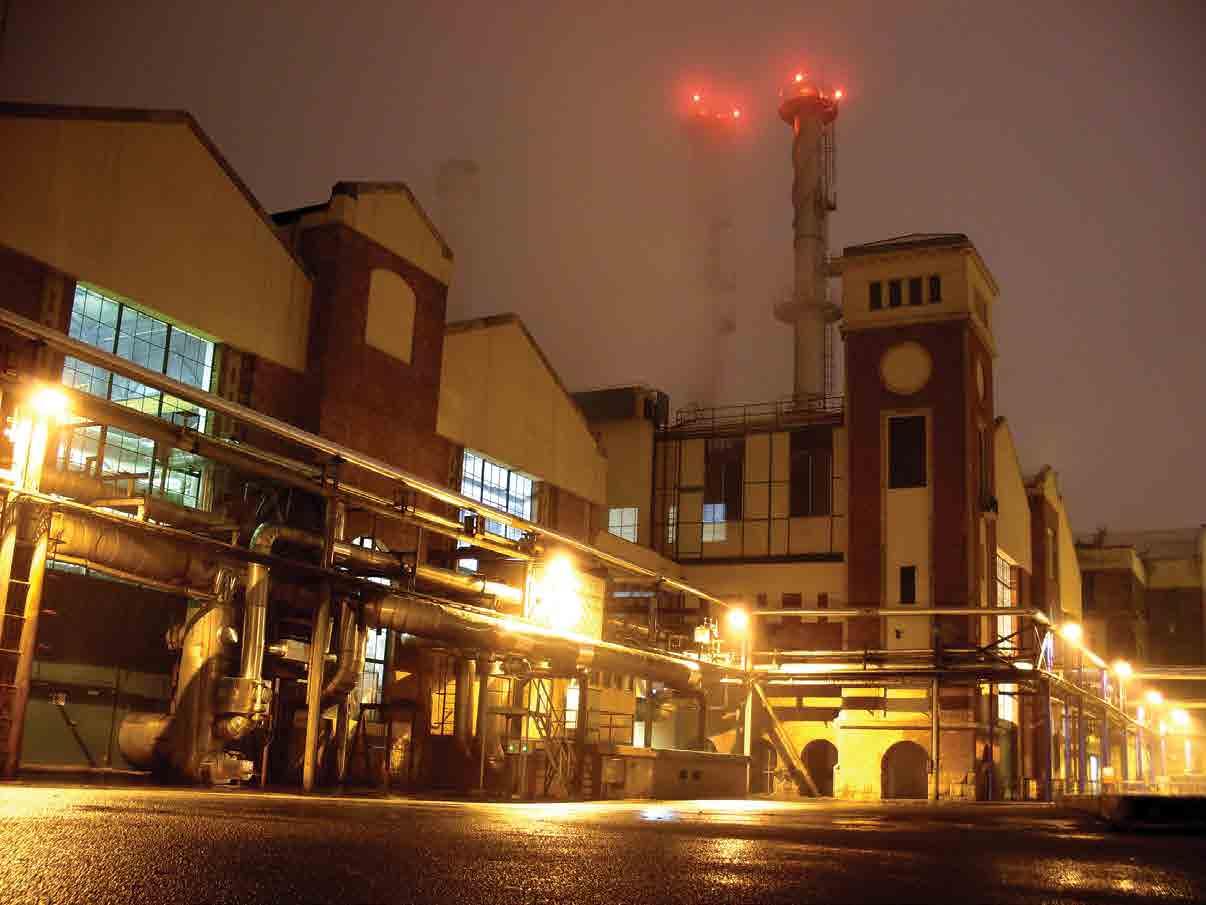
sions, implementing piping systems and the construction tasks were taken care of by sub-contractors. During the development the safe completion of the site was a major issue, all parties involved provided extra attention to safety and therefore the project was completed without accidents or related safety issues. The performance measures carried out during the testing period confirmed that the company achieved the expected results; in fact they exceeded those in some parameters.
Some of the buildings owned and operated by Budapest Power Plant may look as though they belong to another century but look deeper and you find state-of-theart equipment producing 60 per cent of the power for the city of Budapest. Meeting the challenges of producing the essential power and warmth requirements for a major capital city requires a business that is prepared to adapt to changing requests from customers, changing legislation and changing technology. BERT not only meets that challenge but embraces it, proudly preserving its past whilst developing its future with technology to meet the requirements of the 21st century. n
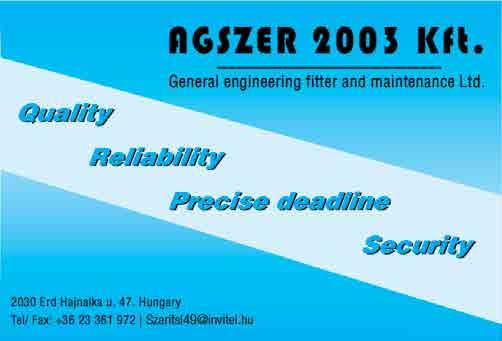
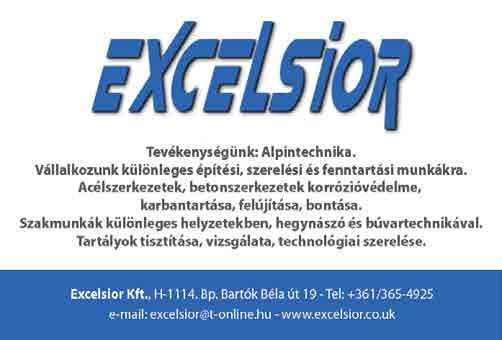
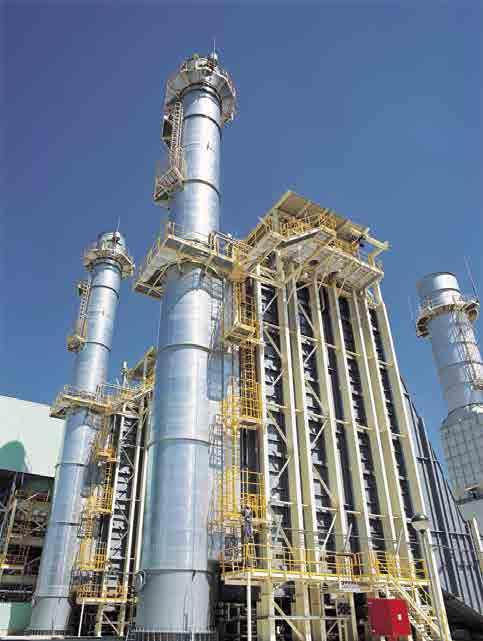

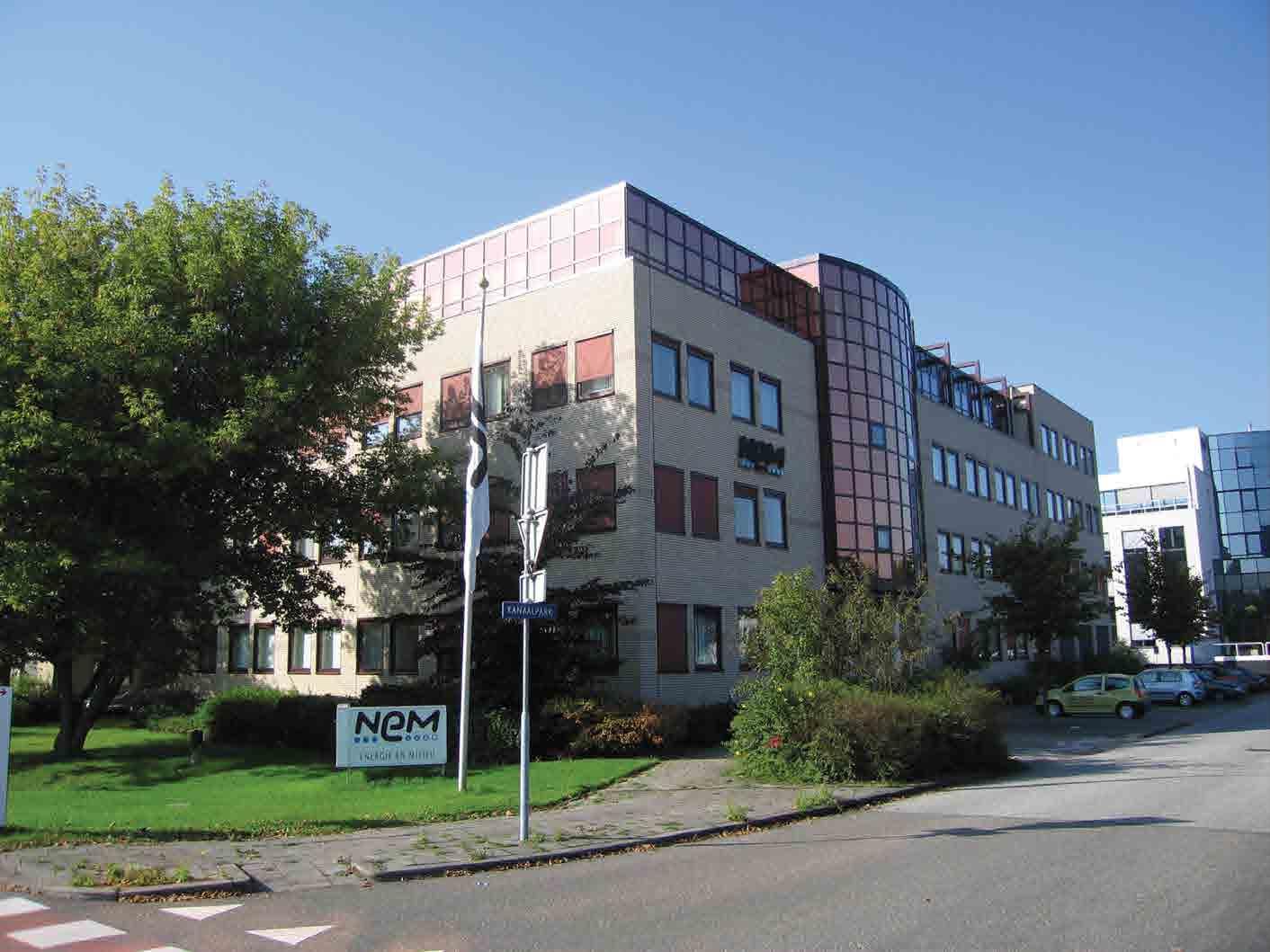