
4 minute read
Nordic Brass Nordic Brass

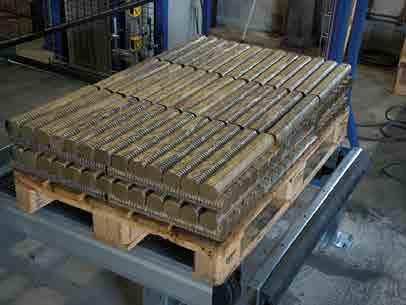
NORDIC BRASS
Nordic Brass is a leading manufacturer and supplier of high-quality brass products. Philip Yorke talked to Tommy Werlefors, the company’s CEO, about its unique structure, flexible manufacturing facilities and its move into new market segments.
Nordic Brass Gusum is one of the longestestablished smelting companies in Scandinavia with its origins in brass manufacturing dating back to 1607. That was the year when one of the original companies, Skultuna Messingsbruk, was founded. Nordic’s other founding company, Gusums Bruk, was also established in Sweden in 1653. These companies formed the strong foundation that is Nordic Brass Gusum, Sweden. The company has set consistently high quality standards with its semi-finished and finished products, all of which are manufactured at one of Europe’s most advanced brass production facilities. Nordic’s state-of-the-art plant is located at Gusum in Sweden and has a capacity to produce more than 40,000 tonnes of highquality brass products annually.
Nordic Brass’s products include standard unfinished items such as round, square and hexagonal rods, profiles and ingots, as well as a range of finished nuts. The company is supplying to customers producing ready-tomarket products. These products include screws, nuts, taps, pipe fittings and lock parts, as well as electrical components and ornaments. Nordic Brass’s products are in demand in a wide range of industries from companies involved in the heating, ventilation and sanitary sectors, to those operating in the automotive, building, electrical and telecoms industries.
Guaranteed quality
Quality is the hallmark of the company’s culture and its success. This is evident in every aspect of its operations, from its dedication to customers’ needs, to its commitment to recycling and sustainability. Certified to the quality management system ISO 9001:2000, Nordic Brass ensures that reliable manufacturing and control routines are strictly maintained all the way from purchasing to the finished product. Furthermore, it guarantees that all customer requirements are fulfilled during its operational processes, from providing original quotes to the final delivery of the finished product.
All Nordic’s operations are based on its wellproven research and development practices and are carried out in close cooperation with its customers. This provides them with access to technical advice, high-quality products and the shortest possible lead times, as well as the opportunity of discovering new applications for innovative brass products.
Mr Werlefors said, “We are fortunate in that we have everything under one roof here which helps to ensure that we achieve the highest standards at every step of our manufacturing processes. Our factory is one of the most advanced in Europe and is complete with casting machines, melting shop, press lines and finishing lines, all designed to work with optimum efficiency. We also carry large stocks of both finished and unfinished products at the site and keep a wide range of standard products in stock for express deliveries.
“We also have our own fleet of ‘brass lorries’, and as well as our set delivery routes, we also offer special collection services for the retrieval of scrap, which is mostly turnings. In addition to our standard range of products we can also produce special rods
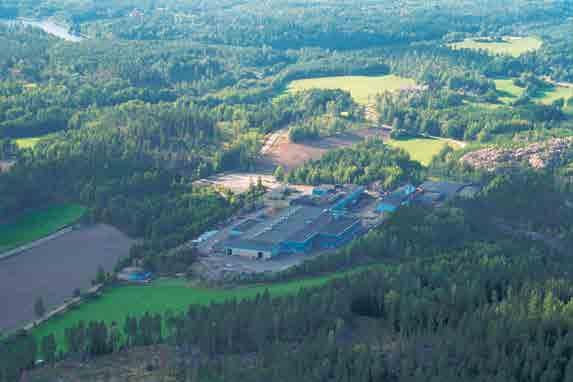
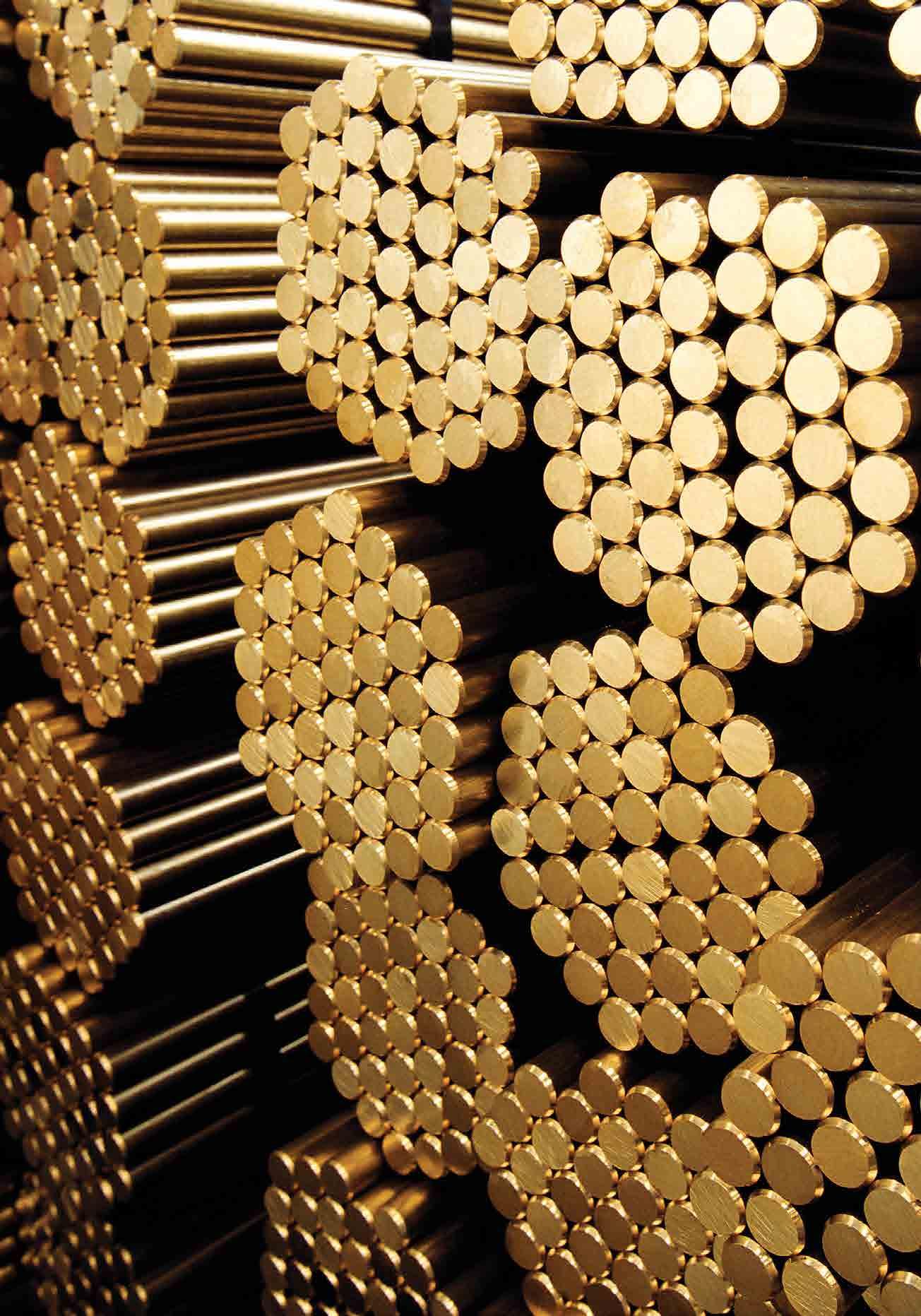
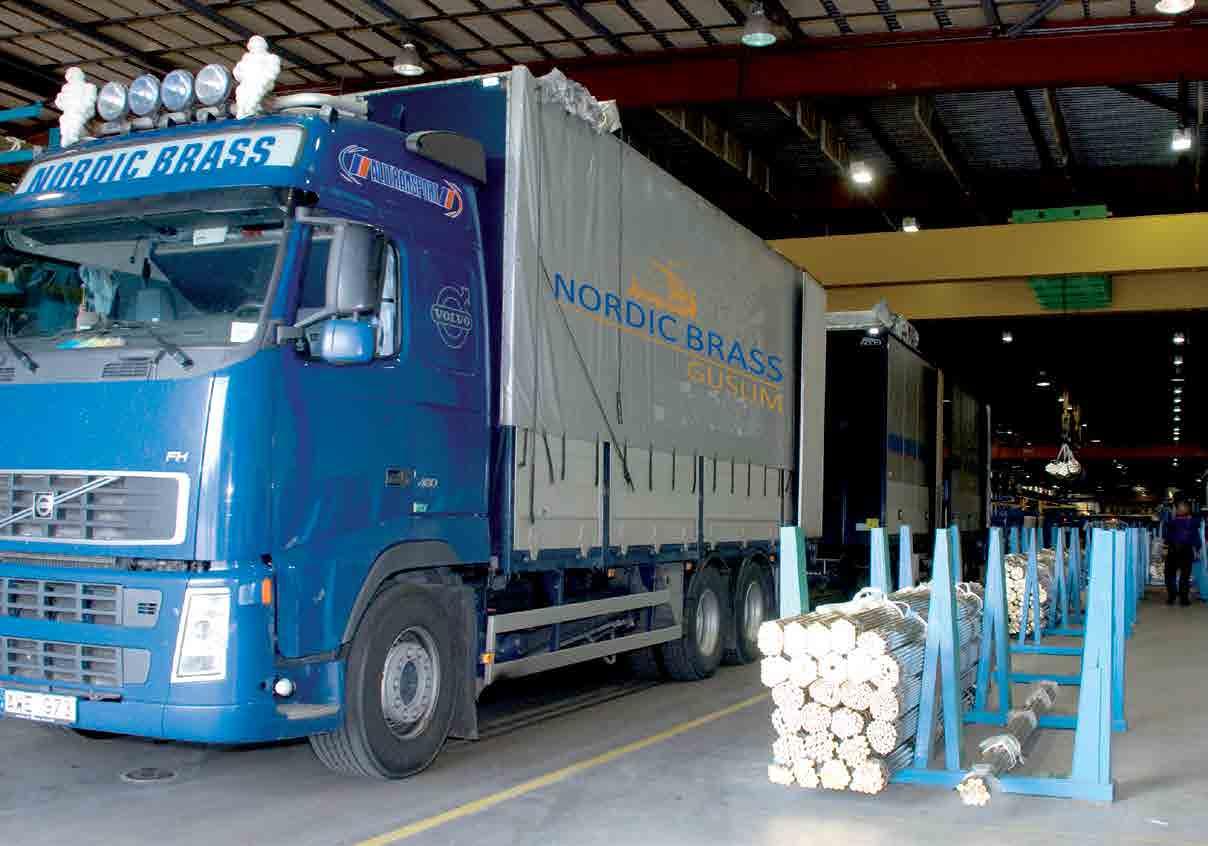
and profiles using various alloy compositions, all at very short notice.”
Mr Werlefors added, “We are the only manufacturer of brass products in the Nordic region with our main competition coming from Germany, France and Italy. However, we are able to produce very high quality products which are to the same standards as the best available in mainland Europe. We are also very flexible when it comes to meeting the challenges that our clients set us and we work closely with them to achieve the best possible outcomes. We will continue to rely on our organic growth for the foreseeable future and are moving into new market sectors, such as the heavy truck industry where the preference is for brass fittings for connectors involved in a truck’s hydraulic systems. We are also seeing growth in the general manufacturing industry where a lot of brass is used, as well as in the sanitary and building industries.”
Taking recycling to a new level
The company’s day-to-day business revolves around the recycling of scrap metal. Brass production, which involves smelting, casting and extrusion, has an effect on the environment in various ways and is strictly controlled by legal requirements and government licences. As one of the early pioneers of sustainable production, Nordic Brass has worked systematically to employ a programme of continual improvement throughout its manufacturing processes. By combining an awareness of environmental issues with the involvement of its employees and setting clear, environmental targets, Nordic Brass Gusum has continued to set the standards in the industry. This dedication is supported by a company environmental control system that fulfils all the requirements of SS-EN ISO 14001:2004, and which is fully certified by BVQI.
Mr Werlefors commented, “The brass business is by its nature a recycling business as our products are manufactured from the recycling of our customers’ scrap metal and from materials from our local Nordic scrap metal merchants. It is profitable to recycle brass and nearly 90 per cent of the raw materials that we use are derived from brass scrap. It is also important to mention that in order to avoid impurities, we insist that the highest demands are made when sorting and classifying recycled material. We also work to ensure that our logistics determine the shortest possible transport links when it comes to delivering our products.” n
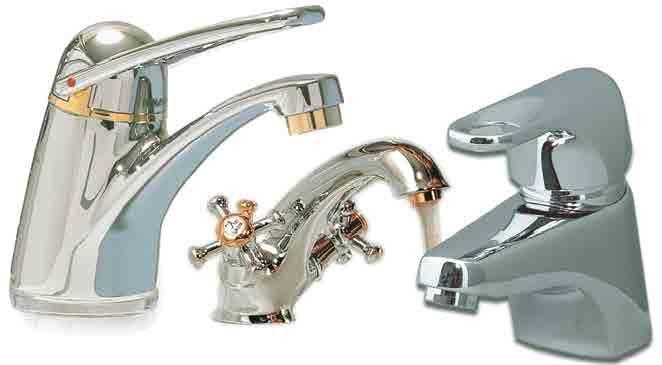