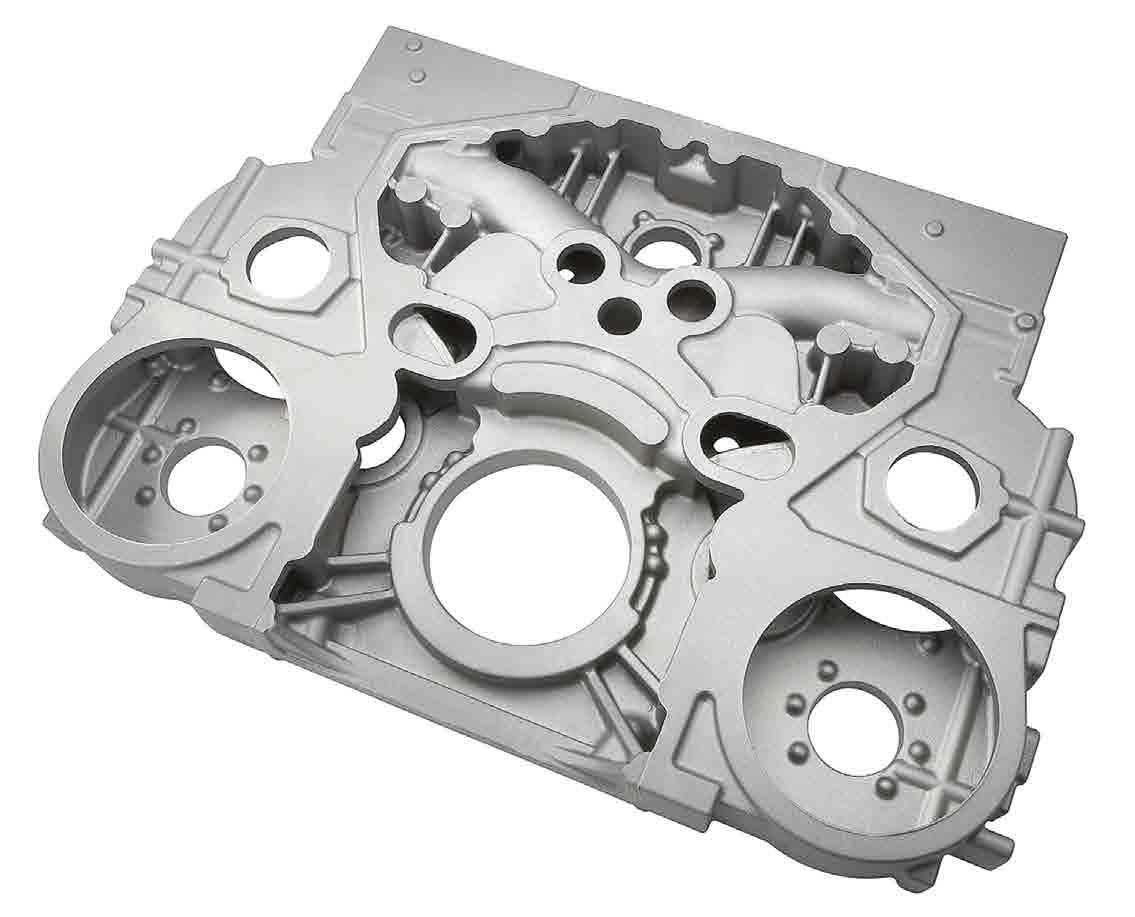
4 minute read
Complex castings Luitpoldhütte
COMPLEX CASTINGS
Germany’s Luitpoldhütte AG is a foundry producing sophisticated castings for customers worldwide. Marco Siebel spoke with the company’s new CEO, Dr Thomas Fessl.

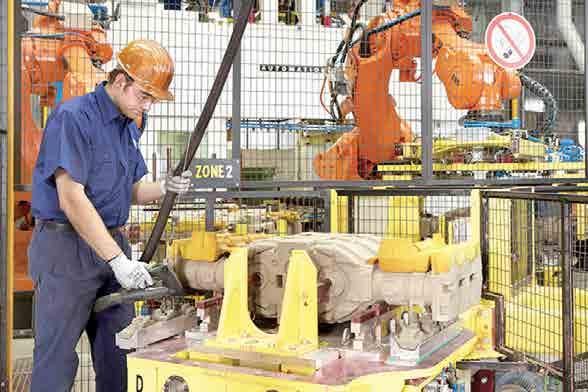
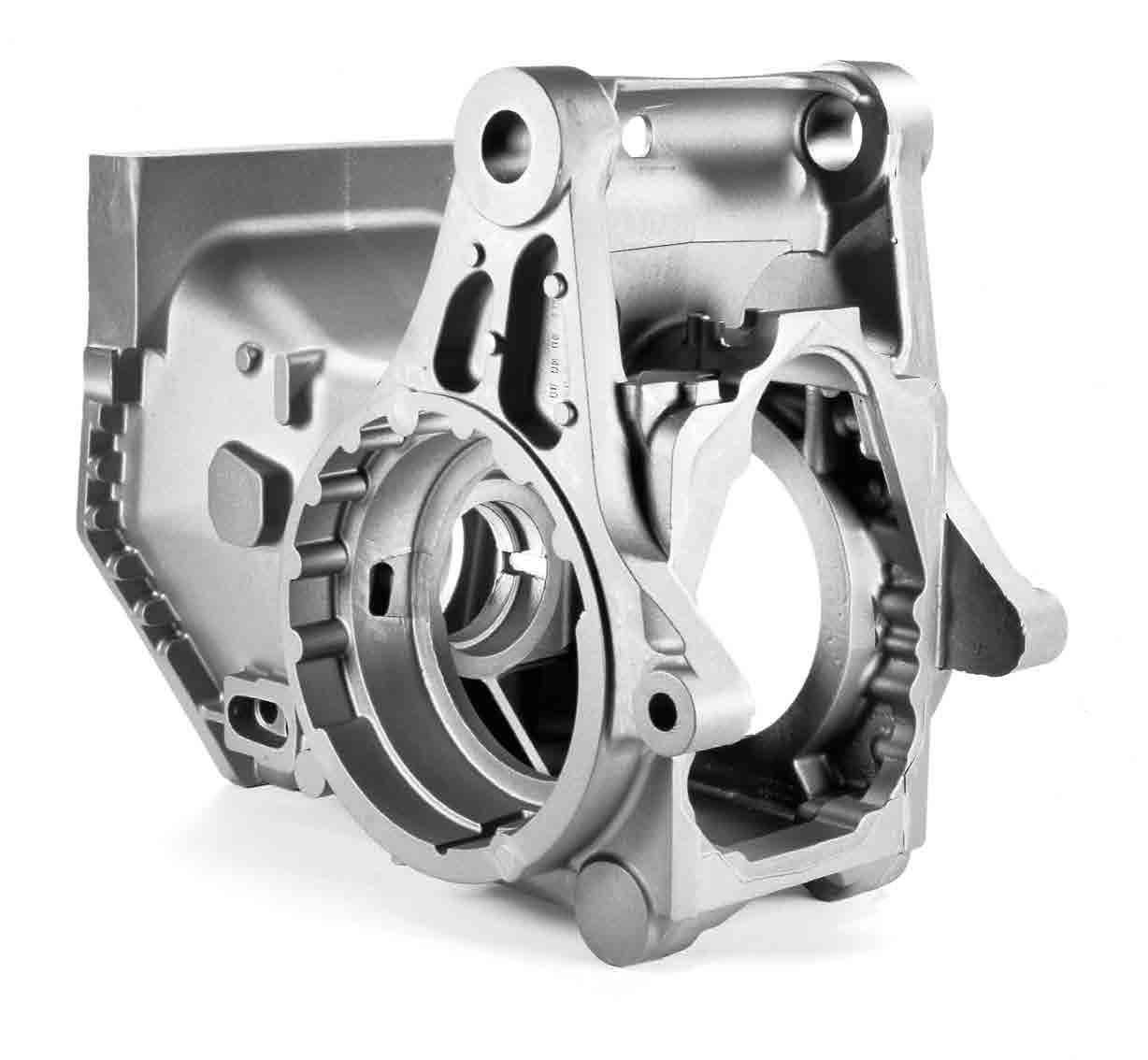
The first blast furnace in the little town of Amberg in Bavaria was established in the year 1883, followed by the setting up of the first foundry in 1911. It was called Luitpoldhütte, in honour of the prince Luitpold, ruler of Bavaria at the time.
Today, Luitpoldhütte manufactures engine blocks and engine parts, transmission housings for agricultural equipment and machinery, transmission housings for construction equipment, industrial transmission housings and compressor housings.
With a staff of 420 employees on average, the production volume achieved in the 2010/2011 business year was 53.400 tonnes and turnover was around €75.3 million. This makes Luitpoldhütte one of the most efficient foundries for small and medium-sized series with unit weights of 100 to 1000kg.
Moderate yet steady growth
Luitpoldhütte has core, melting, moulding and finishing shops where it can provide customers worldwide with just-in-time deliveries of large, highly complex and machine-moulded products in mediumsize series.
Turnover for 2012 is expected to reach EUR 100 million, accompanied by an increase of the workforce to about 490 employees. Luitpoldhütte has been able to keep on its permanent staff, and even has been able to hire extra temporary staff to handle the increasing numbers of orders.
Thomas Fessl said “We will continue to deploy extra temporary staff so as to be able to compensate for fluctuations in sales. It looks as if the near future will see moderate growth, so that at the moment we can look confidently at what is ahead. We have been investing in starting up new products, and there are already additional projects in the pipeline that are expected to commence production later this year. The only risk we can see is that as production grows in Europe and Asia, raw materials will most probably become scarce and hence more expensive.”
Via Lazio 24 – Z.I. Schio 1 36014 Santorso (Vicenza) Italy Phone: +39 0445 575079 Fax: +39 0445 575468 E-mail: info@stipsrl.it www.stipsrl.it
Contacts: Poier Matteo & Poier Sergio (owners)
S.Ti.P. Srl – Patternmaker since 1969
Patterns for crankcase, heads, axles, differential gears, etc. CN machine tools, support for the design (CAD/CAM system).
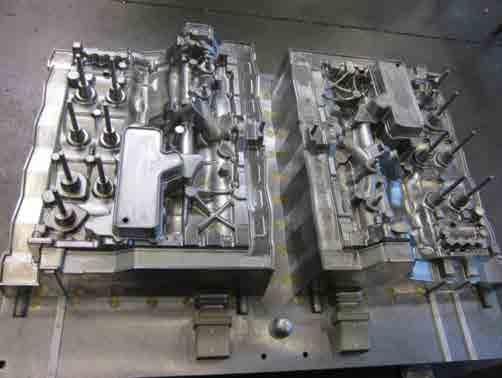

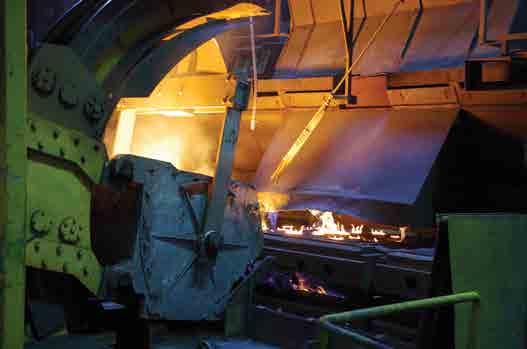
Complex supply contracts
Luitpoldhütte has been working with engine manufacturer MTU, a German supplier of engines and transmission systems worldwide for off-road applications as well as decentralised energy plants.
Initially the business relations were limited to supplying engine components but Luitpoldhütte now develops and manufactures additional castings, up to and including the initiation of serial production. The total time span from the first prototypes of the V8 engine to serial production took only 18 months. From 2011 Luitpoldhütte started producing and assembling the first serial castings from a specially redesigned core shop.
Luitpoldhütte has also been supplying General Electric Transportations Systems with cylinder jackets for locomotive engines. At regular intervals, the engines have to undergo maintenance checks, and on every occasion a certain number of cylinder jackets have to be replaced.
Mr Fessl explained “We are very pleased that the long-standing partnership and business relations between GE and LH are now being intensified, proof of which are the various mutual visits that have taken place.”
CGI castings
Whereas a high duty grey cast iron product reaches its limits at a strength of just over 300N/mm², the modified compacted or vermicular graphite iron casting will “flex its muscles” at over 450N/mm²! It is combining

the strength of ductile cast iron (high strength and heat resistance) with those of grey iron (thermal conductivity and resistance).
In grey cast iron, the carbon separates in the form of graphite flakes with pointed ends; the special treatment of CGI, by contrast, rounds off these flake ends so strongly that under the microscope the graphite looks like worms, all of this with a shrinkage behaviour similar to that of grey cast iron (for grey cast iron and CGI the same pattern can be used), good castability and a very good vibration damping, absolutely necessary in engine construction.
After several very successful trials and prototype productions back in 2009, Luitpoldhütte has been offering the CGI technology to its customers, following the increasing demands of the market.
Mr Fessl concluded “With a consistent policy of people investment and investments in the latest technologies, Luitpoldhütte is pursuing the consistent implementation of its strategy of being the premium supplier of large, highly complex and machine-moulded products in medium-size series.” n
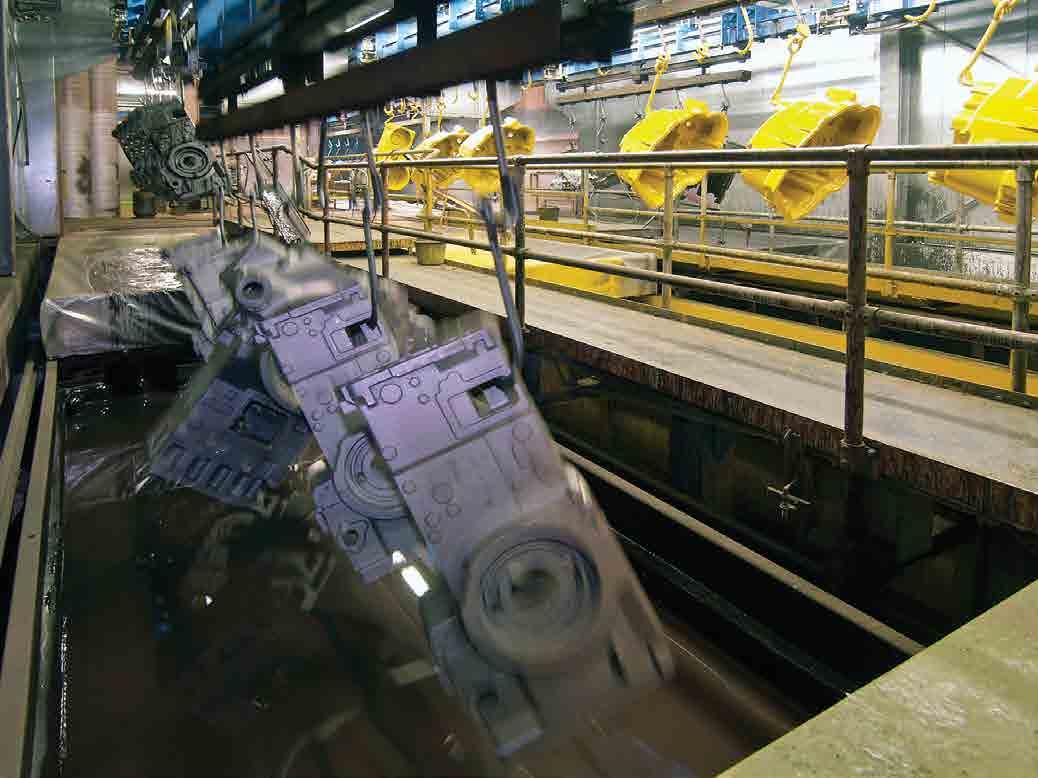
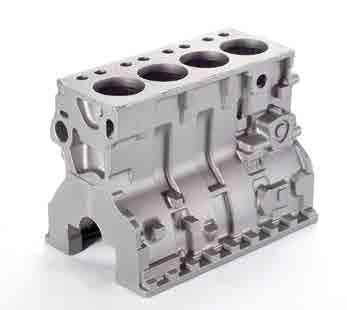
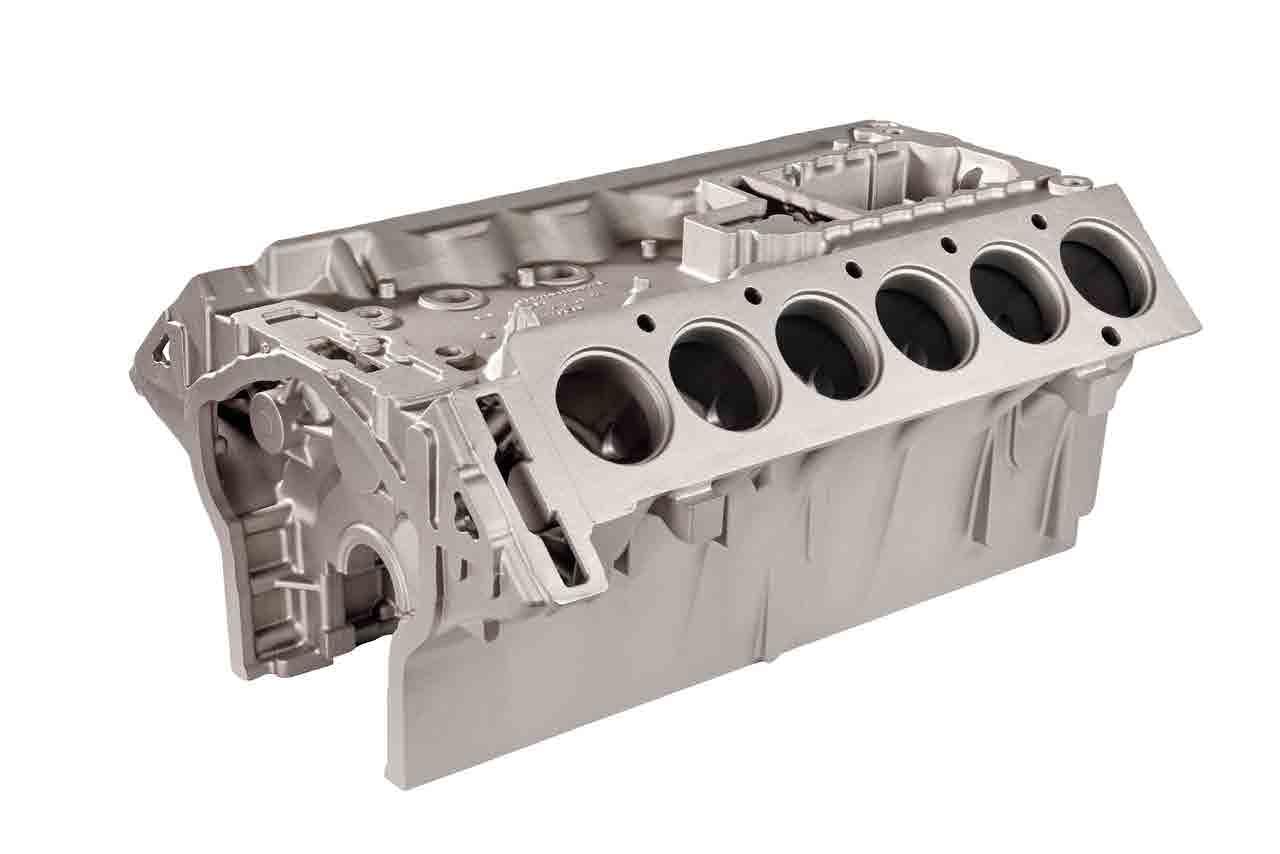