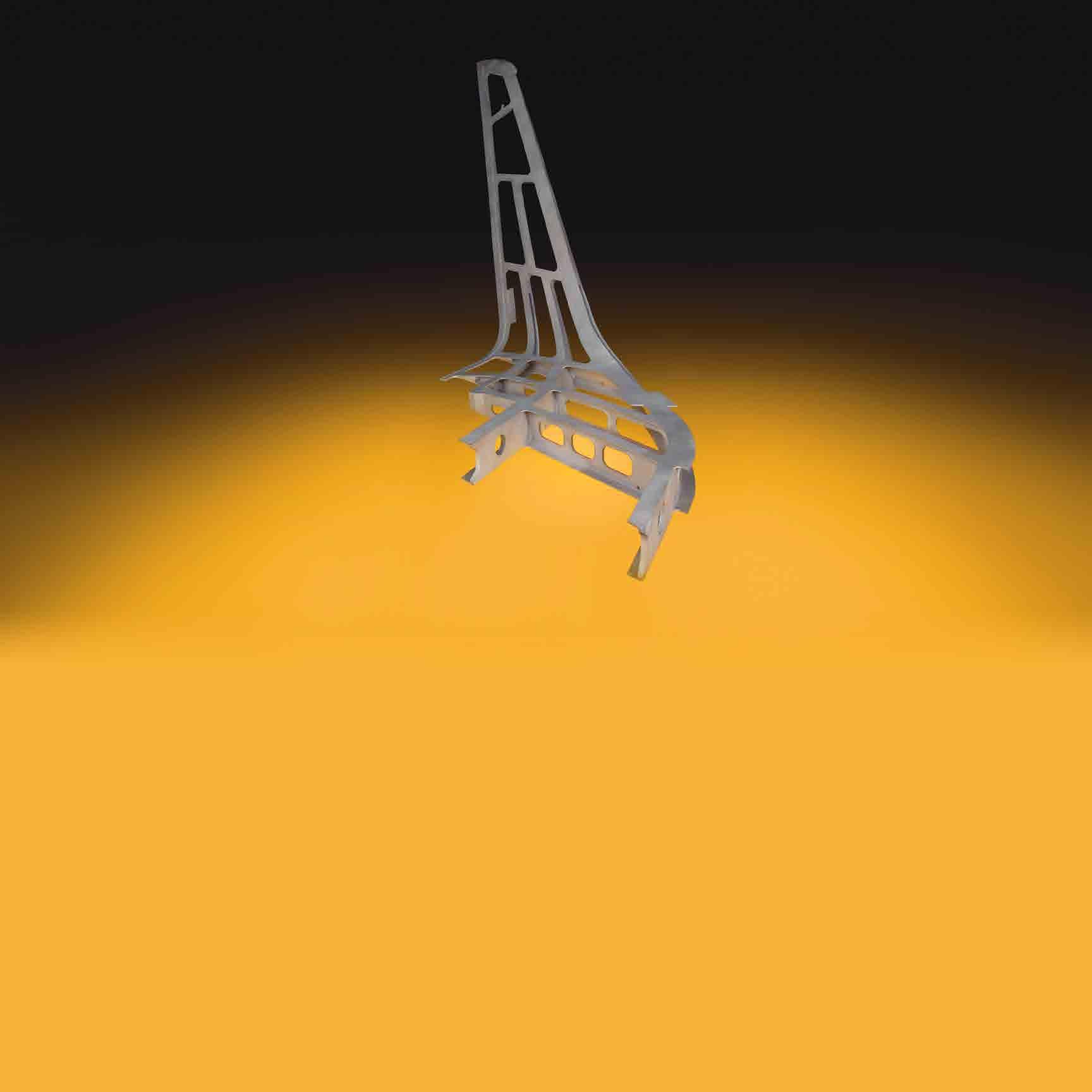
4 minute read
Aero dynamic Aeromet International
AERO DYNAMIC
Aeromet International PLC is a global leader in the casting of aluminium and magnesium for critical components used by the aerospace and defence industries. Philip Yorke talked to Alan Dustan, the company’s business development director, about its ground-breaking new alloy and its move into new markets.
Aeromet International PLC was founded in the UK more than 30 years ago and has grown to become a world leader in the manufacture of premium quality aluminium sand and investment castings and magnesium sand castings. The company has continued to invest in new technology since its inception, both in the sand and investment casting processes, for the aerospace, defence and auto sport industries.
The company operates three major manufacturing plants in the UK. The first is located at Sittingbourne in Kent, where Aeromet produces aluminium and magnesium sand castings with mould sizes up to 1m3. The company also operates two modern investment foundries, one in Rochester and another in Worcester, which are capable of producing aluminium investment castings that range from 10mm3 to 1.5m3, by either conventional or advanced SOPHIA casting processes.
Aeromet’s Worcester facility has the accolade of being the only Boeing-approved
European investment casting foundry that produces castings by both conventional and SOPHIA high property processes. Aeromet specialises in the production of avionic chassis and housings, escape doors, fuel pumps, aero engine heat exchangers, air intakes and aircraft canopies. In addition, the company makes large complex structural castings, fuel connectors and transmission castings. Today Aeromet employs more than 250 people and in 2011 recorded sales of over €25 million.
Extending the frontiers of high performance alloys
Aeromet is a dynamic, innovation-led company that prides itself on its ability to produce castings that set the benchmark for others. Its commitment to maintaining high levels of innovative technology and dedicated customer services has won it the confidence of the world’s leading aircraft manufacturers. These include such giants as Aero Engine Controls, Airbus UK, Boeing, Embraer, Meggitt, GKN Aerospace and Rolls Royce.
Mr Dustan said, “In terms of cast alloys there has been very little in the way of new developments for over 20 years, although production methods have become much more efficient and cost-effective. However, at Aeromet we have developed a new alloy that is a true break through in terms of offering significantly improved properties. This is a very high performance alloy, which we have patented and named A20X®. We developed this world-beating product in-house and in cooperation with LSM in Rotherham and the University of Birmingham.
“The potential of this product for a diverse range of applications is very significant, especially in relation to our key markets and in particular to the aerospace industry. This innovative alloy places us at the forefront of new cast aluminium alloy development and the benefits of using A20X® cannot be overstated. This high performance alloy has a much higher strength to weight ratio than any conventional cast alloys and also offers improved corrosion resistance, extended fatigue life and improved ‘buy-to-fly’ ratios. Another important advantage is that it provides improved elevated temperature properties over traditional cast alloys, as well as over wrought 7000 materials.”
Mr Dustan added, “Currently around 85 per cent of our business is dedicated to serving the aerospace industry and this is where we see our main growth for the future. Our other key market is the defence sector, which has remained static as a result of government cut-backs. However,

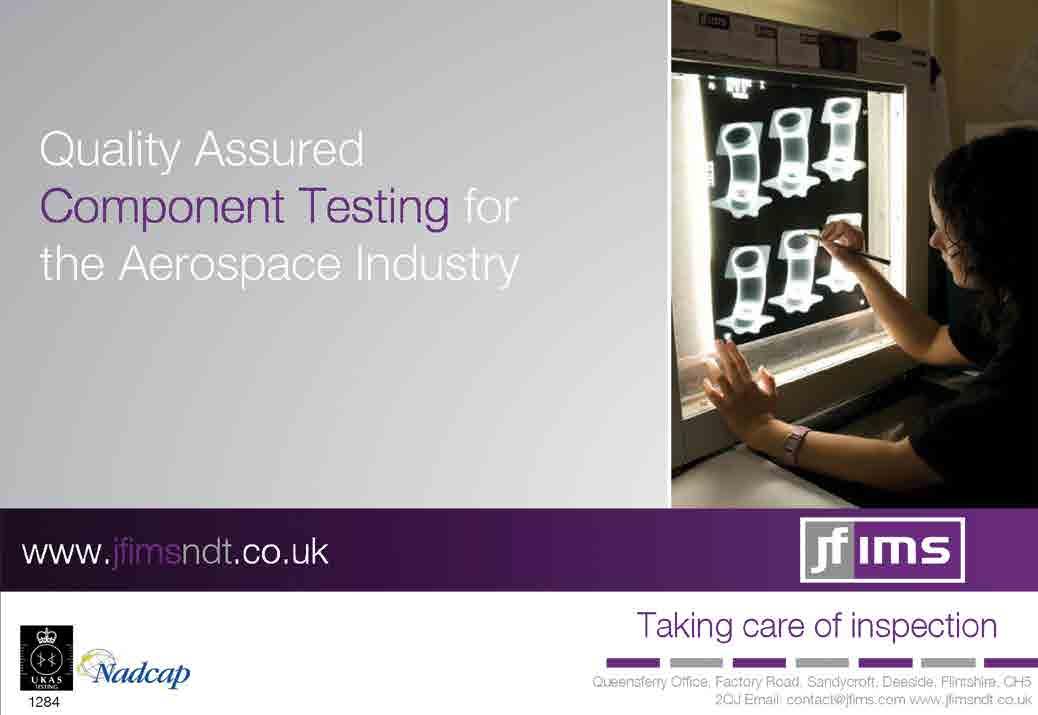
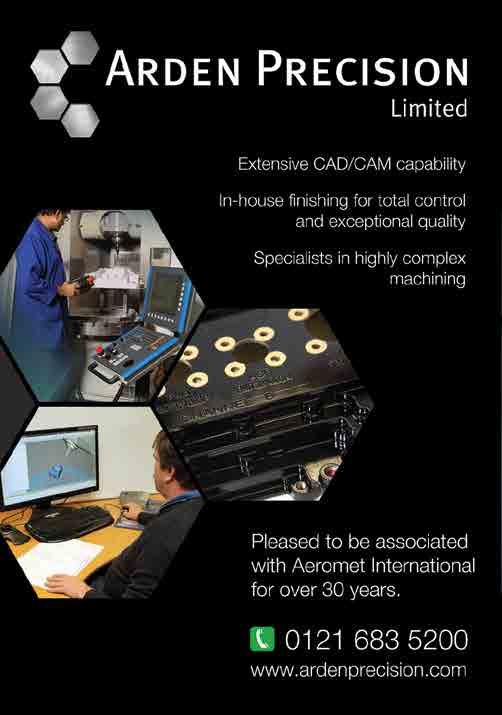
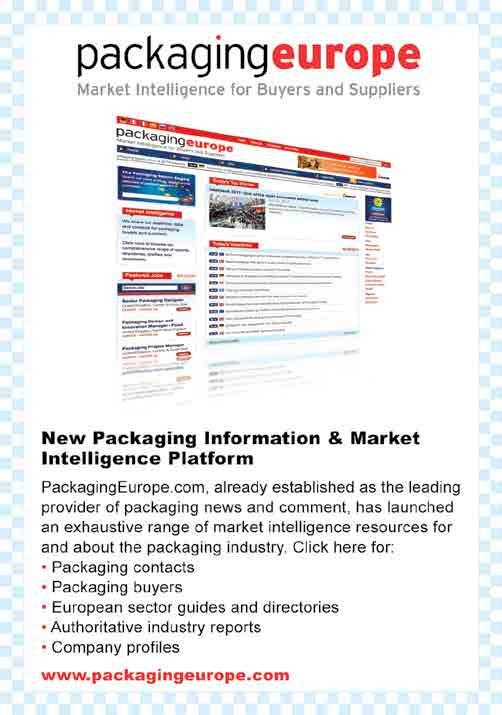
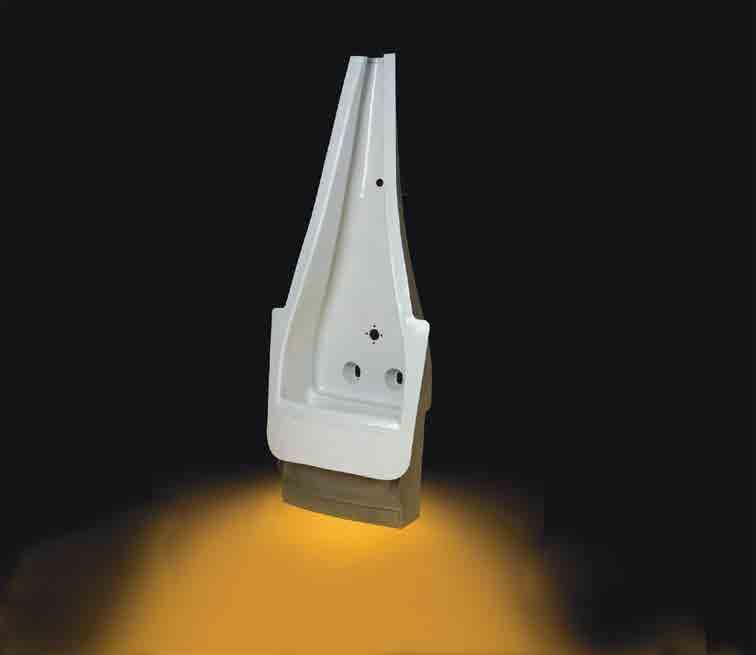
with the advent of A20X® we can see new opportunities in this sector, as well as in other niche markets in industry as a whole. The A20X® properties are on a par with aluminium wrought material properties so that aerospace designers can now for the first time select a cast aluminium material over a wrought aluminium material and have greater freedom of design. We look to the future with confidence in three specific areas: First of all we are expecting significant organic growth to come from our existing programmes of work for Airbus and Boeing; and then there is the huge potential that A20X® offers. We are also at an advanced stage with new work concerning more conventional materials for our existing and related markets.”
The strongest cast aluminium alloy
This latest breakthrough from Aeromet is based upon a modified version of the aluminium copper alloy A201 and eliminates the problems associated with the poor castability of the aluminium copper series of alloys. In addition, A20X® has the fluidity that compares favourably with aluminium silicon based alloys such as A357.
This novel and innovative alloy will be welcomed by a broad spectrum of industries as it has overcome shrinkage porosity and segregation. Furthermore, it is not prone to hot-tearing and is far more resistant to stress corrosion and fatigue cracking – a very important consideration in the aerospace industries – and is today the strongest cast aluminium alloy available on the market.
Yield strengths of A20X® up to 440MPa, with tensile strengths of 500MPa and elongation of 3.5 per cent, are typical of this new alloy and define new boundaries for cast aluminium properties. This revolutionary new alloy has been developed over many years by specialists in the Aeromet R&D department at Worcester and A20X® has now been approved by the SAE Aerospace Council and has been designated as AMS4471 for investment castings and AMS4482 for sand castings with MMPDS confirmation available by the end of September. More information about Aeromet’s products and technical data concerning A20X® is available from: www.aeromet.co.uk n
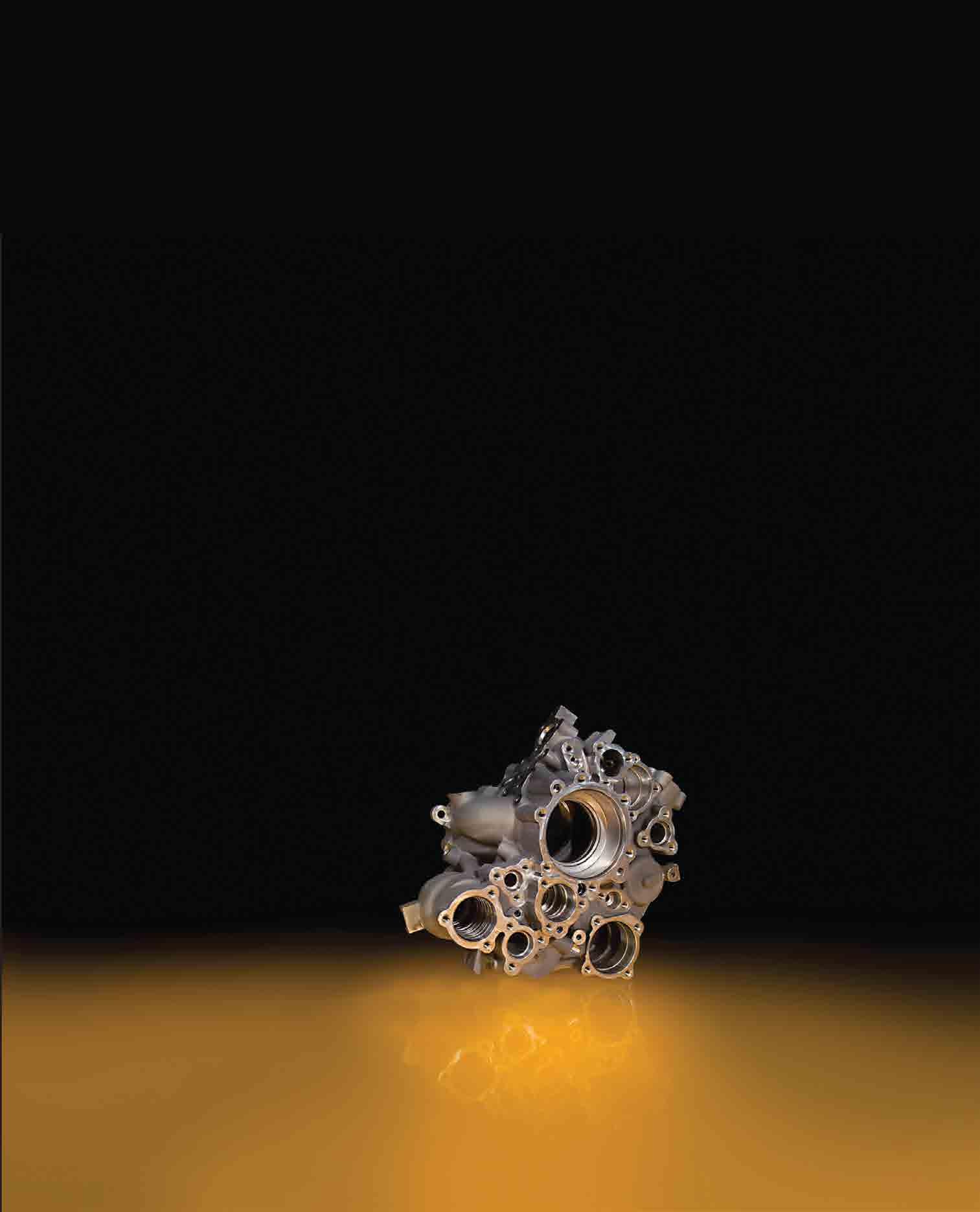