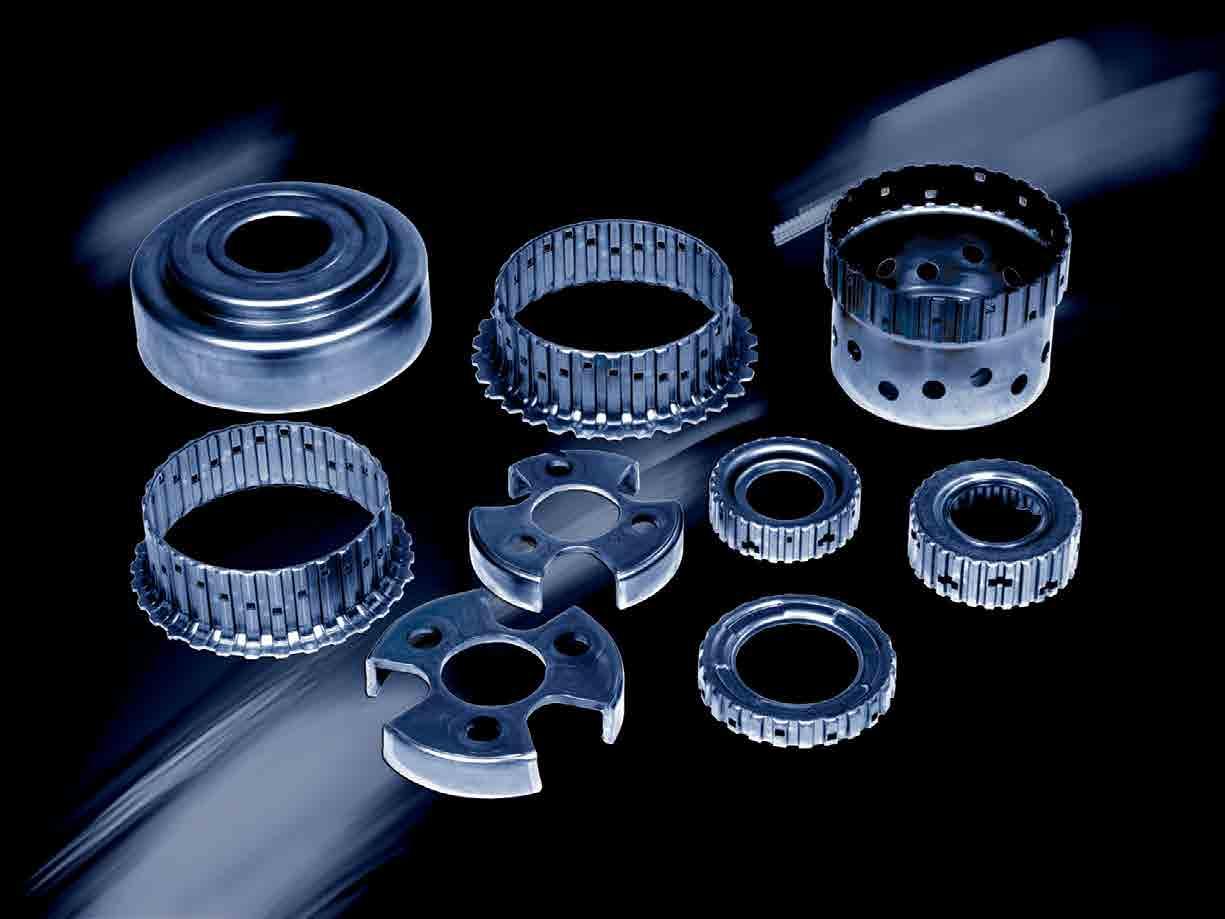
6 minute read
Defining the art of fine-precision automotive part manufacturing Voit Group
DEFINING THE ART OF FINE-PRECISIONAUTOMOTIVE PART MANUFACTURING
The Voit group is a global leader in the manufacture of complex, high-precision parts and components for the automotive industry. Philip Yorke talked to Stefan Beinkaempen, the company’s business development director, about its unique manufacturing capabilities and major investments in new plant and technology.
The Voit Group is an independent familyowned business that was established in Germany in 1947 and has grown to become a leading international systems supplier to the automotive industry. The company is headquartered in Sankt Ingbert, Germany, and employs more than 1,800 people worldwide. Voit is the clear technology leader in its field with a focus on forward-looking technology and process optimisation. Its commitment to the environment and the development of new technology is underscored by its continuous investment in process technology and production capacity worldwide, amounting to more than €60 million over the last three years alone.
The Voit Group creates complex highprecision finished parts and components from steel plates, and aluminium die cast materials. The company’s main customers are in the automotive and automotive supply industry and Voit components can be found in more than 50 per cent of all cars on the world’s roads today. Voit parts are at work in the many diverse, functional areas of automobiles, such as the drive train, engine, fuel system, exhaust system, chassis and the car body itself. Voit’s customers include ZF, Bosch, Denso, Brose, Continental and AMK and supplies therefore Audi, BMW, Mercedes, VW, Ford, Opel, Jaguar and Land Rover indirectly, resulting in more than 170 million automotive parts being produced by the company each year.
Improving weight/performance ratios
Reducing fuel consumption and CO2 emissions is a major priority for the world’s automotive manufacturers. Voit is applying its unparalleled experience and cutting-edge technology to the drive for improved weight/ performance ratios demanded by increased
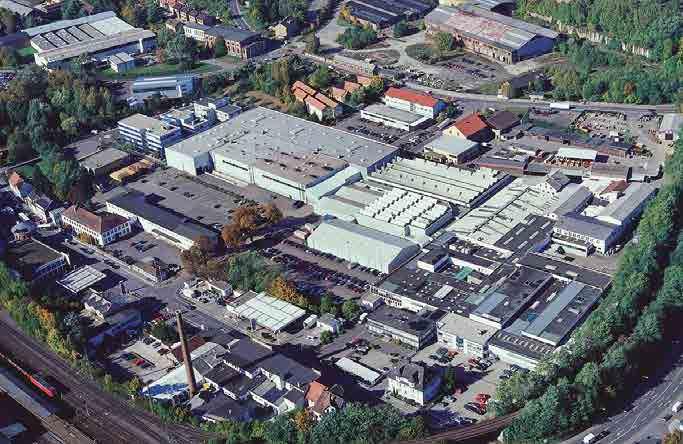
EU legislation. Over recent years Voit has been developing components that provide maximum strength with simultaneous weight reduction and its latest hot-forming technology is delivering optimal results. This new process is being used increasingly for key body and chassis parts such as side impact protection systems, bumper reinforcements and for highstrength inflexible structural parts for automotive ‘body-in-white’ components.
The main advantages of the latest Voit hot forming process can be found in its precise dimensional stability and excellent reproducibility, as well as in its high-strength and hardness values, as Mr Beinkaempen explains, “We are the technology leaders in the development and manufacture of complex hot-forming lightweight parts and components. Our press hardening for body structures, underbody parts and pillars offers our customers optimal weight to strength performance ratios. Car builders today are looking for lightweight design as can be seen in the latest VW Golf and Passat etc. These global companies are looking to us to produce complex parts in the press hardening market as well as combining hybrid materials for tomorrow’s electric vehicles where we are providing parts for high-voltage and soft-start solutions.
“This is one of many areas where the demand for our high-performance die casting parts is seeing strong growth. Recently some of the world’s biggest automotive OEMs in the USA have asked us to work with them since they have become aware of our new technology and what this can achieve for them. One of the key advantages to hotforming is that there is no spring-back effect as this process allows the manufacture of
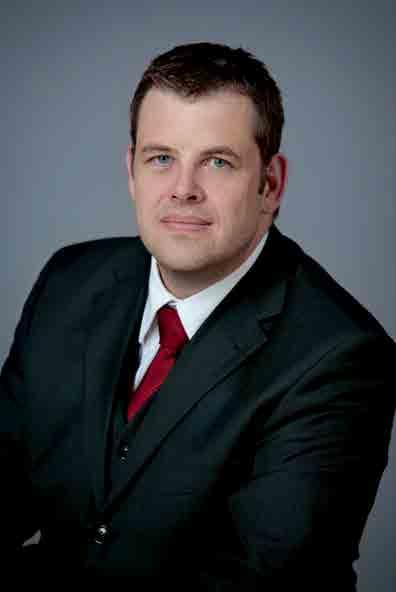
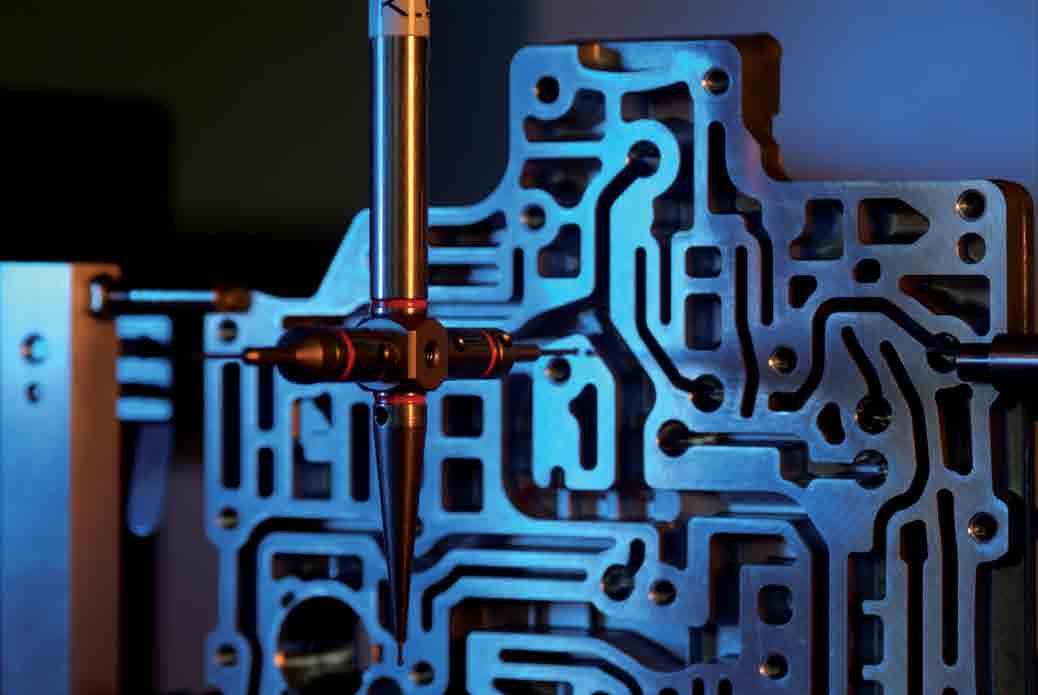
highly complex, precise and dimensionally accurate parts, which could not be achieved using the traditional cold-forming process. The defining principle in hot-forming is known as ‘tailored properties through tailored tempering’ and involves having various strengths and different levels of hardness even within one individual component, so that strength areas and crumple zones are both possible to achieve in one single component.” There are very few companies today that can master this latest hot forming process technology and therefore capacities in the international marketplace are correspondingly in short supply. Voit is addressing this problem with its major investments in this new technology. In this respect the company is focusing on large-scale production with a capacity of up to three million passes to be made available within the next three years. What’s more, with a total of six new facilities currently in the design phase, capacity will increase by up to 10 million parts and components per year in the near future.
Mr Beinkaempen added, “Whilst much of our production capability is centred in Europe at our plants in Germany, France and Poland we have established a manufacturing facility in Mexico to supply also the North American market. Here we have installed a state-of-theart 800 ton press and we have installed similar presses in France of 400 and 630 tons, with a direct-drive technology which can significantly accelerate speed between strokes. In Germany also we have installed the latest 1,000 ton press for the press hardening process.
Further we providing parts in AL die casting for high-voltage and start-stopp solutions.
“This is one of many areas where the demand for our high-performance die casting parts is seeing strong growth. Recently some of the world’s biggest automotive OEMs in the USA nominated us to work with them since they have become aware of our die casting performance and what this can achieve for them.
“For the production of components for electric braking and steering systems, we have developed a unique surface treatment system to avoid short-circuits in today’s advanced electrical systems”
All this investment is focussed in two directions: • Complex parts for powertrain, driver assistant’s and seat systems including sub system mounting • Body structure parts for the OEM demand
The Voit Group’s portfolio of products and its potential for the development of new technology to meet the challenges of tomor-
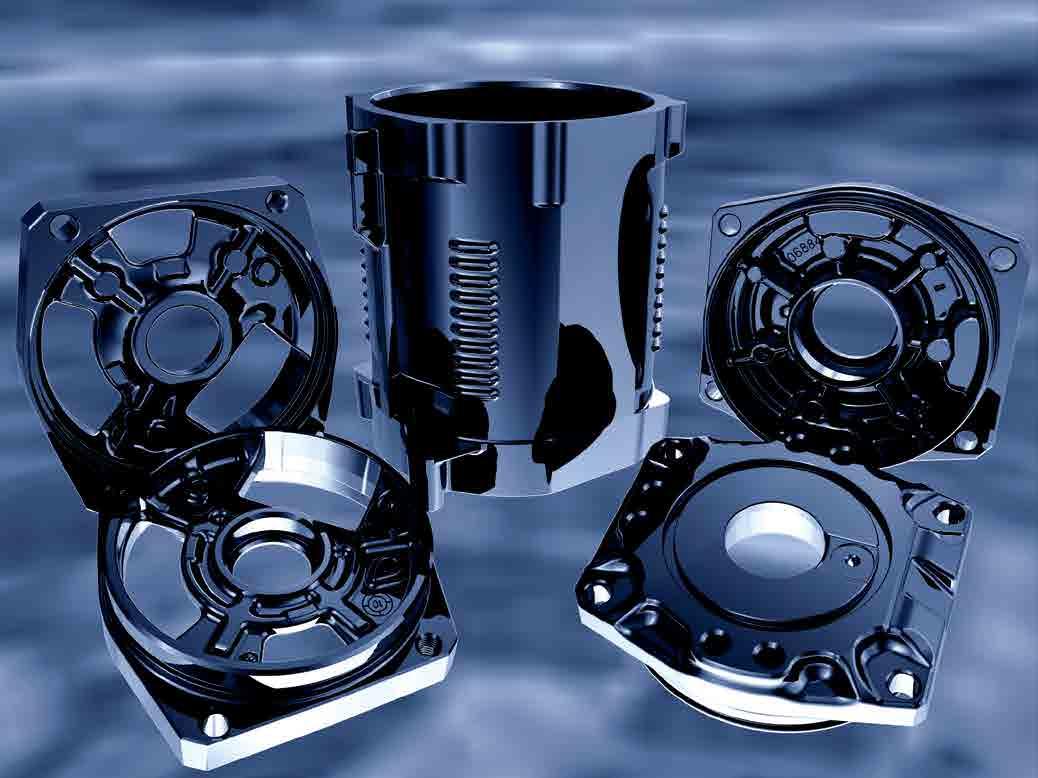
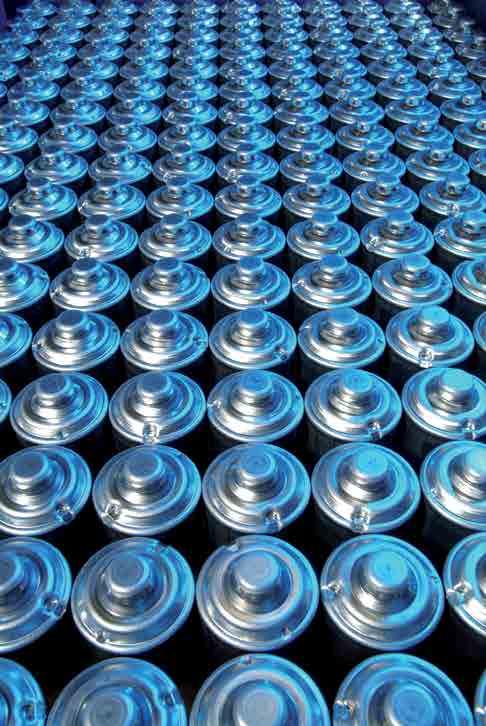

The special chucks producer / specialist for easy deformable parts.
Stiefelmayer Spanntechnik GmbH & Co. KG Rechbergstraße 42, 73770 Denkendorf Phone: +49 (711) 93 440 - 311 Fax: +49 (711) 93 440 - 11 E-mail: spanntechnik@stiefelmayer.de www.stiefelmayer.de
row is unsurpassed. That is why the world’s leading tier-one suppliers to the automotive industry, such as Bosch, ZF, Brose and Continental, rely on Voit for a diverse range of key automotive components.
Voit is comprised of three main business units – aluminium high-pressure die-casting, cold-forming and hot-forming technologies. The list of the company’s production capabilities is extensive and includes the development and manufacturing of complex, high-precision and finished parts and components for the entire powertrain as well as for brake systems, power electronics, engine casings, lever systems and servo drives. This is in addition to engine cooling and thermal management and structural aluminium. Putting in place the most stringent quality control procedures has resulted in Voit consistently achieving a record of ‘zero defects’ as standard practice. n
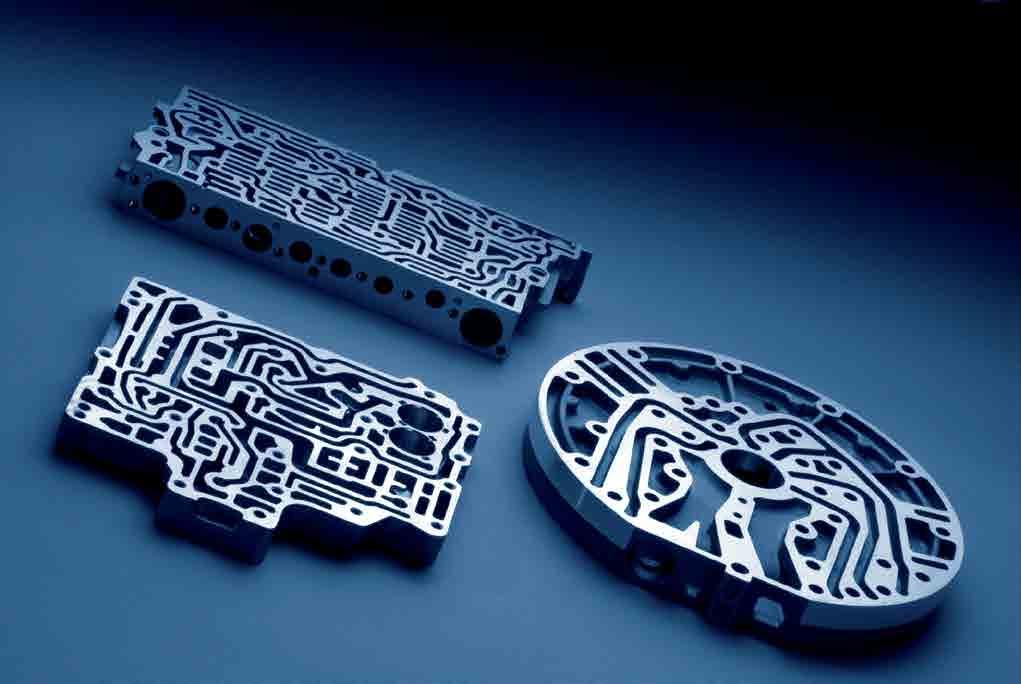