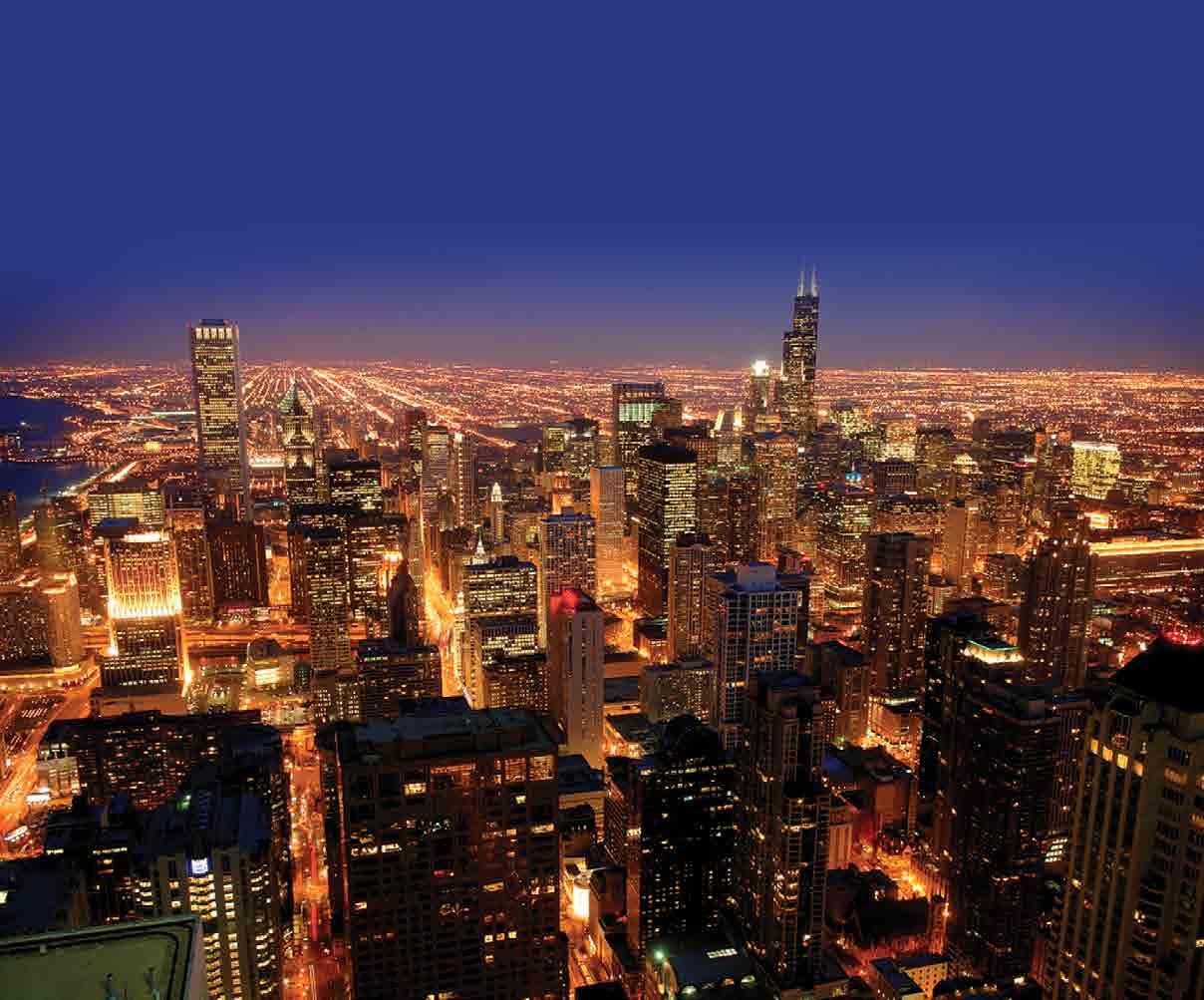
5 minute read
Essential support for power plants
The German company GEA Westfalia Separator Group manufactures separators and decanters for many different applications in the food, pharmaceutical, marine and chemical industries. The separators play a vital role in the energy sector, where they are used in the treatment of fuel for power plants. Joseph Altham interviewed Nick Fernkorn, GEA Westfalia Separator Group’s director of business line energy, to find out how the company’s separators are helping developing countries to generate electricity.

GEA Westfalia Separator Group is based in Oelde, where it has been making separators since 1893. Today the company is part of the powerful GEA Group, a leading global supplier of process technology for the food and energy industries. Even on its own, GEA Westfalia Separator Group would be considered a substantial organisation. It employs over 3000 people and has a total of five factories, three in Europe, one in India and one in China.
GEA Westfalia Separator Group has almost completed construction of a new production hall, 25,000m2 in area, at its Oelde site, and expects to move into the new building in early 2013. For the energy business line, the company’s main factory is at Château-Thierry in France. The factory in China, at Wuqing, is relatively small, employing only 150 people, but GEA Westfalia Separator Group has big plans to expand its activity in Asia. “For the moment, this is really an assembly plant for the local market,” said Mr Fernkorn, “but we are investing in a new site which we expect to be up and running by the end of 2013. Eventually we will employ around 600 people there. It’s essential to manufacture in Asia in order to meet the demands of this huge market.”
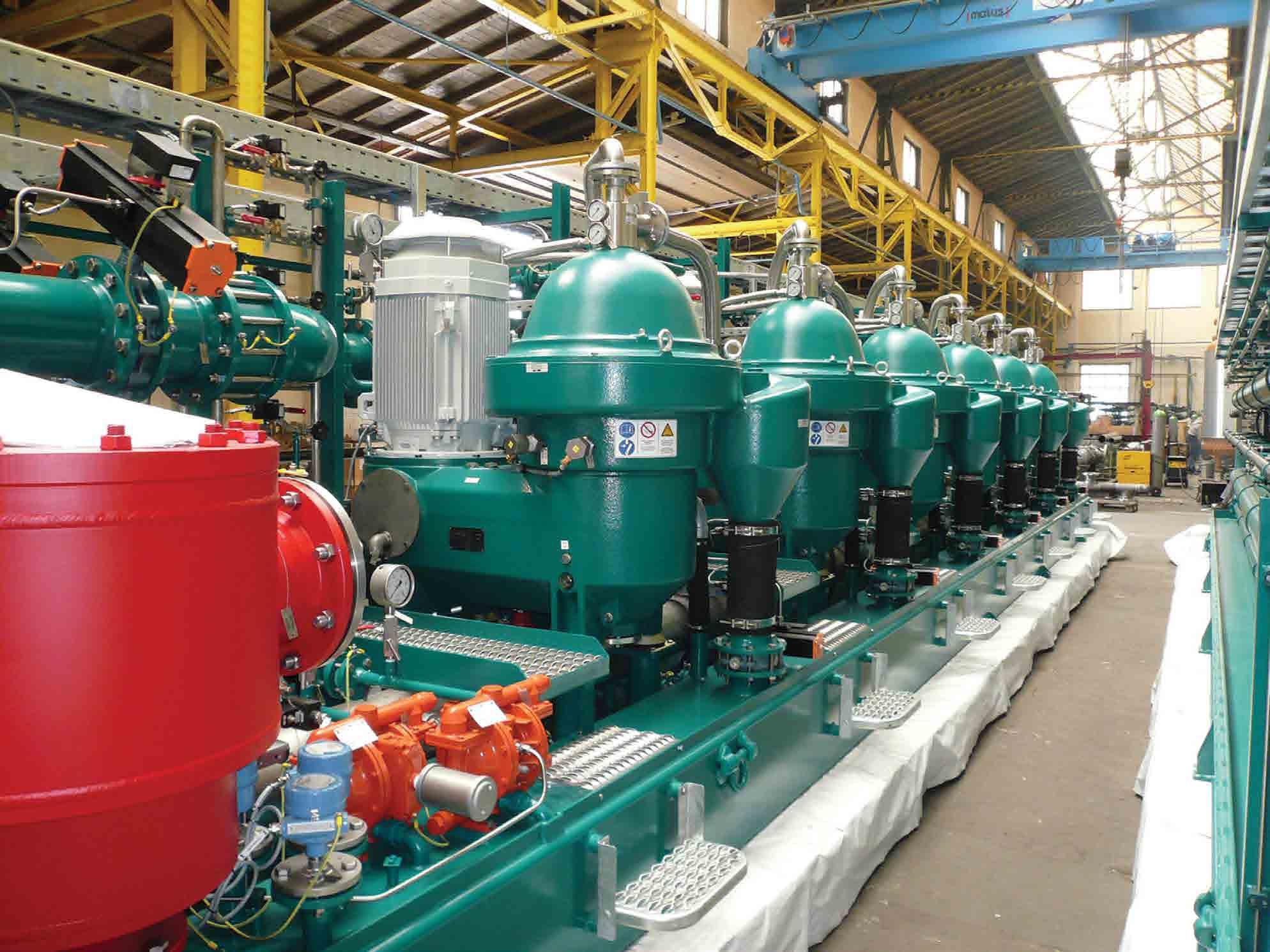
Headquarters. Oelde, Germany Factory Wuqing, China Fuel processing facility with self-cleaning separators
Consistently reliable technology
GEA Westfalia Separator Group produces separators and systems for use in power generation. The function of the separators is to process the oil that is consumed by gas turbines or diesel engines in power plants. Mr Fernkorn explained that a gas turbine doesn’t necessarily use natural gas. “Natural gas would be the simplest and easiest way of powering a gas turbine. But gas turbines have also been adapted to run off liquid fuel. At a high enough temperature, the heavy fuel oil (HFO) in the burning chamber becomes a gas.” The separators use centrifugal force to
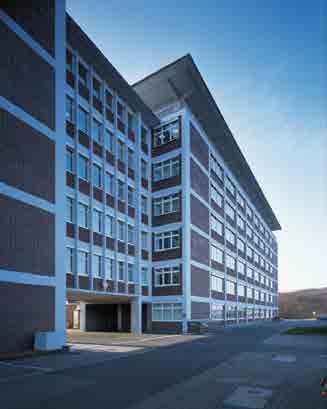
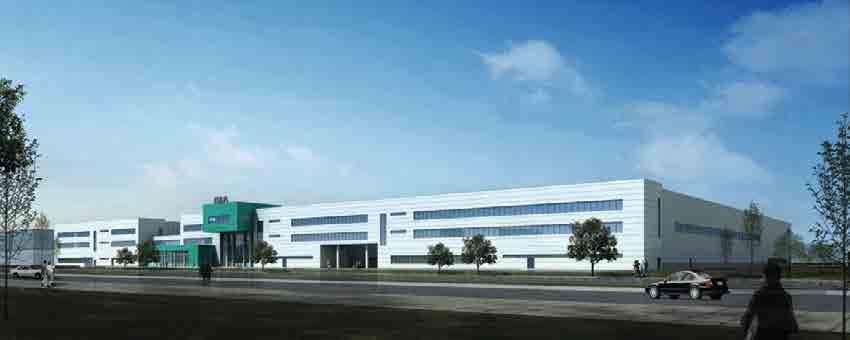
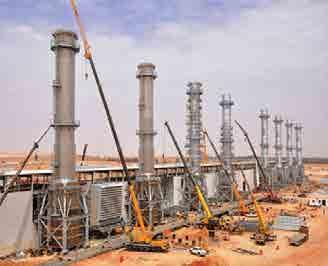
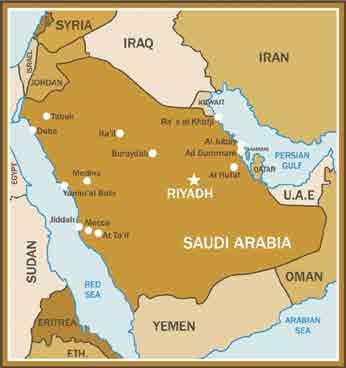
separate solids and substances from liquids. Crude oil or HFO needs to be treated in this way to remove impurities in the fuel that would otherwise damage the turbine.
“Traces of dirt or dust can get into the fuel during transport. These must be taken out before the fuel can be used. The fuel can also contain salts like sodium or potassium which must be removed to avoid corrosion.”
Proper fuel treatment is critical to the operations of the power station as a whole, so customers value the high production standards that GEA Westfalia Separator Group observes. “For our customers, quality of production ensures reliability. If something went wrong with the equipment, this might eventually cause the generator to break down and result in a blackout. Our separators are heavy duty and built to last a long time. This is necessary because customers expect a power station to have a lifetime of 25 years.”
Market-driven improvements
In some parts of the world, building a power station that runs on crude oil or HFO is the most practical way for a region to start generating its own electricity. Mr Fernkorn explained that there is a growing tendency for power stations to use poorer quality fuel. “Improvements to our products are driven by the market. Diesel has become more expensive, so power stations are often being built to run on HFO instead. As the quality of the fuel being used gets worse, our equipment has to be better.” HFO is cheaper but is more difficult to treat.
GEA Westfalia Separator Group designs processing installations on a customised basis and offers complete solutions for fuel oil treatment including the pumps, heaters and connecting elements. “Project specifications are becoming more complicated
World energy consumption is growing quickly, but no region has experienced such a considerable demand for electricity in the recent years than the Middle East. Driven by economic expansion and population growth this region has an insatiable appetite for energy.
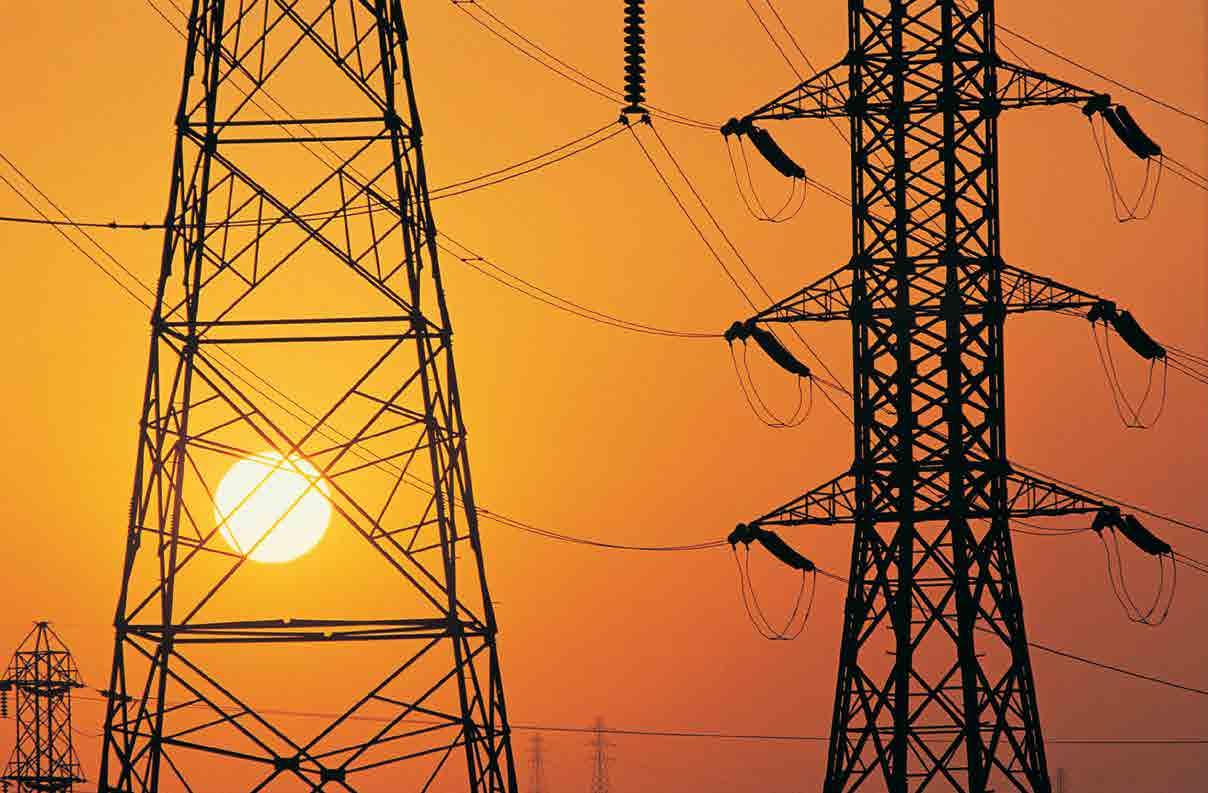

and our customers are asking us to take on more and more engineering responsibilities.”, he adds.
Global presence
GEA Westfalia Separator Group has 50 sales companies and 23 authorised workshops, putting the company within easy reach of its customers. “A lot of things have to be installed on site. We are there with our service people. We even have people in Iraq. In general, a lot of our work comes from oil-rich countries.”
For the energy business line, the Middle East is the largest market. In Saudi Arabia, GEA Westfalia Separator Group has recently supplied crude oil treatment systems for two large power plants near Riyadh. The 36 separators that the company delivered for the PP10 power plant are capable of processing a total of 1200 cubic metres of crude oil every hour.
Demand for electricity is rising, both in the emerging market countries and in many oilrich nations as well, so the outlook for GEA Westfalia Separator Group looks promising. There could be interesting opportunities in Africa, Mr Fernkorn believes, particularly in those countries that have their own oil reserves. n
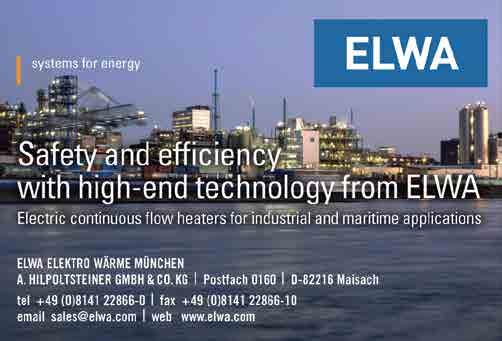
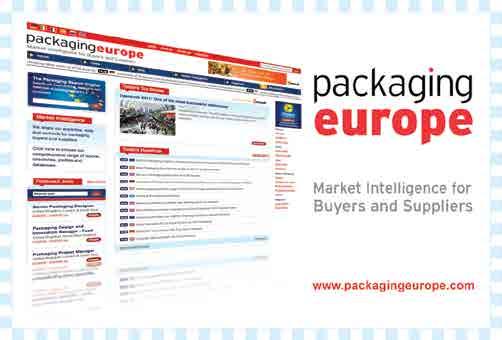