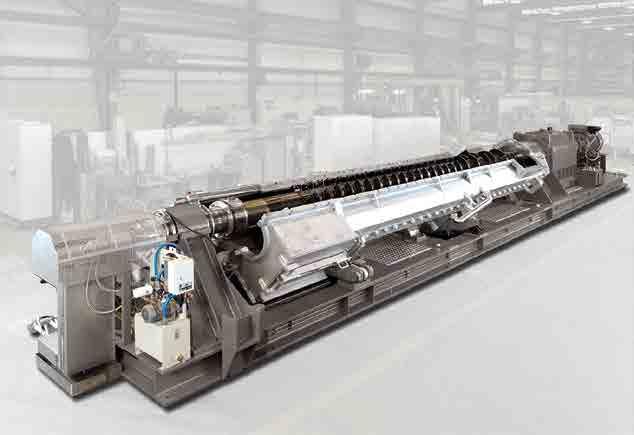
6 minute read
Compounding success Buss
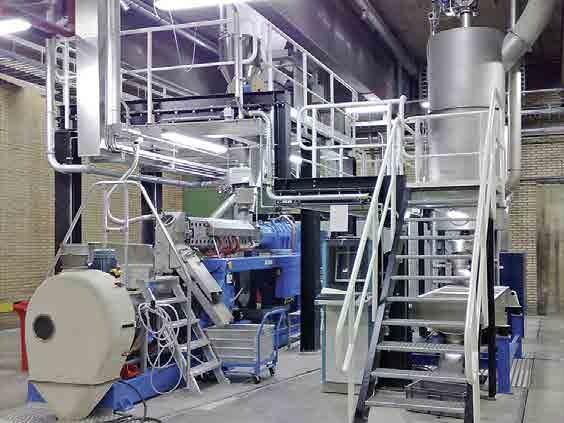

COMPOUNDING SUCCESS
Continuing innovation enables Buss AG to maintain its position as market leader in compounding technology.
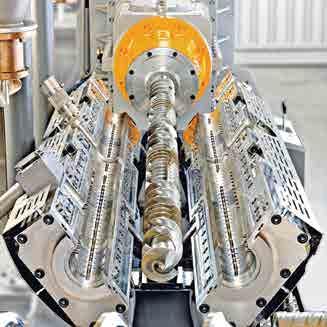
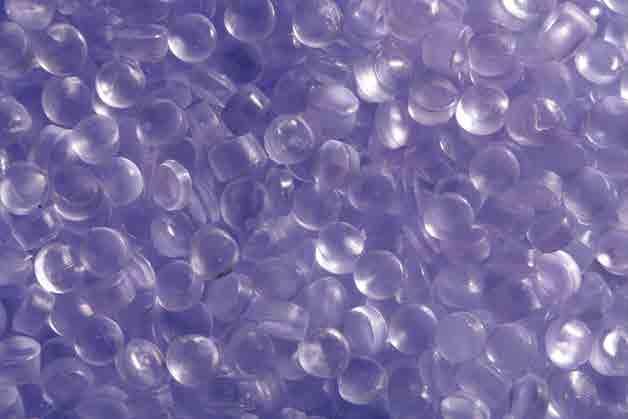
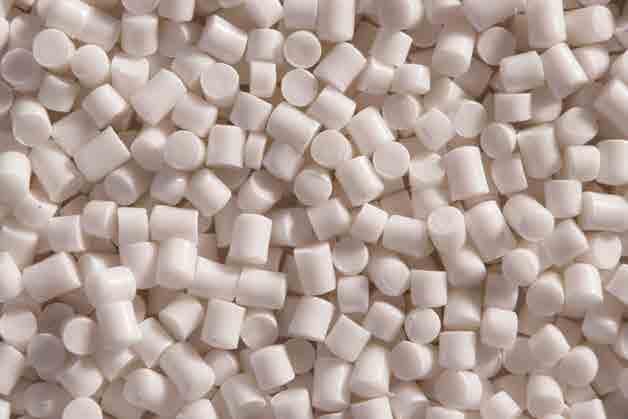
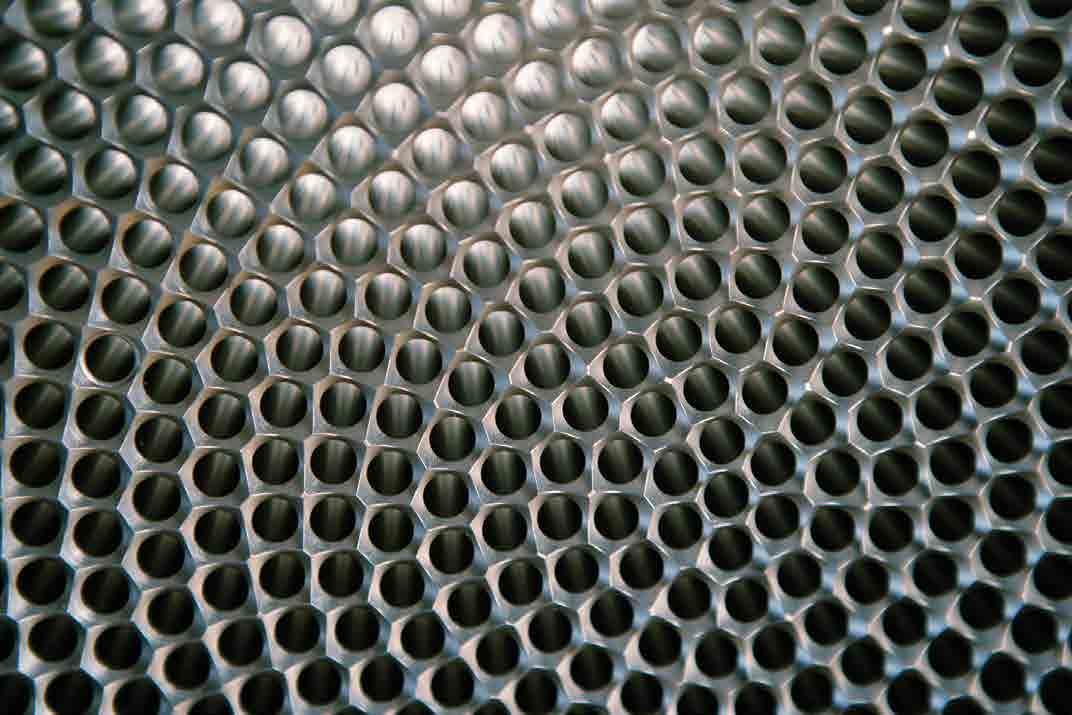
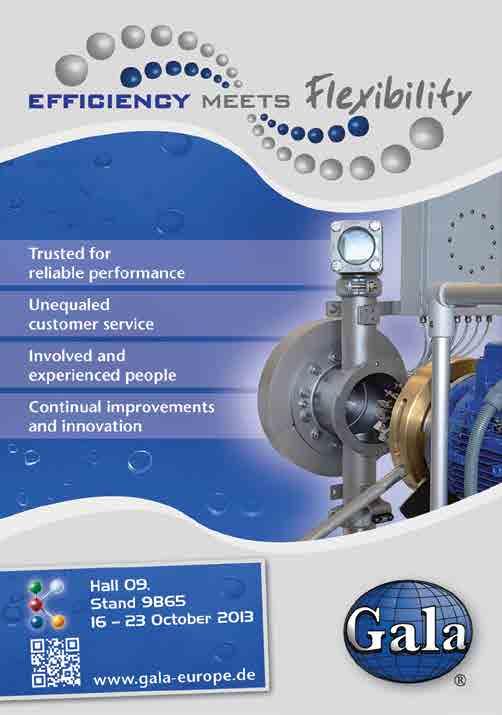
Buss AG is the global leader in kneaders for demanding compounding solutions. Based in Pratteln, Switzerland, Buss has been refining this technology for sixty years and has achieved significant advances both in technical leadership and in market positioning, above all in the BUSS core segment of temperature and shear sensitive plastics compounding.
Buss is familiar with all its customers’ processes and their differing requirements. Its focus is primarily on the niche market segments of the plastics, aluminium, chemical and food industries. Its competencies include PVC pelletising, cable compounds, masterbatches, calendar feeding, thermosets, powder coatings and toners, foodstuffs and anode paste. Buss has accumulated extensive know-how in these technologies over many years. Specific processes are tested and validated for customers in its laboratories to keep them ahead of competitors.
Buss separated from the Coperion Group by friendly agreement in January 2006 and has since been once again a free agent on the market, with a clearly defined strategy of the development of Buss Kneader technology. It has its own subsidiaries and representatives as well as its own corporate identity. The company believes that its owes its strength not to size but to its commitment to innovation, flexibility and speed of response to customer needs
The Buss Kneader
The BUSS Kneader was first introduced more than sixty years ago. Its distinguishing features are a housing with kneading teeth, and a kneading screw that performs an axial oscillation with each revolution. To enable both these motions simultaneously, the screw flights have openings through which the kneading teeth pass. The combination of rotational and axial motion in the BUSS Kneader generates a highly dispersive mixing action throughout the kneading chamber – rather than only in part of it. It is due to this homogeneous action without stress peaks that the BUSS Kneader mixes so efficiently while at the same time minimizing the temperature rise caused by shear energy input to the melt.
Today Buss Kneader polyvalent systems are ideal for numerous industrial processes such as: mixing, fusion, plasticizing, homogenizing, disperging, degassing, dissolving, reacting, crystallising and pelletising. The extremely wide application range extends from pastry to thermoplastic and thermosetting products and elastomers.
Comprehensive services
BUSS offers customers comprehensive services packages to ensure sustainable plant reliability and productivity. The basis of these packages is the fast-response service organization that has been established for all the BUSS Kneaders sold globally to date. This service organization is focused on worldwide locations that can supply customers with practically every wearing part and numerous other spare parts within 24 hours. Furthermore, the BUSS service hotline is globally available to customers for support and assistance on a 24/7 basis, 365 days per year.
BUSS has greatly expanded its services in recent years with customized service and inspection agreements. These enable customers to decide the extent of service and maintenance delegation to BUSS, and they
invariably facilitate downtime planning and maintenance cost budgeting. With modernization arrangements, plant owners can benefit in full from the optimization potential that arises after some time. And for upgrading kneaders with conventional 3-flight screw technology, BUSS offers a selection of retrofit kits – e.g. for converting individual zones to 4-flight technology. Depending on the product and the machine configuration, this can increase throughput by up to 20 per cent.
The BUSS Academy bundles BUSS compounding know-how and makes it available to customers. Their personnel can undergo thorough training here on BUSS Kneader features and operating behaviour. For specific compounding applications, customers can work out with our experts the optimal operating parameters for their existing machinery. And they also gain useful information on effective spare parts logistics and emergencies management. In this way, BUSS customers can significantly improve their compounding line efficiency at low outlay, and minimize downtime. Here again, BUSS is truly a problem solver for its customers. Single source supply
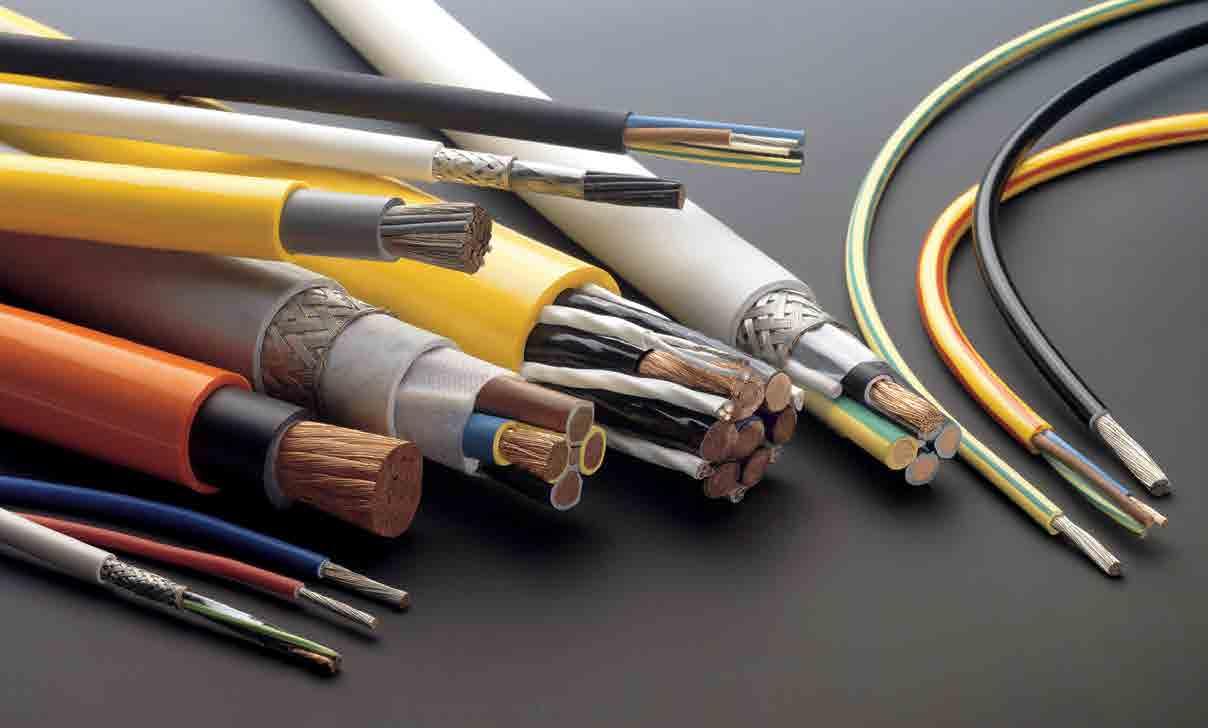
Four years ago Buss AG delivered the world’s largest cable compound line to Kabelbedrijven Draka Nederland B.V.,Emmen. Maximum throughput is 4500 to 5000 kg/h, depending on formulation. The comprehensive production line, extending over four floors of the plant building, can process eight different PVC formulations using one and the same kneader screw geometry, without any other conversion outlay. Right from the startup in March 2009, this compounding line has met all the owner’s expectations particularly with regard to product quality, dependability, operating convenience, and minimal product changeover times.
Decisive for unmatched cable compound quality is the BUSS quantec® 110 EV Kneader at the heart of this line. With a nominal kneader screw diameter D = 110 mm and processing length L = 15 x D, this high-performance Kneader features the innovative four-flight technology already practice-proven in more than 100 compounding lines. Thanks to the enlarged intake zone, even the biggest filler volumes are handled without problem. The mixing and kneading screw configuration enables exceptionally homogeneous colored compound production with high fillers content. To build up the necessary pelletizing pressure, the PVC compound is transferred through a cascade ducting system to a single-screw discharge extruder. This is followed either by dry or water-mist pelletizing, whichever is preferable, at a relatively low pressure to minimize temperature peaks on the die plate.
BUSS was responsible for the entire plant engineering, from heater-cooler premixer and gravimetric feeding system into the compounding line, to PVC pelletizing, cooling and drying for storage or bagging.
The overall concept worked out by BUSS in teamwork with the customer also met some important additional requirements, including integration of the entire compounding system in the existing plant, and time-saving erection with minimal impact on the ongoing production. BUSS engineering also covered the comprehensive central control system, focusing in particular on precise coordination between the heatercooler mixer and the compounding line, above all for startup, which now takes only a few minutes.
With regard to the customer’s demanding requirements, BUSS technical director Stefan Nägele points out that “Above all for such a complex PVC compounding line, it was decisive that BUSS assumed overall responsibility ranging from engineering, manufacturing and procurement to erection and commissioning. Without this singlesource supply, it would hardly have been possible to complete the entire plant so rapidly and cost-effectively or to attain such consistently high product quality and short product changeover times thanks to the comprehensive control system”.
Buss also recently completed a major order for China’s aluminium industry. In January 2011 China ordered two anode paste compounding lines from the Swiss company. These lines process petroleum coke and pitch into high grade anode paste for making electrolysis anodes used in the aluminium industry. Each line, both of which were installed in South China by the end of 2011, has a capacity of 40 t/h. Production startup was early 2012.
This order further strengthens the market positioning of Buss AG as provider to the aluminium industry in China – where more than ten such compounding lines are already operating. n