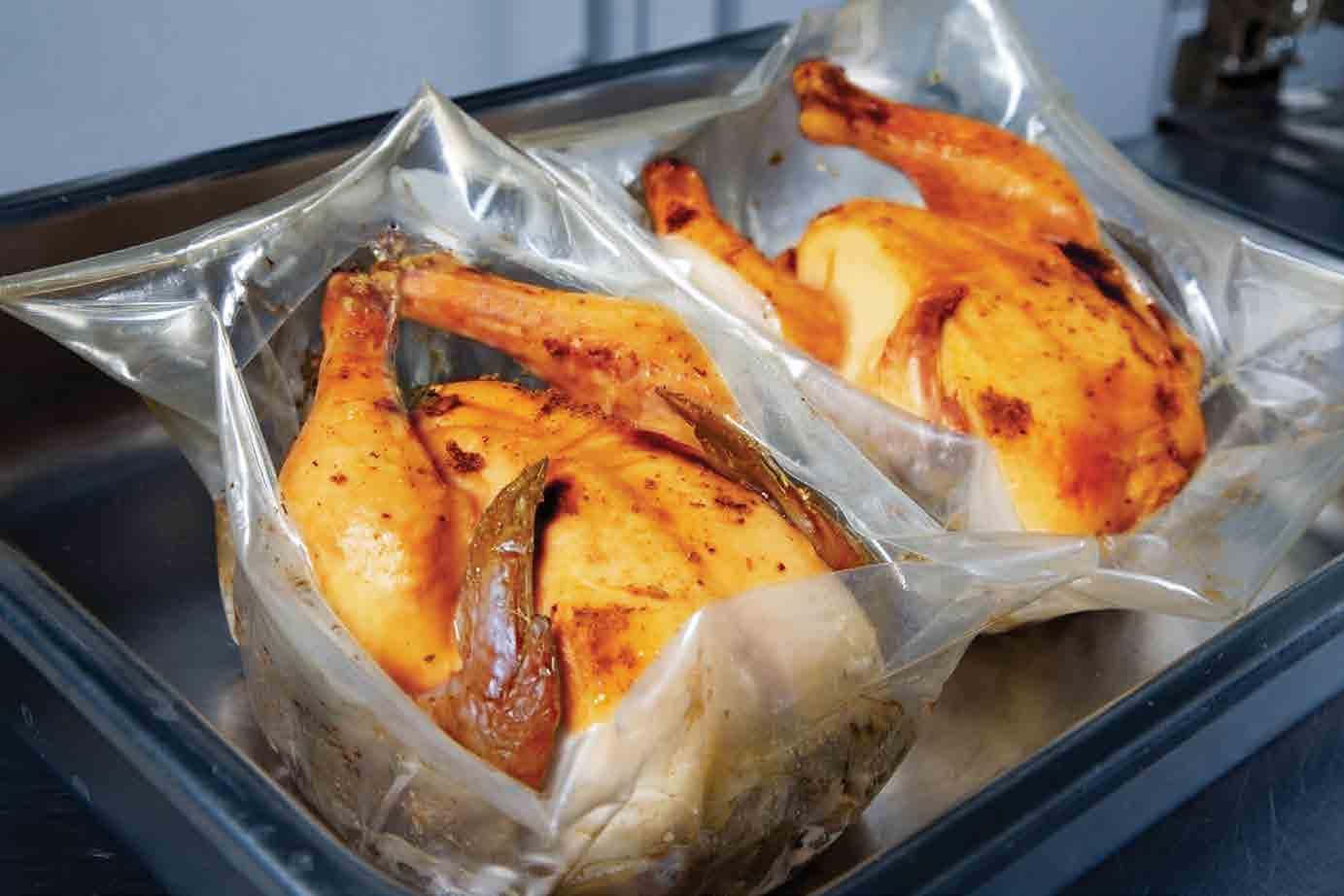
4 minute read
Optimising the performance of industrial films
Dupont Teijin Films is the world’s largest producer of polyester films for manufacturing industries. The company specialises in film products and services for advanced magnetic media and photo systems, as well as for the electrical, packaging and industrial markets. Philip Yorke reports on a company that continues to optimise its products through innovative R&D and reveals its current focus on the growing renewable energy market.
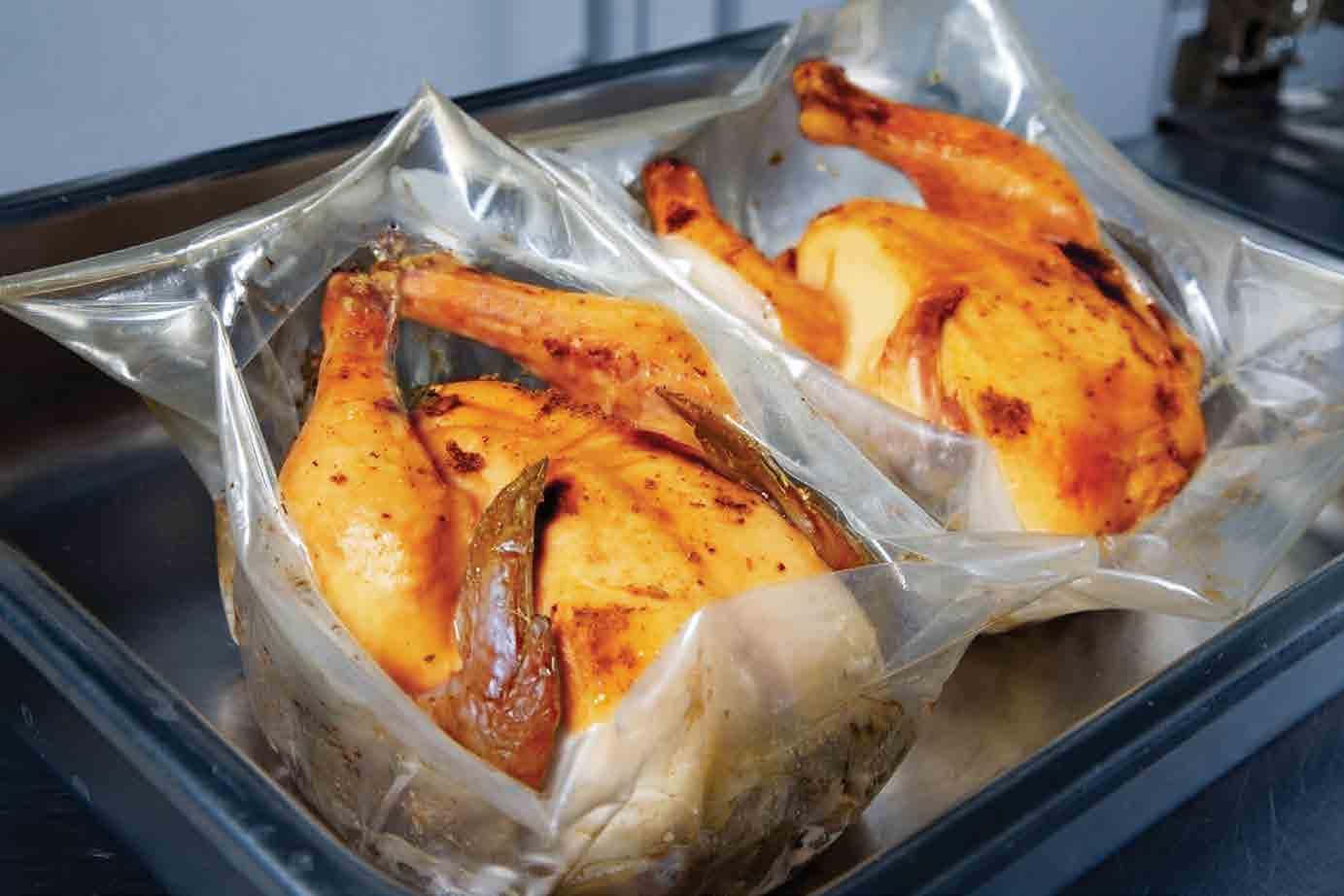
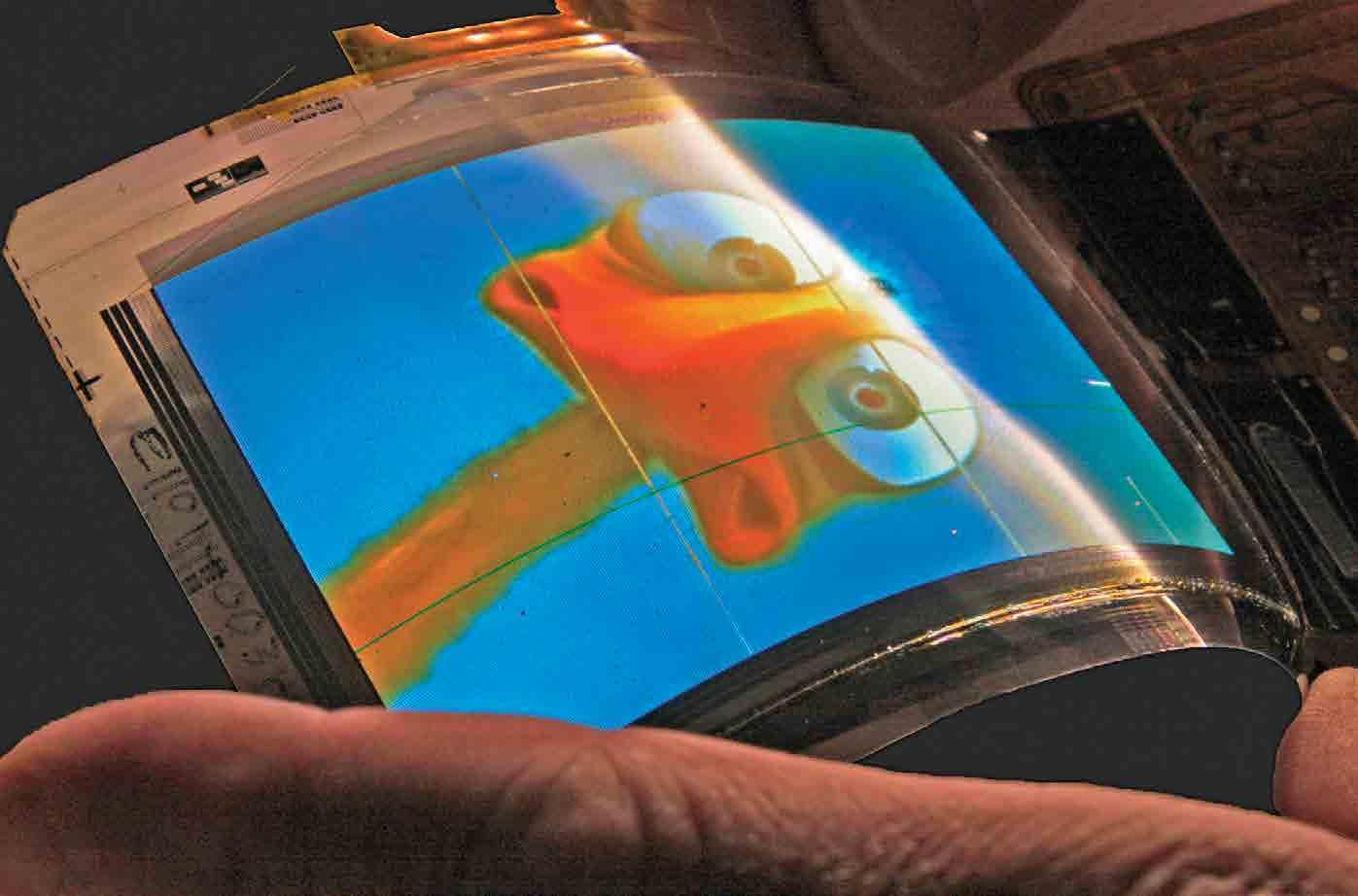
Dupont Teijin Films is a fifty-fifty joint venture between DuPont and Teijin and is the world’s leading differentiated producer of polyester films. The company was formed in January 2000 when the US chemical giant DuPont combined its polyester film operations with leading Japanese chemical company Teijin. Together they represent many of the best-known film brands in the world, such as Mylar, Melinex, Tetoron and Teijin polyester films. This global business also encompasses other existing joint ventures with DuPont, such as the Hongii Films Foshan Co of China. In 2012 the company recorded sales of more than US$1.1 billion and today employs more than 3000 people worldwide.
Research and innovation driving sales
Dupont Teijin Films has always led from the front regarding technological innovation and one area that is seeing strong growth globally is the renewable energy sector. The company has therefore continued to invest heavily in this area to produce the most efficient photovoltaic films on the market. The company’s on-going commitment to innovation, combined with its market-driven product development capabilities, has led to the development of a high-performance film that is seeing strong demand worldwide from the world’s solar panel manufacturers.
Despite Europe’s temperamental climate, it remains by far largest market for solar panel installations with a 70 per cent global share. This huge demand is thanks in part to the Pan-European government support of special grants to promote renewable energy systems for domestic applications as well for industry. Today as China and Japan both begin to embrace solar energy production in a significant way, the market for photovoltaic modules is set to increase dramatically.
This is particularly good news for the company’s state-of-the-art production facility located in Dumfries in Scotland, which makes the special photovoltaic films. More than 280 people are employed at the extensive 100 acre site, which also makes products for a wide variety of other industrial applications. These include food packaging, medical test strips, labels and ID cards and now in addition, a new film designed specifically for the solar energy market.
This new film forms the ‘backsheet’ of the solar panel which provides vital electrical insulation and resistance to moisture and extreme temperatures. Traditionally, ‘backsheets’ were based largely on a fluoropolymer material which until now provided much better resistance to weathering than polyester film. However, the boom in the photovoltaic market, combined with a shortage of fluoropolymer materials, created a gap in the market which DuPont Teijin were quick to capitalise on.
Moray Mackenzie, the site and operations manager at the Dumfries plant said, “Traditional polyester films offer inherently poor resistance to UV and water degradation. However, our in-depth experience and understanding of developing UV resistant
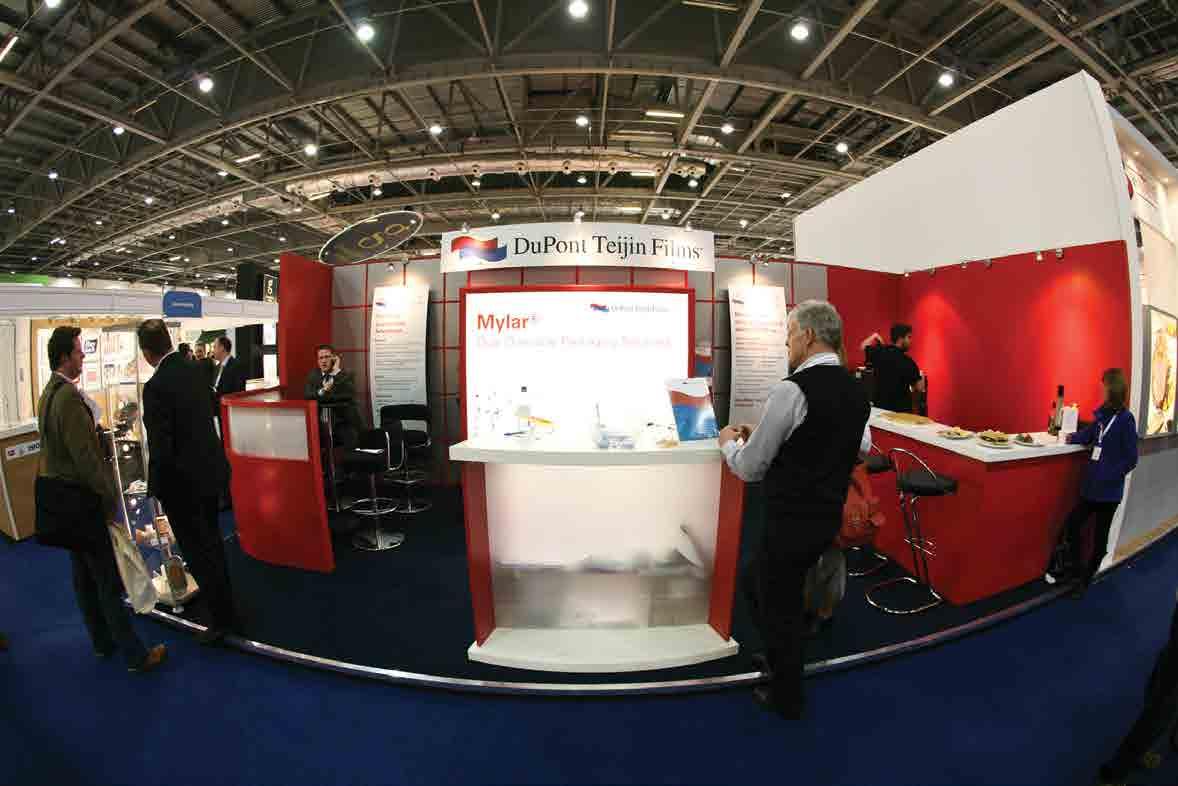
film and also hydrolysis-resistant film has allowed us to bring the two properties together. This has resulted in a unique range of high performance polyester films that offer excellent outdoor weathering resistance.”
Currently DuPont Teijin Films have a 15 per cent share of the global photovoltaic market and they have ambitious plans to grow that market share to more than 20 per cent within the next few years. This is significant growth indeed when one considers that it is an industry that is seeing consistent growth of over 15 per cent, year on year.
Hygienic, value-added polyester films
As the inventor of the world’s first heatsealable and dual, ‘ovenable’ polyester films, the Mylar® brand is the trusted market leader in convenience packaging solutions for virtually any food fresh or frozen. However, as consumer lifestyles constantly change and food safety becomes an increasingly important issue, DuPont Teijin is not resting on its laurels. The company’s scientists are taking the unique thermal and mechanical properties of Mylar® polyester films and providing value-added functions that include reduced cooking times, improved taste and texture and the control of harmful pathogens such as campylobac-
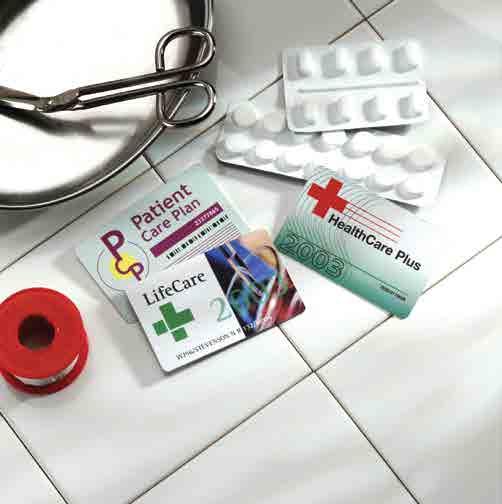
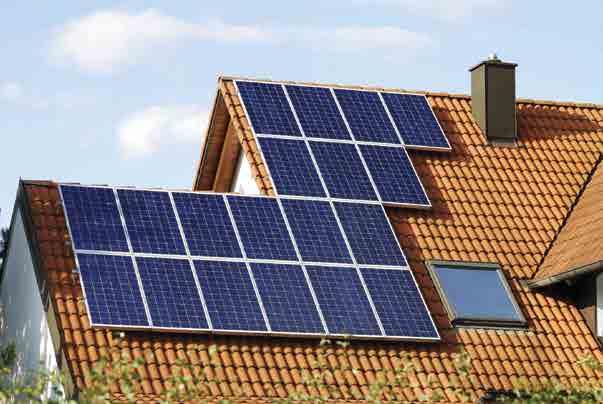

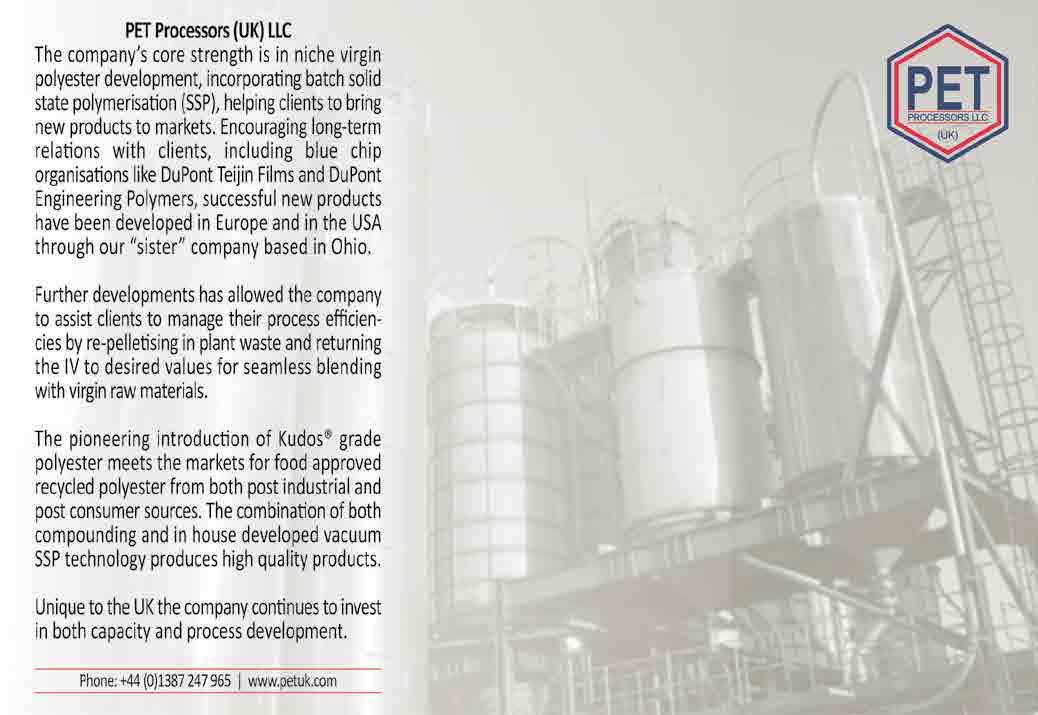
ter, and the avoidance of cross contamination during the cooking process.
At its global Technology Centre based at Wilton in the UK, DuPont Teijin Films targets its considerable innovation resources to meeting today’s hygiene challenges, which were recently fuelled by recent publicity about food safety and the need for new solutions. Using novel process capabilities, the company has engineered an active, functional effect into its polyester film which can effectively meet the real microbial challenges, such as MRSA and Ecoli, which occur in everyday situations, particularly in the healthcare and food preparation areas.
Other related work streams within the company’s R&D centre at Wilton are also making progress towards the on-line detection of sub-micron contamination and surface damage, as well as the understanding of adhesion forces at play between contamination and process surfaces. This research forms part of a wider programme to increase barrier performance through intrinsic cleanliness, thus establishing the first steps towards the OLED/OPV process. n
For further details about DuPont Teijin Film’s latest innovative film products and services visit: www.dupontteijinfilms.com