
6 minute read
Meeting all refractory needs SANAC

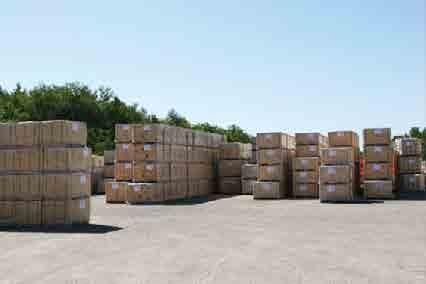
MEETING ALL REFRACTORY NEEDS
With 35 per cent of the Italian refractory market, SANAC SpA is an industry leader at national level, as well as being a successful exporter, as Barbara Rossi finds out. Quality, price and immediate delivery of products are the differentiating factors working in the company’s favour.
SANAC (Società Anonima Nazionale Argille e Caolini) SpA has been working in the refractory field since 1939, having been established as a state-owned minerals company by IRI (Istituto per la Ricostruzione Industriale) in Sardinia. The company was privatised in 1995 and today belongs to the Riva Group.
With its wide range of products the company practically covers the totality of refractory applications. It operates from four sites, all based in Italy, and has a production output of about 200,000 tons a year, a yearly turnover of €150 million and 400 employees. It manufactures a wide range of the refractory products necessary for plant construction, maintenance and operation in a variety of sectors, ranging from steel, pig-iron, non-ferrous metals and glass, to cement, lime, ceramics, petrochemical, chemical, chimneys, boilers and incinerators.
One of the company’s works is located in Sardinia, while the other three are based in northern Italy. The Gattinara site, north-western Italy, specialises in the production of aluminous fired and chemically bonded bricks, basic resin bonded fired bricks, aluminous and basic unshaped materials, products for bottom casting, zirconia spouts and special pieces. The Sardinian plant, Grogastu, also manufactures aluminous fired and chemically bonded bricks, alongside Al2O3-SiC-C, Al2O3-MgO-C and
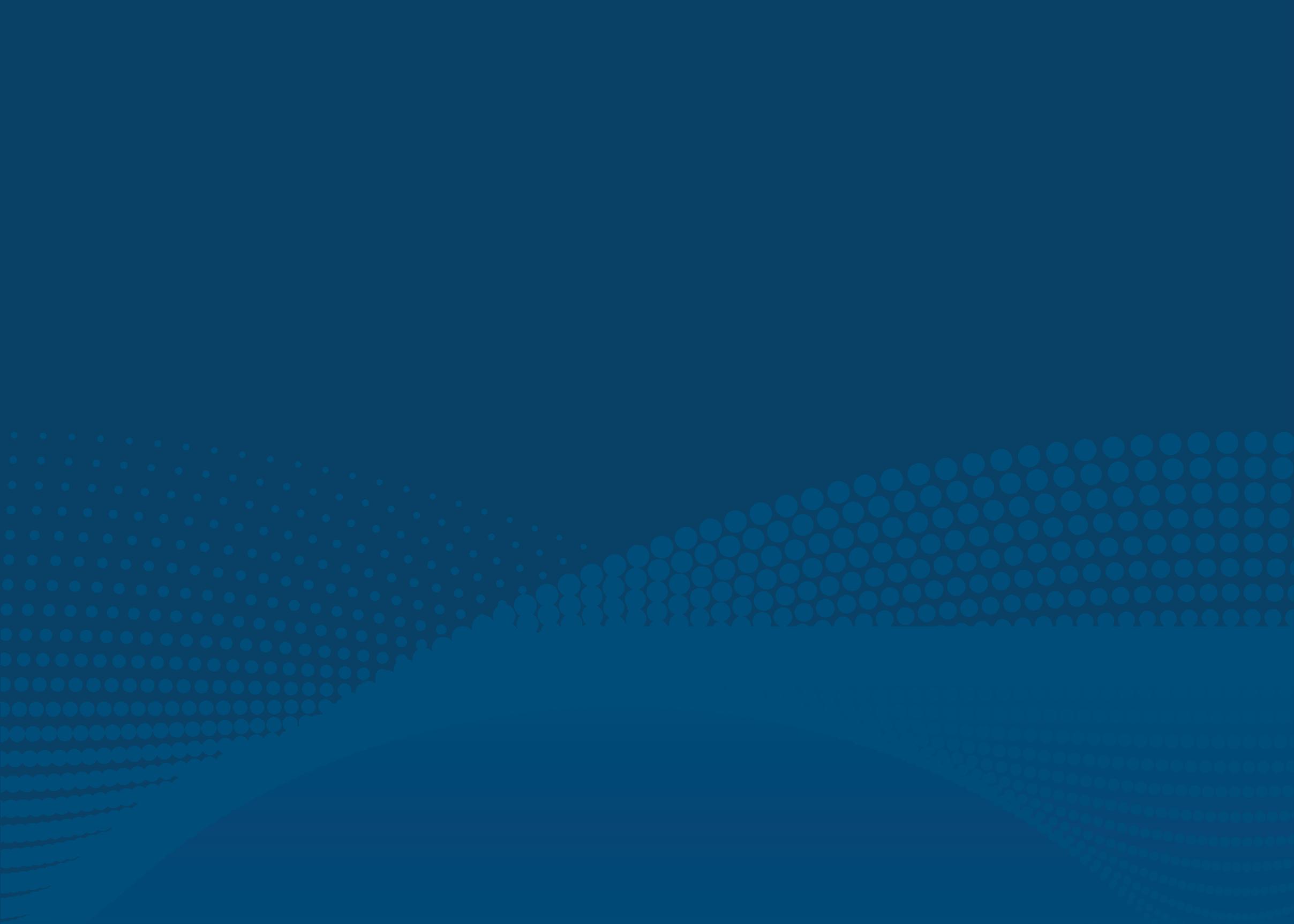

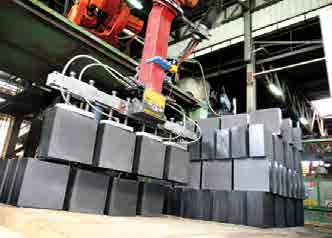
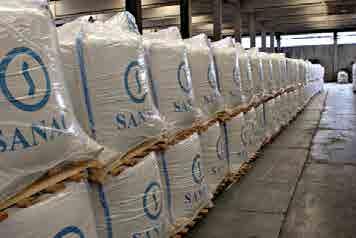
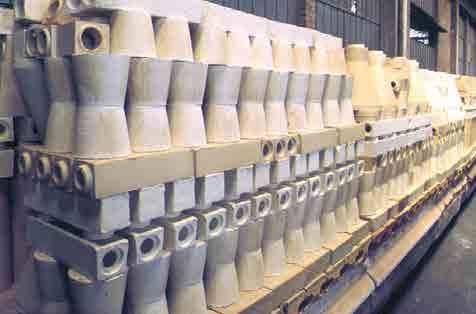


basic fired bricks; while the works in Massa, northern Tuscany, specialises in resin bonded MgO-C bricks, basic unshaped materials, purging plugs, tap-hole blocks and rings, and sliding gate plates. The facility in Vado Ligure, west of Genoa, as well as manufacturing monolithic alumina and thixotropic materials, pre-shaped aluminous products and lances, and purging systems, also houses the sales and the project departments, the research and development laboratory, technical assistance and quality assurance.
Tailor-made solutions
SANAC is totally aware of the fact that there isn’t a single refractory which can represent a standard ideal solution; every customer has different needs, even for similar production processes. SANAC is able to produce a wide range of products, thanks to its capacity to manage different new materials, resulting in the obtaining of the right mix for the production of tailor-made refractories fulfilling any customer request.
30 per cent of production is for export, reaching several countries in the world. In Europe, the company exports to Austria, Belgium, Finland, France, Germany, Greece, Luxembourg, Russia, Spain, Sweden and Turkey, while countries served in other continents include Canada, Chile, Mexico, Peru, Algeria, Tunisia and Taiwan.
SANAC invests 2/3 per cent of its annual turnover in R&D on a yearly basis. This is because, especially due to the advances achieved in the last few years in terms of industrial process developments, there has been an ensuing demand for increasingly sophisticated quality materials. In order to be at the cutting-edge and ready to fully respond to market demand for innovative products, not only does SANAC have individual laboratories at each of its plants, for production checking and testing, covering all stages from raw materials to finished products, but it can also avail itself of a central research laboratory at its Vado Ligure site. Thanks to the fact that this laboratory possesses the most modern instruments suitable for most sectors’ technological requirements, the company can carry out its activity in applied research, new products manufacturing and development, improvement of existing products and relevant manufacturing processes. A whole range of test are carried out here, including boron content in magnesite by colorimetry, permeability, granulometry, rupture modulus, compressive strength, density, total and apparent porosity, hydration resistance, thermal resistance in water or air, thermal conductivity, soluble tar content, unshaped setting time, unshaped workability, thixo and self-flowing vibration time, ramming and plastics workability, and slag or fused metals attack resistance.
The company is engaged in researching sources of European raw materials which could be used in the refractory process and is experimenting with supplies from Russia. The company came to this decision because it expects that China, a major supplier of these products, will shortly be unable to perform this function,
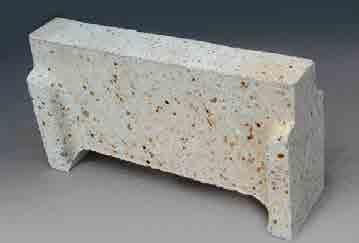
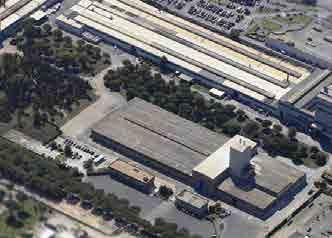
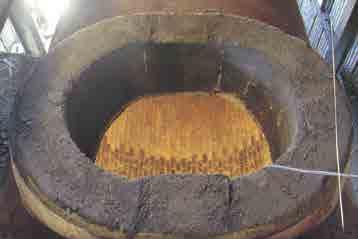
Premier Periclase Ltd
Premier Periclase Limited, a fully owned subsidiary of RHI AG is a manufacturer of high grade Seawater Magnesia, in Drogheda, Ireland exporting Magnesia products worldwide.
Our unique “Large crystal” Dead Burned Magnesia product is mainly used in the manufacture of Refractory linings for the Steel, Glass, Cement and Non Ferrous Industries. Linings containing our Large Crystal Magnesia continuously show impressive results in the most severe wear areas of Steel convertors, ladles and other appliances exposed to extremely high temperatures.
Our Magnesium oxide powder “TechMag” is suitable for high activity use in Agricultural, Chemical. Industrial and Environment applications.
Our Magnesim Hydroxide “ECOMAG” is an aqueous suspension and a cost effective means of neutralising and removing heavy metals in waste water streams.
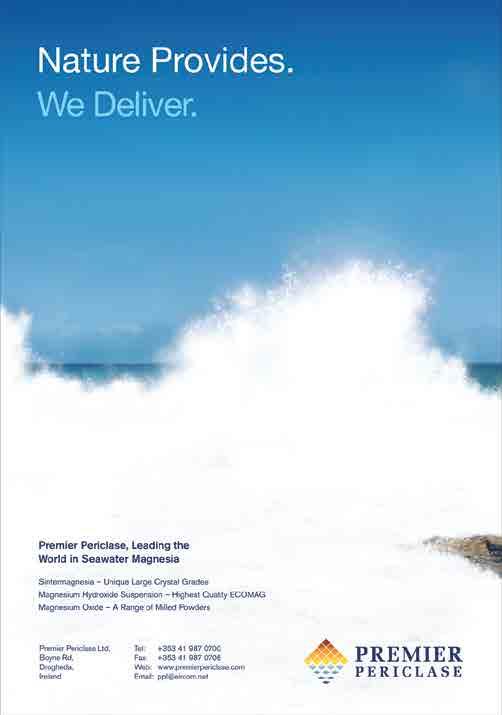
due to its own increasing internal demand. In fact, apart from dolomite, quartz and some types of clay, and despite the existence of plants engaged in the extraction of magnesite from sea water, Italy is not rich in raw materials for refractory production, hence they have to be imported.
Another priority in terms of investments is improvement in safety and environmental standards, achieved through the implementation of technology; alongside this there is a regular updating of the machinery used for production at the different sites.
The experience and business insight accrued over the years represent real assets for SANAC in the current difficult economic climate. Another asset at its disposal is its technical assistance office, which is a real benefit to clients, as it fulfils tasks which were once carried out by the customers themselves, but which nowadays they may have difficulty in performing due to the reduction of staff levels in the iron and steel industry. SANAC’s ability to provide this service offers a saving in manpower costs for its clients. Furthermore, SANAC keeps a full stock of refractory materials, a fact of extreme importance because it guarantees quick deliveries at a time when the majority of clients no longer wish to keep a warehouse or stock of goods. n
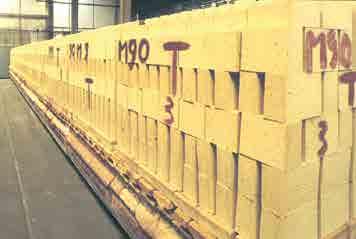
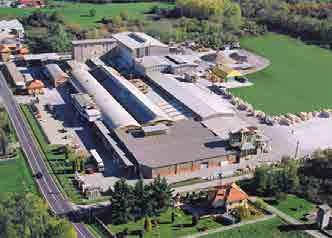
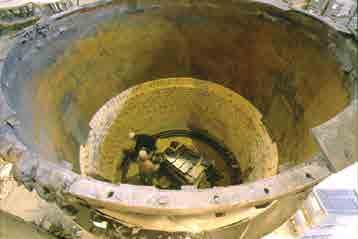