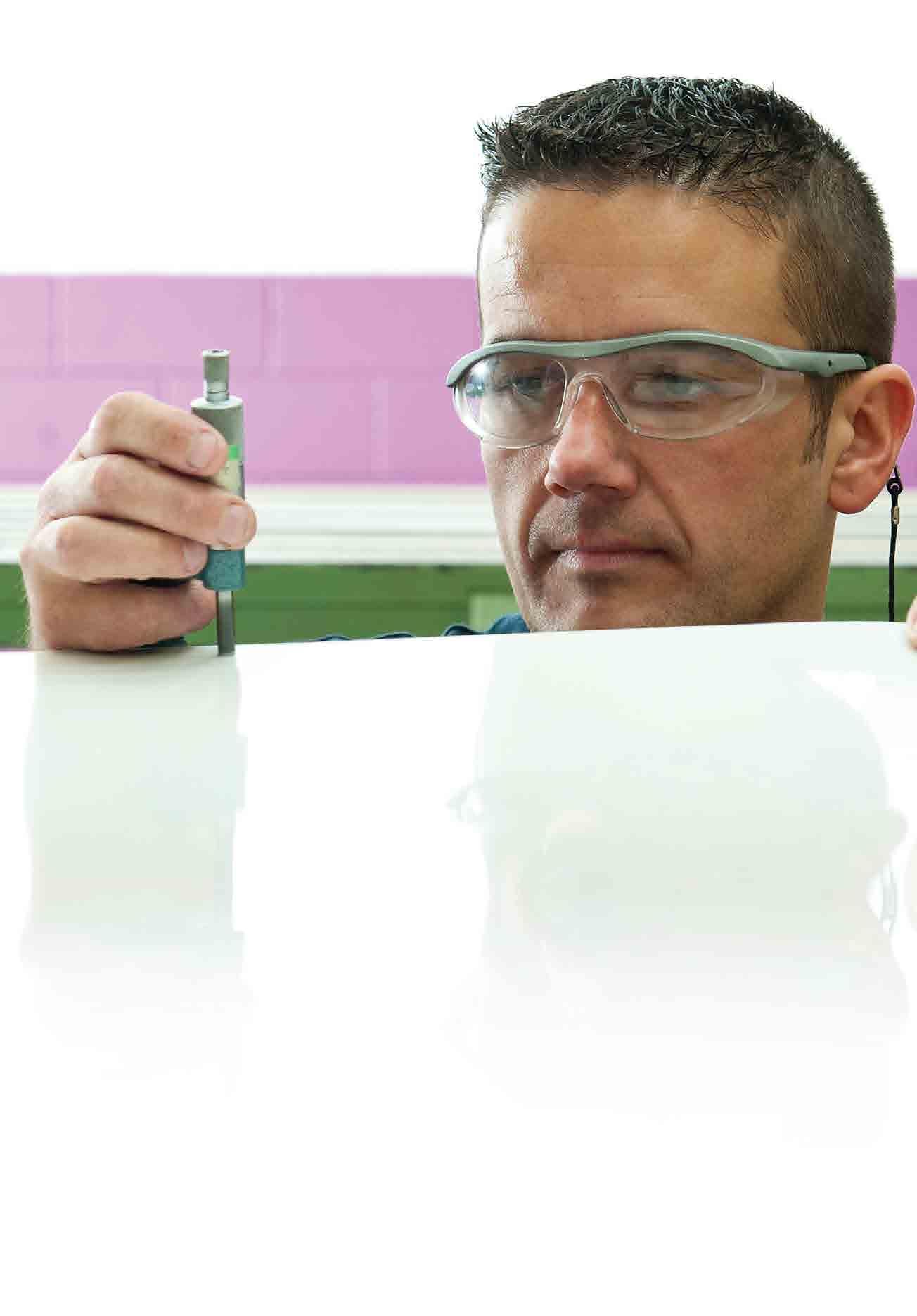
5 minute read
Putting a gloss on it Athlone Extrusions
PUTTING A GLOSS ON IT
Athlone Extrusions is known for its thermoplastic sheet products. As it launches its new Durogloss range, Abigail Saltmarsh looks at the company.
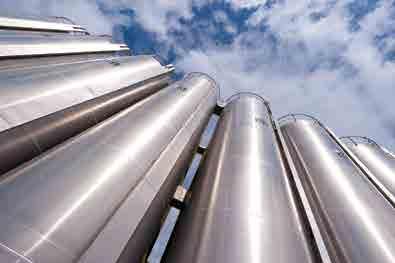
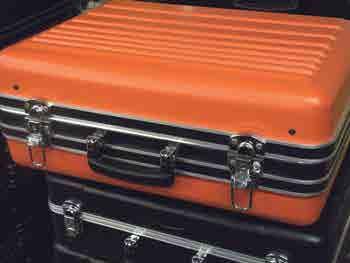
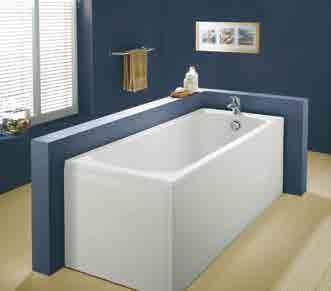
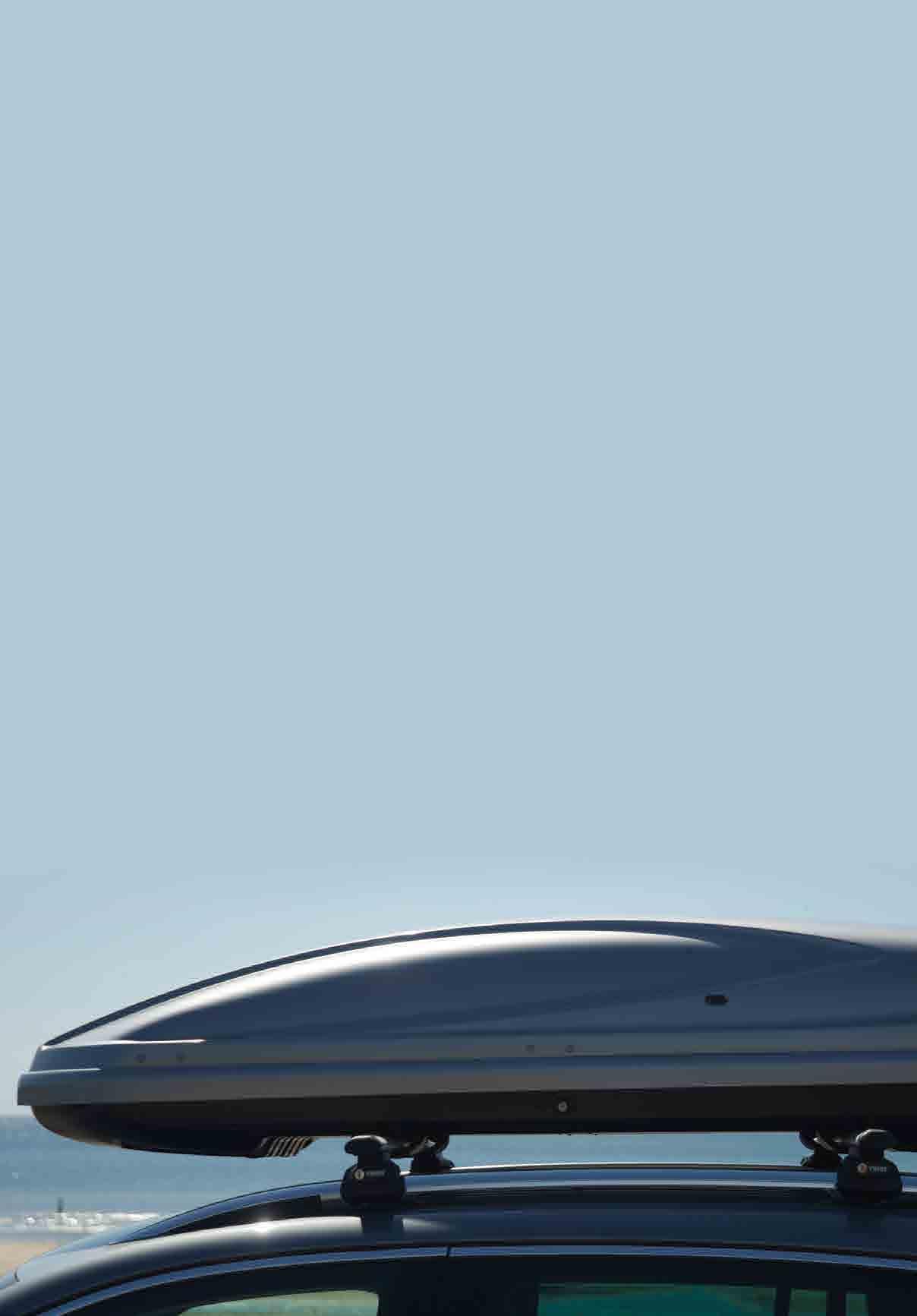


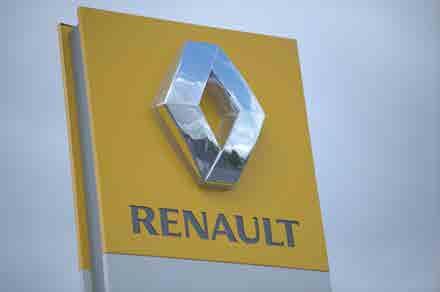
AS a leading European manufacturer of thermoplastic sheet and film products, with more than 40 years experience, Athlone Extrusions is known for its innovation. The company has a reputation for its ranges of polystyrene, ABS and PMMA/ABS, which have a broad array of applications in industries ranging from automotive through to sanitaryware.
Now, as sales and marketing manager Robert Kearney and commercial manager Adrian Dickson explain, the Ireland-based operation is starting to make waves with Durogloss, a co-extruded ABS/PMMA sheet for the furniture industry.
“This is a very high end, high gloss product, which cannot afford to have any blemishes on it at all, and we are able to produce it to the very highest standards required,” says Mr Dickson. “We only have a limited number of competitors in the world in this area and we are finding that it is already being very well received.”
Growing markets
At its facility in Athlone, Ireland, the privately owned company employs approximately 140 people and runs 14 extrusion lines and an in-house colouring compound. It has a production capacity of some 30,000 tonnes.
“We have these three main groups of products and within those we have subgroups,” explains Mr Kearney. “We produce about 500 tonnes a week for a worldwide customer base.”
About 45 per cent of the company’s turnover is generated through its sales in its main market of the UK but it has more than 600 customers across 40 countries. Potential for growth has been identified in Turkey, the BRIC countries and South Africa.
“India is a huge growth market,” he adds. “There is a demand for products at the high end of the market and where there is added value, especially for products from Europe.”
Reputation in polystyrene
In polystyrene, Athlone Extrusion’s products include a range of options which are used for applications from point of sale and packaging through to bath panels. UV stabilised polystyrene can be used for the likes of outdoor advertising or phone or radio masts.
GPPS or general purpose polystyrene is a clear low impact product available in crystal clear or colour tints in smooth and embossed patterns. It is not readily vacuumformed and is most commonly used in secondary glazing applications and in the fabrication industry where it acts as a more economic alternative to PMMA (acrylic), SAN, PET and other clear polymers.
High impact polystyrene (HIPS) is a rubber modified version of GPPS. This polymer offers much higher impact strengths and is easily vacuum-formed. It exhibits great versatility and provides a low-cost route to the moulding of a diversity of products in a multitude of industry sectors.
Internal and external
In ABS, Athlone Extrusion again produces the full spectrum, from recycled ABS through to super high impact ABS. Applications include the likes of instrument cases, automotive interior trim, machine housings and signage. Foil-laminated ABS is manufactured for use in end products requiring a decorative finish, as well as door panels.
“In PMMA/ABS, we have our Durosan and Durosun ranges,” explains Mr Kearney. “These have internal and external applications, such as sanitaryware and body panels for construction and agricultural machinery.”
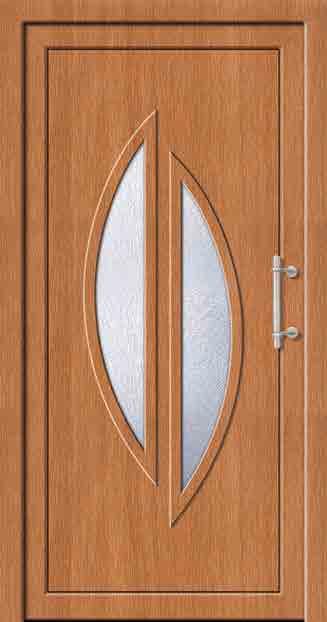
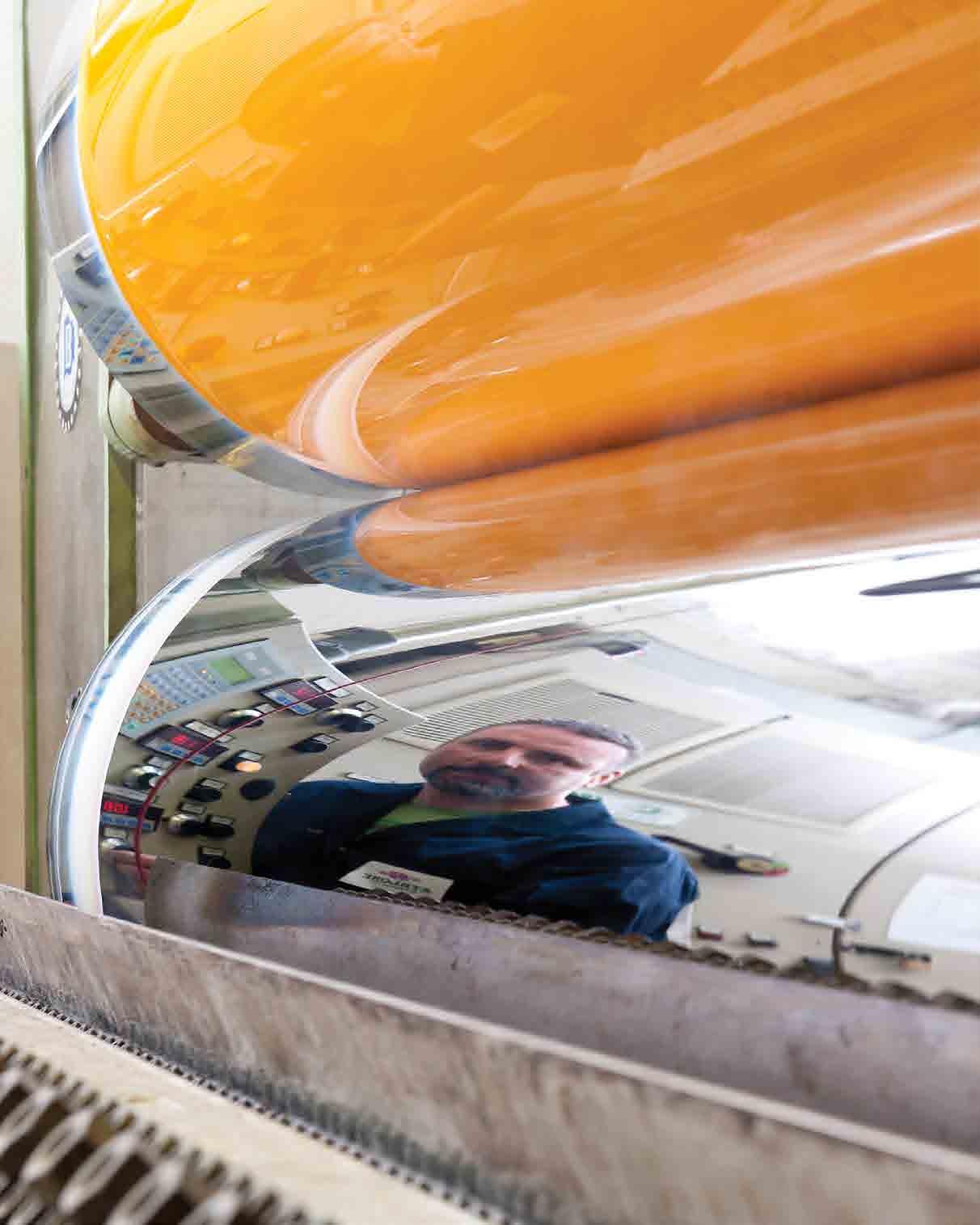
Opportunity for high gloss
But it is Durogloss that is currently causing such excitement at Athlone Extrusions and across its customer base. This co-extruded ABS/PMMA sheet has been developed by the innovative research and development division specifically for the furniture industry in which its inherent high gloss and scratch resistance is complemented by the company’s renowned colour matching ability.
Durogloss is available in sheet or reel configurations. Acrylic foils are flat-laminated to either MDF or chipboard panels using specially formulated hot-melt PUR adhesives and find their way on to kitchen cabinets, wardrobe doors and bathroom furniture etc. The product is UV stable, allowing it to be installed in areas of direct sunlight without risk of long-term damage.
“We started development on this about two years ago after realising there was a growing market for it, brought about by the likes of IKEA and other companies that were selling kitchen and other furniture products in high gloss,” says Mr Dickson. “With our existing competencies and technologies, we saw an opportunity in the market.”
A market leader
By the end of 2013, Athlone will have invested some £1.5 million in the production of Durogloss. Existing machinery has been upgraded to required standards, the plant building itself has been improved and staff have been taken through programmes.

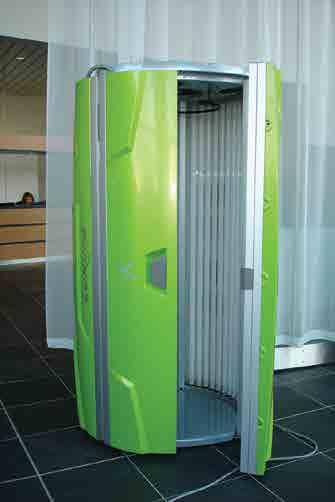
The company continues to develop its other product ranges too – including a specialist ABS/TPU – and is aiming for approximately 10 per cent growth every year for the next five years.
“Traditionally, we have grown organically in the past and we do have existing capacity for where we are now but now we are thinking more about acquisition and, long-term, the benefits of moving into a new purpose-built facility,” said Mr Dickson. “We need to think about where our customers are and where we can serve them most efficiently from.
“We would, however, always have a production facility in Ireland. We are proud of the flexibility and quality we can offer from here and hope to continue to grow profitably as we introduce more innovative products and continue to be seen as a market leader.” n
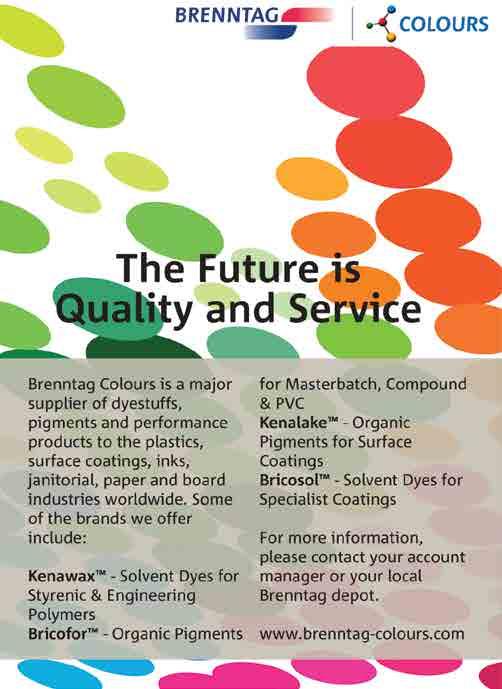