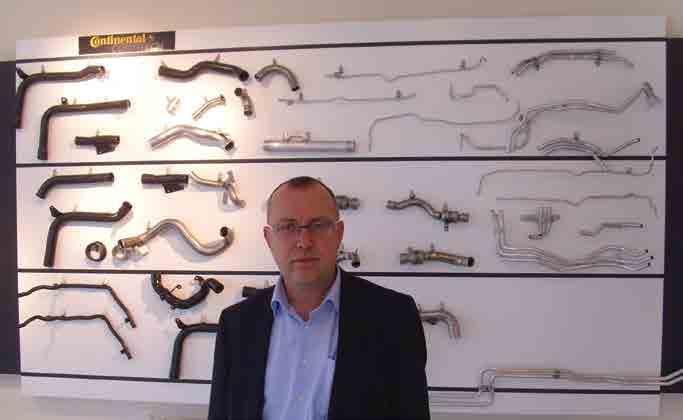
5 minute read
Breaking through the economic gloom Hüner Kriko
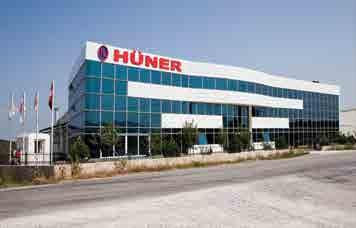
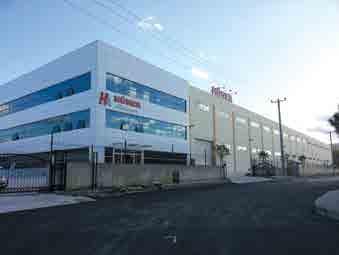
BREAKING THROUGH THE ECONOMIC GLOOM
While many countries in Europe are discussing rescue plans for their troubled economies, Turkey quietly continues to grow, in part thanks to the investments from its solid base of manufacturing businesses, many of which are family run. Hüner Group Companies are typical of these businesses, and have been manufacturing spare parts for the automobile industry since 1975. Its general manager, Ergun Günevi, talked to Aynur Adiller about the company’s development.


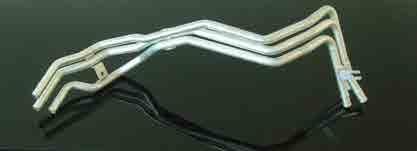
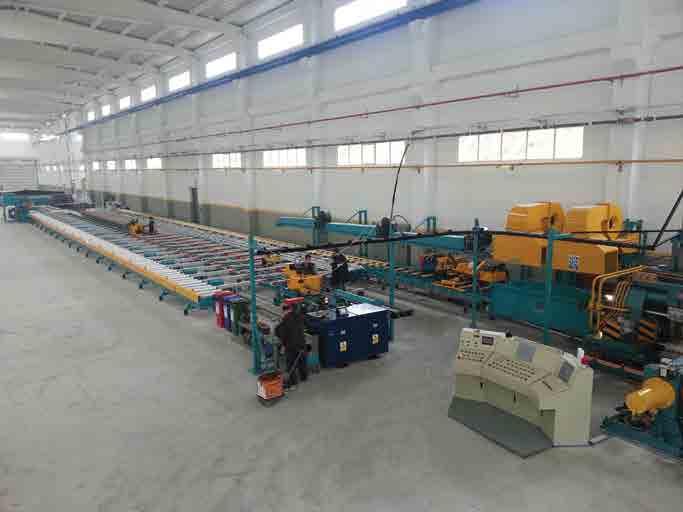
Hüner Group’s first member, Hüner Kriko, was founded by Hüseyin Karabacak, when, while working as Chief of the Acquisitions Cost Analysis Department of the TOFAS, a FIAT subsidiary, he observed problems with the Italian car jacks that the company used for lifting windshields and decided to set up his own firm to manufacture these parts domestically. Ergün Günevi now remembers fondly the days when the company began production of in a 12m2 workshop, selling its jacks to Mr Karabacak’s former employer.
A decade later, as demand for TOFAS products increased, Hüner Group benefitted from bigger contracts and began a period of growth. The company then took on new partners and became an established family business in 1985. In 1989, it opened a new production facility in the Demirtaş Organised Industrial Zone (DOSAB) in the city of Bursa, upgrading from its workshop to a large factory with a 12,040m2 enclosed facility and 7000m2 of open land. With this bigger facility the company was able to expand its product and service portfolio to include the manufacture of metal sheets and pipes and metal injection capabilities and thus offered complete products suitable for various assemblies. Initially it continued to produce parts exclusively for TOFAS, but later also began to serve other companies, including Continental Contitech, Tristone, Hutchinson, Veritas, Avon Automotive and FIAT. Moving into exports
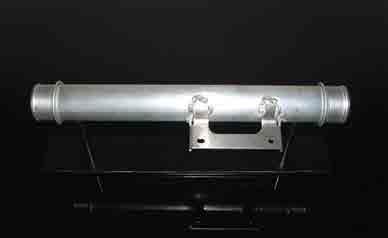
As Mr Günevi explains, in 2002, as the Turkish state was encouraging its manufacturers to focus on exports, the company began to make investments to gain the quality assurance certification needed in order to open itself up to new markets. This was another key turning point for the Hüner Group, which a few years later led to the acquisition of new customers, as the company was able to offer a more complete range of services to the automotive industry.
In 2009, it made another significant investment when it bought a factory in the Hasanağa Organized Industrial Zone (HOSAB) which it allocated solely to the manufacture of formed metal pipes. This 17,000m2 factory
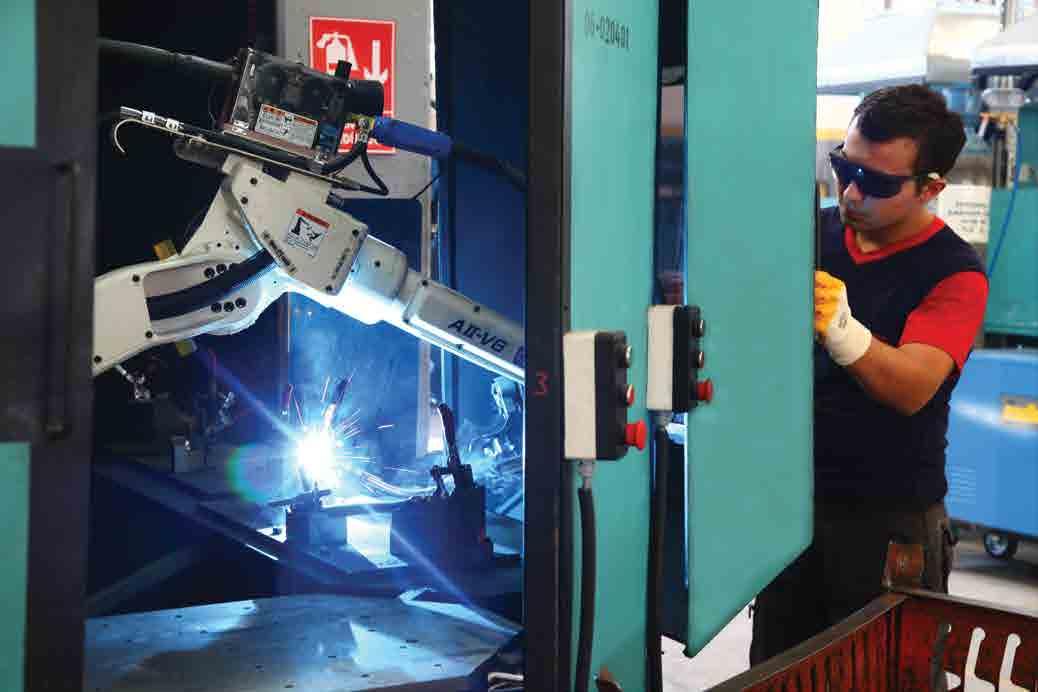

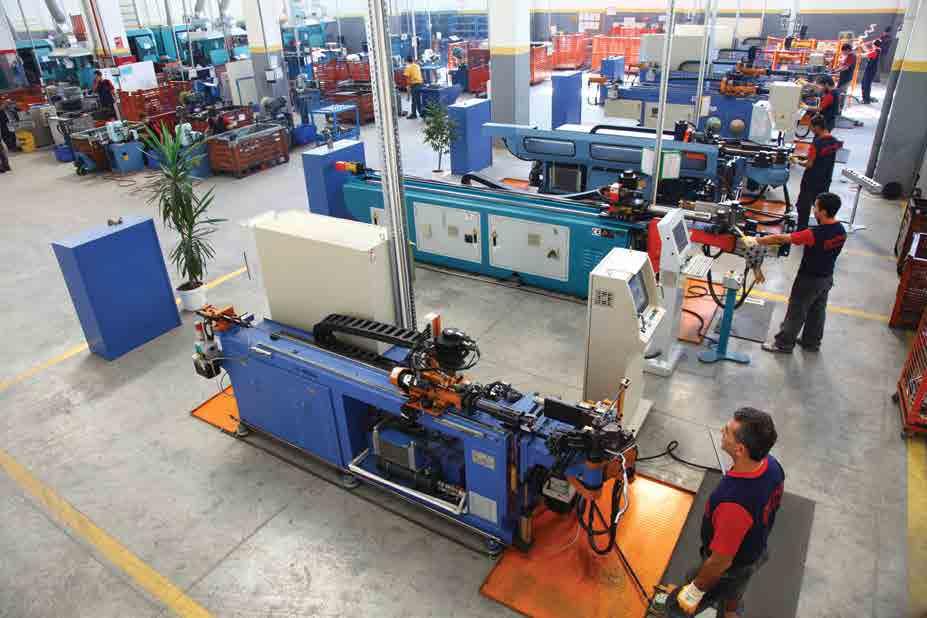
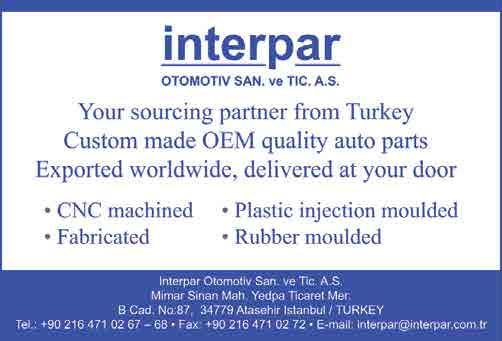
is highly efficient as it is built on only one floor where the pipes are cut, bent, end formed, welded, tested and packed all under one roof. The factory now has thirteen fully automated pipe bending machines and nine welding robots, and 90–95 per cent of its products are exported. Some of the pipes, which are designed and tested entirely in-house, are used in the latest models of Jaguar Land Rovers and Porsche.
The fourth stage: A move into aviation?
Speaking of the effects of the 2008 financial crisis and the subsequent instability in the Eurozone, Mr Günevi states that the ill-effects were relatively limited in Turkey and highlights the importance of the company using its own capital to be able to continue investments, rather than relying on bank credits. He also describes how, although the economic difficulties led to the Hüner Group losing some profits from older projects, it was able to compensate by adapting to the changing needs of the market.
In 2011, the Hüner Group chose to make investments in aluminium and ordered the state-of-the-art 1540 UST (6”) high capacity aluminium extrusion line. At the beginning of 2013 the line began production of aluminium profiles in a variety of sizes, particularly for use by the automotive sector.
The Group has grown even further after its investment in a new mould design and production plant which began to be put into place in 2012 and is expected to start production in the second half of 2013. The company’s know-how in this area has been developing at their plant at DOSAB since 1989. Its expertise in the area will be used extensively in the fourth factory and it is from here that, aside from the automotive sector that the company has been serving for numerous years, it also plans to enter a new area by responding to the needs of the aviation and railway industries.
Scope for growth
Together, Hüner’s factories are currently working at two-thirds under capacity and with a fourth plant on the way there is plenty of scope for growth. Mr Günevi says that the company’s turnover has increased by 25 per cent from 2009 to the end of 2012, reaching 17 million Turkish lira. The company has plans to increase this to 25 million.
Some of this growth is expected to come from exports – the company’s most important markets being in Germany and Italy, with other clients in Portugal, Poland, Macedonia, France, China and the USA. Mr Günevi says that the company’s export ratio currently stands at around 65 per cent and he hopes it will reach 70 per cent by the end of this year.
He also explains that all four production facilities are now registered as separate entities, meaning that Hüner is now established as a group of companies. Executives are focusing heavily on improving management processes and establishing conventions to enable the different companies to share information, control processes and to follow through on established targets. n
