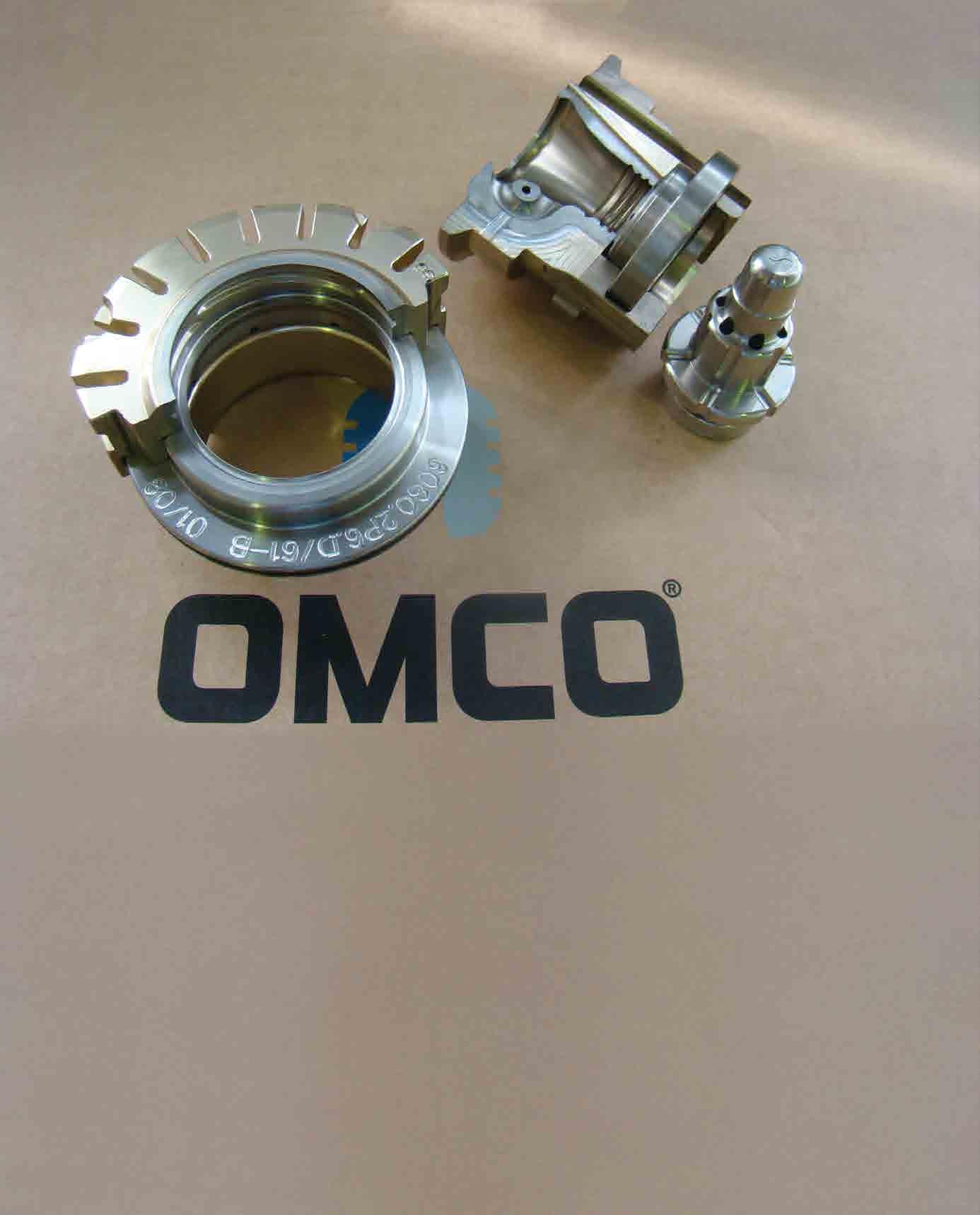
5 minute read
Unrivalled expertise in glass moulds Omco
UNRIVALLED EXPERTISE IN GLASS MOULDS
Omco is a global leader in the development and manufacture of tailor-made glass moulds for industry. Philip Yorke looks at the company’s latest achievements, its strategic investments and its move into new market sectors.
Omco (Overmeyer Mould Corporation) was a major producer of glass moulds in the USA, when it decided to establish a division in Aalter, Belgium, in 1964 to strengthen its presence in the European market. Initially the company outsourced its requirements to third parties but by the early 1970s the demand for its products had increased to a point where it was necessary to establish its own foundry, and when the Bekaert foundry in Hamme, Belgium came up for sale, Omco purchased it without delay.
Difficult trading conditions in 1984 led to a management buy-out and from that time onward, Omco became a Belgian company. Following 20 years of consistent growth, Omco NV merged with BMT NV and subsequently became a publicly traded company. In the year 2000 a second foundry was acquired in Slovenia which was then
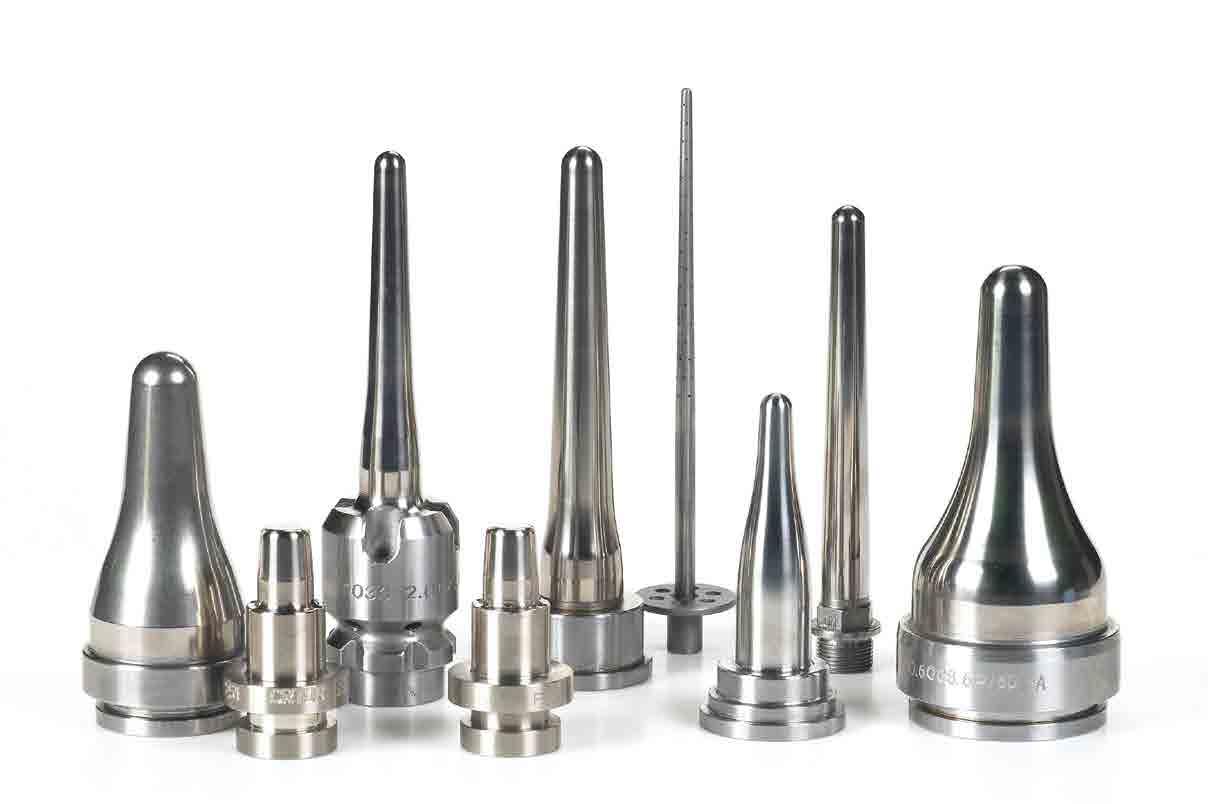
geared to produce industrial glass moulds for Croatia and Austria whilst the company’s main foundry in Hamme became increasingly focused on manufacturing moulds for customers outside of the group.
Five key steps to success
Omco’s global success is built around five key steps: engineering, foundry, manufacturing, quality assurance and moulds. Each of these business units is supported by a multinational group of engineers who are available to service its customers worldwide. The company’s foundry division has strategically located facilities in Belgium and Slovenia from which it can guarantee flexible supplies of high-quality cast iron and aluminium bronze castings. In addition, the company’s manufacturing group has been equipped with the latest state-of-the-art CNC and robotic machinery. These modern and comprehensive facilities mean that Omco is able to offer a diverse range of precision equipment and welding techniques that are able to meet any challenge and in turn offer significantly increased mould life.
Omco offers products for the hollow glass industry based upon specially developed castings in both grey and nodular iron and aluminium bronze. Throughout its many facilities the company has established the required level of expertise to enable it to manufacture any mould for any machine, whatever its shape or size. The company specialises in the production of glass moulds for a diverse range of industrial applications including food, beverages, spirits and pharmaceuticals.
The company’s ongoing success is also enhanced by its highly specialised expertise in the manufacture of pieces with complex geometry, including core-intensive mould production techniques. Furthermore, Omco’s foundries offer aluminium bronze castings as well as machining, painting, galvanising, pressure testing and many other value-added customer services.
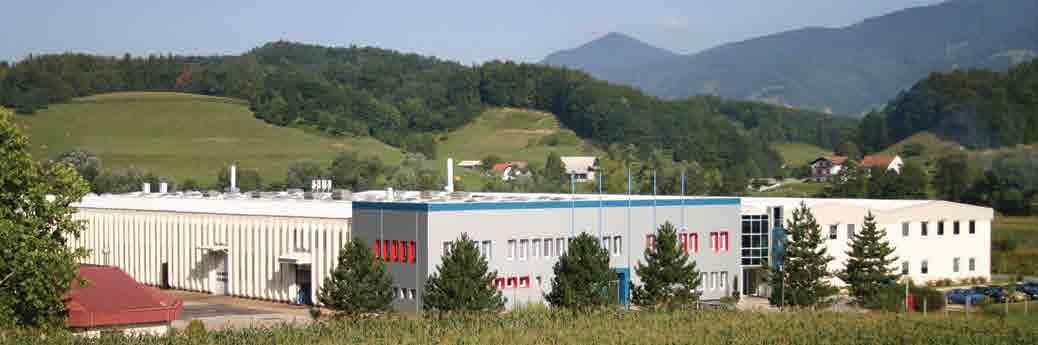

The fine quality of the metals used by the company is assured by ISO-TS standards certified by Lloyds. In a new move to provide better logistics support for its customers, Omco has recently invested in a variety of new logistics systems including a fully automated warehouse, which improves the efficiency and accessibility of its products which are primarily destined for the automotive markets worldwide.
Energy-efficient recyclable containers
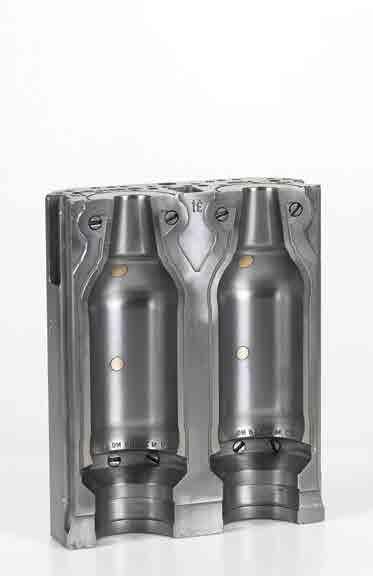
The increasing international pressure for greater sustainability has resulted in a surge in the demand for Omco’s glass products, which are 100 per cent recyclable. This has enabled the company to increase capacity at three of its main European facilities. What’s more, a recent joint venture with Hindustan National Glass of India has also added significantly to the company’s global manufacturing capability. The new company is operating under the name of Omco HNG Engineering Ltd, and this modern plant is equipped with the latest CNC machines and foundry equipment.
In addition, the company has also made significant investments in new technology at its Romanian, Croatian and UK production sites in order to meet the growing demand for energy-efficient, recyclable glass containers.
As well as saving energy costs, Omco is also able to manufacture its precision moulds with unparalleled speed and efficiency. The company’s ‘Individual Sector’ (IS) is capable of producing more than 600 hollow glass products per minute from a single mould, and each mould has the ability to manufacture up to one million glass containers. Omco also applies a special nickel coating to protect the edges of each mould, thereby ensuring that there is no ‘break-away.
Market segment focus
Omco has seen exceptional growth of more than 20 per cent per annum in the last few years, despite the global economic downturn. This has been attributed not to a major increase in volumes of products manufactured, but through achieving a better focus on serving its individual market sectors, which includes shorter, low and ultra-low series that employ more complex casting and special composite alloys.
One of the company’s biggest market sectors is the automotive industry where the focus is on glass moulds and metal-based products. However, the company also delivers special alloys and castings tailored to satisfy the direct needs of key customers in other sectors of industry, such as agriculture, earthwork machinery, pumps and incinerators. Omco constantly looks to the world markets to identify new industry trends and consumer needs and it responds to these with tailor-made, optimal solutions. n
For further details about Omco’s specialised range of foundry products and engineering services visit: www.omcomould.com
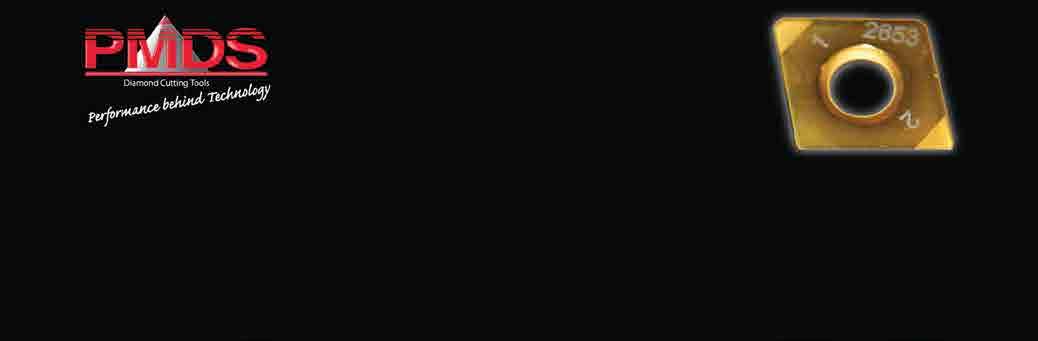
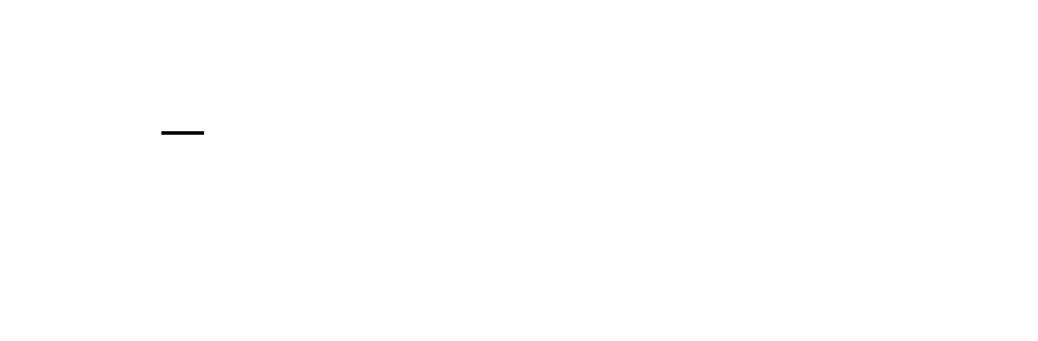
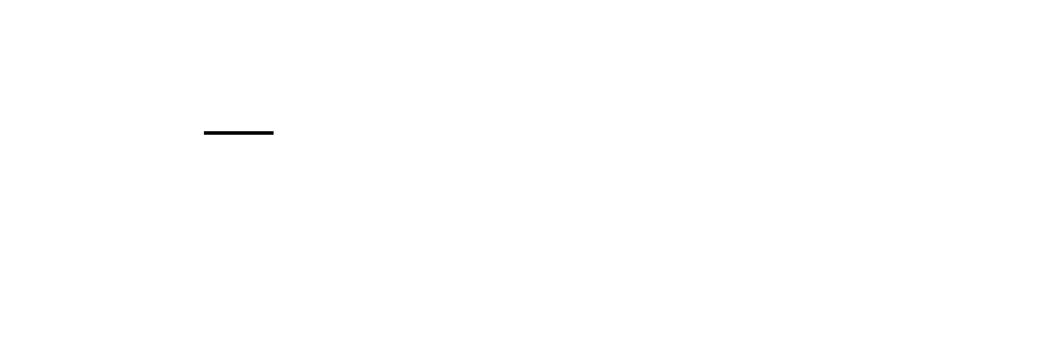
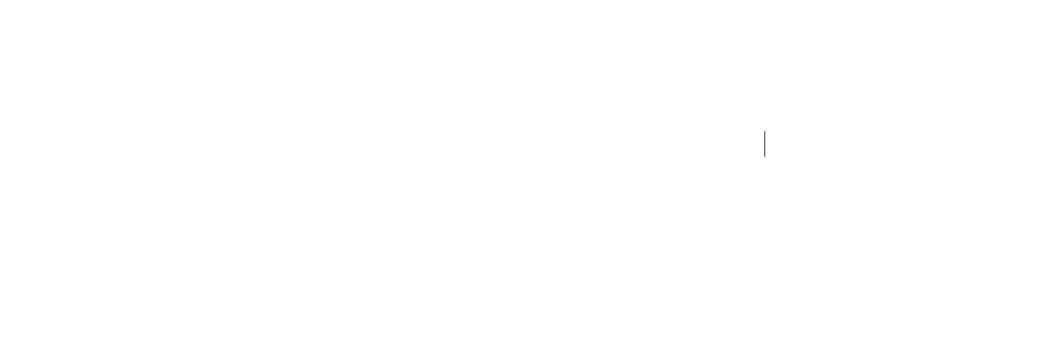
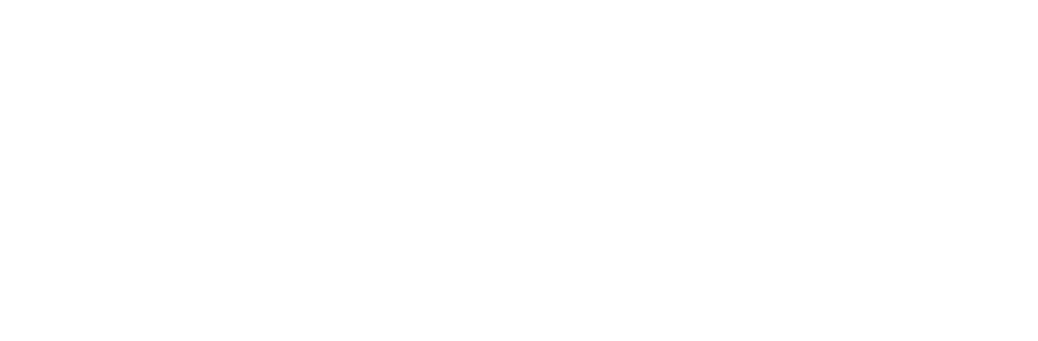
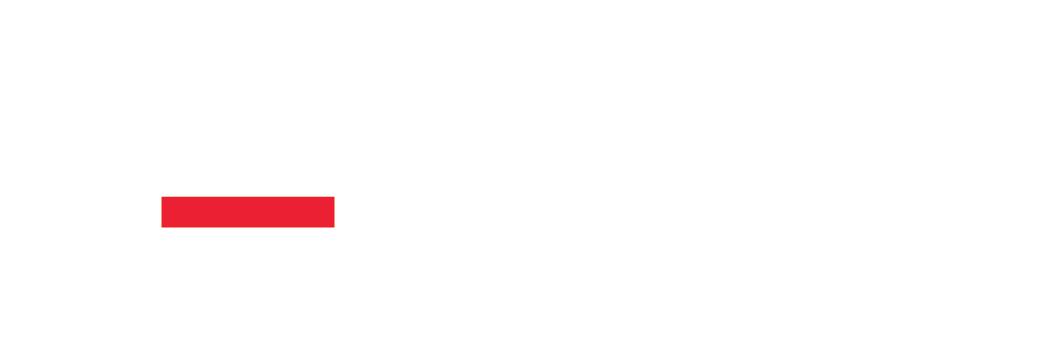
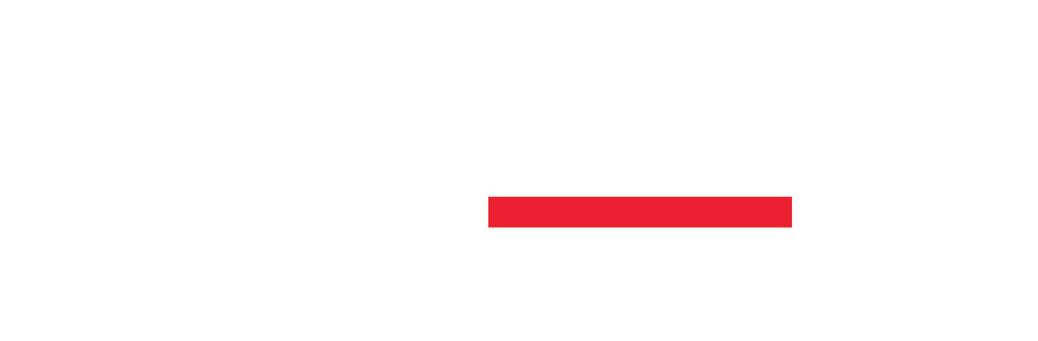
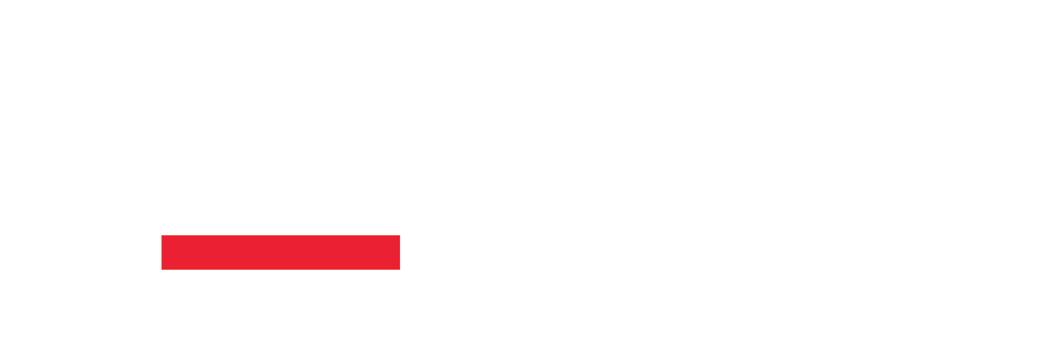

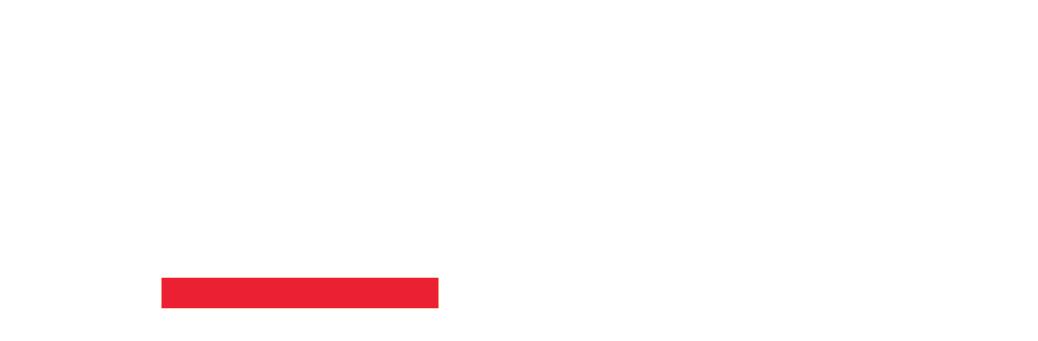